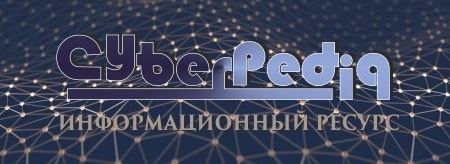
Эмиссия газов от очистных сооружений канализации: В последние годы внимание мирового сообщества сосредоточено на экологических проблемах...
Автоматическое растормаживание колес: Тормозные устройства колес предназначены для уменьшения длины пробега и улучшения маневрирования ВС при...
Топ:
Процедура выполнения команд. Рабочий цикл процессора: Функционирование процессора в основном состоит из повторяющихся рабочих циклов, каждый из которых соответствует...
Методика измерений сопротивления растеканию тока анодного заземления: Анодный заземлитель (анод) – проводник, погруженный в электролитическую среду (грунт, раствор электролита) и подключенный к положительному...
Комплексной системы оценки состояния охраны труда на производственном объекте (КСОТ-П): Цели и задачи Комплексной системы оценки состояния охраны труда и определению факторов рисков по охране труда...
Интересное:
Наиболее распространенные виды рака: Раковая опухоль — это самостоятельное новообразование, которое может возникнуть и от повышенного давления...
Принципы управления денежными потоками: одним из методов контроля за состоянием денежной наличности является...
Распространение рака на другие отдаленные от желудка органы: Характерных симптомов рака желудка не существует. Выраженные симптомы появляются, когда опухоль...
Дисциплины:
![]() |
![]() |
5.00
из
|
Заказать работу |
|
|
Тип опор | Радиальное и осевое биение шпинделя, мкм | Отклонение от круглости обработанного изделия, мкм | Скоростной параметр ![]() |
Качения | 1,00 | 1,0 | 0-10 |
Гидродинамические | 0,50 | 0,5 | 1-10 |
Гидростатические | 0,05 | 0,2 | 0-15 |
Аэростатические | 0,10 | 0,5 | 5-40 |
Учитывая эти параметры, а также то, что подшипники качения имеют меньшую стоимость при централизованном изготовлении и просты в эксплуатации, в настоящее время более 95% станков изготовляют со шпиндельными узлами на подшипниках качения.
В шпинделях станков для обеспечения высокой грузоподъемности, точности вращения, повышенной жесткости и минимальных выделений теплоты, как правило, применяют подшипники качения специальных конструкций. Для восприятия радиальных нагрузок широко используют двухрядные подшипники 3182100 с цилиндрическими роликами. Два ряда точных роликов, расположенных в шахматном порядке, обеспечивают грузоподъемность и жесткость подшипника при высокой точности вращения.
Для шпинделей также практически применяют все основные типы подшипников качения: шариковые радиальные и радиально-упорные, роликовые с коническими и цилиндрическими роликами и др. В качестве характеристики работоспособности шпиндельных опор качения можно принять следующие показатели:
;
;
;
,
где N – мощность привода; n max – наибольшая частота вращения шпинделя; D – максимальный диаметр обрабатываемой детали; d к – диаметр шпинделя в передней опоре.
Здесь показатели К 1 и К 3 характеризуют среднюю нагруженность шпиндельных узлов станка, а К 2 и К 4 – их быстроходность. Развитие конструкций шпиндельных узлов характеризуется возрастанием указанных показателей. Это связано с применением специальных типов подшипников качения, основные из которых показаны на рис. 1. Шарикоподшипник упорно-радиальный двухрядный с углом контакта 60° (рис. 1, а) предназначен для восприятия осевой нагрузки.
|
а) | б) | в) | г) | д) |
Рис. 1. Подшипники качения шпиндельных узлов
Его устанавливают рядом с двухрядным роликоподшипником с короткими цилиндрическими роликами. Параметр быстроходности мм · мин-1, что в 2-2,5 раза больше, чем у обычных упорных шарикоподшипников. Роликоподшипники конические однорядные и двухрядные с буртом на наружном кольце (рис. 1, б, д) предназначены для восприятия радиальной и осевой нагрузок. Их устанавливают, как правило, в передней опоре шпинделя;
мм · мин-1. Роликоподшипник конический однорядный с широким наружным кольцом (рис. 1, в) устанавливают в заднюю опору шпинделя. Параметр быстроходности имеет то же значение, что у подшипников, показанных на рис. 1, б, д.
