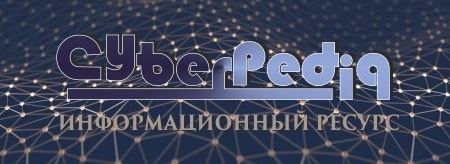
Биохимия спиртового брожения: Основу технологии получения пива составляет спиртовое брожение, - при котором сахар превращается...
История развития хранилищ для нефти: Первые склады нефти появились в XVII веке. Они представляли собой землянные ямы-амбара глубиной 4…5 м...
Топ:
Выпускная квалификационная работа: Основная часть ВКР, как правило, состоит из двух-трех глав, каждая из которых, в свою очередь...
История развития методов оптимизации: теорема Куна-Таккера, метод Лагранжа, роль выпуклости в оптимизации...
Характеристика АТП и сварочно-жестяницкого участка: Транспорт в настоящее время является одной из важнейших отраслей народного...
Интересное:
Искусственное повышение поверхности территории: Варианты искусственного повышения поверхности территории необходимо выбирать на основе анализа следующих характеристик защищаемой территории...
Лечение прогрессирующих форм рака: Одним из наиболее важных достижений экспериментальной химиотерапии опухолей, начатой в 60-х и реализованной в 70-х годах, является...
Аура как энергетическое поле: многослойную ауру человека можно представить себе подобным...
Дисциплины:
![]() |
![]() |
5.00
из
|
Заказать работу |
|
|
ТЕХНОЛОГИЧЕСКАЯ ИНСТРУКЦИЯ
ТИ 102 – СТ.К – 278 – 2013
Н.Тагил
2013
Открытое акционерное общество
«ЕВРАЗ Нижнетагильский металлургический комбинат»
УТВЕРЖДАЮ
Главный инженер ЕВРАЗ НТМК
В.А. Сизов
«» 2013
ВНЕПЕЧНАЯ ОБРАБОТКА СТАЛИ НА УСТАНОВКАХ
ВАКУУМИРОВАНИЯ № 1, № 2 КОНВЕРТЕРНОГО ЦЕХА № 1
ТЕХНОЛОГИЧЕСКАЯ ИНСТРУКЦИЯ
ТИ 102 – СТ.К – 278 – 2013
(Взамен ТИ 102 – СТ.К – 81 – 2011,
ТИ 102 – СТ.К – 318 – 2012,
в части вакуумирования в циркуляционном вакууматоре)
РАЗРАБОТАНА | |
Начальник технического управления М.С. Фомичев | |
И.о. начальника конвертерного цеха № 1 В.М. Кулик |
Всего страниц 34
ОАО «ЕВРАЗ НТМК» | Технологическая инструкция «Внепечная обработка стали на установках вакуумирования № 1, № 2 конвертерного цеха № 1» | ТИ 102 - СТ.К - 278 - 2013 Взамен ТИ 102 - СТ.К - 81 - 2011, ТИ 102 - СТ.К - 318 - 2012, в части вакуумирования в циркуляционном вакууматоре |
Настоящая технологическая инструкция устанавливает технологию обработки стали на установках вакуумирования (вакууматор) № 1, № 2 конвертерного цеха № 1.
Инструкция разработана на основе опыта эксплуатации установок вакуумирования.
Инструкция предназначена для подручных сталевара, сталеваров, сменных мастеров, мастеров, старшего мастера участка внепечной обработки стали (ВОС) конвертерного цеха № 1 (КЦ № 1), обслуживающего персонала КЦ № 1.
Контроль за соблюдением требований настоящей технологической инструкции осуществляют начальник КЦ № 1, старший мастер участка ВОС КЦ № 1, старший мастер участка УТК КЦ № 1.
|
Перечень ссылочных документов приведен в приложении А.
ТЕХНИЧЕСКИЕ ХАРАКТЕРИСТИКИ ОБОРУДОВАНИЯ
1.1 Технические характеристики оборудования установок вакуумирования № 1, № 2 приведены в приложении Б.
ОСНОВНЫЕ МАТЕРИАЛЫ И ТРЕБОВАНИЯ, ПРЕДЪЯВЛЯЕМЫЕ К НИМ
2.1 Основные материалы, применяемые при внепечной обработке стали, указаны в приложении В.
Газы
2.2.1 Аргон газообразный по ГОСТ 10157.
2.2.2 Азот, чистота 99,5 %, по ГОСТ 9293.
