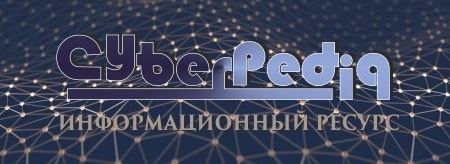
Поперечные профили набережных и береговой полосы: На городских территориях берегоукрепление проектируют с учетом технических и экономических требований, но особое значение придают эстетическим...
Кормораздатчик мобильный электрифицированный: схема и процесс работы устройства...
Топ:
Оценка эффективности инструментов коммуникационной политики: Внешние коммуникации - обмен информацией между организацией и её внешней средой...
Марксистская теория происхождения государства: По мнению Маркса и Энгельса, в основе развития общества, происходящих в нем изменений лежит...
Интересное:
Лечение прогрессирующих форм рака: Одним из наиболее важных достижений экспериментальной химиотерапии опухолей, начатой в 60-х и реализованной в 70-х годах, является...
Инженерная защита территорий, зданий и сооружений от опасных геологических процессов: Изучение оползневых явлений, оценка устойчивости склонов и проектирование противооползневых сооружений — актуальнейшие задачи, стоящие перед отечественными...
Влияние предпринимательской среды на эффективное функционирование предприятия: Предпринимательская среда – это совокупность внешних и внутренних факторов, оказывающих влияние на функционирование фирмы...
Дисциплины:
![]() |
![]() |
5.00
из
|
Заказать работу |
|
|
Выбор способа и средств для измерения геометрических размеров зависит от ряда факторов, основными из которых являются:
допуски на размеры и точность изготовления измеряемой детали;
метод контроля (пассивный или активный) и его точность;
объем выпуска деталей;
конструктивные особенности детали и экономические показатели назначаемых средств измерения (стоимость прибора, его производительность, время настройки, требуемая квалификация контролера).
Для обеспечения взаимозаменяемости деталей и узлов различных изделий создана единая система допусков и посадок. Эта система охватывает нормы взаимозаменяемости всех типов соединений, включая электрические. Основу единой системы допусков и посадок (ЕСДП) составляют ряды допусков, называемые квалитетами и ряды основных отклонений, определяющих положение полей допусков относительно линии номинального размера
3.1 Методы диагностирования изделий
В зависимости от технических средств и диагностических параметров, которые используют при проведении диагностирования, можно составить следующий неполный список методов диагностирования:
· органолептические методы диагностирования, которые основаны на использовании органов чувств человека (осмотр, ослушивание);
· вибрационные методы диагностирования, которые основаны на анализе параметров вибраций технических объектов;
· акустические методы диагностирования, основанные на анализе параметров звуковых волн, генерируемых техническими объектами и их составными частями;
· тепловые методы; сюда же относятся методы диагностирования, основанные на использовании тепловизоров;
· специфические методы для каждой из областей техники (например, при диагностировании гидропривода широко применяется статопараметрический метод, основанный на анализе задросселированного потока жидкости; в электротехнике применяют методы, основанные на анализе параметров электрических сигналов, и т. д.).
|
Визуальный конроль
На опасных производственных объектах визуальный и измерительный контроль регламентируется руководящим документом РД 03-606-03. Визуальный контроль - это единственный вид неразрушающего контроля, который может быть выполнен без какого-либо оборудования с использованием простейших измерительных средств.
Дефекты диагностируемого объекта и отклонения от заданной геометрической формы, обнаруженные при визуальном контроле, подлежат измерению с помощью различных измерительных инструментов и визуально-оптических приборов. Для измерения малых дефектов используются стандартные измерительные инструменты, применяемые в машиностроении: линейки, рулетки, штангенциркули глубиномеры, струны, отвесы, шаблоны и др. Визуальный контроль с применением оптических средств называют визуально-оптическим. Применение оптических средств позволяет существенно расширить пределы естественных возможностей человеческого зрения: производить измерения с более высокой точностью, обнаруживать более мелкие дефекты, осуществлять контроль в недоступных для человека местах закрытых конструкций. В зависимости от увеличения разрешающая способность при этом может достигать 1...5 мкм.
Приборы для визуально-оптического контроля подразделяются на три группы:
· для контроля близко расположенных объектов (лупы, микроскопы);
· для контроля удаленных объектов (зрительные трубы, бинокли, телескопы);
· для контроля закрытых объектов (эндоскопы).
В процессе технической диагностики чаще всего применяют дальномеры, нивелиры, теодолиты и тахеометры (рис. 3.1.1).
