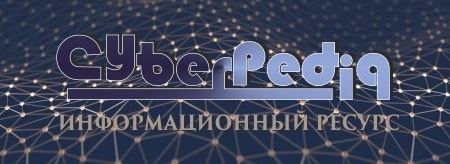
Эмиссия газов от очистных сооружений канализации: В последние годы внимание мирового сообщества сосредоточено на экологических проблемах...
Поперечные профили набережных и береговой полосы: На городских территориях берегоукрепление проектируют с учетом технических и экономических требований, но особое значение придают эстетическим...
Топ:
Определение места расположения распределительного центра: Фирма реализует продукцию на рынках сбыта и имеет постоянных поставщиков в разных регионах. Увеличение объема продаж...
Генеалогическое древо Султанов Османской империи: Османские правители, вначале, будучи еще бейлербеями Анатолии, женились на дочерях византийских императоров...
Устройство и оснащение процедурного кабинета: Решающая роль в обеспечении правильного лечения пациентов отводится процедурной медсестре...
Интересное:
Лечение прогрессирующих форм рака: Одним из наиболее важных достижений экспериментальной химиотерапии опухолей, начатой в 60-х и реализованной в 70-х годах, является...
Подходы к решению темы фильма: Существует три основных типа исторического фильма, имеющих между собой много общего...
Средства для ингаляционного наркоза: Наркоз наступает в результате вдыхания (ингаляции) средств, которое осуществляют или с помощью маски...
Дисциплины:
![]() |
![]() |
5.00
из
|
Заказать работу |
|
|
Контроль качества фильтра будем выполнять визуально-измерительным методом и гидравлические испытания.
Контроль качества выполняют в три этапа:
- контроль сборки под сварку;
- контроль над режимами сварки;
- контроль готовых швов.
Контроль перед сваркой и сборкой проводится для проверки изделия на наличие дефектов исходного материала.
А также правильности подготовки материала к сварке и сборке, то есть качественная зачистка материала, подготовка кромок для сварки и т.д. Во время сварки контролируют процесс формирования сварного шва и режимы сварки.
После процесса сварки готовое изделие должно пройти контроль качества сварных швов. Первый контроль выполняется визуальным осмотром после зачистки швов. Если видимых дефектов не обнаружено, швы подвергаются более тщательной проверке. Перед сборкой свариваемые материалы подвергают внешнему осмотру для выявления вмятин, заусенцев, окалины, ржавчины. Необходимо отчистить поверхность металла от ржавчины, грязи, масел и другого рода неметаллических включений. Проверяют качество подготовки кромок под сварку и сборку заготовок. Узлы и детали конструкций собирают под сварку в сборочных приспособлениях или на выверенных стеллажах.
Основными контролируемыми размерами при сборке являются:
- для стыковых швов;
- зазоров между кромками, притупление и угол раскрытия шва.
Наблюдение за процессом сварки включает в себя все этапы изготовления сварных изделий. Режимы сварки контролируют в первую очередь с целью соблюдения параметров процесса сварки визуальным наблюдением по приборам и внешнему виду сварочного шва. Чрезмерное усиление шва, резкие переходы от шва к основному металлу, бугристость и т.п. снижают работоспособность сварных соединений при вибрационных нагрузках и повышенной склонности основного металла к хрупкому разрушению. Особенно опасные дефекты, нарушающие целостность сварочного соединения, они в большинстве случаев относятся к недопустимым дефектам сварных соединений.
|
Контроль качества сварных швов полотен производится с помощью неразрушающего метода качества, рентгенографическим методом и визуально-оптическим методом контроля.
Визуально-оптический метод контроля, или внешний осмотр, имеет различные разновидности – внешний осмотр сварных соединений и их замеры, осмотр с помощью оптических приборов, например эндоскопов, активный контроль в процессе сварки с оперативной обратной связью. Оптические приборы позволяют намного расширить пределы визуального контроля проводимого человеком. Они обеспечивают возможность осматривать сварные соединения и поверхности элементов конструкций, скрытые близлежайшими деталями и недоступные наблюдению, а также контролировать состояние внутренних поверхностей различных конструкций. Визуальный контроль с применением оптических приборов называют визуально-оптическим.
Внешний осмотр во многих случаях достаточно информативен, дешевый и оперативный метод контроля, однако у него недостаточно высокая достоверность и чувствительность. Его применяют для поиска поверхностных дефектов (трещин, поверхностных повреждений, мест разрушения свариваемой конструкции, загрязнений, течей).
