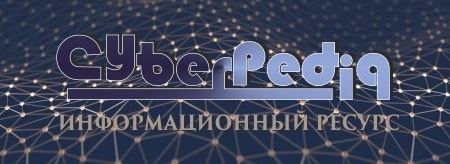
Состав сооружений: решетки и песколовки: Решетки – это первое устройство в схеме очистных сооружений. Они представляют...
Биохимия спиртового брожения: Основу технологии получения пива составляет спиртовое брожение, - при котором сахар превращается...
Топ:
Эволюция кровеносной системы позвоночных животных: Биологическая эволюция – необратимый процесс исторического развития живой природы...
Характеристика АТП и сварочно-жестяницкого участка: Транспорт в настоящее время является одной из важнейших отраслей народного...
Выпускная квалификационная работа: Основная часть ВКР, как правило, состоит из двух-трех глав, каждая из которых, в свою очередь...
Интересное:
Мероприятия для защиты от морозного пучения грунтов: Инженерная защита от морозного (криогенного) пучения грунтов необходима для легких малоэтажных зданий и других сооружений...
Отражение на счетах бухгалтерского учета процесса приобретения: Процесс заготовления представляет систему экономических событий, включающих приобретение организацией у поставщиков сырья...
Искусственное повышение поверхности территории: Варианты искусственного повышения поверхности территории необходимо выбирать на основе анализа следующих характеристик защищаемой территории...
Дисциплины:
![]() |
![]() |
5.00
из
|
Заказать работу |
|
|
Методы обработки металлов резанием
Методы обработки металлов резанием различаются между собой конструкцией используемого режущего инструмента и характером относительных движений, совершаемых инструментом и обрабатываемой заготовкой.
Заготовку и инструмент закрепляют в рабочих органах металлорежущих станков. Кинематика станков основана на использовании механизмов, сообщающих исполнительным органам только два простейших движения – вращательное и поступательное. Сочетания и количественные соотношения этих двух движений определяют все известные виды обработки резанием. Комплекс всех движений, сообщаемых заготовке и инструменту, можно разделить на основные и вспомогательные. К основным относят движения процесса резания, а к вспомогательным – движения необходимые для подготовки и завершения обработки резанием.
Основных движений два: n – движение резания (главное движение) и s – движение подачи.
Движение резания (главное движение) – это движение, определяющее скорость деформирования материала и отделение стружки.
Движение подачи – движение, обеспечивающее врезание режущей кромки инструмента в материал заготовки.
Характер выполняемых работ, вид режущего инструмента и сочетание основных движений определяют метод обработки резанием: точение, сверление, фрезерование, строгание, шлифование, протягивание и т. д.
При точении (рис. 5. 4) движение резания (вращательное) сообщается заготовке, а движение подачи (поступательное) – инструменту.
При сверлении (рис. 5. 5) на сверлильных станках как движение резания (вращательное), так и движение подачи (поступательное) обычно сообщаются инструменту.
|
При фрезеровании движение резания (вращательное) сообщается инструменту, а движение подачи (поступательное) заготовке (рис. 5. 6).
Поверхности на обрабатываемых заготовках
Заготовки, предназначенные для обработки резанием при изготовлении деталей машин, имеют исходные поверхности. В процессе обработки резанием с заготовки срезается припуск. При этом срезается исходная поверхность и образуется новая.
Поверхности на заготовках, срезаемые за каждый очередной проход инструмента, принято называть обрабатываемыми поверхностями (пов.1 рис. 5. 7).
Поверхности на заготовках, образующиеся после снятия слоя металла в результате обработки резанием, называют обработанными поверхностями (пов.2 рис. 5. 7).
Промежуточную поверхность, временно существующую в процессе резания между обрабатываемой и обработанной поверхностями, принято называть поверхностью резания (пов.3 рис. 5. 7).
Сечение срезаемого слоя
Площадь поперечного сечения срезаемого слоя, имеет форму, близкую к параллелограмму (рис. 5. 13).
Она является функцией подачи S и глубины резания t.
Обе эти величины являются производственными параметрами, посредством которых удобно рассчитывать и назначать режимы резания.
За толщину срезаемого слоя принимается величина a и определяется как расстояние между двумя последующими положения главной режущей кромки, занимаемыми через один оборот заготовки, в направлении, перпендикулярном главной режущей кромке.