Дальномер служит для определения расстояния до заданной цели. Первые оптические дальномеры имели два объектива, разнесенные на некоторое расстояние между собой. С помощью системы линз и зеркал изображения объекта контроля от разных объективов передавались в один окуляр и накладывались друг на друга.
|
Рисунок 3.1.1 - Геодезические оптико-электронные приборы:
а - цифровой нивелир DiNi 22; 6 - электронный теодолит DJD5-1; в - электронный тахеометр DTM-352W
3.1.2 Тепловой контроль
Методы теплового вида контроля (по ГОСТ 23483-79) основаны на взаимодействии теплового поля объекта с термометрическим чувствительным элементом (термопарой, фоторезистором, термоиндикаторами, пирокристаллом и т.п.) и преобразовании параметров поля (интенсивности, температурного градиента, контраста, лучистостей и др.) в параметры электрического или другого сигнала и передаче его на регистрирующий прибор.
Тепловой вид неразрушающего контроля включает в себя методы инфракрасной дефектоскопии и пирометрии.
Инфракрасная дефектоскопия нашла применение в гражданской промышленности лишь в конце 1970-х гг. Метод основан на том, что в местах дефектов металла подогретого объекта или в зонах утонения стенок трубопровода с подогретой средой тепло передается от внутренней к внешней поверхности стенки несколько в большей степени, чем в окружающих бездефектных зонах. Тепловизор преобразует картину теплового распределения на поверхности объекта в видеоизображение. Чувствительность современных тепловизоров исчисляется десятыми долями градуса. Внешний вид некоторых тепловидеокамер показан на рис. 3.1.2. Все приборы снабжены лазерным указателем рассматриваемой зоны.
а б в
Рисунок 3.1.2 - Современные модели тепловизоров: а - «SAT S-160»; б - «SAT S-280»; в - «SAT HY-6800»; г - «SAT G-90».
Пирометрия - дистанционное измерение температуры объекта, применяется в литейном производстве для оценки температуры расплавов и в теплоэнергетике. Выполняется более простыми приборами - пирометрами (рис. 3.1.2.1).
А б в
Рисунок 3.1.2.1 - Пирометр марки «Кельвин»: а - внешний вид; б, в - измерение температуры паропроводов
Преимущества аппаратных средств пирометрии заключаются в выведении оператора из зоны действия повышенной температуры.
Вибрационный контроль
|
Вибрационная диагностика основана на измерении и анализе параметров вибрации диагностируемого оборудования и занимает особое место среди прочих видов диагностики.
При изменении параметров вибрации используют два метода измерения: кинематический и динамический.
Кинематический метод заключается в том, что измеряют координаты точек объекта относительно выбранной неподвижной системы координат. Измерительные преобразователи, основанные на этом методе измерения, называют преобразователями относительной вибрации.
Динамический метод основан на том, что параметры вибрации измеряют относительно искусственной неподвижной системы отчета, в большинстве случаях инерционного элемента, связанного с объектом через упругий подвес.
В настоящее время большинство ответственных роторных машин оснащено контрольно-сигнальной виброаппаратурой (КСА), позволяющей регистрировать в контролируемых точках среднеквадратическое отклонение виброскорости в рабочей полосе частот 10...1000 Гц, автоматически включать предупредительную сигнализацию или отключать машины при достижении предельно допустимого уровня вибрации. При отсутствии КСА дежурный персонал производит измерения переносными виброметрами.
Современные системы вибромониторинга, разрабатываемые рядом организаций (ВАСТ, ТНТ и др.), предусматривают наряду с методикой измерения и обработки вибросигналов использование специализированного программного обеспечения по диагностике оборудования различных типов.
Применение таких программ обеспечивает автоматизированную диагностику неисправностей. Так, на рис. 3.1.3 приведена схема точек измерения вибрации газоперекачивающего агрегата КТ-6, оснащенного системой вибромониторинга, разработанного отечественной фирмой «ИНКОТЕС» (г. Нижний Новгород).
Рис. 3.1.3 - Схема точек измерения вибрации (температуры) компрессора КТ-6
Типовая программа диагностирования роторных машин, не оснащенных системами вибромониторинга, включает следующие основные этапы:
1. Изучение и анализ технической и эксплуатационной документации и результатов оперативного контроля.
|
2. Визуальный осмотр машины и фундамента, проверка состояния соединительных муфт, уплотнений и других элементов, оценка функциональной работоспособности машины по параметрическим критериям и КПД, проверка работоспособности вспомогательного оборудования, систем управления и контроля, снятие контурной характеристики машины.
3.Разработка индивидуальной программы диагностирования и графика проведения работ с учетом конструктивных особенностей машины и условий ее эксплуатации.
4.Подключение в назначенных контрольных точках и тарировка вибродиагностической аппаратуры, регистрация параметров вибрации подшипников, корпуса, фундамента. Расшифровка и анализ спектральных составляющих вибросигналов.
