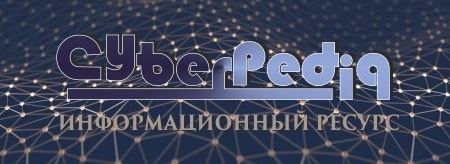
Эмиссия газов от очистных сооружений канализации: В последние годы внимание мирового сообщества сосредоточено на экологических проблемах...
Адаптации растений и животных к жизни в горах: Большое значение для жизни организмов в горах имеют степень расчленения, крутизна и экспозиционные различия склонов...
Топ:
Характеристика АТП и сварочно-жестяницкого участка: Транспорт в настоящее время является одной из важнейших отраслей народного...
Оснащения врачебно-сестринской бригады.
Эволюция кровеносной системы позвоночных животных: Биологическая эволюция – необратимый процесс исторического развития живой природы...
Интересное:
Отражение на счетах бухгалтерского учета процесса приобретения: Процесс заготовления представляет систему экономических событий, включающих приобретение организацией у поставщиков сырья...
Принципы управления денежными потоками: одним из методов контроля за состоянием денежной наличности является...
Финансовый рынок и его значение в управлении денежными потоками на современном этапе: любому предприятию для расширения производства и увеличения прибыли нужны...
Дисциплины:
![]() |
![]() |
5.00
из
|
Заказать работу |
Содержание книги
Поиск на нашем сайте
|
|
НОВОТРОИЦКИЙ ФИЛИАЛ
Кафедра металлургических технологий и оборудования
Н.Г. Куницина
ТЕОРИЯ И ТЕХНОЛОГИЯ ПРОЦЕССОВ
ОбработкИ металлов давлением
Учебное пособие
по дисциплинам «Обработка металлов давлением»,
«Технологии процессов обработки металлов давлением»
для студентов направлений подготовки
22.03.02 «Металлургия», 38.03.01 «Экономика»
всех форм обучения
Новотроицк, 2015
УДК 669.771
Рецензенты:
Доцент кафедры технологий обработки материалов Института металлургии,
машиностроения и материалообработки ФГБОУ ВПО МГТУ им. Г.И. Носова,
к.т.н. Синицкий О.В.
Заведующий кафедрой металлургических технологий и оборудования
Новотроицкого филиала ФГАОУ ВПО НИТУ «МИСиС», к.т.н. Шаповалов А.Н.
Куницина Н.Г. Учебное пособие по дисциплинам «Обработка металлов давлением», «Технологии процессов обработки металлов давлением» для студентов направлений подготовки 22.03.02 «Металлургия», 38.03.01 «Экономика» всех форм обучения. – Новотроицк: НФ НИТУ МИСиС, 2015. – 100 с.
Учебное пособие содержит основные сведения теории и технологии процессов обработки металлов давлением. Достаточно подробно изложены материалы по основам теории пластической деформации: напряженное и деформированное состояние, внешнее трение, физическая сущность обработки давлением. Освещен сортамент профилей, основные операциии и оборудование цехов обработки металлов давлением.
Материал учебного пособия подготовлен на основе трудов ведущих специалистов в области обработки металлов давлением Бахтинова В.Б., Громова Н.П., Зото-ва В.Ф., Суворова И.К. и др.
Пособие составлено в соответствии с требованиями ФГОС ВО подготовки бакалавров направлений 22.03.02 «Металлургия» и 38.03.01 «Экономика», обучающихся в Новотроицком филиале НИТУ «МИСиС».
|
Рекомендовано Методическим советом Новотроицкого филиала НИТУ «МИСиС»
© Новотроицкий филиал
ФГАОУ ВПО «Национальный
исследовательский
технологический университет
«МИСиС», 2015.
