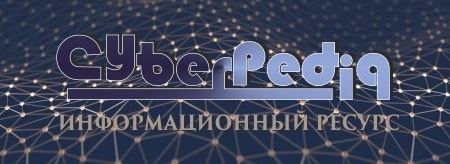
Эмиссия газов от очистных сооружений канализации: В последние годы внимание мирового сообщества сосредоточено на экологических проблемах...
Своеобразие русской архитектуры: Основной материал – дерево – быстрота постройки, но недолговечность и необходимость деления...
Топ:
Марксистская теория происхождения государства: По мнению Маркса и Энгельса, в основе развития общества, происходящих в нем изменений лежит...
Характеристика АТП и сварочно-жестяницкого участка: Транспорт в настоящее время является одной из важнейших отраслей народного хозяйства...
Теоретическая значимость работы: Описание теоретической значимости (ценности) результатов исследования должно присутствовать во введении...
Интересное:
Финансовый рынок и его значение в управлении денежными потоками на современном этапе: любому предприятию для расширения производства и увеличения прибыли нужны...
Уполаживание и террасирование склонов: Если глубина оврага более 5 м необходимо устройство берм. Варианты использования оврагов для градостроительных целей...
Наиболее распространенные виды рака: Раковая опухоль — это самостоятельное новообразование, которое может возникнуть и от повышенного давления...
Дисциплины:
![]() |
![]() |
5.00
из
|
Заказать работу |
|
|
Итоговые показатели, характеризующие разработанные проектные решения по участку, цеху, заводу, необходимы для оценки качества и экспертизы проекта. К ним относятся:
основные показатели: годовой выпуск в натуральном выражении и в оптовых ценах; добавленная стоимость годового выпуска; численность работающих с разбивкой по группам; основные промышленно-производственные фонды; капитальные вложения, связанные с реализацией проекта; трудоемкость выпускаемой продукции;
показатели уровня техники, технологии, механизации и автоматизации производства: количество основного оборудования; удельный вес применяемых прогрессивных, малоотходных видов заготовок; фондовооруженность работающих (отношение основных фондов к числу работающих); коэффициент использования материала; уровень механизации и автоматизации производственных процессов; наличие собственных технических решений, защищенных авторскими свидетельствами и патентами;
показатели уровня организации труда, производства и управления: производительность труда (добавленная стоимость годового выпуска) на одного работающего, фондоотдача (добавленная стоимость годового выпуска, отнесенная к основным фондам), коэффициент сменности работы оборудования, коэффициент кооперирования производства, количество примененной вычислительной техники в управлении и организации производства;
показатели уровня эффективности проекта: себестоимость продукции, рентабельность (отношение ожидаемой прибыли к приведенным затратам на годовой выпуск), срок окупаемости капитальных вложений, эффективность от внедрения проекта на рубль затрат на проектирование;
|
показатели социальных факторов и условий труда: наличие решений по обеспечению наиболее благоприятных и безопасных условий труда; удельный вес рабочих, занятых на ручных операциях; наличие решений по охране окружающей среды и использованию отходов производства;
показатели оформления проекта: комплектность документации и соответствие ее нормативным документам о порядке разработки и утверждения проектов.
Объективно оценить качество проекта и сопоставить различные варианты очень сложно ввиду многочисленности и разноплановости приведенных показателей. Поэтому часто используют интегральный (комплексный) показатель. Для этого прибегают к методу векторной оптимизации, когда каждому частному показателю устанавливают соответствующий коэффициент значимости при использовании аддитивных моделей или коэффициент эластичности при использовании мультипликативных моделей. В первом случае интегральный показатель качества проекта определяют по формуле
где К i — коэффициент значимости соответствующего частного показателя Xi во втором — на основе использования корреляционных зависимостей вида
где b — постоянный коэффициент; α i — коэффициент эластичности, определяющий степень влияния частного показателя X i.
В целях обеспечения высокого уровня проектных решений и наибольшей эффективности предполагаемых инвестиций проводят экспертизу проектов и смет с привлечением ведущих специалистов из независимых проектных организаций и фирм.
