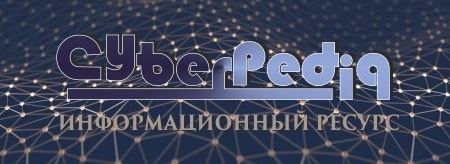
Поперечные профили набережных и береговой полосы: На городских территориях берегоукрепление проектируют с учетом технических и экономических требований, но особое значение придают эстетическим...
Археология об основании Рима: Новые раскопки проясняют и такой острый дискуссионный вопрос, как дата самого возникновения Рима...
Топ:
Характеристика АТП и сварочно-жестяницкого участка: Транспорт в настоящее время является одной из важнейших отраслей народного...
Оснащения врачебно-сестринской бригады.
Выпускная квалификационная работа: Основная часть ВКР, как правило, состоит из двух-трех глав, каждая из которых, в свою очередь...
Интересное:
Что нужно делать при лейкемии: Прежде всего, необходимо выяснить, не страдаете ли вы каким-либо душевным недугом...
Средства для ингаляционного наркоза: Наркоз наступает в результате вдыхания (ингаляции) средств, которое осуществляют или с помощью маски...
Берегоукрепление оползневых склонов: На прибрежных склонах основной причиной развития оползневых процессов является подмыв водами рек естественных склонов...
Дисциплины:
![]() |
![]() |
5.00
из
|
Заказать работу |
|
|
Цель работы: ознакомление с основами литейного производства и получение практических навыков изготовления фасонных отливок в различные литейные формы.
Теоретическая часть
1.1. Сущность процессов литья металлов и задача литейного производства
Литейное производство – отрасль машиностроения, занимающаяся изготовлением фасонных заготовок или деталей путём заливки расплавленного металла в специальную форму, полость которой имеет конфигурацию заготовки (детали). При охлаждении залитый металл затвердевает и в твёрдом состоянии сохраняет конфигурацию той полости, в которую он был залит. Конечную продукцию называют отливкой. В процессе кристаллизации расплавленного металла и последующего охлаждения формируются механические и эксплуатационные свойства отливок.
Литье –наиболее простой и дешёвый способ формообразования заготовок. При всём разнообразии приёмов литья, сложившихся за длительный период развития его технологии, принципиальная схема технологического процесса литья практически не изменилась за более чем 70 веков его развития и включает четыре основных этапа: плавку металла, изготовление форм, заливку жидкого металла в форму, извлечение затвердевшей отливки из формы.
Можно получить отливки разной массы (от нескольких граммов до сотен тонн), простой и сложной формы из чугуна, стали, сплавов меди и алюминия, цинка и магния и т.д. Особенно эффективно применение отливок для литья фасонных изделий сложной конфигурации, которые невозможно или экономически нецелесообразно изготавливать другими методами обработки металлов (давлением, сваркой, резанием), а также для литья изделий из малопластичных металлов и сплавов. Отливки широко применяют во всех отраслях машиностроения, металлургии, строительстве.
|
Основной задачей литейного производства является изготовление из литейных сплавов отливок, имеющих разнообразную конфигурацию с максимальным приближением их формы и размеров к форме и размерам детали (при литье невозможно получить отливку, форма и размеры которой соответствует форме и размерам детали).
Основным инструментом литейного производства является литейная форма.
Литейная форма - система элементов, образующих рабочую полость, при заливке которой расплавленным металлом и после охлаждения получают отливку.
По степени использования литейные формы делятся:
Разовые |
Постоянные |
Полупостоянные |
е
Разовые формы служат для изготовления только одной отливки и изготовляют их из кварцевого песка, зерна которого соединены каким – либо связующим веществом.
Полупостоянные формы – это формы, в которых получают несколько отливок (до 10-20), такие формы изготовляют из специального гипса (гипсо-динас), керамики.
Постоянные формы – формы, в которых получают от нескольких десятков до нескольких сотен тысяч отливок. Такие формы изготовляют обычно из чугуна или стали.
Литейную форму заливают расплавом через литниковую систему (рисунок 1).
