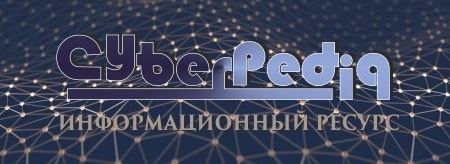
Индивидуальные и групповые автопоилки: для животных. Схемы и конструкции...
Автоматическое растормаживание колес: Тормозные устройства колес предназначены для уменьшения длины пробега и улучшения маневрирования ВС при...
Топ:
Выпускная квалификационная работа: Основная часть ВКР, как правило, состоит из двух-трех глав, каждая из которых, в свою очередь...
Характеристика АТП и сварочно-жестяницкого участка: Транспорт в настоящее время является одной из важнейших отраслей народного...
Устройство и оснащение процедурного кабинета: Решающая роль в обеспечении правильного лечения пациентов отводится процедурной медсестре...
Интересное:
Берегоукрепление оползневых склонов: На прибрежных склонах основной причиной развития оползневых процессов является подмыв водами рек естественных склонов...
Аура как энергетическое поле: многослойную ауру человека можно представить себе подобным...
Финансовый рынок и его значение в управлении денежными потоками на современном этапе: любому предприятию для расширения производства и увеличения прибыли нужны...
Дисциплины:
![]() |
![]() |
5.00
из
|
Заказать работу |
|
|
Введение
Тема дипломного проекта: «Разработка технологического процесса изготовления детали «АК04.05.23 Гильза».
Цель проекта – усовершенствование маршрута обработки детали «АК04.05.23 Гильза».
Данный дипломный проект включает в себя следующие документы:
1. Расчетно-пояснительная записка;
2. Комплект технологических документов;
3. Графические документы.
Расчетно-пояснительная записка содержит следующие части: технологическую, организационную, экономическую и реальную.
В технологической части подробно рассматривается проектируемый технологический процесс: произведен выбор производства, анализ заводского техпроцесса, выбор метода получения заготовки, выбор технологических баз, произведен выбор оборудования, приспособлений, режущих и мерительных инструментов, произведен расчет операционных припусков и операционных размеров на наружную цилиндрическую поверхность диаметром 18,5f7 табличным методом, рассчитаны режимы резания и техническая норма времени на операцию 010 и 015 Токарно-фрезерная с ЧПУ и разработана управляющая программа на операцию 015.
В организационной части рассмотрена оптимизация рабочего места по системе 5S, разработан стандарт безопасности рабочего места.
В экономической части произведена калькуляция себестоимости детали.
В реальной части спроектирован и изготовлен стенд на тему: «Виды механической обработки; достижимая шероховатость и точность»
В комплекте технологической документации представлены маршрутные и операционные карты на измененный технологический процесс и управляющая программа на операцию 010 Токарная с ЧПУ.
Графические документы включают в себя рабочий чертеж детали, карты наладки на операции 010 Токарно-фрезерная с ЧПУ и 015 Токарно-фрезерная с ЧПУ.
|
Глава1. Технологическая часть
1.1 Назначение и описание условий работы детали, технические требования при изготовлении, материал и его характеристика, термообработка и ее режимы, выбор и обоснование типа производства
Данная деталь «АК04.05.23 Гильза» устанавливается в рулевом гидроприводе и служит для перемещения под давлением жидкости и подачи сигнала на электромагнитный датчик.
Технические требования при изготовлении:
1. Твердость HRC ≥56. Группа контроля 4 ОСТ 1 00021-78. Допускается наличие окисной плёнки жёлтых и золотистых тонов, кроме поверхностей Д, Д1, Д2 и Д3.
2. H14; h14; ±IT/2.
3. Трещины не допускаются.
4. Взаимное расположение 2-х отв. Ø1,5Н14, 4-х отв. Ø1,5Н14 и 4 пазов шириной 2 мм – произвольное.
5. * - Размеры обеспечить инструментом.
6. *1 – Допуск биения указан для среднего диаметра резьбы.
Деталь «АК04.05.23 Гильза» изготавливается из стали 95Х18-б ТУ 14-1-377-72.
Сталь 95Х18-б ТУ 14-1-377-72 – жаропрочная коррозионностойкая сталь применяется для деталей ответственного назначения, от которых требуется повышенная твердость, работающая под действием больших давлений.
Использование в промышленности: втулки, оси, стержни, шариковые и роликовые подшипники в другие детали, к которым предъявляются требования высокой твердости и износостойкости и работающие при температуре до 500 °С или подвергающиеся действию умеренных агрессивных сред.
