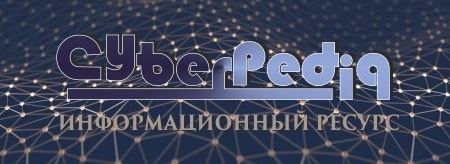
Общие условия выбора системы дренажа: Система дренажа выбирается в зависимости от характера защищаемого...
Семя – орган полового размножения и расселения растений: наружи у семян имеется плотный покров – кожура...
Топ:
Процедура выполнения команд. Рабочий цикл процессора: Функционирование процессора в основном состоит из повторяющихся рабочих циклов, каждый из которых соответствует...
Особенности труда и отдыха в условиях низких температур: К работам при низких температурах на открытом воздухе и в не отапливаемых помещениях допускаются лица не моложе 18 лет, прошедшие...
Определение места расположения распределительного центра: Фирма реализует продукцию на рынках сбыта и имеет постоянных поставщиков в разных регионах. Увеличение объема продаж...
Интересное:
Искусственное повышение поверхности территории: Варианты искусственного повышения поверхности территории необходимо выбирать на основе анализа следующих характеристик защищаемой территории...
Национальное богатство страны и его составляющие: для оценки элементов национального богатства используются...
Финансовый рынок и его значение в управлении денежными потоками на современном этапе: любому предприятию для расширения производства и увеличения прибыли нужны...
Дисциплины:
![]() |
![]() |
5.00
из
|
Заказать работу |
|
|
Маятниковый копёр.
Сортамент металлопроката
Балка двутавровая
Балка тавровая
Ч Е Р Ч Е Н И Е
В машиностроении все размеры указываются в милиметрах (мм). На чертежах ставятся цифры без обозначения единиц измерений.
Сборочные чертежи выполняют тогда, когда изделие состоит из нескольких деталей. Этот чертеж состоит из изображений составляющих изделие деталей и информации, необходимой для их изготовления и сборки.
Сборочным чертежом называется документ, содержащий изображение сборочной единицы, дающий представление о расположении и взаимной связи составных частей, соединенных между собой, и обеспечивающий возможность осуществления сборки и контроля сборочной единицы.
Сборочный чертеж должен давать полное представление о форме, функциональном назначении и составе сборочной единицы.
По сборочному чертежу из отдельных деталей, собирают простейшие узлы и сложнейшие машины, технические устройства.
По сборочному чертежу можно представить взаимное расположение составных частей, способы соединения деталей между собой и принцип работы.
Сборочный чертеж содержит:
1) изображение сборочной единицы. В центре располагается главный вид или вид спереди. Далее вид сверху, вид с боку, сечения и разрезы.
2) необходимые размеры. На сборочном чертеже обязательно должны быть заданы размеры, которые характеризуют изделие в целом, а также те, которые необходимо выдержать при сборке и контроле изготавливаемого изделия.
габаритные размеры, т. е. наибольшие внешние размеры изделия по трем измерениям (высота, длина, ширина);
|
установочный - размер, определяющий положение предмета на месте монтажа или положение составной части при её установке в изделие;
присоединительные, т. е. размеры элементов детали, изделия, обеспечивающих возможность присоединения их к другому изделию;
монтажные, т. е. размеры, необходимые для правильной установки деталей относительно друг друга, например, размеры между центровыми и осевыми линиями;
эксплуатационные, указывающие крайние положения движущихся частей изделий, например ход поршня, рычага;
3) номера позиций;
4) технические требования;
5) техническую характеристику изделия (при необходимости);
6) спецификация.
Каждый сборочный чертеж сопровождается спецификацией.
Спецификация — основной конструкторский документ, выполненный в виде таблицы, в которой приводятся наименования, номера позиций всех составных частей сборочной единицы и указывается их число.
В спецификации документацию и составные части сборочной единицы перечисляют в определенной последовательности: документация, комплексы, сборочные единицы, детали, стандартные изделия, прочие изделия, материалы, комплекты.
Спецификацию выполняют на отдельных листах (одном или нескольких) формата А4 или размешают непосредственно на сборочном чертеже, выполненном на формате A4, если имеется достаточно места для ее размещения. Спецификацию выполняют прежде, чем на сборочном чертеже наносятся номера позиций деталей, входящих в сборочную единицу. Она необходима для изготовления изделия.
