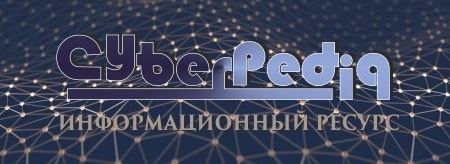
Историки об Елизавете Петровне: Елизавета попала между двумя встречными культурными течениями, воспитывалась среди новых европейских веяний и преданий...
История создания датчика движения: Первый прибор для обнаружения движения был изобретен немецким физиком Генрихом Герцем...
Топ:
Марксистская теория происхождения государства: По мнению Маркса и Энгельса, в основе развития общества, происходящих в нем изменений лежит...
Оценка эффективности инструментов коммуникационной политики: Внешние коммуникации - обмен информацией между организацией и её внешней средой...
Устройство и оснащение процедурного кабинета: Решающая роль в обеспечении правильного лечения пациентов отводится процедурной медсестре...
Интересное:
Искусственное повышение поверхности территории: Варианты искусственного повышения поверхности территории необходимо выбирать на основе анализа следующих характеристик защищаемой территории...
Уполаживание и террасирование склонов: Если глубина оврага более 5 м необходимо устройство берм. Варианты использования оврагов для градостроительных целей...
Берегоукрепление оползневых склонов: На прибрежных склонах основной причиной развития оползневых процессов является подмыв водами рек естественных склонов...
Дисциплины:
![]() |
![]() |
5.00
из
|
Заказать работу |
|
|
Кадомцев А.Н., Буторин Л.В., Стреляев Д.В.
ДЕТАЛИ МАШИН
Учебно – практическое пособие
Содержание
Введение ………………………………………………………………...…………4
Глава 1 ………………………………………………………………..……………4
1.1 Основные критерии работоспособности……………………………………..4
1.2 Типы расчетных задач. Критерии прочности………………………………..5
1.3 Виды нагрузок…………………………………………………………………6
1.4 Методики выбора допускаемых напряжений………………………………..7
Вопросы для самоконтроля …………………………………………………7
Тесты к главе 1 ……………….………………………………………………8
Глава 2. Соединения. Общие сведения и классификация. …………………9
2.1 Неразъемные соединения……………………………………………………..9
2.2 Сварные соединения…………………………………………………………..9
2.3 Заклепочные соединения…………………………………………………….10
Вопросы для самоконтроля ………………………………………………..12
Тесты к главе 2 …………………………………………..…………………..12
Глава 3. Разъемные соединения ……………………………………………….13
3.1 Соединения типа «Вал-ступица»…………………………………………….13
3.2 Резьбовые соединения………………………………………………………..16
Вопросы для самоконтроля ………………………………………………..19
Тесты к главе 3 ………………….…………………………………………...20
Глава 4. Механические передачи ……………………………………………..21
4.1 Кинематические и силовые соотношения в передачах…………………….22
4.2 Зубчатые передачи……………………………………………………………24
4.3 Прямозубые цилиндрические передачи……………………………………..25
4.4 Конические зубчатые передачи……………………………………………...30
|
4.5 Червячные передачи………………………………………………………….33
Вопросы для самоконтроля..…………………………………………..…..37
Тесты к главе 4 …………………………………………………………..…..37
Глава 5. Валы и опоры …….……………………………………………………39
5.1 Валы и оси……………………………………………………………………..39
5.2 Подшипники…………………………………………….……………………..42
Вопросы для самоконтроля ……………………….………………………..45
Тесты к главе 5…. …………………………………………………………....45
Ответы на тесты …………..……………………………………………………..46
Примеры зачетных заданий ……………………………………………………47 Тесты по дисциплине.. …………………………………………………………..51
Словарь основных понятий …………………………………………………….55
Библиографический список …………………………………………………….57
Введение
В курсе «Детали машин» рассматриваются теоретические основы расчета и конструирования типовых деталей и узлов машин, т.е. таких деталей и узлов, которые встречаются в различных машинах вне зависимости от их назначения. Под машиной принято понимать устройство, преобразующее за счет механического движения вид энергии, материал или информацию. Соответственно назначению машины называют энергетическими, технологическими, информационными.
