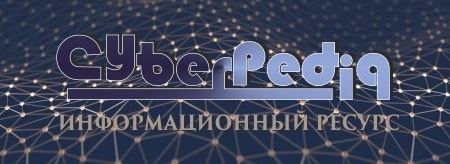
Семя – орган полового размножения и расселения растений: наружи у семян имеется плотный покров – кожура...
Особенности сооружения опор в сложных условиях: Сооружение ВЛ в районах с суровыми климатическими и тяжелыми геологическими условиями...
Топ:
Особенности труда и отдыха в условиях низких температур: К работам при низких температурах на открытом воздухе и в не отапливаемых помещениях допускаются лица не моложе 18 лет, прошедшие...
Проблема типологии научных революций: Глобальные научные революции и типы научной рациональности...
Установка замедленного коксования: Чем выше температура и ниже давление, тем место разрыва углеродной цепи всё больше смещается к её концу и значительно возрастает...
Интересное:
Инженерная защита территорий, зданий и сооружений от опасных геологических процессов: Изучение оползневых явлений, оценка устойчивости склонов и проектирование противооползневых сооружений — актуальнейшие задачи, стоящие перед отечественными...
Распространение рака на другие отдаленные от желудка органы: Характерных симптомов рака желудка не существует. Выраженные симптомы появляются, когда опухоль...
Как мы говорим и как мы слушаем: общение можно сравнить с огромным зонтиком, под которым скрыто все...
Дисциплины:
![]() |
![]() |
5.00
из
|
Заказать работу |
|
|
При проектировании нового цеха большое значение имеет выбор типа производственного здания, его компоновки и размеров в плане. При реконструкции и техническом перевооружении производства возникает задача наилучшего использования имеющихся производственных зданий для размещения новых участков и цехов. Стоимость производственных зданий в машиностроении довольно высока и достигает 30...40 % стоимости основных фондов предприятий.
Объемно-планировочные решения производственных зданий могут быть разнообразными. Для цехов механосборочного производства пригодны одно- и многоэтажные здания со светоаэ- рационными фонарями и без них, крановые (оборудованные мостовыми кранами) и бескрановые здания с использованием напольного и подвесного транспорта. По форме в плане здания обычно проектируют прямоугольными, однако в отдельных случаях применяют Г-, П- или Ш-образные конструкции. Это связано обычно с конкретными условиями территории завода или стремлением зарезервировать площадь для дальнейшего расширения цехов путем пристройки дополнительных пролетов.
При проектировании производственных зданий наиболее широкое применение получили каркасные здания с использованием унифицированных железобетонных строительных элементов заводского изготовления. Для ускорения и удешевления строительного проектирования разработаны унифицированные типовые секции, представляющие собой объемную часть здания и состоящие из одного или нескольких пролетов одинаковой длины.
Типовое проектирование позволяет разместить в одном здании несколько цехов, если это не противоречит условиям производства и противопожарным требованиям. Блокирование нескольких цехов в одном здании способствует сокращению коммуникаций и транспортных расходов.
|
При оформлении компоновочных планов здание в плане показывают в виде сетки продольных и поперечных разбивочных осей (см. рис. 7.4). При этом продольные разбивочные оси, образующие пролеты здания, обозначают заглавными буквами русского алфавита, а поперечные — арабскими цифрами.
Для проектирования производственных зданий разработан типаж основных и дополнительных унифицированных секций. Размеры основных секций в плане составляют 72x72 м или 72x144 м, причем первый размер соответствует длине пролета, второй — ширине секции. Основные секции могут быть крановыми и бескрановыми, с сеткой колонн 18x12 м или 24x12 м при высоте пролета 6; 7,2 или 8,4 м для бескрановых и 10,8; 12,6 м и более — для крановых зданий. Площадь основных секций составляет 5 184 м2 или 10 368 м2. Помимо основных предусмотрены дополнительные одно- или двухпролетные секции длиной 72 м, оборудованные кранами с высотой пролета 10,8; 12,6; 16,2 или 18 м. Эти пролеты имеют ширину 24 или 30 м и предназначаются для размещения производства крупных изделий. На рис. 7.28 показаны разрезы бескрановых и крановых пролетов производственных зданий, а также пристройки для административных и бытовых помещений.