Марка материала | Si | Mn | Ni | S | Ti | C | P | Cr |
95Х18-б | 0,8 | 0,8 | 0,6 | 0,025 | 0,2 | 0,9-1,0 | 0,030 | 17-19 |
Таблица 1 - Химический состав стали 95Х18-б ТУ 14-1-377-72
Таблица 2 - Механические свойства стали 95Х18-б ТУ 14-1-377-72
Сортамент | Размер | σ0,2 | σв | δ5 | ψ | КСU |
- | мм | МПа | МПа | % | % | кДЖ/м2 |
прокат | 420 | 770 | 15 | 30 | - |
где σ0,2 - предел пропорциональности, Мпа
σв - предел кратковременной прочности, Мпа
Ψ- относительное сужение,%
δ5 - относительное удлинение при разрыве, %
|
КСU- ударная вязкость, кДж / м2
Таблица 3 - Физические свойства стали 95Х18-б ТУ 14-1-377-72
Т | Е10-5 | а 106 | I | r | С |
Град | МПа | 1/Град | Вт/(м·град) | кг/м3 | (Дж/кг·град) |
20 | 2,04 | 11,8 | 24 | 7800 | 483 |
где T - температура, при которой получены данные свойства, Град
Е10-5 - модуль упругости первого рода, Мпа
а 106 - коэффициент температурного расширения, 1/Град
I - коэффициент теплопроводности, Вт/(м·град)
r - плотность материала, кг/м3
С - удельная теплоемкость материала, Дж/(кг·град)
Термообработка и ее режимы
Термической обработкой называется совокупность операций нагрева, выдержки и охлаждения твёрдых металлических сплавов с целью получения заданных свойств за счёт изменения внутреннего строения и структуры. Тепловая обработка используется либо в качестве промежуточной операции для улучшения обрабатываемости давлением, резанием, либо как окончательная операция технологического процесса, обеспечивающая заданный уровень свойств изделия.
Таблица 4 – Режимы термообработки
Вид ТО | Температура, °С | Время выдержки | Охлаждающая среда |
Закалка | 850-950 | 0,35 | Масло |
Выбор и обоснование типа производства
Для того чтобы определить тип производства необходимо вычислить массу детали. Определяем массу с помощью программы КОМПАС-3D V14.
Масса детали составляет 10 г.
Рисунок 1- Модель детали «АК04.05.23 Гильза»
Таблица 5 - Определения типа производства
Масса детали, кг | Тип производства | ||||
Единичное | Мелко-серийное | Средне-серийное | Крупно-серийное | Массовое | |
<1,0 | <10 | 10-2000 | 1500-100000 | 75000-200000 | 200000 |
1,0-2,5 | <10 | 10-1000 | 1000-50000 | 50000-100000 | 100000 |
2,5-5,0 | <10 | 10-500 | 500-35000 | 35000-75000 | 75000 |
5,0-10 | <10 | 10-300 | 300-25000 | 25000-50000 | 50000 |
>10 | <10 | 10-200 | 200-10000 | 10000-25000 | 25000 |
По заданию годовая программа выпуска деталей составляет 4000 штук. Исходя из данных таблицы 5 принимаем тип производства - среднесерийное.
Среднесерийное производство характеризуется ограниченной номенклатурой изделий, изготовляемых периодически повторяющимися партиями, и сравнительно большим объемом выпуска, в сравнении с единичным производством.
В среднесерийном типе производства используется универсальное, специализированное и частично специальное оборудование. Широко используются станки с ЧПУ, обрабатывающие центры и находят применение гибкие автоматизированные системы станков с ЧПУ.
|
Технологическая оснастка в основном универсальная. Большое распространение имеет универсально-сборная, переналаживаемая и специальная технологическая оснастка, позволяющая существенно повысить коэффициент оснащенности серийного производства.
В качестве исходной заготовки используется горячий и холодный прокат, литье в землю и под давлением, точное литье, поковки и точные штамповки и прессовки.
Требуемая точность достигается как методами автоматического получения размеров, так и методами пробных ходов и промеров с частичным применением разметки.
Средняя квалификация рабочих выше, чем в массовом производстве, но ниже чем в единичном.
В среднесерийном производстве технологический процесс изготовления изделия дифференцирован, то есть расчленен на отдельные самостоятельные операции, выполняемые на определенных станках.