При технико-экономической оценке вариантов проектов необходимо учитывать перспективы развития производственных систем, которое в машиностроении непосредственно связано с автоматизацией производства, обеспечением его гибкости и все более широкой интеграции на базе использования компьютерной техники и информационных технологий. В будущем это ведет к созданию заводов как высокоавтоматизированных производств с минимальным участием людей и постоянным совершенствованием по мере развития научно-технического прогресса.
|
Создание гибких интегрированных производств требует не только постоянных усилий в направлении автоматизации основных и вспомогательных процессов, но и применения новых решений как в технологии машиностроения, так и в организации производства. Эти решения начинают проявляться в следующих направлениях.
1. Все более широкое использование малооперационной технологии и уменьшение степени дифференциации ТП изготовления и сборки изделий. Связано это с тем, что возрастание сложности машиностроительной продукции и, как следствие, многочисленность операций при дифференциации обработки привели к непроизводительному увеличению вспомогательных операций, длительности производственного цикла и объема незавершенного производства в условиях непоточного производства, а следовательно, к росту необходимых оборотных средств предприятия и снижению его эффективности.
Именно этим объясняется то, что применяемая ранее передовая технология с дифференциацией операций при гибкой автоматизации оказалась менее эффективной. Данная тенденция подтверждается более широким использованием в механообработке многоцелевых станков, позволяющих выполнять в одной операции различные виды обработки, например фрезерование, сверление, растачивание, шлифование и другие, а также отказом от поточно-конвейерной технологии сборки автомобилей на ряде фирм массового производства, таких как «Вольво», «СААБ-Скания» (Швеция), «Дженерал моторе» (США), где применена бригадная сборка автомобилей на одном рабочем месте. Благодаря этому обеспечивается гибкость (возможность сборки изделий различной модификации), высокое качество и ответственность персонала.
2. Повышение гибкости и мобильности производства. Традиционно наиболее высокая производительность достигалась при широком использовании специального и специализированного оборудования, АС и скомпонованных на их базе АЛ. Однако проектирование и изготовление специального оборудования, после того как изделие спроектировано, длится около 5 лет. Если к этому сроку прибавить 5—6 лет, необходимые для амортизации оборудования, то получается, что изделие не может изменяться около 10 лет. В этом заключается консерватизм производства на базе АЛ из специализированного оборудования.
|
Использование многоцелевых сверлильно-фрезерно-расточных станков с автоматической сменой отдельных инструментов и многошпиндельных головок, токарных многоцелевых станков с одной или несколькими револьверными головками позволяет разрешить противоречие между высокой производительностью и малой гибкостью, характерное для производственных систем на базе специализированного оборудования, и одновременно обеспечить высокие производительность и гибкость. Таким образом, становится возможным выпускать новые изделия на действующем оборудовании.
3. Интенсификация процессов изготовления деталей. Для повышения производительности технологического оборудования следует развивать многоинструментную и многопозиционную обработки с использованием параллельных и параллельно-последовательных схем построения операций. Для этого многоцелевые станки и модули ГПС необходимо выпускать в различных исполнениях для производств различного типа. Так, обработку сложных корпусных деталей, изготавливаемых в условиях крупносерийного и массового производства, целесообразно вести на ГАЛ из модулей, имеющих несколько шпиндельных головок для обработки заготовок с разных сторон. При этом должна быть обеспечена возможность смены многошпиндельных головок и автоматической передачи заготовок по гибкому маршруту. В случае изготовления аналогичных деталей малыми партиями целесообразно использовать ГПС из одношпиндельных многоцелевых станков с автоматической сменой отдельных инструментов и использованием многошпиндельных головок для обработки унифицированных сочетаний поверхностей, например отверстий для установки электродвигателей и других стандартных изделий.
