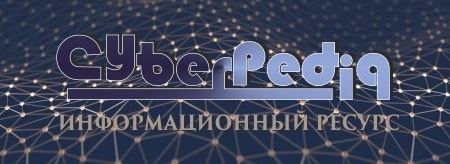
Опора деревянной одностоечной и способы укрепление угловых опор: Опоры ВЛ - конструкции, предназначенные для поддерживания проводов на необходимой высоте над землей, водой...
Механическое удерживание земляных масс: Механическое удерживание земляных масс на склоне обеспечивают контрфорсными сооружениями различных конструкций...
Топ:
Основы обеспечения единства измерений: Обеспечение единства измерений - деятельность метрологических служб, направленная на достижение...
Организация стока поверхностных вод: Наибольшее количество влаги на земном шаре испаряется с поверхности морей и океанов...
Характеристика АТП и сварочно-жестяницкого участка: Транспорт в настоящее время является одной из важнейших отраслей народного хозяйства...
Интересное:
Наиболее распространенные виды рака: Раковая опухоль — это самостоятельное новообразование, которое может возникнуть и от повышенного давления...
Что нужно делать при лейкемии: Прежде всего, необходимо выяснить, не страдаете ли вы каким-либо душевным недугом...
Уполаживание и террасирование склонов: Если глубина оврага более 5 м необходимо устройство берм. Варианты использования оврагов для градостроительных целей...
Дисциплины:
![]() |
![]() |
5.00
из
|
Заказать работу |
|
|
Поверхностную закалку токами высокой частоты (ТВЧ), разработанную академиком В. П. Вологдиным, широко применяют в судоремонте. Метод основан на использовании явлений электромагнитной индукции. В детали, внесенной в высокочастотное магнитное поле, иНДуцируются вихревые токи, которые вызывают нагревание ее поверхностного слоя. Глубина проникновения тепла (в сантиметрах) соответствует глубине проникновения тока. Закалку ТВЧ осуществляют следующим образом. Специальный индуктор создает переменное магнитное поле при пропускании через него переменного тока высокой частоты (2500-5000 Гц), вырабатываемого машинным генератором при одновитковом разъемном индукторе или ламповым генератором при непрерывно последовательном способе. Благодаря тепловому действию тока происходит быстрый нагрев поверхностных слоев детали (обычно за 273 с). По достижении температуры закалки ток выключается, и через отверстия на внутренней поверхности индуктора подается под давлением вода. Происходит закалка поверхности на заданную глубину.
При одновременной закалке одновитковым разъемным индуктором вся поверхность.детали охватывается индуктором и нагревается одновременно. Этот способ применяют для коротких деталей, например шеек коленчатых и распределительных валов. Детали
же, имеющие большую длину, аакаливают непрерывно-последовательным способом. При этом способе индуктор перемещается относительно шейки вала со скоростью 0,3-3 м/с. Глубина закаленного слоя коленчатых валов обычно не менее 4-7 мм. Нагретую поверхность охла:ждают водой, которая подается через гребенку, расположенную рядом с ин,дуктором. Внутренние поверхности втулок цилиндров и других деталей закаливают непрерывно последовательным способом. После закалки производятся отпуск (в печи) при температуре 250-3000 С и механическое упрочнение посредством обкатки роликами,
|
шариками или обдувки дробью. Высокочастотную закалку хорошо принимают детали из чугуна. Закалке с нагревом ТВЧ обычно подвергают чугунные поршни, втулки цилиндров, шестерни, эксцентрики, параллели, золотники и др. Поверхностную закалку газовым пламенем (ацетилено-кислородным пламенем) осуществляют специальными горелками дозакалочной температуры на глубину 1-6 мм и сразу же охлаждают деталь водой или воздухом. Глубина закалки стальных и чугунных деталей при скорости передвижения пламени от 80 до 150 мм/мин составляет 1-5 мм. Давление кислорода, подаваемого в горелку, равно 0,2-0,4 МПа, ацетилена - 0,002-0,08 МПа. Этот способ используется для закалки CTaJIbHblX и чугунных деталей, подвергающихся интенсивному изиашиванию (шейки коленчатых, гребных и промежуточных валов, кулачки распределительных валов, толкатели клапанов, шестерни и другие детали). Изотермическая закалка является перспективным видом термической обработки. Различают светлую ступенчатую закалку и закалку в расплавленных щелочах. При светлой ступенчатой закалке деталь помещают в охлаждающую среду, имеющую температуру 200-3000 С, и выдерживают в ней до тех пор, пока деталь не приобретет эту температуру; далее охлаждение ведется в масле или на воздухе. Светлую ступенчатую закалку применяют при изготовлении деталей из легированных и инструментальных сталей марок У7, У12, ШХI5, 8Б, 60С2А, 65Г и др. Применение изотермической закалки дает возможность увеличить износостойкость деталей в 2-5 раз и более, повысить предел прочности разрыву на 50-80%, снизить трудоемкость обработки за счет исключения операций отпуска. Обработка холодом заключается в медленном охлаждении стальных деталей до температуры минус 800 С и ниже. В качестве холодильных агенов для создания низких температур используют жидкий азот, жидкий воздух или углекислоту в твердом состоянии. В результате глубокого охлаждения происходят дополнительные превращения остаточного аустенита в мартенсит, что повышает твердость и износостойкость деталей. Обработка холодом для большинства стальных деталей должна производиться непосредственно после закалки во избежание стабилизации аустенита. Обработку холодом в судоремонте применяют для повышения износостойкости поршневых пальцев, плунжерных пар, кулачных шайб и других деталей; для стабилизации размеров закаленных деталей; для повышения стойкости режущего инструмента; для уменьшения размеров деталей под посадку и т. д.
|
|
|
Биохимия спиртового брожения: Основу технологии получения пива составляет спиртовое брожение, - при котором сахар превращается...
Таксономические единицы (категории) растений: Каждая система классификации состоит из определённых соподчиненных друг другу...
Автоматическое растормаживание колес: Тормозные устройства колес предназначены для уменьшения длины пробега и улучшения маневрирования ВС при...
Типы сооружений для обработки осадков: Септиками называются сооружения, в которых одновременно происходят осветление сточной жидкости...
© cyberpedia.su 2017-2024 - Не является автором материалов. Исключительное право сохранено за автором текста.
Если вы не хотите, чтобы данный материал был у нас на сайте, перейдите по ссылке: Нарушение авторских прав. Мы поможем в написании вашей работы!