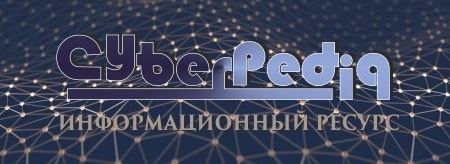
Индивидуальные и групповые автопоилки: для животных. Схемы и конструкции...
История создания датчика движения: Первый прибор для обнаружения движения был изобретен немецким физиком Генрихом Герцем...
Топ:
Особенности труда и отдыха в условиях низких температур: К работам при низких температурах на открытом воздухе и в не отапливаемых помещениях допускаются лица не моложе 18 лет, прошедшие...
Комплексной системы оценки состояния охраны труда на производственном объекте (КСОТ-П): Цели и задачи Комплексной системы оценки состояния охраны труда и определению факторов рисков по охране труда...
Выпускная квалификационная работа: Основная часть ВКР, как правило, состоит из двух-трех глав, каждая из которых, в свою очередь...
Интересное:
Распространение рака на другие отдаленные от желудка органы: Характерных симптомов рака желудка не существует. Выраженные симптомы появляются, когда опухоль...
Национальное богатство страны и его составляющие: для оценки элементов национального богатства используются...
Мероприятия для защиты от морозного пучения грунтов: Инженерная защита от морозного (криогенного) пучения грунтов необходима для легких малоэтажных зданий и других сооружений...
Дисциплины:
![]() |
![]() |
5.00
из
|
Заказать работу |
|
|
Операция 010 и 015 Токарно-фрезерная с ЧПУ применяется патрон трехкулачковый Ø80 мм.
Операция 035 Круглошлифовальная применяется центр гладкий, центр вращающийся.
Вывод: использование данных приспособлений позволит уменьшить вспомогательное время на установку и снятие детали или заготовки и обеспечит требуемую точность обработки.
1.4.4 Обоснование выбора режущих и вспомогательных инструментов
При выборе режущего инструмента его конструкции и размеров значительную роль играет метод обработки свойства обрабатываемого материала, требуемая точность обработки и качество обработанной поверхности твердость режущего инструмента должна превышать твердость обрабатываемого материала. Твердость режущего инструмента должна превышать твердость обрабатываемого материала. При выборе режущего инструмента необходимо принимать стандартный инструмент, но иногда целесообразно следует применить специальный, комбинированный фасонный инструмент, позволяющий совмещать обработку нескольких поверхностей. Наиболее оправданным в данном случае представляется выбор цельно твердосплавного инструмента, либо инструмента, оснащенного твердым сплавом, т.к. именно твердый сплав применяют для изготовления режущего инструмента, предназначенного для обработки металлов с высокими скоростями резания.
Правильный выбор режущей части инструмента имеет большое значение для повышения производительности и снижения себестоимости обработки.
При разработке режущего инструмента, его вид, конструкция определяется методами обработки, свойствами обрабатываемого материала, требуемой точностью обработки и качеством обрабатываемой поверхности. При выборе режущего инструмента необходимо стремиться выбирать по возможности стандартный инструмент.
|
Характер производства влияет на выбор режущего инструмента с экономической точки зрения. Следует учитывать, что применение нормализованного инструмента во всех возможных случаях следует признать более желанным, поскольку он всегда дешевле специального.
Тип станка также оказывает влияние на выбор инструмента и приспособлений. Так наличие мощных и точных станков, при работе которых обеспечивается точность, и жесткость крепления обрабатываемой детали позволяет применять более производительный инструмент.
Размер и конфигурация детали влияют на выбор инструмента в отношении его размеров и конструкции, причем к специальной конструкции прибегают при необходимости обработки фасонных или таких поверхностей, обработка которых с помощью нормализованного инструмента экономически нецелесообразна или технически невозможна.
Материал обрабатываемой детали также влияет на выбор режущего инструмента, а точнее на выбор материала из которого он будет изготовлен и на геометрические параметры режущих частей.
Правильной выбор режущей части инструмента имеет большое значение для повышения производительности и снабжения себестоимости обработки.
При выборе режущих инструментов необходимо стремиться к обеспечению наибольшей производительности механической обработки. Это требование можно обеспечить за счет применения в техпроцессе твердосплавного инструмента и инструмента из быстрорежущей стали повышенной производительности.
