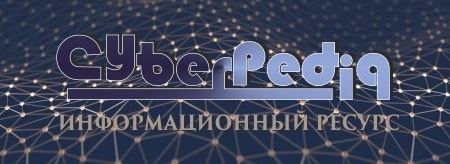
Поперечные профили набережных и береговой полосы: На городских территориях берегоукрепление проектируют с учетом технических и экономических требований, но особое значение придают эстетическим...
Организация стока поверхностных вод: Наибольшее количество влаги на земном шаре испаряется с поверхности морей и океанов (88‰)...
Топ:
Выпускная квалификационная работа: Основная часть ВКР, как правило, состоит из двух-трех глав, каждая из которых, в свою очередь...
История развития методов оптимизации: теорема Куна-Таккера, метод Лагранжа, роль выпуклости в оптимизации...
Техника безопасности при работе на пароконвектомате: К обслуживанию пароконвектомата допускаются лица, прошедшие технический минимум по эксплуатации оборудования...
Интересное:
Наиболее распространенные виды рака: Раковая опухоль — это самостоятельное новообразование, которое может возникнуть и от повышенного давления...
Как мы говорим и как мы слушаем: общение можно сравнить с огромным зонтиком, под которым скрыто все...
Отражение на счетах бухгалтерского учета процесса приобретения: Процесс заготовления представляет систему экономических событий, включающих приобретение организацией у поставщиков сырья...
Дисциплины:
![]() |
![]() |
5.00
из
|
Заказать работу |
|
|
Введение
Техническая диагностика - область знаний, включающая в себя сведения о методах и средствах оценки технического состояния машин, механизмов, оборудования, конструкций и других технических объектов.
Основной задачей технического диагностирования объектов НГП является сокращение затрат на техническое обслуживание объектов, и на уменьшение потерь от простоя в результате отказов.
Диагностирование технических объектов включает в себя следующие функции:
· оценка технического состояния объекта;
· обнаружение и определение места локализации неисправностей;
· прогнозирование остаточного ресурса объекта;
· мониторинг технического состояния объекта.
Требования, предъявляемые к техническим системам и объектам:
· Высокая производительность при обеспечении качества, точности и условий эксплуатации.
· Малая металлоемкость и габаритные размеры. Технологичность конструкции.
· Простота обслуживания и ремонта.
· Приемлемая стоимость.
· Качество и конкурентоспособность.
Целью данного расчетно-графического задания является изучение основ надежности и диагностирования машин и оборудования НГП на примере компрессора КТ-6 в объеме, позволяющем получить общие методические представления, знания, умения и компетенции по перечисленным вопросам для умения использовать эти знания и компетенции в будущей инженерной деятельности.
Задачи:
Изучить основы диагностирования;
Технические объекты НГП;
Методы и средства диагностики
Особенности диагностирования КТ- 6
Оценка показателей надежности
1. Общие вопросы и проблемы КТС и диагностики изделий НГП
Компрессор нефтяной диагностирование
|
Основы ДТС
Техническая диагностика - область знаний, включающая в себя сведения о методах и средствах оценки технического состояния машин, механизмов, оборудования, конструкций и других технических объектов.
Целью технической диагностики являются определение возможности и условий дальнейшей эксплуатации диагностируемого оборудования и в конечном итоге повышение промышленной и экологической безопасности
Диагностирование проводят как при ТО, так и при ремонте.
При ТО задачи диагностирования заключаются в том, чтобы установить потребность в проведении капитального или текущего ремонта машины или ее сборочных единиц; качество функционирования механизмов и систем машин; перечень работ, которые необходимо выполнить при очередном техническом обслуживании.
При ремонте машин задачи диагностирования сводятся к выявлению сборочных единиц, подлежащих восстановлению, а также оценке качества ремонтных работ.
Диагностирование технических объектов включает в себя следующие функции:
· оценка технического состояния объекта;
· обнаружение и определение места дефектов и локализации неисправностей;
· прогнозирование остаточного ресурса объекта;
· мониторинг технического состояния объекта.
Различают прямые и косвенные диагностические параметры. Первые непосредственно характеризуют состояние объекта, а вторые связаны с прямыми параметрами функциональной зависимостью.
