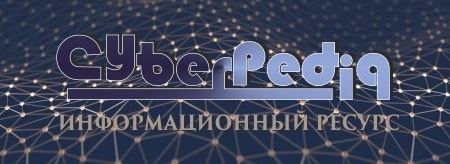
Папиллярные узоры пальцев рук - маркер спортивных способностей: дерматоглифические признаки формируются на 3-5 месяце беременности, не изменяются в течение жизни...
Биохимия спиртового брожения: Основу технологии получения пива составляет спиртовое брожение, - при котором сахар превращается...
Топ:
Техника безопасности при работе на пароконвектомате: К обслуживанию пароконвектомата допускаются лица, прошедшие технический минимум по эксплуатации оборудования...
Комплексной системы оценки состояния охраны труда на производственном объекте (КСОТ-П): Цели и задачи Комплексной системы оценки состояния охраны труда и определению факторов рисков по охране труда...
Интересное:
Финансовый рынок и его значение в управлении денежными потоками на современном этапе: любому предприятию для расширения производства и увеличения прибыли нужны...
Подходы к решению темы фильма: Существует три основных типа исторического фильма, имеющих между собой много общего...
Мероприятия для защиты от морозного пучения грунтов: Инженерная защита от морозного (криогенного) пучения грунтов необходима для легких малоэтажных зданий и других сооружений...
Дисциплины:
![]() |
![]() |
5.00
из
|
Заказать работу |
|
|
Металлургия сварки характеризуется теми физико-химическими процессами, которые протекают в сварочной зоне. Они определяются взаимодействием расплавленного металла со сварочными флюсами, шлаками и газами, а также охлаждением и кристаллизацией металла шва и превращениями основного металла в зоне термического влияния.
Металлургические процессы при дуговой сварке протекают совершенно в других условиях, чем при производстве стали. Это объясняется прежде всего небольшим объемом расплавленного металла, называемого сварочной ванной, и быстрым его затвердеванием. При ручной дуговой сварке объем расплавленного металла не превышает 8 см3 (длина сварочной ванны 20 – 30 мм, ширина 8 – 12 мм, глубина 2 – 3 мм), а время затвердевания — несколько секунд. Между тем при производстве стали объем расплавленного металла измеряется десятками и сотнями тонн, а время плавления и затвердевания — часами, хотя температура расплавленного металла ниже, чем в сварочной ванне. В результате быстрого затвердевания металла сварочной ванны химические реакции, протекающие в расплавленном металле, не успевают закончиться. Поэтому при сварке незащищенной дугой содержание кислорода в металле сварного соединения примерно в 15 раз больше, чем у мартеновской стали. А чем больше кислорода, тем ниже механические свойства металла.
Расплавленный металл электрода переходит в сварочную ванну в виде небольших капель. Металл капель подвергается в дуговом промежутке воздействию шлака покрытия электрода и газов окружающей среды. При ручной сварке электродами, имеющими покрытие, одновременно с основным и электродным металлами плавится и покрытие, в результате чего образуется расплавленный неметаллический слой шлака. Назначение шлака — улучшать свойства расплавленного металла. Шлак защищает металл капли и сварочной ванны от воздействия окружающего воздуха, раскисляет и легирует металл сварочной ванны, в шлаке растворяются вредные примеси. В ряде случаев шлак способствует устойчивому горению дуги.
|
В процессе плавления электродного покрытия наряду с образованием слоя расплавленного шлака выделяются газы, возникающие при сгорании газообразующих компонентов покрытия (целлюлоза, крахмал, древесная мука) и разложении молекул мела, мрамора. Реакции между газообразными веществами и жидким металлом протекают быстрее, чем при использовании шлаковой защиты, поэтому действие последней более интенсивно.
Сварка также является металлургическим процессом, но отличается от других подобных процессов следующими особенностями:
- происходит при высокой температуре нагрева;
- протекает с большой скоростью;
- характеризуется очень малыми объемами нагретого и расплавленного металла;
- при сварке имеет место быстрый отвод тепла от расплавленного металла сварочной ванны в прилегающие к ней зоны твердого основного металла;
- на расплавленный металл в зоне сварки интенсивно воздействуют окружающие его газы и шлаки;
- в ряде случаев для образования металла шва используется присадочный металл, химический состав которого может значительно отличаться от состава основного металла.