1.2 Обоснование и выбор метода получения заготовки, определение общих припусков на заготовку, ее размеров и коэффициента использования материала (КИМ)
Необходимость экономии материальных ресурсов предъявляет высокие требования к рациональному выбору заготовок, к уровню их технологичности, в значительной мере определяющей затраты на технологическую подготовку производства, себестоимость, надежность и долговечность изделий.
Правильно выбрать способ получения заготовки – означает определить рациональный технологический процесс ее получения с учетом материала детали, требований к точности её изготовления, технических условий, эксплуатационных характеристик и серийности выпуска.
Машиностроение располагает большим количеством способов получения деталей. Это многообразие, с одной стороны, позволяет существенно повысить эксплуатационные характеристики машин за счет использования свойств исходного материала, с другой – создаёт трудности при выборе рационального, экономичного способа получения детали.
Особенно важно правильно выбрать вид заготовки, назначить наиболее рациональный технологический процесс её изготовления в условиях автоматизированного производства, когда размеры детали при механической обработке получаются «автоматически» на предварительно настроенных агрегатных станках или станках с числовым программным управлением (ЧПУ). В этом случае недостаточные припуски также вредны, как и излишние, а неравномерная твердость материала или большие уклоны на заготовке могут вызвать значительные колебания в допусках размеров готовой детали.
|
Поэтому очень важен экономически и технологически обоснованный выбор вида заготовки для данного производства.
Максимальное приближение геометрических форм и размеров заготовки для данного производства.
Заданные конструктором геометрия, размеры и марка материала детали во многом определяют технологию изготовления. Таким образом, выбор вида заготовки происходит в процессе конструирования, т.к. при расчете детали на прочность, износостойкость и ли при учете других показателей эксплуатационных характеристик конструктор исходит из физико-механических свойств, применяемого материала с учетом влияния способа получения заготовки. В машиностроении основными видами заготовок для деталей являются стальные и чугунные отливки, отливки из цветных металлов цветных металлов и сплавов, штамповки и всевозможные профили проката. Способ получения заготовок должен быть наиболее экономичным при заданном объеме выпуска деталей. На выбор формы, размеров и способа получения заготовки большое влияние оказывает конструкция и материал детали. Вид заготовки влияет на характер технологического процесса, трудоемкость и экономичность ее обработки.
При выборе вида заготовки необходимо учитывать не только эксплуатационные условия работы детали, ее размера, форму, но и экономичность ее производства. Так же необходимо обратить внимание на свойство материала детали: хорошо ли деформируется, можно ли сваривать и т.д.
Для получения заготовок из стали 95Х18-б ТУ 14-1-377-72 рассмотрим следующие методы:
1. Отливка
2. Прокат (из прутка);
3. Обработка давлением (поковка)
1. Литье. Используется для изготовления крупных корпусных заготовок, отливок в виде тел вращения, переходников, рукояток, шестерен, втулок, плит и так далее. Однако изготовление форм требует больших затрат времени.
В данном случае этот метод не подходит, так как сталь 95Х18 ГОСТ 5632-2014 не является литейной.
2. Прокат. Используется для получения: листового проката; сортового проката (прутки квадратного, круглого, шестигранного, прямоугольного сечения, уголок, швеллер, тавр, двутавр, рельс); специального вида проката (штучные заготовки – колеса, кольца, шары).
Рисунок 2 - Модель заготовки (Прокат)
Определяем коэффициент использования материала:
КИМ = (5) [6, с.23]
|
где: - масса детали, кг
- масса заготовки, кг
Для проката:
КИМ = =0,16
3. Штамповка – более производительный процесс. Штампованная деталь приобретает форму более близкую к форме детали. Осуществляется в штампах. Оборудование – кривошипные прессы, горизонтально-ковочные машины. Характерно для серийного и массового производств.
Горячая штамповка выполняется по двум схемам: в открытых и закрытых штампах. При штамповке в открытых штампах получаются более точные штампованные заготовки, меньше расходуют материал; производительность высокая при пониженной стойкости штампов и ограниченности форм штамповок (круглые, типа шестерен, фланцев, стаканов).
Штамповка в открытых штампах характеризуется тем, что полость штампа в процесс деформирования остается открытой. Зазор между подвижной и неподвижной частями штампа постоянный и небольшой. Устройство таких штампов зависит от типа машины, на которой штампуют. Открытый штамп имеет две взаимно перпендикулярные плоскости разъема.
Метод не подходит для данной детали, так как заготовка почти не будет отличаться от проката.
Вывод: рассмотрев три метода получения заготовки, можно сделать вывод, что наиболее рациональным методом получения заготовки в данном случае прокат, так как деталь не обладает сложным профилем, тем самым не требует изготовления штампов.
