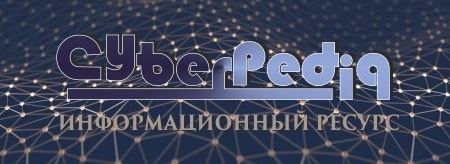
Археология об основании Рима: Новые раскопки проясняют и такой острый дискуссионный вопрос, как дата самого возникновения Рима...
Семя – орган полового размножения и расселения растений: наружи у семян имеется плотный покров – кожура...
Топ:
Комплексной системы оценки состояния охраны труда на производственном объекте (КСОТ-П): Цели и задачи Комплексной системы оценки состояния охраны труда и определению факторов рисков по охране труда...
Проблема типологии научных революций: Глобальные научные революции и типы научной рациональности...
Генеалогическое древо Султанов Османской империи: Османские правители, вначале, будучи еще бейлербеями Анатолии, женились на дочерях византийских императоров...
Интересное:
Влияние предпринимательской среды на эффективное функционирование предприятия: Предпринимательская среда – это совокупность внешних и внутренних факторов, оказывающих влияние на функционирование фирмы...
Отражение на счетах бухгалтерского учета процесса приобретения: Процесс заготовления представляет систему экономических событий, включающих приобретение организацией у поставщиков сырья...
Мероприятия для защиты от морозного пучения грунтов: Инженерная защита от морозного (криогенного) пучения грунтов необходима для легких малоэтажных зданий и других сооружений...
Дисциплины:
![]() |
![]() |
5.00
из
|
Заказать работу |
|
|
Шаг 1: Оценка
Запуск двигателя в регенеративную работу является главным риском во время операции торможения. Что касается этого риска, то вождение автомобиля крутящий момент приводного шкива должен быть неотрицательным. Соответственно,максимальное замедление составляет
(31)
Тогда, исходя из Формулы (20), расчетное время замедления составляет
(32)
В отношении риска разлива материала, вызванного чрезмерным низкая скорость ремня, скорость ремня на хвостовом шкиве должна быть больше, чем 1.7 м/с после операции торможения.
Шаг 2: Расчет
Рис. 9 иллюстрирует результаты исследования работы замедления от 4 м/с до 2 м/с в течение 17 с. Рис.9а представляет собой вождение автомобиля силы, приложенные к приводному шкиву. Схема показана в самом начале в процессе торможения движущая сила постепенно уменьшается с течением времени. Между тем, как натяжение ремня, так и скорость ремня плавно изменяйтесь, см. рис. 9b и d соответственно. Однако диаграмма на фиг. 9а показывает, что в момент времени 11 сек. движущая сила уменьшается до дна 0 кн, и тогда движущие силы теряются. Это явление продолжается около 8 С. Как показано на фиг. 9b к с показывает, пояс натяжение и скорость вдоль конвейера не поддаются контролю во время работы конвейера.этот период. Схема на рис. 9с также ясно показывает что пояс скорость на приводном шкиве не соответствует эталонной скорости. Таким образом, работа замедления от 4 м/с до 2 м/с в течение 17 сек. является неприемлемый.
Кроме внезапной потери движущей силы, торможение также это приводит к проскальзыванию ремня вокруг приводного шкива. Как на диаграмме на рисунке. 9а показывает, что в момент времени 26 сек. движущая сила достигает своего значения предел, а затем происходит проскальзывание ремня. Проскальзывание вызывает неконтролируемую волну ускорения, как показано на фиг. 9c и d. диаграмма в рис. 9c далее показывает, что проскальзывание приводит к неожиданной скорости отклонение, которое длится около 10 секунд.
|
Схема на рис. 9d также показывает большое отклонение скорости во время и после торможения тоже. Самое большое отклонение между приводами а хвостовые шкивы могут быть более 1 м/с. На рисунке далее показано, что момент времени 24 сек., скорость хвостового шкива падает до 0,9 м/с, меньше половины желаемой скорости. Это может привести к утечке материала в сторону от ремень в зоне погрузки.
Таблица 3
Функция нахождения корня с секущим методом. Остановка критерием является |ϵ | < 0,1.