Кинематическую основу машин составляют механизмы. Механизмом называют систему взаимосвязанных тел, преобразующую движения одного или нескольких твердых тел в требуемое движение других твердых тел. Твердые тела, входящие в состав механизма, называют звеньями. Звено механизма может состоять из одной или нескольких деталей, неподвижно соединенных между собой. Деталью называется изделие, изготовленное из однородного материала без применения сборочных операций. Звенья соединяются между собой кинематическими парами, обеспечивающими их относительное движение.
Проектирование машины представляет собой сложную задачу, включающую в себя выбор материалов, разработку конструктивных форм деталей, технологию их изготовления, обеспечивающих работоспособностью машины в целом. Работоспособность – способность выполнять заданные функции в течение заданного срока.
|
Глава 1
Основные критерии работоспособности
Основными критериями работоспособности являются:
- прочность, т.е. способность детали сопротивляться действующим нагрузкам без разрушения или пластического деформирования;
- жесткость, т.е. способность сопротивляться изменению формы и размеров под действием приложенных силовых факторов;
- износостойкость, т.е. способность сохранять форму и размеры поверхностей трения в течение срока эксплуатации.
На работоспособность также влияют теплостойкость, виброустойчивость, термическая акустическая усталость, эрозионная и коррозионная стойкость и т. д.
Работоспособность детали тесно связана с понятием надежности, т.е. способностью выполнять свои функции в течение заданной наработки при сохранении эксплуатационных характеристик в необходимых пределах.
Основными показателями надежности служат безотказность, долговечность и ремонтопригодность.
Виды нагрузок
Нагрузки, действующие на детали современных машин, можно разделить на три большие группы.
1. Ударные (динамические) нагрузки характеризуются очень кратким во времени действием, но могут быть весьма значительными по величине. Сопротивление конструкционных материалов таким нагрузкам определяется их ударной вязкостью и представляет собой самостоятельную задачу. Подобный вид нагружения характерен для деталей транспортных машин.
2. Статические нагрузки характеризуются постоянством во времени
(рис. 1.1). Чисто статическое нагружение на практике реализуется крайне редко. К данному виду можно условно отнести нагрузки, действующие на детали, работающие в условиях длительного эксплуатационного цикла (резервуары давления, стержни болтов в соединениях с предварительной затяжкой и т.д.). В связи с этим, рассматривая нагружение деталей машин как статическое, правильнее использовать понятие длительной прочности.
Рис. 1.1
|
3.
|
|
Рис. 1.2 Рис. 1.3
Если переменная нагрузка повторяется периодически, ее называют циклической (рис.1.3).
Цикл напряжений характеризуется следующими показателями:
- максимальными напряжениями s (t)max;
- минимальными напряжениями s (t)min;
- амплитудными напряжениями s (t)а;
- средними напряжениями s (t)m;
- коэффициентом асимметрии цикла R, равным отношению smin/smax.
Вопросы для самоконтроля
1. Каковы основные критерии работоспособности деталей машин?
2. Какие типы расчетных задач рассматривает дисциплина “Детали машин ”?
3. Какие существуют методики выбора допускаемых напряжений и определения коэффициентов запаса прочности?
Тесты к главе 1
1.1 Перечислите основные критерии работоспособности детали:
а) Прочность
б) Жесткость
в) Долговечность
г) Теплостойкость
д) Виброустойчивость
е) Безотказность
ж) Ремонтоспособность
1.2 Как называется расчет, определяющий фактические характеристики главного критерия работоспособности детали?
а) Проектный расчет
б) Проверочный расчет
1.3 Укажите детали, которые относятся к деталям машин общего
назначения:
а) Ротор
б) Поршень
в) Клапан
г) Патрон токарного станка
д) Детали общего назначения не перечислены
1.4 Что называется прочностью?
а) это способность детали сопротивляться изменению формы и размеров под действием нагрузок
б) способность детали сопротивляться действующим нагрузкам без разрушения или пластического деформирования
в) способность сохранять форму и размеры поверхности трения в течении срока эксплуатации
1.5 Что называется жесткостью?
а) это способность детали сопротивляться изменению формы и размеров под действием нагрузок
б) способность детали сопротивляться действующим нагрузкам без разрушения или пластического деформирования
|
в) способность сохранять форму и размеры поверхности трения в течении срока эксплуатации
Глава 2
Сварные соединения
Сварными называются соединения деталей, связанных в зоне контакта межатомными силами, которые возникают при местном сплавлении или совместном пластическом деформировании. Поэтому различают два вида сварки – плавлением и давлением.
