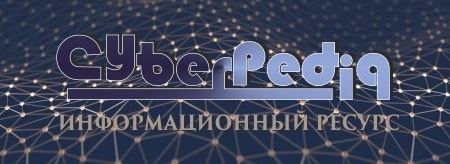
Поперечные профили набережных и береговой полосы: На городских территориях берегоукрепление проектируют с учетом технических и экономических требований, но особое значение придают эстетическим...
Историки об Елизавете Петровне: Елизавета попала между двумя встречными культурными течениями, воспитывалась среди новых европейских веяний и преданий...
Топ:
Эволюция кровеносной системы позвоночных животных: Биологическая эволюция – необратимый процесс исторического развития живой природы...
Устройство и оснащение процедурного кабинета: Решающая роль в обеспечении правильного лечения пациентов отводится процедурной медсестре...
Интересное:
Мероприятия для защиты от морозного пучения грунтов: Инженерная защита от морозного (криогенного) пучения грунтов необходима для легких малоэтажных зданий и других сооружений...
Как мы говорим и как мы слушаем: общение можно сравнить с огромным зонтиком, под которым скрыто все...
Отражение на счетах бухгалтерского учета процесса приобретения: Процесс заготовления представляет систему экономических событий, включающих приобретение организацией у поставщиков сырья...
Дисциплины:
![]() |
![]() |
5.00
из
|
Заказать работу |
|
|
1.4.1. Правила эксплуатации станков
Эксплуатация станков представляет собой систему мероприятий, включающую транспортирование и монтаж станков, их настройку и наладку, контроль геометрической и технологической точности, уход и обслуживание.
Транспортирование станков необходимо осуществлять строго по инструкции, указанной в руководстве по эксплуатации. Перемещать станки по цеху можно лишь волоком на листе или на специальной тележке. Тяжелые станки для удобства ремонта располагают в зоне действия подъемно-транспортных средств.
Станки нормальной точности, легкие и средние, устанавливают на общее бетонное полотно цеха с тщательной выверкой положения уровнем и регулировкой с помощью клиньев. Надежное крепление осуществляется посредством фундаментных болтов и заливкой основания станка бетоном.
Точные и тяжелые станки устанавливают на индивидуальные фундаменты. Также на индивидуальные виброизолирующие фундаменты ставят станки с большими динамическими нагрузками и повышенной вибрацией при работе, для того чтобы изолировать станок от другого оборудования и воспрепятствовать передаче колебаний через грунт. С той же целью станки устанавливают на виброизолирующие опоры.
Если станки транспортируют в частично разобранном состоянии, то после установки их монтируют. Выполняют заземление, подводят электропитание и, если необходимо, соединяют коммуникации центральной подачи смазывающе-охлаждающей жидкости, стружкоудаления, сети сжатого воздуха.
Наладку и настройку станков производят также в строгом соответствии с руководством по эксплуатации. Наладка – это совокупность операций по подготовке и регулированию станка, включающих настройку кинематических цепей, установку и регулирование приспособлений, инструментов, а также другие работы, необходимые для обработки деталей.
|
Настройка – это регулирование параметров машины в связи с изменением режима работы в период эксплуатации. Со временем настройка станка частично нарушается, и периодически требуется ее восстановление (подналадка).
На универсальных станках настройку режимов резания производит станочник непосредственно перед или во время обработки, устанавливая рукоятками частоту вращения шпинделя, подачу и глубину резания. На специальных и специализированных станках режимы резания устанавливаются заранее, согласно карте наладки, путем установки сменных колес в цепях главного движения и подач. Наладку завершают регулировкой инструментов на размер и пробными работами.
Геометрическую точность станков проверяют в соответствии с ГОСТами. Суть проверки заключается в контроле точности и взаимного расположения базовых поверхностей, формы траектории движения исполнительных органов (например биение шпинделя), в проверке соответствия фактических перемещений исполнительного органа номиналу (например, точность позиционирования, кинематическая точность).
Технологическую точность, которая относится в большей степени к специальным и специализированным станкам и станочным системам, контролируют перед началом эксплуатации оборудования. Для этого на станке обрабатывают партию деталей, измеряют их и сиспользованием методов математической статистики оценивают рассеяние размеров, вероятность выпадения размеров за пределы заданного допуска и другие показатели технологической точности.
