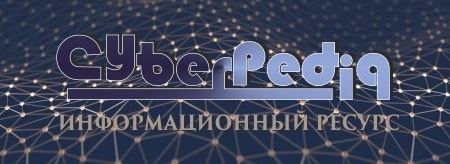
Механическое удерживание земляных масс: Механическое удерживание земляных масс на склоне обеспечивают контрфорсными сооружениями различных конструкций...
Кормораздатчик мобильный электрифицированный: схема и процесс работы устройства...
Топ:
Основы обеспечения единства измерений: Обеспечение единства измерений - деятельность метрологических служб, направленная на достижение...
Оснащения врачебно-сестринской бригады.
Эволюция кровеносной системы позвоночных животных: Биологическая эволюция – необратимый процесс исторического развития живой природы...
Интересное:
Как мы говорим и как мы слушаем: общение можно сравнить с огромным зонтиком, под которым скрыто все...
Распространение рака на другие отдаленные от желудка органы: Характерных симптомов рака желудка не существует. Выраженные симптомы появляются, когда опухоль...
Финансовый рынок и его значение в управлении денежными потоками на современном этапе: любому предприятию для расширения производства и увеличения прибыли нужны...
Дисциплины:
![]() |
![]() |
5.00
из
|
Заказать работу |
|
|
Введение
Сварка является технологическим процессом, широко применяемая практически во всех отраслях народного хозяйства. Сварка - это технологический процесс получения неразъёмного соединения посредством установления межатомных и межмолекулярных связей между свариваемыми частями изделия при их нагреве (местном или общем), или пластическом деформировании.
С применением сварки создаются серийные и уникальные машины. Сварка внесла коренные изменения в конструкцию и технологию производства многих изделий. При изготовлении металлоконструкций, прокладке трубопроводов, установке технологического оборудования, на сварку приходится четвертая часть всех строительно-монтажных работ. Основным видом сварки является дуговая сварка.
Сварка применяется для соединения металлов и их сплавов, термопластов во всех областях производства
Так же производство сварных конструкций имеет свои особенности. Возможность снижения металлоемкости, высокая технологичность.
От выбора способа сварки и качества выполнения этих работ зависит качество готового изделия и эффективность сварочного производства в целом. Поэтому находят и применяют оптимальные решения в конструкторском и технологическом плане.
Физические признаки, в зависимости от формы энергии, используемой для образования сварного соединения, подразделяются на три класса:
- термический класс: виды сварки, осуществляемые плавлением с использованием тепловой энергии;
- термомеханический класс: виды сварки, осуществляемые с использованием тепловой энергии и давления;
- механический класс: виды сварки, осуществляемые с использованием механической энергии и давления.
|
Сварка во многих случаях заменила такие трудоёмкие процессы изготовления конструкций, как клёпка и литьё, соединение на резьбе и ковка.
Преимущество сварки перед этими процессами следующие:
- экономия металла – 10...30 % и более в зависимости от сложности конструкции;
- уменьшение трудоёмкости работ, сокращение сроков работ и уменьшение их стоимости;
- удешевление оборудования;
- возможность механизации и автоматизации сварочного процесса;
- возможность использования наплавки для восстановления изношенных деталей;
- герметичность сварных соединений выше, чем клепаных или резьбовых;
- уменьшение производственного шума и улучшение условий труда рабочих;
- сварка позволяет создавать соединения, не уступающее по прочности применяемому металлу.
Технологическая часть
Описание конструкции изделия
Сегодня практически любая проблема, связанная с подготовкой питьевой и технической воды, может быть решена с использованием фильтров для воды.
Изделие, рассматриваемое в курсовом проекте – водяной фильтр (рисунок 1).
Рисунок 1– Барьерный фильтр
Магистральная вода нуждается в нескольких стадиях очищения. Фильтры первого уровня производят только первичную грубую очистку. Они удаляют примеси крупной фракции: песок, частицы поверхности водопроводных систем, окалину, ржавчину. Воду для пищевых, питьевых, фармацевтических целей необходимо очищать и обеззараживать. Барьерный фильтр удаляет из магистральной воды все загрязнения фракцией более 0,5 мкм, включая тончайшие взвеси грунта, органику, бактерии, вирусы.
Устройство барьерных фильтров.