Рис. 5. 13. Поперечное сечение срезаемого слоя.
Ширина срезаемого слоя обозначается буквой b и определяется как длина сечения срезаемого слоя вдоль режущей кромки.
Из схемы следует, что толщина срезаемого слоя a = S · sin j, а ширина срезаемого слоя b = t / sin j, где j главный угол в плане.
Площадь поперечного сечения A = a · b = S · t.
5.8. Процесс образования стружки
Основоположниками науки о резании металлов являются русские ученые И. А. Тиме, К. А. Зворыкин и Я. Г. Усачов. И.А. Тиме показал, что процесс образования стружки происходит по элементам.
|
В начальный момент процесса резания, когда движущийся резец под действием силы резания вдавливается в металл, в срезаемом слое возникают упругие деформации. При движении резца они, накапливаясь по абсолютной величине, переходят в пластические. В плоскости, перпендикулярной к траектории движения резца возникают нормальные напряжения, а в плоскости, совпадающей с траекторией движения резца – касательные t. Таким образом, в прирезцовом слое материала заготовки возникает сложное упругонапряженное состояние. Срезаемый слой находится под действием давления резца, касательных и нормальных напряжений.
Сложное упругонапряженное состояние металла приводит к пластической деформации, а рост пластической деформации – к сдвиговым деформациям, т. е. к смещению отдельных объемов металла относительно друг друга.
Когда напряжения превысят силу внутреннего сцепления частиц металла, происходит сдвиг элемента стружки. При дальнейшем движении резца таким же образом отделяются второй и последующие элементы стружки. Плоскость АВ, по которой происходит скалывание отдельных элементов стружки, принято называть плоскостью скалывания или сдвига. При этом угол q между направлением движения резца и плоскостью скалывания называют углом скалывания или сдвига. Он равен ≈30° и не зависит от угла резания d.
5.9. Типы образующихся стружек
В зависимости от условий обработки стружка может быть различных типов: а) сливная стружка; б) стружка скалывания; в) стружка надлома. Сливная стружка образуется при резании пластичных металлов и представляет собой ленту с гладкой прирезцовой стороной. На внешней стороне ее видны слабые пилообразные зазубрины.
Стружка скалывания (суставчатая), образуется при резании металлов средней твердости, представляет собой лепту с гладкой прирезцовой стороной, на внешней стороне ярко выраженные зазубрины, а на боковой поверхности отчетливо видны плоскости скалывания между отдельными элементами. Элементы этой стружки имеют менее прочную связь, поэтому стружка после образования нескольких завитков обычно обламывается под действием собственного веса.
Стружка надлома (элементная) образуется при резании хрупких металлов и неметаллических материалов. Связь между отдельными элементами практически отсутствует.
|
Вид образующейся стружки зависит от физико-механических свойств металла обрабатываемой заготовки, режима резания, геометрических параметров режущего инструмента, применяемых в процессе резания СОЖ.
Сила резания
В процессе резания на лезвие инструмента действуют силы сопротивления перемещению его по траектории относительного рабочего движения. Результирующая этих сил называется силой резания.
Взаимодействие режущего инструмента с обрабатываемым материалом осуществляется через контактные площади, расположенные на задней поверхностях режущего лезвия. Обрабатываемый материал, оказывая сопротивление рабочему движению инструмента, воздействует на контактные площадки неравномерно распределенной нагрузкой. Закон распределения давления по передней и задней поверхностям выглядит следующим образом (рис. 5. 16).
На передней поверхности наибольшее давление Р max действует вблизи главной режущей кромки (точка 1). По мере удаления от нее давления Р убывает, и в точке 2, в которой прекращается контакт сбегающей стружки с лезвием, давление равно 0. Ширина 1 – 2 контактной площадки при образовании хрупких материалов, например чугуна, равна или немного больше толщины срезаемого слоя. При обработке пластичных материалов ширина контактной площадки в 1,5 … 3 раза больше толщины срезаемого слоя. На заднюю поверхность лезвия также действует неравномерно распределенная нагрузка на Р ′.
