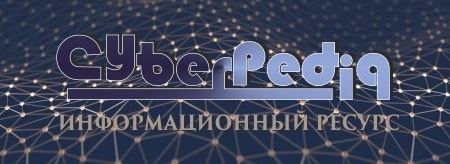
Механическое удерживание земляных масс: Механическое удерживание земляных масс на склоне обеспечивают контрфорсными сооружениями различных конструкций...
История развития хранилищ для нефти: Первые склады нефти появились в XVII веке. Они представляли собой землянные ямы-амбара глубиной 4…5 м...
Топ:
Генеалогическое древо Султанов Османской империи: Османские правители, вначале, будучи еще бейлербеями Анатолии, женились на дочерях византийских императоров...
Отражение на счетах бухгалтерского учета процесса приобретения: Процесс заготовления представляет систему экономических событий, включающих приобретение организацией у поставщиков сырья...
Установка замедленного коксования: Чем выше температура и ниже давление, тем место разрыва углеродной цепи всё больше смещается к её концу и значительно возрастает...
Интересное:
Наиболее распространенные виды рака: Раковая опухоль — это самостоятельное новообразование, которое может возникнуть и от повышенного давления...
Подходы к решению темы фильма: Существует три основных типа исторического фильма, имеющих между собой много общего...
Лечение прогрессирующих форм рака: Одним из наиболее важных достижений экспериментальной химиотерапии опухолей, начатой в 60-х и реализованной в 70-х годах, является...
Дисциплины:
![]() |
![]() |
5.00
из
|
Заказать работу |
УЧЕБНАЯ ПРАКТИКА В МАСТЕРСКИХ
Методическое пособие по учебной практике
в мастерских для студентов специальностей:
Астрахань – 2015
Автор:
Уксусов С.С. – ст. преподаватель кафедры судостроения и энергетических комплексов морской техники;
Петровский В.А. – ст. преподаватель кафедры судостроения и энергетических комплексов морской техники
Рецензент:
Кораблин А.В. – к.т.н., профессор кафедры техники и технологии наземного транспорта
Учебная практика в мастерских. Методическое пособие по учебной практике содержит краткие теоретические и прикладные сведения по обработки металлов резанием и слесарным видам работ
Методические указания утверждены на заседании кафедры «Судостроение и энергетические комплексы морской техники» «11» декабря 2015 года, протокол № 4.
© Астраханский государственный технический университет
СОДЕРЖАНИЕ
Введение……………………………………………………………………………………. | 4 | |
Часть 1 | Методические указания при обработке на токарных станках…………………………. | 4 |
Требования по ТБ при работе на токарных станках ……………………..…………… | 4 | |
1.1. | Назначение и типы токарных станков ……………………………………..…………….. | 5 |
1.2. | Основные узлы токарно-винторезного станка.…… …………………………………..... | 9 |
1.3. | Режущий инструмент…………………….………………………………….…………….. | 12 |
1.4. | Установка, закрепление и обработка заготовок ……………………………………….… | 18 |
1.5. | Элементы режима резания при точении……………………………………………...…... | 31 |
1.6. | Технология обработки деталей на токарных станках………………………………....… | 32 |
1.7. | Правила ухода за токарным станком …………………………………………………...... | 35 |
Часть 2 | Выполнение работ на фрезерных станках……………………………………………..... | 35 |
Требования по ТБ при работе на фрезерных станках ……………………………….….. | 36 | |
2.1. | Особенности процесса фрезерования…………………………………………………..… | 36 |
2.2. | Работы, выполняемые на фрезерных станках………………………………………….... | 37 |
2.3. | Типы фрезерных станков ………………………………………………………………..... | 38 |
2.4. | Основные узлы фрезерных станков…………………………………………………...….. | 44 |
2.5. | Управление консольно-фрезерным станком……………………………………………... | 46 |
2.6. | Основные сведения об устройстве режущих инструментов для фрезерования…….. | 48 |
2.7. | Принадлежности к фрезерным станкам………………………………………………….. | 52 |
Часть 3 | Практика по слесарным работам…………………………………………………………. | 56 |
Техника безопасности, охрана труда и соблюдение | ||