1.3 Проектирование вариантов маршрута техпроцесса
1.3.1 Формирование двух маршрутов обработки заготовки и выбор оптимального варианта
Таблица 6 – Сравнение двух маршрутов обработки детали «АК04.05.23 Гильза»
№ операции | 1-й вариант | 2-й вариант |
1 | 2 | 3 |
005 | Заготовительная: Заготовка – прокат Ø14х42 | Заготовительная: Заготовка – прокат Ø14х42 |
Продолжение таблицы 6
1 | 2 | 3 |
010 | Токарная с ЧПУ: Оборудование: NL-1500 1) подрезать торец, снимая припуск 4 мм и точить поверхность, выдерживая размер ∅10; 2) сверлить отв. ∅3,8 на проход; 3) точить 6 канавок, выдерживая размеры 3,5; 6,7; 10,6; 14; 2,5; 1,8; ∅9; ∅7,8; 4) сверлить 2 отв. ∅1,5; 5) сверлить 4 отв. ∅1,5; 6) расточить отв. ∅6 на длину 3; 7) фрезеровать 4 паза шириной 2 на глубину 1,5. | Токарная с ЧПУ:
Оборудование: NL-1500
Установ А:
1) подрезать торец, снимая припуск 4 мм и точить поверхность, выдерживая размер ∅10;
2) сверлить отв. ∅3,8 на проход;
3) точить 6 канавок, выдерживая размеры 3,5; 6,7; 10,6; 14; 2,5; 1,8; ∅9; ∅7,8;
4) сверлить 2 отв. ∅1,5;
5) сверлить 4 отв. ∅1,5;
6) расточить отв. ∅6 на длину 3;
7) фрезеровать 4 паза шириной 2 на глубину 1,5.
Установ Б:
1) подрезать торец в размер 35 и точить наружную поверхность детали, выдерживая размер ![]() ![]() ![]() |
Продолжение таблицы 6
1 | 2 | 3 |
4) нарезать резьбу М8х0,5 – 6Н на глубину 7 мм. | ||
015 | Токарная: Оборудование: ИЖ250 снять заусенцы по кромкам детали, острые кромки притупить R0,3. | Токарная: Оборудование: ИЖ250 снять заусенцы по кромкам детали, острые кромки притупить R0,3. |
020 | Слесарная: Оборудование: верстак снять заусенцы по кромкам 6 отв. ∅1,5, а также 4 пазам 2 мм. | Слесарная: Оборудование: верстак снять заусенцы по кромкам 6 отв. ∅1,5, а также 4 пазам 2 мм. |
025 | Токарная с ЧПУ:
Оборудование: NL-1500
1) подрезать торец в размер 35 и точить наружную поверхность детали, выдерживая размер ![]() ![]() ![]() | Термическая: Оборудование: печь Р85SZ 1) закалить деталь; 2) отпустить деталь до твёрдости ≥ 56 HRC. |
030 | Токарная: Оборудование: ИЖ250 снять заусенцы по кромкам детали, острые кромки притупить R0,3. | Внутришлифовальная: Оборудование: 3А228 шлифовать отв., выдерживая размер ∅4+0,08 |
Продолжение таблицы 6
1 | 2 | 3 |
035 | Термическая: Оборудование: печь Р85SZ 1) закалить деталь; 2) отпустить деталь до твёрдости ≥ 56 HRC. | Промывочная: Оборудование: ванна Промыть деталь |
040 | Внутришлифовальная: Оборудование: 3А228 шлифовать отв., выдерживая размер ∅4+0,08 | Контрольная: Оборудование: стол БТК Проверить деталь на соответствие чертежу и отсутствие трещин |
045 | Промывочная: Оборудование: ванна Промыть деталь | |
050 | Контрольная: Оборудование: стол БТК Проверить деталь на соответствие чертежу и отсутствие трещин |
Вывод: в проекте предлагается применить второй вариант технологического процесса, так как такой технологический процесс обеспечивает повышение производительности труда за счет концентрации операций на высокопроизводительном оборудовании с числовым программным управлением. Обработка детали с минимальным количеством переустановок от одних и тех же технологических баз позволяет повысить точность обработки, уменьшить количество необходимого оборудования, оснастки и рабочей силы.
1.3.2 Выбор технологических баз
Выбор технологических баз — это ответственный этап проектирования технологического процесса обработки резанием. Выбор баз связан с построением маршрута обработки заготовки. При выборе баз нужно представлять общий (укрупненный) план обработки заготовки, который на последующих этапах подвергается дальнейшей детализации и уточнению. Исходными данными при выборе баз являются рабочий чертеж детали, чертеж заготовки, технические условия на изготовление детали и заготовки.