Чтение чертежей.
Рекомендуется следующая последовательность чтения чертежей.
1. По основной надписи установить наименование изделия, номер, масштаб чертежа, массу изделия.
2. Выяснить содержание и особенности чертежа (определить все изображения, составляющие чертеж).
3. По спецификации установить наименование каждой детали изделия, найти их, уяснить геометрические формы.
4. Установить характер соединения составных частей изделия между собой. Для неразъемных соединений определить каждый элемент соединения. Для разъемных соединений выявить все крепежные детали, входящие в соединение.
|
5. Выяснить порядок сборки изделия. При этом следует помнить, что в спецификации и на сборочном чертеже порядок записи и обозначения составных частей не связаны с последовательностью сборки.
Примеры обозначения сварных швов.
Пример 1.
![]() | ![]() | ![]() |
Форма поперечного сечения шва | а) стрелка указывает на лицевую сторону шва | б) стрелка указывает на обратную сторону шва |
Шов стыкового соединения с криволинейным скосом одной кромки, двусторонний выполняемый дуговой ручной сваркой (С13 по ГОСТ 5264 - 80) при монтаже изделия (). Усиление снято с обеих сторон (
). Параметр шероховатости поверхности шва: с лицевой стороны – Rz 20 мкм; с оборотной стороны - Rz 80 мкм.
Пример 2.
![]() | ![]() | ![]() |
Форма поперечного сечения шва | а) стрелка указывает на лицевую сторону шва | б) стрелка указывает на обратную сторону шва |
Шов углового соединения без скоса кромок, двусторонний (У2 по ГОСТ 11533-75) выполняемый автоматической дуговой сваркой под флюсом (А по ГОСТ 11533-75) по замкнутой линии.
Пример 3.
![]() | ![]() | ![]() |
Форма поперечного сечения шва | а) стрелка указывает на лицевую сторону шва | б) стрелка указывает на обратную сторону шва |
Шов стыкового соединения без скоса кромок, односторонний, на остающейся подкладке (C3 по ГОСТ 16310–80), выполняемый сваркой нагретым газом с присадкой (Г по ГОСТ 16310–80).
Пример 4.
Шов таврового соединения без скоса кромок, двусторонний прерывистый с шахматным расположением (Т3 по ГОСТ 14806-80) выполняемый дуговой ручной сваркой в защитных газах неплавящимся металлическим электродом (РИНп по ГОСТ 14806-80). Катет шва 6 мм (Δ6), длина провариваемого участка 50 мм, шаг 100 мм (Z).
Tш - длина провариваемого участка шва
t пр - длинна участка шага прерывистого шва
Пример 5.
Шов соединения внахлестку без скоса кромок, односторонний (Н1 по ГОСТ 14806-80), выполняемый дуговой сваркой в защитных газах плавящимся электродом (ПИП по ГОСТ 14806-80). Шов по незамкнутой линии (). Катет шва 5 мм (Δ5).
Пример 6.
Шов соединения внахлестку без скоса кромок, односторонний (Н1 по ГОСТ 14806-80), выполняемый дуговой полуавтоматической сваркой в защитных газах плавящимся электродом (ПИП по ГОСТ 14806-80). Шов по замкнутой линии ( круговой шов). Катет шва 5 мм (Δ5).
|
Строение сварочной дуги.
По длине дугового промежутка дуга разделяется на три области: катодную, анодную и находящийся между ними столб дуги.
Катодная область включает в себя нагретую поверхность катода, называемую катодным пятном, и часть дугового промежутка, примыкающую к ней.
Строение электрической дуги и распределение напряжения в ней:
1 - катодная область, 2 - столб дуги, 3 - анодная область
Катодная область характеризуется повышенной напряженностью и протекающими в ней процессами получения электронов, являющимися необходимым условием для существования дугового разряда. Температура катодного пятна для стальных электродов достигает 2400 - 2700°С. На нем выделяется до 38% общей теплоты дуги. Основным физическим процессом в этой области является электронная эмиссия и разгон электронов. Падение напряжения в катодной области UK составляет порядка 12 - 17 В.