Особо быстроходный радиально-упорный шарикоподшипник в универсальном исполнении (рис. 1, г) предназначен для восприятия радиальной и осевой нагрузок. Подшипники собирают в комплекты (два, три или четыре подшипника). Для обеспечения высокой точности вращения шпиндели устанавливают в подшипниках повышенных классов точности; высокий (5 кл.), прецизионный (4 кл.), сверхпрецизионный (2 кл.)
Методы смазывания во многом определяют надежность работы шпиндельного узла. Для подшипников качения применяют жидкий либо твердый смазочный материал. Примерные границы применимости различных методов смазывания по параметру (dn)max указаны далее.
Смазывание | ![]() |
Погружением | 5,5-8* |
Разбрызгиванием | 2,2-3,2 |
Циркуляционное | 4,2-6 |
Капельное | 2,8-4 |
Масляным туманом | 5,5-8 |
Под давлением | 7,5-10 |
* – меньшие значения для тяжелых серий подшипников, большие – для особо легких |
Смазывание погружением для шпиндельных узлов практически не применяют. При смазывании разбрызгиванием от шестерен привода масло подается в подшипники либо непосредственно, либо через специальный сборник. Следует учитывать, что в этом случае масло поступает к подшипникам, загрязненным продуктами изнашивания шестерен коробки, кроме того, для нормальной работы системы смазывания частота вращения шпинделя не должна быть низкой.
|
Циркуляционное смазывание обеспечивает необходимый по условиям теплоотвода расход масла через подшипник и охлаждает его. В большинстве случаев система циркуляционного смазывания общая для шпинделя и всей коробки скоростей.
При капельном методе подшипники смазываются независимо от других элементов, в них подается ограниченное количество масла (от 1 до 100 г в 1 ч), что снижает тепловыделение. В этом случае необходимо предотвращать попадание в подшипники смазки из коробки скоростей.
Смазывание методом масляного тумана применяют в высокоскоростных узлах; при этом кроме постоянного и равномерного смазывания осуществляется интенсивное охлаждение подшипника сжатым воздухом, служащим для образования масляного тумана. Избыточное давление воздуха в подшипнике препятствует попаданию в него внешних загрязнений.
Проточное смазывание при строгом дозировании применяют при работе шпиндельного узла в особо напряженных условиях (при высоких частотах вращения). В этом случае масло под давлением с помощью специальных дозаторов периодически впрыскивают через сопла непосредственно в зазор между сепаратором и кольцом подшипника.
Твердые смазочные материалы применяют в шпиндельных узлах при относительно низких частотах вращения, особенно они удобны для шпиндельных узлов, работающих в вертикальном или наклонном положении. Следует учитывать, что избыток смазочного материала, закладываемого в подшипник, ведет к повышению температуры в опоре и вытеканию смазочного материала, а недостаточное его количество – к быстрому выходу подшипников из строя.
Уплотнения шпиндельных узлов служат для защиты подшипников шпинделя от проникновения в них грязи, пыли и охлаждаемой жидкости, а также препятствуют вытеканию смазочного материала из подшипника. В шпиндельных узлах чаще всего применяют различные бесконтактные лабиринтные уплотнения для уменьшения тепловыделений в узле и исключения изнашивания уплотнений. Для надежной работы необходимо, чтобы радиальные зазоры в них были не более 0,2-0,3 мм. В шпиндельных узлах, работающих в тяжелых (по загрязнению) условиях, лабиринт заполняют твердым смазочным материалом, а при жидком смазочном материале иногда применяют продувку воздуха через уплотнение. В уплотнениях размещают полости и каналы для отвода смазочного материала от подшипников. Основные типы уплотнений приведены на рис. 2.