Здания без светоаэрационных фонарей с подвесным потолком (см. рис. 7.28, б) применяют для термоконстантных цехов. В межферменном пространстве при этом располагают воздуховоды и фильтры для систем кондиционирования.
Административно-технические службы и бытовые помещения цехов размещают в пристройках к производственным зданиям (см. рис. 7.28, г) или в отдельно стоящих помещениях. В последнем случае предусматривают утепленные переходы в производственные корпуса.
При детальной разработке строительной части проекта расчет площади административно-бытовых помещений ведут по соответствующим нормам для всех категорий работающих. При укрупненных расчетах для принятия компоновочных решений общая площадь этих помещений может быть определена по норме 5…6 м2 на одного списочного работающего.
|
Рис. 7.28. Поперечные разрезы зданий: а — бескрановое здание со светоаэрационным фонарем; б, в — то же с плоской кровлей и подвесным потолком; г — пристройка к производственному зданию для административных и бытовых помещений; 1 — подвесной потолок; 2 — люминесцентные светильники
Площадь отдельных помещений устанавливают исходя из следующих нормативов на одного работающего, м2: 2,86 — для санитарно-гигиенических (гардеробно-душевые блоки, туалеты и др.); 1 — для служебных; 0,7 — для пунктов общественного питания; 0,4 — для объектов культурно-массового обслуживания и 0,08 — для медицинских помещений.
Для пристроек и отдельно стоящих административно-бытовых зданий применяют унифицированные типовые секции с сеткой колонн 6x6 м. Ширина пристроек 12 м, а отдельно стоящих зданий 18 м. В зависимости от конкретных условий пристройка может располагаться с торцевой части здания или вдоль крайнего пролета. Первый вариант применяют чаще.
При выборе компоновки здания следует исходить из данных об общей площади цехов, принятого варианта их взаимного размещения, а также необходимости организации вспомогательных служб для технического и хозяйственного обслуживания цехов. При объединении вспомогательных служб целесообразно создавать общий корпусной склад заготовок и металла; объединять подразделения для организации ремонтного обслуживания технологического, энергетического и подъемно-транспортного оборудования.
Общие системы обеспечения станков СОЖ, сбора стружки, транспортного оборудования, обеспечения инструментом и т. п. способствуют лучшему использованию сложного оборудования, сокращению численности вспомогательных рабочих и требуемой площади.
В процессе общей компоновки корпуса и уточнения ранее принятых планировочных решений определяют габариты и структуру производственного здания. Компоновочные планы выполняют для каждого этажа здания, показывая на них основные стены, границы между цехами и участками, вспомогательные устройства (трансформаторные подстанции, насосные вентиляционные камеры и т. д.), основные подъемно-транспортные устройства (краны, кран-балки, конвейеры) и их трассы, основные грузопотоки, основные проезды и проходы, вводы железнодорожных путей, а также границы подвалов, антресолей, тоннелей, магистральных стружкоуборочных каналов и т. д. с указанием вертикальных отметок относительно уровня пола основного этажа.
|
Компоночные планы выполняют в масштабах 1:200 и 1:400 (1:800) на основе чертежа архитектурно-строительной части с сохранением принятой в нем разбивки и маркировки осей колонн, стен и других строительных конструкций.
В качестве исходных данных для разработки компоновочного плана используют состав отделений и служб цехов с данными об их площадях; выбранную ранее компоновочную схему, определяющую общую последовательность производственного процесса, а также основные параметры и общую компоновку здания.
Основные принципы, определяющие выбор компоновки цехов, следующие:
1) обеспечение прямоточности производственного процесса; исключение, по возможности, возвратных движений грузопотоков;
2) компактность, т. е. использование минимальной производственной площади для размещения участков и цехов;
3) обеспечение условий для использования наиболее экономичных прогрессивных видов транспорта;
4) минимизация транспортных операций при перемещении изделий в процессе их производства;
5) совместимость ТП, размещаемых на смежных участках или цехах, с учетом взаимного влияния на качество изделий, а также исходя из условий труда и пожарной безопасности;
6) возможность последующего расширения производства и перепланировки оборудования, связанных с изменением или внедрением новых ТП и производств;
7) использование рациональных компоновок зданий из унифицированных типовых секций.