Уход и обслуживание включает чистку и смазывание, осмотр и контроль состояния механизмов идеталей, уход за гидросистемой, системами смазывания и подачи СОЖ, регулировку и устранение мелких неисправностей. При эксплуатации автоматизированных станков применяют смешанную форму обслуживания: наладку производит наладчик, а подналадку – оператор. При этом функции оператора разнообразны: приемка заготовок и их установка, снятие готовых деталей, оперативное управление, периодический контроль деталей, смена или регулирование режущего инструмента, регулирование подачи СОЖ, контроль удаления стружки идр.
|
Уход за гидросистемой предусматривает контроль температуры масла, которая обычно не должна превышать + 50 ° С. Первую замену масла в гидросистеме, как правило, производят через 0,5-1 месяц работы, чтобы удалить продукты притирки механизмов. В дальнейшем замену масла производят через четыре-шесть месяцев. Необходимо систематически контролировать иподдерживать уровень масла, следить за состоянием трубопроводов, чтобы не было утечек и не попал воздух в гидросистему, регулярно проводить чистку фильтров.
Уход за электрооборудованием включает ежемесячную очистку аппаратов от пыли и грязи, подтягивание винтовых соединений, контроль плавности перемещений и надежность возврата подвижных частей электроаппаратов в исходное положение. Периодически смазывают приводы аппаратов тонким слоем смазочного материала, не допуская попадания его на контакты. Раз в полгода меняют полярность рабочих контактов у кнопок и выключателей, работающих в цепях постоянного тока, проверяют состояние контактов. При появлении пригара или капель металла на поверхности контактов их слегка зачищают бархатным надфилем (зачистка абразивными материалами недопустима).
Особенности эксплуатации станков обязательно указывают в инструкциях по эксплуатации. Соблюдение инструкций обеспечит длительную, бесперебойную работу оборудования.
Испытания станков
Если исследования станка (точнее, его прототипа) проводят, как правило, до начала конструирования, тоиспытания завершают процесс его изготовления. В настоящее время основными видами испытаний являются приемочные испытания опытных образцов новых моделей станков и приемосдаточные испытания серийно выпускаемых станков.
Первый вид испытаний предназначен для решения вопроса о целесообразности постановки на производство данной модели станка или передачи ее в эксплуатацию. Эти испытания обычно проводят в лабораторных условиях, а материалы испытаний предъявляют государственной приемочной комиссии.
|
Приемосдаточные испытания проводят контролеры ОТК завода в цеховых условиях сцелью проверки работоспособности готового серийного станка и соответствия его заранее установленным техническим условиям.
В соответствии с существующими типовыми методиками испытаний металлорежущих станков каждый вид испытаний включает три группы проверок: в статическом состоянии; на холостом ходу; при работе. Объем и содержание проверок могут сильно различаться в зависимости от вида испытаний. Более полными и сложными являются проверки, которым подвергают станок в ходе приемочных испытаний. В несколько упрощенном и сокращенном виде эти же проверки составляют содержание приемосдаточных испытаний серийных станков. С порядком проведения испытаний можно познакомиться на примере приемочных испытаний станков при выполнении лабораторных работ.
Перед проведением испытаний станок устанавливают на специальном фундаменте. Клиновыми башмаками, располагаемыми так же, как при эксплуатации, станок выверяют по уровню в продольном и поперечном направлениях в соответствии с требованиями ГОСТ 8-82. Фундаментные болты не затягивают. В зависимости от класса точности станка используют разные уровни сценой деления 0,04 мм/м для станков классов точности Н и П; 0,02 мм/м – для станков классов точности В, А и С.
После этого приступают к проверкам станка в статическом состоянии. Вначале проверяют соответствие нормам точности – это одна из важнейших проверок. Для того чтобы проверить точность работы станка, надо знать характер и степень влияния отдельных факторов, вызывающих погрешности обработки. Пока практически не существует таких норм точности работы станка, которые определяли бы ее однозначно. Это объясняется большим количеством факторов, влияющих на точность его работы. Основными из них являются следующие: геометрическая, в том числе кинематическая, точность станка, включая погрешности технологической базы заготовки; температурные деформации станка; его упругие деформации под нагрузкой; устойчивость системы станка при перемещениях узлов и обработке; вынужденные колебания; размерный износ инструмента.
|
Все эти факторы, за исключением геометрической точности станка, являются переменными и отчасти управляемыми; влияние их на точность детали можно почти устранить, снижая или меняя режим обработки и т.д., так что в конечном итоге достижимая точность будет определяться геометрической точностью станка. Последняя характеризует качество изготовления и сборки станка и, хотя не может количественно характеризовать точность детали, обработанной на этом станке, является одной из важных характеристик возможностей станка.