В конструкциях нового оборудования должна быть обеспечена возможность интенсификации режимов резания при применении высокопроизводительных режущих инструментов. Уже в настоящее время на передовых фирмах выпускается оборудование, обеспечивающее возможность обработки со скоростями резания при токарной обработке до 800 м/мин.
|
4. Постоянная модернизация производства в ходе научно- технического прогресса. Для обеспечения конкурентоспособности выпускаемых изделий необходимо совершенствовать не только их конструкции, но и производство, постоянно повышая его эффективность. С этой целью гибкие производственные системы следует строить с использованием блочно-модульного принципа создания гибких модулей обработки и сборки, элементов автоматизированных транспортно-накопительных и складских систем, систем инструментообеспечения и других компонентов. Этот принцип позволяет осуществлять постоянную модернизацию без остановки производства, внедряя и расширяя ГПС поэтапно, учитывая что ГАП является капиталоемким предприятием. Высокая стоимость ГПС требует тщательного анализа вариантов технологических и производственных процессов и затрат на их реализацию. В этих условиях становится не только необходимым, но и неизбежным моделирование производственных процессов при решении вопросов перспективного развития.
5. Переход на использование систем машин для выполнения комплекса работ, обеспечивающих непрерывность производственных процессов. Задача повышения эффективности производства в значительной мере связана с сокращением сроков ТПП и производственного цикла. При создании нового изделия до 99 % времени затрачивали на конструирование изделия и его техническую подготовку и только 1 % — на изготовление и испытание опытных образцов. При традиционном подходе в условиях серийного производства только 5 % времени уходит непосредственно на обработку и сборку, а остальные 95 % времени заготовки и детали находятся на складах и рабочих местах в ожидании обработки и сборки. Непрерывные производственные процессы требуют прежде всего интеграции конструкторской и ТПП на базе системы автоматизированного конструирования и технологического проектирования CAD-CAM. Дальнейшая интеграция связана с объединением автоматизированных систем технической подготовки и планирования производства с ГПС различных видов обработки и сборки.
Например, использование интегрированных систем позволило уменьшить производственный цикл изготовления весьма сложных многоцелевых станков в ГПС «Система 21» фирмы «Ямаза- ки» (Япония) до четырех недель по сравнению с четырьмя месяцами, которые были необходимы при использовании станков с ЧПУ. По данным этой фирмы, производственный цикл будет доведен до одной недели.
Время на переналадку при переходе от изготовления одной достаточно сложной детали гидроаппаратуры к другой на одной из лучших отечественных ГПС АЛП-3-2 составляет 30 с (время, необходимое для смены палеты). Это обеспечивает возможность вести обработку комплектных групп деталей для единицы изделия и работать практически без складов по принципу «все только тогда, когда нужно». Одновременно сокращение заделов ведет к уменьшению требуемой площади.
|
6. Минимизация потерь от брака и выпуск высококачественной продукции. Качество продукции в ГПС все более широко будет обеспечиваться применением соответствующих систем автоматического контроля и управления ТП. Внедрение автоматических систем контроля качества заготовок и материалов на входе,
в процессе изготовления деталей и сборки изделий, а также контроль и испытание готовой продукции с необходимой адаптацией ТП к изменяющейся производственной ситуации практически исключает брак, обеспечивает высокое качество продукции, не зависящее от квалификации оператора.
Повысить качество обработки позволило более широкое использование самонастраивающихся и самоподнастраивающихся систем автоматизации, систем с автоматическим контролем выходных параметров обработки и адаптивных систем. Аналогичные системы автоматизации нашли применение и на этапе сборки, например робототехнические системы, оснащенные устройствами распознавания образов для автоматической ориентации разнообразных деталей и тактильными датчиками для автоматического управления процессами выполнения соединений.
7. Снижение материалоемкости изделий и энергопотребления ТП. Решению задачи максимального приближения форм и размеров заготовок к размерам и форме готовых деталей способствует более широкое использование литья под давлением, в оболочковые, вакуумно-пленочные и песчано-восковые формы; жидкой и объемной холодной штамповок, горячей штамповки и прессования в закрытых штампах; методов порошковой металлургии. Замена литых заготовок штампосварными снижает их массу на 30 %. Использование новых материалов и точных заготовок имеет целью и позволяет снизить удельные затраты на производство деталей и изделий.
8. Углубление технологической, подетальной и предметной специализации. Мировой опыт развития машино- и приборостроения показывает, что неуклонно уменьшается число заводов с полным циклом производства и растет число заводов и фирм, специализированных по признаку выполняемых ТП (литейных, кузнечных, сборочных и др.) либо по признаку изготовляемых деталей или изделий (производства зубчатых колес, поршневых колец, подшипников, карбюраторов, электродвигателей, автотракторного электрооборудования, двигателей и др.). Это создает условия, при которых даже массовая продукция, комплектуемая часто по желанию потребителя из унифицированных деталей и изделий, выпускаемых на специализированных производствах в массовом порядке, становится более индивидуальной. Таким образом, налицо тенденция, при которой каждое производство становится звеном сети кооперирующихся предприятий.