Операция 010 Токарно-фрезерная с ЧПУ применяются следующий режущий инструмент:
- для подрезки торца и для точения поверхности применяется резец проходной упорный Т15К6 ГОСТ 3882-74: h=16 мм, b=16 мм, f = 20 мм, l1= 100 мм, l4= 32,2 γ=0̊, λS = - 9̊;
- для точения канавки применяется резец канавочный Т15К6 ГОСТ 3882-74: s=2,0 мм, Tmax=4 мм, h=12 мм, b=12 мм, f1=9,9 мм, l1=131,5 мм, l4 =31,5 мм, s1=4,5 мм;
|
- для сверления отверстия применяется сверло спиральное с цилиндрическим хвостовиком Ø10 мм Р6М5 ГОСТ 10902-77: Dc=10 мм, d1=10 мм, LC=39 мм, l1=89 мм, l2=55 мм;
- для растачивания отверстия применяется резец расточной. Материал режущей части Т15К6 ГОСТ 3882-74: Dmin=9,80 мм, d1=7 мм, f=5,25 мм, h=6,3 мм, l1=60 мм, γ=0̊, λS= - 9̊;
- для фрезерования паза применяем дисковую фрезу Р6М5 ГОСТ 10902-77: D = 80 мм, dH7 = 27 мм, H = 18 мм, s = 4 мм, d1= 42 мм, z = 8;
- для нарезания наружной резьбы применяем резец резьбовой Т15К6 ГОСТ 3882-74: Шаг Р = 1,5 мм, l = 16 мм, d=9,525 мм, r=0,08 мм, X=1,2 мм, Y=1,7 мм;
Операция 015 Токарно-фрезерная с ЧПУ применяются следующий режущий инструмент:
- для подрезки торца применяется резец проходной упорный. Материал режущей части Т15К6 ГОСТ 3882-74: h=25 мм, b=16 мм, f=20 мм, l1=100 мм, l4=32,2 γ=0̊, λ= - 9̊;
- для растачивания отверстия применяется резец расточной. Материал режущей части Т15К6 ГОСТ 3882-74: Dmin=9,80 мм, d1=7 мм, f=5,25 мм, h=6,3 мм, l1=60 мм, γ=0̊, λS= - 9̊;
- для растачивания канавки применяется резец фасонный Т15К6 ГОСТ 3882-74: s=3,0 мм,Tmax =3 мм, Dmin = 16 мм, f = 11 мм, l4 = 29,4 мм,l21 = 149,4 мм;
- для нарезания внутренней резьбы применяем резец резьбовой Т15К6 ГОСТ 3882-74: Шаг Р = 1,5 мм, l = 11 мм, d = 6,35 мм, r = 0,05 мм, X = 0,8 мм, Y = 0,9 мм;
- для фрезерования шестигранника применяем концевую фрезу Т15К6 ГОСТ 10902-77: Dc = 10 мм, LC= 22 мм, l1=72 мм, l4 = 32 мм, d1 = 10 мм, z = 4;
- для растачивания фаски применяется резец расточной. Материал режущей части Т15К6 ГОСТ 3882-74: Dmin=9,80 мм, d1=7 мм, f=5,25 мм, h=6,3 мм, l1=60 мм, γ=0̊, λS= - 9̊;
Операция 035 Круглошлифовальная применяем режущий инструмент:
- для шлифования наружной поверхности применяем шлифовальный круг тип 1 150х16х32 25А F46 L 6 V 35м/с Б 3
Тип 1 – прямого профиля (ПП);
25А – электрокорунд;
F46 – зернистость, средний размер зерна - 370 мкм;
L – твердость (среднемягкий);
6 – структура (средняя);
V – связка керамическая;
35 м/с – рабочая скорость;
Б – класс точности (для менее ответственных операций);
3 – класс неуравновешенности.
Вспомогательным инструментом к токарным станкам являются пластины резцовые (подкладки) предназначенные для установки резцов по высоте относительно центра заготовки. Пластины выполняются согласно нормали МН 2509-88 различной толщины в пределах от 1 до 5 мм, длиной 200 мм и шириной 40 мм.
1.4.5 Обоснование выбора измерительных инструментов, приборов, приспособлений
При проектировании технологического процесса механической обработки заготовки для межоперационного и окончательного контроля обрабатываемых поверхностей необходимо использовать стандартный измерительный инструмент, учитывая тип производство. Метод контроля должен способствовать повышению производительности труда и снижать ее себестоимость. В среднесерийном производстве рекомендуется применять предельные калибры (скобы, пробки, шаблоны и т.п.) и методы активного контроля, которые получили широкое
|
распространение во многих отраслях машиностроения.
