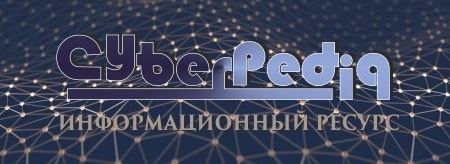
Археология об основании Рима: Новые раскопки проясняют и такой острый дискуссионный вопрос, как дата самого возникновения Рима...
Семя – орган полового размножения и расселения растений: наружи у семян имеется плотный покров – кожура...
Топ:
Оснащения врачебно-сестринской бригады.
Установка замедленного коксования: Чем выше температура и ниже давление, тем место разрыва углеродной цепи всё больше смещается к её концу и значительно возрастает...
Организация стока поверхностных вод: Наибольшее количество влаги на земном шаре испаряется с поверхности морей и океанов...
Интересное:
Распространение рака на другие отдаленные от желудка органы: Характерных симптомов рака желудка не существует. Выраженные симптомы появляются, когда опухоль...
Инженерная защита территорий, зданий и сооружений от опасных геологических процессов: Изучение оползневых явлений, оценка устойчивости склонов и проектирование противооползневых сооружений — актуальнейшие задачи, стоящие перед отечественными...
Что нужно делать при лейкемии: Прежде всего, необходимо выяснить, не страдаете ли вы каким-либо душевным недугом...
Дисциплины:
![]() |
![]() |
5.00
из
|
Заказать работу |
|
|
Источник сварочного тока преобразует высокое сетевое напряжение в существенно более низкое сварочное напряжение и обеспечивает требуемые, для сварки, высокие значения силы тока, которые отсутствуют в сети. Кроме того, он поддерживает и регулирует необходимые значения тока. Для сварки применяется как переменный, так и постоянный ток. Следовательно, источники тока делятся на постоянного и переменного тока.
Назначение и устройство сварочного выпрямителя.
Сварочные выпрямители - это аппараты, преобразующие переменное напряжение сети в постоянное напряжение электросварки. Существует множество схем построения сварочных выпрямителей с различными механизмами формирования выходных параметров тока и напряжения. Используются различные способы регулирования тока и формирования внешней вольт - амперной характеристики выпрямителей.
В наиболее простых аппаратах регулирование тока осуществляется трансформатором, а для его выпрямления используются диоды. Силовая часть таких аппаратов состоит из трансформатора, выпрямительного блока на неуправляемых вентилях и сглаживающего дросселя.
Блок-схема сварочного выпрямителя: T - трансформатор, VD - выпрямительный блок, L - сглаживающий дроссель.
Трансформатор в такой схеме используется для понижения напряжения, формирования необходимой внешней характеристики и регулирования режима.
Однофазные схемы выпрямления переменного напряжения используются в цепях с небольшой потребляемой мощностью. По сравнению с однофазными, трехфазные схемы обеспечивают существенно меньшую пульсацию выпрямленного напряжения. Работа трехфазной мостовой схемы выпрямления Ларионова с использованием диодов, применяемая во многих сварочных выпрямителях, показана на рисунке ниже.
|
Трехфазная мостовая схема выпрямления и диаграмма напряжения
Преимущества и недостатки сварочных выпрямителей по сравнению со сварочными трансформаторами.
Преимущества. Т.к. на выходе получается постоянный ток, он обеспечивает надёжность зажигания и устойчивое горение дуги и как следствие более качественный шов. Возможность сварки не только углеродистой и низколегированной стали, но и нержавеющей стали и цветных металлов при минимальном количестве брызг. Отсутствие вращающихся частей и большую долговечность, высокий КПД и меньшие потери холостого хода, меньшую массу.
Недостатки: потеря части мощности, сильные изменения напряжения в сети при сварке, диоды очень чувствительны к перепадам напряжения.
Горелку (электрододержатель) и заземляющий кабель подключает электрогазосварщик с группой по электробезопасности не ниже II. Источник сварочного тока подключает к сети 380В электротехнический персонал с группой электробезопасности не ниже III.
Назначение и устройство сварочного трансформатора.