Использование изложенных принципов и новых подходов при создании производственных систем обеспечивает высокую производительность труда и фондоотдачу.
Все сказанное не означает полного отрицания традиционных решений, однако характеризует тенденции совершенствования производственных систем в машиностроении и отражает опыт наиболее передовых фирм.
Контрольные вопросы
1.Назовите критерии оценки технического уровня производственных систем. Какова структура и последовательность выполнения проектных работ?
2.В чем сущность метода приведения при технологическом проектировании цехов? Как определить приведенную программу?
3.Назовите основные организационные формы механосборочного производства. Какова сущность системного подхода к выбору структуры цеха?
4.Как определяют количество станков и рабочих мест для участков и линий для различных типов производства?
5.В каких случаях выбирают непрерывно или периодически движущийся конвейер? Как определить количество рабочих мест на конвейере и его длину?
6.Дайте характеристику основных компоновочных схем механосборочного производства. В чем достоинства, недостатки этих схем и каковы области их применения?
7.Какие варианты размещения оборудования возможны на станочных участках и линиях? В каких случаях применяют тот или иной вариант?
8.Назовите критерии оптимизации при выборе варианта расположения оборудования и рабочих мест на участке.
9.Дайте характеристику компоновочных схем ГПС.
10.Как определяется число работающих по каждой группе при укрупненном и детальном проектировании?
11.Как определить площадь складов при укрупненных методах расчета и детальном проектировании?
12.Как определить число ячеек автоматизированного склада для хранения приспособлений-спутников и заготовок в таре?
13.Дайте классификацию конвейеров различного типа, расскажите об их конструктивных особенностях и области применения.
14.Каковы функции, выполняемые системой инструментообеспечения и ремонтной службой?
15.Укажите основные принципы, определяющие компоновку цеха.
16.Сформулируйте назначение и структуру технико-экономических показателей проектов производственных систем.
ЛИТЕРАТУРА
Базров Б.М., Таратынов О.В., Клепиков В.В. Технология сборки машин / Под ред. Б.М. Базрова. М.: СПЕКТР, 2011. 368 с.
Васильев А.С., Кондаков А.И. Выбор заготовок в машиностроении: Учебное пособие. М.: Изд-во МГТУ им. Н.Э. Баумана, 2002. 80 с.
Вороненко В.П., Соломенцев Ю.М., Схиртладзе А.Г. Проектирование машиностроительного производства: Учебник для вузов / Под ред. Ю.М. Соломенцева. М.: Дрофа, 2006. 380 с.
Кондаков А.И. САПР технологических процессов. М.: Академия, 2010. 272 с.
Корсаков B. C. Основы конструирования приспособлений. М.: Машиностроение, 1983. 227 с.
Мельников Г.Н., Вороненко В.П. Проектирование машиностроительных цехов: Учебник для вузов. М.: Машиностроение, 1990. 352 с.
Общемашиностроительные нормативы времени и режимов резания для нормирования работ, выполняемых на универсальных и многоцелевых станках с числовым программным управлением. В II ч. М.: Экономика. Ч. I. Нормативы времени. 1990. 208 с.;
Ч. II. Нормативы режимов резания. 1990. 474 с.
Справочник технолога-машиностроителя: В 2 т. Т. 1 / Под ред. А.М. Дальского, А.Г. Косиловой, Р.К. Мещерякова, А.Г. Суслова. М.: Машиностроение-1, 2001. 912 с.
Справочник технолога по автоматическим линиям / А. Г. Ко- силова, А.Г. Лыков, О.М. Деев и др.; Под ред. А.Г. Косиловой. М.: Машиностроение, 1988. 320 с.
Технологические аспекты конверсии машиностроительного производства / А.С. Васильев, С.А. Васин, А.М. Дальский, А.И. Кондаков; Под ред. А.И. Кондакова. М.; Тула: ТулГУ, 2003. 271 с.