Для решения практических задач, распределенную нагрузку на лезвие заменяют эквивалентной по значению и направлению действия результирующей силой резания Р (рис.5.17). Для удобства расчетов результирующую силу Р раскладывают на составляющие. Для этого вводят систему координат. Ось X располагается горизонтально и параллельна оси вращения обрабатываемой заготовки; ось Z вертикальна и направлена вниз. Вектор равнодействующей силы Р может быть проецирован на оси X, Y, Z. Проекция силы Р на ось X называется осевой составляющей силы резанья.
Осевая составляющая Р ос равна сопротивлению обрабатываемого материала врезанию резца в направлении подачи S и действующих в этом направлении сил трения. Значение осевой составляющей Р ос необходимо знать при расчетах на прочность опор и механизма подач станка.
|
Проекция силы Р на ось Y называется радиальной составляющей Р силы резания.
Она изгибает обрабатываемую заготовку в горизонтальной плоскости, что может служить причиной снижения точности обработки длинных заготовок, а также вызывает нежелательные вибрации.
Проекция силы Р на ось Z называется вертикальной или главной составляющей Р силы резания. Если точка приложения равнодействующей линии на высоте оси вращения заготовки, то направления вертикальной составляющей Р и вектора окружной скорости заготовки совпадают. Вертикальная составляющая силы резания Р равна суммарному действию сил сопротивления металла срезаемого слоя пластической деформации стружкообразования, разрушения, связанного с образованием новых поверхностей, изгиба стружки и сил трения, действующих в направлении оси Z.
Мощность процесса резания. Для разрушения материала срезаемого слоя и превращения его в стружку необходимо затратить некоторое количество энергии и произвести работу резания. Мощность, непосредственно затрачиваемая на осуществление процесса резания, называется эффективной мощностью и обозначается N е. Если при резании направления действующей силы резания Р и скорости резания V совпадают, то N е = 60 PV
Если выразить Р в килоньютонах, а V м/мин., то получим единицу мощности – киловатт.
Эффективная мощность N е в общем случае является суммарной мощностью, затраченной в процессе резания всеми составляющими Р x, Р y и Р z силы резания Р.
Мощность осевой составляющей силы резания Nex = Px · n · S, где n – частота вращения обрабатываемой заготовки; S – продольная подача.
Мощность радиальной составляющей силы резания
N ey = P y · V · cos 90 ° = 0, т.к. вектор Р y перпендикулярен вектору V.
Мощность вертикальной составляющей силы резания Р z, направление которой совпадает с направлением скорости резания, определяется уравнением N ez = Pz · V.
Следовательно, эффективная мощность с использованием этих уравнений определяется как N e = N ex + N ey + N ez = P x · n · S + Pz · V.
Скорость подачи, выраженная произведением n · S, примерно на два порядка меньше окружной скорости V. Поэтому мощность N составляет 1…2 % всей затраченной эффективной мощности, а основная доля эффективной мощности (98…99 %) приходится на составляющую N ez. В связи с этим расчет эффективной мощности производится по уравнению
N e = 60 PV,
где под величиной Р условно принимается вертикальная составляющая Р z силы резания.
Рис. 5.22. Типы фрезерных станков
|
В массовом производстве для высокопроизводительного непрерывного фрезерования заготовок небольших размеров (рычаги, кронштейны и т. д.) применяют карусельно-фрезерные (рис. 5.22, г)станки. Более крупные заготовки обрабатывают на барабанно-фрезерных станках. Эти типы станков широко применяют в автотракторной промышленности. Копировально-фрезерные станки (рис. 5.22, е)предназначены для получения деталей со сложными фасонными поверхностями в индивидуальном и мелкосерийном производствах. Примером таких деталей являются штампы и пресс-формы. Фрезерные станки (рис. 5.22, д)с ЧПУ делают на базе универсальных фрезерных станков, поэтому в них наиболее полно сочетаются широкие технологические возможности универсальных станков с достоинствами автоматизированного цикла обработки.
Использованная литература
1. Технология конструкционных материалов. /Дальский А.М., Арутюнова И.А., Барсукова Т.Н. и др. – М.: Машиностроение, 1977. – 664с.
5.5. Обработка заготовок на сверлильных и расточных станках
Характеристика методов сверления и растачивания. Сверление и растачивание – весьма распространенный способ получения отверстий в обрабатываемом изделии. Режущим инструментом при сверлении и растачивании являются сверла, а также зенкеры, развертки. Сверление и растачивание осуществляют при сочетании двух движений: главного движения резания Dr – вращательного движения сверла, зенкера или развертки (рис. 5.23) и движения подачи Ds – поступательного движения сверла или другого режущего инструмента, т. е. оба движения на сверлильном станке сообщают инструменту.