![]() | ![]() | ![]() | ![]() | ![]() | ![]() | |
1 | 41 | 71 | 55.01 | 5.0930 | -5.8101 | -1.6228 |
2 | 71 | 55.01 | 48.81 | -5.8101 | -1.6228 | 0.8562 |
3 | 55.01 | 48.81 | 50.95 | -1.6228 | 0.8562 | -0.0732 |
Шаг 3: Оптимизация
Из результатов обследования Рис. 9, несколько рисков, таких как толчок двигателя в генеративную операцию, наблюдаются в замедление активности от 4 м/с до 2 м/с в течение 17 сек. эти неожиданные риски должны быть предотвращены при здоровой работе замедления. При учете рисков, показанных на рис. 9, проблема нахождения требуемое минимальное время торможения можно определить как:
(33)
в котором
корень функции
относительно к риску проскальзывания ремня безопасности
корень функции
относительно риск перевода двигателя в режим регенерации
корень функции
относительно риск разлива материала, вызванного чрезмерно низким скорость ленты.
Секущий метод также используется для нахождения корня функций ,
и
. Затем, сравнивая эти корни, он дает следующие результаты: требуемое минимальное время торможения для работы торможения от 4 м/с до 2 м / с при приемлемых динамических характеристиках.Важно отметить, что для реализации секущего метода, значения движущих сил должны быть не менее 49,5 кН или менее 0 кН.
|
Сначала мы попытаемся найти корень функции . Начальная точка установлены значения 17 и 47, а критерий остановки равен |ϵ | < 0.1. Корень есть подходим после четырехкратных итераций и в таблице 4 представлены следующие результаты: результат поиска корня. Данные таблицы 4 показывают, что минимальный время торможения составляет 30,37 сек по отношению к риску проскальзывания ремня.
Данные в таблице 4 также включают значения функций и
в точке Т3. Он показывает, когда используется время замедления 30,37 С, то минимальная движущая сила при торможении значительно превышает 0 кн. Поэтому активность нахождения корня из
может быть отмененный. Однако это также показывает, что все еще существует риск утечки материала, Когда
= 30,37. Таким образом, корневое нахождение функции
Рис. 8. Динамика ленточного конвейера в режиме разгона от 2 м/с до 4 м / с в течение 51 с. (а) движущие силы, действующие на приводной шкив. b) натяжение ремня в каждой узловой точке. c) скорость ремня на приводном шкиве. d) скорость ленты в каждой узловой точке вдоль маршрута транспортировки.
должно быть выполнено. Данные во второй строке далее показывают, что корень функции
больше, чем 35.2. А потом в самом корень нахождения функции
, начальные точки установлены в 35.2 и 47. После того, как три раза итераций, корень 35.44 успешно нашли с помощью секущего метода. В таблице 5 подробно описан корень нахождения
. Наконец, получается требуемое минимальное время торможения, которое равняется 35.44 сек. Если мы продолжим обход корня до ближайшего целого числа что не меньше, чем корень, минимальное время замедления этого время замедления составляет около 36 сек.
Рис. 10 представлены динамические характеристики ленточного конвейера во время работы торможения от 4 м/с до 2 м/с в течение 36 с. На рисунке показано во время и после выполнения 36 секунд’ работа замедления, величина движущих сил всегда остается неизменно положительный, но ниже предела трения. Между тем, оба натяжения ремня
Рис. 9. Динамическое поведение ленточного конвейера при замедлении от 4 м/с до 2 м/с в течение 17 сек. (a) движущие силы, действующие на приводной шкив. b) натяжение ремня в каждой узловой точке. c) скорость ремня на приводном шкиве. d) скорость ленты в каждой узловой точке вдоль маршрута транспортировки.
|
Таблица 4
Функция нахождения корня с секущим методом. Остановка критерием является |ϵ| < 0,1. Также даны значения функций
и
![]() | ![]() | ![]() | ![]() | ![]() | ![]() | |
1 | 17 | 47 | 35.2 | -6.4518 | 12.0559 | -0.0109 |
2 | 47 | 35.2 | 25.23 | 8.0495 | 1.5833 | -0.6066 |
3 | 35.2 | 25.23 | 30.76 | -0.6148 | 7.9286 | -0.2487 |
4 | 25.23 | 30.76 | 30.37 | -0.0479 | 7.5258 | -0.2719 |
Таблица 5
Функция нахождения корня с помощью секущего метода. Остановка критерием является |ϵ| < 0,01. Также приведены значения функций
и
.