Технология производства гусеничных и колесных машин /
Н.М. Капустин, К.М. Сухоруков, Р.К. Мещеряков и др.; Под ред. Н.М. Капустина. М.: Машиностроение, 1989. 223 с.
Холодкова А.Г. Технология автоматической сборки. М.: Машиностроение, 2010. 560 с.
Холодкова А.Г. Технологическая оснастка. М.: Академия, 2008.
ОГЛАВЛЕНИЕ
Предисловие …………………………………………………………. 3
Введение ……………………………………………………………… 5
1. Организационное обеспечение технологической подготовки производства ………………………………………………………… 7
1.1. Организация службы технологической подготовки производства………………………………………………………………....7
1.2. Функции, организационное и информационное обеспечение технологической подготовки производства………………………... 9
1.2.1. Обеспечение технологичности конструкций изделии.…..…9
1.2.2. Обеспечение технологического проектирования……….…15
1.2.3. Обеспечение выбора и подготовки заготовок….…………..23
1.2.4. Организация контроля и управления технологическими процессами……………………………………………………………25
1.3. Технологическая подготовка технического перевооружения
и реконструкции участков и цехов предприятий…………………..30
1.4. Автоматизация технологической подготовки производства…33
1.4.1. Концептуальные модели автоматизированных систем технологической подготовки производства………………………...33
1.4.2. Проблемы автоматизации технологической подготовки производства………………………………………………………….40
Контрольные вопросы………………………………………………..43
2. Станочные, сборочные и контрольные приспособления …...44
2.1. Классификация станочных приспособлений ………………...44
2.2. Выбор установочных элементов приспособлений………….....46
2.2.1. Установка заготовки на плоские технологические
базы……………………………………………………………….…46
2.2.2. Установка заготовки на внутреннюю цилиндрическую поверхность и перпендикулярную ее оси
плоскость…………………………………………………………....52
2.2.3. Установка заготовки на два цилиндрических отверстия с параллельными осями и на перпендикулярную им плоскость……54
2.2.4. Установка заготовки на центровые отверстия ………….…56
2.2.5. Установка заготовки по зубчатым поверхностям…………57
2.3. Зажимные устройства станочных приспособлений и их
расчет…………………………………………………………….….58
2.3.1. Характеристика зажимных устройств……………………...58
2.3.2. Основные схемы установки заготовок и расчет сил закрепления…………………………………………………………...63
2.3.3. Схемы для расчета сил закрепления заготовки под действием внешнего момента………………………………………..66
2.3.4. Расчет простейших зажимных устройств станочных приспособлений ……………………………………………. ……….70
2.3.5. Расчет центрирующих зажимных механизмов ……………75
2.3.6. Расчет пневмогидравлических зажимных механизмов …………………………………………................................................82
2.3.7. Расчет электромагнитных зажимных устройств…………..88
2.3.8. Расчет магнитных зажимных устройств...............................89
2.3.9. Расчет комбинированных зажимных устройств …………..90
2.4. Направляющие и вспомогательные устройства приспособлений……………………………………………...…….....93
2.5. Общая последовательность проектирования. Пример разработки специального станочного приспособления..................101
2.6. Классификация сборочных приспособлений и основные
этапы их проектирования...................................................................110
2.7. Особенности проектирования сборочных приспособлений..................................................................................112
2.7.1. Загрузочные устройства……………………………………112
2.7.2. Установочные приспособления …………………………...118
2.7.3. Ориентирующие устройства……………………………….120
2.7.4. Рабочие приспособления …………………………………..121
2.7.5. Контрольные приспособления…………………………….124
2.8. Особенности проектирования контрольных приспособлений..................................................................................126
2.8.1. Назначение контрольных приспособлений ………………126
2.8.2. Погрешность измерения и основные виды погрешностей контрольных приспособлений……………………………………...126
2.8.3. Расчеты, связанные с определением составляющих общей погрешности контрольного приспособления ……………………..130
2.8.4 Последовательность конструирования и пример расчета погрешности контрольного приспособления..............148
