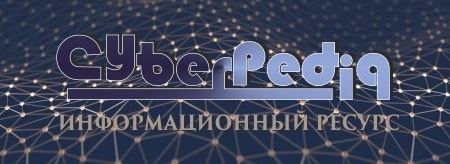
Общие условия выбора системы дренажа: Система дренажа выбирается в зависимости от характера защищаемого...
Типы сооружений для обработки осадков: Септиками называются сооружения, в которых одновременно происходят осветление сточной жидкости...
Топ:
Генеалогическое древо Султанов Османской империи: Османские правители, вначале, будучи еще бейлербеями Анатолии, женились на дочерях византийских императоров...
Основы обеспечения единства измерений: Обеспечение единства измерений - деятельность метрологических служб, направленная на достижение...
Интересное:
Финансовый рынок и его значение в управлении денежными потоками на современном этапе: любому предприятию для расширения производства и увеличения прибыли нужны...
Что нужно делать при лейкемии: Прежде всего, необходимо выяснить, не страдаете ли вы каким-либо душевным недугом...
Принципы управления денежными потоками: одним из методов контроля за состоянием денежной наличности является...
Дисциплины:
![]() |
![]() |
5.00
из
|
Заказать работу |
|
|
Традиционные методы технического обслуживания, применяемые на промышленных предприятиях, можно грубо разделить на две категории: эксплуатация оборудования до выхода из строя и планово-профилактическое техническое обслуживание.
Эксплуатация оборудования до выхода из строя. На промышленных предприятиях, использующих многочисленные недорогие машины с дублированием каждого ответственно го участка технологического процесса, машинное оборудование обычно эксплуатируется до тех пор, пока оно не выходит из строя.
В таком случае мониторизация механических колебаний является бесполезной, так как обычно знание того, когда выход из строя будет иметь место, не приносит ни экономических выгод, ни преимуществ в отношении техники безопасности, а причины выхода из строя большинства простых машин обычно являются очевидными.
В настоящее время на некоторых немногочисленных промышленных предприятиях большие производственные машины без дублирования все еще эксплуатируются до выхода их из строя. В этом случае очень большое значение имеет получение сведений о том, неисправность какого элемента возникает и когда, вероятнее всего, произойдет выход из строя. Эта информация может быть получена путем изучения тенденций изменений спектров механических колебаний, определяемых через регулярные интервалы времени. Сведения о том, неисправность какого элемента возникает, позволяют заказать необходимые запасные части перед ожидаемым выходом из строя и, следовательно, предотвратить создание больших запасов используемых запчастей. Кроме того, персонал по техническому обслуживанию в этом случае оказывается лучше подготовленным, что обеспечивает проведение более надежного ремонта в более короткий срок.
|
Планово-профилактическое техническое обслуживание. На тех промышленных предприятиях, где важные машины не дублируются полностью, или где непредусмотренные остановки производства могут привести к большим потерям, техническое обслуживание часто проводится с фиксированными интервала ми, например, через каждые 3000 часов работы или один раз в год. Поэтому такая система получила название профилактического технического обслуживания или более правильно - планово-профилактического технического обслуживания.
Интервалы между циклами технического обслуживания часто определяются статистически как период с момента начала работы нового или прошедшего полное техническое обслуживание машинного оборудования до того момента, когда изготовитель ожидает, что не более 2% машинного парка выйдет из строя. Обычно считается, что при проведении технического обслуживания с этими интервалами выход из строя будет происходить редко, так как 98% машин проработает без неполадок этот период.
Опыт показывает, что в подавляющем большинстве случаев планово-профилактическое техническое обслуживание оказывается экономически нецелесообразным. Примечательным фактором является то, что частота выхода из строя многих машин не снижается при регулярной замене изношенных деталей. Наоборот, надежность работы машин после технического обслуживания часто временно снижается вследствие влияния человека. Так как нельзя предсказать действительную картину возникновения неполадок для каждой отдельной машины, планово-профилактическое техническое обслуживание не является эффективным методом. Необходимо использовать индивидуальный подход, что является аксиомой системы технического обслуживания на основе состояния машинного оборудования.