При проведении технического диагностирования выделяют две основные проблемы:
· вероятность пропуска неисправности;
· вероятность «ложной тревоги», то есть вероятность ложного сигнала о наличии неисправности.
Чем выше вероятность «ложной тревоги», тем меньше вероятность пропуска неисправности, и наоборот. Задача технической диагностики состоит в нахождении «золотой середины» между этими двумя проблемами.
Системы диагностирования
Совокупность средств диагностирования, объекта и исполнителей, действующих по установленным алгоритмам, называется системой диагностирования.
|
Алгоритм - это совокупность предписаний, определяющих последовательность действий при диагностировании, т.е. алгоритм устанавливает порядок проведения проверок состояния элементов объекта и правила анализа их результатов. Причем безусловный алгоритм диагностирования устанавливает заранее определенную последовательность проверок, а условный - в зависимости от результатов предыдущих проверок.
Системы диагностирования предназначаются для контроля работоспособности, проверки правильности функционирования и поиска дефектов. В соответствии с ГОСТ 20417-75 устанавливаются следующие основные области применения систем диагностирования:
) в процессе производства изделия: при наладке и приеме;
) в процессе эксплуатации изделия: при техническом обслуживании на стадиях хранения, транспортирования и использования;
) перед ремонтом или после ремонта изделия.
В процессе эксплуатации диагностирование призвано обеспечить проведение технического обслуживания и ремонта двигателей по их фактическому техническому состоянию. Диагностирование двигателя проводится в следующей последовательности: выполнение подготовительных работ - измерение диагностических параметров - оценка и прогнозирование технического состояния составных частей - принятие решения об объеме технического обслуживания или ремонта.
При техническом обслуживании или ремонте не допускаются восстановительные операции агрегатов двигателя, если значения их диагностических параметров находятся в допустимых пределах. В этом случае восстановительные и регулировочные работы соответствующего вида технического обслуживания откладывают до следующего технического обслуживания, а текущий или капитальный ремонт проводят по истечении наработки, назначенной на основе прогнозирования остаточного ресурса.
Применяемые методы контроля и ДТС
Для разработки методов и средств технической диагностики какой-либо машины, прежде всего, следует выявить, какие параметры характеризуют работу проверяемой машины и определяют ее надежность. Затем надо установить диагностические критерии количественной величины параметров и для их определения разработать соответствующие методы и средства.
|
Методы и средства диагностики отдельных агрегатов, систем и механизмов определяются их конструкцией и выполняемыми функциями.
В зависимости от вида диагностических параметров применяют следующие методы технической диагностики: измерение потерь на трение в механизмах; определение теплового состояния механизмов; проверка состояния сопряжения, установочных размеров, герметичности и утечек, контроль шума и вибраций в работе механизма; анализ картерного масла (двигателя, ротора, вертлюга и др.).
Компрессор КТ-6
Компрессор КТ-6 - двухступенчатый, трехцилиндровый. поршневой с W- образным расположением цилиндров.
Компрессор КТ-6 состоит из корпуса (картера) 13, двух цилиндров 29 низкого давления (ЦНД), имеющих угол развала 120°. одного цилиндра 6 высокого давления (ЦВД) и холодильника 8 радиаторного типа с предохранительным клапаном 10, узла шатунов 7 и поршней 2, 5.
Рисунок 2.1.1 - Компрессор КТ-6
Корпус 18 имеет три привалочных фланца для установки цилиндров и два люка для доступа к деталям, находящимся внутри. Сбоку к корпусу прикреплен масляный насос 20 с редукционным клапаном 21, а в нижней части корпуса помещен сетчатый масляный фильтр 25. Передняя часть корпуса (со стороны привода) закрыта съемной крышкой, в которой расположен один из двух шарикоподшипников коленчатого вала 19. Второй шарикоподшипник расположен в корпусе со стороны масляного насоса. Все три цилиндра имеют ребра: ЦВД выполнен с горизонтальным оребрением для лучшей теплоотдачи, а ЦНД имеют вертикальные ребра для придания цилиндрам большей жесткости. В верхней части цилиндров расположены клапанные коробки 1 и 4. Система смазки компрессора комбинированная: под давлением смазываются шатунная шейка коленчатого вала, пальцы прицепных шатунов и поршневые пальцы; остальные детали смазываются разбрызгиванием. Масло заливается в картер компрессора через отверстие в боковой крышке, закрываемое пробкой 27 (или через патрубок сапуна 3). Уровень масла контролируется маслоуказателем автомобильного типа.