![]() | ![]() | ![]() | ![]() | ![]() | ![]() | |
1 | 35.2 | 47 | 35.78 | -7.1217 | 12.5364 | 0.0163 |
2 | 47 | 35.78 | 34.83 | -6.0124 | 11.7427 | -0.0288 |
3 | 35.78 | 34.83 | 35.44 | -6.7318 | 12.2563 | 0.0005 |
и скорость ленты вдоль маршрута транспортировки плавно меняется.По-видимому, эта операция замедления вполне приемлема.
В случае ленточных конвейеров с переменной скоростью подачи материала,ожидается, что скорость ремня будет точно отрегулирована в соответствии с изменения массового расхода. Однако, как предполагают Панг и Лодевейкс [14],регулировка скорости должна осуществляться дискретно, чтобы предотвратить непрерывное высокое напряжение. В терминах исследуемого ленточного конвейера предполагается, что что выбранные скорости составляют 2 м/с, 2,5 м/с, 3 м/с, 3,5 м/с, 4 м/ с, 4,5 м/с, 5 м /с и 5,2 м/с. используя метод ЭКО, больше исследований проводятся работы по нахождению минимального времени регулировки скорости для различных переходных режимов работы. Результаты оптимизированной настройки время, включая операции ускорения и замедления, проиллюстрировано на рис. 11. Эти результаты могут быть непосредственно использованы в будущем применение регулирования скорости движения в условиях исследуемого ленточного конвейера.
5. Заключение и рекомендации
В данной работе предложен метод ЭКО для обеспечения здорового переходного процесса эксплуатация длинномерных и высокопроизводительных ленточных конвейеров на обработка сыпучих твердых материалов. Метод ЭКО был использован для расчета требуемого минимального времени регулировки скорости для различных видов транспорта. переходные операции, как при ускорении, так и при замедлении. Основываясь на результатах вычислительного моделирования, можно сделать следующие выводы из этого можно сделать определенные выводы:
|
* Динамические характеристики конвейера сложны, особенно в случай длинного и высокопроизводительного ленточного конвейера система. Для расчета можно использовать метод конечных элементов динамика конвейера в переходных режимах работы при быстродействии контроль.
• Метод ЭКО может быть использован для определения востребованных минимальное время регулировки, принимая оба риска в переходном процессе деятельность и динамика транспортера под управлением скорости в счет.
* Секущий метод повышает эффективность нахождения минимального времени регулировки скорости.
• Метод ЭКО обеспечивает здоровые переходные операции и улучшает применимость контроля скорости.
Кроме того, некоторые важные рекомендации на будущее исследования формулируются следующим образом:
* Оптимизация конструкции ленточного конвейера. По результатам моделирования ясно видно, что в терминах исследуемого ленточный транспортер, явление скольжения ленты вокруг приводной шкив может происходить чаще, чем другие потенциальные риски.
Поэтому в будущем при проектировании ленточных конвейерных систем необходимо масса гравитационного приемного устройства должна быть оптимизирована таким образом, чтобы (1) уменьшите риск смещения ленты для того чтобы сделать ленточный транспортер система более здоровая; (2) уменьшите коэффициент трения пояса конвейерные системы для получения более высокой энергоэффективности.
* Частота переходных операций и величина переходного процесса запас прочности. Если нагрузка остается постоянной при длительных операциях или она умеренно изменяется в промежутках между длительными операциями, скорость конвейера фиксируется в определенный промежуток времени, несмотря на то, что небольших и / или временных изменений в потоке материала. В
Рис. 10. Динамика ленточного конвейера в режиме замедления от 4 м/с до 2 м/с в течение 36 с. (а) движущие силы, действующие на приводной шкив. b) натяжение ремня в каждой узловой точке. c) скорость ремня на приводном шкиве. (d) скорость ленты в каждой узловой точке вдоль маршрута транспортировки.
Рис. 11. Минимальное время регулировки скорости для различных диапазонов регулировки скорости. (a) Минимальное время разгона. b) минимальное время замедления.