правил производственной санитарии и гигиены………………………………………… | 56 | |
Виды работ, выполняемые при слесарной обработке………………………………….. | 57 | |
3.1. | Разметка ……………………………………………………………………………………. | 58 |
3.2. | Правка ……………………………………………………………………………………… | 62 |
3.3. | Гибка ……………………………………………………………………………………….. | 65 |
1.4. | Рубка………………………………………………………………………………………… | 66 |
3.5. | Резка …………………………………………………………………………………...…… | 70 |
3.6. | Опиливание ………………………………………………………………………………… | 72 |
3.7. | Шабровка ………………………………………………………………………………...… | 78 |
3.8. | Притирка ………………………………………………………………………………..…. | 81 |
3.9. | Клепка…………………………………………………………………………………..….. | 83 |
3.10. | Сверлильные работы ……………………………………………………………………... | 86 |
3.11. | Нарезание резьбы метчиками и плашками…………………………………………….… | 93 |
Заключение…………………………………………………………………………………. | 95 | |
Рекомендуемая литература...……………………………………………………………… | 96 | |
Приложение………………………………………………………………………………… | 97 | |
Инструкции по технике безопасности при работе на металлорежущем оборудовании………………………………………………………………………………… | 97 | |
1. | Общие требования…………………………………………………………………………. | 97 |
2. | Требования безопасности перед началом работы ……………………………………….. | 97 |
3. | Требования безопасности по окончании работы ………………………………………... | 98 |
4. | Требования безопасности в аварийных ситуациях ……………………………………… | 98 |
Введение
Учебная практика в мастерских является начальным этапом технологической подготовки студента механических специальностей, необходимым для изучения последующих курсов технических и экономических дисциплин, а также при проектной и конструкторской деятельности в качестве бакалавра и специалиста.
Задачами практики являются:
- ознакомление с металлорежущим оборудованием;
- изучение методов обработки металлов резанием;
- получение практических навыков работы на металлорежущих станках.
- получение навыков работы с ручным инструментом при слесарной обработке материалов.
Методическое пособие содержит 3 части указаний и Приложение:
Часть 1. Выполнение работ на токарных станках.
Часть 2. Выполнение работ на фрезерных станках.
Часть 3. Выполнение слесарных работ.
Приложение. Инструкции по технике безопасности при работе на металлорежущем оборудовании
Часть 1. Методические указания
При обработке на токарных станках
Требования по технике безопасности
Токарно-револьверные станки
Токарно-револьверные станки (Рис.1.1) предназначены для серийного изготовления деталей с поверхностями вращения из прутка различной формы или штучных заготовок, полученных отливкой, штамповкой или ковкой.
Револьверные станки разделяют:
а) по виду заготовки - прутковые и патронные;
б) по расположению оси револьверной головки - с вертикальной (карусельной) и горизонтальной (барабанной) осью головки;
в) по числу гнезд в головке для инструмента - 4-х, 6-ти и 16-ти позиционные;
г) по степени автоматизации - обычные и полуавтоматы.
Револьверные станки, в отличив от токарно-винторезных, вместо задней бабки имеют револьверную головку (круглую или шестигранную) - поворотный механизм для установки различных инструментов. Револьверная головка имеет только продольную подачу, поперечная подача осуществляется поперечным суппортом.
Рисунок1.1. Токарно-револьверный станок:
1 - станина с направляющими; 2 - коробка подач суппортов;
3 - шпиндельная бабка; 4 - патрон на шпинделе;
5 - резцедержатель суппорта; 6 -суппорт с фартуком;
7 - шестигранная револьверная головка с гнездами для установки
режущих инструментов; 8 -револьверный суппорт;
9 -барабан револьверного суппорта с упорами
Время обработки детали на револьверном станке значительно меньше, чем на обычном токарном, вследствие сокращения времени на перестановку инструментов, применения отключающих упоров и одновременной работы нескольких инструментов.