Анодная область состоит из анодного пятна на поверхности анода и части дугового промежутка, примыкающего к нему. Ток в анодной области определяется потоком электронов, идущих из столба дуги. Анодное пятно имеет примерно такую же температуру, как и катодное пятно, но в результате бомбардировки электронами на нем выделяется больше теплоты, чем на катоде. Анодная область также характеризуется повышенной напряженностью. Падение напряжения в ней Uк составляет порядка 2 - 11 В. Протяженность этой области также мала.
Столб дуги занимает наибольшую протяженность дугового промежутка, расположенную между катодной и анодной областями. Основным процессом образования заряженных частиц здесь является ионизация газа. В целом столб дуги не имеет заряда. Он нейтрален, так как в каждом сечении его одновременно находятся равные количества противоположно заряженных частиц. Температура столба дуги достигает 6000 - 8000°С и более. Падение напряжения в нем Uc изменяется практически линейно по длине, увеличиваясь с увеличением длины столба.
Вольт - амперная характеристика сварочной дуги.
|
Непременным условием получения качественного сварного соединения является устойчивое горение дуги (ее стабильность). Под этим понимают такой режим ее существования, при котором дуга длительное время горит при заданных значениях силы тока и напряжения, не прерываясь и не переходя в другие виды разрядов.
При устойчивом горении сварочной дуги основные ее параметры- сила тока и напряжение- находятся в определенной взаимозависимости. Поэтому одной из основных характеристик дугового разряда является зависимость ее напряжения от силы тока при постоянной длине дуги. Графическое изображение этой зависимости при работе в статическом режиме (в состоянии устойчивого горения дуги) называют статической вольтамперной характеристикой дуги.
Кривую статической характеристики можно разделить на три области: падающую, жесткую и возрастающую.
В первой области увеличение тока приводит к резкому падению напряжения дуги. Это обусловлено тем, что с увеличением силы тока увеличиваются площадь сечения столба дуги и его электропроводность. Горение дуги на режимах в этой области отличается малой устойчивостью.
Во второй области увеличение силы тока не связано с изменением напряжения дуга. Это объясняется тем, что площадь сечения столба дуги и активных пятен изменяется пропорционально силе тока, в связи с чем плотность тока и падение напряжения в дуге сохраняются постоянными.
В третьей области с увеличением силы тока напряжение возрастает. Это связано с тем, что диаметр катодного пятна становится равным диаметру электрода и увеличиваться далее не может, при этом в дуге возрастает плотность тока и падает напряжение. Дуга с возрастающей статической характеристикой широко используется при автоматической и механизированной сварке под флюсом и в защитных газах с применением тонкой сварочной проволоки.
Магнитная дефектоскопия
При контроле качества сварки магнитными дефектоскопами используется явление электромагнетизма. Прибор создает вокруг исследуемой области магнитное поле, поток линий которого, проходя через металл, искривляется в местах дефектов. Это искажение фиксируется определенными способами, из которых в сварочном производстве используются два - магнитопорошковый и магнитографический. При первом, на поверхность сварного соединения наносят сухой или влажный (в смеси с маслом, керосином или мыльным раствором) ферромагнитный порошок (например - железный), который скапливается в местах дефектов, свидетельствуя, таким образом, о наличие несплошностей.
Проверка качества сварных швов магнитной дефектоскопией
Более совершенный магнитографический способ предполагает наложение на шов ферромагнитной ленты, на которой после пропускания ее через прибор проявляются имеющиеся дефекты.
|
Проверка качества сварных швов магнитной дефектоскопией: 1 - магнит, 2 - сварной шов, 3 - дефект, 4 - магнитная пленка.
Магнитным способам контроля могут подвергаться только ферромагнитные металлы. Хромоникелевые стали, алюминий, медь, не являющиеся ферромагнетиками, магнитному контролю не подлежат.
Сварочные материалы.
Электроды для ручной дуговой сварки.
Ручная дуговая сварка осуществляется плавящимся электродом, покрытым специальной обмазкой. Металлический стержень электрода включается в цепь сварочного тока для подвода его к дуге и при сварке расплавляется, выполняя роль присадочного металла.
