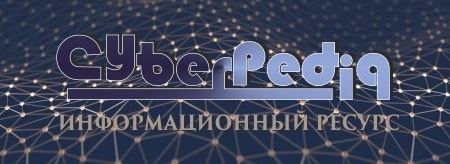
Археология об основании Рима: Новые раскопки проясняют и такой острый дискуссионный вопрос, как дата самого возникновения Рима...
Общие условия выбора системы дренажа: Система дренажа выбирается в зависимости от характера защищаемого...
Топ:
Характеристика АТП и сварочно-жестяницкого участка: Транспорт в настоящее время является одной из важнейших отраслей народного хозяйства...
История развития методов оптимизации: теорема Куна-Таккера, метод Лагранжа, роль выпуклости в оптимизации...
Устройство и оснащение процедурного кабинета: Решающая роль в обеспечении правильного лечения пациентов отводится процедурной медсестре...
Интересное:
Влияние предпринимательской среды на эффективное функционирование предприятия: Предпринимательская среда – это совокупность внешних и внутренних факторов, оказывающих влияние на функционирование фирмы...
Уполаживание и террасирование склонов: Если глубина оврага более 5 м необходимо устройство берм. Варианты использования оврагов для градостроительных целей...
Аура как энергетическое поле: многослойную ауру человека можно представить себе подобным...
Дисциплины:
![]() |
![]() |
5.00
из
|
Заказать работу |
|
|
Предохранительный клапан
Пружинный Полноподъемный предохранительный клапан
Подбор и установка манометров на сосудах и оборудовании.
Каждый сосуд и самостоятельные полости с разными давлениями должны быть снабжены манометрами прямого действия. Манометр устанавливается на штуцере сосуда или трубопроводе между сосудом и запорной арматурой. Манометры должны иметь класс точности не ниже: 2,5 - при рабочем давлении сосуда до 2,5 МПа (25 кгс/см2), 1,5 - при рабочем давлении сосуда выше 2,5 МПа (25 кгс/см2).
Манометр должен выбираться с такой шкалой, чтобы предел измерения рабочего давления находился во второй трети шкалы.
Пример:
Рабочее давление сосуда 10 кгс/см2 , 10х3=30 кгс/см2, 30/2=15 кгс/см2, на 15 кгс/см2 манометров нет, ставим ближайший по показаниям 16 кгс/см2
ГОСТ 2405-88 Манометры, вакуумметры, мановакуумметры, напоромеры, тягомеры и тягонапоромеры. Общие технические условия
Диапазон показаний (записи) прибора должен выбираться из таблицы.
Рис. №1. Заглушка фланцевая.
Фланцевая заглушка фиксируется крепежом (шпильками, болтами) к концевому фланцу трубопровода или оборудования. Уплотнение для фланцевого соединения с глухим фланцем подбирается в зависимости от среды, температуры и давления. Фланцевая заглушка по форме идентична фланцу, но не имеет отверстия для прохождения транспортируемого вещества.
Межфланцевая поворотная заглушка по форме напоминает очки и может также называться очковой заглушкой или очками Шмидта, другие названия – реверсивная заглушка и обтюратор.
Рис.№2. Межфланцевая поворотная заглушка.
|
Поворотная заглушка состоит из двух частей: одна часть – глухая, которая служит для перекрытия среды, а в другой части есть отверстие для открытия потока. Между собой две части соединены перемычкой с отверстием для фиксации на оси. В роли оси, вокруг которой вращают заглушку, выполняет шпилька (болт), применяемая для стяжки фланцевого соединения, устанавливаемая прямо в болтовые отверстия фланцев. Для обеспечения герметичности соединения на сердечник заглушки с двух сторон крепится уплотнитель, который подбирается для заданных условий эксплуатации трубопровода.
Рис. №3. Фланцевое соединение с поворотной заглушкой.
Межфланцевая заглушка с рукояткой состоит из глухой части и рукоятки (хвостовика) прикрепленного к ней.
Рис. №4. Межфланцевая заглушка с рукояткой.
Заглушки с рукояткой также предназначены для установки между фланцами на время проведения работ. После использования заглушка вынимается и фланцы стягиваются.
Рис. №5. Фланцевое соединение с заглушкой с рукояткой.
Все фланцевые заглушки должны быть из марки металла, соответствующей условиям эксплуатации трубопровода. Температурные пределы применения материала заглушки должен соответствовать температурным пределам применения материала фланцев.
