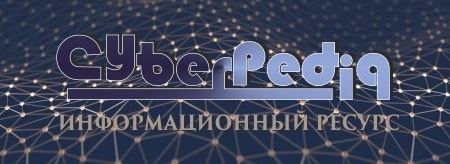
Эмиссия газов от очистных сооружений канализации: В последние годы внимание мирового сообщества сосредоточено на экологических проблемах...
Организация стока поверхностных вод: Наибольшее количество влаги на земном шаре испаряется с поверхности морей и океанов (88‰)...
Топ:
Определение места расположения распределительного центра: Фирма реализует продукцию на рынках сбыта и имеет постоянных поставщиков в разных регионах. Увеличение объема продаж...
Особенности труда и отдыха в условиях низких температур: К работам при низких температурах на открытом воздухе и в не отапливаемых помещениях допускаются лица не моложе 18 лет, прошедшие...
Генеалогическое древо Султанов Османской империи: Османские правители, вначале, будучи еще бейлербеями Анатолии, женились на дочерях византийских императоров...
Интересное:
Средства для ингаляционного наркоза: Наркоз наступает в результате вдыхания (ингаляции) средств, которое осуществляют или с помощью маски...
Берегоукрепление оползневых склонов: На прибрежных склонах основной причиной развития оползневых процессов является подмыв водами рек естественных склонов...
Финансовый рынок и его значение в управлении денежными потоками на современном этапе: любому предприятию для расширения производства и увеличения прибыли нужны...
Дисциплины:
![]() |
![]() |
5.00
из
|
Заказать работу |
Оборудование для контактной сварки состоит из двух взаимосвязанных частей:
- электрической, обеспечивающей нагрев зоны соединения проходящим по свариваемым деталям током;
- механической, выполняющей сжатие свариваемых деталей, подвод к ним сварочного тока, перемещение деталей во время сварки и необходимую пластическую деформацию металла в зоне соединения.
Электрическая часть контактной машины состоит из ряда функциональных блоков:
1. внешний контур - совокупность токоведущих элементов машины и контактов между ними, передающих сварочный ток от источника питания к свариваемым деталям. Часть элементов внешнего контура участвует в сжатии и перемещении свариваемых деталей, т.е. участвует в передаче механического усилия.
2. источник питания, преобразующий энергию электрической сети в сварочный ток необходимой величины, формы и длительности.
3. контактор - управляемое устройство, коммутирующее ток в первичной цепи контактной машины, участвующее в формировании величины, формы и длительности сварочного тока, а также являющееся силовым исполнительным элементом при организации системы автоматического управления процессом.
4. аппаратура управления и контроля, обеспечивающая заданную последовательность всех операций цикла сварки, установку и стабилизацию электрических и механических параметров процесса, их контроль, управление и регистрацию.
Механическая часть контактной машины включает в себя комплекс конструктивных элементов обеспечивающих жесткость, маневренность, эксплуатационную надежность контактной машины, и механизмы, выполняющие закрепление, сжатие и перемещение свариваемых деталей. Некоторые элементы проводят сварочный ток.
ГОСТ 297-80 устанавливает следующую классификацию контактных машин:
- по виду получаемого соединения: точечные, шовные, рельефные, стыковые;
- по конструктивному исполнению: стационарные прессового и радиального типов, подвесные со встроенным и отдельным трансформатором;
- по типу источника питания: переменного тока промышленной частоты, низкочастотные, постоянного тока, конденсаторные, переменного тока повышенной частоты;
- по типу сжатия: с постоянной и переменной силой.