Требования к электродам: спокойное устойчивое горение дуги, равномерное расплавление стержня и покрытия, надежная защита жидкого металла и равномерное покрытие ванны шлаком, легкое удаление шлака после затвердевания, удобство выполнения швов в требуемых положениях, отсутствие токсичности, покрытие электрода должно быть достаточно прочным и не осыпаться при транспортировке и сварке.
Для того чтобы электроды удовлетворяли этим требованиям, должны быть правильно подобраны электродная проволока для изготовления стержней и состав покрытия электродов.
Электродные стержни изготовляют из стальной сварочной проволоки, соответствующей ГОСТ 2246—70. Проволоку поставляют в мотках, к каждому мотку прикрепляют бирку, в которой указывается наименование предприятия- изготовителя, наименование (марка) проволоки, ее диаметр, номер ГОСТа. К каждой партии проволоки прилагается сертификат - документ, удостоверяющий соответствие проволоки ГОСТу. В соответствии с ГОСТ 2246—-70 она разделяется на группы в зависимости от химического состава: низкоуглеродистая, легированная и высоколегированная. Марки проволоки имеют условное обозначение. Например Св-08ГА: первые две буквы означают, что эта проволока сварочная, следующие за ними цифры н буквы характеризуют содержание различных элементов в металле проволоки - первые две цифры -выраженная в сотых долях процента массовая доля углерода, в данной марке она равна 0,08 %. Буква Г указывает на содержание в проволоке марганца, в данном случае 0,8-1,1 %, а буква А- на изготовление ее из высококачественной стали с уменьшенным содержанием вредных примесей (серы и фосфора). Если в конце марки стоят две буквы А (Св-08АА), то значит, что вредных примесей еще меньше.
В других марках после первых двух цифр, указывающих на содержание углерода, ставятся буквы и цифры: буквы обозначают содержание отдельных элементов, цифры - их массовую долю в целых процентах. Если цифра за буквой отсутствует, то это означает содержание этого элемента до 1%. Например: Св-08Г2С. Св обозначает, что это сварочная проволока; 08 обозначает содержание углерода 0,08%; Г2 обозначает содержание марганца 2%; С обозначает содержание кремния до 1%.
Перед установкой кассеты с проволокой необходимо внимательно прочитать марку и диаметр.
Обозначение элементов в марках электродной проволоки: Азот - А, Кремний – С, Ниобий- Б, Тнтан -Т, Вольфрам- В, Ванадий- Ф, Марганец- Г, Хром- X, Медь- Д, Цирконий- Ц, Молибден- М, Алюминий –Ю, Никель-Н.
Покрытия электродов. В состав покрытия входит ряд материалов, которые выполняют определенные функции при сварке. Покрытие образуется из хорошо размолотых и перемешанных материалов, связанных жидким стеклом и нанесенных на стержни под давлением слоем до 2 мм на специальном прессе. Покрытие электрода при сварке плавится несколько позже самого стержня, вследствие чего на конце электрода образуется небольшой чехольчик, расплавление которого должно быть равномерным; недопустимо одностороннее распределение, которое мешает сварщику поддерживать дугу требуемой длины.
Применяемые для электродного покрытия материалы разделяют на группы в соответствии с их функциями.
Шлакообразующие составляющие защищают расплавленный металл от воздействия кислорода и азота воздуха и частично очищают его, образуя шлаковые оболочки вокруг капель электродного металла. Эти составляющие включают в себя титановый концентрат, марганцовую руду, полевой шпат, каолин, мел, мрамор, кварцевый песок, доломит.
Газообразующие составляющие при сгорании создают газовую защиту, которая предохраняет расплавленный металл от кислорода и азота воздуха. Газообразующие составляющие состоят из древесной муки хлопчатобумажной ткани, крахмала, пищевой муки, декстрина, целлюлозы.
Раскисляющие составляющие необходимы для раскисления расплавленного металла сварочной ванны. К ним относятся элементы, которые обладают большим сродством к кислороду, чем железо: марганец, кремний, титан, алюминий и др.
Легирующие элементы необходимы в составе покрытия для придания металлу шва специальных свойств: жаростойкости, износостойкости, сопротивления коррозии и повышения механических свойств. Легирующими элементами служат марганец, хром, титан, ванадий, молибден, никель, вольфрам и другие элементы.