При сварке плавлением детали в месте соединения доводятся до расплавленного состояния. Остывая, расплав формирует сварной шов.
При сварке давлением шов образуется в месте соединения деталей, доведенных до пластического состояния за счет приложения внешней силы.
|
Сварные соединения обладают высокой прочностью при статическом нагружении, хорошей технологичностью, герметичностью. Сопротивление сварных соединений усталости понижено вследствие наличия в швах концентраторов напряжений – трещин, непроваров, и т.д.
![]() |
а) б) в)
Рис. 2.1
По взаимному расположению соединяемых деталей различают стыковые, нахлесточные и угловые сварные соединения (рис. 2.1).
Сварные соединения проверяют на прочность по номинальным сечениям соединяемых деталей без учета утолщения швов.
Условие прочности имеет вид –
(4)
(5)
(6)
Нахлесточные сварные соединения подразделяют по взаимному положению сварного шва и направлению действующей нагрузки на лобовые, фланговые и комбинированные.
Для флангового шва (рис.2.1, а) можно получить –
или
, (7)
где k - катет,
lсум - суммарная длина сварного шва.
В прикладных расчетах лобовых швов используют условие прочности (2), пологая lсум = 2b (рис. 2.1 б).
h = k cos 450 = 0,7 k
lсум = 21
В случаем применения комбинированного шва приложенная нагрузка F воспринимается как его лобовой, так и фланговой частями -
, (8)
где Fл = 0,7klсумлtср¢, а Fф=0,7klсумфtср¢. Если ввести обозначение lсум = lсумл +lсумф, то при расчетах комбинированных сварных швов можно использовать условие прочности (2).
|
Для сваривания тонкостенных листовых конструкций часто используются точечные сварные соединения. Такие соединения проверяют на срез, принимая гипотезу о равномерном распределении нагрузки между силовыми точками.
Условие прочности имеет вид –
(9)
где d – диаметр, z – число силовых точек.
Заклепочные соединения
Для соединения листовых и профильных элементов конструкций корпусов, ферм, резервуаров давления и т.д. используется заклепочные соединения. В соответствии с обычными условиями эксплуатации основными нагрузками для них служат продольные силы, стремящиеся сдвинуть соединяемые детали одну относительно другой.
Заклепочные соединения обладают большей, чем сварные, прочностью при повторных ударных и вибрационных нагрузках, легче контролируются.
![]() |
Заклепка (Рис 2.2) представляет собой стержень круглого поперечного сечения с головками той или иной формы (в зависимости от условий работы соединения). Одну из них, закладную, выполняют на заготовке заранее. Вторую, замыкающую, формируют посредством обжимки при сборке. Располагалась в определенном порядке, заклепки образуют заклепочные швы. В соответствии с эксплуатационными требованиями (прочность, герметичность и т.д.) заклепочные соединения выполняют прочными, плотными, прочно-плотными, одно-, двух- и многорядными. Рядность соединения определяется количеством рядов отверстий под заклепки в детали, непосредственно воспринимающей нагрузку. По количеству одновременно перерезываемых в заклепке сечений различают одно-, двух- и многосрезные заклепочные соединения. По взаимному расположению соединяемых конструктивных элементов заклепочные соединения делятся на нахлесточные и стыковые – с одной или двумя накладками (рис. 2.3).
|
Рис. 2.3
Основные виды заклепочных соединений (Рис. 2.3): нахлесточные (а); стыковое (однорядное, односрезное) (б); стыковое (двухрядное, двухсрезное) с двумя накладками (в).
В прикладных расчетах полагают, что заклепки работают на смятие и срез. Действие напряжений изгиба и растяжения учитывают, как правило, с помощью поправочных коэффициентов, понижая допускаемые напряжения [s]см и [t]ср. Условие прочности на срез можно записать в виде –
(10)
Т.к. напряжения смятия в зоне контакта двух цилиндрических тел определяют поверхностью, равной площади проекции цилиндра на плоскость, перпендикулярную направлению действующей силы, условие прочности на смятие принимает вид –
(11)
Вопросы для самоконтроля
1. Какие виды сварки получили распространение в промышленности?