Точность нормируется ГОСТами «Нормы точности», построенными на предположении, что геометрические погрешности данного станка являются систематическими, которые полностью переносятся на обрабатываемую деталь. Это позволяет не проводить анализ результирующей погрешности на детали в целях выявления влияния только геометрических погрешностей станка, что очень трудно, а заменить проверку детали соответствующей геометрической проверкой станка.
При проведении испытаний большое значение имеют условия, при которых проводят измерения. Проверку нужно проводить при температуре 20°С; колебания температуры не должны превышать ±0,5°С для станков класса точности С, ±1°С для станков классов А и В и ±2°С для менее точных станков. Станок на точность проверяют после его обкатки. Объем испытаний определяется соответствующими нормами точности, предусмотренными ГОСТом. В качестве типовых обычно указывают проверки точности геометрических форм базирующих поверхностей (прямолинейность, плоскостность, овальность, конусность и т. п.), взаимного расположения этих поверхностей (параллельность, перпендикулярность, соосность), формы траектории движения исполнительных звеньев станка, взаимосвязанных движений (кинематической точности), координатных перемещений (линейных и угловых). Все проверки проводят без внешней нагрузки. В ГОСТах приведены схемы и способы измерения геометрической точности.
Другой не менее важной и обязательной является проверка статической жесткости станка. Жесткость – один из основных критериев работоспособности станка, определяющих его точность под нагрузкой в установившемся режиме работы.
Чтобы результаты проверки на жесткость были достаточно достоверны и объективны, необходимо при испытаниях по возможности приблизиться к наиболее типичным реальным случаям обработки, сохраняя для простоты испытаний статическое нагружение станка. Направление и координаты точки приложения нагружающей силы должны соответствовать направлению и точке приложения силы резания при типичном случае обработки. Нагружающая сила должна быть достаточной для того, чтобы вызвать перемещения, которые можно точно зафиксировать с помощью обычного индикатора с ценой деления 0,01 мм, но она не должна превышать допустимой для испытуемого станка нагрузки. Рекомендуется определенное типичное расположение перемещаемых узлов на станке.
|
Для проведения испытаний на жесткость используют специальные приборы. Основными частями каждого такого прибора являются нагрузочное устройство (домкрат и предварительно отградуированный динамометр с индикатором нагрузки) и индикаторы перемещений,
При проверке обычно измеряют суммарную податливость станка, характеризуемую относительным смещением его узлов, несущих инструмент и обрабатываемую заготовку, при заданной нагружающей силе. Нормируют наибольшее допустимое перемещение (т.е. нижнюю границу жесткости).
Знание только суммарной податливости не всегда достаточно. Поэтому при испытании опытного образца станка может быть составлен баланс упругих перемещений. Для этого при статическом нагружении измеряют, а затем пересчитывают к точке приложения, силы перемещения элементов упругой системы станка. Баланс упругих перемещений позволяет оценить долю отдельных элементов или узлов станка в суммарном относительном смещении его испытательных звеньев, отыскать слабые (по жесткости) элементы, оценить качество их изготовления и сборки.
В значительной степени жесткость станка может зависеть от регулировки подшипников шпинделя, поэтому предусмотрена проверка зазоров-натягов этих подшипников. Проверку проводят как в холодном, так и в разогретом до установившейся температуры состоянии подшипников. В процессе проверки, например радиального зазора-натяга переднего подшипника, измеряют перемещение шпинделя (относительно корпуса шпиндельной бабки) при нагружении его силой, действующей в направлении, перпендикулярном к оси шпинделя. Нагружение осуществляется ступенчато до состояния, при котором достигается линейная зависимость между силой и перемещением. Отрезок, отсекаемый на оси ординат касательной к линейной части графика D = f (F), может оказаться выше или ниже начала координат (рис. 20). В первом случае он характеризует радиальный зазор, во втором – натяг проверяемого подшипника. Аналогично проверяют величину осевого зазора-натяга подшипников.