Главным при выборе компоновочной схемы является обеспечение кратчайшего пути основных технологических грузопотоков
от получения заготовок и полуфабрикатов до выхода готовой продукции. При этом цеховые или корпусные склады заготовок должны располагаться в корпусе со стороны заготовительных цехов, а выход готовых изделий — со стороны склада готовой продукции. Подразделения технического, ремонтного и инструментального обслуживания, как правило, размещают в стороне от основных технологических потоков по периферии корпуса либо по границам цехов внутри крупных корпусов.
|
Между производственными участками обычно не предусматривают перегородок. Исключение составляют термоконстантные или пожароопасные производства. Размещение каналов для транспортирования стружки, системы энергетических разводок и подвода СОЖ должны обеспечивать возможность переустановки оборудования или его замену на новое при замене объекта или технологии производства.
Границами производственных участков и цехов, как правило, являются продольные и поперечные проезды шириной 4,5...5,5 м. Расстояние между проездами не нормируют, оно определяется условиями рационального размещения поточных линий, предметно-замкнутых или подетально-специализированных участков. Длина участков обычно составляет 35...50 м.
Компоновка производственной системы неразрывно связана с принятой организационной формой производства. При этом одновременно формируют информационные потоки в производственной системе и определяют места расположения средств управления.
На рис. 7.29 дан компоновочный план главного корпуса станкостроительного завода, рассчитанного на выпуск 4 425 станков в год. Общая площадь корпуса без бытовых помещений 43 тыс. м2. В одном корпусе размещены цех подготовки заготовок, склады металла и заготовок, механические цехи с термоконстантным отделением, инструментальный и термический цехи, отделения и участки металлопокрытий и окраски, склады готовых деталей и комплектующих, электромонтажный и сборочный цехи, а также комплекс вспомогательных служб корпусного и цехового подчинения.
Отливки и штампованные заготовки, а также прокат поступают с разгрузочной площадки, располагаемой параллельно пролетам и оборудованной козловыми кранами 1 и 2. В зону разгрузочно-погрузочной площадки предусмотрен железнодорожный ввод. Отливки сначала подвергают очистке и обрубке, после чего проводят обдирку их основных плоскостей. Далее они на элект- рофицированной тележке поступают в цех термической обработки на старение для снятия остаточных напряжений. После этого проводят окраску необрабатываемых поверхностей заготовок в отделении окраски, чтобы связать остатки формовочной смеси на их поверхности и предотвратить возможность попадания смеси в дальнейшем на поверхности трения. Подготовленные к обработке заготовки передают на склад литых заготовок.
Металлический прокат поступает на склад металла и далее в заготовительный цех для резки на штучные заготовки. Полученные резкой или по кооперации штучные заготовки направляют на централизованный склад заготовок. Многоярусный стеллажный склад оборудован краном-штабелером 8. Со склада заготовки партиями передают для обработки в механические цехи с помощью электрогрузовозов с автоматическим адресованием. В цехе крупных деталей межоперационную передачу осуществляют мостовым краном 4. В цехах по производству средних и мелких деталей используют автоматизированные транспортно-накопительные системы. Стальные заготовки напольным транспортом направляют в термический цех для термообработки и далее на обработку в механический цех.
|
Рис. 7.29. Компоновочный план типового проекта 1, 2 — козловые краны грузоподъемностью (20 и 10 т соответственно); 3 — ны (5, 5, 20/5 и 20/5 т соответственно); 5 — елочные стеллажи; 6 — электро- краны-штабелеры (0,5 и 1 т соответственно); 9 — электрогрузовоз; 10 — леры; 13 — подвесные однобалочные краны (2 т); 14, 22 — полукозловые шагающий конвейер; 21 — сборочный шагающий конвейер;
ИРК — инстглавного корпуса станкостроительного завода: электрофицированная перегрузочная тележка; 4, 12, 18, 19 — мостовые кра- штабелер с захватным устройством для прутков
(1 т); 7— стеллажи; 8, 17— подвесной конвейер для подачи заготовок на склад; 11, 16 — электроштабе- краны (1 т);
15 — подвесной однобалочный кран (3 т); 20 — окрасочный рументально-раздаточная кладовая; ОТК — отдел технического контроля
В конце подетально-специализированных линий механической обработки расположены контрольные посты.