При выборе технологических баз следует стремиться к более полному соблюдению принципа единства баз. В этом случае погрешности базирования равны нулю и точность обработки повышается. При невозможности выдержать данный принцип (например, из-за недостаточной устойчивости установки при малых размерах измерительной базы) за технологическую базу принимают другую поверхность, стремясь уменьшить нежелательные последствия не совмещения баз.
Выполнение принципа постоянства баз способствует повышению точности взаимного положения поверхностей детали. Высокая точность по концентричности расположения поверхностей вращения обеспечивается путем использования на разных операциях обработки (или переходах) одной и той же технологической базы. Лучший результат при этом обеспечивается выполнением всех переходов за одну установку и одно закрепление обрабатываемой заготовки. При нескольких установках на одну и ту же базу точность взаимного расположения поверхностей снижается.
Для того, чтобы погрешность базирования была равна нулю, необходимо, чтобы измерительная и конструкторская базы совпадали.
Для операции 010 Токарно-фрезерная с ЧПУ Установ А базовой поверхностью является наружная цилиндрическая поверхность. Деталь устанавливается в цанговый патрон.
Рисунок 6 - Схема базирования на операцию 010 Установ А
Для операции 010 Токарно-фрезерная с ЧПУ Установ Б базовой поверхностью является наружная цилиндрическая поверхность. Деталь устанавливается в цанговый патрон.
Рисунок 7 - Схема базирования на операцию 010 Установ Б
Для операции 030 Внутришлифовальная базовыми поверхностями являются наружная цилиндрическая поверхность и торцы. Деталь устанавливается в цанговый патрон.
Рисунок 8 - Схема базирования на операцию 035
1.4 Краткая характеристика разработанного технологического процесса
1.4.1 Обоснование принятой последовательности обработки и содержания операций
Обоснование последовательности обработки поверхностей заготовки ведут с учетом конструктивных особенностей детали и требований к ее качеству, состава переходов по обработке поверхностей заготовки и ее базирования в технологическом процессе, необходимости термической обработки, условий организации производственного процесса и других.
В начале технологического процесса с заготовки удаляем наибольшие припуски, что способствует перераспределению остаточных напряжений в материале заготовки.
На последовательность и количество этапов обработки поверхностей заготовки влияет термическая обработка, которая неизбежно приводит к деформации заготовки, поэтому операцию «шлифование» выполняем после термической обработки. В конце технологического процесса выполняют промывку и контроль.
Намеченная последовательность обработки поверхностей заготовки позволяет составить маршрут технологического процесса изготовления детали в виде списка переходов с соблюдением последовательности их выполнения.
Операция 005 Заготовительная
В качестве заготовки используется прокат Ø 14 х 42 мм
Операция 010 Токарно-фрезерная с ЧПУ
Установ А подрезается торец, точится поверхность, выдерживая размер ∅10; сверлится отверстие ∅3,8 на проход; точатся 6 канавок, выдерживая размеры 3,5; 6,7; 10,6; 14; 2,5; 1,8; ∅9; ∅7,8; сверлятся 2 отв. ∅1,5; сверлятся 4 отв. ∅1,5; растачивается отверстие ∅6 на длину 3; фрезеруется 4 паза шириной 2 на глубину 1,5.
Установ Б подрезается торец в размер 35, точится наружная поверхность детали, выдерживая размер 10; растачивается отверстие, выдерживая размеры
7,2; ∅6; 23; 14; ∅7,5; 7; растачивается канавка, выдерживая размеры
8,2; 14; 2; нарезается резьба М8х0,5 – 6Н на длину 7 мм.
Операция 015 Токарная
На данной операции снимаются заусенцы по кромкам детали, острые кромки притупляются R0,3.
Операция 020 Слесарная
На данной операции снимаются заусенцы по кромкам 6 отв. ∅1,5, а также 4 пазам 2 мм.
Операция 025 Термическая
На данной операции деталь закаливается и отпускается деталь до твёрдости ≥ 56 HRC.
Операция 030 Внутришлифовальная
шлифовать отв., выдерживая размер ∅4+0,08Операция 020 Промывочная
Промыть деталь
Операция 025 Контрольная
Контролировать размеры перед термической обработкой
Операция 030 Термическая
Закалить до твердости HRCэ 25…40
Операция 035 Круглошлифовальная
Выполнить шлифование наружной цилиндрической поверхности
Операция 040 Слесарная
Притупить острые кромки согласно чертежу
Операция 045 Гальваническая
На данной операции нужно покрыть деталь Хим. Окс.