Содержание
Введение..................................................................................................................................................... 4
1 Основы теории процессов обработки металлов давлением........................................................ 5
1.1 Основные процессы обработки металлов давлением........................................................... 5
1.2 Кристаллическое строение металлов....................................................................................... 6
1.3 Упругая и пластическая деформация....................................................................................... 7
1.4 Напряженно – деформированное состояние металла в процессах
обработки давлением.......................................................................................................................... 9
1.5 Механизмы пластической деформации металлов............................................................... 10
1.6 Наклеп и рекристаллизация...................................................................................................... 12
1.7 Пластичность металлов и сопротивление металлов пластической деформации....... 14
1.8 Внешнее трение при обработке металлов давлением......................................................... 16
2 Прокатное производство................................................................................................................... 21
2.1 Общая характеристика прокатного производства............................................................... 21
2.2 Профильный и марочный сортамент прокатной продукции........................................... 22
2.3 Сущность процесса прокатки. Характеристики деформации при прокатке.................. 26
2.4 Классификация прокатных станов........................................................................................... 39
2.5 Технологические операции при производстве проката..................................................... 45
2.6 Производство полупродукта.................................................................................................... 52
2.7 Производство сортового проката............................................................................................ 53
|
2.8 Производство горячекатаных листов..................................................................................... 54
2.9 Производство холоднокатаных листов.................................................................................. 56
3 Прессовое производство................................................................................................................... 60
3.1 Сущность прессования. Основные способы прессования
Характеристики деформации при прессовании.......................................................................... 60
3.2 Оборудование для прессования............................................................................................... 64
3.3 Технологические операции при прессовании...................................................................... 65
4 Волочение............................................................................................................................................. 66
4.1 Сущность волочения. Характеристики деформации при волочении............................. 66
4.2 Оборудование для волочения.................................................................................................. 70
4.3 Технологические операции при волочении.......................................................................... 71
5 Ковка металла...................................................................................................................................... 75
5.1 Сущность ковки. Операции свободной ковки. Характеристики
деформации при ковке...................................................................................................................... 75
5.2 Оборудование для свободной ковки....................................................................................... 80
5.3 Технологические операции при свободной ковке............................................................... 81
6 Штамповка металла............................................................................................................................ 82
6.1 Объемная штамповка.................................................................................................................. 82
6.2 Листовая штамповка................................................................................................................... 88
7 Специальные процессы обработки металлов давлением........................................................... 93
7.1 Производство гнутых профилей.............................................................................................. 93
7.2 Производство периодического проката................................................................................. 94
7.3 Производство железнодорожных колес................................................................................ 95
7.4 Производство зубчатых колес.................................................................................................. 96
7.5 Производство шаров................................................................................................................... 97
Список использованных источников................................................................................................. 99
|
Введение
Металлургическое производство подразделяется на две основные стадии. В первой получают металл заданного химического состава из исходных материалов. Во второй стадии металлу в пластическом состоянии придают ту или иную необходимую форму при практически неизменном химическом составе обрабатываемого материала. При этом изменение формы тела осуществляется преимущественно с помощью давящего на металл инструмента. Поэтому получение изделия таким способом называют обработкой металлов давлением или пластической обработкой.
Пластическое деформирование при обработке давлением, состоящее в преобразовании заготовки простой формы в деталь более сложной формы того же объема, относится к малоотходной технологии.
Обработкой давлением получают не только заданную форму и размеры, но и обеспечивают требуемое качество металла, надежность работы изделия.
Высокая производительность обработки давлением, низкая себестоимость и высокое качество продукции привели к широкому применению этих процессов.
Динамичный и пропорциональный рост черной и цветной металлургии, производство изделий из металлов и сплавов пластической обработкой основываются на дальнейшем развитии теории обработки металлов давлением, являющейся научной базой разработки технологических операций получения изделий из металлов и сплавов. Теория пластической обработки металлов позволяет оценить экономическую целесообразность принятого способа деформации, выявить влияние условий обработки на свойства получаемых изделий, определить силовые и энергетические параметры процесса и указать пути их рационального изменения, дает возможность управлять процессом обработки с точки зрения улучшения способности металлов пластически деформироваться. Знание закономерностей обработки металлов давлением помогает выбирать наиболее оптимальные режимы технологических процессов, требуемое основное и вспомогательное оборудование и технически грамотно его эксплуатировать.
1 Основы теории процессов обработки металлов давлением
|
Обработки давлением
Если к металлическому телу, один конец которого закреплен, приложить внешнюю, например, растягивающую силу, то в теле возникнут внутренние силы, направленные в сторону, противоположную действию внешней силы. Появление в теле внутренних сил необходимо для уравновешивания внешних сил. Взаимно уравновешиваться эти силы могут только при действии на абсолютно твердые тела. Поскольку таких тел в природе нет, то при действии внешней силы металлическое тело испытывает деформацию. Деформация осуществляется до тех пор, пока между внешними и внутренними силами не наступит равновесие.