ДЕФЕКТЫ СВАРНЫХ СОЕДИНЕНИЙ
Сварка плавлением
При сварке плавлением образуются дефекты различного вида, которые можно условно классифицировать на:
- дефекты подготовки и сборки (неправильный угол скоса кромок шва с разделкой, неправильный размер притупления, непостоянство зазора между кромками, несовпадение стыкуемых поверхностей, слишком большой зазор между кромками, расслоения и загрязнение кромок)
- Дефекты формы шва (неравномерная ширина и высота сварного шва, бугры, седловины и неравномерная высота катетов)
Неравномерная ширина швов образуется при неправильном движении электрода при РДС, а также в результате отклонения от заданного зазора кромок при сборке. При автоматической сварке дефект образуется при нарушении скорости подачи проволоки, скорости сварки и т.д.
Местные бугры и седловины получаются из-за недостаточной квалификации сварщика и в первую очередь зрительно-двигательной координацией сварщика, неправильными приемами заварки прихваток, плохим качеством электродов. При автоматической сварке такие дефекты возникают, как правило, при нарушении регулирующего скорость сварки устройства.
Дефекты формы шва снижают прочность соединения и косвенно указывают на возможность образования внутренних дефектов.
- Наружные (наплывы, подрезы, неразделанные кратеры, прожоги) и внутренние (поры, шлаковые включения, непровары, несплавления и трещины) дефекты.
Наплывы образуются в результате стекания расплавленного металла электрода на нерасплавленный основной металл или ранее выполненный валик без сплавления с ним. Возникают наплывы из-за: чрезмерной силы тока при большой длине дуги и скорости сварки, неудобного пространственного положения, неправильного ведения электрода, недостаточного опыта сварки.
Подрезы представляют собой углубления в основном металле, идущие по краям шва. Причины образования дефекта: большие значения силы тока и напряжения дуги, неудобное расположение шва и небрежность сварщика. Подрезы уменьшают рабочую толщину металла, вызывают местную концентрацию напряжений от рабочих нагрузок и могут быть причиной разрушения швов в процессе эксплуатации.
Кратер - углубление, образующееся в конце шва при внезапном прекращении сварки. Незаделанные кратеры снижают прочность сварного соединения, так как концентрируют напряжения.
Прожоги - дефекты в виде сквозного отверстия в сварном шве, образующиеся при вытекании сварочной ванны. Причины прожогов: слишком высокая погонная энергия, неравномерная скорость сварки, большой зазор.
Поджоги возникают в результате возбуждения дуги чирканьем на краю кромки. Этот дефект служит концентратором напряжений, его обязательно удаляют механической обработкой.
Поры - полости округлой формы, заполненные газом, образуются из-за: загрязненности кромок, неподготовленных должным образом сварочных материалов, недостаточной защиты шва, увеличенных скорости сварки и длинны дуги.
Равномерная пористость обычно возникает при постоянно действующих факторах: загрязненность основного металла или непостоянной толщине электродного покрытия.
Скопления пор образуется в условиях местного загрязнения, отклонения от установленного режима сварки, нарушении сплошности покрытия электрода, обрыве дуги или случайных изменениях длинны дуги.
Цепочки пор образуются когда газообразные продукты проникают в металл по оси шва на всем его протяжении(сварка по ржавчине, подсос воздуха через зазор между кромками).
Одиночные поры возникают за счет действия случайных факторов(колебание напряжения сети при источниках питания без стабилизаторов).
Шлаковые включения - это полости заполненные неметаллическими веществами(шлаками, оксидами) которые не выведены из металла сварочной ванны до кристаллизации сварного шва.
Макроскопические возникают из-за плохой очистки свариваемых кромок от окалины и других загрязнений.
Микроскопические образуются в процессе плавления некоторых химических соединений остающихся в шве при кристаллизации.
Непровары - это дефекты в виде местного несплавления в сварном соединении вследствие неполного расплавления кромок.