Сварочный трансформатор - это устройство, преобразующее переменное напряжение входной сети в переменное напряжение для электросварки. Основным его узлом является силовой трансформатор, с помощью которого сетевое напряжение снижается до напряжения холостого хода (вторичное напряжение), составляющего обычно 50-60В.
Простая для понимания схема сварочного трансформатора имеет следующий вид:
Схема сварочного трансформатора: 1 - трансформатор; 2 - реактор с переменной индуктивностью; 3 - электрод; 4 - свариваемая деталь.
Для ограничения тока короткого замыкания и устойчивого горения дуги трансформатор должен иметь круто падающую внешнюю вольт - амперную характеристику. Для этого либо используют трансформаторы с увеличенным магнитным рассеянием, вследствие чего сопротивление при коротком замыкании оказывается у них в несколько раз больше, чем у обычных силовых трансформаторов. Либо в цепь с трансформатором с нормальным магнитным рассеянием включают реактивную катушку с большим индуктивным сопротивлением - дроссель (дроссель может быть включен не в цепь вторичной обмотки, а в цепь первичной, где меньше ток). Если у дросселя можно изменять индуктивность, регулируя её, изменяют форму внешней вольт - амперной характеристики трансформатора и ток дуги I21 или I22, соответствующий напряжению дуги Uд.
|
Регулирование сварочного тока. Сила тока в сварочных трансформаторах может регулироваться изменением индуктивного сопротивления цепи (амплитудное регулирование с нормальным или увеличенным магнитным рассеянием) или с помощью тиристоров (фазное регулирование).
По типу питающей сети сварочные трансформаторы бывают однофазными и трехфазными. Последние, как правило, могут подключаться и к однофазной сети.
На рисунке ниже представлены однофазный и трехфазный трансформаторы с регулированием тока магнитным шунтом.
Достоинства и недостатки сварочных трансформаторов.
Достоинства: сравнительно высокий КПД (70-90%), простота эксплуатации и ремонта, надежность и дешевизна.
Недостатки: низкая стабильность горения дуги, обусловленная свойствами самого переменного тока (наличие безтоковых пауз при переходе электрического сигнала через ноль). Для качественной сварки необходимо использовать специальные электроды, предназначенные для работы при переменном токе. Отрицательно сказываются на стабильности горения дуги и колебания входного напряжения.
Сварочным трансформатором нельзя сваривать нержавеющую сталь, которая требует постоянного тока, и цветные металлы.
Если мощность сварочного трансформатора достаточно велика, его вес может доставлять определенные трудности при переносе трансформатора с места на место.
Аппаратура для возбуждения и стабилизации дуги при ручной сварке
Для возбуждения и повышения устойчивости горения дуги применяются специальные аппараты(устройства), приспособленные для работы с серийными источниками питания переменного и постоянного тока. Эти аппараты обеспечивают наложение тока высокого напряжения и высокой частоты на сварочную цепь.
Они разделяются на два типа: возбудители непрерывного действия и возбудители импульсного питания.
|
К первым относятся осцилляторы, которые, работая совместно с источниками питания дуги, обеспечивают ее возбуждение наложением на сварочные провода тока высокого напряжения (3000—6000 В) и высокой частоты (150—250 кГц). Такой ток не представляет большой опасности для сварщика при соблюдением правил электробезопасностн, но дает возможность возбуждать дугу, не касаясь электродом изделия. Высокая частота обеспечивает спокойное горение дуги даже при малых сварочных токах основного источника. Электрическая схема осциллятора ОСПЗ-201 приведена на рис. 4.11.
Рис. 4.11, Электрическая схема осциллятора, включенного в сварочную цепь параллельно
Рис, 4.12. Электрическая схема осциллятора последовательного включения
Как видно из схемы 4.11 осциллятор включен в сварочную цепь параллельно цепи переменного тока напряжением 220 В и частотой 50 Гц. Предохранитель Пр обеспечивает безаварийную работу помехозащитного фильтра ПЗ, состоящего из батареи конденсаторов. Высоковольтный низкочастотный трансформатор Т1 повышает напряжение до 6 кВ. На стороне высокого напряжения трансформатора 77 находится высокочастотный искровой генератор, состоящий из разрядника ФВ, конденсатора Сг и первичной обмотки трансформатора высокой частоты и напряжения Т2. Этот генератор является колебательным контуром, в котором беспрерывно,с большой скоростью, накапливаются в конденсаторе и разряжаются через искровой разрядник импульсы тока высокого напряжения, создавая высокочастотную характеристику трансформатора Т2. Для защиты источника от гока высокого напряжения служит фильтр в виде конденсатора Сп, а предохранитель Прч защищает обмотку трансформатора Т2 от пробоев фильтра С„. Осциллятор может питаться не от сети, а непосредственно от сварочной цепи, что улучшает его свойства.
