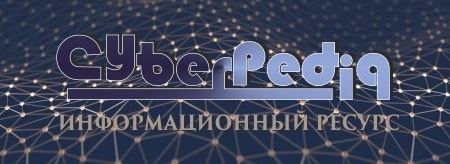
Двойное оплодотворение у цветковых растений: Оплодотворение - это процесс слияния мужской и женской половых клеток с образованием зиготы...
Поперечные профили набережных и береговой полосы: На городских территориях берегоукрепление проектируют с учетом технических и экономических требований, но особое значение придают эстетическим...
Топ:
Характеристика АТП и сварочно-жестяницкого участка: Транспорт в настоящее время является одной из важнейших отраслей народного...
Эволюция кровеносной системы позвоночных животных: Биологическая эволюция – необратимый процесс исторического развития живой природы...
Особенности труда и отдыха в условиях низких температур: К работам при низких температурах на открытом воздухе и в не отапливаемых помещениях допускаются лица не моложе 18 лет, прошедшие...
Интересное:
Уполаживание и террасирование склонов: Если глубина оврага более 5 м необходимо устройство берм. Варианты использования оврагов для градостроительных целей...
Принципы управления денежными потоками: одним из методов контроля за состоянием денежной наличности является...
Распространение рака на другие отдаленные от желудка органы: Характерных симптомов рака желудка не существует. Выраженные симптомы появляются, когда опухоль...
Дисциплины:
![]() |
![]() |
5.00
из
|
Заказать работу |
|
|
Эмаль представляет собой стеклообразное (или преимущественно стеклообразное) вещество, в основном состоящее из оксидов, полученное плавлением или фриттованием (неполным плавлением), которое одним или несколькими слоями наносят на металлическое изделие. В технологии эмали существует та же проблема, что и при изготовлении металлостеклянных спаев — согласование физико-механических характеристик металлической и оксидной систем для обеспечения их прочного сцепления и допустимого уровня напряжений в обеих составляющих. В связи с этим разные металлы эмалируют разными эмалями. Известно и общее требование: обычно формирование бездефектного покрытия и процессы, обеспечивающие сцепление, следует вести при вязкости эмали около 100 Па-с и поверхностном натяжении около 300 мДж/м2.
Химический состав эмали определяется назначением эмалевого покрытия и характеристиками защищаемого металла. Области применения эмалевых покрытий столь разнообразны, что выделение каких-либо общих физико-химических их характеристик, как и у стекол, невозможно. В отличие от стекла, структурные превращения в эмали оказывают значительно большее влияние на совокупность эксплуатационных свойств покрытия. Эти преобразования имеют существенное значение и для достижения прочного сцепления эмали в твердом состоянии с металлом.
Процессы, обусловливающие сцепление эмали с металлом, более подробно исследованы для черных металлов. В этом случае применяют эмали на основе щелочноборосиликатных стекол с введением в качестве способствующих адгезии и сцеплению оксидов переходных металлов—кобальта, никеля, марганца, меди и т. д. (так называемых оксидов сцепления). Эти исследования привели к возникновению ряда ги-' потез (электрохимическая, механическая и др.), имеющих описательный характер и взаимно дополняющих друг друга. Начальными стадиями процесса, обеспечивающего сцепление твердой эмали с металлом, являются смачивание и химическое взаимодействие металла с эмалью или стекловидной составляющей неорганического эмалевого покрытия. А. А. Аппен показал целесообразность анализа при исследовании этого процесса следующих основных критериев: изобарных потенциалов реакций, протекающих в моноатомном пограничном слое и определяющих состав и строение новообразований на поверхности раздела соприкасающихся фаз; средних энергий единичных связей металл — кислород (или другой анион), либо средних значений энергий атомизации соединений на поверхности раздела эмаль — металл; нормальных электродных потенциалов на этой границе; степени недостроенности электронных оболочек атомов на границе раздела соприкасающихся фаз и статистического веса атомов со стабильными электронными конфигурациями; разрядного потенциала и плотности заряда на границе металл — неорганический диэлектрик (стекло).
|
Во многих случаях сцепление определяется не столько этими критериями, сколько составом и свойствами переходного слоя толщиной в десятки микрометров, образующегося в результате взаимодействия эмали с металлом. Однако во всех случаях особо велика роль площади действительного контакта металла с эмалевым покрытием, которая зависит не только от состава эмали, но и от всей технологии формирова. ния покрытия.
