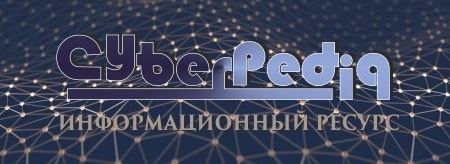
Архитектура электронного правительства: Единая архитектура – это методологический подход при создании системы управления государства, который строится...
Адаптации растений и животных к жизни в горах: Большое значение для жизни организмов в горах имеют степень расчленения, крутизна и экспозиционные различия склонов...
Топ:
Техника безопасности при работе на пароконвектомате: К обслуживанию пароконвектомата допускаются лица, прошедшие технический минимум по эксплуатации оборудования...
Отражение на счетах бухгалтерского учета процесса приобретения: Процесс заготовления представляет систему экономических событий, включающих приобретение организацией у поставщиков сырья...
Определение места расположения распределительного центра: Фирма реализует продукцию на рынках сбыта и имеет постоянных поставщиков в разных регионах. Увеличение объема продаж...
Интересное:
Средства для ингаляционного наркоза: Наркоз наступает в результате вдыхания (ингаляции) средств, которое осуществляют или с помощью маски...
Уполаживание и террасирование склонов: Если глубина оврага более 5 м необходимо устройство берм. Варианты использования оврагов для градостроительных целей...
Что нужно делать при лейкемии: Прежде всего, необходимо выяснить, не страдаете ли вы каким-либо душевным недугом...
Дисциплины:
![]() |
![]() |
5.00
из
|
Заказать работу |
|
|
Природа кластеров. Неметаллические включения в расплавах и влияние их на свойства жидких расплавов.
Первые данные рентгеноструктурного анализа, полученные в 1920-х годах, показали, что расположение атомов в жидкости не статически равномерное в любой точке, а подчиняется определенному порядку. В жидкостях вообще и в жидких металлах в частности при небольшом удалении от температуры кристаллизации сохраняется так называемый ближний порядок, подобный 30 таковому в кристаллической решетке, где имеется еще и дальний порядок. Сущность ближнего порядка состоит в том, что число ближайших соседей любого атома сохраняется постоянным во времени, так же как и общее размещение ближайших атомов вокруг произвольного центра. При этом отдельные атомы непрерывно меняют свою позицию, но схема общего расположения сохраняется. В настоящее время достоверно установлено существование в жидких металлах группировок в несколько десятков атомов с динамическим ближним порядком, соответствующим ближнему порядку кристаллической решетки в твердом металле. Эти группировки называют кластерами. Наряду с кластерами в жидких металлах часть объема занята бесструктурной жидкостью. Чем ближе температура к точке кристаллизации, тем большая доля объема приходится на кластеры. Чем выше температура, тем больше в расплаве доля бесструктурной жидкости. В некоторых металлах с "рыхлыми" структурами (В1,Са,Н&) обнаружены так называемые некристаллизуемые кластеры с отличным от кристаллической решетки ближним порядком.
Жидкие сплавы представляют собой сложную систему, содержащую большое количество взвешенных частиц нерастворимых примесей. Во многих случаях металлические расплавы имеют микрогетерогенное строение.
|
Неметаллические включения (примеси) в отливках представляют собой твердые частицы соединений компонентов сплавов с неметаллическими примесями. Их размеры колеблются от долей микрона до десятков микрон. Основная масса неметаллических включений в литейных сплавах делится по составу на окислы и сульфиды. По видам источников неметаллические включения делятся на попадающие в сплав вместе с шихтой, из футеровки, материала формы (экзогенные, внесенные) и на продукты взаимодействия компонентов сплава с примесями или добавками, с атмосферой, футеровкой (эндогенные, собственные). Эндогенные включения – это окислы, сульфиды, нитриды их в сплавах до 90%. К экзогенным – сложные окислы металлов и неметаллов, силициды. По формам неметаллические включения делятся на круглые, кристаллические, дендритные и пленочные (рис.1),
Примеси в сплавах бывают: растворимые и мало или почти нерастворимые. Растворимые примеси формируются в качестве самостоятельной фазы только при кристаллизации; нерастворимые примеси могут существовать в жидком металле в виде мелких частиц. Соединения, входящие в состав неметаллических включений, наиболее части встречающихся в литейных сплавах: сферические; кристаллические; дендритные; пленочные.