2. Какие различают типы сварных швов?
3. Как проводят расчет стыковых сварных швов?
4. Как выполняют расчет угловых сварных швов – лобовых, фланговых, комбинированных?
5. Какими преимуществами обладают сварные соединения по сравнению с заклепочными?
6. Какие различают заклепки по назначению и по форме их головок?
7. Какие заклепочные швы различают по назначению и по конструкции?
8. Что учитывается коэффициентом прочности заклепочного шва?
9. Как рассчитывают прочные и прочноплотные заклепочные швы?
Тесты к главе 2
2.1 Из перечисленных деталей назовите детали, которые относятся к группе “детали соединения”:
а) Муфты д) Валы
б) Шпонки
в) Заклепки
г) Подшипники
2.2 Какой способ сварки рекомендуется применить для соединения
толстых стальных листов внахлестку?
а) Газовую
б) Электродуговую
в) Контактную
2.3 Укажите наиболее простую конструкцию сварного соединения:
а) Внахлестку
б) Стыковое
в) Тавровое
г) Угловое
д) С накладками
2.4 Где применяются заклепочные соединения?
а) В корпусах судов
б) В фермах железнодорожных мостов
в) В авиастроении
г) В автомобилестроении
2.5 Какой вид неразъемного соединения стальных деталей имеет в
настоящее время наибольшее распространение
а) Заклепочное
б) Сварное
Глава 3
Разъемные соединения
Резьбовые соединения
Цилиндрическая резьба характеризуется следующими параметрами:
- формой и размером профиля;
- наружным, внутренним и средним диаметрами;
- шагом;
- числом заходов;
- углом подъема;
Профилем называют контур сечения резьбы плоскостью, проходящей через ее ось. По виду профиля различают резьбы метрические (в основе профиля лежит равносторонний треугольник); дюймовые (равнобедренный треугольник), разновидностью которых являются трубные (мелкие дюймовые); трапецеидальные (равнобочная трапеция); круглые и квадратные (рис. 3.6). Стандартизованы параметры всех резь, кроме квадратной.
Профиль резьбы характеризуется углом, теоретической и рабочей высотами (рис. 3.6). Угол профиля a - угол между его боковыми сторонами в осевой плоскости. Теоретическая высота профиля H – высота полного треугольного профиля, полученного условием продолжением его боковых сторон до их пересечения. Рабочая высота профиля h – высота, на которой происходит контакт витков резьбы винта и гайки.
Рис. 3.6
Наружный (номинальный) диаметр резьбы d – диаметр цилиндра, описанного вокруг ее вершин. Внутренний диаметр резьбы d1 – диаметр цилиндра, описанного вокруг ее впадин. Средний диаметр резьбы d2 - диаметр воображаемого цилиндра, на поверхности которого равны толщина витков и ширина впадин (рис. 3.6). По диаметру d2 резьбы контролируют при изготовлении.
Важнейшим параметром резьбы является ее шаг р – расстояние между одноименными точками профиля соседних витков в осевом направлении (рис. 3.6). Ход резьбы t определяется перемещением инструмента при ее изготовлении в осевом направлении за один оборот заготовки. Резьбы выполняют одно-, двух-, и многозаходными. Пусть число заходов равно, а. тогда ход резьбы составит
(16)
Широкое распространение в машиностроении получили разъемные Резьбовые соединения, собранные с помощью резьбовых крепежных элементов или резьб, выполненных непосредственно на соединяемых деталях.
Такие соединения обладают высокими несущей способностью и надежностью. Они характеризуются простой сборки-разборки и легкостью замены поврежденных элементов крепежа. Резьбовые соединения позволяют применять однотипные стандартные детали в различных машинах. Но их существенным недостатком является концентрация напряжений в резьбе, снижающая сопротивление циклическим нагрузкам.
К основным типам резьбовых элементов крепежа относятся болты, винты, шпильки, гайки и резьбовые вставки.
|
Болтовые соединения (рис. 3.7) используются для соединения деталей относительно небольшой толщины при наличии места для гайки и головки Если данные условия не выполняются, но в одной из деталей можно высверлить резьбовые отверстия, используют винтовые соединения (рис. 3.7).