Первоначально целью эмалирования было создание декоративного эффекта, в основном, на изделиях из драгоценных металлов. Высокого художественного уровня декоративное эмалирование достигло в начале нашей эры в Византии, что оказало существенное влияние на развитие этой техники в других странах, в том числе и в Киевской Руси. При изготовлении украшений с использованием техники «перегородчатых» и «выемчатых» эмалей ювелир должен был решать задачу прочного соединения эмалей с металлами и обеспечить многообразие цветов и оттенков покрытия. Для изготовления эмалированных ювелирных изделий и в настоящее время применяют низкопробные сплавы драгоценных металлов, при их эмалировании можно использовать многообразные возможности окрашивания стекла.
|
Наряду с традиционным применением в качестве декоративных покрытий на изделиях бытового и технического назначения, эмалевые покрытия все в возрастающей степени призваны решать задачу антикоррозийной защиты металлов в самых разнообразных областях. Известно, что в результате коррозии ежегодно теряется около 10 % мирового выпуска черных металлов.
Развитие науки и техники связано с использованием все более высоких температур. По этой причине непрерывно возрастают требования к защите разнообразных металлов и, в первую очередь, жаропрочных сталей и сплавов от газовой коррозии, в особенности от окисления. Эту задачу призваны решать жаропрочные эмали и покрытия. Современная техника нуждается, например, в аппаратуре, работоспособной в парах серы до 1000°С, иода и иодидов—до 1100°С, в хлоре и хлористом водороде—при 400—600°С, в парах пентоксида ванадия, содержащихся в продуктах сгорания и переработки нефти,—при 500—700°С. При таких высоких температурах многие стекла ведут себя не как твердое тело, а как высоковязкая жидкость, и не могут обеспечить длительной эксплуатации изделия. В указанных условиях работоспособными могут быть лишь кристаллические соединения. Таким образом, для решения подобных задач технология эмалирования должна использовать метод направленной кристаллизации эмалей или основываться на введении в покрытие при его формировании значительных количеств кристаллических огнеупорных наполнителей.
В то же время усиливающийся интерес вызывает и технология эмалирования легких сплавов, особенностью которой является применение возможно более легкоплавких эмалей. Например, алюминий чистотой 99,5 % имеет температуру плавления 658°С, а температура плавления эвтектик в литейных алюминиевых сплавах лежит около 450°С. Таким образом, температура формирования эмалевого покрытия на этих сплавах должна существенно различаться, чтобы избежать деформации изделий. Особые трудности возникают при необходимости обеспечения электрической изоляции или антикоррозионной защиты полупроводниковых металлов — кремния, германия и т. п., так как для сохранения их характеристик температура их нагрева не может превышать 300-350 °С.
|
При выборе металла и соответствующей эмали наряду с температурой плавления металла и температурой, обеспечивающей достаточно низкую вязкость эмали при формировании покрытия, следует учитывать и температуры, до которых работоспособны металлическая основа и эмаль. Ползучесть и рекристаллизация металла и релаксационные процессы в эмали могут приводить к изменению напряженного состояния системы, способного вызвать разрушения связи металл — эмалевое покрытие. Другими важными факторами разрушения могут быть при более низких температурах тот или иной вид коррозии, при достаточно высоких температурах—диффузионные процессы на границе раздела металл — эмаль. Действие этих факторов проявляется во время эксплуатации покрытия; неблагоприятные напряжения могут вызвать разрушение покрытия уже в процессе его нанесения.
Величинами, определяющими напряженное состояние системы эмаль — металл при заданной температуре, являются разница термических коэффициентов линейного расширения, соотношение модулей упругости и сдвига и толщины слоев металла и эмали. Значения указанных свойств материалов существенно изменяются с температурой. В случае стекла (эмали) эти изменения особенно значительны вблизи температуры стеклования, где ТКЛР, например, может возрастать в 2-Зраза.
Многие сплавы, особенно чугун, меняют свою структуру при нагревании до температуры формирования покрытия. Эти преобразования находят свое выражение в изменении не только ТКЛР, но и объема металла, что создает дополнительные трудности при эмалировании. Жаростойкие металлы, например, Та, Мо, Mb, W и V, и некоторые их соединения относительно легко окисляются на воздухе. Оксиды этих металлов, образующиеся на поверхности, летучи и непрочно связаны с металлом; рост пленки оксидов при обжиге покрытия и недостаточная скорость ее растворения в эмали часто являются причиной потери адгезии и отслаивания покрытия. Вместе с тем экспериментально установлено, что достаточно хорошее сцепление эмалевого покрытия с большей частью металлов достигается при обжиге в кислородсодержащей среде. В этом случае на поверхности образуется пленка из оксидов (например, железа), взаимодействующих с эмалью и растворяющихся в ней с образованием переходного слоя. При эмалировании черных металлов процесс сцепления стимулируют добавками в эмаль или на поверхность эмалируемого изделия указанных выше оксидов сцепления — Ni2O5 и т. д. При обжиге в инертной атмосфере сцепление эмали с некоторыми металлами обеспечивается образованием переходного слоя, содержащего новые соединения, например, интер-металлиды.