Индивидуальный подход - техническое обслуживание на основе состояния машинного оборудования. При использовании данного метода каждая машина рассматривается отдельно.
|
Путем замены проведения технического обслуживания с фиксированными интервалами на проведение измерений с фиксированными интервалами создается возможность вплотную следить за изменениями рабочего состояния каждой отдельной машины. Как было ранее указано, механические колебания являются очень хорошим показателем рабочего состояния машин. измерения и анализа механических колебаний. | ![]() |
Следовательно, наиболее общей формой мониторизации состояния машинного оборудования является использование в качестве показателя результатов. Аксиома системы технического обслуживания на основе состояния машинного оборудования говорит о том, что проведение технического обслуживания разрешается только в том случае, когда оно оказывается необходимым. Это положение также находится в соответствии с инстинктивным мнением большинства специалистов о том, что неблагоразумно вмешиваться в исправно работающие машины.
Путем регулярных измерений механических колебаний может быть выявлено возникновение неисправностей и прослежено их развитие. Может быть осуществлена экстраполяция результатов измерений для того, чтобы определить момент, когда механические колебания достигнут неприемлемого уровня, т.е. когда необходимо провести техническое обслуживание машины. Этот процесс, получивший название мониторизация тенденций, дает возможность заблаговременно запланировать проведение ремонта.
Экономическая эффективность внедрения технического обслуживания на основе состояния машинного оборудования. Техническое обслуживание на основе состояния машинного оборудования, базирующееся на мониторизации механических колебаний, успешно используется на промышленных предприятиях с непрерывными технологическими процессами с начала 70-х годов данный метод был очень быстро внедрен на нефтехимических предприятиях с достижением большой экономии благо даря повышению степени использования производственного оборудования и соответствующего повышения производительности.
С тех пор мониторизация состояния машинного оборудования широко распространилась на промышленных предприятиях, использующих машины с вращающимися элементами. Имеется много примеров успешного использования такой системы. На одном химическом комбинате после внедрения технического обслуживания на основе состояния машинного оборудования число проводимых техобслуживаний /ремонтов снизилось с 274 до 14. Проведение практически всех этих мероприятий было запланировано, так как создавалась возможность для определения причины и даты выхода из строя. Также и на нефтеперерабатывающем заводе затраты на проведение технического обслуживания электродвигателей снизились на 75%. На бумажной фабрике экономия в течение первого года составила не менее 250000 долларов США, что в десять раз перекрыло расходы предприятия на закупку аппаратуры для мониторизации механических колебаний. На атомной электростанции в течение одного года была достигнута экономия в 3 миллиона долларов США за счет снижения затрат на проведение технического обслуживания и дополнительное увеличение доходов в размере 19 миллионов долларов США.
|
Такое значительное уменьшение объема работ по техническому обслуживанию не обязательно означает увольнение персонала по техническому обслуживанию. Он занимается подготовкой и проведением измерений и, возможно, располагает временем для более тщательного проведения работ по осмотру и проверке каждой машины, снятой с эксплуатации для проведения ремонта, благодаря чему делаются еще большие усилия по повышению долгосрочной надежности машинного оборудования. Проведение срочных работ, которые раньше могли быть выполнены только наспех, стали достоянием прошлого.
Специалисты по техническому обслуживанию сталкиваются с задачами оценки соотношения расходов и прибыли от внедрения мониторизации механических колебаний для проведения технического обслуживания на основе состояния машинного оборудования. На рисунке вверху приведены некоторые наиболее важные факторы, которые должны быть приняты при этом во внимание.
Успешное выполнение программ технического обслуживания не обязательно зависит от больших начальных капитальных затрат на сложное оборудование (например, на систему на базе ЭВМ). Во многих случаях успешный старт достигается при использовании относительно недорогих систем с несложными виброметрами для проведения замеров на представительной группе машин. По мере приобретения опыта и расширения системы естественным образом расширяется и применение более быстро действующих и более эффективных приборов. Однако, всегда рационально приобрести высококачественную аппаратуру с самого начала. Неточные и противоречивые результаты, особенно на стадии внедрения системы, могут значительно ограничить доверие к программам технического обслуживания на основе состояния машинного оборудования.
|
4. Аппаратура и системы, способствующие техническому обслуживанию на основе
состояния машинного оборудования
Системы мониторизации механических колебаний можно грубо разбить на три группы по степени сложности. Эта классификация отражает их быстродействие, насколько рано они могут вы являть неисправности и насколько точно может быть с их помощью определен момент выхода машинного оборудования из строя.
