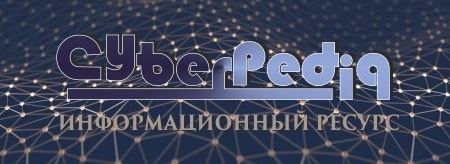
Организация стока поверхностных вод: Наибольшее количество влаги на земном шаре испаряется с поверхности морей и океанов (88‰)...
Историки об Елизавете Петровне: Елизавета попала между двумя встречными культурными течениями, воспитывалась среди новых европейских веяний и преданий...
Топ:
Эволюция кровеносной системы позвоночных животных: Биологическая эволюция – необратимый процесс исторического развития живой природы...
Когда производится ограждение поезда, остановившегося на перегоне: Во всех случаях немедленно должно быть ограждено место препятствия для движения поездов на смежном пути двухпутного...
Интересное:
Аура как энергетическое поле: многослойную ауру человека можно представить себе подобным...
Берегоукрепление оползневых склонов: На прибрежных склонах основной причиной развития оползневых процессов является подмыв водами рек естественных склонов...
Национальное богатство страны и его составляющие: для оценки элементов национального богатства используются...
Дисциплины:
![]() |
![]() |
5.00
из
|
Заказать работу |
Содержание книги
Поиск на нашем сайте
|
|
Использование активных углей позволяет получать серную кислоту, но концентрацией 20 %.
Применение цеолитов и оксидов металлов дает возможность проводить адсорбцию при высоких температурах и получать при оптимальных условиях регенерации сорбентов газы с концентрацией диоксида серы до 25 %, которые можно переработать в серную кислоту.
Недостаток адсорбционных методов - необходимость регенерации адсорбентов, их механическое разрушение.
Оксиды азота
Источники выброса газов, содержащих оксиды, разнообразны. Эти газы различаются по содержанию в них оксидов азота и других примесей, степени окисления оксидов азота, температуре, давлению и т.д. При этом объемная доля оксидов азота в отходящих газах может колебаться от 0,07 до 30 %.
Методы очистки газов от оксидов азота делятся на окислительные, восстановительные и сорбционные.
Окислительные методы основаны на предварительном окислении монооксида азота с последующим поглощением диоксида азота и триоксида азота различными поглотителями. Окисление монооксида азота можно проводить несколькими путями: в газовой фазе кислородом, в жидкой фазе с газообразным кислородом; наиболее эффективный метод окисления NO газообразным кислородом на катализаторах (силикагель, карбоалюмогель, гопкалит).
Окисление монооксида жидкими окислителями (водный раствор пероксида водорода, азотная кислота, хроматы и бихроматы, перманганат калия) – эффективный процесс, обеспечивающий окисление до остаточного содержания оксидов азота в газе от 50 до 100 см3/м3, процесс протекает при обычном давлении и температуре:
ЗН2О2 + 2NO ® 2HNO3 + 2Н2О
KMnO4 + NO ® KNO3 + MnO2
HNO3 + NO ® NO2 + HNO2
K2Cr2O7 + 2NO + 3H2O ®KNO3 + 2 Cr(OH)3
Однако жидкие окислители дороги, требуется их регенерация, большое количество отходов.
Восстановительные методы основаны на восстановлении оксидов азота до азота различными восстановителями в присутствии катализаторов и под действием высоких температур.
Селективное восстановление оксидов азота с помощью аммиака на алюмованадиевом катализаторе при t = 300 °С протекает по следующей схеме:
NO + 4NH3 ® 5N2 + 6H2O
6NO2 + 8NH3 ® 7N2 + 12H2O6
4NO + 4NH3 + О2 ® 4N2 + 6H2O
4NH3 + 3O2 ® 2N2+ 6H2O.
Для более полного протекания реакций содержание аммиака должно превышать стехиометрическое на 20-30 %. Процесс достаточно прост по аппаратурному оформлению и внедрен в производстве азотной кислоты. Процесс обеспечивает 96 % очистку нитрозных газов.
Технологическая схема очистки отходящих производственных газов от окислов азота представлена на примере процесса датской фирмы «Денокс» (рис. 4.7)
|
Рис. 4.7. Принципиальная технологическая схема очистки
отходящих производственных газов от оксидов азота:
1 – резервуар для жидкого аммиака; 2 – испаритель; 3 – сопловой
распределитель; 4 – реактор; 5 – пароструйные воздуходувки
Жидкий аммиак из резервуара 1 подается в испаритель 2, откуда пары аммиака, смешиваясь с воздухом высокого давления, поступают в поток очищаемого газа через сопловый распределитель 3, обеспечивающий равномерное распределение аммиака в сечение газового потока.