Малорастворимые включения (например, окислы в стали) при увеличении скорости кристаллизации в широком диапазоне не изменяют своих размеров.
При размерах порядка микрона всплывание происходит настолько медленно, что очищение металла за время затвердевания даже крупных слитков практически не происходит.
Растворимые включения (например, сульфиды в стали) существенно изменяются в зависимости от условий кристаллизации. При увеличении скорости кристаллизации уменьшается и их размер, и объемная доля. Это объясняется тем, что при ускорении охлаждения диффузия в жидкой фазе не успевает выровнять состав вблизи границ зерен. Кроме того, происходит измельчение самого зерна.
|
Перечислить фазы, участвующие в плавках и привести основные химические реакции взаимодействия фаз между собой. Привести состав каждой фазы и влияние отдельных соединений на качество сплавов (химические реакции)
Условные обозначения в реакциях: () – сплав, [] – шлак, áñ – футеровка, {} – газ.
Межфазные взаимодействия при плавке. Отдельные вещества (компоненты) и однородные совокупности веществ, ограниченные поверхностью раздела (фазы) вступают между собой в различные взаимодействия.
Наибольшее влияние на конечный результат плавки оказывает взаимодействие газов, шлака и металла между собой.
Твердые фазы. Для описания строения твердых фаз обычно используют хорошо разработанную в физике твердого тела теорию кристаллического строения вещества. Строение металла как в твердом, так и в жидком состоянии характеризуется наличием металлических связей, что определяет его свойства: электро- и теплопроводность, прочность и т.д.
Значительное влияние на качество и свойства полученного сплава может оказать строение исходной металлической шихты, так как при плавлении сохраняется ближний порядок в расположении атомов, и поэтому, например, грубая структура чушкового чугуна может при недостаточном перегреве «перейти» в готовый сплав. Это один из признаков наследственности. В связи с этим очень важным является вопрос о степени сохранности структуры исходных твердых фаз. Ее можно приблизительно оценить по размерам кластеров, сохраняющих структуру твердого металла в жидком.
Температура плавления различных составляющих шихты неодинакова. Это оказывает влияние па степень разупорядоченности кристаллической структуры. С ростом степени перегрева жидкого сплава над температурой плавления разупорядоченность возрастает, вероятность перехода исходной структуры в структуру сплава при затвердевании уменьшается. Это относится не только к структуре самого сплава, но и к неметаллическим включениям
Футеровки выполняют из огнеупорных материалов. Окислы, как правило, составляющие основную массу футеровки, переходят в шлак в результате ее оплавления и оказывают влияние на металлургические процессы плавки. Основой кислых огнеупоров является окись кремния SiO2. Глиноземистые огнеупоры является (основа Al2O3) по своим свойствам близки к нейтральным. В смеси с SiO2 они является полукислыми. Основные огнеупоры содержат MgO, СаО и другие основные или амфортерные окислы.
|
Жидкий шлак. В составе шлаков обычно содержатся окислы кремния, алюминия, кальция, Агния, железа марганца и других элементов и соединений, входящих в состав сплава, футеровки и флюсов.
Существует несколько теорий строения шлаковых расплавов. Согласно молекулярной теории, шлак состоит из молекул окислов: SiО2, Аl2О3, СаО, FeO, MgO, MnO и др. В то же время опытные данные свидетельствуют о том, что в шлаке присутствуют электрически заряженные частицы, и на этой основе развивается ионная теория строения шлаков. В соответствии с этой теорией, шлаки представляют собой ионный раствор, содержащий катионы Са2+, Fe2+, Mg2+ и анионы О2-, SiO44-, АlО33-, РО43-, CrO42-, МоО42-, WО42-, MnO42-, FeO42- и др. Возможность существования тех или иных ионов надо рассматривать, исходя в первую очередь из характера химических связей. Химическая связь тем полярнее, чем больше разность электроотрицательностей Е участвующих в ней атомов. Иначе говоря, с увеличением Е увеличивается степень ионности связи, т.е.е возрастает эффективный q на атомах. Если абсолютное значение q в долях заряда электрона е больше 0,5, считают, что атомы превратились в ионы, а связь становится тонной. Это происходит при Е = 1,9. Окислы FeO (Е = 1,7), MnO (Е = 2,0), Al2О3 (Е = 2,0) и SiO2 (Е = 1,7). Находятся как бы на грани между ионными и ковалентными соединениями. Окислы MgO (Е = 2,3) и СаО (Е = 1,5) можно отнести к соединениям с ионной связью.