Рис. 20. Определение зазоров и натягов подшипников
Проверкам, рассмотренным ранее, подвергают все станки, в том числе и серийные. Для опытных образцов станков на этом этапе дополнительно проверяют работоспособность электрооборудования (в основном, прочность и сопротивление изоляции силовых цепей), а для опытных образцов – соответствие органов ручного управления требованиям эргономики (ГОСТ 21752-76).
Вторую группу проверок (самую большую) составляют проверки станка на холостом ходу. Испытания на холостом ходу начинают с включения станка и проверок правильности функционирования основных его механизмов и систем. Проверяют электрооборудование (работу путевых выключателей, защитных блокировок, нулевой, тепловой и максимальной защиты, нагрев катушек аппаратов, резисторов и пр.), работу систем смазывания и охлаждения, системы управления скоростями движения рабочих органов станка, правильность функционирования главного привода и механизмов привода подачи.
Главный привод проверяют на всех частотах вращения, а также в режимах частых пусков, остановов и реверсирования. На максимальной частоте вращения шпинделя станок должен проработать до момента стабилизации температуры шпиндельных подшипников, обмоток электромагнитных муфт и электродвигателя, но не менее 30-ти мин. При этом температура поверхности шпиндельной бабки в области переднего и заднего подшипников шпинделя не должна превышать заранее установленных допустимых значений.
Теплообразование и связанные с ним температурные деформации являются одним из факторов, обусловливающих погрешности механической обработки – отклонения размеров и искажения геометрической формы обрабатываемых деталей. В наибольшей степени на точность обработки влияет изменение положения оси шпинделя относительно суппорта (или стола) вследствие температурных деформаций. Поэтому для опытных образцов станков наряду с проверкой нагрева подшипников шпинделя по ГОСТу предусмотрена проверка их температурной стабильности.
Одним из критериев качества изготовления и сборки станка является шум, возникающий при его работе. Для обеспечения нормальных условий работы людей в производственных помещениях шум каждого станка регламентирован. Цель проверки шумовых характеристик – установить, не превышает ли уровень шума станка допустимого значения. Допустимые значения устанавливаются в зависимости от чувствительности человеческого уха к шумам в различных частотных диапазонах (до 90 дБ – для частот менее 350 Гц, до 75 дБ – для частот выше 4 кГц). Для оценки шума используют шумомеры, реагирующие на звук подобно человеческому уху.
Шум измеряют обычно при наибольшей частоте вращения шпинделя. Три переключаемых корректирующих контура могут изменять частотную характеристику шумомера в зависимости от уровня шума, что позволяет более объективно оценить шум проверяемого станка. Для опытных образцов проводят частотный анализ шума с помощью включения полосовых фильтров, позволяющих определить уровень шума в узких полосах частот. Для точного анализа используют октавные (отношение средних частот соседних полос 1: 2) и третьоктавные (отношение 1: 1,26) фильтры. Результаты анализа представляют в виде спектра шума, показывающего уровни шума на разных частотах исследуемого диапазона.
Ярким показателем качества изготовления и сборки станка является уровень его колебаний на холостом ходу. Наибольший интерес представляют измерения относительных колебаний инструмента и заготовки, как непосредственно влияющих на точность обработки. При испытании опытных образцов станков относительные колебания измеряют во всем диапазоне частот вращения шпинделя. В конусное отверстие шпинделя устанавливают регулируемую оправку с биением измерительной шейки менее 3 мкм.
Датчиком (емкостным или индуктивным), установленным на суппорте станка, измеряют относительные колебания и подвергают их частотному анализу в диапазоне частот до 1 кГц. Частотный спектр колебаний холостого хода определяется в основном наиболее мощными возбудителями колебаний (неуравновешенные вращающиеся детали привода главного движения станка, погрешности зубчатых и ременных передач, муфт, подшипников качения и др.) и собственными колебаниями элементов упругой системы станка. Колебания холостого хода нормируют по частотным диапазонам: нормы на составляющие спектра, частоты которых лежат ближе к частоте потенциально неустойчивой формы колебаний станка (частота возможных в системе автоколебаний), должны быть более жесткими, чем для других частотных диапазонов.
Для серийных станков эту проверку проводят на частоте вращения шпинделя, соответствующей чистовой обработке.