Непровары в виде несплавления основного металла с наплавленным представляют собой тонкую прослойку оксидов, а в некоторых случаях - грубую шлаковую прослойку между основным и наплавленным металлом. Причинами образования таких непро- варов являются:
- плохая зачистка кромок свариваемых деталей от окалины, ржавчины, краски, шлака, масла и других загрязнений;
- блуждание или отклонение дуги под влиянием магнитных полей, особенно при сварке на постоянном токе;
- электроды из легкоплавкого материала (при выполнении шва такими электродами жидкий металл натекает на неоплавленные свариваемые кромки);
- чрезмерная скорость сварки, при которой свариваемые кромки не успевают расплавиться;
- значительное смещение электрода в сторону одной из свариваемых кромок, при этом расплавленный металл натекает на вторую нерасплавленную кромку, прикрывая непровар;
- неудовлетворительное качество основного металла, сварочной проволоки, электродов, флюсов и т.д.;
- плохая работа сварочного оборудования - колебания силы сварочного тока и напряжения дуги в процессе сварки;
- низкая квалификация сварщика.
Причинами непровара в корне шва кроме указанных выше могут быть: недостаточный угол скоса кромок; большая величина их притупления; маленький зазор между кромками свариваемых деталей; большое сечение электрода или присадочной проволоки, укладываемой в разделку шва, что значительно затрудняет расплавление основного металла. Непровары между отдельными слоями возникают по следующим причинам: из-за не полностью удаленного шлака, образовавшегося при наложении предыдущего валика, что возможно из-за трудности его удаления или небрежности сварщика; недостаточной тепловой мощности (малый ток, излишне длинная или короткая дуга).
Трещины - частичное местное разрушение сварного соединения в виде разрыва Образованию трещин способствуют следующие факторы:
- сварка легированных сталей в жестко закрепленных конструкциях;
- высокая скорость охлаждения при сварке углеродистых сталей, склонных к закалке на воздухе;
- применение высокоуглеродистой электродной проволоки при автоматической сварке конструкционной легированной стали;
- использование повышенных плотностей сварочного тока при наложении первого слоя многослойного шва толстостенных сосудов и изделий;
- недостаточный зазор между кромками деталей при электрошлаковой сварке;
- слишком глубокие и узкие швы при автоматической сварке под флюсом;
- выполнение сварочных работ при низкой температуре;
- чрезмерное нагромождение швов для усиления конструкции (применение накладок и т.п.), в результате чего возрастают сварочные напряжения, способствующие образованию трещин в сварном соединении;
- наличие в сварных соединениях других дефектов, являющихся концентраторами напряжений, под действием которых в области дефектов начинают развиваться трещины.
Существенным фактором, влияющим на образование горячих трещин (ГТ), является засоренность основного и присадочного металлов вредными примесями серы и фосфора. Холодные трещины (XT) образуются при наличии составляющих мартснситного и бейнитного типов, концентрации диффузного водорода в зоне зарождения трещин и растягивающих напряжений I рода. Трещины относятся к наиболее опасным дефектам и по всем действующим нормативно-техническим документам (НТД) недопустимы.
Металлические включения. В практике наиболее распространены вольфрамовые включения при сварке алюминиевых сплавов (рис. 16.11). Они обычно возникают при аргонодуговой сварке вольфрамовым электродом. При этом могут наблюдаться мгновенная нестабильность дуги и появление одновременно с вольфрамовыми включениями оксидных включений. Вольфрамовые включения могут располагаться внутри шва и на поверхности соединений в виде брызг. При попадании вольфрама в жидкую ванну он обычно погружается на дно ванны. Вольфрам в алюминии нерастворим и обладает большой плотностью. На рентгеновском снимке он дает характерные ясные изображения произвольной формы (см. рис. 16.11). Вольфрамовые включения, как правило, образуются в местах обрыва дуги, при этом вольфрам скапливается в вершине кратеров, где часто образуются трещины.
Вольфрамовые включения подразделяют на две основные группы: изолированные и групповые. Размер диаметра изолированных включений 0.4...3.2 мм. Групповые включения описываются (по рентгенограмме) размером группы, количеством и размером отдельных (изолированных) включений в группе, при этом размер группы характеризуется размером минимальной окружности, в которую вписывается группа включений. Если изображение нескольких включений сливается, то их принимают за одно включение.