На револьверных станках, как и на карусельных, отсутствует винторезная цепь, поэтому резьбу можно нарезать только специальными инструментами: плашками, метчиками, резьбонарезными головками и др.
Токарно-карусельные станки
На токарно-карусельных стенках (Рис.1.2) обрабатывают детали тел вращения больших диаметров при относительно малой высоте (маховики, шкивы, колеса и др.).
Ось вращения обрабатываемых деталей вертикальна, что упрощает установку на станок заготовок большой массы.
Рисунок1.2. Токарно-карусельный станок
Карусельные станки могут иметь два или четыре суппорта, одну или две станинные стойки и круглый вращающийся стол (планшайбу) большого диаметра. Один из суппортов (верхний) оснащен револьверной головкой для закрепления нескольких режущих инструментов.
На карусельных станках можно выполнять все виды токарных работ, кроме нарезания резьб резцами, т.к. в кинематической цепи карусельных станков нет винторезной цепи.
Токарно-лобовые станки
Токарно-лобовой станок (Рис.1.3) предназначен для обработки торцевых, цилиндрических, конических, фасонных поверхностей типа дисков и фланцев больших диаметров и небольшой длины.
Ось вращения детали в этих станках расположена горизонтально, закрепление детали осуществляется на планшайбе большого диаметра и нет задней бабки.
Лобовые станки отличаются от токарных главным образом тем, что у них отсутствует задняя бабка.
Рисунок1.3. Токарно-лобовой станок
Токарно-винторезные станки
Наибольшее применение имеют универсальные токарно-винторезные станки (Рис.1.5 и 1.6), на которых могут выполняться все виды токарных работ:
Рисунок1.6. Токарно-винторезный станок 16ТВ30 Рисунок.1.5. Токарно-винторезный станок 16В20.
Станина
На станине 11, установленной на двух тумбах, монтируются все основные узлы станка (Рис.1.7).
Станина изготовляется из чугуна и состоит из двух продольных стенок, соединенных поперечными ребрами жесткости.
Станина имеет две плоские и две призматические направляющие.
Каретка суппорта движется, опираясь на одну призматическую и одну плоскую направляющие. Другие направляющие - призматическая и плоская - служат для передвижения задней бабки и закрепления ее в требуемом положении.
На левом конце станины закрепляют переднюю бабку.
Передняя бабка
Передняя бабка 3 служит для закрепления обрабатываемой детали и передачи ей главного движения - вращения. Наиболее ответственной деталью передней бабки является шпиндель, представляющий собой стальной пустотелый вал. На переднем конце шпинделя нарезана точная резьба, на которую можно навернуть патрон (кулачковый, поводковый, цанговый, мембранный) или планшайбу. В этом же конце шпинделя имеется коническое отверстие, в которое можно вставлять передний центр. Шпиндель вращается в подшипниках передней бабки.
В передней бабке расположена коробка скоростей, в которой вращательное движение вала электродвигателя преобразуется в необходимое по скорости и направлению вращение шпинделя.
Имеются токарные станки с коробкой скоростей, расположенной вне корпуса передней бабки.
Механизмы подачи
Движения подачи режущего инструмента относительно вращающейся заготовки осуществляются механизмами подачи, которые размещаются в коробке подач 2 и фартуке суппорта 9.
Механизмы подачи предназначены для передачи движения от шпинделя к суппорту с резцом.
Суппорт
Суппорт (Рис.1.8) токарного станка предназначен для закрепления на нем режущего инструмента и сообщения ему движения подачи при обработке. Нижняя плита 1 суппорта, называемая кареткой или продольными салазками, перемешается по направляющим станины механически или вручную. Резец при этом движется в продольном направлении (это и есть движение продольной подачи).
На верхней поверхности каретки имеются поперечные направляющие 12 в форме ласточкина хвоста, расположенные перпендикулярно к направляющим станины. На направляющих 12 перемещаются поперечные салазки 3 суппорта, посредством которых резец получает движение, перпендикулярное к оси шпинделя. На верхней поверхности поперечных салазок 3 расположена поворотная плита 4 суппорта, которая закрепляется после поворота гайкой 10.