Появление в металлическом теле внутренних сил свидетельствует о том, что тело находится в напряженном состоянии. Под напряженным состоянием тела понимают состояние вынужденного отклонения атомов от положения устойчивого равновесия в элементарной кристаллической решетке, вследствие чего атомы стремятся вернуться к своим нормальным положениям.
Напряженное состояние в точке или в некотором объеме деформируемого тела характеризуется схемой главных нормальных напряжений, действующих в трех взаимно перпендикулярных площадках. Схема главных напряжений дает графическое представление о наличии и знаке главных напряжений, возникающих под влиянием внешне приложенных сил.
Возможны девять схем напряженного состояния (рисунок 8). Напряженное состояние в точке может быть линейным, плоским или объемным.
Рисунок 8 – Схемы напряженного состояния
Схемы с напряжениями одного знака называют одноименными, а с напряжениями разных знаков – разноименными. Условно растягивающие напряжения считают положительными, а сжимающие – отрицательными.
Схема напряженного состояния оказывает влияние на пластичность металла. На значение главных напряжений оказывают существенное влияние силы трения, возникающие в месте контакта заготовки с инструментом, и форма инструмента.
В реальных процессах обработки давлением в большинстве случаев встречаются схемы всестороннего сжатия и состояния с одним растягивающим и двумя сжимающими напряжениями.
При прокатке, прессовании, ковке и объемной штамповке напряженное состояние металла характеризуется схемой всестороннего сжатия О1. При этом во всех случаях главное напряжение сжатия – максимальное, так как создается давлением инструмента на металл. Напряжения
и
меньше
, так как создаются либо подпирающими силами трения, препятствующими течению металла в соответствующем направлении, либо боковыми стенками инструмента (калибра, штампа). Наибольшее течение металла происходит в направлении той оси, где действует минимальное напряжение (чаще всего
).
|
При волочении напряженное состояние характеризуется схемой О2: по оси прутка действует напряжение растяжения, по двум другим осям – напряжения сжатия, возникающие из-за давления волоки.
При листовой штамповке отдельные участки изделия характеризуются различными схемами напряженного состояния.
Схема деформированного состояния графически отображает наличие и направление деформации по трем взаимно перпендикулярным направлениям.
Возможны три схемы деформированного состояния (рисунок 9).
Рисунок 9 – Схемы деформированного состояния
При схеме D1 уменьшаются размеры тела по высоте, за счет этого увеличиваются два других размера (ковка, прокатка).
При схеме D2 происходит уменьшение одного размера, чаще высоты, другой размер (длина) увеличивается, а третий (ширина) не изменяется. Например, прокатка широкого листа, когда его ширина в процессе прокатки практически не изменяется. Это схема плоской деформации.
Наиболее рациональной с точки зрения производительности процесса обработки давлением является схема D3 размеры тела уменьшаются по двум направлениям, и увеличивается третий размер (прессование, волочение).
Совокупность схем главных напряжений и главных деформаций характеризуют пластичность металла. Напряженное состояние при прессовании металла характеризуется такой же схемой напряженного состояния, как при ковке, а схема главных деформаций характеризуется двумя деформациями сжатия и одной – растяжения. При ковке и штамповке растягивающие напряжения играют большую роль, поэтому пластичность металла меньше.
Наклеп и рекристаллизация
Как было показано выше, изменение формы и размеров поликристаллического металла в результате пластической деформации в той или иной мере связано с изменением формы отдельно взятого зерна. Поэтому при пластической деформации металл претерпевает структурные изменения, что ведет к изменению механических и других свойств металла. В деформируемом металле с увеличением степени деформации увеличиваются его прочностные характеристики. Явление изменения структуры и увеличение механических свойств металла в процессе пластической деформации называется наклепом или упрочнением. Явление упрочнения в настоящее время объясняет теория дислокаций. Упрочнение – это увеличение сопротивляемости сдвигу, которое вызывается накоплением (повышением плотности) дислокаций при пластической деформации. Продвижение дислокаций по кристаллу затрудняется в связи со скоплением их у препятствий. Такими препятствиями могут быть другие дислокации, границы зерен и т.д. В результате плотность дислокаций значительно возрастает. Так, предельная плотность дислокаций в упрочненном металле составляет 1011–1012 на 1 см2 площади. Кроме того, упрочнение вызывается также торможением дислокаций в связи с измельчением зерен, искажением решетки металла, возникновением напряжений. Особенно эффективными «барьерами» для дислокаций являются границы зерен.