Барьерный фильтр комплектуют фильтрующими элементами (картриджами). Степень их чистоты необходимо контролировать. Патрубки на входе в фильтродержатель и на выходе из системы водоочистки оборудуются манометрами. Перепады давления (более 1 кгс/см) являются показателем критической загрязнённости картриджей. Барьерные фильтры заключены в универсальные корпуса - фильтродержатели, обеспечивающие быструю замену модулей. Степень водоочистки в барьерной системе определяется типом модулей, количеством фильтрующих элементов. Заключительное обеззараживание воды при необходимости производится УФ-стерилизаторами.
|
Способ сварки изделия
Сварка – это процесс получения неразъемных соединений материалов путем создания межатомных связей при их местном или пластическом деформировании. С помощью нее в основном соединяют металлы и сплавы, как однородные, так и разные по составу.
Наиболее распространенными типами производства изделия:
- ручная дуговая сварка;
- сварка под флюсом;
- сварка в защитных газах;
- электронно-лучевая сварка.
При ручной дуговой сварке покрытыми металлическими электродами, сварочная дуга горит с электрода на изделие, оплавляя кромки свариваемого изделия и расплавляя металл электродного стержня и покрытие электрода (рисунок 2).
Рисунок 2 – Схема сварки покрытым металлическим электродом
Кристаллизация основного металла и металла электродного стержня образует сварной шов.
Электрод состоит из электродного стержня и электродного покрытия. Электродный стержень – сварочная проволока; электродное покрытие – многокомпонентная смесь металлов и их оксидов.
По функциональным признакам компоненты электродного покрытия разделяют:
Газообразующие:
- защитный газ;
- ионизирующий газ.
Шлакообразующие:
- для физической изоляции расплавленного металла от активных газов атмосферного воздуха;
- раскислители;
- рафинирующие элементы;
- легирующие элементы;
- связующие;
- пластификаторы.
Перед зажиганием (возбуждением) дуги следует установить необходимую силу сварочного тока, которая зависит от марки электрода, типа сварного соединения, положения шва в пространстве и др.
Зажигание (возбуждение) производиться двумя способами. При первом способе электрод подводят перпендикулярно к месту начала сварки и после сравнительно легкого прикосновения к изделию отводят верх на расстояние 25 мм. Второй способ напоминает процесс, зажигая спички. При обрыве дуги повторное зажигание ее осуществляется впереди кратера на основном металле с возвратом к наплавленному металлу для вывода на поверхность загрязнений, скопившихся в кратере. После этого сварку ведут в нужном направлении.
|
Применение того или иного способа зажигания дуги зависит от условий сварки и от навыка сварщика.
Положение электрода зависит от положения шва в пространстве. Различают следующие положения швов: нижнее, вертикальное и горизонтальное на вертикальной плоскости, потолочное. Сварку вертикальных швов можно выполнять сверху вниз и снизу вверх.
При сварке в нижнем положении электрод имеет наклон от вертикали в сторону направления сварки. Перемещение электрода при сварке может осуществляться способами к себе и от себя.
Достоинства способа:
- простота оборудования;
- возможность сварки во всех пространственных положениях;
- возможность сварки в труднодоступных местах;
- быстрый, по времени переход от одного вида материала к другому;
- большая номенклатура свариваемых металлов.
Недостатки способа:
- большие материальные и временные затраты на подготовку сварщика;
- качество сварного соединения и его свойства во многом определяются субъективным фактором;
- низкая производительность (пропорциональна сварочному току, увеличение сварочного тока приводит к разрушению электродного покрытия);
- вредные и тяжёлые условия труда.
Рациональные области применения:
- сварка на монтаже;
- сварка непротяжённых швов;
- шлаковая и др.
Сварка под флюсом.
При автоматической дуговой сварке под флюсом электрическая дуга горит под слоем флюса между концом сварочной проволоки и свариваемым металлом.
Схема процесса сварки под флюсом показана на рисунке 3.
Рисунок 3 – Схема сварки под флюсом
Ролики механизма автоматически вытягивают электродную проволоку в дугу. Сварочный ток, переменный или постоянный, прямой или обратной полярности подводится к электродной проволоке, а другим контактом к изделию.