В случае необходимости частой сборки-разборки подобного вида соединений, вызывающей изнашивание резьбовых отверстий в детали, вместо винтовых применяют шпилечные соединения (рис. 3.7) или в резьбовые отверстия вкручивают резьбовые вставки, которые представляют собой втулки из износостойких материалов с наружной и внутренней резьбой. Шпилечные соединения или резьбовые вставки обычно используют, когда материал детали с резьбовым отверстием не обладает высокой твердостью (легкие сплавы, пластмассы).
Головки болта, винтов и гайки в зависимости от назначения и конструктивных особенностей соединяемых деталей выполняются завинчивающим инструментом.
Наибольшую опасность для крепежных резь представляет срез витков по сечениям, показанным на (рис. 3.8).
В прикладных расчетах витков резьб винтов и гаек в целях упрощения полагают, что осевая нагрузка на винт Q распределяется между всеми виткам резьбы равномерно. Реально первый виток резьбы воспринимает более 30% всей нагрузки, а десятый – около 1%. Таким образом, выполнять число витков резьбы z более 10 нецелесообразно.
Если развернуть виток резьбы винта (гайки) на плоскость по диаметру d1(d), опасное сечение будет представлять собой прямоугольник со сторонами аср и pd1(pd).
Для витков резьбы винта и гайки –
(17)
, (18)
где kc = 1/pас = const – коэффициент, определяющий полноту профиля резьбы в отношении среза; H = z×p – высота гайки.
Значение коэффициента kc зависит от вида профиля резьбы. Его принимают равным 0,6…0,65 для трапецеидальных, 0,8 для квадратных и 0,87 для метрических резьб. Проверочный расчет витков резьбы на срез производят по формуле:
(19)
Вопросы для самоконтроля
1. Какие различают типы шпонок?
2. Каковы области применения шпонок различных типов?
3. Как определяют размеры шпонок?
4. Как проводят расчет призматических и сегментных шпонок?
5. Каковы преимущества шлицевых соединений по сравнению со шпоночными?
6. Как классифицируют шлицевые соединения и выполняют их расчет?
7. Как проводят расчеты соединений типа “вал - ступица”?
8. Какие различают типы резьб?
9. Какие типы резьб стандартизованы?
10. Почему для крепежных изделий применяют резьбу треугольного профиля?
11. Какие различают виды метрической резьбы?
12. Почему метрическая резьба с крупным шагом получила наибольшее распространение?
13. Когда применяют резьбы с мелким шагом?
14. Каковы геометрические параметры резьбы?
15. Какие используют резьбовые элементы крепежа, каковы области их применения и особенности конструктивного исполнения?
16. Какой формы выполняют головки болтов и винтов?
17. В каких случаях применяют шпильки и винты вместо болтов?
18. Как рассчитывают резьбу?
Тесты к главе 3
3.1 Назовите тип шпонки, наиболее приемлемой для вала с конической
поверхностью
а) Призматическая с плоским торцом
б) Призматическая с закругленным торцом
в) Сегментная
г) Клиновая без головки
д) Специальная
3.2 Материалы, применяемые для шпонок
а) Сталь углеродистая
б) Чугун
в) Латунь
г) Бронза
д) Сталь легированная
3.3 Каковы достоинства зубчатых соединений по сравнению со
шпоночными?
а) Имеют большую нагрузочную способность
б) Обеспечивается лучшее центрирование соединяемых деталей
в) Уменьшается длина ступицы
3.4 Зубчатые (шлицевые) соединения проверяют по условию прочности
на…
а) … изгиб
б) … кручение
в) … смятие
г) … срез
3.5 Что называется шагом резьбы?
а) Расстояние между двумя одноименными точками резьбы одной и
той же винтовой линии
б) Расстояние между двумя одноименными точками двух рядом
расположенных витков резьбы
Глава 4
Механические передачи
Большинство современных технологических машин как в пищевой промышленности, так и в других отраслях проектируют и создают по схеме: энергетическая машина, передаточный механизм, исполнительный орган машины, система управления.
Устройство, состоящее из двигателя, передаточных механизмов и системы управления для приведения в движение машин и механизмов называется приводом.