Стабилизирующими составляющими являются те элементы, которые имеют небольшой потенциал ионизации (калий, натрий и кальций), поддерживая этим горение дуги и облегчая её загорание при непрерывном изменении полярности переменного тока.
Связующие (клеящие) составляющие применяют для связывания составляющих покрытий между собой и со стержнем электрода. В качестве них применяют калиевые или натриевое жидкое стекло, декстрин, желатин и др.
ГОСТ 9466-75 на электроды покрытые металлические для ручной дуговой сварки сталей и наплавки устанавливает некоторые характеристики электродных покрытий.
По толщине нанесенного покрытия электроды подразделяются: с тонким покрытием М при отношении (D /a) х1,2 (D - диаметр электрода с покрытием, d — диаметр стержня); со средним покрытием С при (D/d) ^ 1,45; с толстым покрытием Д при (D/d) > (1,45- 1, 8); с особо толстым покрытием Г при (D/d) >1,8.
Этот же ГОСТ устанавливает шесть видов электродных покрытий с условным обозначением: А, Б, Ц, Р, П и смешанный.
- Кислое покрытие А отличается тем, что в его состав входят образующие шлаковую защиту различные руды и материалы, содержащие большое количество кислорода. Например гематит содержит 92 % Fe2О3, гранит 66-71 % Si0 2, 15-21 % А12Оз и т. п. Для удаления кислорода и восстановления железа из оксидов применяют ферросплавы, для газовой защиты вводят органические примеси — крахмал, декстрин. Сварка электродами с этим покрытием возможна на постоянном и переменном токе во всех положениях. В сварочной ванне происходит активное раскисление железа, она кипит, что способствует дегазации металла. Допускается сварка при небольшой окалине и ржавчине, однако при этом происходит повышенное разбрызгивание, и вследствие применения ферромарганца выделяется значительное количество токсичных марганцевых соединений, что ограничивает применение таких покрытий. Кроме того, металл шва склонен к образованию кристаллизационных трещин.
- Основное покрытие Б содержит: фтористокальциевое соединение -плавиковый шпат, в котором CaF более 75 %; карбонаты кальция - мрамор, мел с содержанием более 92 % СаСОз и ферросплавы. При расплавлении это покрытие кроме шлака выделяет большое количество защитного углекислого газа, образующегося вследствие диссоциации карбонатов. Сварка электродами с основным покрытием возможна постоянным током с обратной полярностью и во всех положениях. Для сварки переменным током в покрытие добавляют более активные стабилизаторы- калиевое жидкое стекло, поташ и др. Металл, наплавленный электродами с основным покрытием, обладает высокими механическими показателями, особенно ударной вязкостью при положительных и низких температурах; не склонен к образованию кристаллизационных трещин и старению; содержит минимальное количество
кислорода и азота. Эти электроды применяют для сварки наиболее ответственных деталей и конструкций. Следует иметь в виду, что сварка электродами с основным покрытием должна вестись короткой дугой и при хорошей очистке свариваемых кромок от ржавчины, окалины, жира и влаги во избежание образования пористости в швах.
- Целлюлозное покрытие Ц содержит в основном оксицеллюлозу или аналогичные ей органические вещества, а также рутил и ферросплавы. Это покрытие при расплавлении выделяет главным образом многозащитного газа и небольшое количество шлака для процесса раскисления. Электроды с этим покрытием пригодны для сварки во всех положениях на постоянном и переменном токе и употребляются в основном для сварки первого слоя стыков труб.
- Рутиловое покрытие Р содержит 50 % рутилового концентрата, в котором 50% ТЮ2, карбонаты кальция— мрамор, тальк, мусковит, магнезит, ферросплавы,целлюлозу. Газовая защита обеспечивается за счет диссоциации материалов и органической составляющей. Раскисление и легирование — ферросплавами.Электроды с рутиловым покрытием пригодны для сварки постоянным и переменным токами во всех положениях. Они обеспечивают высокое качество наплавленного металла, обладают хорошими технологическими свойствами и применяются для сварки низкоуглеродистой стали.
- Покрытия, обозначенные буквой П, не имеют явно выраженного кислого, основного, целлюлозного или рутилового состава.