Проверку детали на отсутствие заусенцев, забоин, грязи и стружки можно осуществить визуально с помощью стандартной лупы четырехкратного увеличения ЛП-1 ГОСТ 25796-2013. Такая лупа обеспечивает заданный уровень производительности и точность контрольной операции.
Проверку заданной рабочим чертежом твердости целесообразно проводить применительно к нескольким деталям из партии твердомером Роквелла.
Для контроля радиусов скругления R0,1, R0,3, R0,5, применяем шаблоны радиусные набор №1.
На операцию 010 Токарно-фрезерная с ЧПУ используются: ШЦ-I-125-0,1; калибр – скоба Ø18,6h8 ПР-НЕ; фаскомер 1,5±0,1х45º±1º; калибр - пробка Ø10H9 ПР-НЕ, фаскомер 0,5±0,1х30º±1º; шаблон на профиль 3,8H12+0,12; калибр - кольцо резьбовое М18х1,5-6g
На операцию 015 Токарно-фрезерная с ЧПУ используются: ШЦ-I-125-0,1; калибр - пробка Ø12,5H7 ПР-НЕ; индикаторные ножницы Ø14,5 фаскомер 45º; калибр - пробка резьбовая М14х1,5-6Н; фаскомер 1±0,1х30º±1º; фаскомер 1,5±0,1х45º±1º
На операцию 035 Круглошлифовальная используются: МК 25-0,01
1.5 Определение операционных припусков и операционных размеров табличным методом (на одну основную поверхность)
Этот метод определения припусков и операционных размеров состоит в том, что по ГОСТ выбирает общий припуск на обработку поверхности, а затем по таблице соответствующих видов обработки устанавливаются размеры промежуточных припусков и определяются промежуточные размеры заготовки.
Расчет операционных припусков и операционных размеров табличным методом на размер Ø
Прежде чем выбрать из таблиц необходимые припуски, наметим технологический маршрут обработки:
|
1) заготовительная операция (прокат);
2) точение черновое;
3) точение получистовое;
4) точение чистовое;
5) шлифование чистовое.
Для удобства определения промежуточных припусков, перед их расчетом, исходные и расчетные данные по каждой операции на конкретную обрабатываемую поверхность в технологической последовательности заносят в таблицу.
Таблица 11 – Расчет припусков, допусков и операционных размеров по технологическим операциям на поверхность размером Ø мм
Наименование операции | Точн. обраб. | Шерох. | Наим. значен. 2Zi min, мкм | Допуск, δ, мкм | Расчет разм., мм | Предельный размер, мм | Предельный припуск, мкм | ||
Di max | Di min | 2Zi max | 2Zi min | ||||||
Заготовка – прокат | h14 | 12,5 | - | 1300 | 19,632 | 21,343 | 20,043 | - | - |
Точение черновое | h11 | 6,3 | 795 | 210 | 18,842 | 19,253 | 19,043 | 2090 | 790 |
Точение получистовое | h9 | 3,2 | 246 | 130 | 18,596 | 18,803 | 18,673 | 450 | 240 |
Точение чистовое | h8 | 1,6 | 124 | 52 | 18,471 | 18,543 | 18,491 | 260 | 130 |
Шлифование чистовое | f7 | 0,8 | 12,6 | 21 | 18,458 | 18,48 | 18,459 | 63 | 11 |
Промежуточные размеры определяют методом сложения (для вавла) значений припусков по максимальным и минимальным значениям, начиная действия с размеров детали.
Минимальные промежуточные размеры определяем по формуле:
Dmin i-1 = Dmax i + 2Zmin i (2) [7, с. 62]
где Dmin i – предельные размеры поверхностей по операциям (переходам), мм;
2Zmin i – предельные (округленные) в сторону увеличения согласно степени точности припуски на операцию (переход), мм.