Для передачи готовых деталей и комплектующих на склад используют подвесные электрогрузовозы 9 с автоматическим адресованием, перемещающиеся по монорельсу.
Сборочное производство расположено в двух пролетах, перпендикулярных пролетам механического цеха. В пролете, примыкающем к складу готовых деталей, размещены участки узловой сборки и конвейер общей сборки серийных станков, а также электромонтажный цех и участок испытания станков. В следующем пролете находится сборочное отделение специальных станков, цех окраски и экспедиция.
Финишную обработку высокоточных деталей и сборку шпиндельных узлов выполняют в термоконстантном помещении, здесь же расположен склад прецизионных деталей и центральная измерительная лаборатория. Для передачи комплектов деталей со склада на сборку предусмотрена монорельсовая дорога, оборудованная электрогрузовозами 9 с автоматическим адресованием.
Тяжелые базовые детали станков на сборку транспортируют на электрофицированной перегрузочной тележке 3.
Вспомогательные отделения систем технического и ремонтного обслуживания расположены в стороне от основных технологических потоков и сгруппированы по функциональному назначению (инструментально-раздаточные кладовые, заточное отделение, корпусная ремонтная база, центральные инструментальный и абразивный склады и т.д.).
Бытовые помещения размещены в отдельно стоящих зданиях (на рис. 7.29 не показаны) и соединены с производственным зданием переходами.
Рассмотренную компоновку отличает прямоточность основных производственных процессов, отсутствие возвратных движений грузопотоков, компактность и использование прогрессивных видов транспорта. Как уже отмечалось, для всех операций межцеховой передачи мелких и средних заготовок и деталей использованы подвесные электрогрузовозы с автоматическим адресованием, которые не требуют наличия широких проездов. Применение автоматизированных транспортно-накопительных систем стеллажного типа со штабелерами-операторами или кареток-операторов с накопителями башенного типа обеспечивает автоматизацию межоперационной передачи и межоперационного складирования заготовок.
7.6.2. Уточнение планировки рабочих мест и численности работающих
В процессе общей компоновки цеха с учетом выбранного варианта транспортно-складской системы, систем инструментообеспечения, ремонтного и технического обслуживания, контроля качества изделий, а также мероприятий по охране труда проводят уточнение планировки отдельных производственных участков. Это связано в первую очередь со стыковкой общецеховой транспортной системы цеха с устройствами межоперационной передачи на участках в процессе обработки. Для этой цели на производственных участках уточняют расположение зон приема заготовок и отправки готовых деталей и узлов; определяют расположение терминалов, обеспечивающих связь с диспетчерскими или управляющими пунктами. Чтобы увязать расположение оборудования смежных участков, планировку всего корпуса выполняют обычно в масштабе 1:200.
В процессе общей планировки уточняют взаимное размещение рядов станков, линейных и магистральных конвейеров для удаления стружки, определяют расположение приводных станций и емкостей для ее сбора, уточняют маршруты напольного транспорта, окончательно устанавливают трассы подвесного транспорта (подвесных конвейеров, монорельсов с автоматическими грузовозами, кран-балок и др.). При этом определяют высоту трасс на отдельных участках; намечают участки подъема и спуска с учетом расположения оборудования, проездов и складов; решают вопросы передачи деталей и узлов из одного пролета в другой; определяют места расположения рабочих мест мастеров; уточняют размещение межоперационных заделов, циркуляционных установок СОЖ, трансформаторных подстанций, вентиляционных камер и компрессорных станций. На основе общей планировки окончательно устанавливают площадь цеха и его подразделений.