Контактная сварка
Основными наружными дефектами швов сварных соединений, выполненных точечной сваркой, являются:
- наружные трещины (рис. 16.12);
- прожог;
- наружный выплеск;
- вырыв точек;
- выход на поверхность литой структуры;
- разрыв металла у кромки соединения;
- поверхностное нарушение сплошности металла во вмятине от электрода;
- чрезмерная вмятина и неправильная форма вмятины от электродов;
- темная поверхность сварных точек.
Образованию этих дефектов способствуют:
- большая величина или длительность импульса сварочного тока;
- малое усилие сжатия электродов или отсутствие его;
- плохая подготовка поверхностей свариваемых деталей;
- загрязнение электродов;
- малое ковочное усилие;
- позднее приложение последнего;
- недостаточное охлаждение электродов;
- неисправное сварочное оборудование;
- неправильная форма контактных поверхностен электродов;
- большие натяги деталей при сварке и в процессе правки;
- неверное установление электродов и т.д.;
- близость сварной точки к краю соединения;
- малая величина нахлестки и др.;
- небольшой размер рабочей поверхности электродов;
- перекос деталей или электродов;
- неправильная заточка или неравномерный износ рабочей поверхности электродов;
~ перекос свариваемых электродов конструкции.
Основные внутренние дефекты точечной сварки:
- непровар (рис. 16.13) - отсутствие взаимной литой зоны соединяемых элементов сварной конструкции;
- внутренние трещины, поры и раковины;
- внутренний выплеск металла (рис. 16.14);
- несимметричное расположение ядра точки;
- чрезмерное проплавление - проплавление >80 % толщины свариваемого листа.
Причины образования внутренних дефектов:
- недостаточная величина или импульс сварочного тока;
- большое усилие сжатия электродов;
- шунтирование сварочного тока;
- увеличение рабочей поверхности электродов;
- нестабильность контактного сопротивления, вызванная плохой подготовкой поверхностей деталей;
- большой плакирующий слой;
- раннее приложение ковочного усилия;
- малое усилие сжатия электродов;
- малое ковочное усилие;
- запаздывание включения ковочного усилия;
- большой сварочный ток;
- продолжительное время сварки;
- большое контактное сопротивление деталей;
- плохая зачистка электродов;
- большая величина сварочного тока или его импульса;
- плохая подготовка поверхностей деталей;
- загрязнение электродов;
- малое усилие сжатия электродов;
- перекос свариваемых элементов конструкции;
- смещение сварной точки к краю нахлестки;
- малая нахлестка;
- неправильный подбор размеров контактных поверхностей электродов;
- сварка различных по химическому составу материалов;
- сварка деталей разной толшины и лр.
Основным дефектом контактной стыковой сварки сопротивлением или оплавлением является «слипание», при котором между свариваемыми элементами имеется механический контакт, но отсутствует взаимное прорастание зерен между соединяемыми границами. Подобный дефект часто образуется при сварке трением, давлением, диффузионной и сварке взрывом. Уверенно обнаружить слипание известными физическими методами контроля достаточно сложно. Для предупреждения его образования применяют так называемые параметрические методы контроля, при которых ряд доминирующих параметров (ток, напряжение, давление, длительность, скорость осадки и т.д.) поддерживается в определенных заранее установленных границах.
Общие условия выбора системы дренажа: Система дренажа выбирается в зависимости от характера защищаемого...
Историки об Елизавете Петровне: Елизавета попала между двумя встречными культурными течениями, воспитывалась среди новых европейских веяний и преданий...
Индивидуальные и групповые автопоилки: для животных. Схемы и конструкции...
Таксономические единицы (категории) растений: Каждая система классификации состоит из определённых соподчиненных друг другу...
© cyberpedia.su 2017-2024 - Не является автором материалов. Исключительное право сохранено за автором текста.
Если вы не хотите, чтобы данный материал был у нас на сайте, перейдите по ссылке: Нарушение авторских прав. Мы поможем в написании вашей работы!