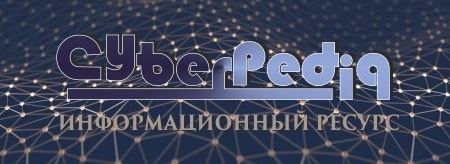
Типы сооружений для обработки осадков: Септиками называются сооружения, в которых одновременно происходят осветление сточной жидкости...
Своеобразие русской архитектуры: Основной материал – дерево – быстрота постройки, но недолговечность и необходимость деления...
Топ:
Характеристика АТП и сварочно-жестяницкого участка: Транспорт в настоящее время является одной из важнейших отраслей народного...
Оценка эффективности инструментов коммуникационной политики: Внешние коммуникации - обмен информацией между организацией и её внешней средой...
Интересное:
Распространение рака на другие отдаленные от желудка органы: Характерных симптомов рака желудка не существует. Выраженные симптомы появляются, когда опухоль...
Берегоукрепление оползневых склонов: На прибрежных склонах основной причиной развития оползневых процессов является подмыв водами рек естественных склонов...
Уполаживание и террасирование склонов: Если глубина оврага более 5 м необходимо устройство берм. Варианты использования оврагов для градостроительных целей...
Дисциплины:
![]() |
![]() |
5.00
из
|
Заказать работу |
Содержание книги
Поиск на нашем сайте
|
|
Литье (заливка) вакуумным высасыванием заключается в заполнении формы металлом за счет создаваемого в нем вакуума. При данном способе литья полость формы заполняется за счет перепада давлений от атмосферного (над зеркалом расплава) до пониженного – 10-80 кПа (в полости формы).
На практике реализуются две основные схемы процесса литья вакуумным всасыванием (ЛВВ):
а) размещение литейной формы в герметичной камере и соединение ее с металлопроводом, погруженным в тигель с расплавом. В данном случае можно использовать формы, полученные любыми известными способами: металлические, песчаные, керамические оболочковые, гипсовые, графитовые и др.;
герметизация полости формы, сообщающейся посредством металлопровода с расплавом. Эта схема широко используется при литье в водоохлаждаемую металлическую форму – кристаллизатор. При этом получают как полые, так и сплошные заготовки и слитки. При наличии герметичного кожуха могут быть использованы и перечисленные в пункте «а» формы.
Преимущества способа заливки вакуумным всасыванием: высокая плотность отливок; отсутствие газовых и усадочных пор, а также литниковой системы и прибылей; хорошее качество поверхности; повышенные механические свойства отливок; достаточная производительность.
Недостатки ЛВВ (в случае использования форм-кристаллизаторов): применимоть его для получения отливок лишь простой формы; волнистость внутренних поверхностей отливок (например, втулок) и, как следствие, необходимость обеспечения припусков на механическую обработку.
Центробежное литье.
Данный способ литья представляет собой процесс формирования отливок под действием центробежных сил при свободной заливке металла во вращающиеся формы. Центробежным способом получают отливки из чугуна, стали, сплавов меди, алюминия. цинка, магния, титана и др.
|
Литейные центробежные машины используются в трех вариантах: с горизонтальной, вертикальной или наклонной осью вращения. В ряде случаев внутренняя поверхность отливки является свободной, поскольку формируется без непосредственного контакта с литейной формой или стержнем. На рабочую поверхность металлических форм (изложниц), предварительно нагретых (или охлажденных) до 300°С, наносят огнеупорное покрытие в виде красок, облицовок (например, смесь песка с пульвербакелитом) и других материалов. Покрытие повышает стойкость формы, снижает скорость охлаждения отливки и возможность образования в ней трещин. Оно может также регулировать структуру и состав поверхностных слоев отливки.
Преимуществами данного способа литья являются: большая производительность способа и возможность его автоматизации; высокий выход годного металла (90-95%); высокая плотность и мелкозернистое строение отливок (за счет больших скоростей охлаждения); реализация направленного затвердевания отливок из сплавов с низкой жидкотекучестью.
Недостатки способа: химическая неоднородность (ликвация) в толстостенных отливках; высокое внутренние напряжение в поверхностном слое, способствующие образованию трещин; возможность деформации формы под давлением жидкого металла, в результате чего отливки образуются с подутостью; разностенность по высоте отливок, полученных в машинах с вертикальной осью вращения.
11.5. Специальные технологии получения художественных изделий методом ОМД.
Формообразование обработкой давлением основано на способности заготовок из металлов и других материалов изменять свою форму без разрушения под действием внешних сил. Обработка давлением – один из прогрессивных, экономичных и высокопроизводительных способов производства заготовок в машино- и приборостроении. Почти 90% всей выплавляемой стали и 60% цветных металлов и сплавов подвергаются тем или иным способом обработки давлением – прокатке, прессованию, волочению, ковке, объемной или листовой штамповке.
|
Механизм деформации поликристаллического тела при обработке давлением можно представить в такой последовательности. В начале под действием приложенных сил начинается сдвиговая пластическая деформация в зернах, плоскости скольжения которых совпадают или близки вектору максимальных касательных напряжений, а также по плоскостям, плоскость дислокаций в которых максимальна. Затем последовательно в процесс включаются плоскости, сопротивление сдвигу которых более высоко. Одновременно происходит смещение и поворот соседних зерен, т. е. переориентация их в пространстве и по отношению к действующим силам.
Прокатка.