5.Контроль основных узлов и деталей роторной машины неразрушающими методами (при необходимости).
6.Обследование состояния фундамента и строительных конструкций здания. Обследование проводится в том случае, если при предварительном осмотре установлено нарушение их целостности или выявлены изменения вибрационной характеристики системы «ротор-фундамент» (оценка состояния фундамента и строительных конструкций здания производится по соответствующим методикам).
7.Окончательная обработка и анализ результатов контроля, принятие решения: продолжение эксплуатации машины, вывод ее в ремонт или замена на новую.
Преимущества:
1. метод позволяет находить скрытые дефекты;
2. метод, как правило, не требует сборки-разборки оборудования;
. малое время диагностирования;
. возможность обнаружения неисправностей на этапе их зарождения.
Недостатки:
. особые требования к способу крепления датчика вибрации;
. зависимость параметров вибрации от большого количества факторов и сложность выделения вибрационного сигнала.
Средства КТС и ДТС
На данный момент существует множество приборов для измерения вибрации, представляющие собой как переносные, так и стационарные системы. Атлант-8 - многоканальный синхронный регистратор и анализатор вибросигналов (виброанализатор).
Рис. 3.2 - Атлант-8 - многоканальный синхронный регистратор и анализатор вибросигналов (виброанализатор).
Многоканальный синхронный регистратор-анализатор вибросигналов Атлант-8 является современным прибором, предназначенным для решения наиболее сложных задач в вибрационной диагностике состояния оборудования. Основу виброанализатора Атлант составляет переносный компьютер типа "ноутбук", в котором объединены функции регистрации сигналов, обработки, хранения. Функции первичной обработки вибросигналов, фильтрации и синхронного цифрового преобразования реализуются во внешнем блоке. К этому блоку подключаются вибродатчики и отметчик фазы, используемый при балансировке.
|
Диана-2М - двухканальный анализатор вибросигналов (виброанализатор)
Анализатор вибрации двухканальный "Диана-2М" (виброанализатор) предназначен для диагностики состояния и балансировки вращающегося оборудования.
Он является портативным, малогабаритным, автономным, переносным, эффективным и дешевым решением для проведения наиболее часто встречающихся в практике диагностических работ. Прибор прост в работе и доступен специалистам, имеющим различный уровень вибрационной подготовки.
Рис. 3.2.1 -Диана-2М - двухканальный анализатор вибросигналов
Он является портативным, малогабаритным, автономным, переносным, эффективным и дешевым решением для проведения наиболее часто встречающихся в практике диагностических работ. Прибор прост в работе и доступен специалистам, имеющим различный уровень вибрационной подготовки. Анализатор вибрации «Диана-2М» обладает уникальными возможностями в регистрации и обработке сигналов.
Рис. 3.2.2 - Методы виброзащиты
4. Методы повышения надежности компрессоров и их элементов
Общие положения о надежности изделий
Надежность - это свойство объекта выполнять заданные функции, сохраняя во времени значения установленных эксплуатационных показателей в заданных пределах, соответствующих заданным режимам и условиям использования, технического обслуживания, ремонтов, хранения и транспортирования (ГОСТ 13377-75).
В это определение входят три основных составляющих:• выполнение заданных функций;• время их выполнения;• условия эксплуатации.Рассмотрим эти составляющие подробнее.
Что касается выполнения заданных функций, то здесь необходимо сказать о двух понятиях тесно связанных с теорией и практикой надежности: работоспособность и исправность.
Работоспособность - состояние объекта, при котором он способен выполнять заданные функции с параметрами, установленными требованиями технической документации.
Неверно отождествлять работоспособность и исправность потому, что исправность - это состояние объекта, при котором он соответствует всем требованиям технической документации.
Вторым важнейшим элементом, входящим в понятие надежности, является время. Это - естественно, так как физическая сущность надежности состоит в том, что изделие должно сохранять свои технические характеристики во времени.
Показатели надежности
Показатель надежности - количественная характеристика одного или нескольких свойств, составляющих надежность объекта.
Под номенклатурой показателей надежности понимают состав показателей, необходимый и достаточный для характеристики объекта или решения поставленной задачи. Полный состав номенклатуры показателей надежности, из которой выбираются показатели для конкретного объекта и решаемой задачи, установлен ГОСТ 27.002-89.
Показатели надежности принято классифицировать по следующим признакам:
по свойствам надежности:
показатели безотказности;
показатели долговечности;
показатели ремонтопригодности;
показатели сохраняемости;
по числу свойств надежности, характеризуемых показателем:
единичные показатели (характеризуют одно из свойств надежности);
комплексные показатели (характеризуют одновременно несколько свойств надежности);
по числу характеризуемых объектов:
групповые показатели;
индивидуальные показатели;
смешанные показатели;
Групповые показатели - показатели, которые могут быть определены и установлены только для совокупности объектов; уровень надежности отдельного экземпляра объекта они не регламентируют.