Dmin5 = 18,459 мм
Dmin4 = Dmax5 + 2Zmin5 = 18,48 + 0,011 = 18,491 мм
Dmin3 = Dmax4 + 2Zmin4 = 18,543 + 0,13 = 18,673 мм
Dmin2 = Dmax3 + 2Zmin3 = 18,803 + 0,24 = 19,043 мм
Dmin1 = Dmax2 + 2Zmin2 = 19,253 + 0,79 = 20,043 мм
Максимальные промежуточные размеры по каждому переходу определим по формуле:
Dmax i = Dmin i + δ i (3) [7, с. 62]
где Dmin i - предельные размеры поверхностей по операциям, мм;
δD в – допуск на размер на выполняемом переходе, мкм.
Dmax5 = 18,48 мм
Dmax4 = Dmin4 + δ 4 = 18,491 + 0,052 = 18,543 мм
Dmax3 = Dmin3 + δ 3 = 18,673 + 0,13 = 18,803 мм
Dmax2 = Dmin2 + δ 2 = 19,043 + 0,21 = 19,253 мм
Dmax1 = Dmin1 + δ 1 = 20,043 + 1,3 = 21,343 мм
Максимальный припуск на обработку поверхности детали определим по формуле:
2Zi max = 2Zi min + δп (4) [7, с. 59]
где δп - допуск на размер на предыдущем переходе, мкм.
2Zmaх5 = 2Zmin5 + δ4 = 11 + 52 = 63 мкм
2Zmaх4 = 2Zmin4 + δ3 = 130 + 130 = 260 мкм
2Zmaх3 = 2Zmin3 + δ2 = 240 + 210 = 450 мкм
2Zmaх2 = 2Zmin2 + δ1 = 790 + 1300 = 2090 мкм
Рисунок 11 - Расположение полей допусков и промежуточных размеров для операций и переходов обработки поверхности Ø мм
1.6 Разработать с комментариями: - УП при ручном программировании
Программа на операцию 010 Токарно-фрезерная с ЧПУ:
G54 | Система координат станка |
G90 | Абсолютная система отсчета, |
G53 G0 X50 Z50 | Ускоренное перемещение к исходной точке в системе координат детали |
M3 S2100 | Запуск вращения шпинделя по часовой стрелке, с частотой 2100 мин-1 |
G95 | Подача в мм/об |
T1 01; резец подрезной | Выбор инструмента - позиция 1 |
G04 X2 | Пауза в 2 секунды |
G0 X17,5 Z0 | Ускоренное перемещение к точке 1 |
G1 G42 F1 D01 | Рабочий ход, снимаемый припуск 1мм, перемещение к точке 2 |
X2 | Перемещение к точке 3 |
G0 Z5 | Ускоренное перемещение к точке 4 |
G40 | Отмена коррекции радиуса |
G53 X50 Z50 | Ускоренное перемещение к исходной точке в системе координат детали |
S3000 | Вращение шпинделя 3000 мин-1 |
T2 02; резец расточной | Выбор инструмента - позиция 2 |
G90 G94 | Абсолютная система отсчета, подача в мм/об |
G04 X2 | Пауза в 2 секунды |
G0 X6,25 Z5 | Ускоренное перемещение к точке 1 |
G1 Z-13 F0,5 | Рабочий ход, снимаемый припуск 0,5 мм, перемещение к точке 2 |
X6 | Перемещение к точке 3 |
Z5 | Перемещение к точке 4 |
G53 G0 X50 Z50 | Ускоренное перемещение к исходной точке в системе координат детали |
S2630 | Вращение шпинделя 2630 мин-1 |
T3 03; резец канавочный | Выбор инструмента - позиция 3 |
G04 X2 | Пауза в 2 секунды |
G0 X-5 Z5 | Ускоренное перемещение к точке 1 |
G1 Z-11,5 | Рабочий ход, перемещение к точке 2 |
X-6,75 | Перемещение к точке 3 |
X-5 | Перемещение к точке 4 |
Z5 | Перемещение к точке 5 |
G53 G0 X50 Z50 | Ускоренное перемещение к исходной точке в системе координат детали |
S295 | Вращение шпинделя 2630 мин-1 |
G95 | Скорость подачи мм |
T4 04; резец резьбовой | Выбор инструмента - позиция 4 |
G0 X7 Z5 | Ускоренное перемещение к точке 1 |
