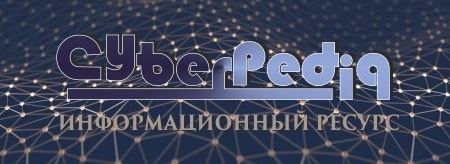
История развития хранилищ для нефти: Первые склады нефти появились в XVII веке. Они представляли собой землянные ямы-амбара глубиной 4…5 м...
Автоматическое растормаживание колес: Тормозные устройства колес предназначены для уменьшения длины пробега и улучшения маневрирования ВС при...
Топ:
Марксистская теория происхождения государства: По мнению Маркса и Энгельса, в основе развития общества, происходящих в нем изменений лежит...
Выпускная квалификационная работа: Основная часть ВКР, как правило, состоит из двух-трех глав, каждая из которых, в свою очередь...
Проблема типологии научных революций: Глобальные научные революции и типы научной рациональности...
Интересное:
Мероприятия для защиты от морозного пучения грунтов: Инженерная защита от морозного (криогенного) пучения грунтов необходима для легких малоэтажных зданий и других сооружений...
Аура как энергетическое поле: многослойную ауру человека можно представить себе подобным...
Подходы к решению темы фильма: Существует три основных типа исторического фильма, имеющих между собой много общего...
Дисциплины:
![]() |
![]() |
5.00
из
|
Заказать работу |
|
|
Автоматизация производства современных машин и необходимость повышения их качества требуют значительного сокращения времени, затрачиваемого на контроль, повышения точности и надежности контроля. Очень важно, чтобы контроль предупреждал появление брака. По степени автоматизации средства контроля разделяют на механизированные приспособления, полуавтоматы и автоматы.
Механизированные приспособления применяют для одновременной или последовательной проверки нескольких размеров сложных деталей в серийном и массовом производстве. В таких приспособлениях операции загрузки и съема контролируемых деталей осуществляют вручную, а результаты контроля (годная деталь, брак исправимый, брак неисправимый) оцениваются автоматически.
Полуавтоматы (загрузку контролируемых деталей осуществляют вручную, а все остальные операции автоматизированы) и автоматы (все процессы полностью автоматизированы) широко применяют для сортировки готовых деталей по группам размеров при селективной сборке, при 100%-ном контроле наиболее ответственных деталей, когда пропуск бракованных деталей недопустим, а также в тех случаях, когда нестабильность технологического процесса не позволяет применять выборочный контроль.
По воздействию на технологический процесс средства контроля разделяют на средства послеоперационного (пассивного) контроля и средства активного (управляющего) контроля. Первые лишь фиксируют размер деталей, разделяя их на годные, брак неисправимый и исправимый, или сортируют их на группы. Такие средства не влияют непосредственно на ход технологического процесса — отсюда их название.
Средства активного контроля контролируют размеры деталей в процессе, до или по окончании их обработки и по результатам контроля подают команду на изменение режимов обработки, на выключение станка или на подналадку системы станок — приспособление — инструмент — деталь. Отличительной особенностью средств активного контроля является наличие обратной связи, позволяющей по результатам контроля управлять точностью технологического процесса и тем предупреждать появление брака.
|
Средства активного контроля наиболее целесообразно применять да финишных операциях (шлифование, хонингование), где требуется высокая точность обработки. Потери от брака на этих операциях особенно нежелательны, так как в деталь уже вложено много труда. Активный контроль широко используют также в непрерывных производственных процессах, например при прокатке листов, лент, труб.
Основную группу технологической оснастки составляют приспособления механосборочного производства. Приспособлениями в машиностроении называются вспомогательные устройства к технологическому оборудованию, используемые при выполнении операций механической обработки, сборки и контроля.
Применение приспособлений позволяет: устранить разметку заготовок перед обработкой, повысить точность обработки, снизить себестоимость продукции, облегчить условия работы и обеспечить ее безопасность, расширить технологические возможности оборудования, организовать станочное обслуживание, применить технически обоснованные нормы, времени, сократить число рабочих, необходимых для выпуска продукции.
В серийном производстве необходимо использовать специализированные быстро налаживаемые и обратимые системы приспособлений. В мелкосерийном и единичном производствах все более широко применяют систему универсально-сборных приспособлений.
Ряд принципиально новых требований, предъявляемых к приспособлениям, определены расширением парка станков с ЧПУ, переналадка которых на обработку новой заготовки сводится к замене программы и к замене или переналадке приспособления для базирования и закрепления заготовки.
|
Изучение закономерности влияния приспособления на точность и производительность выполняемых операций позволят проектировать приспособления, интенсифицирующие производство и повышающие его точность. Проводимая работа по унификации и стандартизации элементов приспособлений создала основу для автоматизированного проектирования приспособлений с использованием электронно-вычислительной техники и автоматов для графического изображения. Это приводит к ускорению технологической подготовки производства.