Угловые скорости двигателя wдв и рабочего органа машины wром, как правило, не равны. Электротехническая промышленность для общемашиностроительного применения выпускает электродвигатели с синхронной частотой вращения nC = 3000 мин-1, nC = 1500 мин-1,
nC = 1000 мин-1 и nC = 750 мин-1. Рабочие органы технологических машин функционируют при очень большом разнообразии угловых скоростей. Для решения этих противоречий применяют приводы. Ключевым звеном привода является передача.
Передачами в машинах называются устройства, служащие для передачи энергии механического движения на расстояние и преобразования его параметров. Общее назначение передач совмещается с выполнением частных функций, к числу которых относятся: распределение энергии, понижение или повышение скорости, преобразование видов движения (например, вращательного в поступательное или наоборот), регулирование скорости, пуск, остановки и реверсирование. Наиболее широкое распространение в технике получило вращательное движение, так как оно может быть осуществлено наиболее простыми способами.
Передачи используются как для понижения (редукции), так и для повышения угловой скорости двигателя до заданной угловой скорости рабочего звена (органа) машины. В зубчатых передачах первые, называются редукторами, а вторые – мультипликаторами.
По способу передачи движения от ведущего вала к ведомому различаются передачи трением и зацеплением; непосредственного касания (фрикционные, зубчатые, червячные, глобоидные, гипоидные, спироидные, волновые, винтовые) и с гибкой связью (ременные, зубчато-ременные, цепные); по назначению – кинематические и силовые; по взаимному расположению валов в пространстве – между параллельными, пересекающимися, перекрещивающимися и соосными осями валов. Выбор того или иного типа передачи обуславливается габаритами, массой и компоновочной схемой машины, режимом ее работы, частотой и направлением вращения ведущего и ведомого валов, пределами и условиями регулирования их скорости.
Поскольку
Р = Т×w w = (p×n) / 30, (24)
то (25)
Зубчатые передачи
Зубчатые передачи предназначены для передачи и преобразования вращательного движения с изменением угловых скоростей и крутящих моментов посредством зубчатого зацепления.
|
Зубчатые передачи между параллельными валами осуществляются с помощью цилиндрических зубчатых колес, образующие венцов которых параллельны осям валов. Наиболее широкое применение в технике нашли цилиндрические зубчатые колеса с прямыми,косыми и шевронными зубьями (рис. 4.1 а,б,в).
Рис. 4.1
Если оси валов пересекаются, для передачи используются конические зубчатые колеса с прямыми, круговыми (рис. 4.1 г.д. ) и (реже) косыми
(рис. 4.1 е) зубьями.
Когда оси валов перекрещиваются, применяются комбинированные зубчато-винтовые передачи, наиболее распространенным видом которых является червячная, состоящая из ведущего червяка 1, представляющего собой силовой винт, и ведомого червячного колеса 2 (рис. 4.1 ж).
По сравнению с другими механическими передачами зубчатые обладают следующими преимуществами:
- относительно малыми габаритами и высокими (до 0,985) КПД;
- сравнительно большой долговечностью и надежностью в работе;
- постоянством передаточного отношения вследствие практического отсутствия проскальзывания;
- возможностью применения для широкого диапазона крутящих моментов, угловых скоростей и передаточных отношений.
Наибольшее распространение получили зубчатые передачи с эвольвентным профилем зуба.
Эвольвентные зубчатые колеса могут быть нарезаны инструментом, имеющим прямолинейный профиль зубьев. Такие колеса удобны для контроля. Кроме того, эвольвентное зацепление допускает корригирование (улучшение профиля зубьев), т.е. использование таких участков эвольвенты, которые обеспечивают наилучшую работу передачи и позволяют устранить возможные при нарезании дефекты зубьев (подрез ножки и заострение головки).
4.3. Прямозубые цилиндрические передачи
Часть зубчатого колеса, содержащая все зубья, связанные друг с другом прилегающей к ним поверхностью тела зубчатого колеса, называется зубчатым венцом.
Червячные передачи
Силы в зацеплении
В приработанной червячной передаче, как и в зубчатых передачах, нагрузка воспринимается не одним, а несколькими зубьями колеса. Для упрощения расчета силу взаимодействия червяка и колеса принимают сосредоточенной приложенной в полюсе зацепления П по нормали к рабочей поверхности витка. По правилу параллелепипеда Fn раскладывают по трем взаимно перпендикулярным направлениям на составляющие Ff1, Fr1, Fa1. Окружная сила на червяке Ff1 числено равна осевой силе на червячным колесе: (84)
где Т1 - вращающий момент на червяке, Н×м; d1- делительный диаметр червяка, мм.