Рисунок1- Литейная форма с элементами литниковой системы: 1- литниковая чаша; 2- стояк; 3- шлакоуловитель; 4- питатели; 5,6- чаша и стояк выпоров (прибылей); 7- фильтр из спец. стеклоткани.
Литниковой системой называют совокупность каналов и резервуаров, по которым расплав поступает из ковша в полость формы. Литниковая система должна обеспечить непрерывное поступление расплава в форму, питание отливки для компенсации усадки, предотвращать разрушение формы, попадание шлака и воздуха со струёй расплава. Основными элементами литниковой системы являются литниковая чаша, стояк, шлакоуловитель, питатели. Чаша уменьшает размывающее действие струи расплава, задерживает всплывающий шлак.
|
Для лучшего удержания шлака в литниковой системе, площадь стояка должна быть больше площадки шлакоуловителя и больше площади питания:
Различные по форме, размерам и точности отливки из различных сплавов невозможно наиболее экономично получить одним и тем же способом. Экономически целесообразно изготовлять отливку с определёнными качественными свойствами каким- либо одним или двумя способами. В настоящее время в литейном производстве используют более 15 способов литья, основными считаются:
1) Литьё в песчано - глинистые формы («в землю»);
2) Литьё в ЖСС (жидкие самоотвердевающие смеси);
3) Литьё в оболочковые формы;
4) Литьё в кокиль (металлические защищённые формы);
5) Литьё по выплавляемым моделям;
6) Литьё под давлением;
7) Центробежное литьё;
Для получения жидкого металла в литейных цехах и участках используют различные плавильные агрегаты (вагранки, печи сопротивления, индукционные, дуговые, газопламенные печи).
Для изготовления отливок применяют большое число различных приспособлений, называемых литейной оснасткой. В комплект технологической оснастки для изготовления форм из формовочных смесей входят модели, модельные плиты, стержневые ящики и др.
Конфигурация отливок может быть любой, она определяется возможностью изготовления технологической оснастки - формы, литейными свойствами сплавов, способом литья. Выбор способа литья в зависимости от конфигурации отливки основывается чаще всего на экономических соображениях, реже из условия высокой производительности и др.
1.2. Схема технологического процесса изготовления отливки.
Технологичной считают отливку, которую можно изготовить в данных производственных условиях, применяя наиболее экономически выгодную технологию, с минимальными затратами и потерями от брака, при высоком качестве изделия.
1.3. Основные свойства литейных сплавов и влияние их на качество отливок
Конструируя литую деталь, необходимо учитывать литейные свойства заливаемого сплава. К основным свойствам литейных сплавов относят следующие:
Жидкотекучесть - способность расплава заполнять литейную форму; определяет выбор оптимальной толщины стенки детали. Чем больше жидкотекучесть, тем тоньше может быть получаемая стенка. В то же время жидкотекучесть зависит от условий теплоотдачи в форме. В водоохлаждаемых стальных формах жидкотекучесть сплава падает очень быстро.
|
Кристаллизация сплава происходит в направлении, перпендикулярном поверхности теплоотдачи. Скорость кристаллизации меняется от максимальной у поверхности до минимальной в центре стенки отливки. Одновременно происходит рост кристаллов- зёрен. Для создания равномерной и мелкозернистой структуры желательно уменьшать толщину отливок.
Усадка – свойство металлов и сплавов уменьшаться в объёме при охлаждении. Размеры модели делают больше, чем соответствующие размеры отливки, на величину линейной усадки сплава, которая для углеродистой стали составляет 1,8-2% для стали, а для чугуна 0,8- 1,2%. Если отливки подвергают механической обработке, то в соответствующих размерах модели учитывают размер припусков - слоя металла, удаляемого при механической обработке. Формы и стержни не должны препятствовать усадке металла. Линейная усадка вызывает образование трещин и коробление вследствие торможения усадки в отдельных местах отливки. Объёмная усадка приводит к образованию усадочной пористости в утолщённых местах отливок. При наличии препятствий для усадки возникают напряжения, возможно коробление отливки и образование трещин – для этого необходимы литейные уклоны, размер которых зависит от высоты изделия и составляет 1-8 мм, или 0,5-3о.
Перечисленные свойства сплавов определяют равностенность, радиусы закруглений, плавные переходы, уклоны, отверстия и армирование.