Основная система. Простая система мониторизации механических колебаний может быть реализована в виде комбинации несложного карманного виброметра для определения общих уровней механических колебаний, стробоскопа для определения рабочей скорости машин и относительного перемещения их деталей и наушников для прослушивания механических колебаний машинного оборудования. Для каждой машины может быть проведено сравнение общих уровней механических колебаний с установленными стандартами или заданными опорными значениями. С помощью стробоскопа осуществляется кажущееся замедление элементов машин, совершающих возвратно-поступательное или вращательное движение, что дает возможность человеческому глазу наблюдать за движениями этих элементов. Использование соединенных с виброметром наушников дает возможность оператору непосредственно прослушать работу машины.
Портативная система для отыскания неисправностей и диагностики. Раннее выявление неисправности совместно с диагностированием и определением момента выхода из строя становится возможным при использовании систем, осуществляющих частотный анализ механических колебаний. В идеальном случае соответствующая система должна быть портативной, способной выдерживать влияние неблагоприятных окружающих условий и иметь возможность хранения результатов измерений и анализа. Она также должна иметь диагностические возможности, в том числе возможность проведения частотного анализа на месте эксплуатации оборудования и представления спектрограмм для каждой контролируемой точки. Позднее может быть проведено автоматическое сравнение результатов анализа с хранящимися опорными спектрами для выявления увеличения амплитуд от дельных частотных составляющих. Встроенные дополнительные устройства позволяют проводить подробный анализ любой подозреваемой неисправности, что способствует решению конкретных проблем на более ранней стадии.
|
Системы на базе ЭВМ. При увеличении числа точек замера и сложности выявления не исправностей наиболее экономичным решением становится применение систем на базе ЭВМ. Типичная система включает в себя устройства для проведения анализа и выявления неисправностей на месте эксплуатации оборудования, собранные в портативный комплект с централизованной базой данных и диагностическими возможностями ЭВМ. Получение результатов мониторизации механических колебаний отдельных машин может быть организовано с помощью ЭВМ на основе заданных последовательностей операций. Применение таких последовательностей обеспечивает многократную мониторизацию каждой машины, а также такое ее проведение, которое наиболее подходит для отыскания неисправностей на ранних этапах их развития.
В расширенной системе на базе ЭВМ для регистрации сигналов механических колебаний отдельных машин при выполнении содержащих последовательности операций планов используется магнитофон (аналоговый или цифровой). Результаты измерений и анализа вводятся в ЭВМ для последующей обработки и хранения в центральной базе данных. При этом ЭВМ опять может служить в качестве как устройства диагностики, так и блока управления системой мониторизации. Большое преимущество описанного метода сбора данных заключается в том, что отображающие механические колебания сигналы все время хранятся на магнитной ленте и допускают дальнейшую обработку самыми разнообразными методами.
![]() | Системы непрерывной мониторизации.Если определенная машина является критической точкой производства (и следовательно, процесса получения прибыли) или если полный выход машины из строя может привести к дорого стоящим ремонтам, следует рассмотреть внедрение непрерывной мониторизации. Специальные мониторы механических колебаний, соединенные со стационарно установленными акселерометрами, обеспечивают мгновенную индикацию изменений состояния контролируемого машинного оборудования. Мониторы могут обеспечивать тревожную сигнализацию при обнаружении слишком высоких уровней механических колебаний и, при необходимости, останавливать машины. |
Простой подход: один, два, три. Для предприятий, на которых система мониторизации состояния машинного оборудования вводится постепенно, прочную основу для внедрения программы мониторизации могут обеспечить высококачественные портативные виброметры, с помощью которых определяются общие уровни механических колебаний.