|
За исключением эмалей на чистых драгоценных металлах, эмалевое покрытие представляет собой в основном трехслойную композицию металла, переходного слоя и слоя эмали. Напряженное состояние такой системы в области упругого состояния может быть достаточно точно рассчитано, причем, как правило, напряжения в металле невелики и не оказывают определяющего влияния на прочность композиции в целом.
Напряженное состояние эмалевого покрытия зависит от геометрии поверхности и эти зависимости также могут быть рассчитаны. Композиции могут разрушаться как вследствие рассмотренных нормальных напряжений, так и связанных с ними тангенциальных напряжений, особенно на выпуклых поверхностях.
При эксплуатации изделия в меняющихся температурных полях напряжения, возникающие вследствие различия свойств материалов, будут суммироваться с термоупругими напряжениями, возникающими из-за различий средних температур металла, переходного слоя и эмалевого покрытия. Коэффициенты тепло- и температуропроводности эмалей, как и всех стекол, существенно ниже, чем металлов. Поэтому во время охлаждения на поверхности эмалевого покрытия возникают опасные растягивающие напряжения. По этой причине характеристики эмалевого покрытия подбирают таким образом, чтобы при эксплуатации оно находилось под действием допустимых сжимающих нагрузок. Например, при эмалировании стали и чугуна переходный слой формируют при помощи так называемых грунтовых эмалей, а требуемых эксплуатационных характеристик покрытия достигают, применяя соответствующие покровные эмали.
При эмалировании наряду с достижением заданного напряженного состояния и адгезии необходимо получать бездефектные покрытия. Важное значение при этом имеют физико-химические процессы смачивания и растекания. Существенная роль принадлежит состоянию поверхности металла и составу газовой среды, в которой формируется эмалевое покрытие. О характере новообразований на поверхности раздела металл — эмалевое покрытие, возникающих вследствие их химического взаимодействия при заданных температурах, можно судить на основе расчета изобарно-изотермических потенциалов вероятных химических реакций. В результате этих реакций образуются поверхностные
|
Рис. 33.1. Изменение напряжений в стекловидном эмалевом покрытии при изотермической выдержке (а) и при направленной кристаллизации (б)
———— исходное покрытие; — — — покрытие после термической обработки
фазы, заметно влияющие на процессы смачивания, растекания и сцепления, причем важную роль играет состав среды. Собственно процесс получения бездефектного покрытия определяется убылью свободной поверхностной энергии в системе в целом, т. е. в конечном счете, поверхностным натяжением на границах раздела металла, эмали и газовой среды при обжиге. Анализ этих явлений в практической технологии затруднен тем, что покрытие формируется в меняющемся температурном поле, и система не находится в состоянии равновесия. Несомненно, одно, что задачи, поставленные перед технологией эмалирования, требуют как учета состава и структур используемых материалов, так и целенаправленного осуществления технологического процесса.
Составы и свойства эмалей
В процессе формирования эмалевого покрытия эмалевая фритта, первоначально резко закаленная от температуры варки грануляцией в воду или прокаткой между водоохлаждаемыми валиками, претерпевает многократный нагрев от твердого до вязкого состояния при температуре обжига и последующее охлаждение. Так, при эмалировании крупногабаритной химической аппаратуры цикл нанесения и обжига каждого слоя длится часами. В подавляющем большинстве случаев эмаль на поверхность изделия наносят шликерным способом. Шликер — суспензия, включающая эмаль, иногда — кристаллические наполнители, глинистые минералы, электролиты, вводимые для обеспечения седиментационной устойчивости, и воду. Приготовляют шликер мокрым помолом эмали в шаровых мельницах, в процессе которого эмаль взаимодействует с компонентами шликера.
Таким образом, процесс эмалирования следует рассматривать как вторичную термическую обработку эмали в нестационарных температурных полях, осложненную разнообразными химическими взаимодействиями при изготовлении и хранении шликера. Несколько проще обстоит дело при нанесении эмали на горячее металлическое изделие
пудровым способом, при котором эмаль подвергают сухому помолу, но этот метод применяют лишь для чугунных изделий.