Толщина стенки заглушки определяется расчетом на прочность в зависимости от рабочих параметров и коррозионно-эрозийных свойств среды транспортируемой трубопроводом.
В связи с тем, что фланцевое соединение с установленной в него заглушкой должно отвечать высоким требованиям по безопасности и герметичности, большое внимание уделяется правильному подбору уплотнения для конкретного узла, в зависимости от рабочей среды, температуры и давления. В качестве уплотнительного элемента в заглушках используются: паронит, фторопласт, прокладки на графитовой основе или стальные прокладки, оптимально подобранные под условия эксплуатации трубопровода.
|
Исполнение фланцевых и межфланцевых заглушек.
Уплотнительная поверхность фланцевых и межфланцевых заглушек – поверхность контакта двух фланцев и межфланцевой фланцевой заглушки или поверхность контакта фланца и фланцевой заглушки. Фланцы и заглушки должны иметь соответствующие друг другу уплотнительные поверхности. Пример: для фланца, имеющего выточку под прокладку, заглушка должна быть с выступом, так как форма уплотнительной поверхности заглушки отвечает форме контактной поверхности фланца.
По исполнению уплотнительной поверхности заглушки различаются:
- исполнение 1 - заглушки с соединительным выступом на условное давление до 4,0 МПа (40 кгс/см2);
Рис. №6. Заглушка межфланцевая с рукояткой исполнение 1.
- исполнение 2 - заглушки с выступом и впадиной на условное давление от 4,0 до 6,3 МПа (от 40 до 63 кгс/см2);
Рис. №7. Заглушка межфланцевая с рукояткой исполнение 2.
- исполнение 3 - заглушки с шипом и пазом на условное давление от 0,6 до 6,3 МПа (от 6 до 63 кгс/см2);
Рис. №8. Заглушка межфланцевая с рукояткой исполнение 3.
- исполнение 4 - заглушки под прокладку овального сечения на условное давление от 6,3 до 16,0 МПа (от 63 до 160 кгс/см2);
Рис. №9. Заглушка межфланцевая поворотная исполнение 3.
Маркировка заглушек.
На каждой заглушке (на хвостовике, а при его отсутствии - на цилиндрической поверхности) должно быть четко выбиты:
- номер заглушки согласно перечня ответственных заглушек. На каждом технологическом объекте существует перечень ответственных заглушек, в котором каждой заглушке присвоен свой номер и указаны: материал заглушки, номер сертификата на изготовление заглушки, толщина заглушки, отбраковочная (расчетная) толщина заглушки;
- марка стали из которой изготовлена заглушка;
- условное давление, Ру;
- условный проход, Ду.
Пример: на хвостовике заглушки выбито
№ 2
Ст20
Ду 50
Ру 16
Это значит, что в перечне ответственных заглушек данная заглушка числится за №2.
Заглушка изготовлена из стали марки Ст20. Заглушка диаметром 57 мм и расчитана (исполнение 1) на давление 1,6 МПа (16 кгс/см2)
Элемент трубопровода, предназначенный для глухого запечатывания его выходных отверстий.
|
Особые концевые заглушки используют также для закрывания входных и выходных отверстий трубопроводов при проведении испытаний. Необходимы концевые заглушки и при построении разветвленных магистральных сетей.
Металлические концевые заглушки различаются по виду своего исполнения и используемому типу крепления. Здесь можно выделить следующие типы концевых заглушек:
- плоские заглушки, закрепляемые с помощью сварки;
- фланцевые стальные;
- эллиптические;
- сферические;
- быстросъемные;
- межфланцевые.
Как показывает опыт эксплуатации трубопроводов, заглушки металлические концевые являются сегодня их самым слабым местом. Испытывая повышенные нагрузки и не имея достаточно надежного слоя изоляции, заглушки в первую очередь подвергаются разрушению и разгерметизации.
По конструктивному исполнению заглушки стальные для трубопроводов подразделяют на приварные сферические, плоские, плоские ребристые и фланцевые.
Рис. Заглушки для технологических трубопроводов: а – сферическая, б – плоская, в – плоская ребристая, г – фланцевая.
Фото Заглушка сферическая для концевых участков трубопроводов.
Фото Заглушка фланцевая (концевая).
Допускается применение приварных плоских и ребристых заглушек из листовой стали для трубопроводов при PN до 2,5 МПа, с условным проходом от 40 до 600 мм.
Заглушки сферические стальные применяются на условное давление до 10МПа с условным диаметром от 300 до 1600 мм. Они должны изготавливаться из листовой стали марок МСт3 и сталь 20 и 10Г2.