G33 Z-10 F1,5 D3 H0,92 | Цикл многопроходного точения 3 раза, перемещение к точке 2, шаг резьбы 1,5 высота профиля 0,95 |
G0 Z5 | Ускоренное перемещение к точке 3 |
G53 X50 Z50 | Ускоренное перемещение к исходной точке в системе координат детали |
F1800 | Вращение инструмента 1800 мин-1 |
T5 05 фреза d10 | Выбор инструмента - позиция 5 |
G0 G43 X19,5 Y-10,5 Z-7 Н5 | Ускоренное перемещение к точке 1, подвод к точке безопасности с учетом коррекции длины инструмента |
M98 P9960 | Вызов подпрограммы «о9901» |
G68 X0 Y0 R60 | Выполнение смещения координатных осей на 60° |
M98 P9960 | Вызов подпрограммы «о9901» |
G68 X0 Y0 R120 | Выполнение смещения координатных осей на 120° |
M98 P9960 | Вызов подпрограммы «о9901» |
G68 X0 Y0 R180 | Выполнение смещения координатных осей на 180° |
M98 P9960 | Вызов подпрограммы «о9901» |
G68 X0 Y0 R240 | Выполнение смещения координатных осей на 240° |
M98 P9960 | Вызов подпрограммы «о9901» |
G68 X0 Y0 R300 | Выполнение смещения координатных осей на 300° |
M98 P9960 | Вызов подпрограммы «о9901» |
G69 | Отмена смещения координатных осей |
G53 G0 X50 Z50 | Ускоренное перемещение к исходной точке в системе координат детали |
S3000 | Вращение шпинделя 3000 мин-1 |
G95 | Скорость подачи мм/об |
T2 02 резец расточной | Выбор инструмента - позиция 2 |
G4 X2 | Пауза в 2 секунды |
G0 X-12,7 Z5 | Ускоренное перемещение к точке 1 |
G1 X5 Z-2,7 | Рабочий ход, перемещение к точке 2 |
Z-13 | Перемещение к точке 3 |
X6 | Перемещение к точке 4 |
Z-13 | Перемещение к точке 5 |
X-4 Z16,5 | Перемещение к точке 6 |
X-12,7 Z5 | Перемещение к точке 4 |
G53 G0 X50 Z50 | Ускоренное перемещение к исходной точке в системе координат детали |
M5 | Останов шпинделя |
M30 | Конец программы |
o9960 подпрограмма 9960 | Имя подпрограммы |
G1 X14,5 | Рабочий ход, прямолинейное перемещение |
Y10,5 | Перемещение к точке |
X19,5 | Перемещение к точке |
|
1.7 Определение режимов резания и технических норм времени
Расчеты режимов резания на операцию 010 Токарно-фрезерная с ЧПУ. Обработка ведется на токарном станке с ЧПУ CL-253B.
Для 4, 5 и 6 переходов:
1. Выбор режущего инструмента
В качестве режущего инструмента принимаются:
1) Сверло спиральное с цилиндрическим хвостовиком Ø10 мм Р6М5;
2) Резец расточной Т15К6;
3) Дисковая фреза Ø 80 Р6М5
2. Назначение режимов резания
Глубина резания: t1= 49 мм; t2= 0,5 мм; t3= 8,5 мм
3. Определение длины рабочего хода (по карте наладки)
Lрх1 = 54+5=59мм
Lрх2 = 7 + 54 + 2 + 59 = 122 мм
Lрх3 = 5 + 11,3 + 5 = 21,3 мм
4. Назначение подачи суппорта на оборот шпинделя
Сверление – II группа подач
So1 = 0,15 мм/об | [3, с.70] |
So2 = 0,3 мм/об | [3, с.15] |
So = Sz ∙ z Sz = 0,07 So3 = 0,07 ∙ 8 = 0,56 мм/об | [3, с.44] [3, с.48] |
5. Определение стойкости инструмента
Тр = Тм · λ, (5) [3, с.17]
где Тр - стойкость;
Тм - нормированная стойкость инструмента;
λ - коэффициент времени резания;
Тм1 = 20 | [3, с.69] |
Тм2 = 30 | [3, с.17] |
Тм3 = 110 | [3, с.51] |
λ = , (6) [3, с.18]
λ1 = = 83 = 1
λ2 = = 0,4
λ3 = = 0,53
λ>0,7, значит она не учитывается.
