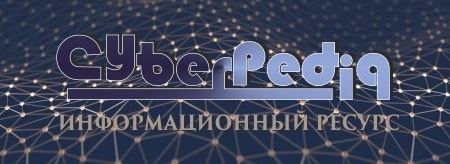
Опора деревянной одностоечной и способы укрепление угловых опор: Опоры ВЛ - конструкции, предназначенные для поддерживания проводов на необходимой высоте над землей, водой...
Своеобразие русской архитектуры: Основной материал – дерево – быстрота постройки, но недолговечность и необходимость деления...
Топ:
Процедура выполнения команд. Рабочий цикл процессора: Функционирование процессора в основном состоит из повторяющихся рабочих циклов, каждый из которых соответствует...
Устройство и оснащение процедурного кабинета: Решающая роль в обеспечении правильного лечения пациентов отводится процедурной медсестре...
Интересное:
Наиболее распространенные виды рака: Раковая опухоль — это самостоятельное новообразование, которое может возникнуть и от повышенного давления...
Инженерная защита территорий, зданий и сооружений от опасных геологических процессов: Изучение оползневых явлений, оценка устойчивости склонов и проектирование противооползневых сооружений — актуальнейшие задачи, стоящие перед отечественными...
Как мы говорим и как мы слушаем: общение можно сравнить с огромным зонтиком, под которым скрыто все...
Дисциплины:
![]() |
![]() |
5.00
из
|
Заказать работу |
|
|
К соединениям типа «Вал-ступица» относятся разъемные шпоночные и шлицевые (зубчатые). Они предназначены для передачи вращательного движения и крутящего момента от валов к присоединенным деталям и наоборот.
Шпоночные соединения сравнительно просты и надежны, технологичны, обеспечивают относительное удобство сборки-разборки. Их недостатком является наличие у валов и ступиц шпоночных пазов, ослабляющих сечения соединяемых деталей и вызывающих значительную концентрацию напряжений, что понижает сопротивление валов усталости.
По конструкции шпонки подразделяются на: призматические, сегментные, клиновые. Геометрические параметры всех типов шпонок стандартизованы. Наибольшее распространение получили призматические шпонки.
В зависимости от назначения их разделяют на обыкновенные, направляющие и специальные. Как правило, призматические шпонки бывают
трех исполнений (рис.3.1):
Рис.3.1
Рабочими поверхностями призматических шпонок являются боковые грани. В прикладных расчетах полагают, что призматические шпонки работают на смятие и срез (рис.3.2).
Рис. 3.2
Условие прочности на срез –
, (12)
где Т – передаваемый крутящий момент. Поэтому проверочный расчет шпонок на срез по формуле (12) выполняют только для ответственных соединений.
Условие прочности при смятии -
(13)
Допускаемые напряжения [s]см выбирают в зависимости от материалов соединяемых деталей и шпонок. Для стальных валов, ступиц и шпонок принимают [s]см = 120…180 МПа.
Соединения сегментными шпонками, представляющими собой пластины в форме части диска (рис. 3.3), по принципу работы аналогичны соединениям призматическими шпонками. По сравнению с ними они более технологичны, но значительнее ослабляют валы. Проверочные расчеты таких соединений производят на срез и реже на смятие.
|
|
Рис. 3.3
|
Клиновые шпонки (рис. 3.4) представляют собой клинья с уклоном рабочих поверхностей 1:100 и позволяют передавать как крутящий момент, так и осевую силу, создавая натяг между валом и ступицей.
Рис. 3.4
Но применение таких шпонок вызывает перекос соединяемых деталей. Кроме того, происходит радиальное смещение ступицы по отношению к валу, что приводит к биениям. Поэтому область применения клиновых шпонок ограничивается тихоходными передачами невысокой точности.
Шлицевые соединения образуются при вхождении выступов–зубьев на валах в соответствующие впадины-пазы на ступицах. Такие соединения можно рассматривать как многошпоночные, учитывая, что шпонки в данном случае Рис. 3.5 Шлицевые соединения. Типы зубьев.
представляют одно целое с валами. Шлицы выполняют прямобочного, эвольвентного и треугольного профилей (рис. 3.5). Параметры шлицевых соединений стандартизованы (кроме соединений с зубьями треугольного профиля.
Шлицевым соединениям присуще лучшие, чем шпоночным, нагрузочная способность (вследствие большей рабочей поверхности контакта и равномерности распределения давления по высоте зубьев), сопротивление валов усталости (за счет отсутствия шпоночных пазов и меньшей концентрации напряжений), технологичность и точность.
При использовании шлицевых соединений прямобочного профиля применяют три вида центрирования:
- по боковым граням (наименее точное, но обеспечивающее наибольшую нагрузочную способность);
- по наружному диаметру D (используется для ступицы малой твердости);
- по внутреннему диаметру d.