Заглушки межфланцевые предназначены для отключения и герметизации оборудования или участков трубопроводов от действующей технологической системы при выводе в ремонт и на обслуживание.
Заглушки должны изготавливаться в заводских условиях в соответствии с нормативно-технической документацией. На материалы из которых изготовлены заглушки должен быть сертификат.
Тип заглушки должен соответствовать типу фланцевого соединения.
Рис. Заглушка межфланцевая
Рис. Заглушка межфланцевая поворотная
Заглушки, устанавливаемые между фланцами, не рекомендуется в целях обеспечения безопасности применять для разделения двух трубопроводов с различными средами, смешение которых недопустимо.
|
Заглушки устанавливаются по распоряжению ответственного лица.
На торце или хвостовике заглушки должно быть выбито условное давление, диаметр, № заглушки, марка стали из которой она изготовлена.
Перед установкой заглушки данные заносятся в «Журнал установки и снятии заглушек» с указанием:
- порядковый номер записи
- дата и времени установки
- точное место установки
- № заглушки, Ду, Ру
- должность лица, давшего указание на установку
- кто установил
- кто дал распоряжение на снятие
- кто снял
Контрольные вопросы:
1. Дайте определение, что такое заглушки для фланцевых соединений.
2. На какие виды разделяются заглушки?
3. Из какой марки металла должны быть изготовлены заглушки?
4. Как определяется необходимая толщина заглушки?
5. Какие уплотнительные поверхности должны иметь заглушки устанавливаемые на фланцевые соединения?
6. Что должно быть четко выбито (на хвостовике, а при его отсутствии - на цилиндрической поверхности) фланцевой заглушки?
Классификация трубопроводов
Трубопровод – сооружение из труб, деталей трубопровода, арматуры, плотно соединённых между собой, предназначенное для транспортирования газообразных и жидких продуктов.
Соединение фланцевое – неподвижное разъёмное соединение трубопровода, герметичность которого обеспечивается путём сжатия непосредственно друг с другом или через посредство расположенных между ними прокладок из более мягкого материала, сжатых крепёжными деталями.
Соединение сварное – неподвижное соединение трубопровода, герметичность которого обеспечивается с использованием сварки.
Отвод – фасонная деталь трубопровода, обеспечивающая изменение направления потока транспортируемого вещества.
Переход - деталь, предназначенная для плавного изменения диаметра трубопровода.
Тройник – фасонная деталь трубопровода для слияния или деления потоков транспортируемого вещества под углом 90º.
Штуцер – деталь, предназначенная для присоединения к трубопроводу арматуры, контрольно-измерительных приборов и т.п.
Трубопроводная арматура – устройства, устанавливаемые на трубопроводах и обеспечивающие управление потоками рабочих сред путём изменения проходного сечения.
Дренажи - устройства для периодического или непрерывного отвода жидкости.
Опоры и подвески трубопроводов - трубопроводы следует монтировать на опорах или подвесках. Расположение опор (неподвижных, скользящих, катковых, пружинных и т.д.), подвесок и расстояние между ними определяются проектом.
Компенсаторы - температурные деформации следует компенсировать за счет поворотов и изгибов трассы трубопроводов. При невозможности ограничиться самокомпенсацией (например, на совершенно прямых участках значительной протяженности) на трубопроводах устанавливаются П-образные, линзовые, волнистые и другие компенсаторы.
|
Предохранительный клапан – устройство для сброса избыточного давления.
Трубопроводы с давлением до 10 МПа (100 кгс/см2) включительно в зависимости от класса опасности транспортируемого вещества (взрыво-, пожароопасность и вредность) подразделяются на группы (А, Б, В) и в зависимости от рабочих параметров среды (давления и температуры) - на пять категорий (I, II, III, IV, V).
Категории трубопроводов определяют совокупность технических требований к конструкции, монтажу и объему контроля трубопроводов (табл.1).
Класс опасности технологических сред определяется разработчиком проекта на основании классов опасности веществ, содержащихся в технологической среде, и их соотношений.
Категории трубопроводов устанавливаются разработчиком проекта для каждого трубопровода и указываются в проектной документации.
Допускается в зависимости от условий эксплуатации принимать более ответственную (чем определяемую рабочими параметрами среды) категорию трубопроводов.