Подача смазки осуществляется масляным насосом лопастного типа. Масляный насос состоит из крышки, корпуса и фланца, соединенных четырьмя шпильками и центрируемых двумя штифтами.
|
Цилиндры низкого давления расположены так, что в то время когда в левом цилиндре происходит всасывание воздуха, в правом происходит его нагнетание в холодильник, и наоборот. Из холодильника воздух всасывается в цилиндр высокого давления, где происходит его дальнейшее сжатие.
Таблица 1 - Технические характеристики компрессора
Наименование параметров | Норма для компрессора | |
Тип компрессора | W-образный, поршневой двухступенчатый, однорядный с воздушным охлаждением оборудован устройством для перевода на холостой ход. | |
Производительность по всасыванию, м³/мин | 5,3 | |
Давление нагнетания, кгс/см² | 9 | |
Частота вращения коленчатого вала, об/мин | 850 | |
Мощность потребляемая при частоте вращения, кВт: | ||
850 об/мин | 44,1 | |
750 об/мин | 39 | |
440 об/мин | 22,8 | |
Количество цилиндров | 3 | |
Охлаждение компрессора | воздушное | |
Режим работы при давлении нагнетания ПВ, %: | ||
5 кгс/см² | 100 | |
9 кгс/см² | 50 | |
Направление вращения коленчатого вала (смотреть со стороны привода) - по часовой стрелке (КТ7 - против часовой стрелки). | ||
Привод - от электродвигателя или ДВС через эластичную муфту | ||
Габаритные размеры, мм: | КТ6; КТ7 | КТ6Эл |
длина | 760 | 760 |
ширина | 1320 | 1255 |
высота | 1050 | 1050 |
Масса (без масла и ЗИП), кг | 610 | 600 |
Особенности эксплуатации компрессора
Длительная нормальная работа компрессора может быть обеспечена только при соответствующем уходе за ним, заключающемся в соблюдении предусмотренных технической характеристикой параметров его работы; внимательном ежедневном наблюдении за состоянием и работой компрессора и его узлов; своевременном устранении неисправностей и принятии профилактических мер для их предупреждения. В процессе эксплуатации нужно следить за сохранением установленной величины зазоров между сопрягаемыми подвижными деталями компрессора, так как при увеличенных зазорах начинается ускоренный износ деталей. Увеличение зазоров сопровождается появлением стуков и одновременным снижением давления масла в компрессоре.
ПОДГОТОВКА К ПУСКУ
Проверить уровень масла в картере компрессора, который должен быть между рисками на маслоуказателе.
Для смазки применять масла, разрешаемые настоящим паспортом, так как применение других масел может вызвать повышенное нагарообразование на клапанах или полное стекание масла со стенок цилиндров.
Температура масла в компрессоре перед пуском должна быть не ниже +15 С.
Осмотрите компрессор для выявления течи масла, состояние креплений, соединений и пр.
ПУСК
После монтажа при первом пуске компрессор должен работать 10... 15 мин. при открытых кранах на главных воздушных резервуарах. После этого краны должны быть закрытыми и компрессор переведён в работу под нагрузкой.
|
При каждом пуске компрессора:
а) откройте сливные краны и продуйте холодильник;
б) по манометру, установленному на компрессоре, проверьте
давление масла, которое должен быть 1,5...6кгс/см (компрессор
должен быть прогрет).
в) убедитесь в отсутствии посторонних шумов и стуков;
КОНТРОЛЬ ВО ВРЕМЯ РАБОТЫ
Работа компрессора сопровождается шумом определённой низкой тональности. С переходом компрессора с рабочего на холостой ход и обратно (тепловозный режим) уровень шума незначительно меняется. Во время работы компрессора посторонний шум или стуки показывают, что в компрессоре появился дефект.