В результате пластической деформации при низкой температуре металл не только упрочняется, но также изменяются многие его свойства. Более интенсивно изменение свойств происходит в области малых деформаций. При больших деформациях свойства изменяются в меньшей степени. Применительно к механическим свойствам металлов следует отметить, что с увеличением степени пластической деформации характеристики прочности возрастают, а характеристики пластичности убывают.
Появление наклепа при деформации позволяет в широких пределах регулировать конечные свойства металлоизделий. Холодной пластической обработкой (прокаткой, волочением и др.) можно в 2–3 раза повысить предел прочности и увеличить предел текучести.
С другой стороны, упрочнение заметно увеличивает сопротивление металла пластической деформации, а это увеличивает усилия, необходимые при деформировании. Одновременно с этим наклеп вызывает понижение пластических свойств металла, что приводит к опасности образования трещин, расслоений и других дефектов при дальнейшей деформации.
В наклепанном металле в результате пластической деформации происходит искажение кристаллической решетки. Атомы в такой решетке стремятся к перестройке, приводящей к уменьшению ее искажений, т.е. стремятся к более устойчивому состоянию. При низких температурах подвижность атомов мала. С повышением температуры она увеличивается, начинают развиваться процессы, которые приводят металл к равновесному состоянию.
Различают следующие стадии процесса устранения наклепа при нагреве: отдых (возврат), первичная рекристаллизация или рекристаллизация обработки, собирательная рекристаллизация или рост зерен, вторичная рекристаллизация.
Под отдыхом (возвратом) понимают частичное снятие напряжений и восстановление упруго искаженной кристаллической решетки путем перемещения атомов на небольшие расстояния, при нагреве металла на относительно невысокие температуры (ниже температуры рекристаллизации). При отдыхе заметных изменений в микроструктуре не наблюдается, металл сохраняет волокнистое строение. В результате отдыха твердость и прочность несколько понижаются, а пластичность возрастает.
При нагреве до достаточно высоких температур подвижность атомов заметно возрастает, и происходят процессы рекристаллизации.
Рекристаллизацией называется процесс образования и роста новых зерен при нагреве наклепанного металла до определенной температуры (температуры начала рекристаллизации). Этот процесс протекает в две стадии. Различают рекристаллизацию первичную (обработки) и собирательную.
Первичная рекристаллизация заключается в образовании зародышей и росте новых
зерен с неискаженной кристаллической решеткой. Зародыши новых зерен возникают у границ, и особенно в местах пересечения границ зерен, пачек скольжения двойников. В местах, связанных с наибольшими искажениями решетки при наклепе, происходит перемещение атомов, восстановление решетки и возникновение зародышей новых равноосных зерен. Вначале процесс протекает медленно, происходит зарождение центров кристаллизации, затем образуются мелкие зерна, которые растут и входят в непосредственное соприкосновение друг с другом. Стадия первичной рекристаллизации длится до тех пор, пока новые неискаженные зерна не заполнят весь объем металла.
Собирательная рекристаллизация является второй стадией процесса рекристаллизации и заключается в росте образовавшихся зерен. При этом одни зерна растут за счет других, за счет перехода атомов через границы раздела. Процессы собирательной рекристаллизации могут совершаться и до полного завершения первичной рекристаллизации. Результатом этого процесса может быть резкая неоднородность структуры по величине зерна.
Скорость рекристаллизации и характер конечной структуры зависят от многих факторов: степени предварительной деформации, температуры нагрева, скорости нагрева, скорости деформации, наличия примесей в сплаве и др. Основными из указанных факторов являются степень предварительной деформации и температура нагрева.
С началом рекристаллизации происходит существенное изменение свойств металла, которое противоположно изменению свойств металла при наклепе. При повышении температуры происходит разупрочнение металла, понижается прочность и твердость, а также электросопротивление и другие свойства, которые повышаются при наклепе. В то же время увеличиваются пластичность, а также вязкость, теплопроводность и другие свойства по сравнению с наклепанным состоянием.
При обработке металлов давлением процессы упрочнения (наклепа) и разупрочнения (рекристаллизационного отжига) протекают одновременно. Эти процессы обусловлены условиями деформации (температурой, скоростью, степенью деформации), происходят во времени, с определенными скоростями, а также зависят от природы деформируемого металла.