2.2.3 Сжатый воздух, температура + 20 °С.
2.2.4 Природный газ.
2.2.5 Технический кислород с содержанием O2 не менее 99,5 %.
2.2.6 Сухой, перегретый пар, температура от + 190 °С до + 200 °С.
Разработана техническим управлением, КЦ № 1 | Внесена техническим управлением | Срок действия с до |
Требования, предъявляемые к используемым материалам
2.3.1 Используемые на установках вакуумирования легирующие и раскислители должны иметь размер кусков от 10 до 50 мм.
2.3.2 Фракция шлакообразующих материалов от 10 до 70 мм.
2.3.3 Влажность используемых материалов не должна превышать 1,0 %.
ПОДГОТОВКА ОБОРУДОВАНИЯ И СИСТЕМ
ТЕХНОЛОГИЧЕСКОГО ОБЕСПЕЧЕНИЯ
3.1 При подготовке вакууматоров к работе необходимо проверить:
- исправность всех механизмов, средств измерений, футеровки камеры и патрубков;
- исправность трайб-аппаратов;
- исправность работы установки дожигания окиси углерода (СО) и работы контрольно-измерительных приборов;
- наличие необходимого количества ферросплавов и других материалов в загрузочных бункерах для ведения технологического процесса;
- обеспеченность энергоресурсами (пар, вода, азот, аргон, кислород, сжатый воздух). Давление (пара, азота, аргона, кислорода) - в соответствии с таблицей 1;
- герметичность уплотнений, готовность средств отбора проб и замера температуры стали, устройств контроля окисленности стали и содержания водорода;
|
- степень нагрева футеровки. Температура газов в камере вакууматора № 1 должна быть не менее 1250 °С, температура футеровки - не менее 1000 °С. Температура футеровки камеры вакууматора № 2 должна быть не менее 1150 °С.
Таблица 1
Энергоресурс | Давление, бар, не менее | |
Вакууматор № 1 | Вакууматор № 2 | |
Пар | 10,0 | |
Аргон | 14,0 | |
Азот | 4,5 | 8,0 |
Кислород | 16,0 |
3.2 Перед обработкой стали на установке вакуумирования необходимо обеспечить:
- заполнение бункеров необходимыми материалами с химическим, фракционным составом и влажностью согласно нормативной и технической документации (НТД);
- наличие алюминиевой и необходимых порошковых проволок;
- исправную работу системы загрузки и разгрузки материалов, энергетических систем, систем контроля, управления и сигнализации;
- наличие на рабочей площадке средств отбора проб металла, контроля температуры и содержания кислорода в стали;
- исправную работу установки дожигания СО;
- включение и исправную работу аспирационной установки для очистки отходящих газов при подаче легирующих материалов, стенда ввода алюминиевой и порошковой проволоки и системы подачи утепляющей смеси.
3.3 Разогрев новой футеровки вакуум-камеры или после ремонта нижней ее части производится согласно графикам, представленным в приложении Г.
3.4 Плавки, предназначенные для обработки на установке вакуумирования, сливаются в сталеразливочный ковш с просушенной и исправной футеровкой. Верхний край ковша (обортовка и шлаковый пояс) должен быть чистым.
3.5 Во время выпуска плавки из конвертера в сталеразливочный ковш производится отсечка конвертерного шлака, обеспечивающая его минимальное попадание в сталеразливочный ковш. Толщина слоя конвертерного шлака в сталеразливочном ковше должна быть не более 100 мм (определяется визуально).
3.6 Расстояние от верхней кромки ковша до уровня шлака в сталеразливочном ковше должно быть не более 400 мм и не менее 250 мм (определяется визуально).
3.7 При недостаточном уровне металла в сталеразливочном ковше (расстояние от верхней кромки ковша до уровня шлака в сталеразливочном ковше более 400 мм) допускается его корректировка путем налива остатков металла из ковша предыдущей плавки аналогичной марки стали.
Не допускается производить перелив металла из ковша с неисправным механизмом кантовки, с «заросшей» или «закозленной» обортовкой.
|
Масса металла в ковше при переливе должна быть не более 13 т.
3.8 После слива плавки из конвертера, отбора пробы металла и замера температуры сталеразливочный ковш выдается в разливочный пролет и передается в пролет участка внепечной обработки стали. При проведении вакуумирования стали перед обработкой на установке «печь-ковш», длительность передвижения ковша после слива металла из конвертера до позиции обработки на вакууматоре должна быть не более 25 мин.