Рисунок 1.8. Суппорт токарно-винторезного станка.
На верхней поверхности поворотной плиты расположены направляющие 5, по которым при вращении рукоятки 13 перемещается верхняя плита 11 - верхние салазки суппорта.
На верхней части суппорта устанавливают резцедержатель или резцовую головку для закрепления резцов. Чаще всего на токарно-винторезных станках средних размеров применяют четырехгранные поворотный резцедержатель (Рис.1.8), в котором можно закрепить 4 резца одновременно. Работать можно любым из установленных резцов. Для этого нужно повернуть головку и поставить требуемый резец в рабочее положение.
Перед поворотом резцедержатель необходимо открепить, повернув рукоятку 9, связанную с гайкой, сидящей на винте 7.
После каждого поворота головку нужно снова зажать рукояткой 9.
На мелких и средних станках применяют одноместный резцедержатель 5 (рис.1.9 а).
Нижняя часть 1 резцедержателя, имеющая Т-образную форму, закрепляется на верхней части суппорта гайкой 4. Для регулирования положения режущей кромки по высоте центров в резцедержателе имеется подкладка 2, нижняя сферическая поверхность которой опирается на такую же поверхность колодки резцедержателя. Закрепляют резец в резцедержателе двумя болтами 3.
Рисунок1.9. Резцедержатели
На крупных токарных станках применяют одноместные резцедержатели (Рис.1.9 б). В этом случае резец устанавливают на поверхность 7 верхней части суппорта и закрепляют планкой 2, затягивая гайку 4.
Для предохранения болта 3 от изгиба планка 2 поддерживается винтом 5, опирающимся на башмак 6. При отвертывании гайки 4 пружина 1 приподнимает планку 2.
Фартук
К нижней поверхности продольных салазок суппорта прикреплен фартук 9 (Рис.1.7) - часть станка, в которой заключены механизмы для продольного и поперечного перемещения суппорта с резцом. Эти перемещения могут совершаться механически и вручную.
Движение продольной подачи резца при выполнении всех токарных работ, кроме нарезания резьбы резцом, осуществляется при помощи, скрепленной со станиной зубчатой рейки и катящегося по ней зубчатого (реечного) колеса. Это колесо может получать вращение либо механически - от ходового вала 8, либо вручную.
Движения поперечной и наклонной подачи резца осуществляются винтовыми механизмами также механически или вручную.
Задняя бабка
Корпус задней бабки 7 (Рис.1.7)расположен на плите, передвигаемой по направляющим станины. В отверстии корпуса может в продольном направлении перемещаться пиноль с закрепленной в ней гайкой. С переднего конца пиноль снабжена коническим отверстием, в которое вставляется конический хвостовик центра, а иногда хвостовая часть сверла, зенкера или развертки. Перемещается пиноль при помощи маховичка вращающего винт, который при вращении перемещает гайку, а вместе с ней и пиноль.
Чтобы при вращении маховичка пиноль не проворачивалась, в ней сделан (внизу) шпоночный паз, в который входит шпонка, заложенная в корпус задней бабки. Закрепление пиноли в корпусе бабки осуществляется рукояткой с эксцентриком. Оси шпинделя станка и пиноли задней бабки должны совпадать, для установки пиноли по оси шпинделя служит поперечный винт.
Поперечным винтом можно смещать корпус относительно плиты в поперечном направлении, к чему прибегают иногда при точении конических поверхностей.
Для обтачивания в центрах деталей разной длины перемещают заднюю бабку вместе с плитой вдоль станины и закрепляют в нужном положении двумя зажимными болтами и скобой к станине станка. Отпустив скобу, передвигают заднюю бабку и, установив ее в нужном положении, снова затягивают скобу.
В некоторых конструкциях токарно-винторезных станков задняя бабка крепится на станине одной рукояткой при помощи эксцентрикового зажима и системы рычагов.