При холодной деформации главенствует упрочнение, а процессы разупрочнения (возврата и рекристаллизации) полностью отсутствуют. В результате плотность и пластичность уменьшаются, металл охрупчивается, при высоких степенях деформации образуется текстура.
В результате теплой деформации рекристаллизация и разупрочнение проходят не полностью, структура металла может быть полосчатой (волокнистой) без следов рекристаллизации, а при значительной деформации наблюдается текстура деформации. Пластические свойства такого металла выше, чем металла, деформированного при отсутствии возврата, а прочностные свойства несколько ниже.
Производство полупродукта
Полупродукт – это промежуточный продукт технологического процесса, предназначенный для дальнейшей переработки. В производстве проката полупродуктом являются блюмы, слябы, заготовка. В настоящее время полупродукт получают двумя способами: прокаткой слитков на обжимных и заготовочных станах и непрерывной разливкой на машинах непрерывного литья заготовок.
Обжимные и заготовочные станы являются промежуточным звеном между сталеплавильными и прокатными цехами, производящими готовый прокат.
На блюмингах и слябингах осуществляется прокатка слитков, различных по размерам и массе, что определяется марочным составом стали, изготовляемым на заводе.
Перед прокаткой осуществляется нагрев слитков в нагревательных колодцах с целью придания металлу высокой пластичности и наименьшего сопротивления его деформации.
Продолжительность нагрева слитков определяется их химическим составом, температурой посада металла в нагревательные устройства и отношением поверхности к их массе.
В настоящее время свыше 90 % слитков в нагревательные колодцы блюмингов и слябингов поступает с температурой 800–900 0С. Такой метод нагрева называется горячим посадом слитков. Применение горячего посада значительно экономит топливо и резко увеличивает пропускную способность нагревательных колодцев.
Посадку слитков производят специальным клещевым краном, а в колодцах их уста-
навливают прибыльной частью вверх. Нагретые слитки при помощи тележки с опрокидывателем (слитковоза) подают к рабочей клети блюминга или слябинга.
Число проходов, за которые прокатывают слитки, предусматривают технологиче-
скими инструкциями. На отечественных обжимных станах стремятся к увеличению обжатий за проход, что приводит к сокращению их числа, а значит, и повышению производительности станов.
Эффективным путем повышения производительности обжимных станов является технология многослитковой прокатки. Многослитковая прокатка заключается в последовательной прокатке двух или более слитков, лежащих на рольганге последовательно один за другим. В каждом пропуске второй слиток подается в валки стана непосредственно за первым без паузы или с минимальной паузой. Многослитковая прокатка ведется опреде-
ленное число пропусков. При достижении раскатами значительной длины каждым в пос-
ледних пропусках их кантуют порознь, а прокатывают парами или по одному.
Технология многослитковой прокатки обеспечивает уменьшение почти в два раза суммарного времени пауз и некоторое уменьшение машинного времени.
После выхода из клети полупродукт в технологическом потоке проходит сплошную зачистку поверхности в машинах огневой зачистки. Эта операция полностью
механизирована и частично автоматизирована.
Иногда на блюмингах и заготовочных станах вместо машин огневой зачистки устанавливают фрезерные многорезцовые станки – термофрезерные машины – для механической зачистки снятием стружки с горячих слитков, блюмов, слябов и заготовки. Этот способ является весьма эффективным.
За машиной огневой зачистки осуществляется обрезка переднего и заднего концов раскатов и порезка их на мерные длины на ножницах. Величина обрези в зависимости от марки стали и условий кристаллизации со стороны усадочной раковины обычно составляет 12–14 % от массы раската, с донной части 2–3 %.
После разрезки на ножницах блюмы или слябы клеймят с торца в горячем состоянии при помощи специального клеймовочного устройства. В клеймо обычно входят следующие знаки и цифры: условный знак завода, марка стали, номер плавки, литера головного блюма или сляба от данного слитка и др.
Полученный полупродукт больших сечений может сразу в потоке прокатываться на заготовочных станах или передаваться к печам сортовых станов.
Готовые блюмы и слябы в пролете остывания укладывают в штабеля.
Остывший полупродукт, в случае необходимости, зачищают и после приемки контроллерами передают на склад заготовки.
Оборудование для волочения
Технологический процесс волочения осуществляется на специальных волочильных станах.
