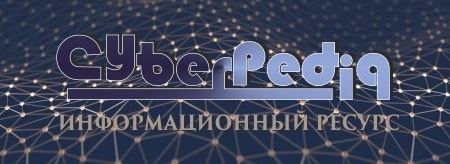
Индивидуальные очистные сооружения: К классу индивидуальных очистных сооружений относят сооружения, пропускная способность которых...
История развития пистолетов-пулеметов: Предпосылкой для возникновения пистолетов-пулеметов послужила давняя тенденция тяготения винтовок...
Топ:
Генеалогическое древо Султанов Османской империи: Османские правители, вначале, будучи еще бейлербеями Анатолии, женились на дочерях византийских императоров...
Оценка эффективности инструментов коммуникационной политики: Внешние коммуникации - обмен информацией между организацией и её внешней средой...
Комплексной системы оценки состояния охраны труда на производственном объекте (КСОТ-П): Цели и задачи Комплексной системы оценки состояния охраны труда и определению факторов рисков по охране труда...
Интересное:
Уполаживание и террасирование склонов: Если глубина оврага более 5 м необходимо устройство берм. Варианты использования оврагов для градостроительных целей...
Искусственное повышение поверхности территории: Варианты искусственного повышения поверхности территории необходимо выбирать на основе анализа следующих характеристик защищаемой территории...
Отражение на счетах бухгалтерского учета процесса приобретения: Процесс заготовления представляет систему экономических событий, включающих приобретение организацией у поставщиков сырья...
Дисциплины:
![]() |
![]() |
5.00
из
|
Заказать работу |
Под режимом резания подразумеваются принятые глубина резания, подача и скорость резания, с которыми производится обработка детали.
Глубина резания при обтачивании выбирается в зависимости от припуска на обработку и вида обработки - черновой или чистовой. Припуск на обработку обычно снимают за два хода, из которых первый ход является черновым, а второй - чистовым; в машиностроении при черновой обработке глубину резания принимают в большинстве случаев от 2 до 5 мм, а при чистовой - 0,5...1 мм.
Подача также зависит от вида обработки: при черновом обтачивании подачу принимают от 0,3 до 1,5 мм/об, а при чистовом - от 0,1 до 0,3 мм/об.
Скорость резания выбирают по специально разработанным таблицам в зависимости от качества обрабатываемого материала, материала резца, глубины резания, подачи, охлаждения и др.
Выбор оптимальных режимов резания
От выбора оптимального режима резания при точении, т.е. оптимального сочетания глубины резания, подачи и скорости резания, зависят производительность процесса резания и затраты на него.
Выбор глубины резания. Припуск на обработку можно снять за один или несколько рабочих ходов, однако целесообразнее работать с возможно меньшим количеством ходов. Следует стремиться весь припуск снимать за один проход, если это возможно. В противном случае необходимо разделить имеющийся припуск на два или, в крайнем случае, три хода (большее количество ходов применяется очень редко).
Если обработанная поверхность должна быть точной и чистой, следует весь припуск распределить на один-два черновых хода, оставляя на чистовую обработку глубину резания не больше 0,5...1 мм.
Выбор подачи. Для сокращения основного (машинного) времени необходимо работать с возможно большей подачей.
При черновой обработке величина подачи ограничивается жесткостью детали, прочностью резца и наиболее слабых звеньев механизма подачи станка. Для выбора подачи служат специальные таблицы, разработанные на основании опытных данных.
При получистовом и чистовом точении величина подачи определяется в зависимости от заданной шероховатости поверхности, радиуса при вершине резца, выбранной скорости резания.
Выбор скорости резания. Скорость резания, допускаемая режущим инструментом, зависит от механических свойств обрабатываемого материала, свойств материала резца, углов заточки резца, его стойкости, глубины резания и подачи, охлаждения и т. п.