- Смешанные покрытия обозначают двойной буквой,
например БЦ - покрытие основного типа со значительным количеством целлюлозы.
Классификация электродов по назначению и допустимым пространственным положениям сварки:
Согласно ГОСТ 9466- 75, электроды разделяются по назначению:
-для сварки углеродистых и низколегированных конструкционных сталей с временным сопротивлением разрыву до 600 МПа - У;
-для сварки легированных конструкционных сталей с временным сопротивлением разрыву свыше 600 МПа - Л;
-для сварки легированных теплоустойчивых сталей - Т;
-для сварки высоколегированных сталей с особыми свойствами - В;
-для наплавки поверхностных слоев с особыми свойствами - Н.
По допустимым пространственным положения сварки или наплавки электроды подразделяются:
для всех положений -1;
для всех положений, кроме вертикального сверху вниз, - 2;
для нижнего, горизонтального и вертикального снизу вверх -3;
для нижнего и нижнего ≪в лодочку≫ - 4.
Виды электродов по роду и полярности сварочного тока
Рекомендуемая полярность постоянного тока |
Напряжение холостого хода источника переменного тока, В |
Обозначение | |
Номинальное напряжение | Предельное отклонение | ||
Обратная | - | - | 0 |
Любая | 50 | ±5 | 1 |
Прямая | 2 | ||
Обратная | 3 | ||
Любая | 70 | ±10 | 4 |
Прямая | 5 | ||
Обратная | 6 | ||
Любая | 90 | ±5 | 7 |
Прямая | 8 | ||
Обратная | 9 |
Цифрой 0 обозначают электроды, предназначенные для сварки или наплавки только на постоянном токе обратной полярности (сварочный электрод соединяется с плюсом).
Электроды подразделяются на типы согласно ГОСТ
ГОСТ 9467-75 предусматривает 14 типов электродов сварки конструкционных сталей и 9 типов для сварки теплоустойчивых сталей.
ГОСТ 10052-75 предусматривает 49 типов электродов ручной дуговой сварки высоколегированных сталей с особыми свойствами.
ГОСТ 10051-75 предусматривает 44 типов электродов дуговой наплавки поверхностных слоев с особыми свойствами. Кроме регламентированного химического состава установлены требования к твердости наплавленного металла.
Типы электродов для сварки конструкционных сталей обозначают буквой Э, после которой следуют цифры минимального временного сопротивления наплавленного этим электродом металла в кг/мм2. Например: электроды Э42 должны гарантировать минимальное временное сопротивление 42 кг/мм2. Буква А, стоящая после цифр (например, Э46А) означает, что электроды этого типа обеспечивают более высокие пластические свойства наплавленного металла, чем электроды без буквы А.
Каждому типу электродов для сварки сталей соответствует несколько марок электродов, особенно много марок разработано и выпускается для сварки конструкционных сталей. Например, к типу электродов Э46А относятся электроды марки УОНИИ-13/45, СМ-11 и др.
Например:
Э46А – УОНИ-13/45 – 3.0 – УД
Е – 432 (5) – Б20 – ГОСТ 9466, ГОСТ 9467
В числителе последовательно: тип электрода (Э46А), марка (УОНИ–13/45), диаметр (3.0мм), класс (У - для углеродистых сталей), обозначение толщины покрытия (Д - толстое).
В знаменателе последовательно: Е - группа индексов, указывающих характеристики наплавленного металла или металла шва по ГОСТ 9467,
43 - обозначает предел прочности, σв = 430 МПа,
2 - обозначает относительное удлинение, δ = 22 %,
5 - обозначает температуру хладноломкости, при которой определяется ударная вязкость.
обозначение вида покрытия (Б – основное),
обозначение допустимого пространственного положения сварки (2- для всех положений, кроме вертикального сверху вниз),
обозначение рода и полярности сварочного тока (О - постоянный ток обратной полярности).
обозначение стандарта ГОСТ 9466 и обозначение стандарта на данный класс электродов (ГОСТ 9467).
Прокалка электродов, хранение их на рабочем месте.
В складе должны быть установлены печи для прокалки электродов, порошковой проволоки и флюса с температурой до 400°С, сушильные шкафы с температурой до 80 -115 °С, обеспечивающие суточную потребность участка в электродах и проволоке.