Внешнему контролю подвергают материал заготовок, который бракуется при наличии вмятин, заусенцев, окислов, ржавчины и т.д. Определяют качество кромок под сварку и сбору заготовок. Для контроля применяются шаблоны или специальный инструмент.
Сварные швы принимают по внешнему виду в сравнении с эталонами. Геометрические характеристики швов замеряют с помощью шаблонов или измерительных инструментов.
Для измерения формы и размеров изделий и сварных соединений, угловых и линейных величин полуфабрикатов, деталей, сборочных единиц, сварных соединений, изделий, а также поверхностных дефектов следует применять исправные, прошедшие метрологическую поверку, инструменты и приборы:
|
- лупы измерительные по ГОСТ 25706;
- линейки измерительные металлические по ГОСТ 427;
- угольники поверочные 90 лекальные по ГОСТ 3749;
- штангенциркули по ГОСТ 166 и штанге рейсмасы по ГОСТ 164;
- щупы № 2...4;
- угломеры с нониусом по ГОСТ 5378;
- стенкомеры и толщиномеры индикаторные по ГОСТ 11358;
- микрометры по ГОСТ 6507;
- нутромеры метрические по ГОСТ 10 и индикаторные по ГОСТ 868;
- шаблоны, в том числе универсальные (например, типа УШС по ТУ 102.338-83), радиусные, резьбовые и др.;
- толщиномеры ультразвуковые, например, УТ-9ЗП и др.
Универсальный сварочный шаблон УШС 3 предназначен для измерения контролируемых параметров труб, контроля качества сборки стыков соединений труб, а также для измерения параметров сварного шва при его контроле.
Рассмотрим универсальный шаблон типа УШС на рисунок 13.
Рисунок 13– Универсальный шаблон УШС
Гидравлические системы, а также системы трубопроводов, насосов, теплообменников и иного оборудования, которое работает в условиях постоянного давления, требуют регулярного контроля их состояния. Среди методов проведения мониторинга наиболее востребован способ неразрушающего контроля – гидравлические испытания. Они проводятся для определения степени прочности и плотности трубопроводов, сосудов, теплообменников, гидросистем, а также их сборочных единиц и составных элементов конструкции. Гидравлическим испытаниям могут быть подвергнуты целые тепловые сети и даже схемы тепломеханического оборудования. Для этого они должны находиться в собранном состоянии.
В большинстве стран принято все оборудование, которое работает под давлением, регулярно подвергать гидравлическим испытаниям. При этом проводится мониторинг в следующих случаях:
После того, как будет изготовлено оборудование или элемент трубопровода компанией-производителем и планируется поставка их на монтаж.
Непосредственно после монтажа трубопроводов и оборудования.
Также в процессе эксплуатации оборудования, трубопроводов, которые постоянно нагружаются давлением пара, воды, пароводяной смеси.
|
Гидравлическое испытание является необходимой процедурой. Она позволяет установить степень надежности трубопроводов и оборудования, работающего под давлением, в течение всего периода эксплуатации. Это имеет крайне важное значение, поскольку в случае неисправности или аварийной ситуации возникает угроза жизни людей, работающих с данным типом оборудования.
Порядок проведения гидравлических испытаний.
Чтобы провести мониторинг состояния оборудования с помощью гидравлического испытания, необходимо создать в испытуемом контуре пробное давление. Оно должно превышать рабочее на определенную величину, которая рассчитывается индивидуально для каждого типа гидросистемы. Обычно превышение составляет порядка 25 %. Создается пробное давление плавно, медленно, поскольку при резком скачке возможен гидроудар или возникновение аварийной ситуации.
Рост давления тщательно контролируется с помощью двух независимых поверенных манометров или каналов измерений. На этапе создания пробного давления допустимы его колебания, связанные с изменением температуры рабочей жидкости.
Проведение процедуры создания пробного давления сопряжено с обязательным принятием мер по недопущению скопления в полостях, заполненных жидкостью, газовых пузырей. После того, как давление искусственно повышено, оборудование должно находиться в таком состоянии в течение всего времени выдержки. При этом повышенное давление не должно падать. Если это происходит, значит, испытуемое оборудование не достаточно герметично. После того, как система пробудет под повышенным давлением весь необходимый период времени, пробное давление начинают постепенно снижать вплоть до рабочего.