Для общей характеристики состава и свойств шлака применяются понятия молекулярного строения шлаков, в соответствии с которыми шлаки содержат кислотные окислы, например SiO2, основные окислы СаО, MgO, FeO, MnO и амфотерные окислы Al2О3 и др.
Кислотность шлака характеризуется степенью кислотности: Ск = КО/ОО, где КО – сумма кислотных окислов, % по массе; ОО – сумма основных окислов, % по массе.
При этом считают шлак сильноосновным при Ск < 0,5; основным при Ск = 0,5-1,0; средним при Ск = 1,0-1,5; кислым при Ск = 1,5-3,0 и сильнокислым при Ск = 3,0.
|
Величина, обратная Ск называется степенью основности: Со = 1 / Ск = ОО/КО.
Для определения основности шлака иногда применяют упрощенные выражения Со = %СаО/%SiO2 или CО = NCaO/NSiO, NCaO и NSiO – мольные доли окислов.
Свойства шлаков (температура плавления, вязкость и др.) в зависимости от их состава изображают в виде двойных, тройных. А в отдельных случаях даже шестикомпонентных диаграмм.
Газовая фаза. В газовой фазе могут присутствовать простые двухатомные газы О2, N2, Н2, газы-окислы Н2О, СО2, СО, SO2, NO и другие газы – СН4, H2S.
Плотность компонентов газовой фазы на несколько порядков ниже, чем плотность компонентов конденсированных фаз, вязкость – на два-три порядка ниже, чем вязкость металлов.
Для газов характерны ковалентные связи, электрическая проводимость появляется лишь при высоких температурах, близких к температурам перехода газов в состоянии плазмы, т.е. ионизированного газа.
Газовая фаза может быть специально создаваемой, активно участвующей в металлургическом процессе, например в качестве теплоносителя или химического реагента, либо присутствующей при плавке в силу сложившихся условий.
Источником образования активной газовой фазы является, как правило, горение топлива, главные составляющие части которого углерод и водород, а также сера: С + О2 ↔ СО2; 4Н + О2 ↔ 2Н2О.
Углеводороды также сгорают с образованием СО2 и Н2О, например, СН4 + 2О2 ↔ СО2 + 2Н2О.
При температуре выше 1700-1800 °С процесс горения оказывается в значительной степени незавершенным, в газовой фазе присутствуют наряду с СО2 и Н2О продукты неполного сгорания СО и Н2.
В формировании газовой фазы участвуют углерод, кислород, водород, азот. Углерод и водород являются восстановителями, а их соединения СО2 и Н2О – окислителями.
Наиболее активных окислитель – кислород. Это объясняется тем, что для электронного строения молекулы кислорода характерно наличие двух неспаренных. Как известно, частицы (атомы, ионы, молекулы), содержащие неспаренные электроны, обладают высокой реакционной способностью. В молекулах Н2 и СО неспаренные электроны отсутствуют.
Основы термодинамической теории кристаллизации. Рост кристаллов с изменением свободной энергии в системе «твердый сплав – жидкий сплав». Факторы, влияющие на свободную энергию системы и скорость кристаллизации (графики, рисунки)
Образование кристаллов при переходе металла из жидкого или газообразного состояния в твердое называется первичной кристаллизацией, а изменение формы кристаллов в твердом состоянии - вторичной. От первичной зависит и вторичная, поэтому она определяет свойства готовой отливки.
Для образования кристаллов из расплава необходим зародыш или центр кристаллизации.
|
Различают два способа образования зародышей: гомогенный и гетерогенный.
С повышением температуры число и размеры кластеров уменьшаются. По мере приближения температуры расплава к точке кристаллизации устойчивость и продолжительность «жизни» их повышается, а при определенной температуре они приобретают полную устойчивость и становятся центрами кристаллизации. Происходит спонтанная кристаллизация, и кристаллы начинают расти на кластерах. Такой тип зарождения кристаллов называется гомогенным.
При гетерогенном образовании зародышей кристаллы растут на инородных зародышах (различных включениях в расплаве).