В зависимости от типа тянущего устройства различают станы: с прямолинейным
движением протягиваемого металла (цепной, реечный); с наматыванием обрабатываемого металла на барабан (барабанный).
Цепные или реечные станы используют для волочения профилей, наматывание которых в бунт вызывает определенные трудности, например, из-за значительных размеров поперечного сечения.
На цепных (реечных) станах протягивают профили и трубы в виде длинных штанг. Протягивание заготовки через волоку осуществляется электрическим двигателем, вращательное движение которого преобразуется в прямолинейное движение цепи и волочильной тележки. Передний конец заготовки, выходящий из волоки, зажимается специальными захватами тележки. Заготовка, протягиваясь через волоку, приобретает форму заданного изделия.
Барабанные станы применяются для волочения проволоки, профилей, форма поперечного сечения которых позволяет сматывать их в бунт. Барабанные станы могут быть однократного или многократного волочения, что определяется числом осуществляемых на них протяжек (рисунок 39).
![]() |
а
б
Рисунок 39 – Схемы барабанного стана однократного (а) и
многократного (б) волочения
Принцип работы станов многократного волочения заключается в том, что пластическое деформирование прутка последовательно выполняется в нескольких волоках. Причем по выходе из одной волоки протягиваемый металл наматывается на барабан и в тоже время другой конец прутка сматывается с него, поступая через следующую волоку на другой барабан и т.д. Это сокращает количество вспомогательных операций и существенно повышает производительность.
Барабан воспринимает значительные усилия волочения при наматывании изделия. Для уменьшения износа барабана его рабочей поверхности придают повышенную твердость.
Деформации при ковке
Ковка представляет собой широко распространенный способ обработки металлов давлением с целью получения изделий, называемых поковками.
Ковка – способ обработки давлением, при котором деформирование нагретого (реже холодного) металла осуществляется или многократными ударами молота или однократным давлением пресса.
Формообразование при ковке происходит за счет пластического течения металла в направлениях, перпендикулярных к движению деформирующего инструмента. При свободной ковке течение металла ограничено частично, трением на контактной поверхности деформируемый металл – поверхность инструмента: бойков плоских или фигурных, подкладных штампов.
Различают ручную и машинную свободную ковку, которые осуществляются с помощью различного кузнечного инструмента (рисунок 42). Ручную ковку применяют главным образом при ремонтных и сборочных работах, а также при изготовлении мелких поковок в небольшом количестве.
Машинная свободная ковка осуществляется с применением кузнечно – прессовых машин. Мелкие и средние по массе поковки (массой до 750 кг) изготовляют на молотах, а крупные (массой до 350 т) – на прессах.
![]() |
а
б
в
а – обжимки; б – наметки, пережимки, раскатки; в – прошивки
Рисунок 42 – Основной кузнечный инструмент
Технологические процессы ковки представляют собой различное сочетание и последовательность основных и вспомогательных операций, таких как осадка, протяжка, прошивка, гибка, кручение, рубка, кузнечная сварка, а также операции отделки и термической обработки (если это требуется).
Осадка – это операция, при которой за счет обжатия по высоте увеличивается площадь поперечного сечения заготовки, перпендикулярного к деформирующей силе (рисунок 43, а).
Осадка является основной операцией для получения формы поковки, но может при-
меняться также как промежуточная для устранения литой структуры или анизотропии свойств металла.
а – осадка; б – высадка; в – протяжка; г – рубка; д – прошивка; е – раскатка;
ж – рубка; з – кручение; и – сварка
Рисунок 43 – Операции свободной ковки
При выполнении осадки требуется, чтобы инструмент перекрывал заготовку. Вследствие трения боковая поверхность осаживаемой заготовки приобретает бочкообразную форму, это характеризует неравномерность деформации. Повторяя осадку несколько раз с разных сторон, можно привести заготовку к первоначальной форме или близкой к ней, получив при этом более высокое качество металла и одинаковые его свойства по всем направлениям.
Во избежание продольного изгиба заготовки необходимо, чтобы при осадке выполнялось следующее условие:
,
где и
– соответственно начальная толщина, ширина или диаметр заготовки, мм.
Деформация металла при осадке характеризуется коэффициентом ковки:
, (62)
где – коэффициент ковки при осадке;
– толщина поковки после осадки, мм;
– площадь поперечного сечения заготовки и поковки, мм2.