Общую планировку цеха используют также для уточнения числа работающих. При этом окончательно определяют зоны многостаночного обслуживания основного и вспомогательного оборудования, а также количество рабочих, обслуживающих подъемно-транспортное оборудование и вспомогательные отделения; устанавливают организационную структуру управления цехом и на основе этого уточняют общую численность работающих по группам, подразделениям и сменам. Результаты расчетов представляют в виде сводной ведомости работающих с указанием должностей, специальностей и разрядов.
7.6.3. Примеры планировочных решений производственных систем механосборочного производства
Рассмотрим характерные схемы планировок участков сборки и механической обработки в серийном производстве с использованием автоматизированных транспортно-накопительных систем.
На рис. 7.30 показана планировка части сборочного цеха завода шлифовальных станков. Сборочный цех размещен в двух пролетах шириной 18 м, оборудованных подвесной кран-балкой на участках узловой сборки и мостовым краном грузоподъемностью 10 т в отделении общего монтажа.
Станины и другие крупные корпусные детали передают из механического цеха в сборочный с использованием электрической рельсовой тележки.
Рис. 7.30. Планировка оборудования и рабочих мест сборочного цеха шлифовальных станков:
1 — радиально-сверлильный станок; 2 — верстаки; 3 — шкаф наладчика; 4 — контрольная плита; 5 — холодильная установка;
6 — сборочные столы; 7 — стеллажи, подставки; 8 — козловой кран; 9 — панельный стенд; 10 — электрическая тележка;
11 — настольно-сверлильный станок на верстаке; 12 — пресс на верстаке; 13 — стенды для испытания гидросистем;
14 — нагревательная установка; 15 — поворотный стеллаж;
16 — моечная машина; 17 — тара; 18 — машина для консервации; 19 — рольганг; 20 — приемоотправочный стол;
21 — многоярусные стеллажи склада; 22 — штабелер
склада готовых деталей
Мелкие и средние детали доставляют на склад готовых деталей с помощью электрокаров в унифицированной таре, оборудованной специальными ложементами для высокоточных деталей (пинолей, шпинделей и др.). При необходимости их моют и консервируют. Хранят детали и комплектующие изделия в ячейках многоярусных стеллажей в таре. Для перемещения деталей по складу используют кран-балку и кран- штабелер; здесь же комплектуют партии деталей и комплектующих изделий перед отправкой их на сборку. Для этого предусмотрены рабочие места с роликовыми конвейерами. Скомплектованные детали и изделия электрокарами или подвесной кран-балкой передают на участки узловой сборки, выполняемой на сборочных столах, верстаках и испытательных стендах. На участках узловой сборки предусмотрен полукозловой кран для передачи собранных узлов на перегрузочную тележку для доставки в пролет общей сборки станков.
Общую сборку осуществляют на панельных стендах, представляющих собой массивные бетонные плиты с закладными металлическими элементами для крепления собираемых станков. Непосредственно на стендах размещены стеллажи-подставки для изделий и сборочного инструмента, а вдоль стендов — верстаки и сборочные столы для предварительной сборки отдельных узлов и механизмов. Установку базовых деталей на сборочные стенды и монтаж крупных узлов осуществляют мостовыми или козловыми кранами, перемещающимися вдоль пролета, а также консольно-поворотными кранами непосредственно у рабочих мест.
На рис. 7.31 показана планировка участка обработки тел вращения с использованием автоматизированной транспортно-складской системы. Проект участка включает 38 станков, в том числе 24 станка с ЧПУ, расположенных в два ряда относительно трассы движения рельсового транспортного манипулятора. Оригинальным является двухуровневое объемно-планировочное решение системы обеспечения функционирования станочных линий. В зоне многоярусного склада 2, обслуживаемого двумя автоматическими штабелерами 1, на первом этаже предусмотрены приемно-отпускная площадка 3 с приводным реверсивным рольгангом и шарнирно-балансирным манипулятором, а также участки мойки 4, контроля 5 и инструментальной подготовки 6 для станков с ЧПУ.