Чтобы удалить задний центр из конического отверстия пиноли, вращают маховичок пинолитаким образом, чтобы пиноль втягивалась в корпус задней бабки до отказа. В крайнем положении конец винта выталкивает центр.
Режущий инструмент
При выполнении работ на токарных станках приходится использовать разнообразные режущие инструменты: резцы, сверла, зенкеры, развертки, метчики, плашки и др.
Чаще всего используются токарные резцы.
Классификация резцов
Классификация токарных резцов представлена на рис. 1.10 и 1.11.
Рисунок 1.10. Токарные резцы по назначению:
а – проходной прямой; б - проходной упорный; в – подрезной; г – прорезной; д - отрезной;
е, ж –расточные; а - резьбовой для наружной резьбы; и - резьбовой для внутренней резьбы; к, л – фасонные.
Проходные резцы (Рис.1.10 а, б и 1.11 а,б) применяют для наружного точения деталей с продольной подачей. Они разделяются на проходные с углом φ = 45; 60 и 75° и проходные-упорные с углом φ = 90° (Рис.1.10 б и 1.11 в) для обработки уступов.
Подрезные (торцовые) резцы (Рис.1.10 в и 1.11 г)применяют для обработки торцовых поверхностей.
а) б)
в) г)
д) е)
Рисунок1.11. Стандартные конструкции токарных резцов:
- проходные: прямой (а), отогнутый (б) и упорный (в); - подрезной (г); - расточные: для сквозных (д) и глухих (е) отверстий.
Прорезные (Рис.1.10 г) и отрезные (Рис.1.10 д) резцы используют для прорезания прямоугольной канавки определенной ширины b и отрезания обработанной детали.
Расточные резцы применяют для растачивания сквозных (Рис.1.10 е и 1.11 д)и глухих (Рис.1.10 ж и 1.11 е) отверстий.
Резьбовые резцы применяют для нарезания наружной (Рис.1.10 з) и внутренней (Рис.1.10 и) резьб.
Фасонные резцы (Рис.1.10 к,л) используют для обработки различных фасонных поверхностей.
По направлению подачи резцы делятся на правые и левые
Правыми называют резцы, которыми работают при подаче справа налево, т. е. от задней к передней бабке станка, и у которых соответственно этому главная режущая кромка расположена слева.
Левыми называют резцы, которыми работают при подаче слева направо, т. е. от передней к задней бабке станка. Главная режущая кромка левых резцов расположена справа.
По форме головки резцы делятся на прямые и отогнутые.
Прямыми называют резцы, у которых ось резца в плане прямая, отогнутыми - резцы, у которых ось резца в плане отогнута вправо или влево.
Отогнутые проходные резцы очень удобны при продольном обтачивании поверхностей, расположенных близко к кулачкам патрона. Кроме того, эти резцы применяют при продольном обтачивании с последующей обработкой торцовой поверхности детали.
По материалу режущей части резцы разделяются на быстрорежущие, твердосплавные, минералокерамические, из композитов и алмазные
Быстрорежущие резцы применяют для черновой и чистовой обработки стали и сплавов цветных металлов на станках сравнительно небольшой мощности.
Твердосплавные резцы используют для черновой и чистовой обработки чугуна, стали, цветных металлов и неметаллических материалов на современных мощных, быстроходных токарных станках
Резцы с минералокерамическими пластинками применяют для получистовой и чистовой обработки чугуна и стали с высокой скоростью резания при условии безударной нагрузки,
Алмазные резцы предназначены для тонкого точения и растачивания преимущественно цветных металлов и сплавов.
Резцы из композитов (эльбор-Р, гексанит-Р и др.) используют при чистовом точении высокотвердых чугунов, закаленных сталей с высокой скоростью резания.
По способу присоединения режущей части резца к его стержню различают резцы цельные, составные с неразъемным креплением (наварные, напайные) и сборные (с механическим креплением),
Резцы из быстрорежущей стали делают обычно не цельными, а наварными: у них пластинка из быстрорежущей стали приваривается к стержню, изготовленному из конструкционной углеродистой стали.