Для выбора скорости резания целесообразно пользоваться специальными таблицами, составленными на основании лабораторных исследований и данных практики.
Последовательность выбора режимов резания.
Режимы резания выбирают в следующей последовательности:
1. Задаются глубиной резания в зависимости от припуска на обработку.
2. Выбирают подачу в зависимости от жесткости детали, станка и резца, требуемой точности и шероховатости обработанной поверхности и уточняют ее по паспорту станка.
3. Задаются желательной стойкостью резца. Средняя стойкость резца обычно принимается равной 60 мин.
4. Выбирают скорость резания в зависимости от глубины резания, подачи и стойкости инструмента по таблицам.
5. Уточняют выбранную табличную скорость резания для того, чтобы привести ее в соответствие с условиями работы: измененной стойкостью инструмента, охлаждением, работой по корке или окалине, маркой обрабатываемого материала и материала резца, отличающимися от принятых.
6. По выбранной скорости резания и диаметру обрабатываемой детали определяют число оборотов шпинделя.
7. Полученное число оборотов уточняют по паспорту станка. Если в паспорте нет требуемого числа оборотов, выбирают наиболее близкое и делают перерасчет скорости резания.
8. По выбранным значениям глубины резания и подачи определяют приблизительно силу резания для данного материала.
9. Определяют момент сопротивления резанию.
10. Из паспорта станка выбирают крутящий момент на шпинделе для принятого числа оборотов и сравнивают его с моментом сопротивления резанию.
Если мощность станка мала, уменьшают скорость резания, а если этого недостаточно, то уменьшают сечение среза.
Технология обработки деталей на токарных станках
Токарная обработка втулок
К классу втулок относятся детали со сквозным отверстием ис наружной гладкой или ступенчатой поверхностью. Втулки широко используются в машинах, Основным техническим требованием большинства втулок является концентричность наружных и внутренних поверхностей и перпендикулярность одной или обеих торцовых поверхностей втулки ее оси.
По форме втулки можно разделить на следующие четыре группы:
1) гладкие;
2) с гладким отверстием и ступенчатой наружной поверхностью;
3) с гладкой наружной поверхностью и ступенчатым отверстием;
4) со ступенчатыми отверстием и наружной поверхностью.
Втулки изготовляют из пруткового материала и заготовок, отлитых из чугуна и цветных металлов и реже кованых и штампованных.
За последнее время стали применять втулки из пластмасс.
а) Обработка гладких втулок из проката.
Рассмотрим наиболее характерные примеры обработки гладких втулок. Такие втулки диаметром до 45...50 мм обычно изготовляются из проката. Последовательность обработки гладкой втулки (Рис.1.39 а) из проката:
- При первой установке отрезать от проката ∅ 45 мм заготовку длиной 80 мм и закрепить патроне с вылетом на ~ 60 мм.
- Операции выполняемые во второй установке:
1. Подрезать торцевую поверхность заготовки (Рис.1.39 б).
2. Обточить цилиндрическую поверхность на ∅ 40 мм (Рис.1.39 в) на длину 55 мм.
3. Сверлить ∅ 22 мм на длине 58 мм (Рис.1.39 г).
4. Расточить отверстие на ∅ 24 мм на длине 56 мм (Рис.1.39 д).
5. Отрезать деталь на длину 51 мм (Рис.1.39 е).
- При третьей установке подрезается другой торец (Рис.1.39 ж)и выдерживается длина 50 мм.
При растачивании отверстия расточным резцом достигают строгой концентричности наружной поверхности втулки к ее отверстию при обработке их с одной установки.
При партии втулок 10, 20 шт. и более, т. е. при серийном производстве, такие гладкие втулки обрабатываются за несколько операций с применением упоров и лимбов. В этом случае целесообразно обрабатывать втулки из длинного прутка, если его диаметр меньше диаметра отверстия в шпинделе.