Осцилляторы последовательного включения (рис.4.12) считаются более эффективными, так как не требуют установки в цепи источника специальной защиты от высокого напряжения. Как видно из схемы, катушка LK включена последовательно со сварочной дугой, остальные обозначения схемы аналогичны рис.4.11. При работе осциллятора разрядник издает тихое потрескивание; искровой зазор величиной 1,6—2 мм может быть установлен регулировочным винтом, но только при отключенном от сети осцилляторе. Следует иметь в виду, что установка и ремонт осцилляторов требуют более высокой квалификации электротехнического персонала. При сварке переменным током требуются возбудители с импульсным питанием, которые наряду с первоначальнымвозбуждением дуги должны способствовать ее зажиганию при смене полярности переменного тока. Казалось бы, что осцилляторы отвечают этому требованию. Однако они неудовлетворительно выполняют повторные зажигания при смене полярности переменноготока источника, в результате чего действующий сварочный ток колеблется и ухудшается качествосварки. Кроме того, несинхронизированные осцилляторы создают значительные радиопомехи.
|
Сварочные инверторы
Слово "инвертор" в своем исходном значении означает устройство для преобразования постоянного тока в переменный. На рисунке ниже приведена упрощенная схема сварочного аппарата инверторного типа.
Блок-схема сварочного инвертора: 1 - сетевой выпрямитель, 2 - сетевой фильтр, 3 - преобразователь частоты (инвертор), 4 - трансформатор, 5 - высокочастотный выпрямитель, 6 - блок управления.
Работа сварочного инвертора происходит следующим образом. Переменный ток частотой 50 Гц поступает на сетевой выпрямитель 1. Выпрямленный ток сглаживается фильтром 2 и преобразуется (инвертируется) модулем 3 в переменный ток с частотой в несколько десятков кГц. В настоящее время достигаются частоты в 100 кГц. Именно этот этап является самым важным в работе сварочного инвертора, позволяющим добиться огромных преимуществ по сравнению с другими типами сварочных аппаратов. Далее с помощью трансформатора 4 высокочастотное переменное напряжение понижается до значений холостого хода (50-60В), а токи повышаются до величин, необходимых для осуществления сварки (100-200А). Высокочастотный выпрямитель 5 выпрямляет переменный ток, который совершает свою полезную работу в сварочной дуге. Воздействуя на параметры преобразователя частоты, регулируют режим и формируют внешние характеристики источника.
Процессы перехода тока из одного состояния в другое контролируются блоком управления 6. В современных аппаратах эта работа выполняется транзисторными модулями IGBT, являющимися самыми дорогими элементами сварочного инвертора.
Система управления с помощью обратных связей формирует идеальные выходные характеристики для любого способа электросварки. Благодаря высокой частоте, вес и размеры трансформатора снижаются в разы.
|
По своей функциональности выпускаются инверторы следующих типов:
Сварочный инвертор
Включение в цепь амперметра (последовательно) и вольтметра (параллельно участку цепи) при измерениях.
Подключение нулевого провода. Отдельный проводник, присоединяемый к спец контакту вилки втычного соединения и к корпусу электроприёмника.
Выполнение сварки
Сварщик должен иметь хорошее образование не только в практической области, но и теории, описывающей особенности технологии. Это необходимо для предупреждения ошибок.
Зажигание электрической дуги.