Сварочная дуга горит в газовом облаке, образованном в результате плавления и испарения флюса и металла. При гашении электрической дуги расплавленный флюс, остывая, образует шлаковую корку, которая отделяется от поверхности шва. Флюс засыпается перед дугой из бункера слоем толщиной 40 – 80 и шириной 40 – 100 мм. Количество флюса, идущего, в шлаковую корку, равно массе расплавленной сварочной проволоки. Не расплавившаяся часть флюса отсасывается пневмоотсосом в бункер и используется вновь.
|
Потери металла на угар и разбрызгивание при горении дуги под флюсом меньше, чем при ручной дуговой и сварке в защитных газах. Расплавленные электродный и основной металлы перемешиваются в сварочной ванне. Кристаллизуясь, они образуют сварной шов.
В промышленности используется сварка проволочными электродами - сварочной проволокой. Иногда сварку проводят ленточными, толщиной до 2 мм и шириной до 40 мм, или комбинированными электродами. Дуга, перемещаясь от одного края ленты к другому, равномерно оплавляет её торец и расплавляет основной металл. Изменяя форму ленты, можно изменить и форму поперечного сечения шва, достигая необходимого проплавления металла или получая равномерную глубину проплавления по всему сечению шва.
При сварке флюс насыпается слоем толщиной 50 – 60 мм; дуга утапливается в массе флюса и горит в жидкой среде расплавленного флюса, в газовом пузыре, образуемом газами и парами, непрерывно создаваемыми дугой. При среднем насыпном весе флюса около 1,5 г/см3 давление слоя флюса на жидкий металл составляет 7 – 9 г/см2. Этого давления достаточно для устранения механических воздействий дуги на ванну жидкого металла, приводящего к разбрызгиванию жидкого металла, нарушению формирования шва даже при очень больших токах.
Для электрической дуги, горящей без флюса нельзя проводить сварку при силе тока выше 500 – 600. А из-за разбрызгивания металла и нарушения формирования шва. Дуга же во флюсе позволяет увеличить токи в до 3000-4000 А с сохранением качества сварки и правильным формированием шва.
В качестве флюсов при сварке применяют искусственные силикаты имеющие слабо кислый характер. Основой флюса являются двойной или тройной силикат закиси марганца, окиси кальция, окиси магния, алюминия и т. д. В качестве добавки, снижающей температуру плавления и вязкость, применяется плавиковый шпат.
Недостатки сварки под флюсом:
- велики трудозатраты, связанные со стоимостью флюса;
- трудности корректировки положения дуги относительно кромок свариваемого изделия;
- экологическое воздействие газов на оператора;
- невидимость места сварки, расположенного под толстым слоем флюса;
- нет возможности выполнять сварку во всех пространственных положениях без специального оборудования;
- повышенная жидко текучесть расплавленного металла и флюса;
- требуется тщательная сборка кромок под сварку;
- при увеличенном зазоре между кромками возможно вытекание в него расплавленного металла и флюса и образование в шве дефектов.
|
Преимущества сварки под флюсом:
- повышенная производительность;
- минимальные потери электродного металла;
- отсутствие брызг;
- максимально надёжная защита зоны сварки;
- минимальная чувствительность к образованию оксидов;
- не требуется защитных приспособлений от светового излучения, так как дуга горит под слоем флюса;
- низкая скорость охлаждения металла обеспечивает высокие показатели механических свойств металла шва.
Дуговая сварка в защитных газах - при сварке в зону дуги через сопло горелки подается защитный газ. Электрическая дуга расплавляет основной металл и электродную проволоку или электрод. Расплавленный металл сварочной ванны, кристаллизуясь, образует шов. При сварке неплавящимся электродом электрод не расплавляется. Защитный газ препятствует взаимодействию расплавленного металла с газами воздуха.
Схема процесса сварки в защитных газах представлена на рисунке 4.
Рисунок 4 – Схема сварки в защитных газах
Дуговая сварка в защитных газах разделяется по виду используемых газов на сварку:
- сварку в инертных газах;
- сварку в активных газах;
- сварку с смеси инертных и активных газах;
- сварку со струйной защитой.
По виду дуги дуговая сварка в защитных газах разделяется на:
- сварка постоянной дугой;
- сварка импульсной дугой.
Инертные газы применяются при сварке химически активных металлов (титан, цирконий, молибден, тантал, ниобий и др.), активные газы используют, когда свойства металла обеспечивается металлургической обработкой. Газовые смеси повышают устойчивость дуги, улучшают форму шва, уменьшают разбрызгивание металла.