При решении прикладных задач шлицевые соединения проверяют на смятие. Условие прочности имеет вид –
(14)
где y - коэффициент, учитывающий неравномерность распределения нагрузки между шлицами; l – длина поверхностей контакта зубьев на валу с пазами в ступице; h – высота данных поверхностей; dcp – их средний диаметр; z – количество зубьев.
|
Параметры h и dcp определяются в зависимости от профиля зубьев. Например, для шлицевых соединений прямобочного профиля значения h и dcp соответственно составляют –
и
(15)
Резьбовые соединения
Цилиндрическая резьба характеризуется следующими параметрами:
- формой и размером профиля;
- наружным, внутренним и средним диаметрами;
- шагом;
- числом заходов;
- углом подъема;
Профилем называют контур сечения резьбы плоскостью, проходящей через ее ось. По виду профиля различают резьбы метрические (в основе профиля лежит равносторонний треугольник); дюймовые (равнобедренный треугольник), разновидностью которых являются трубные (мелкие дюймовые); трапецеидальные (равнобочная трапеция); круглые и квадратные (рис. 3.6). Стандартизованы параметры всех резь, кроме квадратной.
Профиль резьбы характеризуется углом, теоретической и рабочей высотами (рис. 3.6). Угол профиля a - угол между его боковыми сторонами в осевой плоскости. Теоретическая высота профиля H – высота полного треугольного профиля, полученного условием продолжением его боковых сторон до их пересечения. Рабочая высота профиля h – высота, на которой происходит контакт витков резьбы винта и гайки.
Рис. 3.6
Наружный (номинальный) диаметр резьбы d – диаметр цилиндра, описанного вокруг ее вершин. Внутренний диаметр резьбы d1 – диаметр цилиндра, описанного вокруг ее впадин. Средний диаметр резьбы d2 - диаметр воображаемого цилиндра, на поверхности которого равны толщина витков и ширина впадин (рис. 3.6). По диаметру d2 резьбы контролируют при изготовлении.
Важнейшим параметром резьбы является ее шаг р – расстояние между одноименными точками профиля соседних витков в осевом направлении (рис. 3.6). Ход резьбы t определяется перемещением инструмента при ее изготовлении в осевом направлении за один оборот заготовки. Резьбы выполняют одно-, двух-, и многозаходными. Пусть число заходов равно, а. тогда ход резьбы составит
(16)
|
Широкое распространение в машиностроении получили разъемные Резьбовые соединения, собранные с помощью резьбовых крепежных элементов или резьб, выполненных непосредственно на соединяемых деталях.
Такие соединения обладают высокими несущей способностью и надежностью. Они характеризуются простой сборки-разборки и легкостью замены поврежденных элементов крепежа. Резьбовые соединения позволяют применять однотипные стандартные детали в различных машинах. Но их существенным недостатком является концентрация напряжений в резьбе, снижающая сопротивление циклическим нагрузкам.
К основным типам резьбовых элементов крепежа относятся болты, винты, шпильки, гайки и резьбовые вставки.
|
Болтовые соединения (рис. 3.7) используются для соединения деталей относительно небольшой толщины при наличии места для гайки и головки Если данные условия не выполняются, но в одной из деталей можно высверлить резьбовые отверстия, используют винтовые соединения (рис. 3.7).
В случае необходимости частой сборки-разборки подобного вида соединений, вызывающей изнашивание резьбовых отверстий в детали, вместо винтовых применяют шпилечные соединения (рис. 3.7) или в резьбовые отверстия вкручивают резьбовые вставки, которые представляют собой втулки из износостойких материалов с наружной и внутренней резьбой. Шпилечные соединения или резьбовые вставки обычно используют, когда материал детали с резьбовым отверстием не обладает высокой твердостью (легкие сплавы, пластмассы).
Головки болта, винтов и гайки в зависимости от назначения и конструктивных особенностей соединяемых деталей выполняются завинчивающим инструментом.
Наибольшую опасность для крепежных резь представляет срез витков по сечениям, показанным на (рис. 3.8).
В прикладных расчетах витков резьб винтов и гаек в целях упрощения полагают, что осевая нагрузка на винт Q распределяется между всеми виткам резьбы равномерно. Реально первый виток резьбы воспринимает более 30% всей нагрузки, а десятый – около 1%. Таким образом, выполнять число витков резьбы z более 10 нецелесообразно.
|
Если развернуть виток резьбы винта (гайки) на плоскость по диаметру d1(d), опасное сечение будет представлять собой прямоугольник со сторонами аср и pd1(pd).
Для витков резьбы винта и гайки –
(17)
, (18)
где kc = 1/pас = const – коэффициент, определяющий полноту профиля резьбы в отношении среза; H = z×p – высота гайки.
Значение коэффициента kc зависит от вида профиля резьбы. Его принимают равным 0,6…0,65 для трапецеидальных, 0,8 для квадратных и 0,87 для метрических резьб. Проверочный расчет витков резьбы на срез производят по формуле:
(19)
Вопросы для самоконтроля
1. Какие различают типы шпонок?