После включения переключателя горелки начинается подача защитного газа, проволочный электрод приходит в движение с установленной скоростью. Одновременно при помощи реле тока к нему подключается электрический ток. При прикосновении к поверхности изделия возникает короткое замыкание. Из-за высокой плотности тока на конце электрода в точке соприкосновения начинается расплавление сварочной проволоки, и происходит зажигание дуги. При высокой скорости подачи еще слабая дуга может быть потушена быстро подаваемой проволокой. Так что зажигание может произойти со второй или третьей попытки. Зажигание дуги необходимо производить на оси сварного шва. Как только дуга начнет гореть стабильно, точки зажигания должна быть расплавлена. От непроваренных точек зажигания могут расходиться трещины из-за высокой скорости остывания этих локально нагретых мест.
Ведение горелки
Горелка наклоняется на 10°-20° в направлении сварки и ведется волочащим или колющим движениями. При слишком сильном наклоне горелки существует опасность не эффективной защиты расплавленного металла.
Расстояние между горелкой и изделием (вылет электрода) должно быть таким, чтобы расстояние между свободным концом электрода (нижней кромкой токоподводящего мундштука) и точкой соприкосновения дуги и изделия составляло примерно 10-12 диаметров проволоки.
Сварка вертикального шва сверху вниз производится, как правило, при сваривании листов толщиной до 4 мм. У более толстых листов существует опасность, что из-за опережающего металла шва возникнут дефекты сцепления. Дефекты сцепления из-за опережающего металла шва могут возникнуть и сварке в других положениях при слишком высокой скорости сварки. Поэтому следует избегать раскачивания горелки с широкой амплитудой. Обычной формой маятникового движения является треугольник.
Окончание сварки.
Нельзя резко тушить дугу в конце шва и убирать горелку от кратера. В первую очередь при сваривании толстых листов, где в наплавленных валиках большого объема могут возникнуть глубокие кратеры, рекомендуется медленно отводить дугу от ванны или, если позволяет установка, задать программу заполнения кратера.
У большинства установок можно задать также определенное время, в течение которого подача газа еще будет продолжаться, чтобы последний, еще жидкий, металл шва застывал в среде защитного газа. Но это будет действовать только в том случае, если горелка еще некоторое время будет находиться в конце шва.
Все сварочное оборудование оснащено синергетической системой управления сварочным процессом.
Синергетическое управление позволяет сварщику сосредоточиться исключительно на ведении шва, не требуя применения специальной техники сварки при смене пространственных положений, колебаниях вылета электрода и других изменениях условий сварки. Процесс настройки источника под выполнение конкретной операции заключается в выборе необходимой синергетической программы на панели механизма подачи и задания требуемой скорости подачи проволоки.
Используя адаптивное управление, системы с синергетикой поддерживают постоянные условия сварки даже при значительных вылетах электрода при сварке труднодоступных участков шва. Система в прямом смысле жонглирует многочисленными переменными сварочного процесса, одновременно подстраивая сам процесс так, чтобы дуга всегда наилучшим образом соответствовала сварке в настоящий момент времени. Даже значительные колебания состава свариваемых материалов, зазора и положения сварочной горелки легко и автоматически компенсируются изменением эпюры сварочного тока.
Система синергетического управления позволяет не только выбирать уже имеющиеся программы, но и вводить новые-как разработанные компанией Lincoln Electric, так и собственные. Ввод программ осуществляется с помощью персонального компьютера.
Благодаря синергетике стало возможным широкое внедрение передового процесса импульсного переноса металла при сварке проволокой, ранее доступного лишь наиболее квалифицированным сварщикам.
С П Е Ц Т Е Х Н О Л О Г И Я
Подготовка металла под сварку.
При подготовке деталей под сварку поступающий металл подвергается очистке, правке, разметке, наметке, резке, подготовке кромок под сварку, холодной или горячей гибке.
Основной металл перед сваркой должен быть тщательно осмотрен, очищены от ржавчины, масла, влаги, окалины и др. на расстоянии не менее 10 мм от оси шва или края разделки кромок.
Зачистка наружных дефектов может быть удалены путём пологой вырубки или абразивным инструментом. Наличие указанных загрязнений приводит к образованию в сварных швах пор, трещин, шлаковых включений, что приводит к снижению прочности и плотности сварного соединения.