|
а) | б) | в) | г) |
Рис. 2. Основные типы уплотнений шпиндельных узлов:
а – контактное манжетное резиновое армированное уплотнение с пружиной; б – контактное манжетное кожаное уплотнение с пружиной; в – бесконтактное лабиринтное уплотнение;
г – лабиринтное дисковое уплотнение; D, d, b – основные конструктивные размеры;
h = 0,4÷0,6 мм – лабиринтный зазор; 1 – вращающийся стакан; 2 – кольца; 3 – диски;
4 – невращающийся стакан; 5 – резиновое кольцо; 6 – фиксирующий винт
В качестве материалов шпинделей станков нормальной точности применяют конструкционные стали 45, 50, 40Х с поверхностной закалкой (обычно закалка с нагревом ТВЧ) до твердости HRCэ 48-56. Шпиндели сложной формы изготавливают из сталей 50Х, 40ХГР и применяют объемную закалку до HRCэ 56-60. Для прецизионных станков в условиях жидкостной смазки применяют низкоуглеродные стали 20Х, 18ХГГ, 12ХНЗА с цементацией и закалкой до твердости HRCэ 56-60. Для слабонагруженных шпинделей высокоточных станков для уменьшения внутренних деформаций применяют азотируемые стали 38Х2МЮА, 38ХВФЮА с закалкой до твердости HRCэ 63-68.
Для изготовления полых шпинделей большого диаметра иногда применяют серый чугун СЧ 20.
На рис. 3 представлены рекомендуемые компоновочные схемы шпиндельных узлов, расположенных по мере возрастания параметра d n.
Уменьшение быстроходности и виброустойчивости | I. Низкоскоростные | ||
1 | ![]() | d n < 100000¸140000 мм × мин-1 | |
2 | ![]() | d n < 150000¸180000 мм × мин-1 | |
3 | ![]() | d n < 160000¸250000 мм × мин-1 | |
II. Среднескоростные | |||
4 | ![]() | d n < 250000¸350000 мм × мин-1 | |
5 | ![]() | d n < 300000¸450000 мм × мин-1 | |
6 | ![]() | d n < 400000¸500000 мм × мин-1 | |
III. Высокоскоростные | |||
7 | ![]() | d n < 500000¸600000 мм × мин-1 | |
8 | ![]() | d n < 600000¸800000 мм × мин-1 | |
9 | ![]() | d n < 700000¸1000000 мм × мин-1 | |
10 | ![]() | d n < 1000000¸1500000 мм × мин-1 |
Рис. 3. Компоновочные схемы шпиндельных узлов
|
Все компоновочные схемы разбиты на три группы. Низкоскоростные обладают наибольшей радиальной и осевой жесткостью. Их рекомендуется применять в тяжело нагруженных фрезерных, токарных, сверлильных станках. Схема 1 выполнена на игольчатых подшипниках, имеет наибольшую радиальную и осевую жесткости, но при этом она самая низкоскоростная.
Для шпиндельных узлов, выполненных на радиально-упорных шарикоподшипниках из керамических материалов и системой принудительного охлаждения корпуса и шпинделя, параметр d n повышается до 30%-40%.
Более точное значение параметра d n зависит от выбранного типа системы смазки, класса точности подшипников, радиального зазора-натяга роликоподшипников, предварительного натяга шарикоподшипников, количества подшипников в опоре, серии подшипников и их предельной частоты вращения, указанной в справочнике.
На рис. 4 показана конструкция шпиндельного узла, соответствующая компоновке 2 (см. рис. 3).
Рис. 4. Конструкция низкоскоростного шпиндельного узла
Конструкция шпиндельного узла, выполненная по компоновке 3, представлена на рис. 5.
Рис. 5. Конструкция шпиндельного узла на роликовом подшипнике
|
|
Индивидуальные очистные сооружения: К классу индивидуальных очистных сооружений относят сооружения, пропускная способность которых...
Эмиссия газов от очистных сооружений канализации: В последние годы внимание мирового сообщества сосредоточено на экологических проблемах...
Состав сооружений: решетки и песколовки: Решетки – это первое устройство в схеме очистных сооружений. Они представляют...
История развития хранилищ для нефти: Первые склады нефти появились в XVII веке. Они представляли собой землянные ямы-амбара глубиной 4…5 м...
© cyberpedia.su 2017-2024 - Не является автором материалов. Исключительное право сохранено за автором текста.
Если вы не хотите, чтобы данный материал был у нас на сайте, перейдите по ссылке: Нарушение авторских прав. Мы поможем в написании вашей работы!