Система газораспределения на входе в реактор 4 обеспечивает равномерный профиль распределения газа перед слоем катализатора, что обеспечивает эффективное использование последнего при сравнительно малом аэродинамическом сопротивлении слоя катализатора. Реактор имеет обычно прямоугольное сечение и содержит два или более слоя катализатора, между которыми при необходимости располагают пароструйные воздуходувки 5 для удаления пыли и летучей золы с поверхности катализатора.
Метод гомогенного восстановления оксидов азота основан на селективном восстановлении оксидов азота аммиаком в газовой фазе при отсутствии катализатора. При взаимодействии аммиака с NОх в присутствии паров воды в газовой фазе при температуре 30-40 °С протекают следующие экзотермические процессы:
NH3 + Н2О ® NH4OH
2NO2 + 2NH4OH ® NH4NO2 + NH4NO3
N2O3 + 2NH4OH ® 2NH4NO2 + H2O
Последующее нагревание газового потока до 240 °С приводит к разложению образовавшихся аэрозолей нитритов и нитратов аммония на безвредные продукты:
NH4NO2 ® N2 + 2Н2О
NH4NO3® N2 + 2H2O + 1/2O2.
Каталитическое восстановление оксидов азота проводят в присутствии катализатора из сплавов металлов платиновой группы или составов, содержащих никель, хром, медь, цинк, ванадий и др. Восстановителями служат водород, оксид углерода, метан и другие углеводороды:
NO(NO2) + СН4 ® N2 + СО2 + Н2О
NO(NO2) + Н2 ® N2 + Н2О
NO(NO2) + СО ® N2 + СО2
Газы, подлежащие очистке, в смеси с газом-восстановителем нагревают до требуемой температуры 150-480 °С (в зависимости от вида восстановителя и катализатора) и пропускают через слой катализатора. Отходящие газы содержат значительное количество кислорода, который окисляет восстановители. В процессе выделяется большое количество тепла, резко возрастает температура, что обусловливает повышенное требование к термостабильности и механической прочности катализатора. Тепло, выделяющееся в процессе восстановления, можно использовать в газовых турбинах для получения дополнительной энергии, что улучшает экономические показатели процесса очистки.
|
Сорбционные методы основаны на поглощении оксидов азота жидкими или твердыми сорбентами.
Щелочная абсорбция целесообразна при санитарной очистке газов от оксидов азота при степени окисления близкой к 50 %. В качестве абсорбентов можно применять растворы соды Na2CO3, едкого натра NaOH, известкового молока СаСОз и мочевину CO(NH2)2 (40 %-ный раствор):
NO + NO2 + CO(NH2)2 → 2N2 + CO2 + 2H2O
Хемосорбционные методы применяются для одновременной очистки от оксидов серы и азота. В качестве сорбента используют соединения меди, которые поглощают оксиды серы, а оксиды азота восстанавливаются с помощью подаваемого аммиака. Процесс проводят в «кипящем» слое при температуре от 400 до 450 °С.
Сероводород
Очистка газов от сероводорода осуществляется по двум направлениям: санитарная очистка отходящих производственных и вентиляционных газов и очистка технологических газов, используемых для дальнейшей переработки. От сероводорода очищают природный газ, газы различных нефтеперерабатывающих и нефтехимических процессов (гидроочистка, крекинг, риформинг, пиролиз и др.). Газы различаются содержанием сероводорода. Требования к степени очистки от сероводорода зависят от назначения газа. При очистке газов, выбрасываемых в атмосферу, содержание сероводорода должно соответствовать ПДК. При очистке технического газа содержание сероводорода регламентируется требованиями технологического процесса. В частности для химических синтезов содержание сероводорода в технологическом газе находится в пределах от 1 до 50 мг/м3. Сероводород, выделяемый при очистке, перерабатывают в элементарную серу или серную кислоту.
Методы очистки газов от сероводорода делятся на две основные группы: сорбционные и каталитического окисления.
Абсорбционные методы. Наибольшее распространение получил метод хемосорбции, обеспечивающий степень очистки до 99,9 %. В качестве сорбента используются этаноламины. При этом моно- и диэтаноламины извлекают из газов как H2S, так и СО2, а триэтаноламин – только сероводород.