Рис. 5.23. Элементы режима резания при сверлении
Элементами режима резания являются: скорость главного движения резания; подача; глубина резания; площадь поперечного сечения среза.
Скоростью главного движения резания v при сверлении и растачивании называют окружную скорость точки режущей кромки, наиболее удаленной от оси сверла. Скорость резания определяют по формуле
V = π Dn /1000 м/мин, где D – диаметр сверла, мм; n – частота вращения сверла в минуту.
Выбор скорости резания при сверлении и растачивании зависит от ряда факторов – механических свойств обрабатываемого материала и материала режущей части сверла, диаметра сверла, величины подачи, стойкости инструмента, охлаждения, глубины сверления и т.д.
Подача S равна величине перемещения сверла, зенкера, развертки вдоль оси. Поскольку сверло имеет две режущие кромки, то подача, приходящаяся на каждую кромку, Sz = S /2, мм/об, (рис. 5.23, а).
Глубина резания t при сверлении отверстий в сплошном материале составляет половину диаметра сверла t = D /2 (см. рис. 5.23, а), а при растачивании t =(D - d)/2, где d – диаметр растачиваемого отверстия. Площадь сечения срезаемого слоя, снимаемого двумя главными режущими кромками сверла за один оборот, определяют как удвоенное произведение толщины a на ширину среза b (рис. 5.23, а). Ширину и толщину среза (без учета перемычки) определяют по формулам:
b=D/2sin φ, мм; a=S/2sin φ, мм.
Мощность резания, или эффективную мощность при сверлении N p определяют, исходя из крутящего момента сопротивления резанию М к р , и частоты вращения сверла n, мин-1. Для определения крутящего момента пользуются эксперементальной формулой
M кр= C м Dx м Sy м K м,
где С м, К м, х м, у м – коэфициенты и степени, характеризующие свойства обрабатываемого материала и другие условия обработки (определяются по таблицам).
Тогда Np = M кр n /(176,2*103*1,36) кВт.
Список литературы
1. Горбунов Б. И. «Обработка металлов резанием, металлорежущий инструмент и станки»: Учебное пособие для вузов.-М.: Машиностроение, 1981.
2. В. Т. Жадан «Материаловедение и технология металлов», -М.: Металлургия, 1994.
Типы шлифовальных кругов
Круги различают по форме на плоские прямого профиля ПП, дисковые Д, плоские с выточкой ПВ, плоские с выточкой конические, плоские накладные, периферийные 2П и 3П, кольцевые 1К, чашечные цилиндрические ЧЦ и чашечные конические ЧК, тарельчатые 1Т, сегментные и др.
Рис. Типы шлифовальных кругов (см. альбом)
Зернистость шлифовальных кругов. Абразивные зерна имеют различную зернистость. Согласно ГОСТ 3647—71, размер зерен определяют в сотых долях миллиметра и обозначают определенным номером зернистости: 200, 160, 125, 100, 80, 63, 50, 40, 32, 25, 20, 16, 12, 10, 8, 6,5, 4, 3, М40, М28, М14, М10, М7, М5.
В зависимости от величины зерна установлено три группы зернистости
шлифзерна от №200 до №16 (2000 мкм – 160 мкм)
шлифпорошки от №12 до №3 (125 мкм – 28 мкм)
микрошлифпорошки от № М40 до № М5 (40 мкм – 3 мкм) Абразивные зерна разделяют по номерам зернистости, просеивая их через систему сит, каждое из которых имеет определенное количество ячеек, приходящихся на один погонный дюйм, что определяет номер сита. Под номером зерна принято понимать номер сита, через которое данные зерна прошли, прежде чем задержаться на следующем сите.
Для полировальных паст, полотен, лент, а также брусков используют микропорошки (М40—М5), размер зерен которых измеряют в микронах.