в таких случаях частота переходных операций очень мала.Однако в случаях с умеренно изменяющейся степенью нагрузки в промежутках между кратковременными операциями, если учесть изменение материального потока во времени, количество переходных процессов увеличивается,операции значительно увеличат и скорость регулировки так будет чаще. В этих случаях повышается переходная безопасность фактор предложен для того чтобы остаться транспортером здоровым. Так что внутри будущие исследования, взаимосвязь между частотой возникновения переходные операции и значение коэффициента безопасности переходного процесса должны быть изучены. Кроме того, экономия энергии должна быть оцененным в течение различного количества циклов стресса, вызванных переходные операции.
|
Список литературы
[1] F.V. Hetzel, Belt Conveyors and Belt Elevators, J. Wiley and Sons. 1922.
[2] Y. Pang, Intelligent Belt Conveyor Monitoring and Control, Netherlands TRAIL Research School, Delft, the Netherlands, 2010.978-90-5584-134-9.
[3] G. Lodewijks, Two decades dynamics of belt conveyor systems, Bulk Solids Handl. 22 (2) (2002) 124–132. ISSN 0173-9980.
[4] A.J.G. Nuttall, Design Aspects of Multiple Driven Belt Conveyors, TU Delft, Delft University of Technology. 2007.(Ph.D. thesis).
[5] D. Clénet, Optimising Energy Efficiency of Conveyors, 2010, http://www2. schneider-electric.com/documents/original-equipment-manufacturers/pdf/ Energy-efficiency-of-conveyors.pdf.
[6] J. Hiltermann, Reducing the Electrical Power Consumption of Troughed Belt Conveyor by Speed Control, Delft University of Technology, Delft, the Netherlands, 2008.Masters Thesis.
[7] K. Goto, K. Yogo, T. Higashii, A review of efficiency penalty in a coalfired power plant with post-combustion CO2 capture, Appl. Energy 111 (2013) 710–720. ISSN 0306-2619. http://www.sciencedirect.com/science/article/pii/ S0306261913004212.
[8] International Energy Agency, CO2 emissions from fuel combustion highlight, 2015, https://www.iea.org/publications/freepublications/publication/ CO2EmissionsFromFuelCombustionHighlights2015.pdf. (France).
[9] German Institute for Standardization, Continuous Conveyors-Belt Conveyors for Loose Bulk Materials-Basis for Calculation and Dimensioning, German Institute for Standardization, Germany, 2015.Standard DIN 22101.
[10] W. Daus, S. Koerber, N. Becker, Raw coal loading and belt conveyor system at Nochten Opencast Mine- a new conveying and loading system based on drives controlled and adjusted by frequency converter, Braunkohle 50 (2) (1998) 117–130. ISSN 1431-2719.
[11] J. Hiltermann, G. Lodewijks, D.L. Schott, J.C. Rijsenbrij, J.A.J.M. Dekkers, Y. Pang, A methodology to predict power savings of troughed belt conveyors by speed control, Part. Sci. Technol. 29 (1) (2011) 14–27. ISSN 0272-6351.
[12] S. Zhang, X. Xia, A New Energy Calculation Model of Belt Conveyor, IEEE. 2009, 1–6. 1-4244-3918-3.
[13] International Organization for Standardization, Continuous Mechanical Handling Equipment- Belt Conveyors with Carrying Idlers- Calculation of Operating Power and Tensile Forces, International Organization for Standardization, Switzerland, 1989.standard ISO 5048:1989 (E).
[14] Y. Pang, G. Lodewijks, Improving Energy Efficiency in Material Transport Systems by Fuzzy Speed Control, IEEE. 2011, 159–164. 1-4577-1842-1.
[15] L. Ristic, M. Bebic, D. Jevtic, I. Mihailovic, S. Statkic, N. Rasic, B. Jeftenic, Fuzzy Speed Control of Belt Conveyor System to Improve Energy Efficiency, IEEE. 2012.(DS2a. 9–1–DS2a. 9–7). 1-4673-1970-8.
[16] P. Kulinowski, Dynamic start-up calculations for belt conveyors with measured torque curves of fluid couplings, Proceedings of the Thirteenth International Symposium on Mine Planning and Equipment Selection, Taylor Francis Group, Wroclaw, Poland, 2004, pp. 443–448. (ISBN 04 15535 9376).
[17] A. Nuttall, G. Lodewijks, Dynamics of multiple drive belt conveyor systems, Part. Part. Syst. Charact. 24 (4–5) (2007) 365–369. ISSN 1521-4117.