Разновидностью осадки является высадка части заготовки. Высадка может быть
осуществлена при нагревании только определенной части заготовки (на конце или в середине) или ограничением деформации части заготовки кольцевым инструментом (рисунок 43, б).
Очень важным условием при осадке является условие плоской (двумерной) деформации, т.е. деформации без уширения: при (где
и
– соответственно начальные длина и ширина заготовки, мм) деформация является двумерной, и металл течет только в направлении длины.
Усилие при осадке определяется по той же формуле, что и при прокатке .
Однако контактная площадь определяется иначе
, (63)
где – ширина и длина полученной поковки, мм.
Среднее давление металла на инструмент можно определять, как и при прокатке по формуле
.
Однако в отличие от процесса прокатки коэффициент напряженного состояния при ковке определяется весьма сложно и в зависимости от отношения определяется по-разному.
Таким образом
1) при отношении >2+
и 0<
<0,5
, (64)
где – толщина поковки, мм;
– коэффициент трения в процессе ковки.
2) при 2< <2+
и 0<
<0,5
. (65)
3) при
2 и 0<
<0,5
. (66)
4) при
2 и
0,5
. (67)
Сопротивление металла деформации при ковке необходимо определять по уравнению Л.В. Андреюка – Г.Г. Тюленева.
Скорость деформации при операциях ковки определяется из выражения
, (68)
где – высотная деформация при осадке, определяемая как и при прокатке;
– абсолютное обжатие, мм;
– скорость осадки, м/с.
Протяжка – операция, в процессе которой длина заготовки увеличивается за счет уменьшения ее поперечных размеров при последовательных по длине нажатиях бойками.
При протяжке в отличие от осадки заготовку обрабатывают участками при последовательной подачи ее под бойки молота или пресса (рисунок 43, в).
Если сечение нужно уменьшать за счет толщины и ширины заготовки, то после каждой подачи производится осаживание толщины и затем после кантовки на 90 0 – осадки ширины.
Металл, осаживаемый участками по высоте, течет в направлении длины и ширины. К деформируемому за каждый обжим участку с обеих сторон примыкают участки, не подвергающиеся непосредственно действию инструмента. Эти участки сдерживают течение металла в направлении ширины и принудительно выравнивают деформации в длину по всей ширине.
Так как целью протяжки является увеличение длины за счет уменьшения сечения, необходимо обжим осуществлять так, чтобы течение металла в ширину было минимальным. Этого достигают обжимом малыми подачами при малом отношении подачи к ширине заготовки. Однако при малых подачах увеличивается число обжимов и снижается производительность.
Для интенсификации процесса протяжки и получения достаточно гладкой поверхности подачу следует принимать в следующих пределах
, (69)
где – величина подачи заготовки, мм;
– ширина бойков, мм.
Для определения размеров заготовки после обжатия вводится понятие уковки.
Уковка – это коэффициент вытяжки за обжатие:
, (70)
где – коэффициент уковки при протяжке;
– площадь поперечного сечения заготовки до протяжки и поковки после про
тяжки, мм2.
Кроме того, при осадке и протяжке показателем деформации является высотная деформации
.
Удельное усилие (т.е. усилие, приходящееся на единицу площади или среднее давление) при протяжке определяется по формуле
. (71)
Осадка и протяжка являются основными операциями свободной ковки.
Помимо них к операциям ковки относятся следующие.
Рубка, которую применяют для разделения заготовки на несколько частей или для удаления концов поковок при помощи зубил и кузнечных топоров (рисунок 43, г).
Рубка п
|
|
Историки об Елизавете Петровне: Елизавета попала между двумя встречными культурными течениями, воспитывалась среди новых европейских веяний и преданий...
Таксономические единицы (категории) растений: Каждая система классификации состоит из определённых соподчиненных друг другу...
Механическое удерживание земляных масс: Механическое удерживание земляных масс на склоне обеспечивают контрфорсными сооружениями различных конструкций...
Общие условия выбора системы дренажа: Система дренажа выбирается в зависимости от характера защищаемого...
© cyberpedia.su 2017-2024 - Не является автором материалов. Исключительное право сохранено за автором текста.
Если вы не хотите, чтобы данный материал был у нас на сайте, перейдите по ссылке: Нарушение авторских прав. Мы поможем в написании вашей работы!