Связка. Режущая способность шлифовального круга зависит не только от материала зерен, но и от связующего материала. Основное назначение связки — закрепление абразивных зерен в инструменте и обеспечение высокой прочности круга. Связка также должна быть водостойкой, теплостойкой, устойчивой к агрессивным средам и дешевой. При неправильном выборе связки зерна не будут работать эффективно из-за разрушения связки и выпадения еще неизношенных зерен из рабочей поверхности круга.
В зависимости от сочетания пары абразивное зерно— связка прочность их соединения может быть различной.
Различают связки неорганического и органического происхождения.
К неорганическим связкам относится прежде всего керамическая. Ее достоинства: теплостойкость, водостойкость, стойкость к агрессивным средам. Недостатки: относительно высокая хрупкость, чувствительность к ударам. Обычный состав керамических связок: огнеупорная глина, полевой шпат, кварц, тальк, жидкое стекло и др.
Органические связки. Применяемые в промышленности органические связки – вулканитовые, бакелитовые, минеральные. Вулканитовая связка (В) содержит каучук и 30% серы и обеспечивает высокую эластичность кругов, что позволяет изготавливать отрезные круги толщиной до 0,5 мм диаметром до 150 мм. Скорость вращения кругов может достичь до 75 м/с. Недостатком кругов с вулканитовой связкой является их быстрое засаливание. Наиболее распространена бакелитовая связка (Б), основой которой является фенолформальдегидная смола. Круги на основе бакелитовой связки прессуют в формах, после чего нагревают для отверждения смолы. Особое достоинство ее — эластичность. Круги на бакелитовой связке успешно применяют при обдирочном и отделочном шлифовании, особенно при отрезании, фасонном шлифовании и шлифовании узких пазов и канавок.
Недостатки: относительно невысокая теплостойкость. При температуре 200—250°С прочность сцепления с зерном уменьшается. Эти связки менее стойки к агрессивным охлаждающим жидкостям. Для повышения прочности круга применяют текстолитовые прокладки, а иногда и металлические кольца.
Твердость круга. Твердость шлифовального круга или бруска характеризуется величиной силы, с которой связка удерживает абразивные зерна. ГОСТом предусмотрены семь классов твердости шлифовальных кругов: мягкие Ml, M2, МЗ; среднемягкие СМ1, СМ2; средние Cl, C2; среднетвердые СТ1, СТ2, СТЗ; твердые Т1, Т2; весьма твердые ВТ1, ВТ2; чрезвычайно твердые ЧТ1, ЧТ2.
Во время работы зерна круга тупятся, вследствие чего силы резания, действующие на каждое зерно, возрастают. В тот момент, когда сила, действующая на зерно, превысит силу, с которой оно удерживается связкой, зерно вырывается с поверхности круга и удаляется вместе со стружкой. После удаления зерна связка, оказавшаяся в непосредственном взаимодействии с обрабатываемой заготовкой, быстро стирается поверхностью заготовки, после чего на поверхность круга выступают новые острые зерна. Описанное явление называется самозатачиванием круга. При правильном выборе круга по твердости и правильном режиме шлифования круг работает с самозатачиванием.
Если выбран слишком твердый круг, то он засаливается, если слишком мягкий, то он будет интенсивно изнашиваться (осыпаться) и быстро потеряет свою форму. Обычно для мягких материалов выбирают твердый круг, а для твердых материалов — мягкий круг.
Структура круга. Под структурой абразивного инструмента понимают количественное соотношение объемов зерна, связки и пор характеризуется номером структуры. Различают три группы, включающие 13 номеров. С увеличением номера плотность круга уменьшается.
По структуре различают круги: плотной структуры 0…3 (60…56 % зерен), среднеплотной структуры 4…6 (54…48 % зерен), открытой структуры 7…12 (38…46 % зерен).
Маркировка абразивных инструментов. Каждый абразивный инструмент маркируют, для чего на одной из его нерабочих поверхностей (на его торце) обозначается род шлифующего материала, зернистость, твердость, род связки, структура, форма и размеры, а также наибольшая окружная скорость вращения. Например: 1) М44А40С26К5 расшифровывается так: материал монокорунд 44А, зернистость 40, твердость С2, структура 6, связка керамическая разновидности К5; 2) Э40СМ2К5 означает, что круг из электрокорунда, зернистость круга 40, твердость СМ2, связка керамическая К, структура 5; 3) наиболее полная маркировка: Э60М2В6Д 200´3 ГОСТ 2424-75 50 м/сек: диск состоит из нормального электрокорунда, зернистостью № 60, мягкий 2, связка вулканитовая, структура № 6, диаметр 200мм, толщина 3мм, Vmax = 50 м/сек. 4) ЧАЗ ЭБ 40 СТ3 К5 – Челябинский абразивный завод, электрокорунд белый, зернистость круга 40, твердость СТ3, связка керамическая, структура – 5.