Операция 050 Контрольная
Необходимо произвести проверку детали на наличие трещин и соответствие геометрических параметров по чертежу.
1.4.2 Обоснование выбора и технические характеристики выбранного оборудования
Выбор производиться при назначении метода обработки поверхности, обеспечивающим выполнение технических требований к обрабатываемой поверхности.
Выбор станочного оборудования является одной из важнейших задач при разработке технологического процесса механической обработки заготовки. От правильности его выбора зависит производительность изготовления детали, экономическое использование производственных площадей, механизации и автоматизации ручного труда, электроэнергии и в итоге все это сказывается на себестоимости изделия.
При выборе оборудования необходимо учитывать: характер производства, методы достижения точности при обработк, соответствие станка размерам детали, мощность станка, удобство управления и обслуживание станка, габаритные размеры и стоимость станка.
Для операций 010 и 015 Токарно-фрезерная с ЧПУ применяется станок CL-253B. Предназначен для токарной и фрезерной обработки металлических изделий.
Основные факты:
· Компактная и жесткая конструкция станка
· Направляющие скольжения с выдающимися возможностями демпфирования вибраций
· Простота автоматизации (портальный загрузчик, бар-фидер, интерфейс для подключения робота)
· Жесткая конструкция револьверной головки
· Возможность оснащения револьверной головки с приводным инструментом
· Возможность оснащения станка задней бабкой
· Широкий выбор опционального оборудования
Станина станка была сконструирована с оптимальной конфигурацией и расположением ребер жесткости и технологических карманов. Конструкция на стадии проектирования была проанализирована методом конечных элементов (FEM technology).
Преимущества:
· высокая жесткость
· высокое сопротивление кручению
· небольшие габариты
· легкое удаление стружки
· оптимальная конструкция
· низкое тепловое расширение
Станки серии CL могут оснащаться различными шпинделями, которые имеют широкий диапазон частот вращения и сквозных отверстий для прохода прутковой заготовки.
Преимущества:
· высокая надежность
· уменьшенное время ускорения / торможения
· высокая жесткость
· минимальные вибрации в процессе работы
· большое сквозное отверстие
· способность работы длительное время на тяжелых режимах
Станки серии CL в зависимости от модели могут быть оснащены различными типами револьверных головок на 8, 10 и 12 инструментальных позиций, как с приводным инструментом, так и без приводного инструмента.
Преимущества:
· минимальный нагрев
· минимальные вибрации
· высокая скорость индексации (0,7 сек. на позицию)
· минимальный шум
· жесткая конструкция
· возможность использовать приводной инструмент
· подача СОЖ на режущую кромку инструмента
· размер хвостовика инструмента до 25х25 мм
Станки серии CL в зависимости от модели также могут оснащаться задней бабкой. Задняя бабка с вращающимся центром, который устанавливается в пиноль с гидравлическим выдвижением, служит поддержкой длинных заготовок и увеличения жесткости системы при обработке.
Прямые абсолютные шкалы обратной связи Magnescale (опционально) для непревзойденной точности позиционирования. Магнитная технология считывания положения, в отличие от оптических типа считывания не боится воздействия внешних агрессивных факторов. Поэтому даже при нарушении защиты система работает. Также магнитные линейки имеют и ряд других преимуществ:
· высокая дискретность 0,01мкм
· устойчивость к воздействию конденсата и масла
· устойчивость к вибрациям и ударам
· большая точность, чем у оптических шкал
· долговечность
Таблица 7 – Технические характеристики токарно-фрезерного станка с ЧПУ CL-253B.