Таблица 1
Классификация трубопроводов Pу <= 10 МПа (100 кгс/см2)
Группа среды | Транспортируемые вещества | Категория трубопроводов | |||||||||||||||||||
I | II | III | IV | V | |||||||||||||||||
Pрасч., МПа | tрасч., °C | Pрасч., МПа | tрасч., °C | Pрасч., МПа | tрасч., °C | Pрасч., МПа | tрасч., °C | Pрасч., МПа | tрасч., °C | ||||||||||||
1 | 2 | 3 | 4 | 5 | 6 | 7 | 8 | 9 | 10 | 11 | |||||||||||
А | Вещества с токсичным действием по ГОСТ 12.1.007 | ||||||||||||||||||||
а) чрезвычайно опасные вещества класса 1, высокоопасные вещества класса 2 (бензол, кислоты концентрированные, оксид этилена, сероуглерод и т.п.) | Независимо | Независимо |
|
|
|
|
|
| |||||||||||||
б) умеренно опасные вещества класса 3 (аммиак жидкий и газообразный, кислота акриловая, спирт метиловый, толуол, ксилол и т.п.) | Свыше 2,5 | Свыше 300 или ниже минус 40 | От вакуума 0,08 до 2,5 | От минус 40 до 300 |
|
|
|
|
| ||||||||||||
Вакуум ниже 0,08 | Независимо |
|
|
|
|
| |||||||||||||||
Б | Взрывопожароопасные вещества по ГОСТ 12.1.044 | ||||||||||||||||||||
а) горючие газы (ГГ), в том числе сжиженные углеводородные газы (СУГ) (этан, этилен, пропан, пропилен, водород, метан, факельный газ и т.п.) | Свыше 2,5 | Свыше 300 или ниже минус 40 | От вакуума 0,08 до 2,5 | От минус 40 до 300 |
|
|
|
|
| ||||||||||||
Вакуум ниже 0,08 | Независимо |
|
|
|
|
| |||||||||||||||
б) легковоспламеняющиеся жидкости (ЛВЖ) (ацетон, бензины, керосин, изопентан, пентан, этиловый спирт, нефть, дизельное топливо и т.п.) | Свыше 2,5 | Свыше 300 или ниже минус 40 | Свыше 1,6 до 2,5 | От 120 до 300 |
|
|
|
|
| ||||||||||||
Вакуум ниже 0,08 | Независимо | Вакуум выше 0,08 | От минус 40 до 300 | До 1.6 | От минус 40 до 120 |
|
|
| |||||||||||||
в) горючие жидкости (ГЖ) (мазут, масла, битум, дистилляты и т.п.) | Свыше 6,3 | Свыше 350 или ниже минус 40 | Свыше 2,5 до 6,3 | Свыше 250 до 350 | Свыше 1,6 до 2,5 | Свыше 120 до 250 | До 1,6 | От минус 40 до 120 |
|
| |||||||||||
Вакуум ниже 0,003 | От вакуума 0,003 до вакуума 0,08 | Вакуум выше 0,08 | От минус 40 до 250 |
|
| ||||||||||||||||
В | Трудногорючие (ТГ) и негорючие вещества (НГ) (азот, воздух, инертные газы, пар, вода и т.п.) | Вакуум ниже 0,003 | Свыше 450 или ниже минус 40 | От вакуума 0,003 до вакуума 0,08 или до 6,3 | Свыше 350 до 450 | Свыше 2,5 до 6,3 | От 250 до 350 | Свыше 1,6 до 2,5 | Свыше 120 до 250 | От вакуума 0,08 до 1,6 | От минус 60 до 120 | ||||||||||
Свыше 6,3 | От вакуума 0,08 до 1,6 | Ниже минус 40 | |||||||||||||||||||
Свыше 6,3 | От вакуума 0,08 до 1,6 | Ниже минус 40 | |||||||||||||||||||
Обозначение группы определенной транспортируемой среды включает в себя обозначение группы среды (А, Б, В) и обозначение подгруппы (а, б, в), отражающее класс опасности вещества.
Обозначение группы трубопровода в общем виде соответствует обозначению группы транспортируемой среды. Обозначение "трубопровод группы А (б)" обозначает трубопровод, по которому транспортируется среда группы А (б).
Группа трубопровода, транспортирующего среды, состоящие из различных компонентов, устанавливается по компоненту, требующему отнесения трубопровода к более ответственной группе. При этом, если при содержании в смеси опасных веществ 1, 2 и 3 классов опасности концентрация одного наиболее опасна, группу смеси определяют по этому веществу.
В случае, если наиболее опасный по физико-химическим свойствам компонент входит в состав смеси в незначительном количестве, вопрос об отнесении трубопровода к менее ответственной группе или категории решается проектной организацией.