Время передачи сталеразливочного ковша с установки «печь-ковш» на вакууматор не должно превышать 15 мин. Время между окончанием обработки металла на установке вакуумирования и началом разливки металла на МНЛЗ должно обеспечивать серийность разливки и не превышать 20 мин. Увеличение указанного выше времени производится по согласованию со сменным мастером МНЛЗ или начальником смены.
3.9 За 20 - 30 мин до вакуумирования первой плавки в серии производится тестирование вакуумных насосов для проверки их готовности к работе и разогрев вакуумной системы.
При температуре окружающей среды ниже минус 10 °С тестирование вакуумных насосов производится не реже одного раза в час.
3.10 За 3 - 7 мин до начала вакуумной обработки производится предварительное вакуумирование системы, при котором включаются три водокольцевых насоса и создается остаточное давление в системе 70 - 200 мбар при закрытом вакуумном шибере.
ОБЩИЕ ТРЕБОВАНИЯ ПРИ ВАКУУМНОЙ ДЕГАЗАЦИИ МЕТАЛЛА
4.1 По прибытии сталеразливочного ковша на установку вакуумирования, в систему автоматизации УРОВЕНЬ 2 вводятся данные номера плавки, марки стали, ориентировочной массы металла в сталеразливочном ковше.
4.2 Перед началом вакуумной обработки металла производится замер содержания водорода в металле.
Измерение содержания водорода в жидкой стали производится при помощи системы «Hydris» фирмы «Herаeus Electro-Nite». Правила работы с системой «Hydris» и порядок проведения измерения водорода в стали определяются МУ 102-142-51.
|
4.3 Для циркуляции металла в вакуум-камере в впускной патрубок подается аргон.
При производстве металла с регламентированным содержанием азота по верхнему и нижнему пределу, в качестве транспортирующего газа может применяется азот.
4.4 В процессе вакуумирования, через каждые 5 - 7 мин, производится измерение температуры металла.
Снижение температуры металла в процессе вакуумирования первой плавки после ремонта или простоя вакууматора может составляет до 2 °С/мин, последующих плавок в серии - до 1,5 °С/мин.
4.5 Продолжительность вакуумирования определяется по таблице 2.
Таблица 2
Требуемое содержание водорода, ppm, не более | Продолжительность вакуумирования, мин, не менее |
1,0 | 25 |
1,5 | 20 |
2,0 | 15 |
2,5 | 10 |
3,0 | 8 |
Примечание - Остаточное давление в камере не более 3 мбар. |
4.6 Химический состав металла, при необходимости, может корректироваться перед и после окончания вакуумной обработки вводом порошковой и алюминиевой проволоки.
Во время вакуумирования корректировка химического состава металла может производиться отдачей кусковых легирующих материалов из бункеров.
Отбор проб на химический анализ производится не ранее, чем через 5 мин после окончания присадки науглераживателя, ферросплавов и раскислителей.
Коэффициент усвоения базовых элементов во время вакуумирования, %:
углерод...................................................................................................................... 93-100;
кремний...................................................................................................................... 75-95;
марганец..................................................................................................................... 90-100;
ванадий....................................................................................................................... 95-100;
титан........................................................................................................................... 50-75;
никель......................................................................................................................... 90-100;
молибден.................................................................................................................... 90-100.
4.7 Не позднее 10 мин после окончания вакуумирования в металл вводится порошковая кальцийсодержащая проволока (кроме марок стали, на которых, согласно НТД, ввод кальцийсодержащих материалов производится на установках «печь-ковш»). При этом металл продувается аргоном (азотом) без оголения зеркала металла.
Продолжительность продувки металла аргоном (азотом) после окончания ввода кальцийсодержащей проволоки должна составлять не менее 3 мин, для колесо-бандажного металла - не менее 5 мин, металла для производства рельсов - не менее 10 мин.
4.8 Перед передачей сталеразливочного ковша на МНЛЗ производится замер содержания водорода в металле.
4.9 Температура металла в сталеразливочном ковше перед подачей его на МНЛЗ должна соответствовать указанной в технологической документации и заказу сменного мастера МНЛЗ для данной марки стали.
|
При получении температуры металла меньше, чем необходимо для разливки на МНЛЗ, сталеразливочный ковш снова подается на установку «печь-ковш» для доводки по температуре.