В программу испытаний опытных образцов станка включены также энергетические испытания – проверка мощности, потребляемой главным приводом и приводом подач при работе станка на холостом ходу. Эти показатели характеризуют потери на трение в приводе, которые зависят от конструкции привода, а также правильности сборки и регулирования основных его элементов (натяжение ремня, предварительный натяг подшипников и др.), работы системы смазывания, продолжительности обкатки станка.
Проверка мощности Nc (хх), потребляемой главным приводом на холостом ходу, проводится после разогрева станка при условии, что значение мощности остается неизменным по крайней мере в течение 10-15 мин. Испытания проводят на минимальных, средних и максимальных частотах вращения шпинделя с помощью комплекта приборов для измерения мощности, подключаемых к входным клеммам электродвигателя. По результатам измерений мощности Nc (хх) строят графики Nc (хх) = f (n), на которые наносят кривые или семейства кривых, полученные при испытании.
Для станков с ЧПУ, по сравнению с обычными станками, предусмотрены дополнительные проверки.
Проверка точности позиционирования подвижных исполнительных узлов станка (столов, суппортов, салазок, стоек) является одной из основных проверок его точности.
Следующая проверка связана с контролем отработки системой привода подач станка единичных импульсов программы. Проверяемому узлу сообщают движение единичными импульсами сначала в прямом, а потом в обратном направлении. Число импульсов не менее 20. С помощью многооборотного стрелочного индикатора или какого-либо другого датчика перемещения фиксируют отклонения фактического перемещения узла от номинального значения импульса (дискреты). Наибольшая величина этого отклонения является оценкой точности отработки системой единичного импульса.
В число дополнительных проверок станков с ЧПУ на холостом ходу входит также проверка времени смены инструмента с помощью имеющегося на станке манипулятора.
Третью группу проверок составляют проверки станка при его работе. Прежде всего следует указать на проверки работоспособности станка при максимальных режимах резания: при работе с максимальной силой резания, при резании с наибольшей мощностью, при резании с наибольшим крутящим моментом. Контроль силы резания осуществляется по величине (Nc (рез) – Nc (хх)) при постоянной частоте вращения шпинделя. На режимах, обеспечивающих получение наибольшей мощности, одновременно контролируется падение частоты вращения шпинделя (не более 3 %).
Оценку результатов испытаний проводят по внешнему виду обработанной поверхности, которая не должна иметь следов вибраций. Наблюдая за мощностью Nс (рез),потребляемой электродвигателем главного привода станка (которая должна быть не менее установленной), проверяют работу всех механизмов и систем станка на безотказность.
Одним из важнейших критериев работоспособности станка является его виброустойчивость, которую можно понимать как способность станка сопротивляться возникновению автоколебаний при резании. Программой испытаний станков при работе предусмотрена оценка границ устойчивости процесса резания.
Испытание сводится к определению так называемой предельной стружки t пр.Под предельной стружкой понимают максимальную глубину резания, снимаемую при работе без вибраций.
Для опытных образцов станка определяют зависимость предельной стружки от частоты вращения шпинделя для всех характерных видов обработки и нескольких подач. Например, характерными видами обработки для токарных станков являются продольное точение вала в центрах, обработка вала, закрепленного консольно, и торцовая область кольца.
Определение предельной стружки является довольно трудной задачей, так как предельный режим работы станка по своей природе весьма неустойчив. Признаком предельной стружки обычно служит появление характерного звука при работе станка и довольно резкое увеличение амплитуды относительных колебаний инструмента и заготовки, на которой при этом появляются следы вибраций. Параллельно с определением предельной стружки желательно фиксировать частоту возникающих при этом на станке вибраций (так называемую частоту потенциально неустойчивой формы колебаний).
Полученные данные позволяют построить графики зависимости t npот частоты вращения для каждого вида обработки и не менее чем при трех подачах. Это так называемые графики границ устойчивости (рис. 21). Границы устойчивости оценивают путем сравнения с лучшими образцами аналогичных станков или по производственной характеристике станка (сопоставляя границу устойчивости с другими границами использования станка).
Рис. 21. График границ устойчивости токарного станка при обработке
Консольной заготовки
Испытание серийных станков проводят по сокращенной программе; их цель – проверка виброустойчивости как критерия качества изготовления и сборки каждого станка. Для испытаний выбирают вид обработки, дающий наименьшую виброустойчивость. Подачу рекомендуется брать среднюю, но вызывающую резкое увеличение амплитуды колебаний при увеличении глубины резания.