Класс опасности вредных веществ и показатели пожаровзрывоопасности веществ следует принимать по государственным стандартам.
Категорию трубопровода следует устанавливать по параметру, требующему отнесения его к более ответственной категории.
Для вакуумных трубопроводов следует учитывать не условное давление, а абсолютное рабочее давление.
Трубопроводы, транспортирующие вещества с рабочей температурой, равной или превышающей температуру их самовоспламенения, или рабочей температурой ниже минус 40 град. C, а также несовместимые с водой или кислородом воздуха при нормальных условиях, следует относить к I категории [Руководство по безопасности «Рекомендации по устройству и безопасной эксплуатации технологических трубопроводов». [Серия 03. Выпуск 67. — М.: Закрытое акционерное общество «Научно-технический центр исследований проблем промышленной безопасности», 2013. — 194 с.].
При выборе типа уплотнительной поверхности фланцев по ГОСТ 12815-80 для соединения трубопроводов в зависимости от транспортируемой среды и давления необходимо руководствоваться рекомендациями, представленными в таблице 2.
Таблица 2
Схемы объемных насосов
Рис. 2
а – плунжерный; б – диафрагменный; в – лопастной; г – шестеренный; д - винтовой
Классификация насосов по конструктивному исполнению
Насосы |
Электромагнитные |
Объемные |
Шестеренные |
Винтовые (роторные) |
Возвратно- поступательные |
Поршневые |
Плунжерные |
Диафрагменные |
Динамические |
Лопастные |
Центробежные |
Осевые |
Трения |
Вихревые |
Черепаховые |
Шнековые |
Дисковые |
Вибрационные |
Струйные |
Основные виды уплотнений валов и штоков насосов.
В насосах используют в основном контактные уплотнения вала двух типов: сальники с мягкой набивкой и торцовые уплотнения.
До недавнего времени чаще всего использовались сальниковые уплотнения, достаточно надежные при работе на нетоксичных, невзрывоопасных жидкостях при сравнительно низком давлении. Однако сальники работают при некоторой обязательной утечке жидкости, постепенно увеличивающейся в процессе эксплуатации уплотнения, что требует систематической подтяжки его. Все это удорожает обслуживание и усложняет автоматизацию технологических процессов, а в ряде случаев не обеспечивает необходимой надежности.
Торцовые уплотнения по ряду эксплуатационных преимуществ (не требуют обслуживания, работают практически без утечки, долговечны, экономичны) в последние годы широко применяют в промышленности. Торцовые уплотнения способны работать при давлении до 45 МПа, температуре от-200 до 450 0С, скорости скольжения в парах трения до 100 м/с, в условиях агрессивных и абразивных сред.
Сальниковые уплотнения.
Сальниковое уплотнение с набивкой (рис. 1) относится к контактным уплотнениям и предназначено для предотвращения интенсивных внешних утечек перекачиваемой жидкости из насоса.
Уплотнения сальниковые с набивкой
Рис. 1
а – без гидравлического кольца; б – с разгрузочным осевым импеллером; в – с наружным охлаждением; г – с комбинированным охлаждением;
1 – нажимная втулка; 2 – корпус сальника; 3 – корпус насоса; 4 – кольцо гидрозатвора; 5 – кольца сальниковой набивки; 6 – защитная втулка
Набивные сальниковые уплотнения из-за своей простоты довольно распространены в разных типах насосов. Они надежно работают при давлении перед сальником до 1 МПа и окружной скорости вращения защитной втулки вала до 20 м/с. Корпус 2 сальника фиксируется в корпусе 3 насоса. В нем устанавливают кольца 5 сальниковой набивки, а между ними кольцо 4 гидрозатвора, к которому подводится охлаждающая вода по сверлению.
В осевом направлении кольца набивки сжимаются втулкой 1, при этом набивка прижимается к защитной втулке 6, обеспечивая уплотнение.
Для насосов, перекачивающих нефтепродукты при температуре до 80 0С, используют асбестовые набивки, пропитанные смесью масла и графитом. При температуре перекачиваемой среды до 2000С применяют асбеста-свинцовую набивку, при температуре свыше 2000С – асбеста-алюминиевую.
Одинарные торцовые уплотнения. Несмотря на многообразие конструктивных схем, любое одинарное торцовое уплотнение состоит из нескольких конструктивных постоянных элементов. Торцовое уплотнение включает пару трения, состоящую из двух уплотнительных колец 4 и 6, прилегающих друг к другу по плоскому торцу (рис. 2).