Тр1 = Тм = 20 мин
Тр2 = 30 ∙ 0,4 = 12 мин
Тр3 = 110 ∙ 0,53 = 58,3 мин
6. Расчет скорости резания
υ= υтабл · K1 · K2 · K3, (7) [3, с.19]
где υтабл - скорость по таблице;
К1, К2, К3 - коэффициенты, зависящие от марки и твердости обрабатываемого материала, группы твердого сплава и стойкости инструмента;
υтабл1 = 17 м/мин | [3, с.73] |
υтабл2 = 175 м/мин | [3, с.19] |
υтабл3 = 36 м/мин | [3, с.56] |
K1(1) = 1,05 | [3, с.73] |
K1(2) = 1,15 | [3, с.20] |
K1(3) = 1,15 | [3, с.57] |
K2(1) = 1 | [3, с.21] |
K2(2) = 1 | [3, с.56] |
K2(3) = 1 | [3, с.58] |
K3(1) = 1,35 | [3, с.74] |
K3(2) = 1,4 | [3, с.21] |
υ1 = 17 · 1,05 · 1 · 1,35 = 24,1 м/мин
υ2 = 175 · 1,15 · 1 · 1,4 = 281,75 м/мин
υ3 = 36 · 1,15 · 1 · 0.87 = 36,02 м/мин
7. Частота вращения шпинделя
n = , (8) [3, с.12]
где υ – скорость резания;
D – диаметр обрабатываемой поверхности;
n1 = = 767,52 мин -1
n2 = = 8157,21 мин -1
n3 = = 9140,1 мин -1
Корректировка по паспорту станка:
nп1 = 750 мин -1
Допускается превышение расчетного значения до 5%.
8. Определение действительной скорости резания
υд = , (9) [3, с.30]
где nп - n паспортное;
D – диаметр обрабатываемой поверхности.
υд2 = = 103,62 м/мин
υд3 = = 753,6 м/мин
9. Проверочные расчеты:
9.1. По осевой силе резания
Ро = Ро.табл. ∙ Кр | (10)[3, с.81] |
где Ро.табл. – осевая сила резания по таблице, кН; Кр – коэф. Зависящий от обрабатываемого материала Ро.табл. = 2,8кН Кр = 0,95 Ро1 = 2,8 ∙ 0,95 = 2,66 | [3, с.81] [3, с.81] |
Pz = Pz табл · t где Pz табл - глубина составляющая силы резания по таблице, кН t – глубина резания, мм Pz табл = 0,7 кН Pz2 = 0,7 ∙ 0,5 = 0,35кН | (11) [3,с.26] [3, с.26] |
Процесс резания осуществим.
9.2. По мощности резания
Nр = Nр. табл. · КN · (12) [3, c. 82]
где, Nр. табл. – мощность резания по таблице, кВт;
Кн – коэф. зависящий от обрабатываемого материала;
n – частота вращения, об/мин;
𝜈 – скорость резания, м/мин.
Nр. табл. = 0,9 кВт
КN = 0,95
Np1 = 0,9 ∙ 0,95 ∙ ![]() ![]() ![]() | [3, c. 82] [3, c. 83]
(13)[3, c. 27]
(14)[3, с.64] | ||
Q = где, t – глубина резания; В – ширина фрезерования; Sм – минутная подача Q = Np3 = 60 ∙ 0,95 = 57 кВт | (15)[3, с.65] | ||
Мощность на шпинделе:
N = 1,2 · Nдв · η, где Nдв – номинальная мощность электродвигателя, кВт η – КПД станка | (16)[3, с.421] |
1,2 · 18,5 · 0,8 = 17,76 кВт
1,2 · Nдв · η ≥ Nр
Процесс резания осуществим.
10. Расчет основного машинного времени
Т0 = , (17) [3, c. 13]
Т01 = = 0,52 мин
Т02 = = 0,14 мин
Т03 = = 0,01 мин
Таблица 12 – Расчеты режимов резания на остальные переходы операции 010
Наименование (код) инструмента и материал режущей части | № пере хода | Расчетные параметры | |||||||
t,мм | So мм/об | Tм, мин | V, м/мин | nп, мин-1 | Sм, мм/ мин | Lрх, мм | To, мин | ||
1 | 2 | 3 | 4 | 5 | 6 | 7 | 8 | 9 | 10 |
Продолжение таблицы 12
1 | 2 | 3 | 4 | 5 | 6 | 7 | 8 | 9 | 10 |
Резец проходной упорный Т15К6 | 1 | 0,4 | 30 | 227,7 | 3000 | 1200 | 147 | 0,12 | |
Резец проходной упорный Т15К6 | 2 | 0,5 | 0,4 | 18 | 246,7 | 3000 | 1200 | 22 | 0,018 |
Резец канавочный Т15К6 | 3 | 1,45 | 0,3 | 6 | 144,9 | 2930 | 879 | 6,45 | 0,007 |
Определение основного времени на операции 010:
Тобщ. = 0,52 + 0,14 + 0,01 + 0,12 + 0,018 + 0,007 = 0,815 мин
Определяется расчетная норма времени (мин) на обработку одной детали
, (19) [15, c. 5]
где Тшт – норма штучного времени, мин;
время автоматической работы станка;
вспомогательное время;
К – время на обслуживание рабочего места, отдых и личные потребности, задается в процентах от оперативного времени
, (20) [15, c. 5]
где общее основное время;
вспомогательное автоматическое время
, (21) [15, c. 6]
где расстояние ускоренного перемещения по оси Х;
расстояние ускоренного перемещения по оси Z;
ускоренное перемещение по оси X;
ускоренное перемещение по оси Z;
время смены инструмента.