Металл, имеющий искривления и деформации более допускаемых стандартами должен быть предварительно выправлен.
Прихватки должны быть очищены от шлака и брызг металла.
На кромках, полученных термической резкой, механическим способом должен быть удалён слой металла на глубину 0,8 мм.
Для обеспечения сквозного проплавления и получения сварного шва по всей толщине соединяемых деталей, их кромки должны быть подготовлены под сварку. Основные виды подготовки кромок и обозначение их конструктивных элементов изображены на рис. 1.
Рис. 1. Виды подготовки кромок под сварку
а — с отбортовкой кромок; б, и, к — без скоса кромок; в—со скосом одной кромки; г — со скосом двух кромок; д — с двухсторонним скосом двух кромок; е — с криволинейным скосом кромок; ж —с использованием остающейся или съемной подкладки; з — с замковым расположением деталей; л — дополнительным скосом для устранения влияния разной толщины.
Отбортовку кромок (рис.1,а) применяют для деталей малой толщины s и обычно для сварки неплавящимся электродом без присадочного материала. Формирование шва происходит за счет оплавления кромок.
К элементам геометрической формы подготовке кромок под сварку относятся угол разделки кромок α ( выполняется при толщине металла > 4мм), притупление кромок – t, зазор между стыкуемыми кромками – в.
Разделка кромок позволяет вести сварку отдельными слоями небольшого сечения, что улучшает структуру сварного соединения. Угол разделки кромок α зависит от способа сварки, вида скоса кромок и типа сварного соединения:
для ручной электродуговой сварки при прямолинейном скосе одной кромки, α = = 45° ± 2°, двух — 25° ± 2°, а при криволинейном скосе одной кромки - 20° ± 2° и двух 12° ± 2°;
для автоматической сварки под флюсом, α = 30° ± 5° и 10° ± 2° при прямолинейном и криволинейном скосах кромок в случае стыковых и угловых соединений, тавровые соединения требуют большего угла, который равен соответственно 50° ± 5° и 20° ± 2°;
для сварки в среде защитных газов α == 40° ± 2° и 20° ± 2° при прямолинейном скосе одной и двух" кромок" — в случае криволинейного скоса α = 12° ± 2°.
По форме разделка кромок бывает Х-образная, К-образная, Y-образная, U – образная.
Зазор, правильно установленный перед сваркой, позволяет обеспечить полный провар по сечению соединения. Зазор b составляет 0 + 0,5 при толщине основного металла до 2мм; 0±1 при толщине основного металла 2- 4 мм; и мм при толщине основного металла более 4 мм.
Притупление выполняется для обеспечения устойчивого ведения сечения процесса сварки при выполнении корневого шва. Притупление t кромок назначают от 1 ± 1 до мм (большее притупление соответствует большей толщине основного металла).
Длина прихватки должна составлять (2÷10) ×S, но не более 100мм, а расстояние между ними (10÷40) ×S, но не более 500мм. Для разнотолщинных металлов длина (1÷5) ×S, но не более 50 мм, с шагом не более 250 мм.
Разделку кромок выполняют механической обработкой (точением, фрезерованием, строганием), скалыванием под углом на специальных ножницах, кислородной, плазменной резкой и другими способами.
Детали при стыковом соединении должны иметь одинаковую толщину. Допустимая разность толщины при сварке составляет не более 1 мм при толщине детали до 4 мм; 2 мм при толщине детали от4 до20 мм; 3 мм при толщине детали от 20 до 30 мм; и 4 мм при толщине деталей более 30 мм. Если разность толщины больше, то на детали с большей толщиной делают скос под углом 15° с одной или двух сторон (рис. 1, л).
При угловом соединении допускается не делать скос кромок, а формирование шва производить за счет смещения деталей на величину h (рис. 1, и, к). Смещение может быть менее 0,5 s или более 0,5 s при толщине деталей до 6 и 30 мм соответственно.
Выбор типа соединения и способа подготовки кромок зависит от условий его работы, толщины соединяемых деталей, конфигурации изделия и условий сварки. Так, наиболее дешевые соединения без подготовки кромок, но их сквозное проплавление ограничено толщиной детали. Скосы двух кромок, особенно криволинейные, наиболее трудоемки, но позволяют сократить массу наплавляемого металла и время сварки.