Высокая температура нагрева при сварке значительно ускоряет процессы плавления электродного металла, основного металла, электродного покрытия и флюса. При этом имеет место значительное испарение, разбрызгивание и окисление веществ, участвующих в химических реакциях в зоне сварки.
Молекулы ряда элементов, таких, как кислород, азот, водород, при высоких температурах дуги частично распадаются на атомы (диссоциируют). В атомарном состоянии эти элементы обладают более высокой химической активностью, чем в молекулярном. Вследствие этого окисление элементов, насыщение металла азотом и поглощение водорода в процессе сварки протекает более интенсивно, чем при обычных металлургических процессах.
|
Малые объемы расплавленного металла в сварочной ванне и интенсивный отвод тепла в окружающий металл, обусловливают кратковременность протекающих химических реакций при высоких температурах процесса, поэтому не всегда эти реакции могут полностью завершаться. С другой стороны, сильно ускоряются процессы затвердевания и кристаллизации металла шва, что существенно отражается на строении (структуре) твердого металла шва, получаемого после сварки, а также около шовной зоны основного металла. Из активных защитных газов наибольшее распространение получил углекислый газ СО2. Особенность металлургических процессов в этом случае обусловлена его сильным окислительным действием. Газовая среда в дуге, горящей в СО2, имеет более окислительный характер (33% О2), чем при горении ее на воздухе (21 % О2). Поэтому наблюдается сильное окисление сварочной ванны по реакции Fe + CO2= FeO + CO. Одновременно происходит диссоциация углекислого газа. Атомарный кислород также окисляет в сварочной ванне железо и другие Примеси: кремний, марганец, углерод и др. Эти реакции происходят как в период перехода капель электродного металла в дуге, так и на поверхности самой ванны. Для управления реакцией окисления, а также пополнения потерь элементов применяют электродные Проволоки с повышенным содержанием марганца и кремния (Св-08ГС, Св-08Г2С и др.). При использовании этих проволок в зоне понижения температуры в сварочной ванне протекают реакции раскисления:
Окислению сварочной ванны способствуют находящиеся примеси в защитном газе в виде свободного кислорода и паров воды. При этом окисляется в основном углерод с образованием газообразного оксида СО. Для подавления реакции окисления углерода в сварочной ванне должно находиться достаточное количество раскислителей кремния, марганца. С этой целью при сварке углеродистых сталей используют те же электродные проволоки, что и при сварке в углекислом газе, - с повышенным содержанием.
1.6 Методы подготовки кромок перед сваркой. Обработка швов после сварки
1.6.1 Методы подготовки кромок перед сваркой
|
В тех случаях, когда нельзя обеспечить глубину проплавления по всему сечению шва (большая толщина свариваемых изделий, малая мощность источника тепла, затруднения формирования шва из-за большого объема сварочной ванны, необходимость уменьшения доли основного металла в шве и т.п.), производят специальную разделку кромок. Разделка заключается в скосе кромок для того, чтобы "опустить" сварочную ванну вниз для обеспечения провара корня шва. При этом на кромках оставляют притупление для предотвращения прожогов. При сборке свариваемых изделий между кромками обязательно оставляют зазор, необходимый для приближения источника тепла к притуплению, а также для уменьшения деформаций и напряжений при сварке.
Кромки разделывают в целях полного провара заготовок по сечению, что является одним из условий равно прочности сварного соединения с основным металлом. Формы подготовки кромок под сварку показаны на рисунке 2, различают V, U, X – образные. По характеру выполнения сварные швы могут быть односторонние и двухсторонние. Рассмотрим разделку кромок на рисунке 7.
1 – V-образная; 2 – U -образная; 3 – X-образная; 4 – двусторонняя Х-образная.