В промышленности эмали варят в периодических вращающихся печах при 1250—1350°С, не позволяющих для многих типов эмали достаточно полно провести гомогенизацию и осветление расплава. Практически эмаль не достигает равновесной структуры и подвержена структурным преобразованиям в процессе нанесения. Вместе с тем следует отметить, что для достижения максимальной химической устойчивости обязательным условием является обеспечение однородности микро- и макроструктуры эмалевого покрытия. Это достигается как подбором состава эмали, так и соответствующей технологией нанесения.
Однако неоднородность эмалевого покрытия не всегда является его недостатком. Многие изделия, полученные литьем чугуна или алюминиевых сплавов, являются чрезвычайно газонасыщенными. В таких случаях для получения бездефектных покрытий используют неоднородный и пористый грунтовый слой, который затем перекрывают соответствующими покровными эмалями. Именно по этой причине для чугунных изделий используют, как и прежде, фриттование, то есть не полностью проплавленные эмали, в простейшем случае — на основе смеси из кварцевого стекла, полевых шпатов, буры, плавикового шпата и соды. Для этой же цели иногда применяют «сырые» эмали, которые, как и некоторые глазури, представляют собой суспензию сырьевых компонентов.
Создавая тем или иным путем неоднородность структуры эмалевого покрытия, стремятся обеспечить достаточно высокий уровень термических и механических характеристик. Микронеоднородная структура эмалевого покрытия в этом случае создается либо методом направленной кристаллизации стекла (ситаллизацией), либо введением в покрытие 10—15 % дисперсных кристаллических наполнителей.
Наиболее прост технологический процесс эмалирования золота, серебра, меди и их сплавов. Основной функцией эмали является создание декоративного эффекта вследствие окраски и интенсивного блеска покрытия. Эмалирование производят при 600—650°С с использованием легкоплавких окрашенных прозрачных щелочно-свинцовосиликатных эмалей или заглушенных (непрозрачных) эмалей с добавлением необходимого количества керамических пигментов. Например, используют исходную фритту состава, мол.,%: 40 КдО, 15 РЬО, 30 SiО2 и 15 SnО2.
Хотя чугун стали эмалировать раньше, чем многие другие металлы, до настоящего времени эмалирование чугуна наиболее сложно из-за его газонасыщенности и непостоянства структуры и свойств металла, которые подвержены в том числе и сезонным колебаниям. Первый слой в этом случае формируют с использованием плавленых и фриттованных грунтовых эмалей. Сцепление обеспечивается в основном взаимным прониканием эмали и пористого металла в переходном слое, применять оксиды сцепления во многих случаях не требуется.
В том случае, когда в составе эмали содержание фтора указывается в частях по массе сверх 100 %, соответствующее его количество вводят криолитом NasAlFg или кремнефтористым натрием NaaSiFe. В расчете шихты при этом должно быть учтено соответствующее этим соединениям количество оксидов натрия, алюминия и кремния.
Грунты для чугуна изготовляют фриттованием. Фриттование следует проводить при невысоких температурах во избежание образования кристобалита, которое ведет к скалыванию эмали с поверхности изделий. Обычный мельничный состав при изготовлении шликера содержит, ч. по массе: 100 эмали, 10 глины, 10 кварца, 1 буры, 50—60 воды.
Чтобы увеличить интервал температур, в котором формируется доброкачественное покрытие, обычно используют шликер следующего состава, ч. по массе: 70 фритта эмали 2015, 30 фритта эмали 3132, 10—30 кварцевого песка, 5—6 глины, 1—2 буры и 50—55 воды. Такие грунты применяют при эмалировании стальной посуды.
|
|
Автоматическое растормаживание колес: Тормозные устройства колес предназначены для уменьшения длины пробега и улучшения маневрирования ВС при...
Археология об основании Рима: Новые раскопки проясняют и такой острый дискуссионный вопрос, как дата самого возникновения Рима...
Историки об Елизавете Петровне: Елизавета попала между двумя встречными культурными течениями, воспитывалась среди новых европейских веяний и преданий...
Состав сооружений: решетки и песколовки: Решетки – это первое устройство в схеме очистных сооружений. Они представляют...
© cyberpedia.su 2017-2024 - Не является автором материалов. Исключительное право сохранено за автором текста.
Если вы не хотите, чтобы данный материал был у нас на сайте, перейдите по ссылке: Нарушение авторских прав. Мы поможем в написании вашей работы!