Частоту вращения шпинделя принимают равной п в зоне наименьшего значения t прпо графику границы устойчивости для выбранной ранее подачи. Глубину резания, соответствующую принятым п, S и виду обработки, при которой еще не наступает потеря станком устойчивости, нормируют. Норму устанавливают статистически по результатам испытаний 30-50 станков данной модели.
Проверка геометрической точности, которой подвергается станок в начале испытаний, дает лишь косвенную гарантию точности обработки на станке. Поэтому для оценки непосредственно точности обработки и шероховатости обработанной поверхности программой испытаний станка при его работе предусмотрена обработка контрольного образца (для станков с ЧПУ – партии образцов). Вид образца, его материал, характер и режим обработки, крепление инструмента и т.п. назначают с таким расчетом, чтобы свести к минимуму влияние факторов, не имеющих прямого отношения к качеству изготовления станка, и получить наивысшую точность обработки. Отклонения фактических размеров и формы образца, а также параметров микрогеометрии его поверхности, не должны превышать величин, указанных в соответствующем ГОСТе.
Организация ремонта
Постепенное изнашивание металлорежущих станков в процессе эксплуатации проявляется в снижении точности обработки, появлении повышенного шума, возникновении неполадок и отказов. Поддержать станки в работоспособном состоянии и восстановить утраченные в процессе эксплуатации технические показатели можно только при периодическом осмотре и ремонте.
Ремонт по потребности (т.е. ремонт при остановках, обусловленных поломкой какой-либо из деталей механизмов) – устаревшая форма обслуживания. Недостатки ее: внезапность выхода оборудования из строя, приводящая к нарушению нормального хода производства и наносящая большой ущерб производству; чрезмерный износ оборудования повышает стоимость ремонта и снижает его качество.
На всех промышленных предприятиях нашей страны действует система планово-предупредительного ремонта. Эта система разработана в нашей стране и получила признание за рубежом. Сущность системы планово-предупредительного ремонта оборудования заключается в том, что через определенное число отработанных часов каждого агрегата производят профилактические осмотры и различные виды плановых ремонтов этого агрегата. Основной задачей системы является удлинение межремонтного срока службы оборудования, снижение расходов на ремонт и повышение качества ремонта.
Существует три разновидности планово-предупредительного ремонта.
1. Метод послеосмотровых ремонтов – планируют не ремонты, а лишь периодические осмотры. Если при очередном осмотре выясняется, что станок не проработает нормально до следующего осмотра, то назначают ремонт к определенному сроку. Это дает возможность подготовиться к ремонту, выполнить его быстрее и качественнее. Недостаток метода – отсутствие планирования, что может привести к перегрузке работников ремонтной службы в одни периоды и незанятости в другие.
2. Метод периодических ремонтов – для каждого станка составляют план с указанием сроков и объема ремонтных работ. Допускается корректировка плана с учетом фактических результатов осмотров, что делает систему ремонтов гибкой, обеспечивая наиболее рентабельное использование технологического оборудования за срок его службы. Это наиболее распространенный вид планово-предупредительного ремонта.
3. Метод принудительных ремонтов – обязательный ремонт оборудования в установленные сроки. Ремонт производят по заранее разработанной технологии с обязательной заменой или восстановлением всех намеченных деталей и узлов. Метод целесообразен только на участках с однотипным оборудованием и стабильным режимом работы (поточные линии, энергетическое оборудование).
Периодические осмотры проводят слесари-ремонтники согласно плану ремонта. При этом проверяют работу всех механизмов, производят их регулировку, выявляют состояние и степень износа узлов. Станки, работающие в условиях сильного загрязнения, промывают при частичной разборке. Станки повышенной точности проверяют на точность. При осмотре выявляют все дефекты и неисправности оборудования, но устраняют только такие, наличие которых не позволяет нормально эксплуатировать оборудование до ближайшего планового ремонта. Остальные дефекты подлежат устранению при ближайшем плановом ремонте. Осмотры производят, как правило, в нерабочее время.
Периодический ремонт может быть текущим, средним и капитальным.
Текущий ремонт – это минимальный по объему вид планового ремонта, при котором заменой или восстановлением небольшого числа изношенных деталей, срок службы которых равен межремонтному периоду или меньше его, и регулированием механизмов обеспечивается нормальная эксплуатация станка до очередного планового ремонта. При текущем ремонте производят очистку гидросистемы и смену масла.