Радиальная сила на червяке Fr1 числено равна радиальной силе на колесе Fr2:
Fr1= Fr2= Fr1tga (85)
Осевая сила на червяке Fa1 числено равна окружной силе Ft2 на червячном колесе:
(86)
где Т2 – вращающий момент на червяке, Н×м; d2 – длительный диаметр червяка, мм.
Вопросы для самоконтроля
1. Для чего необходимы механические передачи?
2. По каким признакам классифицируют передачи?
3. Какие виды передач получили наибольшее распространение и каковы их основные характеристики?
4. Что такое передаточное отношение?
5. Каковы главные достоинства зубчатых передач по сравнению с другими механическими передачами?
6. Какие различают виды зубчатых колес и каковы области их применения?
7. Почему наибольшее распространение получили зубчатые передачи с эвольвентным профилем боковых поверхностей зубьев?
8. Что такое шаг и модуль зубчатого колеса?
9. Как определяют делительный диаметр зубчатого колеса?
10. Как вычисляют диаметры вершин и впадин рабочего венца зубчатого колеса?
11. Какое максимальное передаточное отношение позволяет получить одна пара зубчатых колес в зависимости от ее вида?
12. Как определяют силы давления на валы со стороны зубчатых колес?
13. Какие критерии лежат в основе расчетов зубчатых колес на прочность?
14. По какому модулю производится расчет на прочность зубьев конических зубчатых колес?
15. Какими достоинствами и недостатками обладают червячные передачи по сравнению с зубчатыми?
16. Каковы области применения червячных передач?
17. Какая существует зависимость между передаточным отношением, числом заходов червяка и количеством зубьев червячного колеса?
18. Из каких материалов изготавливают червяки и червячные колеса?
Тесты к главе 4
Рис. 4.12
4.1 Передача 10 – 11(см. рис. 4.12) имеет валы, расположенные в
пространстве:
а) параллельные
б) пересекающиеся
в) перекрещивающиеся
г) определить нельзя
4.2 Показать на (см. рис. 4.12) коническую зубчатую
передачу:
а) 2 - 3
б) 4 -5
в) 6 -7
г) 10 – 11
д) 12 – 13
4.3 Покажите на (см. рис. 4.12) машину - орудие (цифрами 1,
П,ПI,IV).
а) I
б) П
в) ПI
г) IV
4.4 Показать на (см. рис. 4.12) ведущее колесо третьей пары.
а) 3
б) 4
в) 5
г) 6
д) 7
4.5 Передача 4 - 5 (см. рис. 4.12) понижающая или повышающая?
а) Понижающая
б)Повышающая
4.6 Сколько ступней имеет передача, показанная на рис. 4.12?
а) 1
б) 2
в) 6
г) 12
Глава 5
Валы и опоры
Валы и оси
Валы и оси предназначены для поддерживания вращающихся элементов машин – зубчатых колес, шкивов, звездочек и т.д. Конструктивно оси и прямые валы, представляющие собой детали цилиндрический формы (иногда с коническими участками), различаются мало.
Характер работы валов и осей принципиально различен: оси воспринимают только изгибающие нагрузки, а валы работают на кручение и изгиб, передавая полезные крутящие моменты. Силовые
|
|
Индивидуальные очистные сооружения: К классу индивидуальных очистных сооружений относят сооружения, пропускная способность которых...
История развития хранилищ для нефти: Первые склады нефти появились в XVII веке. Они представляли собой землянные ямы-амбара глубиной 4…5 м...
Архитектура электронного правительства: Единая архитектура – это методологический подход при создании системы управления государства, который строится...
Наброски и зарисовки растений, плодов, цветов: Освоить конструктивное построение структуры дерева через зарисовки отдельных деревьев, группы деревьев...
© cyberpedia.su 2017-2024 - Не является автором материалов. Исключительное право сохранено за автором текста.
Если вы не хотите, чтобы данный материал был у нас на сайте, перейдите по ссылке: Нарушение авторских прав. Мы поможем в написании вашей работы!