Для начала кристаллизации необходимо уменьшить свободную энергию, то есть переохладить расплав, отвести некоторое количество теплоты, чтобы на имеющихся зародышах начался рост кристалла.
Зависимость свободной энергии G от температуры, как следует из рис.1 различна для жидкой и твердой фаз. При температуре меньше То, более низкую свободную энергию G имеет жидкая фаза, поэтому она будет более устойчивой.
При Тo кривые пересекаются - это температура термодинамического равновесия фаз и в этом случае Gт = Gж, то есть обе фазы обладают одинаковой энергией, достаточной для внешней работы.
Процесс кристаллизации может устойчиво идти при условии Gт < Gж, для чего требуется, чтобы температура кристаллизации (Ткр) была ниже То.
Рис. 1. Изменения свободной энергии жидкой Gж и твердой Gт фаз в зависимости от температуры
Разность температур То – Ткр = DТ называется переохлаждением, которое обеспечивает достаточную для начала кристаллизации разность свободных энергий Gж – Gт. За счет разности энергий возмещается работа, необходимая для образования и роста зародышей: А = 32 s3 [ М.То / r q(То- Ткр)]2, где s – поверхностное натяжение на грани растущего кристалла; М – молекулярная масса вещества кристалла; r – плотность вещества кристалла; q – теплота плавления 1 моля вещества кристалла; То –Ткр – степень переохлаждения.
Свободная энергия (энергия Гиббса) определяется соотношением: G = E – TS + pV = H – ST, где Е – внутренняя энергия, S – энтропия (мера разупорядоченности фазы, то есть мера рассеянной энергии); Т – абсолютная температура; р – давление; V – объем; Н – энтальпия.
При температуре равновесной кристаллизации То: Gт = Gж, то есть Нж – SжТо = Нт – SтТо.
Разность энтальпий жидкой и твердой фаз равна теплоте кристаллизации: DН = L = Hж – Тт = (Sж – Sт)То = DSto, то есть L = DSto.
При переохлаждении DТ с выделением теплоты кристаллизации происходит уменьшение объемной свободной энергии (химической составляющей энергии Гиббса): DGV = (Gж – Gт) V, где V – объем.
При образовании сферического зародыша: DGV = -LDT/To*4/3pr3 одновременно происходит повышение объемной и поверхностной энергии (GS) в результате образования поверхности раздела фаз DGS = s4pr2.
Следовательно, процесс кристаллизации протекает в результате изменения общей свободной энергии: DGобщ = DGV + DGS = -LDT / To 4/3 pr3 + s4pr2
Кристаллизация металлов осуществляется в результате образования кристаллических зародышей, вырастающих затем в зерна или кристаллы путем присоединения атомов. Зародышеобразование начинается тогда. Когда кинетическая энергия несколько атомов жидкого металла достигает достаточно низкого уровня, позволяющего им занять узлы кристаллической решетки, свойственной данному металлу. Рост зародышей развивается по мере отвода от металла тепла. В результате теплоотвода через стенки формы и излучения с поверхности расплава преимущественное формирование зародышей проходит на самых внешних поверхностях металла, расположенных у стенок литейной формы, а также на неметаллических веществах, таких как оксидные пленки на поверхности расплава.
Поскольку расплав всегда контактирует с материалом литейной формы, а также вследствие наличия теплового потока зона наибольшего переохлаждения должна находиться на наружной поверхности расплава, то есть зародышеобразование проходит наиболее легко в наружной поверхности расплава в форме.
Зародыш может контактировать с посторонним твердым веществом по плоскости, ребру или в точке. Очевидно, что первый случай обеспечивает наименьшую поверхностную энергию системы. Если зародыши, контактирующие со стенками формы, преимущественно вырастают в стабильные кристаллы, то литая структура на наружной поверхности должна состоять только из кристаллов, выросших перпендикулярно к поверхности стенки формы (рис.4,а). Однако в реальных условиях затвердевания металлов наружная область представляет собой резко охлажденную зону случайно ориентированных кристалликов (рис.4,б).
Рис.4. Схема направления (→) преимущественного роста кристаллов на стенке литейной формы
С одной стороны, форма имеет шероховатую поверхность и поглощает воздух и влагу еще до заливки жидкого металла (рис.5,а). С другой стороны, поверхность жидкого металла в большинстве случаев покрыта слоем окислов и часто содержит неметаллические включения (рис.5,б). Следовательно, только те зародыши, которые хорошо контактируют со стенками формы, находятся в условиях преимущественного роста.