2. Каковы области применения шпонок различных типов?
3. Как определяют размеры шпонок?
4. Как проводят расчет призматических и сегментных шпонок?
5. Каковы преимущества шлицевых соединений по сравнению со шпоночными?
6. Как классифицируют шлицевые соединения и выполняют их расчет?
7. Как проводят расчеты соединений типа “вал - ступица”?
8. Какие различают типы резьб?
9. Какие типы резьб стандартизованы?
10. Почему для крепежных изделий применяют резьбу треугольного профиля?
11. Какие различают виды метрической резьбы?
12. Почему метрическая резьба с крупным шагом получила наибольшее распространение?
13. Когда применяют резьбы с мелким шагом?
14. Каковы геометрические параметры резьбы?
15. Какие используют резьбовые элементы крепежа, каковы области их применения и особенности конструктивного исполнения?
16. Какой формы выполняют головки болтов и винтов?
17. В каких случаях применяют шпильки и винты вместо болтов?
18. Как рассчитывают резьбу?
Тесты к главе 3
3.1 Назовите тип шпонки, наиболее приемлемой для вала с конической
поверхностью
а) Призматическая с плоским торцом
б) Призматическая с закругленным торцом
в) Сегментная
г) Клиновая без головки
д) Специальная
3.2 Материалы, применяемые для шпонок
а) Сталь углеродистая
б) Чугун
в) Латунь
г) Бронза
д) Сталь легированная
3.3 Каковы достоинства зубчатых соединений по сравнению со
шпоночными?
а) Имеют большую нагрузочную способность
б) Обеспечивается лучшее центрирование соединяемых деталей
в) Уменьшается длина ступицы
3.4 Зубчатые (шлицевые) соединения проверяют по условию прочности
|
на…
а) … изгиб
б) … кручение
в) … смятие
г) … срез
3.5 Что называется шагом резьбы?
а) Расстояние между двумя одноименными точками резьбы одной и
той же винтовой линии
б) Расстояние между двумя одноименными точками двух рядом
расположенных витков резьбы
Глава 4
Механические передачи
Большинство современных технологических машин как в пищевой промышленности, так и в других отраслях проектируют и создают по схеме: энергетическая машина, передаточный механизм, исполнительный орган машины, система управления.
Устройство, состоящее из двигателя, передаточных механизмов и системы управления для приведения в движение машин и механизмов называется приводом.
Угловые скорости двигателя wдв и рабочего органа машины wром, как правило, не равны. Электротехническая промышленность для общемашиностроительного применения выпускает электродвигатели с синхронной частотой вращения nC = 3000 мин-1, nC = 1500 мин-1,
nC = 1000 мин-1 и nC = 750 мин-1. Рабочие органы технологических машин функционируют при очень большом разнообразии угловых скоростей. Для решения этих противоречий применяют приводы. Ключевым звеном привода является передача.
Передачами в машинах называются устройства, служащие для передачи энергии механического движения на расстояние и преобразования его параметров. Общее назначение передач совмещается с выполнением частных функций, к числу которых относятся: распределение энергии, понижение или повышение скорости, преобразование видов движения (например, вращательного в поступательное или наоборот), регулирование скорости, пуск, остановки и реверсирование. Наиболее широкое распространение в технике получило вращательное движение, так как оно может быть осуществлено наиболее простыми способами.
Передачи используются как для понижения (редукции), так и для повышения угловой скорости двигателя до заданной угловой скорости рабочего звена (органа) машины. В зубчатых передачах первые, называются редукторами, а вторые – мультипликаторами.
По способу передачи движения от ведущего вала к ведомому различаются передачи трением и зацеплением; непосредственного касания (фрикционные, зубчатые, червячные, глобоидные, гипоидные, спироидные, волновые, винтовые) и с гибкой связью (ременные, зубчато-ременные, цепные); по назначению – кинематические и силовые; по взаимному расположению валов в пространстве – между параллельными, пересекающимися, перекрещивающимися и соосными осями валов. Выбор того или иного типа передачи обуславливается габаритами, массой и компоновочной схемой машины, режимом ее работы, частотой и направлением вращения ведущего и ведомого валов, пределами и условиями регулирования их скорости.
|
|
Индивидуальные очистные сооружения: К классу индивидуальных очистных сооружений относят сооружения, пропускная способность которых...
Организация стока поверхностных вод: Наибольшее количество влаги на земном шаре испаряется с поверхности морей и океанов (88‰)...
Своеобразие русской архитектуры: Основной материал – дерево – быстрота постройки, но недолговечность и необходимость деления...
История создания датчика движения: Первый прибор для обнаружения движения был изобретен немецким физиком Генрихом Герцем...
© cyberpedia.su 2017-2024 - Не является автором материалов. Исключительное право сохранено за автором текста.
Если вы не хотите, чтобы данный материал был у нас на сайте, перейдите по ссылке: Нарушение авторских прав. Мы поможем в написании вашей работы!