При работе компрессора периодически:
а) проверяйте на слух, не слышны ли в компрессоре повышенный шум и стуки;
б) по манометру, установленному на компрессоре, контролируйте давление масла;
в) проверяйте, не выбрасывает ли компрессор масло через воздушные фильтры.
Дефекты и неисправности КТ-6
Основная причина поломок компрессоров - некачественный монтаж, неправильная эксплуатация. Практика ремонта показала, что они обладают сравнительно низкой ремонтопригодностью. Наиболее распространенной причиной выхода компрессора из строя является износ и повреждение поверхностей трущихся деталей. Вследствие износа увеличиваются зазоры между деталями, нарушается правильность их взаимного расположения, возникают дополнительные динамические нагрузки. Это приводит к ухудшению эксплуатационных свойств компрессора, а в отдельных случаях и к полному выходу его из строя. Так износ деталей узла трения цилиндр-поршень уменьшает хладопроизводительность холодильного агрегата, узла трения коленвал-плунжер масленого насоса нарушает нормальный режим смазки, узла трения палец-поршень вызывает появление шума.
Дефекты цилиндра. Эффективность работы компрессора в большой степени зависит от состояния цилиндра. Износ рабочей поверхности характеризуется увеличением диаметра и искажением формы цилиндра. Даже при незначительном износе его зеркальная поверхность может оказаться матовой и на ней появятся риски, царапины, задиры. При значительном износе изменяется форма цилиндра: вместо цилиндрической она становится овальной, конической. Поршень плохо прижимается к стенкам изношенного цилиндра и частично пропускает пары холодильного агента из одной полости в другую, в результате понижается производительность компрессора и возникает повышенный шум. У изношенного цилиндра в верхней части нарушается нормальная смазка из-за стекания масла, поэтому диаметральный износ цилиндра по высоте оказывается наибольшим в верхней его части.
Дефекты поршня. В процессе эксплуатации поршня отверстие в бобышках для поршневого пальца увеличивается и искажается их форма. Рабочая поверхность поршня изнашивается неравномерно больше в плоскости, перпендикулярной оси вала, причем наибольший износ происходит в момент действия силы в конце хода поршня при сжатии холодильного агента. В результате увеличения размера отверстия под поршневой палец появляется стук в компрессоре.
Дефекты коленчатого вала. В процессе работы холодильного агрегата происходит неравномерный износ шеек вала, который зависит от характера нагрузки на вал. Наибольшая нагрузка имеет место в конце хода поршня при сжатии хладагента. Из-за неравномерного износа шейки вала в сечении становятся овальными. Возникающее при этом биение вала не только нарушает работу компрессора, но и приводит к быстрой разработке подшипника, сопровождаемой стуком. При овальности шатунной шейки вала будет происходить неравномерный износ головок шатуна. При совершении одного оборота вал прижимается к верхней головке во время прямого хода поршня и крышке нижней головки шатуна во время обратного хода. Поэтому зазор и ось шейки вала изменяют свое положение относительно центра нижней головки: они будут находиться соответственно выше или ниже центра. Овальность шатунной шейки вала увеличивает его биение. Это приводит к ускорению выработки, как головок шатуна, так и шатунной шейки. Шатунная шейка может быть перекошенной относительно оси вала. В таком случае возникают следующие дефекты: быстрая разработка верхней головки шатуна, местный износ рабочей поверхности цилиндра в верхней и нижней частях. Некачественная смазка или ее отсутствие приводят к задирам и схватыванию.
Дефекты подшипников скольжения. Из-за разработки подшипников скольжения зазор между статором и ротором электродвигателя может исчезнуть, и тогда они будут представлять собой трущуюся пару. Такое явление может привести к заклиниванию двигателя при его пуске в компрессорах.
Дефекты шатуна. Шатун при работе изнашивается неравномерно вследствие неодинаковой нагрузки на вал в течение одного оборота. Характер износа шатуна определяется износом шатунной шейки коленчатого вала. Изменение условий смазки предопределяет возникновение задиров и схватываний. Износ рабочей поверхности шатуна приводит к исчезновению смазочной канавки.
Дефекты клапанов. От качественной работы клапанов в значительной степени зависит производительность компрессора. Клапаны изготовляются из высококачественных материалов, однако они довольно быстро изнашиваются. Их основные дефекты: износ пластинки (коробление, выкрашивание) или рабочего пояса нагнетательного клапана. Вследствие этих дефектов ухудшается уплотняющая способность клапана, снижается хладопроизводительность компрессора и повышается температура нагнетания.