В зависимости от электродов— сварка плавящимся или неплавящимся (вольфрамовым) электродом. Для сварки неплавящимся электродом используются в основном инертные газы — аргон и гелий или их смеси. Защитные газы оказывают влияние на свойства дуги и форму швов.
В качестве защитных газов применяют инертные (аргон и гелий), активные (углекислый газ, водород, кислород и азот) газы, а также их смеси (Аг + Не, Аг + СО2, Аг + О2, СО2 + О2 и др.).
Недостатки:
К недостаткам способа по сравнению со сваркой под флюсом относится необходимость применения защитных мер против световой и тепловой радиации дуги, использование защитных газов.
Преимущества:
- высокое качество соединения при работе с разными металлами и сплавами вне зависимости от пространственного положения детали;
- широкий диапазон толщин свариваемого металла— от десятой доли до нескольких десятков миллиметров;
- возможность визуального контроля сварочной дуги и ванной, процесса образования сварочного шва;
- узкая зона термического воздействия;
- при многослойной сварке не надо зачищать швы;
- высокая производительность работ;
- не надо удалять флюс или шлак, зачищать швы.
Электронно-лучевая сварка (ЭЛС).
Сущность процесса состоит в использовании кинетической энергии потока электронов, движущихся с высокими скоростями в вакууме. Для уменьшения потери кинетической энергии электронов за счет соударения с молекулами газов воздуха, а также для химической и тепловой защиты катода в электронной пушке создают вакуум порядка 10-4... 10-6 мм рт. ст.
Техника сварки.
Плавление металла происходит на передней стенке кратера, а расплавляемый металл перемещается по боковым стенкам к задней стенке, где он и кристаллизуется. При сварке электронным лучом проплавление имеет форму конуса (рисунок 5).
1 - электронный луч; 2 - передняя стенка кратера;
3 - зона кристаллизации; 4 - путь движения жидкого металла
Рисунок 5 – Сварка электронным лучом
Проплавление при электронно-лучевой сварке обусловлено в основном давлением потока электронов, характером выделения теплоты в объеме твердого металла и реактивным давлением испаряющегося металла, вторичных и тепловых электронов и излучением. Возможна сварка непрерывным электронным лучом. Однако при сварке легкоиспаряющихся металлов (алюминия, магния и др.) эффективность электронного потока и количество выделяющейся в изделии теплоты уменьшаются вследствие потери энергии на ионизацию паров металлов. В этом случае целесообразно сварку вести импульсным электронным лучом с большой плотностью энергии и частотой импульсов 100... 500 Гц. В результате повышается глубина проплавления. При правильной установке соотношения времени паузы и импульса можно сваривать очень тонкие листы. Благодаря теплоотводу во время пауз уменьшается протяженность зоны термического влияния. Однако при этом возможно образование подрезов, которые могут быть устранены сваркой колеблющимся или расфокусированным лучом.
Основные параметры режима электронно-лучевой сварки:
- сила тока в луче;
- ускоряющее напряжение;
- скорость перемещения луча по поверхности изделия;
- продолжительность импульсов и пауз;
- точность фокусировки луча;
- степень вакуумизации.
Основные типы сварных соединений, рекомендуемые для электронно-лучевой сварки, приведены на рисунке 6.
а - стыковое (может быть с бортиком для получения выпуклости шва); б - замковое; в - стыковое деталей разной толщины; г - угловые; д и е - стыковые при сварке шестерен; ж - стыковые с отбортовкой кромок
Рисунок 6 – Основные типы сварных соединений при ЭЛС
Перед сваркой требуется точная сборка деталей (при толщине металла до 5 мм зазор не более 0,07 мм, при толщине до 20 мм зазор до 0,1 мм) и точное направление луча по оси стыка (отклонение не больше 0,2... 0,3 мм).
При увеличенных зазорах (для предупреждения подрезов) требуется дополнительный металл в виде технологических буртиков или присадочной проволоки. В последнем случае появляется возможность металлургического воздействия на металл шва. Изменяя зазор и количество дополнительного металла, можно довести долю присадочного металла в шве до 50 %.
Преимущества:
- высокая концентрация ввода теплоты в изделие, которая выделяется не только на поверхности изделия, но и на некоторой глубине в объеме основного металла;
- фокусировкой электронного луча можно получить пятно нагрева диаметром 0,0002... 5 мм, что позволяет за один проход сваривать металлы толщиной от десятых долей миллиметра до 200 мм.