Служебное назначение технологической оснастки на производстве
Технологическая оснастка является важнейшим фактором успешного осуществления прогресса в машиностроении. В промышленности эксплуатируется более 25 миллионов специальных станочных приспособлений. Затраты на изготовление технологической оснастки приблизились к затратам на производство металлорежущих станков. Задача повышения эффективности и качества технологической оснастки стала одной из важнейших народнохозяйственных проблем. На производстве …..
Для современного этапа развития машиностроения характерен быстрый рост выпуска новых видов продукции. В настоящее время смена новых моделей машин, оборудования, аппаратов, приборов происходит значительно быстрее, чем 10...15 лет назад. Ускорение освоения новых видов продукции и сокращение цикла ее производства, как правило, требует и создания новых приспособлений, так как при изменении номенклатуры выпускаемых машин и приборов специальная оснастка становится непригодной, и ее каждый раз приходится проектировать и изготовлять заново.
Значительные трудовые и материальные затраты определяются тем, что технологическая оснастка оказывает влияние на производительность труда, качество и сокращение сроков освоения производства новых изделий.
Задача повышения производительности труда в машиностроении не может быть решена только за счет ввода в действие даже самого совершенного оборудования. Смена моделей станков в производстве происходит в среднем через 6...8 лет, поэтому наряду с высокопроизводительными современными станками эксплуатируются и станки устаревших моделей.
|
Технологическая оснастка способствует повышению производительности труда в машиностроении и ориентирует производство на интенсивные методы его ведения. На предприятиях машиностроения до 90% организационно-технологических мероприятий, направленных на обеспечение роста производительности труда рабочих-станочников, связано либо с изменением конструкций, либо с изготовлением новых видов инструментов и приспособлений.
Применение технологической оснастки, особенно переналаживаемого типа не только обеспечивает, но и расширяет технологические возможности как универсальных, так и станков с ЧПУ, гибких производственных модулей и робототехнических систем.
Повышение производительности труда при применении технологической оснастки обеспечивается следующим:
- Сокращением вспомогательного времени на установку и закрепление заготовки в приспособлении;
- Интенсификацией режимов резания за счет увеличения прочности, жесткости и виброустойчивости приспособлений.
- Сокращением объема пригоночно-слесарных работ при сборке изделий за счет применения технологи ческой оснастки повышенной точности.
- Расширением многостаночного обслуживания стан ков с ЧПУ путем обработки группы деталей, установленной в многоместном приспособлении. Многостаночное обслуживание применяют, как правило, на операциях, имеющих длительный цикл, осуществляемый в автоматическом режиме. При изготовлении деталей, имеющих короткое время обработки, целесообразно применять многоместные приспособления на станках с ЧПУ.
Для снижения вспомогательного времени необходимо:
- применять механизированные приводы закрепления заготовки;
- создавать удобные условия работы станочнику путем уменьшения различных отвлекающих факторов;
- обеспечивать оптимальное время срабатывания механизированных прижимов. Среднее время срабатывания гидравлического привода прижима равно 1 с. Однако в результате действия различных факторов время срабатывания гидрофицированных прижимов достигает 5 с;
- применять "маятниковый" метод обработки, при котором время установки заготовки и съема готовой детали совмещается с основным технологическим временем;
|
- сокращать время на установку режущего инструмента путем закрепления на приспособлении специальных деталей-установов.
Средства измерения и контроля технических и конструктивных параметров деталей
Стационарные контрольные операции выполняют на стационарных контрольных пунктах. Такие операции планируют для проверки большого числа одинаковых деталей, которые удобно контролировать на специально оборудованном контрольном пункте. Скользящие контрольные операции выполняют непосредственно на рабочих местах. Такие контрольные операции предусматривают на месте изготовления громоздких деталей, а также при малом числе проверяемых деталей.
Сплошной контроль осуществляют после тех этапов обработки, где вероятен повышенный брак, перед сложными операциями, после операций, имеющих решающее значение для качества последующей обработки, а также в конце обработки (при приёмочном контроле). Выборочный контроль выполняют при высокой устойчивости технологического процесса, при большом числе одинаковых деталей, а также после второстепенных операций обработки, не имеющих решающего значения для качества деталей.
Микрометрические измерительные инструменты.
Микрометры гладкие предназначены для измерения наружных размеров; нутромеры – внутренних размеров; глубиномеры – глубин отверстий и пазов; специальные микрометры: листовые, трубные, зубомерные, резьбомерные. Погрешность измерения микрометрами от ± 3 до ± 10 мкм.