Измерение уровней механических колебаний. С помощью портативного виброметра можно непосредственно измерять средние квадратические значения (СК3), макс. СКЗ или пиковые значения ускорения или скорости механических колебаний в задаваемых частотных диапазонах. Может быть осуществлено непосредственное сравнение показаний СКЗ скорости с установленными стандартами критериями жесткости механических колебаний с целью определения необходимости проведения технического обслуживания. Построение графиков зависимости общих уровней от времени, т.е. графиков тенденций, дает возможность оценки темпа изменения состояния машины. При использовании виброметра с карманной ЭВМ (например, Рsion Оrganizer, Dimеx 2) ‚ значительно упрощается сбор и хранение результатов измерений. При соединении виброметра с магнитофоном (аналоговым или цифровым) создается возможность хранения отображающих механические колебания сигналов для последующей обработки более сложной системой. Возможности широкополосных виброметров ограничены по сравнению с системами, осуществляющими частотный анализ, в частности в отношении возможностей выявления неисправностей на ранних стадиях, проведения диагностики и определения момента выхода из строя.
В конкретном случае мониторизации состояния подшипников качения, а также в тех случаях, когда механические колебания, вызванные другими источниками, не оказывают доминирующе го влияния, выявление дефектов подшипников на ранних стадиях может быть осуществлено на основе «пик-фактора». Виброметр устанавливается в режим одновременного измерения пиковых и средних квадратических значений уровней. Образование небольших дефектов на шариках/роликах и наружной и внутренней обоймах сопровождается созданием высокочастотных механических импульсов, которые замеряются с помощью пикового детектора виброметра. СКЗ уровни почти не изменяются на ранних стадиях, а пиковые уровни увеличиваются значительно. Отношение пикового и среднего квадратического значений носит название пик-фактора, а путем его мониторизации могут быть выявлены многие дефекты элементов подшипников качения на ранних стадиях их развития.
«Прослушивание» механических колебаний. Прослушивание оператором подшипника с помощью отвертки сегодня может считаться устаревшим методом выявления неисправностей, несмотря на то, что человеческое ухо является совершенным анализатором сигналов, хотя и с несколько ограниченным динамическим диапазоном. Наушники с усилителем, соединенные с вибродатчиком, позволяют оператору прослушать работу машины. Сравнение создаваемых при работе машины звуков в течение определенного периода времени аналогично сравнению частотных спектров. В руках опытного оператора этот метод может быть довольно эффективным.
«Просматривание» механических колебаний. Также возникает вопрос о том, какую информацию о состоянии машины можно получить в результате визуального наблюдения за ее работой. Если позволить развиваться таким неполадкам, как нарушение соосности или равновесия и ослабление соединений, их можно будет обнаружить визуально без применения всякого рода аппаратуры. Но их можно было бы выявить на более ранней стадии, если бы качество визуальной информации было более высоким. С помощью портативного стробоскопа можно обеспечить кажущееся замедление движения вращающегося элемента, что позволяет не только определить скорость вращения, но и оценить природу орбиты. Несоосные валы могут иметь несимметричные орбиты. Ослабление соединений может проявляться в виде относительного перемещения подшипника и корпуса. Несбалансированный ротор может совершать продольные колебательные движения.
Имеется много других неисправностей, которые могут быть выявлены с помощью описанных выше простых методов. При этом следует напомнить, что чем сложнее природа неисправности, тем более мощные методы необходимо применять для ее выявления.
|
|
Архитектура электронного правительства: Единая архитектура – это методологический подход при создании системы управления государства, который строится...
Эмиссия газов от очистных сооружений канализации: В последние годы внимание мирового сообщества сосредоточено на экологических проблемах...
Состав сооружений: решетки и песколовки: Решетки – это первое устройство в схеме очистных сооружений. Они представляют...
Историки об Елизавете Петровне: Елизавета попала между двумя встречными культурными течениями, воспитывалась среди новых европейских веяний и преданий...
© cyberpedia.su 2017-2024 - Не является автором материалов. Исключительное право сохранено за автором текста.
Если вы не хотите, чтобы данный материал был у нас на сайте, перейдите по ссылке: Нарушение авторских прав. Мы поможем в написании вашей работы!