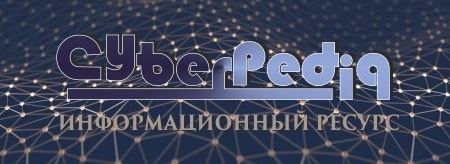
Архитектура электронного правительства: Единая архитектура – это методологический подход при создании системы управления государства, который строится...
Автоматическое растормаживание колес: Тормозные устройства колес предназначены для уменьшения длины пробега и улучшения маневрирования ВС при...
Топ:
Основы обеспечения единства измерений: Обеспечение единства измерений - деятельность метрологических служб, направленная на достижение...
Характеристика АТП и сварочно-жестяницкого участка: Транспорт в настоящее время является одной из важнейших отраслей народного хозяйства...
Эволюция кровеносной системы позвоночных животных: Биологическая эволюция – необратимый процесс исторического развития живой природы...
Интересное:
Уполаживание и террасирование склонов: Если глубина оврага более 5 м необходимо устройство берм. Варианты использования оврагов для градостроительных целей...
Лечение прогрессирующих форм рака: Одним из наиболее важных достижений экспериментальной химиотерапии опухолей, начатой в 60-х и реализованной в 70-х годах, является...
Влияние предпринимательской среды на эффективное функционирование предприятия: Предпринимательская среда – это совокупность внешних и внутренних факторов, оказывающих влияние на функционирование фирмы...
Дисциплины:
![]() |
![]() |
5.00
из
|
Заказать работу |
|
|
Коррозионное разрушение. Коррозией металла называется самопроизвольное его разрушение вследствие физико-химического взаимодействия с окружающей средой. Различают химическую и электрохимическую коррозии, а также биокоррозию.
При химической коррозии окисление металла и восстановление окислительного компонента происходят одновременно и с одинаковыми скоростями.
Электрохимическая коррозия возникает в электролитической токо-проводящей среде. Окисление металла и восстановление окислительного компонента происходят с разными скоростями, которые зависят от электродного потенциала металла.
При химической коррозии воздействующей внешней средой являются воздух, газы и жидкие вещества, не проводящие электрического тока, например, окисление металла на сухом воздухе - это химическая коррозия. В паровых котлах на поверхностях нагрева, паровых коллекторах, арматуре возможна химическая коррозия в результате взаимодействия металлической поверхности с перегретым паром или газом высокой температуры.
Поверхности судовых конструкций, трубопроводов и механизмов, омываемые морской водой, могут подвергаться действию биокоррозии, возникающей под влиянием продуктов жизнедеятельности макро- и микроорганизмов, находящихся на этих поверхностях.
Защита корпуса от коррозии и обрастанийСпособы очистки корпусов судов. Качество защитных покрытий корпуса и их надежность зависят от качества подготовки защищаемой поверхности перед нанесением покрытий. Для очистки поверхности от окалины, ржавчины и старой краски применяют термический, химический, электролитический и механический способы.
Разновидностью химической очистки является использование преобразователей ржавчины. Преобразователь ржавчины очищает поверхность и одновременно создает химические соединения типа защитных грунтов, пригодные к последующему нанесению красок. При оптимальных вариантах срок службы лакокрасочных покрытий возрастает до 7...9 лет. Электролитический способ очистки пригоден для травления поверхности отдельных деталей, однако он не рекомендуется для подводной очистки корпусов судов.
|
Механические способы являются наиболее распространенными для очистки. Ручная очистка скребками, щетками имеет низкую производительность.
Применение ручных очистных машинок повышает производительность. В настоящее время широко внедрены различные очистные механизмы.
Оценка качества очистки поверхности корпуса. Оценка качества очистки производится визуально в сравнении с эталонами качества очистки при ремонте судов. Эталоны позволяют судить о степени очистки в зависимости от исходного состояния корпуса — I и II степени. Для механических и струйноэрозионных способов очистки установлены I, II и III степени очистки. При III степени поверхность корпуса имеет ровный металлический блеск. Для количественной оценки степени очистки применяется специальный фотометрический прибор.