Твердосплавные резцы делают чаще всего напайными: к стержню, изготовленному из конструкционной углеродистой стали, специальным припоем припаяна пластинкатвердого сплава. Такие резцы просты в изготовлении, но имеют ряд недостатков. Одним из недостатков такого метода крепления твердосплавной пластинки является образование после напайки мелких трещин в пластинке.
Этих недостатков не имеют сборные резцы с механическим креплением неперетачивоемой многогранной твердосплавной пластинки. Пластинка из твердого сплавакрепится к стержню прижимной планкойи болтом.
Керамические пластинки, как итвердосплавные, обычно крепят к державке механическим способом.
Резцы, оснащенные композитами, выполняются в виде металлических вставок, которые механически крепятся в державках.
Обработка резьбовых деталей
Резьбы можно классифицировать по следующим признакам:
- по размерности: метрическая, дюймовая, модульная, питчевая;
- по расположению на поверхности: наружная и внутренняя;
- по направлению движения винтовой канавки: правая и левая;
- по числу заходов: одно- и многозаходная;
- по профилю: треугольная, трапецеидальная, круглая, прямоугольная, пилообразная и др.;
- по виду поверхности с резьбой: цилиндрическая и коническая;
- по эксплуатационному назначению: крепежная, ходовая, крепежно-уплотнительная и др.
На токарных станках наиболее широко применяется методы нарезания наружной и внутренней резьб резцами и гребенками, плашками и метчиками.
Резьбовые резцы бывают (Рис.1.35) стержневые, призматические и круглые; их геометрические параметры не отличаются существенно от геометрических параметров фасонных резцов.
Наружную резьбу нарезают прямыми или отогнутыми резцами, внутреннюю – резцом с отогнутой шейкой (в отверстиях малого диаметра) и прямым резцом, установленным в оправку (в отверстиях большого диаметра). Расположение режущих кромок резца должно соответствовать профилю обрабатываемой резьбы.
Рисунок 1.35. Резьбовые резцы:
а – прямой; б – круглый; в – отогнутый
Резьбы треугольного профиля нарезают резцами с углом в плане при вершине ε = 60º±10' для метрической резьбы и ε = 55º±10' для дюймовой резьбы. Учитывая погрешности перемещения суппорта, которые могут привести к увеличению угла резьбы, иногда применяют резцы с ε = 59º30'.
Вершина резца может быть скругленной или с фаской в соответствии с формой впадины нарезаемой резьбы. Боковые задние углы резца с правой и левой сторон обычно делают одинаковыми и равными 3...5º (для нарезания резьбы с углом подъема до 4º) или 6...8º (при нарезании резьбы с углом подъема свыше 4º).
Величина боковых задних углов выбирается исходя из того, чтобы при нарезании резьбы исключить трение боковых поверхностей резца о винтовую поверхность резьбы.
При нарезании метрической резьбы главный задний угол резца α = 10...15º при обработке незакаленных стальных деталей и α = 6º - при обработке закаленных стальных деталей.
При нарезании внутренних резьб треугольного профиля в отверстиях диаметром до 50 мм угол α увеличивают до 18º.
Передний угол резьбонарезных резцов γ = 0...25º в зависимости от обрабатываемого материала. Для твердых и хрупких материалов выбирают меньшие значения γ, для вязких и цветных - большие значения γ.
При нарезании резьбы на деталях из высоколегированных жаропрочных сталей γ = 5...10º для черновых и чистовых резцов.
При нарезании резьбы чистовыми резцами на деталях из конструкционных сталей принимают γ = 0º. Правильность заточки резцов проверяют шаблоном.
Наружную и внутреннюю треугольную резьбу можно нарезать также и резьбовыми гребенками.
Резьбовые гребенки (Рис.1.36), в отличие от обычных резьбовых резцов, имеют на режущей части не один, а несколько зубьев, выполненных по форме профиля резьбы.
Гребенки бывают плоские стержневые (Рис.1.36 а), призматические (рис.35 б), круглые: без резьбы и с винтовой резьбой (Рис.1.36 в).