![]() | Zn | Литье в кокиль | Гладкая поверхность, но шершавее, чем следующий экземпляр.Время кристализаии до 1 мин. |
![]() | Pb | Литье в кокиль с летниковой системой | Очень гладкая поверхность. Время кристализаии несколько секунд |
![]() | Zn | Литьё в песчано – глинистой форме | Шершавая поверхность.Время кристализаии несколько минут. |
Практическая работа №6
Цель работы: ознакомление с основными положениями технологии выполнения сварочных работ и овладение основами техники получения сварных соединений.
Основные положения теории и техники сварки
|
Сваркой называется технологический процесс получения неразъёмного соединения. Для получения сварного соединения соединяемые поверхности сближают на расстояния, в пределах которых действуют силы межатомного сцепления. По методу объединения заготовок различают сварку плавлением и сварку давлением.
Расплавленный металл получают путём плавления кромок заготовок и электродного (или присадочного) металла электрической дугой (рис.1). После заполнения зазора между заготовками металл затвердевает, образуя прочный сварочный шов.
Ручную электродуговую сварку применяют для соединения металлов толщиной от 1 до 60 мм при выполнении коротких швов в различных пространственных положениях (рис.2) и в труднодоступных местах.
1.1. Сварочная дуга и источники сварочного тока
Сварочная дуга - мощный стабильный разряд электричества в ионизированной атмосфере газов и паров металла. Ионизация дугового промежутка происходит во время зажигания дуги и непрерывно поддерживается в процессе её горения. Процесс зажигания дуги включает три этапа: короткое замыкание электрода на заготовку, отвод на расстояние 3-6 мм и возникновение устойчивого дугового разряда. Короткое замыкание (рис.3,а) выполняется для разогрева торца электрода 1 и заготовки 2 в зоне контакта с электродом. После отвода электрода (рис.3,б) с его разогретого торца (катода) под действием электрического поля начинается эмиссия электронов 3. Столкновение быстродвижущихся по направлению к аноду электронов с молекулами газов и паров металла приводит к их ионизации 4. В результате дуговой промежуток становится электропроводным и через него начинается разряд электричества. Процесс зажигания дуги заканчивается возникновением устойчивого дугового разряда 6 (рис.3,в).
Рис.3. Схема процесса зажигания дуги
Для питания сварочной дуги применяют источники переменного (сварочные трансформаторы) и постоянного тока (сварочные генераторы и выпрямители). Сварочные трансформаторы применяют чаще, так как они проще в эксплуатации и долговечнее.
При использовании постоянного тока различают сварку на прямой и обратной полярностях. В первом случае электрод подключается к отрицательному полюсу и служит катодом, во втором – к положительному и служит анодом.
Рассмотрим устройство сварочного трансформатора с повышенным магнитным рассеянием (тип ТДМ). В трансформаторах данного типа (рис.4) на стальном сердечнике 3 установлены две пары обмоток: неподвижная первичная 1 и подвижная вторичная 2. Оба первичные обмотки, также как и вторичные электрически связаны между собой параллельно. Первичная обмотка подключается к сети с напряжением 220/380 B, а вторичная к электрододержателю 5 и сварочному столу 6. Вращением винта 4 вторичная обмотка может быть приближена к неподвижной первичной обмотке или удалена от неё. Величину сварочного тока ICB плавно регулируют, изменяя расстояние между первичной и вторичной обмотками.
|
|
|
Археология об основании Рима: Новые раскопки проясняют и такой острый дискуссионный вопрос, как дата самого возникновения Рима...
Индивидуальные и групповые автопоилки: для животных. Схемы и конструкции...
Типы оградительных сооружений в морском порту: По расположению оградительных сооружений в плане различают волноломы, обе оконечности...
Двойное оплодотворение у цветковых растений: Оплодотворение - это процесс слияния мужской и женской половых клеток с образованием зиготы...
© cyberpedia.su 2017-2024 - Не является автором материалов. Исключительное право сохранено за автором текста.
Если вы не хотите, чтобы данный материал был у нас на сайте, перейдите по ссылке: Нарушение авторских прав. Мы поможем в написании вашей работы!