[18] L. Chen, Research on control theory of belt conveyor, Appl. Mech. Mater. 63 (2011) 209–213. ISSN 3037851376.
[19] G. Li, D. Li, R. Li, Simulation and analysis during conveyor stop process based on AMESim, Adv. Mater. Res. 97 (2010) 570–573. (ISSN 0878492801).
[20] G. Lodewijks, Non-linear dynamics of belt conveyor systems, Bulk Solids Handl. 17 (1) (1997) 57–68. ISSN 0173-9980.
[21] D. He, Y. Pang, G. Lodewijks, Speed control of belt conveyors during transient operation, Powder Technol. 301 (2016) 622–631. ISSN 0032-5910.
[22] G. Lodewijks, Y. Pang, The application of flywheels on belt conveyors, Beltcon 17 (2013) 1–10.
[23] L. Nordell, Improving Belt Conveyor Efficiencies: Power, Strength and Life, 1998, http://www.ckit.co.za/secure/conveyor/papers/troughed/improving/ improving.htm.
[24] M.L. Euler, Remarques sur l’effect du frottement dans l’equilibre, Mem. Acad. Sci. 18 (1762) 265–278.
[25] F. Entelwein, Handbuch der statik Fester korper.., G. Reimer. 1832.
[26] P. Nel, G. Shortt, Controlling belt slip, Bulk Solids Handl. 19 (4) (1999) 481–486. ISSN 0173-9980.
[27] Conveyor Equipment Manufacturers Association, Belt Conveyors for Bulk Materials, 6th edn ed., CEMA. 2005.1-891171-18-6.
[28] E.J. Wiedenbrug, Overheating Electric Motors: A Major Cause of Failure, 2003, http://www.maintenancetechnology.com/2003/04/overheating-electricmotors-a-major-cause-of-failure/.
[29] U. Mirza, Determining Causes for Electric Motor Failure, 2013, http:// www.brighthubengineering.com/commercial-electrical-applications/78579- determining-causes-for-electric-motor-failure/.
[30] A. Emadi, Energy-efficient Electric Motors, 3 edn ed., CRC Press, Chicago, 2004.0-8247-5735-1.
[31] A. Harrison, Criteria for minimising transient stress in conveyor belts, Mech. Eng. Trans. 8 (3) (1983) 129–134.
[32] G. Lodewijks, D. Kruse, The power of field measurements-part I, Bulk Solids Handl. 18 (1998) 415–428. ISSN 0173-9980.
[33] G. Lodewijks, Dynamics of belt systems, TU Delft, Delft University of Technology, Delft, the Netherlands, 1996.(Doctoral thesis).
[34] W.H. Press, B.P. Flannery, S.A. Teukolsky, W.T. Vetterling, P.B. Kramer, Numerical Recipes: The Art of Scientific Computing, Second Edn ed., Press Syndicate of the University of Cambridge. 1987.0-521-43064-X.
[35] G.M. Phillips, P.J. Taylor, Theory and Applications of Numerical Analysis, Academic Press. 1996.0-12-553560-0.
[36] S. Pal, Numerical Methods: Principles, Analyses, and Algorithms, Oxford University Press. 2009.0-19-569375-2.
[37] G. Lodewijks, Y. Pang, Belt de-tensioning in dips, Beltcon 17, 2013, pp. 1–17. South Africa.
|
|
Организация стока поверхностных вод: Наибольшее количество влаги на земном шаре испаряется с поверхности морей и океанов (88‰)...
Поперечные профили набережных и береговой полосы: На городских территориях берегоукрепление проектируют с учетом технических и экономических требований, но особое значение придают эстетическим...
Адаптации растений и животных к жизни в горах: Большое значение для жизни организмов в горах имеют степень расчленения, крутизна и экспозиционные различия склонов...
Типы сооружений для обработки осадков: Септиками называются сооружения, в которых одновременно происходят осветление сточной жидкости...
© cyberpedia.su 2017-2024 - Не является автором материалов. Исключительное право сохранено за автором текста.
Если вы не хотите, чтобы данный материал был у нас на сайте, перейдите по ссылке: Нарушение авторских прав. Мы поможем в написании вашей работы!