4.10 При передаче металла на МНЛЗ № 1, № 3, в сталеразливочный ковш, на поверхность шлака, для утепления металла равномерно подается теплоизолирующая смесь.
Расход теплоизолирующей смеси для плавок, предназначенных для разливки на МНЛЗ № 1:
- сортамент транспортного назначения - не менее десяти мешков на ковш (не менее 100 кг на ковш);
- остальной сортамент – не менее шести мешков на ковш (не менее 60 кг на ковш).
Расход теплоизолирующей смеси для плавок, предназначенных для разливки на МНЛЗ № 3:
- двухручьевой вариант разливки - не менее десяти мешков на ковш (не менее 100 кг на ковш);
- четырехручьевой вариант разливки – не менее шести мешков на ковш (не менее 60 кг на ковш).
4.11 После отдачи теплоизолирующей смеси на ковш устанавливается крышка (кроме МНЛЗ, оборудованных стационарными крышками) и ковш подается на МНЛЗ.
4.12 После каждой вакуумной обработки металла производится осмотр состояния патрубков вакууматора. При износе наружной или внутренней огнеупорной футеровки производится ее торкретирование.
Расход торкретмассы на торкретирование определяется в зависимости от степени износа футеровки патрубков.
Выполнение работ по торкретированию с указанием времени и длительности проведения работ, расхода торкрет-массы отражается в агрегатном журнале.
Контроль за исполнением требований по торкретированию патрубков вакуум – камеры осуществляет сменный мастер участка внепечной обработки стали конвертерного цеха.
4.13 Во время вакуумной дегазации в вакуум-камерах образуются шлакометаллические скрапины, которые удаляются (отжигаются) газокислородной горелкой, отжиг скрапины производят после вакуумирования 40-50 плавок.
4.14 По окончании отжига скрапины, длительного перерыва в работе установки вакуумирования, а также после ремонта огнеупорной футеровки вакуум-камеры рекомендуется проводить вакуумирование плавки рядового сортамента в режиме дегазации в течение 5-10 мин, до обработки на установке «печь-ковш».
4.15 При невозможности обработки первой плавки на вакууматоре до обработки на установке «печь-ковш», плавка готовится с учетом следующих требований.
4.15.1 Содержание углерода должно быть выше нижнего предела не менее, чем на 0,05 %.
4.15.2 Содержание марганца и кремния должно быть близко к верхнему пределу или не менее чем на 0,10 % выше нижнего предела.
4.15.3 После вакуумирования металла в течение 7-10 мин производится отбор пробы для определение химического состава стали. При отклонении химического состава от требований НТД, металл доводится по химическому составу на вакууматоре или возвращается на установку «печь-ковш» для доводки по химическому составу и температуре.
4.16 При невозможности вакуумирования рядового металла первой плавкой после очистки или длительного простоя вакууматора, допускается вакуумирование транспортного металла со следующими дополнениями.
4.16.1 Температура металла в сталеразливочном ковше после слива из конвертера должна быть не менее чем на 25 °С выше установленной для данной марки стали.
4.16.2 Плавка из конвертерного отделения передается на вакууматор, производится вакуумирование в течение 5-10 мин с последующей передачей металла на установку «печь-ковш».
4.16.3 После обработки на установке «печь-ковш» производится повторное вакуумирование плавки.
4.17 Во время обработки на установках вакуумирования серии плавок, в межплавочный период газокислородная горелка для разогрева футеровки вакуум-камеры включается в работу сразу после окончания обработки или завершения операции торкретирования и находится в режиме поддержания необходимой температуры футеровки вакуум-камеры до начала обработки следующей плавки.
|
|
Историки об Елизавете Петровне: Елизавета попала между двумя встречными культурными течениями, воспитывалась среди новых европейских веяний и преданий...
Кормораздатчик мобильный электрифицированный: схема и процесс работы устройства...
Общие условия выбора системы дренажа: Система дренажа выбирается в зависимости от характера защищаемого...
Организация стока поверхностных вод: Наибольшее количество влаги на земном шаре испаряется с поверхности морей и океанов (88‰)...
© cyberpedia.su 2017-2024 - Не является автором материалов. Исключительное право сохранено за автором текста.
Если вы не хотите, чтобы данный материал был у нас на сайте, перейдите по ссылке: Нарушение авторских прав. Мы поможем в написании вашей работы!