Лакокрасочные защитные покрытия. Надежная защита поверхности металла от коррозионной среды требует, чтобы покрытие было сплошным и влагостойким, лишенным пористости и т. д. Этим требованиям удовлетворяет состав лакокрасочных покрытий и соблюдение требований технологических процессов нанесения покрытий,
В состав красок входят пленкообразующие вещества, пигменты и наполнители, пластификаторы, ускорители высыхания и растворители.
Технологические процессы окраски* Типовые технологические процессы (ТТП) окраски судов определены стандартом ОСТ 5.9566—83, а технологические схемы окраски — ОСТ 5.9258—77.
ТТП и схемы окраски неодинаковы для отдельных частей и элементов корпуса судна и для судов различного назначения и районов плавания. В общем случае последовательность окраски такая: очистка и подготовка поверхности, грунтовка поверхности, шпаклевка дефектов и окрашивание, оценка качества окраски.
|
Взаимный подбор грунтов, шпаклевок и красок производится по рекомендациям технических условий или справочников, так как ч эти компоненты могут вступать в химические реакции друг с другом, снижая защитные свойства покрытия.
Окраска производится только по сухой поверхности. Необходимые защитные свойства покрытия обеспечиваются нанесением нескольких слоев краски. Назначение грунта — обеспечить высокую коррозионную стойкость и улучшить адгезию последующих слоев краски.
Для коррозионной защиты используются грунты масляные: фосфатирующие, протекторные. На фосфатирующие грунты шпаклевка не наносится.
Шпаклевка применяется для устранения дефектов поверхности.
Защита цистерн питьевой и технической воды, цистерн топлива и масел и грузовых трюмов. Защита цистерн питьевой воды осуществляется различными способами:
обклейкой листовым полиизобутиленом;
цементированием портландцементом.
Оборудование и инструменты для окрасочных работ. Для малярных судовых работ используются маховые и валиковые кисти, шпатели для нанесения шпаклевок и мастик, гребенки для разделки окрашенных поверхностей, трафареты для нанесения знаков и рисунков, фильтровальные сетки и др.
Механизированная окраска производится валиковыми приставками или краскораспылителями форсуночного типа с наружным или внутренним смешением красок. Вязкость красок снижается подогревом красок и воздуха.
Последнее время используются установки и распылители для безвоздушного нанесения красок, поступающих в форсунку под давлением. В результате резкого перепада давлений происходит дробление краски на мелкие частицы.
Механизация очистных и окрасочных работ. Снижение трудоемкости очистных и окрасочных работ по корпусу судна обеспечивается высокопроизводительными способами и специальными установками.
Все механизированные способы очистки имеют свои преимущества и недостатки, поэтому в зависимости от условий работы и исходного состояния поверхности корпуса они должны использоваться комплексно.
|
Протекторная защита корпусных конструкций. Электрохимическая защита судов применяется только в комплексе с лакокрасочными покрытиями. Сущность электрохимической защиты состоит в сдвиге электродного потенциала металла корпуса в отрицательную сторону.
Катодная защита* При подаче постоянного тока защищаемую конструкцию присоединяют к клемме с—», а клемму «+» — к специальному аноду, обладающему стойкостью к действию анодного тока. На защищаемой поверхности, погруженной в электролит, образуются участки, в которых электрический ток течет от анода через электролит к катодным участкам, и анодные участки разрушаются.
|
|
Архитектура электронного правительства: Единая архитектура – это методологический подход при создании системы управления государства, который строится...
Биохимия спиртового брожения: Основу технологии получения пива составляет спиртовое брожение, - при котором сахар превращается...
Состав сооружений: решетки и песколовки: Решетки – это первое устройство в схеме очистных сооружений. Они представляют...
История развития пистолетов-пулеметов: Предпосылкой для возникновения пистолетов-пулеметов послужила давняя тенденция тяготения винтовок...
© cyberpedia.su 2017-2024 - Не является автором материалов. Исключительное право сохранено за автором текста.
Если вы не хотите, чтобы данный материал был у нас на сайте, перейдите по ссылке: Нарушение авторских прав. Мы поможем в написании вашей работы!