Процесс резания при шлифовании. Шлифовальный круг можно рассматривать как многозубый инструмент, роль режущих зубьев которого выполняют входящие в состав круга абразивные зерна. Каждое зерно шлифовального круга за период его контакта с заготовкой срезает стружку очень малых размеров. Однако, вследствие огромного количества зерен в круге и большой скорости вращения, количество зерен, участвующих в работе в единицу времени, очень велико, и это дает возможность снимать при шлифовании значительные объемы металла.
Зерна шлифовального круга имеют самую различную форму, и поэтому вид и форма стружек, снимаемые различными зернами, будут также различными. При рассмотрении же шлифовальной стружки в микроскоп видим большое количество стружек различной формы и размеров. Кроме таких оформленных стружек, в шлифовальной стружке всегда имеется большое количество мелких комочков, образовавшихся вследствие стекания металлической стружки с частицами абразива. Этот вид стружки образуется при резании зернами, форма которых неблагоприятна для осуществления процесса резания.
Процесс резания при шлифовании сопровождается теми же явлениями, что и при резании металлическими инструментами.
При шлифовании образующаяся стружка и поверхность обрабатываемой заготовки нагреваются до высокой температуры (1000 … 1500 °С)
Для снижения температуры, а также с целью очистки пор круга, для осаживания пыли и удаления ее с поверхности детали. Процесс шлифования производится обычно с охлаждением струей жидкости, подводимой к зоне касания круга с обрабатываемой заготовкой.
Схемы пришлифования. Наиболее распространено круглое внешнее шлифование в центрах.
Шлифование с продольной подачей (рис. 5.24, а). Шлифовальный круг вращается с окружной скоростью V K (м/с), которая является скоростью резания и определяется по формуле:
V к=π D k n k / (60∙1000),
где D K — -диаметр круга, мм; n к — число оборотов круга в минуту.
Электрохимическая обработка
Общие сведения. При протекании постоянного электрического тока
между электродами анодом и катодом, которые находятся в ванне с раствором электролита, происходят определенные физико-химические процессы. На одном из них — явлении анодного растворения — основана электрохимическая обработка металлов. Анодное растворение заключается в том, что при прохождении постоянного тока через электролит электрод, соединенный с положительным полюсом источника тока (анод), растворяется. При этом металл анода (заготовки) на поверхности переходит в ионное состояние и выносится электролитом из рабочей зоны.
Электролитическое полирование. Этот метод получил широкое распространение при тонкой обработке. На поверхности детали, установленной в электролитической ванне на аноде, при прохождении тока образуется защитная пленка, предохраняющая впадины микронеровностей от его воздействия. Эта пленка не препятствует растворению микровыступов вследствие того, что на них действует более плотный поток электронов и поверхность детали сглаживается. Шероховатость обработанной поверхности зависит от тщательности предварительной обработки. Обычно в производственных условиях достигают R а = 0,63—0,08, но при обработке предварительно шлифованных поверхностей может быть достигнута шероховатость R а 0,04…0,01. Электролитическое полирование успешно используется для окончательной обработки сложных по конфигурации деталей (лопатки турбин, клапаны для подачи горючего, режущие и измерительные инструменты и др.). Помимо уменьшения шероховатости поверхности эта обработка благоприятно сказывается на коррозионной стойкости, усталостной прочности и пределе выносливости металла. Это объясняется тем, что при обработке в поверхностном слое не только не нарушается исходная структура, как это бывает при большинстве других методов обработки, но и удаляется ослабленный при предварительной обработке слой.