- появляется возможность сварки тугоплавких металлов (вольфрама, тантала и др.), керамики и т.д.;
- уменьшение протяженности зоны термического влияния снижает вероятность рекристаллизации основного металла в этой зоне;
- малое количество вводимой теплоты;
- отсутствие насыщения расплавленного и нагретого металла газами.
Недостатки электронно- лучевой сварки:
- возможность образования не сплавлении и полостей в корне шва на металлах с большой теплопроводностью и швах с большим отношением глубины к ширине;
- для создания вакуума в рабочей камере после загрузки изделий требуется длительное время.
В результате проделанного анализа, для сварки продольного шва корпуса фильтра выберем сварку в защитных газах в среде СО2.
Обработка швов после сварки
Зачистка сварного шва, проведенная по всем правилам, предотвращает появление на металлоизделии коррозии, препятствует скапливанию в местах соединения грязи. Даже нержавеющая сталь при халатной сварке и обработке соединений со временем может окислиться и заржаветь из-за того, что посторонние частицы проникают в микропоры. Плохо зачищенный сварной шов также в разы сокращает срок эксплуатации изделия, которое используется в местах повышенной влажности или находится под воздействием химически агрессивных сред (кислот или щелочей).
Все работы по зачистке сварного шва подразделяются на несколько процессов:
- очистка участка от окалины и шлаков;
- удаление усиления швов;
- подготовка участка к финишной обработке.
Эти процессы требуют профессионального подхода, определенных знаний и навыков.
Обычно к оборудованию для работы со сварными соединениями относят абразивные материалы и шлифовальные машины. Иногда производители отдают предпочтение обработке специальными средствами – пастами или гелями. Еще один метод – пескоструйная обработка.
Зачистка сварных соединений состоит из таких этапов:
- удаление сварных швов шлифовальными кругами и зачистка около шовной зоны от сторонних образований;
- агрессивная обработка соединений фибровыми или лепестковыми кругами;
- зачистка швов в труднодоступных местах с помощью специализированного инструмента.
Оборудование для выполнения всех вышеперечисленных задач подразделяется на:
- ручной инструмент;
- станки;
- специальные зачистные станции.
Для зачистки сварного шва воспользуемся шлиф машинкой пневматической ручной ШПР-2014. После зачистки кромок для удаления стружки обдувают сжатым воздухом и обезжиривают салфеткой смоченной ацетом. После сварки производят зачистку сварного шва от шлаковой пленки металлической щеткой и дальнейшего контроля внешним осмотром.
Сварочные материалы
Сварочная проволока
Св–08Г2С – один из наиболее универсальных типов сварочной проволоки, используемых в механизированных сварочных процессах. Эта проволока подходит как для использования в сварочных автоматах, так и в устройствах полуавтоматической сварки. Омедненная проволока применяется для сварки в среде защитных газов (CO2 или смесь CO2 с 20 % содержанием Ar). Проволока СВ-08Г2С позволяет использовать при сварке чистый CO2, что значительно удешевляет и ускоряет производственные процессы. Для высоконагруженных конструкций, при сварке проволокой Св-08Г2С можно использовать газовую смесь из CO2 (80 %) и Ar (20 %). В такой газовой смеси сварочный шов, выполненный с использованием омедненной проволоки Св-08Г2С будет иметь самые высокие показатели ударной вязкости и предела прочности. Этот тип проволоки можно использовать любыми сварочными аппаратами в любых пространственных положениях.
Химические состав сварочной проволоки представлены в таблице 3.
Таблица 3 – Химический состав сварочной проволоки СВ-08Г2С
Химический элемент | Химический состав | ||||||
Углерод С | Кремний Sl | Марганец Mn | Хром Cr | Никель Ni | Сера S | Фосфор Р | |
Требования ГОСТ 2246-70 | 0,05-0,11 | 0,70-0,95 | 1,80-2,10 | <0,20 | <0,25 | <0,025 | <0,03 |
Результаты испытаний | 0,06-0,08 | 0,75-0,92 | 1,80-1,92 | 0,05 | 0,044 | 0,010 | 0,01 |
Механические свойства сварочной проволоки представлены в таблице 4.