3. Методы и средства контроля и диагностики поршневых компрессоров
Метод измерений - прием или совокупность приемов сравнения измеряемой физической величины с ее единицей в соответствии с реализованным принципом измерений. Обычно метод измерений обусловлен устройством средства измерений. Различают: дифференциальный, нулевой, контактный и бесконтактный методы измерений, а также методы сравнения с мерой и метод непосредственной оценки.
Таблица - 4.3
Примечание. Знак "+" означает применяемость, знак "-" - неприменяемость, знак "±" - применяемость по усмотрению разработчика.
Порядок технического диагностирования технического объекта:
Рис. 4.3 - Порядок технической диагностики
Заключение
Диагностирование - это процесс определения и контроля технического состояния объекта.
Определяющим фактором качества машин и оборудования является надёжность, проблемы которой решаются на всех стадиях жизненного цикла.
Надежность - это свойство объекта сохранять во времени в установленных пределах сохранять все параметры, обеспечивающие выполнение требуемых функций в заданных условиях эксплуатации.
Техническое диагностирование является на данный момент одним из важнейших показателей, необходимых для контроля состояния оборудования на всех стадиях его жизненного цикла. Стадия жизненного цикла изделия включает ряд этапов, начиная от зарождения идеи нового продукта до его утилизации по окончании срока использования.
Повышение надёжности зависит в каждом случае от многочисленных факторов, правильно выбранных методов и способов повышения надёжности, которые позволяют значительно повысить эффективность работы оборудования.
Результатом данной работы является выполнение поставленных задач, а именно:
· Закреплены знания по общим вопросам и проблемам КТС и диагностики изделий НГП;
· Исследованы: особенности эксплуатации, дефекты и неисправности, а также устройство и принцип действия компрессора КТ-6;
· Представлены методы и средства контроля и диагностики поршневых компрессоров;
· Изучены методы повышения надежности компрессоров и их элементов
· Разработано техническое предложение по повышению надежности.
Введение
Техническая диагностика - область знаний, включающая в себя сведения о методах и средствах оценки технического состояния машин, механизмов, оборудования, конструкций и других технических объектов.
Основной задачей технического диагностирования объектов НГП является сокращение затрат на техническое обслуживание объектов, и на уменьшение потерь от простоя в результате отказов.
Диагностирование технических объектов включает в себя следующие функции:
· оценка технического состояния объекта;
· обнаружение и определение места локализации неисправностей;
· прогнозирование остаточного ресурса объекта;
· мониторинг технического состояния объекта.
Требования, предъявляемые к техническим системам и объектам:
· Высокая производительность при обеспечении качества, точности и условий эксплуатации.
· Малая металлоемкость и габаритные размеры. Технологичность конструкции.
· Простота обслуживания и ремонта.
· Приемлемая стоимость.
· Качество и конкурентоспособность.
Целью данного расчетно-графического задания является изучение основ надежности и диагностирования машин и оборудования НГП на примере компрессора КТ-6 в объеме, позволяющем получить общие методические представления, знания, умения и компетенции по перечисленным вопросам для умения использовать эти знания и компетенции в будущей инженерной деятельности.
Задачи:
Изучить основы диагностирования;
Технические объекты НГП;
Методы и средства диагностики
Особенности диагностирования КТ- 6
Оценка показателей надежности
1. Общие вопросы и проблемы КТС и диагностики изделий НГП
компрессор нефтяной диагностирование
Основы ДТС
Техническая диагностика - область знаний, включающая в себя сведения о методах и средствах оценки технического состояния машин, механизмов, оборудования, конструкций и других технических объектов.
Целью технической диагностики являются определение возможности и условий дальнейшей эксплуатации диагностируемого оборудования и в конечном итоге повышение промышленной и экологической безопасности
Диагностирование проводят как при ТО, так и при ремонте.
При ТО задачи диагностирования заключаются в том, чтобы установить потребность в проведении капитального или текущего ремонта машины или ее сборочных единиц; качество функционирования механизмов и систем машин; перечень работ, которые необходимо выполнить при очередном техническом обслуживании.