Электрохимическая размерная обработка. На рис. 7. 5 показано электрохимическое прошивание отверстия. Анодом при ЭХОК является заготовка 4, а катодом – инструмент (трубка) 5. К заготовке подается электролит через трубку. Зазор между торцом трубки и обрабатываемой поверхностью, исключающийся межэлектродный контакт, создается давлением вытекающего электролита. При прохождении через электролит электрического тока происходит анодное растворение металла заготовки в рабочей зоне и продукты растворения уносятся протекающим электролитом через отверстие в ванночке 7. В процессе обработки трубка 5 под действием пружины 6 совершает движение подачи, сохраняя постоянным межэлектродный зазор. Процесс может идти таким образом, что движение подачи и сохранение необходимого зазора осуществляется станком, на котором ведется обработка.
Рис. 7.5. Схема электрохимической размерной обработки
В струе электролита происходит растворение анода. Растворяет соли на заготовке и удаляет их из зоны обработки. При этом способе одновременно обрабатывается вся поверхность заготовки, которая находится под активным действием катода (инструмента). Это обеспечивает высокую производительность инструменту придает форму обработанную форме обрабатываемой поверхности происходит по методу отражения или копирования износа инструмента отсутствуют, так как по существу основную работу выполняют электролит. Способ используют для обработки заготовки из высокопрочных сплавов и других труднообрабатываемых материалов.
Раздел 5. Механическая обработка заготовок резанием
Металлорежущий станок (М.с), машина для обработки резанием металлических и др. материалов, полуфабрикатов или заготовок с целью получения из них изделий путём снятия стружки металлорежущим инструментом.
М. с. являются основным видом оборудования в машиностроении, приборостроении и др. отраслях промышленности. Совершенствование М. с. предопределяет научно-технический прогресс, развитие технологии и организации машиностроительного производства.
Историческая справка. Обработка материалов резанием известна с древних времён: деталь вращали вручную, обработка велась кремнёвым резцом. В 12 в. появились токарные и сверлильные станки с ручным приводом, а в 14 в. — с приводом от водяных мельниц. Механические станки для токарных работ изготовлялись главным образом в Италии, Франции, откуда были завезены в Россию. В 1711 в Россию из Флоренции привезли станок, сделанный мастером Зингер ом, впоследствии приглашенным на службу Петром I. В придворной токарне были изготовлены станки, в разработке конструкций и создании которых принимал участие А. К. Нартов. Позднее Нартов построил другие станки (гравёрные, копировальные, гильотинные), ему же принадлежит создание первого в мире токарно-винторезного станка с механическим суппортом и сменными зубчатыми колёсами (1738). Основные промышленные типы М. с. разрабатывались позднее в Великобритании, первой вступившей на путь капиталистического развития. В дальнейшем конструкция их совершенствовалась в Германии, Франции, Швейцарии (точное станкостроение), позже (во 2-й половине 19 в.) в США (в частности, автоматические станки для массового производства). В России в 1712—14 на Тульском оружейном заводе мастер Я. Батищев создал прототип современных агрегатных станков для одновременного сверления 24 ружейных стволов, в 1714 В. И. Генин построил на Олонецких заводах многопозиционный станок. Значительный вклад в развитие конструкции М. с. внёс М. В. Ломоносов, который в середине 18 в. построил и применил в своих мастерских оригинальные шлифовальные и др. станки. Вклад в создание новых конструкций станков внесли также рус. инженеры и изобретатели И. Осипов, М. Сидоров, И. Ползунов, И. Кулибин, П. Захаво (первые автоматы для нарезания резьбы, 1810), В. Игнатов, Г. Горохов. Но несмотря на отдельные выдающиеся изобретения, станкостроение в царской России развивалось медленно. В России, в советское время, в процессе индустриализации машиностроительные предприятия стали получать новые станки. В 1932 завод «Красный пролетарий» выпустил первый современный токарно-винторезный станок. В 1933 основан Экспериментальный научно-исследовательский институт металлорежущих станков (ЭНИМС), где было начато проектирование новых типов станков, изготовление гамм станков токарных, револьверных, сверлильных, фрезерных и др. К 1970 в СССР освоено 1817 типоразмеров М. с. Годовой выпуск составил 230 тыс. станков.
Большая заслуга в развитии станкостроения в СССР принадлежит советским учёным В. И. Дикушину, Н. С. Ачеркану, Д. Н. Решетову, А. П. Владзиевскому, Б. С. Балакшину, Г. М. Головину, Г. А. Шаумяну, В. С. Васильеву, А. С. Проникову, В. А. Кудинову, А. С. Бриткину, Б. Л. Богуславскому, конструкторам Н. А. Волчеку, В. Н. Кедринскому, И. А. Ростовцеву, Ю. Б. Эрпшеру и др.