Индивидуальные показатели - показатели, устанавливающие норму надежности для каждого экземпляра объекта из рассматриваемой совокупности (или единичного объекта).
Смешанные показатели могут выступать как групповые или индивидуальные.
по источнику информации для оценки уровня показателя:
расчетные показатели;
экспериментальные показатели;
эксплуатационные показатели;
экстраполированные показатели;
Экстраполированный показатель надежности - показатель надежности, точечная или интервальная оценка которого определяется на основании результатов расчетов, испытаний и (или) эксплуатационных данных путем экстраполирования на другую продолжительность эксплуатации и другие условия эксплуатации.
по размерности показателя различают показатели, выражаемые:
наработкой;
сроком службы;
безразмерные (в том числе, вероятности событий).
Методы повышения надежности
Все методы повышения и поддержания надежности разбиваются на три большие группы: методы, применяемые при проектировании, при изготовлении и при эксплуатации. Методы повышения надежности, применяемые при проектировании К таким методам относятся: 1) резервирование; 2) упрощение системы; 3) выбор наиболее надежных элементов; 4) создание схем с ограниченными последствиями отказов элементов; 5) облегчение электрических, механических, тепловых и других режимов работы элементов; 6) стандартизация и унификация элементов и узлов; 7) встроенный контроль; 8) автоматизация проверок. Эффективность этих методов состоит в том, что они позволяют из малонадежных элементов строить надежные системы. Эти методы позволяют уменьшить интенсивность отказов системы, уменьшить среднее время восстановления и время непрерывной работы системы.
Технические предложения по повышению надежности
Воздух, всасываемый компрессором, очищается в двух воздушных фильтрах, установленных на клапанных коробках / цилиндров 1-й ступени.
После сжатия в цилиндрах 1-й ступени воздух для охлаждения поступает в холодильник компрессора, который состоит из двух секций верхнего коллектора и двух нижних коллекторов. В средней части верхнего коллектора имеется патрубок, соединяющийся с клапанной коробкой 2-й ступени.
На основании рассмотренных мной патентов, стало очевидным, что большой нагрев трущихся поверхностей вращающихся элементов компрессора таких как: подшипники, вал, узел шатунов, приводит к износу деталей и уменьшению их срока эксплуатации. Поэтому, для решения этой проблемы я предлагаю подвести холодный воздух из холодильника во внутреннюю полость нижней части компрессора, где и находятся перечисленные мной элементы. Выполнить это можно с помощью трубы небольшого диаметра (), концы которой "вмонтировать" (например, посредством сварки) в нижнюю часть патрубка, упомянутого выше, а второй конец в корпус КТ-6, соответственно. Также будет происходить охлаждение масла в картере, что положительно скажется на работе компрессора.
Чтобы сбросить избыточное давление во внутренней полости, дополнительно нужно вварить патрубок для присоединения латунного клапана (рис.4.2) с внутренним проходным диаметром 10 мм.
Рисунок 4.2 - Предохранительный клапан
4.3 Показатели качества и надежности компрессора КТ-6
Одним из важнейших требований, предъявляемых к нефтегазоперерабатывающему оборудованию, является его надежность.
Известно, что в общем случае надежность технического устройства можно характеризовать его безотказностью, долговечностью, ремонтопригодностью и сохраняемостью. Для оборудования, работающего в нефтегазопереработке, особенно важны две первые составляющие. Долговечность обеспечивает длительную работу оборудования в условиях принятой системы ремонта и техобслуживания, а безотказность - непрерывность его функционирования в межремонтный период. Высокая безотказность оборудования исключает его внезапные отказы и аварии с их непредсказуемыми и зачастую очень тяжелыми последствиями.
|
|
Эмиссия газов от очистных сооружений канализации: В последние годы внимание мирового сообщества сосредоточено на экологических проблемах...
Индивидуальные очистные сооружения: К классу индивидуальных очистных сооружений относят сооружения, пропускная способность которых...
Опора деревянной одностоечной и способы укрепление угловых опор: Опоры ВЛ - конструкции, предназначенные для поддерживания проводов на необходимой высоте над землей, водой...
История создания датчика движения: Первый прибор для обнаружения движения был изобретен немецким физиком Генрихом Герцем...
© cyberpedia.su 2017-2024 - Не является автором материалов. Исключительное право сохранено за автором текста.
Если вы не хотите, чтобы данный материал был у нас на сайте, перейдите по ссылке: Нарушение авторских прав. Мы поможем в написании вашей работы!