Рисунок 7 – Разделка кромок под сварку
Скос кромок можно производить различными способами. Самым грубым и малопроизводительным из них является срубание кромок ручным или пневматическим зубилом. При этом способе края кромок получаются неровные. Наиболее ровные и чистые кромки получаются при изготовлении их на специальных кромкострогальных или фрезерных станках. Применение кислородной резки, ручной или механизированной, для скоса кромок является самым экономичным. Шлаки и окалина, остающиеся после кислородной резки, должны быть удалены с помощью зубила и стальной щетки.
Скос кромок нашего изделия будем выполнять V -образным (рисунок 8).
Рисунок 8 – V-образный скос кромок
Следует уделять большое внимание чистоте кромок, так как загрязненная поверхность кромок металла приводит к плохому провару и образованию в сварном шве неметаллических включений. Поэтому перед сваркой кромки, а также соседние с каждой кромкой участки на ширину 20 – 30 мм должны очищаться до металлического блеска от окалины, ржавчины, масла, краски и других загрязнений. Очистка от окалины, краски и масла может осуществляться непосредственно пламенем сварочной горелки. При этом окалина отстает от металла, а масло и краска сгорают. После нагрева пламенем поверхность зачищается стальной щеткой.
|
Подготовку кромок нашего изделия произведем обезжириванием, в местах сварки салфеткой, смоченной в нефрасе. Просушка на воздухе. Торцы стыкуемых заготовок перед обезжириванием зачистить.
Материалы:
- нефрас С3 80/120 ГОСТ443-76;
- ванночка алюминиевая;
- салфетка х/б ГОСТ 11680-76;
- шлифовальный круг 80х10х20 25А СМ26 К5Б;
- перчатки х/б ГОСТ 1108-59.
Оборудование:
- шлифовальная машинка ИП-21230;
- маска из органического стекла С-40 ТУ 64-1-456-70.
Шлиф машинка пневматическая ГОСТ12634-80 — это инструмент с электро-пневмоприводом, который используется для шлифовки и полировки поверхностей от ржавчины и царапин. Используется для обработки:
- металла;
- пластмассы;
- цемента;
- гранита;
- природного камня;
- мрамора;
- керамики и др.
Шлиф машинка пневматическая также используется для зачистных работ, проводимых по металлу, при снятии фасок, при зачистке сварочных швов, при проведении отделочных или монтажно-сборочных видов работ. По своим характеристикам пневматические орбитальные шлиф машинки превосходят показатели многих электрических моделей инструментов. Простая и достаточно эффективная конструкция обеспечивает низкую цену данному виду инструмента.
Рассмотрим шлиф машинку пневматическая ручная ШПР-2014 на рисунке 9.
Рисунок 9– Шлиф машинка пневматическая ручная ШПР-2014
Характеристики:
Диаметр абразивного инструмента, мм ………………………………от 125 до150;
Давление сжатого воздуха, МПа …………………………………………..0,5±0,02;
Номинальная мощность, кВт ………………………………………………….1,275;
Частота вращения на холостом ходу, мин ……………………………..5100(-10 %);
Рабочая скорость для абразивного инструмента, м/с …………………не более 40.
Также в данном процессе используем металлическую щётку показанную на рисунке 10.
Рисунок 10 – Щётка металлическая
Как нам известно, щетка металлическая – достаточно жесткий, даже грубый инструмент, который обладает высокими колюще-режущими характеристиками, как и отличаются своей жесткостью. Часто, щетку металлическую используют при проведении разнообразных ремонтно-строительных работ, как в производстве, так и быту - в сочетании с ручными механизированными и электрическими инструментами. Используют часто металлические щетки и в тех случаях, когда есть необходимость применить ударно-очистительное воздействие на поверхность обрабатываемой конструкции, а именно:
|
- при зачистке поверхности конструкции, от остатков красок, лаков, грязи, ржавчины или окалины;
- в подготовительных сварочных работах, для оптимальной и надежной стыковки свариваемых поверхностей металла;
- для зачистки и полировки сварочных швов, после проведенных сварочных работ, т.е. шлифовки “брызг” с поверхности металла.