H2S + N(C2N5OH) ↔ [(HOC2H4)NH]+ [HS]-
Селективными абсорбентами для H2S служат также метилдиэтаноламин, дигликольамин и диизопропаноламин, получившие широкое распространение в России и за рубежом.
|
Характеристика абсорбентов сероводорода и параметры процессов приведены в таблице 4.1.
Эксплуатация систем очистки газов от H2S аминами связана с рядом трудностей, вызываемых пенообразованием, термическим и химическим разложением реагентов и коррозией. В целом очистка больших количеств высокосернистого газа с применением жидких поглотителей - экономически наиболее целесообразна.
Таблица 4.1. Характеристика абсорбентов сероводорода
Абсорбент | Концентрация поглотителя в растворе, % | Температура абсорбции, оС | Степень абсорбции, % |
Этаноламины | - | 20-50 | 96-98 |
Содовый | 15-18 | ||
Поташный | 20-25 | 40-50 | 90-98 |
Мышьяково-содовый | 17,38 | 20-45 | 92-98 |
Цианамид кальция | - | 30-45 | 98-99 |
Мышьяково-поташный | _ | 35-50 | 94-99 |
Этаноламиновая очистка не позволяет очистить газ до содержания сероводорода <0,5 %. Поэтому, для достижения требуемой степени очистки, после этаноламиновой очистки обычно проводят горячую щелочную очистку при температуре 50-80 °С и давлении 2 МПа:
H2S + 2NaOH → Na2S + 2Н2О
Процесс необратим. Это приводит к расходу щелочи, образованию шлама в виде Na2S и потере H2S для дальнейшей переработки.
В последние годы для очистки от сероводорода природного газа широко применяют адсорбционные методы. Содержащие сероводород отходящие газы промышленных производств обычно характеризуются низким, но превышающим требования санитарных норм, содержанием этого загрязнителя. Например, в вентиляционных выбросах производств вискозы его концентрация колеблется в пределах от 0,01 до 0,1 %. Наиболее глубокую очистку газов от сероводорода обеспечивают адсорбционные методы с использованием гидроксида железа, активного угля, цеолитов и других поглотителей.
Процесс очистки газов от сероводорода гидроксидом железа используется давно. При прохождении газа через слой гидроксида железа сероводород поглощается
2Fe(OH)3 + 3H2S → Fe2S3 + 6H2O
Одновременно образуется некоторое количество FeS. Присутствующий в очищенном газе кислород окисляет сульфидную серу с образованием гидроксида железа:
Fe2S3 + 3/2О2 + 3Н2О → 2Fe(OH)3 + 3S
В современной промышленной практике поглотительную массу приготавливают из болотной руды или отходов производства глинозема из бокситов-красных шламов влажностью 50-55 %, содержащих 45-48 % Fe2О3 (на сухое вещество).
Эффективным поглотителем сероводорода является активный уголь. Присутствие в очищенном газе кислорода является необходимым условием реализации процесса, в котором наряду с поглощением сероводорода происходит катализируемое углем окисление последнего в адсорбенте, сопровождающееся выделением тепла (220 кДж на 1 моль H2S).
H2S + 0,5О2 → S + Н2О
Одновременно с этим процессом в адсорбенте происходит также экзотермическая (790 кДж на 1 моль H2S) каталитическая реакция превращения сероводорода в серную кислоту:
|
H2S + 2О2 → H2SО4
Количественная доля последней реакции тем выше, чем больше тяжелых металлов, в частности железа, находится в минеральной составляющей активного угля; она может составлять более трети по отношению к поглощенному сероводороду.
Высокая экзотермичность процессов окисления сероводорода при значительных концентрациях его в очищаемых газах обусловливает интенсивный разогрев слоя поглотителя и связанный с этим риск возгорания активного угля. В этой связи использование активного угля для очистки газов сероводорода обычно ограничивают газами, содержащими до 5 г/м3 этого загрязнителя, хотя известны реализованные в промышленной практике процессы поглощения активными углями сероводорода из газов с высокой его концентрацией (10-13 г/м3).