Схема одинарного торцевого уплотнения
Рис. 2
1 – поджимающий элемент; 2 – пружина; 3,7 – уплотнительные элементы; 4 – уплотнительное кольцо; 5 – поводковая система; 6 – кольцо
Кольцо 6 фиксируют либо в корпусе, либо на валу и герметизируют уплотнительным элементом 7, а кольцо 4, имеющее свободу угловых и осевых перемещений, устанавливают в поджимающем элементе 1. В этот элемент входят пружины 2, прижимающие упруго устанавливаемое уплотнительное кольцо к другому уплотнительному кольцу, вторичный уплотнительный элемент 3, обеспечивающий герметизацию упруго устанавливаемого уплотнительного кольца, и поводковая система 5, передающая момент трения с уплотнительного кольца. Различие в конструкции каждого из этих элементов и особенности их взаимосвязей обеспечивают очень большой набор различных конструкций торцовых уплотнений.
Принципиальные схемы одинарных торцовых уплотнений определяются следующими конструктивными основными решениями: гидравлически разгруженный или неразгруженный стык пары трения, внутреннее или внешнее расположение стыка пары трения относительно уплотняемой жидкости, вращающийся или неподвижный поджимающий элемент и пружина, которая расположена в уплотняемой среде либо вынесена за её пределы. Сочетания указанных конструктивных решений и дают возможные конструкции одинарных торцовых уплотнений. Выбор той или иной конструктивной схемы определяется конкретными условиями эксплуатации.
Торцовые уплотнения типов БО и БД предназначены для герметизации валов центробежных нефтяных насосов, перекачивающих нефть, нефтепродукты, сжиженные углеводородные газы, органические растворители, а также другие жидкости, сходные с указанными по химико-физическим свойствам.
Перекачиваемая жидкость не должна содержать твёрдых взвешенных частиц в количестве боле 0,2% по массе и размером 0,2 мм.
Конструкция торцового уплотнения тип БО показана на рис. 3.
Торцевое уплотнение типа БО
Рис. 3
1 – вращающаяся втулка; 2 – гильза; 3 – неподвижная втулка; 4 – аксиально-подвижная обойма; 5 – корпус уплотнения; 6 – пружины; 7 – резиновые уплотнительные кольца; 8 – фиксирующие штифты; 9 – встроенный импеллер; 10 – кольцевая проточка; 11 – камера; 12 – гнезда; 132 – каналы; 14 – цилиндрическая щель; 15 – эксцентрическая проточка; 16 – входное отверстие
Двойные торцовые уплотнения. Наряду с одинарными торцовыми уплотнениями в промышленности используют и более сложные узлы - уплотнительные комплексы. Наиболее универсальным из них является двойное торцовое уплотнение, состоящее из двух одинарных торцовых уплотнений.
Полное отделение перекачиваемой жидкости от атмосферы может достигаться применением двух одинарных торцовых уплотнений с подачей между ними затворной жидкости. При этом внутреннее уплотнение разделяет перекачиваемую среду и затворную жидкость, а внешнее - затворную жидкость и атмосферу.
Двойные торцовые уплотнения применяют в следующих случаях: для перекачивания газообразных сред и жидкостей, обладающих плохой смазывающей способностью; жидкости под высоким давлением, при высокой температуре, содержащих твердые включения; кристаллизующихся в зоне трения при испарении жидкой фазы; токсичных; легковоспламеняющихся или горючих.
Применение двойных торцовых уплотнений отвечает требованиям техники безопасности и позволяет предотвратить отложение на валу насоса и на деталях уплотнения продуктов, содержащихся в утечках.
Конструкция торцового уплотнения типа УСГ показана на рис. 4
Предохранительный клапан
пружинный Полноподъемный предохранительный клапан
|
|
Двойное оплодотворение у цветковых растений: Оплодотворение - это процесс слияния мужской и женской половых клеток с образованием зиготы...
Организация стока поверхностных вод: Наибольшее количество влаги на земном шаре испаряется с поверхности морей и океанов (88‰)...
Таксономические единицы (категории) растений: Каждая система классификации состоит из определённых соподчиненных друг другу...
Биохимия спиртового брожения: Основу технологии получения пива составляет спиртовое брожение, - при котором сахар превращается...
© cyberpedia.su 2017-2024 - Не является автором материалов. Исключительное право сохранено за автором текста.
Если вы не хотите, чтобы данный материал был у нас на сайте, перейдите по ссылке: Нарушение авторских прав. Мы поможем в написании вашей работы!