Обработка швов после сварки
Зачистка сварного шва, проведенная по всем правилам, предотвращает появление на металлоизделии коррозии, препятствует скапливанию в местах соединения грязи. Даже нержавеющая сталь при халатной сварке и обработке соединений со временем может окислиться и заржаветь из-за того, что посторонние частицы проникают в микропоры. Плохо зачищенный сварной шов также в разы сокращает срок эксплуатации изделия, которое используется в местах повышенной влажности или находится под воздействием химически агрессивных сред (кислот или щелочей).
Все работы по зачистке сварного шва подразделяются на несколько процессов:
- очистка участка от окалины и шлаков;
- удаление усиления швов;
- подготовка участка к финишной обработке.
Эти процессы требуют профессионального подхода, определенных знаний и навыков.
Обычно к оборудованию для работы со сварными соединениями относят абразивные материалы и шлифовальные машины. Иногда производители отдают предпочтение обработке специальными средствами – пастами или гелями. Еще один метод – пескоструйная обработка.
Зачистка сварных соединений состоит из таких этапов:
- удаление сварных швов шлифовальными кругами и зачистка около шовной зоны от сторонних образований;
- агрессивная обработка соединений фибровыми или лепестковыми кругами;
- зачистка швов в труднодоступных местах с помощью специализированного инструмента.
Оборудование для выполнения всех вышеперечисленных задач подразделяется на:
- ручной инструмент;
- станки;
- специальные зачистные станции.
Для зачистки сварного шва воспользуемся шлиф машинкой пневматической ручной ШПР-2014. После зачистки кромок для удаления стружки обдувают сжатым воздухом и обезжиривают салфеткой смоченной ацетом. После сварки производят зачистку сварного шва от шлаковой пленки металлической щеткой и дальнейшего контроля внешним осмотром.
Сварочные материалы
Сварочная проволока
Св–08Г2С – один из наиболее универсальных типов сварочной проволоки, используемых в механизированных сварочных процессах. Эта проволока подходит как для использования в сварочных автоматах, так и в устройствах полуавтоматической сварки. Омедненная проволока применяется для сварки в среде защитных газов (CO2 или смесь CO2 с 20 % содержанием Ar). Проволока СВ-08Г2С позволяет использовать при сварке чистый CO2, что значительно удешевляет и ускоряет производственные процессы. Для высоконагруженных конструкций, при сварке проволокой Св-08Г2С можно использовать газовую смесь из CO2 (80 %) и Ar (20 %). В такой газовой смеси сварочный шов, выполненный с использованием омедненной проволоки Св-08Г2С будет иметь самые высокие показатели ударной вязкости и предела прочности. Этот тип проволоки можно использовать любыми сварочными аппаратами в любых пространственных положениях.
Химические состав сварочной проволоки представлены в таблице 3.
Таблица 3 – Химический состав сварочной проволоки СВ-08Г2С
Химический элемент | Химический состав | ||||||
Углерод С | Кремний Sl | Марганец Mn | Хром Cr | Никель Ni | Сера S | Фосфор Р | |
Требования ГОСТ 2246-70 | 0,05-0,11 | 0,70-0,95 | 1,80-2,10 | <0,20 | <0,25 | <0,025 | <0,03 |
Результаты испытаний | 0,06-0,08 | 0,75-0,92 | 1,80-1,92 | 0,05 | 0,044 | 0,010 | 0,01 |
Механические свойства сварочной проволоки представлены в таблице 4.
Таблица 4 – Механические свойства сварочной проволоки
Диаметр, мм | Требования ГОСТ Временное сопротивление разрыву, МПа | Результаты испытаний Временное сопротивление разрыву, МПа |
0,8 | 880-1323 | 1150-1300 |
1 | 880-1323 | 1250-1300 |
1,2 | 880-1323 | 1050-1300 |
1,6 | 880-1274 | 1000-1150 |
Сварочную проволоку Св-08Г2С при производстве покрывают защитным слоем меди. Омедненная проволока имеет большие сроки хранения и в меньшей степени подвержена химическим и физическим воздействиям во время хранения. В настоящее время сварочная омедненная проволока с маркировкой Св-08Г2С производится многими заводами на территориях России, стран СНГ, Китае и Турции.