2.9. Универсально-сборные приспособления многократного применения ……………………………………………………………...151
Контрольные вопросы ……………………………………………..165
3. Контроль и управление технологическим процессом……... 166
3.1. Технологический процесс как объект контроля и управления……………………………………………………….…..166
3.1.1. Особенности технологических процессов в машиностроении ……………………………………………………………..166
3.1.2. Моделирование технологических процессов ………….…171
3.2. Анализ технологических процессов ………………………….175
3.2.1. Основные задачи анализа …………………………………175
3.2.2. Аппарат анализа ……………………………………………178
3.3. Формирование решений при управлении технологическими процессами ………………………………………………………….181
3.4. Управление технологическими процессами …………………188
3.4.1. Основные методы управления технологическими процессами ………………………………………………………….188
3.4.2. Оперативное регулирование статической настройки технологических систем……………………………………………195
3.4.3. Оперативное регулирование динамической настройки технологических систем…………………………………………... 202
3.4.4. Особенности управления технологическими процессами в автоматизированном производстве ………………………………208
3.4.5. Адаптация технологических процессов к изменяющейся производственной ситуации ………………………………………212
Контрольные вопросы ……………………………………………..215
4. Технологические процессы изготовления деталей в условиях единичного производства ………………………………………. 217
4.1. Характеристика объектов и технологических процессов единичного производства…………………………………………. 217
4.2. Технологические процессы изготовления деталей в тяжелом машиностроении ……………………………………………………223
4.2.1. Методы получения заготовок и припуски ………………. 223
4.2.2. Разметка заготовок ………………………………………... 227
4.2.3. Установка заготовок на оборудование и выверка………..229
4.2.4. Технология изготовления корпусных деталей……………236
4.3. Технологические процессы изготовления прецизионных деталей ………………………………………………………….…...247
4.3.1. Построение операций обработки основных поверхностей прецизионных деталей…………………………………………...…247
4.3.2.Изготовление прецизионных валов ……………………….251
Контрольные вопросы ……………………………………………..259
5. Технологические процессы изготовления деталей в условиях серийного и массового производства ……………………………260
5.1. Характеристика объектов и технологических процессов серийного и массового производства…………………………….. 260
5.2. Изготовление деталей на станках с ЧПУ …………………….264
5.2.1. Технологические возможности станков с ЧПУ и требования к конструкции изготавливаемых деталей …………………………264
5.2.2. Программирование с использованием системы CAD/CAM 2
5.2.3. Наладка станков с ЧПУ…………………………………….277
5.2.4. Программирование и обработка характерных поверхностей 5.2.5. Повышение точности обработки ………………….290
5.3. Изготовление деталей на агрегатных станках и автоматических линиях ……………………………………………………………….293
5.3.1. Установка заготовок ……………………………………….293
5.3.2. Обработка плоских поверхностей ………………………...300
5.3.3. Обработка основных и крепежных отверстий …………...306
5.4. Технологические процессы изготовления характерных
деталей ………………………………………………………………316
5.4.1. Ступенчатые валы ………………………………………….316
5.4.2. Коленчатые валы…………………………………………... 325
5.4.3. Рычаги в шатуны……………………………………………331
5.4.4. Корпусные детали…………………………………………..344
5.4.5. Сложнопрофильные детали………………………………..358
Контрольные вопросы ч…………………………………………. 374
6. Технологические процессы сборки машин ………………….375
6.1. Технологические процессы сборки типовых узлов машин и
Механизмов……………………………………………………….…375
6.1.1. Сборка узлов с подшипниками качения…………………….375
6.1.2. Сборка узлов с подшипниками скольжения………………..380
6.1.3. Сборка узлов с подвижными цилиндрическими
соединениями………………………………………………………. 384
6.1.4. Сборка зубчатых и червячных передач……………………..386
6.1.5. Сборка узлов с плоскими направляющими скольжения ….391
6.2. Балансировка сборочных единиц………………………….…..393
6.3. Технический контроль качества сборки………………………395
6.4. Испытание сборочных единиц и машин……………………...398
6.5. Типовые средства механизации и автоматизации сборки………………………………………………………………. 398