Прокаленные электроды и порошковую проволоку следует выдавать на рабочее место в количестве, необходимом для работы сварщика в течение одной смены.
При сварке конструкций из сталей с пределом текучести более 390 МПа электроды, взятые непосредственно из прокалочной или сушильной печи, необходимо использовать в течение 2 часов.
Прокалкаэлектродов может производиться не более трех раз. Температура и время прокалки – согласно требованиям сертификата или на этикетке пачки электродов. Если электроды после трехкратной прокалки показали неудовлетворительные сварочно-технологические свойства, то применение их для сварочных работ не допускается.
После прокалки электроды должны быть использованы в течение ближайших 5 суток, а флюсы — в течение 15 суток. При хранении прокаленных электродов в сушильном шкафу при температуре 80-115 °С срок их годности не ограничивается.
Порошковая проволока - это непрерывный электрод, который представляет собой металлическую трубку с толщиной стенки 0,2...0,5 мм, диаметром 1,6 - 3,0 мм, заполненную смесью из газо- и шлакообразующих компонентов. Применяют ее для механизированной дуговой сварки открытой дугой. Сохраняя технологические преимущества голой проволоки, порошковые проволоки позволяют создавать надежную газовую и шлаковую защиту сварочной ванны от атмосферного воздуха при работе на открытых площадках, обеспечивая при этом легирование и рафинирование металла шва.
Кроме того, используя их, можно применять ток плотностью 150...170 А/мм2, в то время как при ручной дуговой сварке плотность тока не превышает 20 А/мм2. Это дает возможность повысить производительность процесса 1,5...2 раза.
Для восстановления изношенных поверхностей деталей или придания поверхности заданных свойств (износостойкости, коррозионной стойкости и др.) применяют специальные наплавочные порошковые проволоку и ленту.
Порошковые проволоки: трубчатая цельнотянутая (а), трубчатая свертная (б), трубчатая однозагибная (в), трубчатая двухзагибная (г), трубчатые с повышенной долей металла (5, е) и порошковая лента (ж).
Для получения на поверхности детали слоя, обладающего повышенными твердостью и износостойкостью, применяют порошковую наплавочную ленту.
В марках порошковой проволоки и ленты применяют следующие обозначения: ПП — порошковая проволока; ПЛ — порошковая лента, У — углерод; цифра после буквы У — содержание углерода в десятых долях процента; Ч — проволока для сварки и наплавки чугуна; буква О в конце обозначения указывает, что данную проволоку можно использовать для сварки открытой дугой. Значения остальных букв и цифр такие же, как и в марках стальных сварочных и наплавочных проволок.
Сварка порошковой проволокой.
Одним из преимуществ сварки открытой дугой порошковой проволокой по сравнению со сваркой в углекислом газе является отсутствие необходимости в газовой аппаратуре и возможность сварки на сквозняках, при которых наблюдается сдувание защитной струи углекислого газа. При правильно выбранном режиме сварки обеспечивается устойчивое горение дуги и хорошее формирование шва. В качестве источников тока можно использовать выпрямители с крутопадающими внешними вольт - амперными характеристиками.
Недостатком этого способа сварки является возможность сварки только в нижнем и вертикальном положениях из-за повышенного диаметра выпускаемых промышленностью проволок и повышенной чувствительности процесса сварки к образованию пор при изменениях вылета электрода и напряжения дуги. Особенность порошковых проволок - малая глубина проплавления основного металла.
Защитные газы.
Для газовой защиты расплавляемого при сварке металла применяют инертные газы (аргон, гелий) и активные газы (углекислый газ, азот, водород).
Инертные газы обеспечивают хорошую защиту свариваемого металла от воздуха, не вступают в реакцию с металлом и используются для сварки высоколегированных нержавеющих сталей и цветных металлов. Наиболее широко применяются аргон и в меньшей степени гелий как более дорогой.
Газообразный аргон хранится и транспортируется в стальных баллонах (по ГОСТ 949-73). Баллон с чистым аргоном окрашен в серый цвет, с надписью «Аргон чистый» зеленого цвета.