Средний ремонт – это плановый ремонт, включающий операции текущего ремонта и дополнительные мероприятия по восстановлению предусмотренных ГОСТами или техническими условиями точности, мощности и производительности оборудования на срок до очередного среднего или капитального ремонта. При среднем ремонте заменяют изношенные детали, срок службы которых равен или меньше межремонтного периода, или периода между двумя средними ремонтами. При этом обязательно проводят проверку на точность.
Капитальный ремонт – это наибольший по объему вид планового ремонта, при котором производят полную разборку станка, ремонт базовых деталей (станин, кареток и т.д.), замену и восстановление всех изношенных деталей и узлов в целях возвращения агрегату первоначальных точности, мощности и производительности. При капитальном ремонте, как правило, производят модернизацию оборудования. Из капитального и среднего ремонта оборудование принимает представитель ОТК.
В настоящее время в связи с повышением долговечности станков намечается переход к двухвидовой системе ремонта, включающей текущий и капитальный ремонты.
Кроме периодических плановых ремонтов может быть неплановый ремонт, который не предусмотрен графиком и вызван аварией оборудования. При хорошо организованной на предприятиях системе планово-предупредительного ремонта внеплановые ремонты, как правило, не должны иметь места.
Период между двумя капитальными ремонтами (или от ввода в эксплуатацию до первого капитального ремонта) называют ремонтным циклом, а период времени между двумя очередными плановыми ремонтами – ремонтным периодом. Структура ремонтного цикла, т.е. порядок расположения и чередования ремонтов и осмотров, может быть разной в зависимости от культуры производства и состояния оборудования.
Для металлорежущих станков легких и средних (массой до 10 т) рекомендуется следующая структура ремонтного цикла:
К–О–М–О–М–О–С–О–М–О–М–О–С–О–М–О–М–О–К,
где К – капитальный ремонт; С – средний ремонт; М – текущий ремонт; О – осмотр.
Автоматические линии нуждаются в более частых профилактических осмотрах, поэтому их число в структуре ремонтного цикла удваивается. Для крупных станков массой от 10 до 100 т рекомендуются еще более частые профилактические мероприятия, предупреждающие преждевременный выход оборудования из строя. Число осмотров равно 27.
Продолжительность ремонтного цикла определяется классом точности станка, условиями работы (запыленностью воздуха, твердостью обрабатываемого материала, наличием абразивного материала и пр.), характером производства и, наконец, сроком службы тех основных механизмов и деталей станка, замена или ремонт которых могут быть выполнены во время его полной разборки. Средняя продолжительность ремонтного цикла для легких и средних станков составляет, по данным ЭНИМСа, около 30000 рабочих часов. При этом ремонтный цикл для двухмесячной работы будет 90 месяцев, период между промежуточными ремонтами (ремонтный период) – 10 месяцев, между осмотрами – 5 месяцев.
Трудоемкость и степень сложности ремонта станков, которые зависят от конструктивных (компоновка, кинематическая схема, устройство механизмов, масса и пр.) и технологических (точностные параметры, ремонтопригодность) особенностей, оцениваются категорией сложности ремонта. Чем сложнее станок, тем выше категория сложности ремонта. За эталон принят токарно-винторезный станок 16K20 с высотой центров 200 мм и межцентровым расстоянием 1000 мм. Ему присвоена 11-я категория сложности.
|
|
Историки об Елизавете Петровне: Елизавета попала между двумя встречными культурными течениями, воспитывалась среди новых европейских веяний и преданий...
Наброски и зарисовки растений, плодов, цветов: Освоить конструктивное построение структуры дерева через зарисовки отдельных деревьев, группы деревьев...
Механическое удерживание земляных масс: Механическое удерживание земляных масс на склоне обеспечивают контрфорсными сооружениями различных конструкций...
Биохимия спиртового брожения: Основу технологии получения пива составляет спиртовое брожение, - при котором сахар превращается...
© cyberpedia.su 2017-2024 - Не является автором материалов. Исключительное право сохранено за автором текста.
Если вы не хотите, чтобы данный материал был у нас на сайте, перейдите по ссылке: Нарушение авторских прав. Мы поможем в написании вашей работы!