Ввиду того, что теплопроводность стенок формы микроскопически неоднородна, локальный преимущественный рост зародышей осуществляется в местах повышенной теплопроводности.
Скорость образования зародышей можно рассчитать на основе того, что дозародыш, содержащий I атомов, обладает вероятностью Р+ захватить атом, превратившись при этом в комплекс из (i + 1) атомов, и вероятностью потерять атом. При равновесии значения ni, ni+1 и т.д. таковы, что число дозародышей, покидающих i-тое состояние, равно в любой данный момент числу переходящих в такое состояние атомов. Критический зародыш – это комплекс, у которого Р+ = Р, так что зародыш этих размеров с равной вероятностью может расти или расплавляться.
Если предположить, что дозародыши всех размеров и всех структур находятся в равновесии, то число критических зародышей в единичном объеме определяется выражением: , где ∆G* = (16πσ3)/(∆Gр)2 - избыток свободной энергии критического зародыша.
Если теперь предположить, что каждый критический зародыш перерастет в кристалл и тем самым в распределении комплексов по размерам более не участвует, то соответствующая скорость образования зародышей определяется скоростью, с которой более мелкие дозародыши достигают критических размеров. Скорость образования зародышей I определяется в виде: , где Z – результирующая скорость переноса атомов через поверхность раздела между жидкостью и дозародышем; S* – площадь поверхности критического зародыша; ni* – равновесное число критических зародышей.
Это выражение можно преобразовать к виду: , где ∆GА – свободная энергия активации перехода атомов из жидкости в кристалл; Кν определяется равенством
, где а – зависит от формы зародыша (не обязательно сферической); n* – число атомов на поверхности критического зародыша; n – число атомов в единичном объеме жидкости.
Такой анализ скорости образования зародышей предполагает, что в любой момент достигается равновесное распределение дозародышей по размерам, хотя часть самых крупных дозародышей может превратиться в зародыши и разрастись до более крупных размеров. Это предположение достаточно верно и для проблемы образования зародышей жидкой капли в паровой фазе, но не годится для зарождения кристаллов в жидкости, поскольку из-за сравнительно низкой подвижности атомов жидкости равновесное распределение в ней устанавливается гораздо медленнее. Действительная, или переходная, скорость образования зародышей It определяется в виде:
.
Рост кристаллов. Теоретически возможны различные механизмы роста кристаллов.
1 – путем присоединения отдельных атомов к гладкой грани кристалла, линейная скорость роста при этом прямо пропорциональна переохлаждению.
2 – путем присоединения атомов к постоянно существующей ступеньке на грани, образованной выходом винтовой дислокации. Скорость роста в этом случае пропорциональна квадрату переохлаждения.
3 – рост связан с появлением двумерных зародышей на гладкой грани кристалла. В этом случае скорость роста определяется экспоненциальной зависимостью от переохлаждения.
Рис.6. Условие образования зародышей
Скорости роста реальных металлических кристаллов обычно невелики и при переохлаждениях в 1-5 К составляют 1-10 мм/с. В экстремальных условиях, когда переохлаждение достигает десятков кельвинов, скорости роста доходят до 500-1000 мм/с.
Теория возникновения усадочных, фазовых и термических напряжений в отливках. Влияние состава сплава и технологических факторов на развитие внутренних напряжений в отливках. Остаточные напряжения и меры по их снижению (диаграмма, графики)
По источнику происхождения напряжения подразделяют на усадочные – возникающие в результате сопротивления усадке металла со стороны формы и стержней; термические – возникающие за счет градиента температур по сечению отливки и неравномерного или неодновременного сжатия (расширения) отдельных частей отливки, слоев структурных зон; фазовые – возникающие в результате различия удельных объемов фаз при фазовых превращениях. Независимо от источника происхождения все эти напряжения алгебраически складываются, и их результирующее воздействие зависит от соотношения суммарного напряжения и механических свойств сплава.
Усадочные напряжения всегда растягивающие. Их величина зависит от сопротивления формы и стержней. По размерам области уравновешивания – это в основном напряжения I рода. При высоких температурах происходит релаксация усадочных напряжений вследствие пластической деформации. С переходом сплава в упругое состояние напряжения накапливаются и достигаются максимума к моменту выбивки отливки из формы: после выбивки напряжения частично снимаются.