Плоскопараллельные концевые меры длины составляют основу современных линейных измерений в машиностроении. Их применяют для передачи размера от рабочего эталона единицы длины до изделия, широко используют в лабораторной и цеховой практике линейных измерений;
установки измерительных инструментов и приборов на нуль, а также для особо точных разметочных работ, наладки станков.
К механическим измерительным приборам относятся: индикаторы часового типа, погрешность измерения от ± 2 до ± 10 мкм; рычажные микрометры и скобы, погрешность измерения у рычажного микрометра ± 0,02 мм, у рычажной скобы ± 0,08 мм; рычажно-зубчатые измерительные головки, погрешность измерения ± 2 мкм.
К точным измерительным приборам относятся: оптиметры, длинномеры, измерительные машины, интерферометры, микроскопы.
К специальным измерительным инструментам относятся предельные калибры: гладкие калибры пробки, калибры кольца, калибры скобы, шаблоны; специальные контрольные приспособления.
Методы и средства контроля выбирают с учётом их метрологических характеристик (пределов измерения, пределов показаний, цены деления и погрешности измерения), конструктивных особенностей деталей (габаритных размеров, массы, жёсткости, шероховатости поверхностей), экономической целесообразности, масштаба производства. Результаты выбора средств и методов контроля заносят в таблицу. Допускаемые погрешности измерений составляют от 20 (для грубых квалитетов) до 35% допуска на параметр точности, заданного по чертежу.
|
При единичном и мелкосерийном производствах тип выпускаемой продукции часто меняется. Высокое качество изделий зачастую зависит от индивидуальных навыков и квалификации рабочих и не гарантируется ходом технологического процесса, поэтому здесь особенно необходимы тщательный пооперационный контроль заготовок, соответствующие универсальные измерительные средства и контролёры высокой квалификации. При единичном производстве, как правило, не применяют специальные контрольно-измерительные средства.
Рисунок 2-Средства измерения.
Карта эскизов (КЭ) — основной графический документ, дающий наглядную информацию о выполняемой технологической операции.(Приложение 3)
Эскизы следует выполнять с соблюдением масштаба или без соблюдения масштаба, но с примерным соблюдением пропорций.
При разработке технологической операции необходимо помнить, что сначала разрабатывается и полностью оформляется эскиз на карте эскизов и только потом заполняется текстовая операционная карта.
На каждом эскизе необходимо показать:
- Заготовку в рабочем положении, причем ее контур изображается в таком виде, в каком она получается в конце данной операции или установа. Если операция выполняется за несколько установов, то эскиз оформляется на каждый установ отдельно.
- Поверхности, обрабатываемые на данной операции, выделяются утолщенными линиями.
- Условное обозначение опор, зажимов, установочных устройств выполняется согласно ГОСТ 3.1197—81.
- Размеры, получаемые на данной операции с указанием допусков и шероховатости поверхности. При этом необходимо учесть, что на эскизе проставляются только те размеры, которые обеспечиваются только на данной операции. Проставлять размеры следует таким образом, чтобы не появилась необходимость перерасчета номинальных значений и допусков на них, т.е. простановка размера должна учитывать способ его получения (технологическая база должна быть совмещена с измерительной).
- Габаритные размеры заготовки (в качестве справочных данных).
- Допуски на погрешности формы, взаимного расположения поверхностей, если это необходимо обеспечить на данной операции.
- Режущий инструмент показывается по мере необходимости, предпочтительно в конце рабочего хода (если инструмент затемняет эскиз, то его можно изобразить отведенным от заготовки).
На таких же бланках для карты эскизов оформлена карта наладки. В карте наладки показано базирование заготовки, тип и размеры зажимных устройств и элементов, взаимное расположение заготовки и суппорта, находящегося в нуле программы, типы инструментальных блоков и режущих инструментов и их привязка к позициям револьверной головки или гнездам магазина, а также другие сведения, необходимые для настройки станка.
18.10.19-21.10.19
|
|
Археология об основании Рима: Новые раскопки проясняют и такой острый дискуссионный вопрос, как дата самого возникновения Рима...
Индивидуальные и групповые автопоилки: для животных. Схемы и конструкции...
Биохимия спиртового брожения: Основу технологии получения пива составляет спиртовое брожение, - при котором сахар превращается...
Наброски и зарисовки растений, плодов, цветов: Освоить конструктивное построение структуры дерева через зарисовки отдельных деревьев, группы деревьев...
© cyberpedia.su 2017-2024 - Не является автором материалов. Исключительное право сохранено за автором текста.
Если вы не хотите, чтобы данный материал был у нас на сайте, перейдите по ссылке: Нарушение авторских прав. Мы поможем в написании вашей работы!