Таблица 4 – Механические свойства сварочной проволоки
Диаметр, мм | Требования ГОСТ Временное сопротивление разрыву, МПа | Результаты испытаний Временное сопротивление разрыву, МПа |
0,8 | 880-1323 | 1150-1300 |
1 | 880-1323 | 1250-1300 |
1,2 | 880-1323 | 1050-1300 |
1,6 | 880-1274 | 1000-1150 |
Сварочную проволоку Св-08Г2С при производстве покрывают защитным слоем меди. Омедненная проволока имеет большие сроки хранения и в меньшей степени подвержена химическим и физическим воздействиям во время хранения. В настоящее время сварочная омедненная проволока с маркировкой Св-08Г2С производится многими заводами на территориях России, стран СНГ, Китае и Турции.
Основные преимущества сварочной проволоки:
- отличное качество и герметичность сварочного шва;
- устойчивое горение дуги в широком диапазоне режима сварки (от капельного до струйного переноса электродного металла в сварочную ванну) при использовании сварочного оборудования любого класса сложности;
- уменьшается уровень потери металла на разбрызгивание на 40 % при сварке в защитных газах;
- снижение пористости, улучшенный внешний вид;
- низкий расход медных наконечников (покрытие проволоки не оказывает абразивного воздействия на канал наконечника);
- повышение уровня механизации сварочных работ;
- хорошее повторное зажигание дуги (специально для роботизированной сварки).
Недостатки:
- неравномерная намотка;
- неравномерный диаметр;
Первый недостаток в большинстве случаев приводит к скорому износу всего оборудования для выполнения сварки и его окончательной поломке.
Проволока Св-08Г2С поступает на рынок, как правило, в катушках по 15 или 5 кг. Однако лучшим вариантом считается приобретение материала в упаковке (без намотки на бобину) – 80, 250 кг. В этом случае обеспечивается минимальный износ подающей системы, так как проволока выходит «напрямую». Рассмотрим пример хранения сварочной проволоки Св-08Г2С рисунке 11.
Рисунок 11 – Хранение проволоки Св-08Г2С
Проволока сварочная Св-08Г2С обеспечиваю стабильное горение дуги в широком диапазоне режимов сварки (от капельного до струйного переноса электродного металла в сварочную ванну). При использовании сварочного оборудования любого класса сложности (от простых до импульсных и инверторных источников питания).
Защитный газ
Углекислота (CO2) - применяется для создания защитной среды при сварке металлов, при производстве газированных напитков, для получения сухого льда, для охлаждения, замораживания и хранения пищевых продуктов при прямом и косвенном контакте с ними, для сушки литейных форм, при пожаротушении и других целей во всех отраслях промышленности.
Углекислота жидкая – это, сжиженный углекислый газ под очень высоким давлением, которое обычно равно 70 атмосферам. Жидкость, как и газ, абсолютно бесцветна, имеет слегка кислый привкус.
Углекислота жидкая получается химическим методом, когда очистке поддается двуокись углерода. Из нее удаляются все сернистые соединения, далее происходит процесс конденсации газа в жидкое состояние.
При выпуске сжиженного углекислого газа из баллона, то некоторая его часть начинает испаряться, а остальное образует мелкие хлопья сухого льда. Это действие можно наблюдать при тушении пожара с помощью огнетушителей, когда, при нажатии на рычаг производится струя белой жидкости в результате, белые хлопья тушат пламя.
Поставляется и хранится углекислота в 40-литровых герметичных баллонах, которые защищены от коррозийных разрушений.
Эти баллоны имеют специальную маркировку, также их запрещается хранить вблизи нагревательных приборов и в помещениях с низкой температурой.
Любое механическое сдавливание или удары также могут привести к разгерметизации и порче баллона и его содержимого.
Жидкая углекислота (двуокись углерода) с каждым годом находит все большее применение производителей сварочных работ, где она используется в качестве защитного газа.
В последнее время получает все большее применение на ремонтных предприятиях и в автосервисе метод очистки загрязненных деталей и двигателей гранулами сухого льда.
Регламентирующая документация:
- ГОСТ 12.2.085-2002 Сосуды, работающие под давлением. Клапаны предохранительные. Требования безопасности;
- ПОТ РМ 014-2000. Межотраслевые правила по охране труда. Пункт 8.3. Требования безопасной эксплуатации сосудов, работающих под давлением;
- ГОСТ 8050-85 Двуокись углерода газообразная и жидкая. Технические условия.
Требования к баллонам. Заправка баллонов углекислотой.