Для нейтрализации образующейся в угле серной кислоты может быть использован раствор карбоната натрия (соды) или газообразный аммиак. Использование последнего более эффективно, так как для вымывания водой из угля аммонийных солей требуется меньший ее расход. Кроме того, аммиак интенсифицирует окисление сероводорода, поэтому его можно вводить в очищаемый газ для обеспечения протекания реакции, параллельной основной реакции окисления
H2S + NH3 + 2O2 → (NH4)2SO4
Если в очищенном газе присутствует CO2, наряду с последней реакцией протекает взаимодействие
CO2 + 2NH3 + H2O → (NH4)2CO3
Возможно и периодическое использование аммиака лишь на стадии регенерации насыщенного поглотителя.
Сероемкость используемых для очистки газов от сероводорода активных углей составляет от 200 до 520 кг/м3. При высоте слоя угля более 1 м достигаемая степень насыщения поглотителя превосходит 90 %. Регенерацию насыщенных углей наиболее часто проводят раствором сульфида аммония. При регенерации протекает реакция
2(NH4)2S + 3S2 → 2(NH4)2S4
(NH4)2S + (n-1)S → (NH4)2Sn
Образующийся раствор многосернистого (200-250 кг/м3) обрабатывают острым паром при 125-130 оС под давлением (1,6-1,9)×105 Па с целью выделения серы.
(NH4)2Sn → (NH4)2S + (n-1)S
В условиях такой обработки разлагается и (NH4)2S, поэтому образующиеся пары конденсируют и возвращают в процесс. Получаемую жидкую серу (99,92-99,97 %) отделяют от раствора декантацией. Экстрагированный освобождают от сульфидной серы промывкой его водой, выпаривают для удаления аммонийных солей и сушат.
Для экстракции серы из угля в ряде случаев применяют ксилол, используя резкую разницу растворимости в нем серы при обычных и повышенных температурах. Обработку угля кислородом проводят при 100-110 оС и давлении 2,5×105 Па. При последующем охлаждении вытяжки (до 30 оС) из нее выделяют застывшую серу. Экстрагированный уголь обрабатывают паром для освобождения от ксилола, промывают водой для удаления других продуктов превращений, происходящих на адсорбенте, и вновь пропаривают.
|
Образующиеся углеаммонийные соли при значительном содержании в очищаемых газах могут забивать трубопроводы и арматуру установки. Для предупреждения этого процесса целесообразна пропитка активного угля 0,8 %-ном водным раствором щелочи. Поглотительная способность угля по сероводороду и интенсификация образования элементной серы увеличивается при пропитке поглотителя иодом (1 % от массы угля) или иодидом калия.
Направляемый на очистку газ смешивают с аммиаком, редуцируемым из баллона, и вводят в реактор, где в кипящем слое активного угля происходит его чистка от сероводорода. Очищенный газ удаляют через пылеуловитель. Насыщенный поглотитель из реактора транспортируют в отделение экстракции серы, откуда он поступает в промывное отделение и далее на обезвоживание в сушильную установку. Сухой регенерированный уголь из бункера питателем возвращают в реактор. Для компенсации потерь угля в бункер добавляют свежий поглотитель.
При содержании сероводорода в поступающем на обработку газе до 100 мг/м3 использование очистки на основе активных углей может обеспечить его остаточную концентрацию в газе менее 0,001 %.
Эффективным средством очистки газов от полярных соединений, в частности сероводорода, являются синтетические цеолиты (NaA, CaA, NaX). Поглотительная способность цеолитов поэтому компоненту в условиях его концентраций в поступающих на очистку газах, отвечающих парциальному давлению 13,33; 1,33 и 1,13 кПа при 25 оС может достигать соответственно 14-16; 9,5-10,5 и 4,0-4,8 г на 100 г поглотителя. С увеличением температуры этот показатель синтетических цеолитов снижается, оставаясь, тем не менее, достаточно высоким: при том же содержании сероводорода в газах и температуре 150 оС он достигает 5,5-7,5; 2,0-2,5; 0,2-0,9 г /100 г поглотителя соответственно. Помимо высокой поглотительной способности при низких концентрациях сероводорода в газовых потоках эти адсорбенты характеризуются селективностью его извлечения, в частности, при одновременном присутствии СО2.
Оптимальные результаты использования синтетических цеолитов обеспечиваются при обработке ими газов с содержанием серы 2 %. Концентрация серы в очищаемых ими газах может быть снижена до 1 мг/м3 и ниже.