1 | 2 |
ОБРАБАТЫВАЕМЫЕ ГАБАРИТЫ | |
Наибольший диаметр обработки над станиной (мм) | 520 |
Макс. диаметр токарной обработки (мм) | 460 |
Стандартный диаметр токарной обработки (мм) | 217 |
Макс. длина токарной обработки (мм) | 471 |
Наибольший диаметр обрабатываемого прутка (мм) | 89 |
ПЕРЕМЕЩЕНИЕ | |
Перемещение по оси X (мм) | 2600 |
Продолжение таблицы 7
1 | 2 |
Перемещение по оси Y (мм) | 3000 |
Перемещение по оси Z (мм) | 5000 |
ШПИНДЕЛЬ | |
Диапазон скорости вращения шпинделя (об/мин) | 30-3000 |
Тип торца шпинделя | JISA2-8 |
РЕВОЛЬВЕРНАЯ ГОЛОВА | |
Количество инструментальных позиций | 12 |
Размеры хвостовика инструмента (мм) | 25 |
Диаметр хвостовика расточного инструмента (мм) | Max. 50 |
ПОДАЧА | |
Скорость быстрого перемещения (мм/мин) | X:18000, Z: 24000 |
ЗАДНЯЯ БАБКА | |
Перемещение задней бабки (мм) | 260 |
Диаметр пиноли задней бабки (мм) | 85 |
Конусное отверстие в пиноле задней бабки | МТ4 вращающийся центр |
Перемещение пиноли задней бабки (мм) | 120 |
ДВИГАТЕЛЬ | |
Мощность двигателя шпинделя <30 мин/пост> (кВт) | 18.5 |
Двигатель подачи (кВт) | X: 1,5; Z: 3,5 |
ИСТОЧНИКИ ПИТАНИЯ | |
Электропитание <пост> (кВА) | 35,4 |
ЕМКОСТЬ БАКА | |
Емкость бака для СОЖ (л) | 175 |
ГАБАРИТЫ СТАНКА | |
Высота станка ШхТхВ (мм) | 2000х1775х1955 |
Масса станка (кг) | 4100 |
Таблица 16 - Калькуляция полной себестоимости детали
Статьи затрат | Сумма затрат, руб. | Структура, % | |
на одну деталь | на годовую программу | ||
1 Материальные затраты (за вычетом возвратных отходов) | 6,3 | 45990 | 8,35 |
2 Основная заработная плата производственных рабочих | 20,94 | 152862 | 27,75 |
3 Дополнительная заработная плата производственных рабочих | 6,282 | 45858,6 | 8,32 |
4.Страховые взносы во внебюджетные фонды | 8,49 | 61977 | 11,25 |
Итого: технологическая себестоимость | 42,012 | 306687,6 | |
5 Расходы на содержание и эксплуатацию оборудования | 0,48 | 3504 | 0,64 |
6 Цеховые расходы | 7,329 | 53501,7 | 9,71 |
Итого: цеховая себестоимость | 49,821 | 363693,3 | |
7 Общезаводские расходы | 5,65 | 41245 | 7,49 |
Итого: заводская (производственная) себестоимость | 55,417 | 404544,1 | |
8 Внепроизводственные расходы | 20 | 146000 | 26,5 |
Итого: полная себестоимость | 75,471 | 550938,3 | 100 |
4. Реальная часть
4.1 Назначение и цель спроектированного и изготовленного объекта.
Реальная часть представляет собой проектирование и изготовление стенда «Описание подготовительных и вспомогательных функций применяемых при разработке УП».
С помощью программы Компас-3D V16 разработано:
- таблица с G-кодами;
- фон заливки светло-бирюзовый.
С помощью программы «CorelDRAWX8» разработано:
- рамка толщиной 4мм;
- размер стенда 841х1189 мм.
Изображение для стенда распечатано на полноцветной самоклеящийся пленке, которая наклеена на белом пластике с белой окантовкой толщиной 4мм и шириной 35мм.
Данный стенд может быть использован как пример выполнения разработки управляющей программы по дисциплине «Программирование автоматизированного оборудования».
Литература
1. Абрамов Ф.Н. Справочник по обработке материалов резанием, Техника К.: 1983г.
2. Авраменко В. Е., Терсков Ю.Ю., Расчет припусков и межпереходных размеров, Учебное пособ., К.:2008г.
3. Барановский Ю.В. Режимы резания металлов. Справочник - Ниитавпром М.: 1995г.
4. Горбацевич А.Ф. Курсовое проектирование по технологии машиностроения. Мн. Высшая школа 1975г.
5. Данилевский В.В. Технология машиностроения – Высшая школа М.: 1984г.
6. Добрыднев И.С. Курсовое проектирование по предмету технология машиностроение - Машиностроение М.: 1985г.
7. Косилова А.Г., Мещеряков Р.К. Справочник технолога-машиностроителя. В двух томах. Т. 1 - Машиностроение М.: 1986г.
8. Косилова А.Г., Мещеряков Р.К. Справочник технолога-машиностроителя. В двух томах. Т. 2 - Машиностроение М.: 1986г.
9. Нефедов Н.А. Дипломное проектирование; учебное пособие – М. Высш. шк. 1986 г.