Согласно ГОСТ 10157-79 газообразный и жидкий аргон поставляется двух видов: высшего сорта (с объемной долей аргона не менее 99,993%, объемной долей водяных паров не более 0,0009%) и первого сорта (с объемной долей аргона не менее 99,987%, объемной долей водяных паров не более 0,001%).
Аргон не взрывоопасен и не токсичен, однако при высокой концентрации в воздухе может представлять опасность для жизни: при уменьшении объемной доли кислорода ниже 19% появляется кислородная недостаточность, а при значительном снижении содержания кислорода возникают удушье, потеря сознания и даже смерть.
Сварочные инверторы
Слово "инвертор" в своем исходном значении означает устройство для преобразования постоянного тока в переменный. На рисунке ниже приведена упрощенная схема сварочного аппарата инверторного типа.
Блок-схема сварочного инвертора: 1 - сетевой выпрямитель, 2 - сетевой фильтр, 3 - преобразователь частоты (инвертор), 4 - трансформатор, 5 - высокочастотный выпрямитель, 6 - блок управления.
Работа сварочного инвертора происходит следующим образом. Переменный ток частотой 50 Гц поступает на сетевой выпрямитель 1. Выпрямленный ток сглаживается фильтром 2 и преобразуется (инвертируется) модулем 3 в переменный ток с частотой в несколько десятков кГц. В настоящее время достигаются частоты в 100 кГц. Именно этот этап является самым важным в работе сварочного инвертора, позволяющим добиться огромных преимуществ по сравнению с другими типами сварочных аппаратов. Далее с помощью трансформатора 4 высокочастотное переменное напряжение понижается до значений холостого хода (50-60В), а токи повышаются до величин, необходимых для осуществления сварки (100-200А). Высокочастотный выпрямитель 5 выпрямляет переменный ток, который совершает свою полезную работу в сварочной дуге. Воздействуя на параметры преобразователя частоты, регулируют режим и формируют внешние характеристики источника.
Процессы перехода тока из одного состояния в другое контролируются блоком управления 6. В современных аппаратах эта работа выполняется транзисторными модулями IGBT, являющимися самыми дорогими элементами сварочного инвертора.
Система управления с помощью обратных связей формирует идеальные выходные характеристики для любого способа электросварки. Благодаря высокой частоте, вес и размеры трансформатора снижаются в разы.
По своей функциональности выпускаются инверторы следующих типов:
Сварочный инвертор
Включение в цепь амперметра (последовательно) и вольтметра (параллельно участку цепи) при измерениях.
Подключение нулевого провода. Отдельный проводник, присоединяемый к спец контакту вилки втычного соединения и к корпусу электроприёмника.
Выполнение сварки
Сварщик должен иметь хорошее образование не только в практической области, но и теории, описывающей особенности технологии. Это необходимо для предупреждения ошибок.
Зажигание электрической дуги.
После включения переключателя горелки начинается подача защитного газа, проволочный электрод приходит в движение с установленной скоростью. Одновременно при помощи реле тока к нему подключается электрический ток. При прикосновении к поверхности изделия возникает короткое замыкание. Из-за высокой плотности тока на конце электрода в точке соприкосновения начинается расплавление сварочной проволоки, и происходит зажигание дуги. При высокой скорости подачи еще слабая дуга может быть потушена быстро подаваемой проволокой. Так что зажигание может произойти со второй или третьей попытки. Зажигание дуги необходимо производить на оси сварного шва. Как только дуга начнет гореть стабильно, точки зажигания должна быть расплавле
|
|
История создания датчика движения: Первый прибор для обнаружения движения был изобретен немецким физиком Генрихом Герцем...
Организация стока поверхностных вод: Наибольшее количество влаги на земном шаре испаряется с поверхности морей и океанов (88‰)...
Семя – орган полового размножения и расселения растений: наружи у семян имеется плотный покров – кожура...
Автоматическое растормаживание колес: Тормозные устройства колес предназначены для уменьшения длины пробега и улучшения маневрирования ВС при...
© cyberpedia.su 2017-2024 - Не является автором материалов. Исключительное право сохранено за автором текста.
Если вы не хотите, чтобы данный материал был у нас на сайте, перейдите по ссылке: Нарушение авторских прав. Мы поможем в написании вашей работы!