На антресольном этаже на отметке +6,65 расположена контора склада 7, отделение комплектации 8 и помещения для вычислительного комплекса, управляющего автоматизированной транспортно-складской системой.
Передачу тары со склада на участок и обратно осуществляют с помощью передаточных тележек 9 и накопителей тары 10 башенного типа, располагаемых в начале линии. Для этого над проездом на отметке +4,55 расположены рабочие места диспетчеров и комплектовщиков. Передачу заготовок, деталей, приспособлений и инструментов к рабочим местам, на мойку и контроль осуществляют автоматизированной системой через склад. Для этого на каждом участке, примыкающем к складу, предусмотрены приемно-передающие секции. Накопители 10 башенного типа вместимостью 50 ячеек каждый используют как элеваторы для вертикального перемещения в зону первого этажа, а также как межоперационные склады. Вдоль трассы каретки-оператора 13 размещены одноярусные стеллажи-накопители 12. Для загрузки тяжелых заготовок на станок используют шарнирно-балансирные манипуляторы грузоподъемностью 125 и 500 кг.
Для уборки стружки от станков предусмотрены штанговоершовые конвейеры 11.
Двухуровневое решение системы обеспечения функционирования участка дает экономию производственной площади вследствие лучшего использования высоты пролета, а также освобождает проезд от пересечения с трассой рельсовой каретки оператора.
Рис. 7.31. Схема планировки автоматизированного участка обработки тел вращения (план второго этажа уменьшен)
Автоматизированный участок предназначен для изготовления валов, фланцев, шестерен, втулок, оправок, гильз и других деталей станков в мелкосерийном производстве. Годовой выпуск деталей 500 наименований составляет свыше 50 тыс. шт. Детали изготовляют партиями по 20... 100 шт.
Планировка гибкого цеха по производству узлов станков показана на рис. 7.32. Цех включает ГПС обработки деталей, содержащую 52 станка с ЧПУ, отделение сборки и испытания узлов. В цехе обрабатывают детали типа тел вращения, корпусные детали и плиты; осуществляют сборку и испытание узлов. В ГПС изготавливают детали 72 наименований партиями по 65 шт.
Общая площадь цеха составляет около 7800 м2, в том числе
5 200 м2 занимает площадь ГПС механообработки. Здание цеха состоит из шести параллельных и одного поперечного пролетов шириной 12 м.
Автоматизированная транспортно-складская система включает два автоматических склада, расположенных в первом пролете, и транспортную систему из пяти транспортных роботов, управляемых от проложенного в полу цеха высокочастотного кабеля, с устройствами передачи поддонов у рабочих позиций. Склады мелких и средних 1 и крупных 2 заготовок обеспечивают их необходимый запас. По запросам операторов-наладчиков очередная партия заготовок поступает со склада на рабочую позицию. Кольцевые трассы транспортных роботов охватывают все рабочие позиции и зону передачи готовых деталей на сборку. Возле каждой позиции предусмотрены приемные столы для хранения очередной партии заготовок.
В каждом пролете расположены по одному ряду станочных модулей, оснащенных роботами и тактовыми столами для загрузки или магазинами приспособлений-спутников. Установку заготовок на тактовые столы и в приспособления-спутники выполняют операторы-наладчики. ГПС предназначена для работы в три смены, причем в первую смену 25 человек заняты в основном профилактикой и наладкой оборудования на обработку очередной партии, во вторую смену работает 15 человек, а в третью — 5...7 человек.
Во втором пролете размещена линия 3 обработки мелких и средних деталей типа тел вращения, состоящая из семи токарных роботизированных модулей и одного круглошлифовального станка. В третьем пролете находится участок 4 патронной обработки тел вращения, включающий шесть роботизированных модулей на базе станков модели 1720ПФ30 и три модуля на базе станков модели 1740РФЗ. Далее в трех пролетах производится обработка корпусных и плоскостных деталей. На участке 5 установлены восемь ГПМ на базе многоцелевых станков. Далее располагается участок 6, состоящий из девяти роботизированных модулей на базе двух вертикальных станков и робота-манипуля- тора. На последнем участке 7установлены шесть ГПМ на базе станков ИР 500 с магазинами приспособлений-спутников и три пятикоординатных станка.