мин;
мин
(22) [16, c. 5]
Вспомогательное время Тв.пер, связанное с операцией включает [15, карта 14]:
- установить заданное положение детали и инструмента 0,32 мин
- проверить приход инструмента в заданную точку после обработки (7 инструментов) 0,15 мин
- установить и снять щиток от забрызгивания эмульсией 0,03 мин.
Тв.оп. = 0,32 + 0,15 + 0,03=0,5 мин
Время на установку и снятие детали вручную Тв.уст., мин [15, карта 6]:
Тв.уст. = 0,16 мин
Время на контрольное измерения Тв.изм., мин [15, карта 15]:
Тв. контр.изм. = 0,07 + 0,06 + 0,07 + 0,18 = 0,38 мин
мин
Подготовительно-заключительное время Тпз включает в себя: [14,с.96-97]
- получить наряд, чертеж, технологическую документацию, программоноситель, режущий и вспомогательный инструмент, контрольно-измерительный инструмент, приспособление, заготовки исполнителем до начала и сдать их после окончания обработки партии деталей на рабочем месте - 4 мин;
- ознакомиться с работой, чертежом, тех.документацией, осмотреть заготовки - 2 мин;
- инструктаж мастера - 2 мин;
- установить исходные режимы станка - 0,15 мин;
- установить и снять патрон 3х кулачковый - 2,5 мин;
- время на пробную обработку детали – 3,55х1,15= 4,08 мин.
- установить исходные координаты X, Y, Z - 2,0 мин.
Тпз= 8+0,15+2,5+2,0+4,08= 16,73 мин.
Для токарных патронно-центровых станков принимают К=7% [15, карта 16]
мин
Расчеты режимов резания на операцию 015 Токарная с ЧПУ. Обработка
ведется на токарном станке с ЧПУ CL-253B.
Для 3, 4, и 5 переходов:
1. Выбор режущего инструмента
В качестве режущего инструмента принимаются:
1) Фасонный резец Т15К6;
2) Резец резьбовой Т15К6;
3) Фреза концевая Ø10 Т15К6
2. Назначение режимов резания
Глубина резания: t1= 1,75 мм; t2= 0,95 мм; t3= 2,5 мм
3. Определение длины рабочего хода (по карте наладки)
Lрх1 = 16,5+1,75=18,25мм
Lрх2 = 5 + 10 + 15 = 30 мм
Lрх2 = 5 + 21 + 21,5 = 47,5 мм
Режимы обработки резьб
Р = 1,5 h = 0,812 мм t = 0,92 мм i = 6 | [3, с.96] [3, с.96] [3, с.96] |
4. Определение стойкости инструмента по формуле (5) (6):
Тм1 = 30
Тм3 = 40
![]() Общие условия выбора системы дренажа: Система дренажа выбирается в зависимости от характера защищаемого... ![]() Механическое удерживание земляных масс: Механическое удерживание земляных масс на склоне обеспечивают контрфорсными сооружениями различных конструкций... ![]() Историки об Елизавете Петровне: Елизавета попала между двумя встречными культурными течениями, воспитывалась среди новых европейских веяний и преданий... ![]() Поперечные профили набережных и береговой полосы: На городских территориях берегоукрепление проектируют с учетом технических и экономических требований, но особое значение придают эстетическим... © cyberpedia.su 2017-2024 - Не является автором материалов. Исключительное право сохранено за автором текста. |