При чистовом обтачивании малой партии гладких втулок иногда токари применяют самоцентрирующий патрон с расточенными «сырыми» кулачками. Растачивают кулачки строго по наружному диаметру закрепляемой втулки.
Время обработки втулки можно уменьшить, если совместить черновое обтачивание наружной поверхности со сверлением отверстия.
Рисунок 1.39. Последовательность токарной обработки
одной гладкой втулки
б) Обработка гладких втулок из штучных заготовок.
При серийном производстве гладкие втулки с наружным диаметром более 50...60 мм обрабатывают обычно из штучных заготовок, так как пруток не проходит сквозь отверстие в шпинделе станка. В этом случае пруток предварительно разрезается на мерные заготовки
Для обработки втулок диаметром более 80 мм часто используют заготовки в виде отливок иреже в виде поковок. Заготовки для таких втулок обычно изготовляют с отверстиями.
При обработке единичных втулок заготовку обычно принимают на 20...30 мм длиннее требуемой длины, чтобы ее можно было установить и закрепить в кулачках патрона за эту удлиненную часть, которую затем отрезают. На рис.1.40 показаны эскизы процесса обработки втулки из отлитой заготовки.
Рисунок 1.40. Последовательность токарной обработки
одной втулки из литой заготовки
Начинается обработка с подрезания торца (Рис.1.40 а), затем производятся обтачивание (Рис.1.40 б), растачивание (Рис.1.40 в) и отрезание (Рис.1.40 г). Так как втулка обрабатывается за одну установку, концентричность наружной поверхности к отверстию достигается достаточно высокая (0,03—0,05 мм).
При изготовлении партии аналогичных втулок (диаметром более 100 мм)заготовки отливают с отверстием, но без увеличения их длины на 20 - 30 мм, и обработку производят так, как показано на рис.1.40 в (сверление отверстия в этом случае не требуется).
Токарная обработка дисков
К дискам относятся детали, представляющие собой тела вращения с наружным диаметром, превышающим их длину (или толщину) в несколько раз. К этой группе деталей относятся также заготовки многих зубчатых колес, неширокие шкивы, кольца и др.
Диски могут быть:
- гладкие и с отверстиями;
- с наружными поверхностями - гладкими и ступенчатыми;
- торцовыми поверхностями - гладкими, ступенчатыми и фасонными.
Заготовкой диска может быть поковка, штамповка, отливка, а иногда отрезок из листового проката или прутка. Гладкий диск небольшого диаметра может быть изготовлен из круглого прутка.
Рис.1.41. Последовательность токарной обработки
гладкого диска в индивидуальном производстве
Заготовку зажимают в трехкулачковый патрон; подрезают начисто торец (Рис.1.41 б), обтачивают на ∅ 100 мм на длине 25 мм (Рис.1.41 в) и снимают фаску (Рис.1.41 г). Затем отрезают диск толщиной 21 мм (Рис.1.41 д), оставляя 1 мм для чистового подрезания торца.
Последними переходами являются чистовое подрезание второго торца (Рис.1.41 е)и снятие фаски 2×45° с этого же торца (Рис.1.41 ж).
Наброски и зарисовки растений, плодов, цветов: Освоить конструктивное построение структуры дерева через зарисовки отдельных деревьев, группы деревьев...
Опора деревянной одностоечной и способы укрепление угловых опор: Опоры ВЛ - конструкции, предназначенные для поддерживания проводов на необходимой высоте над землей, водой...
Своеобразие русской архитектуры: Основной материал – дерево – быстрота постройки, но недолговечность и необходимость деления...
Индивидуальные очистные сооружения: К классу индивидуальных очистных сооружений относят сооружения, пропускная способность которых...
© cyberpedia.su 2017-2024 - Не является автором материалов. Исключительное право сохранено за автором текста.
Если вы не хотите, чтобы данный материал был у нас на сайте, перейдите по ссылке: Нарушение авторских прав. Мы поможем в написании вашей работы!