Механическое торможение усадки возникает в отливках, имеющих внутренние полости и выступающие части, так как сокращение наружных размеров отливок встречает сопротивление формы. В зависимости от материала формы (песчаная смесь, металлический кокиль и т.д.) это сопротивление приближенно характеризуют коэффициентом жесткости μ: для абсолютно податливых форм μ = 0, для абсолютно жестких μ = 1, в общем случае 0 < μ < 1. Способность формы к деформированию под влиянием усилий, развиваемых отливкой при усадке, обратная ее жесткости, определяет действительную усадку отливки εотл в отличие от свободной усадки εсв, которую можно получить только в абсолютно податливой форме: .
Нереализованная усадка металла, подавленная сопротивлением формы, является деформацией отливки е: .
В податливых формах (μ ≈ 0) деформация отливки минимальна (е ≈ 0), в жестких формах (μ ≈ 1) деформация численно равна нереализованной (потенциально возможной) свободной усадке е ≈ εсв.
В области высоких температур, когда металл находится в пластическом состоянии, деформации е, превышающие предельную пластичность материала δ, вызывают появление трещин, называемых горячими, или кристаллизационными. Это связано с тем, что в температурном интервале кристаллизации tл-tс, когда дендритные кристаллиты частично разделены прослойками жидкой фазы, пластичность металла резко снижается до 0,1-0,5 %; при этом даже незначительное торможение линейной усадки способно вызвать появление деформаций е, превышающих пластичность δ: , и тогда образуется горячая трещина.
В области низких температур, когда металл переходит в упругое состояние, деформации. Вызванные торможением усадки, способствуют появлению так называемых усадочных напряжений σу = еЕ = μεсв*Е = αтμЕ(t* – t), где Е – модуль упругости, t – текущая температура, εсв* – потенциальная свободная усадка отливки с момента условного перехода металла из чисто пластического в идеально упругое состояние при температуре t*. По мере понижения температуры отливки усадочные напряжения σу(t) нарастают и достигают максимума после полного охлаждения (t = tк ≈ 0): .
Если величина σу(t) в какой-то момент превысит предел прочности σв, произойдет разрушение, и образуется так называемая холодная трещина.
Для уменьшения σу в отливках сложной конфигурации, испытывающих значительное механическое торможение усадки, важно не только снижать жесткость формы μ, но также извлекать отливку из формы при такой температуре выбивки tв, когда σу не достигает σв, то есть
.
Очевидно, что усадочные напряжения не возникают, если выбивку производить при tв > t*, однако при этом могут достигать опасной величины термические напряжения, поэтому необходимо выдерживать отливки в форме до некоторой оптимальной температуры.
Термическое торможение усадки возникает в результате взаимных деформаций при неравномерном охлаждении различных частей отливки сложной конфигурации (рис.2,в). Массивные и тонкие части отливки затвердевают не одновременно и охлаждаются с различной скоростью, в результате чего между ними возникают перепады температур, величина которых сначала возрастает, достигает максимума, а затем снижается до нуля при полном охлаждении отливки. В зависимости от изменения температуры обе части отливки сокращают свои размеры на величину (εсв)1,2 = αтΔt1,2, где индексы 1 и 2 относятся к тонкой и массивной частям соответственно. Если бы они были не связаны и их усадка не зависела друг от друга, тогда она была бы равна свободной: (εотл)1,2 = (εсв)1,2. В связанной системе более интенсивное сокращение размеров одной части вызывает деформации сжатия в другой и, наоборот, приводит к появлению деформаций растяжения в первой. Эти деформации равны разнице между потенциальной свободной усадкой и действительной усадкой отливки как единого целого: (1).