Основные преимущества сварочной проволоки:
- отличное качество и герметичность сварочного шва;
- устойчивое горение дуги в широком диапазоне режима сварки (от капельного до струйного переноса электродного металла в сварочную ванну) при использовании сварочного оборудования любого класса сложности;
- уменьшается уровень потери металла на разбрызгивание на 40 % при сварке в защитных газах;
- снижение пористости, улучшенный внешний вид;
- низкий расход медных наконечников (покрытие проволоки не оказывает абразивного воздействия на канал наконечника);
- повышение уровня механизации сварочных работ;
- хорошее повторное зажигание дуги (специально для роботизированной сварки).
Недостатки:
- неравномерная намотка;
- неравномерный диаметр;
Первый недостаток в большинстве случаев приводит к скорому износу всего оборудования для выполнения сварки и его окончательной поломке.
Проволока Св-08Г2С поступает на рынок, как правило, в катушках по 15 или 5 кг. Однако лучшим вариантом считается приобретение материала в упаковке (без намотки на бобину) – 80, 250 кг. В этом случае обеспечивается минимальный износ подающей системы, так как проволока выходит «напрямую». Рассмотрим пример хранения сварочной проволоки Св-08Г2С рисунке 11.
Рисунок 11 – Хранение проволоки Св-08Г2С
Проволока сварочная Св-08Г2С обеспечиваю стабильное горение дуги в широком диапазоне режимов сварки (от капельного до струйного переноса электродного металла в сварочную ванну). При использовании сварочного оборудования любого класса сложности (от простых до импульсных и инверторных источников питания).
Защитный газ
Углекислота (CO2) - применяется для создания защитной среды при сварке металлов, при производстве газированных напитков, для получения сухого льда, для охлаждения, замораживания и хранения пищевых продуктов при прямом и косвенном контакте с ними, для сушки литейных форм, при пожаротушении и других целей во всех отраслях промышленности.
Углекислота жидкая – это, сжиженный углекислый газ под очень высоким давлением, которое обычно равно 70 атмосферам. Жидкость, как и газ, абсолютно бесцветна, имеет слегка кислый привкус.
Углекислота жидкая получается химическим методом, когда очистке поддается двуокись углерода. Из нее удаляются все сернистые соединения, далее происходит процесс конденсации газа в жидкое состояние.
При выпуске сжиженного углекислого газа из баллона, то некоторая его часть начинает испаряться, а остальное образует мелкие хлопья сухого льда. Это действие можно наблюдать при тушении пожара с помощью огнетушителей, когда, при нажатии на рычаг производится струя белой жидкости в результате, белые хлопья тушат пламя.
Поставляется и хранится углекислота в 40-литровых герметичных баллонах, которые защищены от коррозийных разрушений.
Эти баллоны имеют специальную маркировку, также их запрещается хранить вблизи нагревательных приборов и в помещениях с низкой температурой.
Любое механическое сдавливание или удары также могут привести к разгерметизации и порче баллона и его содержимого.
Жидкая углекислота (двуокись углерода) с каждым годом находит все большее применение производителей сварочных работ, где она используется в качестве защитного газа.
В последнее время получает все большее применение на ремонтных предприятиях и в автосервисе метод очистки загрязненных деталей и двигателей гранулами сухого льда.
Регламентирующая документация:
- ГОСТ 12.2.085-2002 Сосуды, работающие под давлением. Клапаны предохранительные. Требования безопасности;
- ПОТ РМ 014-2000. Межотраслевые правила по охране труда. Пункт 8.3. Требования безопасной эксплуатации сосудов, работающих под давлением;
- ГОСТ 8050-85 Двуокись углерода газообразная и жидкая. Технические условия.
Требования к баллонам. Заправка баллонов углекислотой.
Баллоны CO2 должны быть окрашены в черный цвет, а также содержать на корпусе надпись «Углекислота» желтого цвета.