Совершенствование производства М. с. идёт в нескольких направлениях. Намечается увеличение выпуска агрегатных автоматических и полуавтоматических М. с. и автоматических линий, обеспечивающих автоматизацию технологических процессов в крупносерийном и массовом производстве (в СССР выпуск таких М. с. за период 1966—70 увеличился на 22,6 % при общем росте выпуска М. с. за этот период на 12%). В 1973 выпущено 211 тыс. М. с. Перспективно освоение прецизионных станков, обусловливающих высокую точность и качество обработки деталей. Предусматривается дальнейшее расширение производства М. с. с числовым программным управлением (ЧПУ) для обеспечения автоматизации механической обработки изделий в индивидуальном и серийном производстве. В 1968—70 в серийном производстве освоено 23 типоразмера таких станков, в 1970 — 15 типов опытных образцов; их выпуск в 1973 составил 3800 шт. Внедрение М. с. с использованием адаптивных систем управления (см. Самоприспосабливающаяся система) открывает новые пути повышения точности обработки и производительности. Для удовлетворения разнообразных потребностей народного хозяйства намечается увеличение числа типов тяжёлых уникальных станков. К 1970 создано около 500 типов тяжёлых уникальных М. с.
Подавляющее большинство деталей машин приобретают окончательную форму и размеры только после механической обработки заготовок резанием. Заготовка отличается от детали тем, что в тех местах детали, где при получении ее литьем, обработкой давлением, сваркой невозможно обеспечить необходимую точность размеров и качество поверхности специально оставляется слой металла называемый припуском. Процесс снятия припуска режущим инструментом с целью получения деталей заданной формы, размеров и точности называется резанием. Слой металла, удаляемый в процессе резания с заготовки, подвергается пластическому деформированию и разрушению. В результате этого материал припуска, отделенный от обрабатываемой заготовки, приобретает характерную форму и называется стружкой.
Обработка конструкционных материалов резанием на металлорежущих станках – весьма распространенный технологический процесс. На большинстве машиностроительных предприятий трудоемкость обработки резанием составляет 45 … 60 % от общей трудоемкости изготовления машин. В связи с этим актуальнейшей народнохозяйственной задачей являются: с одной стороны уменьшение объема обработки резанием, с другой – совершенствование технологии резания металлов.
5.1. Методы формообразования поверхностей деталей машин
В элементарной геометрии поверхность определяется как граница тела. Рассматривая границу тела различных деталей машин можно заметить, что она состоит, как правило, из отдельных участков, представляющих собой геометрически правильные поверхности. Имеется ряд классификаций поверхностей: 1) поверхности вращения; 2) плоскости; 3) контурно-сложные линейчатые поверхности; 4) винтовые поверхности; 5) пространственно-сложные поверхности.
Ряд геометрических поверхностей может быть получен как след движения образующей линии по направляющей линии. К числу таких поверхностей относятся поверхности, входящие в первые четыре группы.
1. Поверхности вращения могут быть получены перемещением образующей линии той или иной формы, расположенной в осевой плоскости, по круговой линии, которая является направляющей (рис. 5. 1).
2. Контурно-сложная линейчатая поверхность может быть получена при перемещении образующей линии, остающейся параллельной своему начальному положению, вдоль направл
|
|
Биохимия спиртового брожения: Основу технологии получения пива составляет спиртовое брожение, - при котором сахар превращается...
Историки об Елизавете Петровне: Елизавета попала между двумя встречными культурными течениями, воспитывалась среди новых европейских веяний и преданий...
Двойное оплодотворение у цветковых растений: Оплодотворение - это процесс слияния мужской и женской половых клеток с образованием зиготы...
Опора деревянной одностоечной и способы укрепление угловых опор: Опоры ВЛ - конструкции, предназначенные для поддерживания проводов на необходимой высоте над землей, водой...
© cyberpedia.su 2017-2024 - Не является автором материалов. Исключительное право сохранено за автором текста.
Если вы не хотите, чтобы данный материал был у нас на сайте, перейдите по ссылке: Нарушение авторских прав. Мы поможем в написании вашей работы!