Баллоны CO2 должны быть окрашены в черный цвет, а также содержать на корпусе надпись «Углекислота» желтого цвета.
Кроме надписи на верхней сферической части баллона должны быть нанесены и хорошо читаемы следующие данные: торговый знак производителя баллона, номер баллона, вес пустого баллона с точностью до 0.1 кг., дата следующего освидетельствования баллона.
В соответствии с законодательными требованиями, «сосуды, работающие под давлением, должны подвергаться техническому освидетельствованию (наружному, внутреннему осмотру и гидравлическому испытанию) после монтажа до пуска в работу, а также периодически в процессе эксплуатации и в необходимых случаях – внеочередному освидетельствованию».
Освидетельствование баллонов с углекислотой необходимо производить не реже, чем один раз в 5 лет.
Сертифицированные баллоны заправляют пищевым углекислым газом высшего сорта на специализированных заправках.
Запрещается наполнять газом баллоны, у которых:
- истек срок назначенного освидетельствования;
- истек срок проверки пористой массы;
- поврежден корпус баллона;
- неисправны вентили;
- отсутствуют надлежащая окраска или надписи;
- отсутствует избыточное давление газа;
- отсутствуют установленные клейма.
Запрещается очистка и окраска наполненных газом баллонов, а также укрепление колец на их горловине.
Транспортировка баллонов CO2:
При транспортировке баллонов с углекислым газом следует соблюдать следующие требования:
- транспортировать баллоны на грузовом автомобиле рекомендуется в горизонтальном положении. В вертикальном положении баллоны разрешается транспортировать при наличии специальных ограждений, препятствующих падению баллонов;
- при транспортировке необходимо избегать нагревания баллонов, а также оберегать от ударов (повреждения баллона);
- при перевозке нескольких баллонов следует использовать резиновые защитные кольца, а также деревянные прокладки между баллонами;
- переносить баллоны CO2 вручную или перекатывать баллоны по земле запрещается. Для перемещения следует использовать специальные тележки или носилки;
- запрещается перевозить баллоны с углекислотой внутри корпуса торгового автомата (при транспортировке автомата).
Хранение баллонов CO2:
Баллоны с углекислотой могут храниться как в специальных помещениях, так и на открытом воздухе. При хранении баллонов на улице, следует ограничить доступ к баллонам прямых солнечных лучей и осадков. При хранении углекислоты в помещении, баллоны следует размещать не менее чем в 1 м. от источника отопления. Колпаки и заглушки должны быть завернуты.
В горизонтальном положении баллоны хранят на деревянных рамах или стеллажах, вентили должны быть направлены в одну сторону. При вертикальном хранении баллоны устанавливают в специальные гнезда, клети, или ограждают барьером от падения.
При эксплуатации баллона следует соблюдать следующие правила:
- соединение углекислотного баллона с автоматом должно производиться обязательно через редукционный вентиль, снабженный манометром и предохранительным клапаном;
- разборка и ремонт вентилей баллонов и редукторов на рабочем месте запрещается;
- ремонт должен производиться подготовленным персоналом;
- при работе с баллоном необходимо расположить выходное отверстие вентиля баллона в сторону от работника;
- не следует допускать обмерзания вентиля баллона с углекислотой и редуктора;
- обслуживающий персонал должен быть проинструктирован по работе с углекислотными баллонами.
Сварочное оборудование
Сварочный полуавтомат
Полуавтомат для дуговой сварки ПДГ-508 мощный, с широким диапазоном регулирования сварочных параметров, предназначенный для сварки сплошной проволокой малоуглеродистой и низколегированной стали в защитной среде углекислого газа, а также легированных и нержавеющих (коррозионностойких) сталей в среде аргона (рисунок 15).
Рисунок 15– Полуавтомат ПДГ- 508
Полуавтомат типа ПДГ-508 выполнен со ступенчатым регулированием скорости подачи электродной проволоки за счет переключения шестерен в коробке скоростей. Проволока подается одной парой роликов. Изменяют скорость подачи поворотом маховичков на передней стенке механизма подачи.
Технические параметры полуавтомата приведены в таблице 6.