Обработанные детали в унифицированной таре передают транспортным роботом на площадку 8 и далее на сборочный участок 9, расположенный перпендикулярно направлению пролетов. Далее располагается участок испытаний 10 со стендами для проверки узлов и изделий. В поперечном пролете размещены автоматический склад 12 узлов и комплектующих изделий, а также инструментально-раздаточная кладовая 11. В отдельном помещении 13 находится управляющий вычислительный комплекс, а на каждом участке установлены по два терминала для связи с ним. Для подзарядки аккумуляторных батарей транспортных роботов предусмотрено зарядное устройство 14. Вдоль станочных линий и рабочих мест сборочного отделения расположены трассы подвесных кран-балок, которые наряду с шар- нирно-балансирными манипуляторами используют для подъема и перемещения поддонов с заготовками, а также для установки тяжелых заготовок в приспособления-спутники многоцелевых станков.
В массовом и крупносерийном производствах, для которых характерны поточные линии обработки, принципы прямоточности и минимизации транспортных операций являются определяющими.
Поэтому при компоновке цехов и корпусов линии обработки располагают таким образом, чтобы они заканчивались в том месте конвейера сборки, где в изделие устанавливается данная деталь или сборочная единица. Конвейер общей сборки при этом располагают, как правило, перпендикулярно линиям механической обработки, в конце которых размещают узловую сборку. На рис. 7.33 показан компоновочный план механосборочного корпуса по производству двигателей грузовых автомобилей, рассчитанного на годовой выпуск 200 тыс. шт. Общая площадь корпуса составляет 260 тыс. м2, количество основного производственного оборудования 1177 ед., в том числе 35 AЛ из 327 станков.
Рис. 7.32. Планировка гибкого автоматизированного
цеха по изготовлению узлов станков
Корпус состоит из унифицированных типовых секций с параллельными пролетами шириной 18 м и шагом колонн 12 м. Использован вариант компоновочной схемы со сборочным конвейером в середине здания и линиями обработки, расположенными перпендикулярно конвейеру с обеих сторон. Зона заготовок, доставляемых автотранспортом, размещена вдоль боковых проездов. Поточные линии наиболее трудоемких деталей — блока цилиндров, коленчатого вала, гильзы и головки блока — выполнены зигзагообразными, начало линий находится в зоне проездов, конец — в месте примыкания к сборочному конвейеру.
После основной сборки механизмов двигателя его передают с помощью подвесного конвейера на участок окраски, а затем этим же конвейером — на второй участок сборочного конвейера, где производится окончательная сборка двигателя, включая установку электрооборудования. Собранный двигатель поступает на участок испытания и далее на участок консервации и отправки.
Рис. 7.33. План механосборочного корпуса по производству двигателей грузовых автомобилей
Межоперационная передача в процессе обработки, а также передача с участка на участок осуществляется подвесными конвейерами. В корпусе предусмотрена автоматизированная система транспортирования стружки с участка обработки в отделение для ее переработки. Вспомогательные службы корпуса размещены по его периферии, а также на первом этаже пристройки. Административные и бытовые помещения корпуса находятся на втором и третьем этажах пристройки.
|
|
Индивидуальные очистные сооружения: К классу индивидуальных очистных сооружений относят сооружения, пропускная способность которых...
Механическое удерживание земляных масс: Механическое удерживание земляных масс на склоне обеспечивают контрфорсными сооружениями различных конструкций...
Общие условия выбора системы дренажа: Система дренажа выбирается в зависимости от характера защищаемого...
Индивидуальные и групповые автопоилки: для животных. Схемы и конструкции...
© cyberpedia.su 2017-2024 - Не является автором материалов. Исключительное право сохранено за автором текста.
Если вы не хотите, чтобы данный материал был у нас на сайте, перейдите по ссылке: Нарушение авторских прав. Мы поможем в написании вашей работы!