6.5.1. Механизированное и автоматическое сборочное оборудование ……………………………………………………………398
6.5.2. Автоматизированные линии сборки узлов автомобилей и тракторов ……………………………………………………………405
6.5.3. Средства автоматического контроля ьсборки…………….413
Контрольные вопросы………………………………………………416
7. Производственные системы механической обработки и сборки …………………………………………………………….…417
7.1. Структура производственных систем ………………………...417
7.2. Маркетинг в машиностроительном производстве, оценка технического уровня и выбор стратегии развития производства …………………………………………………………………….…422
7.3. Основные направления и последовательность проектирования производственных систем ……………………………………….....428
7.4. Анализ и синтез структуры построения основных производственных процессов …………………………………………….432
7.4.1. Методы технологического проектирования производственных систем…….…………………………………… 432
7.4.2. Методика выбора структуры производственных
Систем…………………………………………………………….. 440
7.4.3. Расчет количества оборудования………………………….448
7.4.4. Расчет числа рабочих мест…………………………………455
7.4.5. Компоновочные схемы цехов, планировка оборудования и рабочих мест ………………………………………………………..458
7.4.6. Особенности технологического проектирования автоматических производственных систем ……………………………480
7.4.7. Определение состава и численности работающих……….489
7.5. Системы обеспечения функционирования производства …...494
7.5.1. Транспортно-складская система…………………………...494
7.5.2. Система инструментообеспечения……………………….. 511
7.5.3. Система ремонтного и технического обслуживания механосборочного производства ………………………………….513
7.6. Синтез производственных систем…………………………….520
7.6.1. Компоновка производственной системы…………………520
7.6.2. Уточнение планировки рабочих мест и численности работающих………………………………………………………….529
7.6.3. Примеры планировочных решений производственных систем механосборочного производства ………………………….530
7.7. Технико-экономические показатели и перспективы разви
тия производственных систем……………………………………...540
Контрольные вопросы ……………………………………………...546
Литература …………………………………………………………..547
Учебное издание
Бурцев Валерий Михайлович, Васильев Александр Сергеевич, Гемба Игорь Николаевич, Деев Олег Михайлович, Игнатов Алексей Владимирович, Кондаков Александр Иванович, Максимович Борис Дмитриевич, Мельников Георгий Николаевич, Никадимов Евгений Федорович, Соловьев Александр Иванович, Тавров Виталий Иванович, Тихонов Виктор Павлович, Ястребова Надежда Александровна
ТЕХНОЛОГИЯ МАШИНОСТРОЕНИЯ
В двух томах
Том 2 Производство машин
Редактор Е.Н. Ставицкая Технический редактор Э.А. Кулакова Художник Н.Г. Столярова Корректор Р. В. Царева Компьютерная графика О. В. Левашовой Компьютерная верстка Н.Ф. Бердавцевой
Оригинал-макет подготовлен в Издательстве МГТУ им. Н.Э. Баумана.
Санитарно-эпидемиологическое заключение № 77.99.60.953.Д.003961.04.08 от 22.04.2008 г.
Подписано в печать 25.01.12. Формат 60x90 1/16. Уел. печ. л. 34,5. Тираж 1000 экз. Заказ №52
Издательство МГТУ им. Н.Э. Баумана.1'" ^^ 105005, Москва, 2-я Бауманская, 5.
E-mail: [email protected] http://www.baumanpress.ru
Отпечатано в типографии МГТУ им. Н.Э. Баумана. 105005, Москва, 2-я Бауманская, 5.
E-mail: [email protected]
ISBN 978-5-7038-3443-5
9 785703
83443 5
9785703834435
|
|
Состав сооружений: решетки и песколовки: Решетки – это первое устройство в схеме очистных сооружений. Они представляют...
Опора деревянной одностоечной и способы укрепление угловых опор: Опоры ВЛ - конструкции, предназначенные для поддерживания проводов на необходимой высоте над землей, водой...
Адаптации растений и животных к жизни в горах: Большое значение для жизни организмов в горах имеют степень расчленения, крутизна и экспозиционные различия склонов...
Кормораздатчик мобильный электрифицированный: схема и процесс работы устройства...
© cyberpedia.su 2017-2024 - Не является автором материалов. Исключительное право сохранено за автором текста.
Если вы не хотите, чтобы данный материал был у нас на сайте, перейдите по ссылке: Нарушение авторских прав. Мы поможем в написании вашей работы!