Прокатка - вид обработки давлением, при котором исходная заготовка – слиток или отливка – под действием сил трения непрерывно втягивается между вращающимися валками и пластически деформируется с уменьшением толщины с увеличением длины, а иногда ширины. Прокатке подвергаются почти 90% всей выплавляемой стали и значительная часть металлов. В зависимости от формы и расположения валков и заготовок по отношению к ним различают следующие основные виды прокатки: продольная, поперечная и поперечно-винтовая.
При продольной прокатке заготовка деформируется между двумя валками, вращающимися в разные стороны, и перемещается в направлении, перпендикулярном осям валков.
При поперечном прокате валки вращаются в одном направлении, а заготовка, имеющая форму тела вращения, перемещается параллельно осям валков и обжимается по образующей с увеличением длинны и уменьшением площади поперечного сечения.
При поперечно-винтовой прокатке валки расположены под углом друг к другу, вращаются в одну сторону и при обжатии заготовки сообщают ей вращательное и поступательное движения. В процессе прокатки во всех случаях перемещение заготовки между валками обеспечивается наличием контактного трения между обрабатываемой заготовкой и рабочей поверхностью валков.
Прессование.
Прессование – процесс выдавливания металла из контейнера через одно или несколько отверстий в матрице с площадью меньшей, чем поперечное сечение исходной заготовки.
|
Прессование может выполняться двумя методами – прямым и обратным. При прямом методе заготовку помещают в полость контейнера и с помощью мощного процесса через пуансон и пресс-шайбу выдавливают нагретый или холодный металл через отверстие в матрице, укрепленной в матрице-держатель. При обратном прессовании давление пресса передается через полый пуансон с смонтированной внутри его матрицей. Таким образом, металл заготовки течет навстречу движению пуансона.
Волочение.
Волочение – процесс протягивания прутка через отверстие, размеры которого меньше, чем исходные размеры прутка. При этом длинна прутка увеличивается, а поперечное сечение приобретает форму отверстия с одновременным уменьшением поперечного сечения. Волочение производят в холодном состоянии.
Ковка.
Ковкой называют вид обработки давлением, при котором исходную заготовку деформируют универсальным инструментом – бойками: при этом течение металла в стороны перпендикулярно действующему усилию не ограничивается. Ковка предназначена для придания заготовке формы, приближающейся к форме готовой детали. Основные операции ковки – осадка, протяжка, пробивка, прошивка, гибка, скручивание, отрубка и кузнечная сварка.
Осадка – уменьшение высоты заготовки при увеличении площади ее поперечного сечения. Осадку производят бойками или осадочными плитами.
Протяжка – удлинение заготовки или ее части за счет уменьшения площади поперечного сечения. Она осуществляется последовательными обжатиями отдельных, примыкающих друг к другу участков заготовки при ее подаче вдоль оси.
Разновидность протяжки: раскатка и протяжка на оправе. Раскатка – увеличение диаметра кольцевой заготовки при вращении за счет уменьшения ее толщины с помощью бойка и оправки. Инструментами для раскатки служат боек, оправка и люнет. Протяжка на оправке – увеличение длины прошитой или просверленной заготовки за счет обжатия ее по обе стороны оправки двумя бойками (нижним вырезным и верхним плоским или обоими вырезными бойками). При протяжке наружный диаметр и толщина стенки заготовки уменьшается.
|
Гибка – образование или изменение углов между частями заготовки или придание ей криволинейной формы. Гибку осуществляют с помощью различных опор, приспособлений и в подкладных штампах.
Скручивание – поворот части заготовки вокруг продольной оси. Осуществляют, например, при развороте колен коленчатых валов.
Рубка – полное отделение части заготовки по незамкнутому контуру путем внедрения в заготовку деформирующего инструмента. Рубку осуществляют топорами для удаления прибыльной и донной частей слитка, лишних концов поковки или для разделения длинной поковки на более короткие части.
Пробивка – образование в заготовке отверстия с удалением материала в отход путем сдвига. Отверстия диаметром до 500 мм. пробивают сплошным прошивнем с применением прокладного кольца, а отверстия большего диаметра прошивнем, применяя в случае высокой заготовки надставки.
Прошивка – получение полостей в заготовке за счет вытеснения металла.
Кузнечная сварка – образование неразъемного соединения под действием давления в нагретом состоянии.
Штамповка.
Объемная штамповка.
Объемная штамповка – вид обработки металлов давлением, при котором формообразование поковки осуществляется пластическим деформированием заготовки в специальном инструменте – штампе. Полости в верхней и нижней части штампа называют ручьями штампа.
|
|
Организация стока поверхностных вод: Наибольшее количество влаги на земном шаре испаряется с поверхности морей и океанов (88‰)...
Эмиссия газов от очистных сооружений канализации: В последние годы внимание мирового сообщества сосредоточено на экологических проблемах...
Индивидуальные очистные сооружения: К классу индивидуальных очистных сооружений относят сооружения, пропускная способность которых...
Автоматическое растормаживание колес: Тормозные устройства колес предназначены для уменьшения длины пробега и улучшения маневрирования ВС при...
© cyberpedia.su 2017-2024 - Не является автором материалов. Исключительное право сохранено за автором текста.
Если вы не хотите, чтобы данный материал был у нас на сайте, перейдите по ссылке: Нарушение авторских прав. Мы поможем в написании вашей работы!