Кроме надписи на верхней сферической части баллона должны быть нанесены и хорошо читаемы следующие данные: торговый знак производителя баллона, номер баллона, вес пустого баллона с точностью до 0.1 кг., дата следующего освидетельствования баллона.
В соответствии с законодательными требованиями, «сосуды, работающие под давлением, должны подвергаться техническому освидетельствованию (наружному, внутреннему осмотру и гидравлическому испытанию) после монтажа до пуска в работу, а также периодически в процессе эксплуатации и в необходимых случаях – внеочередному освидетельствованию».
Освидетельствование баллонов с углекислотой необходимо производить не реже, чем один раз в 5 лет.
Сертифицированные баллоны заправляют пищевым углекислым газом высшего сорта на специализированных заправках.
Запрещается наполнять газом баллоны, у которых:
- истек срок назначенного освидетельствования;
- истек срок проверки пористой массы;
- поврежден корпус баллона;
- неисправны вентили;
- отсутствуют надлежащая окраска или надписи;
- отсутствует избыточное давление газа;
- отсутствуют установленные клейма.
Запрещается очистка и окраска наполненных газом баллонов, а также укрепление колец на их горловине.
Транспортировка баллонов CO2:
При транспортировке баллонов с углекислым газом следует соблюдать следующие требования:
- транспортировать баллоны на грузовом автомобиле рекомендуется в горизонтальном положении. В вертикальном положении баллоны разрешается транспортировать при наличии специальных ограждений, препятствующих падению баллонов;
- при транспортировке необходимо избегать нагревания баллонов, а также оберегать от ударов (повреждения баллона);
- при перевозке нескольких баллонов следует использовать резиновые защитные кольца, а также деревянные прокладки между баллонами;
- переносить баллоны CO2 вручную или перекатывать баллоны по земле запрещается. Для перемещения следует использовать специальные тележки или носилки;
- запрещается перевозить баллоны с углекислотой внутри корпуса торгового автомата (при транспортировке автомата).
Хранение баллонов CO2:
Баллоны с углекислотой могут храниться как в специальных помещениях, так и на открытом воздухе. При хранении баллонов на улице, следует ограничить доступ к баллонам прямых солнечных лучей и осадков. При хранении углекислоты в помещении, баллоны следует размещать не менее чем в 1 м. от источника отопления. Колпаки и заглушки должны быть завернуты.
В горизонтальном положении баллоны хранят на деревянных рамах или стеллажах, вентили должны быть направлены в одну сторону. При вертикальном хранении баллоны устанавливают в специальные гнезда, клети, или ограждают барьером от падения.
При эксплуатации баллона следует соблюдать следующие правила:
- соединение углекислотного баллона с автоматом должно производиться обязательно через редукционный вентиль, снабженный манометром и предохранительным клапаном;
- разборка и ремонт вентилей баллонов и редукторов на рабочем месте запрещается;
- ремонт должен производиться подготовленным персоналом;
- при работе с баллоном необходимо расположить выходное отверстие вентиля баллона в сторону от работника;
- не следует допускать обмерзания вентиля баллона с углекислотой и редуктора;
- обслуживающий персонал должен быть проинструктирован по работе с углекислотными баллонами.
|
|
Папиллярные узоры пальцев рук - маркер спортивных способностей: дерматоглифические признаки формируются на 3-5 месяце беременности, не изменяются в течение жизни...
Автоматическое растормаживание колес: Тормозные устройства колес предназначены для уменьшения длины пробега и улучшения маневрирования ВС при...
Таксономические единицы (категории) растений: Каждая система классификации состоит из определённых соподчиненных друг другу...
Опора деревянной одностоечной и способы укрепление угловых опор: Опоры ВЛ - конструкции, предназначенные для поддерживания проводов на необходимой высоте над землей, водой...
© cyberpedia.su 2017-2024 - Не является автором материалов. Исключительное право сохранено за автором текста.
Если вы не хотите, чтобы данный материал был у нас на сайте, перейдите по ссылке: Нарушение авторских прав. Мы поможем в написании вашей работы!