Рабочая часть гребенок (Рис.1.36 г) состоит из режущих l 1 и калибрующих l 2 зубьев. Режущие зубья (их бывает обычно 2...3) срезаны под углом φ так, что каждый последующий зуб режет несколько глубже предыдущего. Калибрующая часть, которая следует за режущей частью, имеет также несколько зубьев (3...4) и предназначена для зачистки резьбы.
Рисунок 1.36. Резьбовые гребенки:
а) плоская стержневая; б) призматическая; в) круглая; г) рабочая часть гребенки.
При нарезании резьбы гребенками, благодаря распределению нагрузки между несколькими зубьями, можно увеличить поперечную подачу и, тем самым, уменьшить число ходов по сравнению с резьбовыми резцами. Важно и то, что гребенки служат дольше, чем резьбовые резцы.
Закрепляют призматические гребенки в специальных державках и устанавливают их в резцовой головке точно на высоте центров. Значительно большее применение при нарезании резьб, как наружных, так и внутренних, получили круглые гребенки как более простые в изготовлении.
Плашки (Рис.1.37) предназначены для нарезания или калибрования наружных резьб за один ход. Наиболее широко применяются плашки для нарезания резьб диаметром до 52 мм.
Плашка представляет собой закаленную гайку с осевыми отверстиями, образующими режущие кромки. Обычно на плашках делают 3...6 стружечных отверстий для отвода стружки. Толщина плашки 8...10 витков. Режущую часть плашки выполняют в виде внутреннего конуса. Длина заборной части 2...3 витка.
Рисунок 1.37. Резьбонарезные плашки:
а) круглая; б) квадратная; в) шестигранная; г, д) трубчатая; γ — передний угол
Угол 2 φ = 40...60º при нарезании сквозной резьбы и 2 γ = 90º при нарезании резьбы до упора. Передний угол γ у стандартных плашек γ = 15...20º. Задний угол α = 6...8º и выполняется только на заборной (режущей) части.
Плашку устанавливают в плашкодержатель (патрон), который закрепляют в пиноли задней бабки или в гнезде револьверной головки.
Метчики предназначены для нарезания или калибрования резьбы в отверстиях.
Различают метчики ручные (Рис.1.38), машинные, машинноручные (для нарезания резьбы в гайках) и плашечные (для нарезания резьбы в плашках).
Рис.1.38. Метчик ручной.
Ручные метчики поставляются в комплекте, состоящем из 2...3 метчиков; черновые метчики имеют заниженные размеры, а чистовой - размеры полного профиля резьбы.
Машинноручные (гаечные) метчики выполняют с коротким, длинным и изогнутым хвостовиками.
Рабочая часть метчика l состоит из заборной l 1 и калибрующей l 2 частей. Длина заборной (режущей) части ручных черновых метчиков 4 витка, ручных чистовых метчиков 1,5…2 витка. Длина заборной части машинных метчиков при нарезании сквозных отверстий 5...6 витков, а при нарезании глухих отверстий 2 витка.
У гаечных метчиков длина заборной части 11...12 витков. Калибрующая часть l 2 служит для зачистки и калибрования резьбы и обеспечения правильного направления. Для уменьшения трения калибрующая часть имеет незначительный обратный конус. Хвостовая часть метчика l 3 представляет собой стержень; конец хвостовика l 4 у ручных (а иногда и машинных) метчиков имеет форму квадрата. Профиль канавки метчика оказывает влияние на процесс нарезания резьбы и должен способствовать отводу стружки. Широкое распространение получили метчики с тремя и пятью канавками.
Передний угол метчика γ = 5...10º при обработке стали, γ = 0...5º при обработке чугуна и γ = 10...25º при обработке цветных металлов и их сплавов. Задний угол метчика α = 4...12º.
Обычно метчики изготовляются с прямыми канавками, но в ряде случаев угол наклона канавки ε = 8...15°, что улучшает условия отвода стружки.