Таблица 6 – Технические параметры полуавтомата ПДГ – 508
Параметр | Значение |
Номинальный сварочный ток: при ПВ=60 % и цикле сварки 5 мин, А | 500 |
Номинальное напряжение, питающей сети, В | 380 |
Частота, Гц | 50 |
Расход защитного газа, л/ч | 480-1280 |
Номинальное сварочное напряжение, В | 50 |
Диаметр порошковой проволоки, мм | 1,6-2,8 |
Регулирование скорости подачи электродной проволоки, м/ч | ступенчатое |
Мощность электродвигателя подающего механизма, Вт | 145 |
Пределы регулирования сварочного тока, А | 100-500 |
Диаметр электродной проволоки, мм | 1,2-2,0 |
Скорость подачи электродной проволоки, м/ч | 120-1100 |
Габаритные размеры, мм | 445х316х37 |
Масса не более, кг | 23 |
Управление полуавтоматом осуществляется с помощью органов управления, расположенных на механизме подачи и кнопки на горелке. Полуавтоматы имеют независимое, плавное регулирование скорости подачи электродной проволоки, которое регулируется ручкой потенциометра, расположенного на механизме подачи.
Источник питания
В качестве источника питания дуги может применяться любой сварочный выпрямитель с жесткой характеристикой.
В качестве источника питания используем ВДУ-506.
Сварочный выпрямитель ВДУ-506 предназначен для полуавтоматической (механизированной) и автоматической сварки в составе сварочных полуавтоматов и автоматов плавящейся электродной проволокой в среде защитных газов и под флюсом, а также для сварки порошковой проволокой (рисунок 16).
Рисунок 16 – Сварочный выпрямитель ВДУ- 506
Сварочный выпрямитель ВДУ-506 имеет два вида вольтамперной характеристики: жёсткую и падающую, и может использоваться для ручной дуговой сварки.
Технические характеристики представлены в таблице 7.
Таблица 7 – Технические характеристики ВДУ-506
Наименование параметра | Значение |
Напряжение питания, В, 50 Гц | 3х380 |
Номинальный сварочный ток, А | 500 |
Диапазон регулирования сварочного тока, А Для жестких характеристик Для падающих характеристик | 60-500 50-500 |
Пределы регулирования рабочего напряжения, В Для жестких характеристик Для падающих характеристик | 18-50 22-46 |
Потребляемая мощность, кВА, не более | 40 |
Напряжение холостого хода, В | 85 |
Продолжительность цикла сварки, мин | 10 |
Продолжительность включения (ПВ), % | 60 |
Габаритные размеры ДхШхВ, мм | 830х620х1080 |
Масса, кг | 290,0 |
Достоинства сварочного выпрямителя ВДУ-506:
- плавная дистанционная регулировка напряжения на дуге с помощью потенциометра механизма подачи проволоки (или с трактора);
- плавная регулировка сварочного тока потенциометром на лицевой панели;
- защита от короткого замыкания при помощи автоматического выключателя;
- вольтметр и амперметр для контроля режима сварки;
- контроль работы вентилятора ветровым реле;
- питание 36 В подогревателя СО2;
- режим ручной сварки;
- колеса для перемещения по рабочей зоне.
Сварочный осциллятор
Сварочный осциллятор – это устройство для возбуждения и стабилизации дуги, приспособленное для работы с серийными источниками питания переменного и постоянного тока. Сварочный осциллятор представляет собой искровой генератор затухающих колебаний. Он содержит низкочастотный повышающий трансформатор ПТ, вторичное напряжение которого достигает 2—3 кВ, разрядник, колебательный контур, составленный из емкости, индуктивности, обмотки связи и блокировочного конденсатора. Обмотки, в сварочном осцилляторе образуют высокочастотный трансформатор ВТ. Вторичное напряжение ПТ в начале полупериода заряжает конденсатор и при достижении определенной величины вызывает пробой разрядника. В результате колебательный контур о
|
|
Архитектура электронного правительства: Единая архитектура – это методологический подход при создании системы управления государства, который строится...
Особенности сооружения опор в сложных условиях: Сооружение ВЛ в районах с суровыми климатическими и тяжелыми геологическими условиями...
Своеобразие русской архитектуры: Основной материал – дерево – быстрота постройки, но недолговечность и необходимость деления...
Биохимия спиртового брожения: Основу технологии получения пива составляет спиртовое брожение, - при котором сахар превращается...
© cyberpedia.su 2017-2024 - Не является автором материалов. Исключительное право сохранено за автором текста.
Если вы не хотите, чтобы данный материал был у нас на сайте, перейдите по ссылке: Нарушение авторских прав. Мы поможем в написании вашей работы!