При ремонте машин задачи диагностирования сводятся к выявлению сборочных единиц, подлежащих восстановлению, а также оценке качества ремонтных работ.
Диагностирование технических объектов включает в себя следующие функции:
· оценка технического состояния объекта;
· обнаружение и определение места дефектов и локализации неисправностей;
· прогнозирование остаточного ресурса объекта;
· мониторинг технического состояния объекта.
Различают прямые и косвенные диагностические параметры. Первые непосредственно характеризуют состояние объекта, а вторые связаны с прямыми параметрами функциональной зависимостью.
При проведении технического диагностирования выделяют две основные проблемы:
· вероятность пропуска неисправности;
· вероятность «ложной тревоги», то есть вероятность ложного сигнала о наличии неисправности.
Чем выше вероятность «ложной тревоги», тем меньше вероятность пропуска неисправности, и наоборот. Задача технической диагностики состоит в нахождении «золотой середины» между этими двумя проблемами.
Системы диагностирования
Совокупность средств диагностирования, объекта и исполнителей, действующих по установленным алгоритмам, называется системой диагностирования.
Алгоритм - это совокупность предписаний, определяющих последовательность действий при диагностировании, т.е. алгоритм устанавливает порядок проведения проверок состояния элементов объекта и правила анализа их результатов. Причем безусловный алгоритм диагностирования устанавливает заранее определенную последовательность проверок, а условный - в зависимости от результатов предыдущих проверок.
Системы диагностирования предназначаются для контроля работоспособности, проверки правильности функционирования и поиска дефектов. В соответствии с ГОСТ 20417-75 устанавливаются следующие основные области применения систем диагностирования:
) в процессе производства изделия: при наладке и приеме;
) в процессе эксплуатации изделия: при техническом обслуживании на стадиях хранения, транспортирования и использования;
) перед ремонтом или после ремонта изделия.
В процессе эксплуатации диагностирование призвано обеспечить проведение технического обслуживания и ремонта двигателей по их фактическому техническому состоянию. Диагностирование двигателя проводится в следующей последовательности: выполнение подготовительных работ - измерение диагностических параметров - оценка и прогнозирование технического состояния составных частей - принятие решения об объеме технического обслуживания или ремонта.
При техническом обслуживании или ремонте не допускаются восстановительные операции агрегатов двигателя, если значения их диагностических параметров находятся в допустимых пределах. В этом случае восстановительные и регулировочные работы соответствующего вида технического обслуживания откладывают до следующего технического обслуживания, а текущий или капитальный ремонт проводят по истечении наработки, назначенной на основе прогнозирования остаточного ресурса.
Применяемые методы контроля и ДТС
Для разработки методов и средств технической диагностики какой-либо машины, прежде всего, следует выявить, какие параметры характеризуют работу проверяемой машины и определяют ее надежность. Затем надо установить диагностические критерии количественной величины параметров и для их определения разработать соответствующие методы и средства.
Методы и средства диагностики отдельных агрегатов, систем и механизмов определяются их конструкцией и выполняемыми функциями.
В зависимости от вида диагностических параметров применяют следующие методы технической диагностики: измерение потерь на трение в механизмах; определение теплового состояния механизмов; проверка состояния сопряжения, установочных размеров, герметичности и утечек, контроль шума и вибраций в работе механизма; анализ картерного масла (двигателя, ротора, вертлюга и др.).
|
|
Биохимия спиртового брожения: Основу технологии получения пива составляет спиртовое брожение, - при котором сахар превращается...
Кормораздатчик мобильный электрифицированный: схема и процесс работы устройства...
Историки об Елизавете Петровне: Елизавета попала между двумя встречными культурными течениями, воспитывалась среди новых европейских веяний и преданий...
Автоматическое растормаживание колес: Тормозные устройства колес предназначены для уменьшения длины пробега и улучшения маневрирования ВС при...
© cyberpedia.su 2017-2024 - Не является автором материалов. Исключительное право сохранено за автором текста.
Если вы не хотите, чтобы данный материал был у нас на сайте, перейдите по ссылке: Нарушение авторских прав. Мы поможем в написании вашей работы!