В практике технологической очистки газов от сероводорода используют различные приемы регенерации насыщенных цеолитов – обработку их диоксидом серы при 315 оС (цеолит катализирует процесс образования из сероводорода и диоксида серы воды и элементной серы, пары которой конденсируют с последующим сжиганием трети жидкой серы до диоксида серы), десорбцию водяным паром, продувку очищенными от сероводорода газами при 300-350 оС с последующей промывкой газов десорбции водой и направлением их в цикл.
Использование синтетических цеолитов для решения задач санитарной очистки от сероводорода газовых выбросов промышленных производств сдерживается значительной стоимостью этих адсорбентов.
Находят применение и другие твердофазные поглотители, получаемые на основе оксида цинка, оксидов цинка и меди, а также содержащие цинк и медь отработанные катализаторы процессов низкотемпературной конверсии оксида углерода. Поглощение сероводорода этими хемосорбентами основано на следующих реакциях:
H2S + ZnO = ZnS + H2O
H2S + Cu = CuS + H2
H2S +2Cu = Cu2S + H2
Приведенные реакции практически необратимы в интервале температур от 200 до 500 оС, поэтому процессы очистки газов от сероводорода с использованием названных хемосорбентов требуют предварительного нагрева подвергаемых обработке газовых потоков. Отработанные поглотители обычно не регенерируют, хотя восстановление их поглотительной способности усложняет и удорожает соответствующие процессы.
Сорбционные свойства углей могут быть повышены введением в их состав оксидов меди, железа, никеля, марганца, кобальта.
Наряду с традиционными адсорбентами в последние годы разрабатывают поглотители на основе оксидов молибдена, теллура, марганца и карбонатов щелочных металлов.
Получение серы из сероводорода. Известно несколько способов получения серы из сероводорода, выделяемого на установках очистки нефтепродуктов от серы. Наиболее распространены процессы каталитической конверсии (контактное окисление, или метод «Клауса»).
Метод Клауса. Переработка сероводородного газа производится по трехступенчатому окислительному методу Клауса с применением термической и двух каталитических ступеней.
Термическая стадия заключается в высокотемпературном сжигании сероводорода в топке котла-утилизатора при подаче стехиометрического количества воздуха согласно реакции
H2S + O2 → 2H2O + S2 + 157210 кДж/кг×моль H2S
Стехиометрическое соотношение количества воздуха и сероводорода (отношение объема воздуха к объему сероводородного газа) в зависимости от состава сероводородного газа должно быть в пределах 2:1 – 3:1.
Реакция протекает при температуре 1000-1500 оС в зависимости от концентрации сероводорода в сероводородном газе и наличия в нем углеводородов.
Часть сероводородного газа в топке котла-утилизатора превращается в диоксид серы по реакции
2H2S + 3O2 → 2H2O + 2SО2 + 519160 кДж/кг×моль H2S
Углеводороды и аммиак, содержащиеся в сероводородном газе, сгорают по реакции
С2Н6 +3SO2 → 2CO2 + 3H2O + 1427700 кДж/кг×моль С2Н6
2NH3 + 1,5O2 → N2 + 3H2O
Наличие в составе сероводородного газа газообразных углеводородов в количестве свыше 2 %, а также жидких углеводородов влечет за собой серьезные нарушения процесса дальнейшей каталитической переработки, связанные с возможностью отложения кокса на поверхности катализатора, снижением его активности и понижением выхода серы.
При охлаждении газов после термической ступени происходят следующие реакции:
а) ассоциация молекул S2 в S6 и S8
3S2 → S6 + 91100 кДж/кг×моль S2
4S2 → S8 + 101490 кДж/кг×моль S2
б) ассоциация молекул серы S6 в S8
4S6 → 3S8 + 41660 кДж/кг×моль S8
в) конденсация серы
S8 (г) → S8 (ж) + 95710 кДж/кг×моль S8
На каталитических ступенях процесса при температуре от 200 до 320 оС на катализаторе (активной окиси алюминия марки CR и AM) происходит конверсия сероводорода и диоксида серы с образованием серы по реакциям
2H2S + SO2 → 3/6S6 + 2H2O + 44250 кДж/кг×моль H2S
2H2S + SO2 → 3/8S8 + 2H2O + 52000 кДж/кг×моль H2S
Так как реакции протекают с выделением тепла, то понижение температуры реакции способствует увеличению выхода серы. Минимальная температура реакции определяется температурой точки росы серы. Применение двух каталитических ступеней способствует увеличению выхода серы вследствие более низкой температуры реакции во второй ступени по сравнению с первой. Вывод серы из газовой фазы сдвигает равновесие в сторону увеличения ее выхода и уменьшает температуру точки росы серы в технологическом газе.