Зазоры между соединяемыми деталями обычно невелики, в противном случае возможны вытекание расплавленного металла и прожог кромок. Это обстоятельство особенно может проявиться при автоматической сварке.
Для защиты обратной стороны шва от вытекания металла могут быть использованы ниже перечисленные приемы:
-Замок, т. е. перекрытие одной детали другой (рис. 1, з). Перекрытие деталей b2 составляет 8... 20 мм, а зазор в замке z = 0 +0,5 мм. Способ эффективен, но дорогой.
-Остающаяся стальная подкладка (рис. 1, ж), толщина которой t1> достигает 0,5 толщины детали, но не менее 3 мм, ширина b1 = 10... 30 мм, а зазор между подкладкой и деталями z не должен быть более 0,5... 1 мм. Этот способ применяют, в частности, при сварке шаровых резервуаров, сосудов малого диаметра. Такие подкладки соответствуют соединениям С10, С19.
-Съемная технологическая подкладка из меди для стали, из графита для меди и т. п., которая не приваривается и ее удаляют после сварки (С9, С18).
-Предварительная ручная подварка корня шва (С12, С13, С21, С23, У5, У10, Т2) является трудоемкой, ее применяют, когда свариваемое изделие невозможно кантовать или точно собрать перед сваркой.
Типы сварных соединений.
В зависимости от взаимного расположения свариваемых деталей различают пять типов сварных соединений (согласно ГОСТ 5264-80 "Швы сварных соединений, ручная дуговая сварка" и ГОСТ 14771-76 "Швы сварных соединений, сварка в защитных газах"):
· стыковое – "С"
· торцевое – "С"
· нахлесточное – "Н";
· тавровое – "Т";
· угловое – "У".
В стыковом (С) сварном соединение поверхности свариваемых элементов располагаются в одной плоскости или на одной поверхности, а сварка выполняется по смежным торцам.
Стыковое соединение обеспечивает наиболее высокие механические свойства сварной конструкции, поэтому широко используется для ответственных конструкций. Однако, оно требует достаточно точной подготовки деталей и сборки.
Торцовое (С) соединение сваривается по торцам соединяемых деталей, боковые поверхности которых примыкают друг к другу.
Такие соединения используют, как правило, при сварке тонких деталей во избежание прожога.
В нахлесточном (Н) сварном соединении поверхности свариваемых элементов располагаются параллельно так, чтобы они были смещены и частично перекрывали друг друга.
Нахлесточные соединения менее чувствительны к погрешностям при сборке, но хуже чем стыковые работают при нагрузках, особенно знакопеременных.
Тавровое (Т) сварное соединение получается, когда торец одной детали под прямым или любым другим углом соединяется с поверхностью другой.
Тавровые соединения обеспечивают высокую жесткость конструкции, но чувствительны к изгибающим нагрузкам.
Угловым (У) называют соединение, в котором поверхности свариваемых деталей располагаются под прямым, тупым или острым углом и свариваются по торцам.
Все сварные соединения могут быть выполнены:
односторонними (SS)*, когда источник нагрева перемещается с одной стороны соединения; | ![]() |
двусторонними (BS)*, когда источник нагрева перемещается с двух сторон соединения. В таком сварном соединении корень стыкового шва находится внутри сечения. | ![]() |
|
|
Общие условия выбора системы дренажа: Система дренажа выбирается в зависимости от характера защищаемого...
Индивидуальные и групповые автопоилки: для животных. Схемы и конструкции...
История создания датчика движения: Первый прибор для обнаружения движения был изобретен немецким физиком Генрихом Герцем...
Опора деревянной одностоечной и способы укрепление угловых опор: Опоры ВЛ - конструкции, предназначенные для поддерживания проводов на необходимой высоте над землей, водой...
© cyberpedia.su 2017-2024 - Не является автором материалов. Исключительное право сохранено за автором текста.
Если вы не хотите, чтобы данный материал был у нас на сайте, перейдите по ссылке: Нарушение авторских прав. Мы поможем в написании вашей работы!