Рис.2. Изменение температуры (а) и усадки (б) тонкого (1) и массивного (2) брусков при охлаждении отливки сложного сечения (в)
В области высоких температур (t > t*) деформации носят пластический характер и не приводят к появлению напряжений (Е ≈ 0), хотя и вызывают снижение свойств металла в результате образования большого числа дислокаций в структуре. После перехода всей отливки в упругое состояние (с момента τ* на рис.2,а, когда t2 < t*) возникающие деформации приводят к появлению термических напряжений (σт)1,2 = Ее1,2. С момента τ* до полного остывания массивная часть отливки, охлаждаясь от t2*, получит большую свободную усадку (εсв)2 = αтt2*, чем тонкая (εсв)1 = αтt1 (рис.2,б), поэтому после полного охлаждения массивная часть будет согласно (1) растянута на величину е2 = αтt2* – εотл, так как усадка отливки за тот же период εотл < (εсв)2. Соответственно тонкая часть при остывании от более низкой температуры t1* будет сжата на величину -е1 = αтt1* – εотл, так как εотл > (εсв)1. Выражая εотл через среднюю температуру в момент τ*: , где f1, f2 – сечения тонкого и массивного элементов, получим после несложных преобразований:
(2), где Δt* = t2* – t1* – перепад температур в отливке в момент τ*.
Таким образом, термические напряжения возникают в момент условного перехода отливки в упругое состояние, возрастают по мере охлаждения и достигают максимального значения (2) после полного выравнивания температур. Величина σт определяется перепадом температур Δt*, то есть неравномерностью охлаждения различных частей отливки, а распределение напряжений зависит от соотношения площадей их сечения f1 и f2. Отливки из материала с большим модулем упругости Е имеют более высокий уровень остаточных напряжений.
Уменьшение теплопроводности сплава увеличивает градиент температура по сечению отливки и, следовательно, уровень напряжений I рода. Очевидно также влияние температурного коэффициента линейного расширения αт на уровень напряжений I рода. В результате αт структурных составляющих могут возникать также термические напряжения II рода. Анализ процесса возникновения термических напряжений показывает, что остаточные напряжения не зависят от размеров отливки и пропорциональны различию сечений элементов отливки. При этом в толстых сечениях развиваются растягивающие напряжения, в тонких – сжимающие.
Фазовые напряжения в наибольшей степени зависят от свойств сплава (точнее, от свойств фаз и структурных составляющих). Возникновение и уровень напряжений определяется: 1) различием удельных объемов фаз; 2) упругими и пластическими свойствами матрицы сплава (то есть основной структурной составляющей); 3) последовательностью протекания фазового превращения в объеме отливки (из-за наличия градиента температур фазовые превращения протекают, как правило, не одновременно). Из сказанного, очевидно, что по размерам области уравновешивания это напряжения I и II рода.
Большое значение имеет температура, при которой происходит фазовое превращение, так как с повышением температуры свойства матрицы и избыточных фаз сильно изменяются: снижается прочность и повышается пластичность. Поэтому при высокотемпературных превращениях, даже в случае большого различия удельных объемов фаз, происходит релаксация напряжений в результате микропластических сдвигов и не возникает больших остаточных напряжений. Превращения при температурах в зоне упругости сплава и пониженной пластичности вызывают больших временные напряжения, релаксация которых может осуществляться только путем микроразрушений – образования микротрещин. Наиболее опасны с этой точки зрения фазовые превращения в высоколегированных сталях с мартенситной матрицей, в отбеленных чугунах с ледебуритной матрице и в жаропрочных сплавах, содержащих большое количество интерметаллидов.
Снятие напряжений. Для снятия напряжений обычно используют термическую обработку различных видов. При отжиге I рода температура нагрева не связана с температурой фазовых превращений. Отжиг стальных и чугунных отливок обычно производится при температуре 450-650 ˚C в течение 2-10 ч. Отливки из алюминиевых сплавов отжигают при 250-350 ˚C. С повышением температуры нагрева скорость релаксации напряжений резко возрастает, и, следовательно, сокращается необходимая длительность отжига. Отжиг II рода связан с фазовой перекристаллизацией сплава, поэтому он наиболее полно снимает напряжения в отливках и одновременно исправляет крупнозернистую зернистую структуру в сталях и некоторых сплавах.
Крупногабаритные чугунные отливки (базовые детали станков и т.п.) для частичного снятия остаточных напряжений и предотвращения коробления иногда подвергаются длительному вылеживаю с течение нескольких месяцев при температуре окружающей среды. Этот процесс обычно называют естественным старением, что не соответствует технологии, принятой в металловедении.