10. Пахомов Д.С., Чиненкова Е.Е. Проектирование технологических процессов обработки деталей: учеб. пособие/ Нижегород. гос. техн. ун-т им. Р.Е. Алексеева. – Н. Новгород, 2014. – 170 с.
11. Сорокин В.Г. Марочник сталей и сплавов – Машиностроение М.: 1989г.
12. Тяпкина И.Ф./ Методическое пособие по курсовому проектированию и организационно-экономической части дипломных проектов по дисциплине «Экономика отрасли».
13. Фельдштейн Е.Э. Режущий инструмент: учеб. пособие; - Минск: Новое знание, 2007. – 400 с.
14. Чуваков А.Б., Чиненков Д.В. Основы подготовки и эффективной эксплуатации обрабатывающих станков с ЧПУ, Ниж. Нов.:2014г.
15. Общемашиностроительные нормативы режимов резания. Часть 2.
Введение
Тема дипломного проекта: «Разработка технологического процесса изготовления детали «АК04.05.23 Гильза».
Цель проекта – усовершенствование маршрута обработки детали «АК04.05.23 Гильза».
Данный дипломный проект включает в себя следующие документы:
1. Расчетно-пояснительная записка;
2. Комплект технологических документов;
3. Графические документы.
Расчетно-пояснительная записка содержит следующие части: технологическую, организационную, экономическую и реальную.
В технологической части подробно рассматривается проектируемый технологический процесс: произведен выбор производства, анализ заводского техпроцесса, выбор метода получения заготовки, выбор технологических баз, произведен выбор оборудования, приспособлений, режущих и мерительных инструментов, произведен расчет операционных припусков и операционных размеров на наружную цилиндрическую поверхность диаметром 18,5f7 табличным методом, рассчитаны режимы резания и техническая норма времени на операцию 010 и 015 Токарно-фрезерная с ЧПУ и разработана управляющая программа на операцию 015.
В организационной части рассмотрена оптимизация рабочего места по системе 5S, разработан стандарт безопасности рабочего места.
В экономической части произведена калькуляция себестоимости детали.
В реальной части спроектирован и изготовлен стенд на тему: «Виды механической обработки; достижимая шероховатость и точность»
В комплекте технологической документации представлены маршрутные и операционные карты на измененный технологический процесс и управляющая программа на операцию 010 Токарная с ЧПУ.
Графические документы включают в себя рабочий чертеж детали, карты наладки на операции 010 Токарно-фрезерная с ЧПУ и 015 Токарно-фрезерная с ЧПУ.
Глава1. Технологическая часть
1.1 Назначение и описание условий работы детали, технические требования при изготовлении, материал и его характеристика, термообработка и ее режимы, выбор и обоснование типа производства
Данная деталь «АК04.05.23 Гильза» устанавливается в рулевом гидроприводе и служит для перемещения под давлением жидкости и подачи сигнала на электромагнитный датчик.
Технические требования при изготовлении:
1. Твердость HRC ≥56. Группа контроля 4 ОСТ 1 00021-78. Допускается наличие окисной плёнки жёлтых и золотистых тонов, кроме поверхностей Д, Д1, Д2 и Д3.
2. H14; h14; ±IT/2.
3. Трещины не допускаются.
4. Взаимное расположение 2-х отв. Ø1,5Н14, 4-х отв. Ø1,5Н14 и 4 пазов шириной 2 мм – произвольное.
5. * - Размеры обеспечить инструментом.
6. *1 – Допуск биения указан для среднего диаметра резьбы.
Деталь «АК04.05.23 Гильза» изготавливается из стали 95Х18-б ТУ 14-1-377-72.
Сталь 95Х18-б ТУ 14-1-377-72 – жаропрочная коррозионностойкая сталь применяется для деталей ответственного назначения, от которых требуется повышенная твердость, работающая под действием больших давлений.
Использовани
|
|
Поперечные профили набережных и береговой полосы: На городских территориях берегоукрепление проектируют с учетом технических и экономических требований, но особое значение придают эстетическим...
Особенности сооружения опор в сложных условиях: Сооружение ВЛ в районах с суровыми климатическими и тяжелыми геологическими условиями...
Своеобразие русской архитектуры: Основной материал – дерево – быстрота постройки, но недолговечность и необходимость деления...
История создания датчика движения: Первый прибор для обнаружения движения был изобретен немецким физиком Генрихом Герцем...
© cyberpedia.su 2017-2024 - Не является автором материалов. Исключительное право сохранено за автором текста.
Если вы не хотите, чтобы данный материал был у нас на сайте, перейдите по ссылке: Нарушение авторских прав. Мы поможем в написании вашей работы!