При проведении этих этапов гидравлических испытаний весь рабочий персонал в целях обеспечения безопасности должен находиться вдали от испытуемого оборудования. Это связано с высокими рисками гидравлических испытаний. После снижения и нормализации давления проводится контрольный осмотр сосуда и оборудования в местах, доступных для визуального осмотра. Гидравлические испытания проводятся и на оборудовании с несколькими рабочими полостями, даже если каждая из них рассчитана на свое значение давления. Так, в теплообменниках (комбинированных сосудах с несколькими полостями) гидравлические испытания проводятся для каждой полости отдельно.
|
После проведения испытания производится оценка полученных результатов. Гидросистема считается выдержавшей испытания, если при повышении давления и последующем осмотре не будет выявлено разрывов металла, течей жидкости. Кроме того не должно быть остаточных видимых деформаций, а в процессе выдержки давление не выходило за пределы, которые можно объяснить изменением температуры рабочей жидкости. В противном случае система признается не прошедшей испытания и требующей ремонта.
Рассмотрим поршневой компрессор С 416М на рисунке 14.
Рисунок 14 – Гидравлический компрессор С416М
Технические характеристики гидравлического компрессора С416М представлены в таблице 5.
Таблица 5 – Характеристики гидравлический компрессор С416М
Производительность (м 3/ мин) | 1,0 |
Давление (бар) | 10 |
Мощность (кВ т) | 11 |
Напряжение (В) | 380 |
Объем ресивера (л) | 430 |
Габаритные размеры (см) | 210x70x148 |
Вес (кг) | 480 |
Производительность компрессора составляет 1000 литров в минуту сжатого воздуха.
Процесс сжатия происходит равномерно по всему объему камеры, что снижает уровень шума и вибрации.
Аппарат не требует специальной подготовки фундамента для установки.
Дополнительные характеристики:
– количество цилиндров – 2 шт;
– количество ступеней сжатия – 2 шт;
– соединение – байонет.
Данная модель широко применяется на строительных площадках, в промышленных цехах, при строительстве дорог, прессовке газовых и водопроводных труб, в гаражах, автомастерских и на других объектах для обеспечения энергией сжатого воздуха окрасочного пневмоинструмента, отбойных молотков, пескоструйных аппаратов и другого промышленного пневмооборудования.
Как любой поршневой компрессор, С416М предназначен для эксплуатации в таких условиях производства, которое характеризуется значительными перепадами в потреблении сжатого воздуха. Данная установка не рассчитана на длительную работу без перерыва. Однако наличие в конструкции С416М реле давления компенсирует этот недостаток. В случаях, когда давление превышает установленную норму, реле переводит компрессор в холостой режим. Когда давление снижается, компрессорная установка автоматически запускается вновь.
Популярность компрессора С416М обусловлена его конструктивными особенностями и рядом преимуществ, которые дают возможность использовать его с максимальной отдачей. Среди достоинств данного компрессора можно назвать следующие:
|
- высокая производительность, обеспеченная надежным двигателем, которая дает возможность использовать С416М в промышленном цеху любого масштаба;
- возможность использования в неблагоприятных условиях: при повышенной влажности или загрязненности воздуха, при резких перепадах температур;
- небольшие размеры, позволяющие устанавливать данную модель на сравнительно небольших рабочих площадях;
- наличие ресивера большого объема, который делает поступление сжатого воздуха более плавным и равномерным, что позитивно сказывается на сроке службы оборудования и позволяет экономить электроэнергию;
- реле давления, обеспечивающее равномерную работу компрессора воздушного С416М;
- экономичность – высокая температура привода позволяет снизить потребление электроэнергии и уменьшить производственные расходы;
- износоустойчивость компрессора, которая обеспечивается использованием для изготовления его составных частей качественных и сверхпрочных материалов;
- простая система управления, поддерживающая постоянное давление в пределах заданной нормы;
- простота техобслуживания и ремонта;
- широкий спектр применения.
|
|
Состав сооружений: решетки и песколовки: Решетки – это первое устройство в схеме очистных сооружений. Они представляют...
Наброски и зарисовки растений, плодов, цветов: Освоить конструктивное построение структуры дерева через зарисовки отдельных деревьев, группы деревьев...
Эмиссия газов от очистных сооружений канализации: В последние годы внимание мирового сообщества сосредоточено на экологических проблемах...
История развития хранилищ для нефти: Первые склады нефти появились в XVII веке. Они представляли собой землянные ямы-амбара глубиной 4…5 м...
© cyberpedia.su 2017-2024 - Не является автором материалов. Исключительное право сохранено за автором текста.
Если вы не хотите, чтобы данный материал был у нас на сайте, перейдите по ссылке: Нарушение авторских прав. Мы поможем в написании вашей работы!