Усадочные, фазовые и термические напряжения в отливках. Влияние состава сплава и технологических факторов на развитие внутренних напряжений в отливках. Остаточные напряжения и меры по их снижению (диаграмма, графики)
Большое значение имеет температура, при которой происходит фазовое превращение, так как с повышением температуры свойства матрицы и избыточных фаз сильно изменяются: снижается прочность и повышается пластичность. Поэтому при высокотемпературных превращениях, даже в случае большого различия удельных объемов фаз, происходит релаксация напряжений в результате микропластических сдвигов и не возникает больших остаточных напряжений. Превращения при температурах в зоне упругости сплава и пониженной пластичности вызывают большие временные напряжения, релаксация которых может осуществляться только путем микроразрушений - образования микротрещин. Наиболее опасны с этой точки зрения фазовые превращения в высоколегированных сталях с мартенситной матрицей, в отбеленных чугунах с ледебуритной матрицей и в жаропрочных сплавах, содержащих большое количество интерметаллидов.
По источнику происхождения напряжения подразделяют на усадочные – возникающие в результате сопротивления усадке металла со стороны формы и стержней; термические – возникающие за счет градиента температур по сечению отливки и неравномерного или неодновременного сжатия (расширения) отдельных частей отливки, слоев структурных зон; фазовые – возникающие в результате различия удельных объемов фаз при фазовых превращениях. Независимо от источника происхождения все эти напряжения алгебраически складываются, и их результирующее воздействие зависит от соотношения суммарного напряжения и механических свойств сплава.
Усадочные напряжения всегда растягивающие. Их величина зависит от сопротивления формы и стержней. По размерам области уравновешивания – это в основном напряжения I рода. При высоких температурах происходит релаксация усадочных напряжений вследствие пластической деформации. С переходом сплава в упругое состояние напряжения накапливаются и достигаются максимума к моменту выбивки отливки из формы: после выбивки напряжения частично снимаются.
Механическое торможение усадки возникает в отливках, имеющих внутренние полости и выступающие части, так как сокращение наружных размеров отливок встречает сопротивление формы. В зависимости от материала формы (песчаная смесь, металлический кокиль и т.д.) это сопротивление приближенно характеризуют коэффициентом жесткости μ: для абсолютно податливых форм μ = 0, для абсолютно жестких μ = 1, в общем случае 0 < μ < 1. Способность формы к деформированию под влиянием усилий, развиваемых отливкой при усадке, обратная ее жесткости, определяет действительную усадку отливки εотл в отличие от свободной усадки εсв, которую можно получить только в абсолютно податливой форме: .
Нереализованная усадка металла, подавленная сопротивлением формы, является деформацией отливки е: .
В податливых формах (μ ≈ 0) деформация отливки минимальна (е ≈ 0), в жестких формах (μ ≈ 1) деформация численно равна нереализованной (потенциально возможной) свободной усадке е ≈ εсв.
В области высоких температур, когда металл находится в пластическом состоянии, деформации е, превышающие предельную пластичность материала δ, вызывают появление трещин, называемых горячими, или кристаллизационными. Это связано с тем, что в температурном интервале кристаллизации tл-tс, когда дендритные кристаллиты частично разделены прослойками жидкой фазы, пластичность металла резко снижается до 0,1-0,5 %; при этом даже незначительное торможение линейной усадки способно вызвать появление деформаций е, превышающих пластичность δ: , и тогда образуется горячая трещина.
В области низких температур, когда металл переходит в упругое состояние, деформации. Вызванные торможением усадки, способствуют появлению так называемых усадочных напряжений σу = еЕ = μεсв*Е = αтμЕ(t* – t), где Е – модуль упругости, t – текущая температура, εсв* – потенциальная свободная усадка отливки с момента условного перехода металла из чисто пла<
|
|
Автоматическое растормаживание колес: Тормозные устройства колес предназначены для уменьшения длины пробега и улучшения маневрирования ВС при...
Кормораздатчик мобильный электрифицированный: схема и процесс работы устройства...
Наброски и зарисовки растений, плодов, цветов: Освоить конструктивное построение структуры дерева через зарисовки отдельных деревьев, группы деревьев...
Историки об Елизавете Петровне: Елизавета попала между двумя встречными культурными течениями, воспитывалась среди новых европейских веяний и преданий...
© cyberpedia.su 2017-2024 - Не является автором материалов. Исключительное право сохранено за автором текста.
Если вы не хотите, чтобы данный материал был у нас на сайте, перейдите по ссылке: Нарушение авторских прав. Мы поможем в написании вашей работы!