Токарная обработка втулок
К классу втулок относятся детали со сквозным отверстием ис наружной гладкой или ступенчатой поверхностью. Втулки широко используются в машинах, Основным техническим требованием большинства втулок является концентричность наружных и внутренних поверхностей и перпендикулярность одной или обеих торцовых поверхностей втулки ее оси.
По форме втулки можно разделить на следующие четыре группы:
1) гладкие;
2) с гладким отверстием и ступенчатой наружной поверхностью;
3) с гладкой наружной поверхностью и ступенчатым отверстием;
4) со ступенчатыми отверстием и наружной поверхностью.
Втулки изготовляют из пруткового материала и заготовок, отлитых из чугуна и цветных металлов и реже кованых и штампованных.
За последнее время стали применять втулки из пластмасс.
а) Обработка гладких втулок из проката.
Рассмотрим наиболее характерные примеры обработки гладких втулок. Такие втулки диаметром до 45...50 мм обычно изготовляются из проката. Последовательность обработки гладкой втулки (Рис.1.39 а) из проката:
- При первой установке отрезать от проката ∅ 45 мм заготовку длиной 80 мм и закрепить патроне с вылетом на ~ 60 мм.
- Операции выполняемые во второй установке:
1. Подрезать торцевую поверхность заготовки (Рис.1.39 б).
2. Обточить цилиндрическую поверхность на ∅ 40 мм (Рис.1.39 в) на длину 55 мм.
3. Сверлить ∅ 22 мм на длине 58 мм (Рис.1.39 г).
4. Расточить отверстие на ∅ 24 мм на длине 56 мм (Рис.1.39 д).
5. Отрезать деталь на длину 51 мм (Рис.1.39 е).
- При третьей установке подрезается другой торец (Рис.1.39 ж)и выдерживается длина 50 мм.
При растачивании отверстия расточным резцом достигают строгой концентричности наружной поверхности втулки к ее отверстию при обработке их с одной установки.
При партии втулок 10, 20 шт. и более, т. е. при серийном производстве, такие гладкие втулки обрабатываются за несколько операций с применением упоров и лимбов. В этом случае целесообразно обрабатывать втулки из длинного прутка, если его диаметр меньше диаметра отверстия в шпинделе.
При чистовом обтачивании малой партии гладких втулок иногда токари применяют самоцентрирующий патрон с расточенными «сырыми» кулачками. Растачивают кулачки строго по наружному диаметру закрепляемой втулки.
Время обработки втулки можно уменьшить, если совместить черновое обтачивание наружной поверхности со сверлением отверстия.
Рисунок 1.39. Последовательность токарной обработки
одной гладкой втулки
б) Обработка гладких втулок из штучных заготовок.
При серийном производстве гладкие втулки с наружным диаметром более 50...60 мм обрабатывают обычно из штучных заготовок, так как пруток не проходит сквозь отверстие в шпинделе станка. В этом случае пруток предварительно разрезается на мерные заготовки
Для обработки втулок диаметром более 80 мм часто используют заготовки в виде отливок иреже в виде поковок. Заготовки для таких втулок обычно изготовляют с отверстиями.
При обработке единичных втулок заготовку обычно принимают на 20...30 мм длиннее требуемой длины, чтобы ее можно было установить и закрепить в кулачках патрона за эту удлиненную часть, которую зат
Архитектура электронного правительства: Единая архитектура – это методологический подход при создании системы управления государства, который строится...
Организация стока поверхностных вод: Наибольшее количество влаги на земном шаре испаряется с поверхности морей и океанов (88‰)...
Индивидуальные очистные сооружения: К классу индивидуальных очистных сооружений относят сооружения, пропускная способность которых...
Историки об Елизавете Петровне: Елизавета попала между двумя встречными культурными течениями, воспитывалась среди новых европейских веяний и преданий...
© cyberpedia.su 2017-2024 - Не является автором материалов. Исключительное право сохранено за автором текста.
Если вы не хотите, чтобы данный материал был у нас на сайте, перейдите по ссылке: Нарушение авторских прав. Мы поможем в написании вашей работы!