С этой целью предусмотрено охлаждение технологического газа после каждой ступени конверсии с использованием тепла горячих газов для получения насыщенного водяного пара. Подогрев технологического газа перед каталитическими ступенями осуществляется за счет смешения с продуктами сгорания топливного газа в топках-подогревателях. Выход серы на установке производства серы с узлом доочистки составляет не менее 99,9 %.
Для возможности безопасной транспортировки жидкой серы производится ее дегазация по непрерывному воздушному способу, при этом отходящий серосодержащий газ с производства серы после охлаждения в конденсаторе-генераторе направляется на дальнейшую переработку в секцию очистки отходящих газов. Дожиг остаточного сероводорода до оксида серы производится в печи со сбросом отходящих газов в атмосферу через дымовую трубу.
Катализаторы получения серы методом Клауса (в частности γ-Al2O3) выпускают на катализаторных фабриках из гидроксида алюминия Al(OН)3. Продолжительность эксплуатации катализатора колеблется от одного до семи лет в зависимости от условий его работы, состава кислых газов и многих других факторов. Средний срок активной жизни катализаторов на основе оксида алюминия составляет четыре года. Именно этот срок закладывается в эксплуатационные характеристики установок производства серы методом Клауса.
Состояние и активность слоев катализатора являются основными факторами производительности установки и уровня потерь серы.
Из всего многообразия причин, вызывающих дезактивацию катализаторов Клауса, к наиболее важным следует отнести:
· снижение удельной поверхности за счет термической деструкции γ-Al2O3;
· снижение удельной поверхности за счет гидротермической деструкции;
· снижение числа активных центров за счет хемосорбции диоксида серы;
· сульфатирование поверхности катализатора;
· снижение удельной поверхности и объема пор за счет отложений жидкой серы;
· блокировка поверхности и пор катализатора углеродистыми отложениями.
Катализатор марки АМ, разработанный французской фирмой «Рон-Пуленк», используется в качестве защитного лобового слоя и предохраняет основной слой катализатора от сульфатации. Состав катализатора: обычная γ-Al2O3 (СR), пропитанная сульфатом железа. Он обладает свойством поглощать следы O2 и SO3, присутствующие в газах. Срок службы основного катализатора увеличивается. Катализатор марки АМ используют в качестве защитного слоя в первом реакторе, и в качестве основного слоя в последнем, так как он обладает хорошей активностью в отношении реакции Клауса. Техническая характеристика катализаторов Клауса приведена в таблице 4.2.
Так, на ОАО «СлавнефтьЯрославльнефтеоргсинтез» имеется установка утилизации сероводорода, поступающего с установок переработки нефтяных фракций (гидрокрекинг, каталитический риформинг, пиролиз и т.д.) в элементарную серу (рис. 4.8).
Описание технологической схемы получения элементарной серы из сероводорода (секция Клауса). Сероводородный газ от действующих установок завода поступает в сепаратор 2 для отделения капельной влаги. Сероводородный газ из сепаратора 2 направляется на подогрев в теплообменник 5. Подогретый сероводородный газ смешивается с кислым газом и распределяется на котлы-утилизаторы 6. Воздух для сжигания кислого газа подается в котел-утилизатор 6 воздуходувками 42. В трубках котла-утилизатора 6 продукты сгорания сероводородного газа охлаждаются; при этом в котле образуется насыщенный пар давлением 0,4 МПа, а сера, образовавшаяся в термической ступени, конденсируется и через серозатворы выводится в сборник дегазации 14.
Рис. 4.8. Установка утилизации сероводорода, поступающего с установок переработки нефтяных фракций
В элементарную серу
Таблица 4.2. Техническая характеристика катализаторов Клауса
Показатель | CR | АМ | Отечественный катализатор на основе γ-Al2O3 | Отечественный катализатор на основе TiO |
Состав: мас. доля, % γ-Al2O3 Na2O Fe2O3 SiO2 TiO2 | 94,0 0,60 0,04 0,02 0,01 | сульфат железа | 0,03 0,02 0,02 - | 10 + 1 - 1,0 + 0,5 0,25 83 + 2 |
Удельная поверхность, м2 | 110-140 | |||
Сопротивление раздавливанию, кг | - | |||
Потери при прокали-вании, мас. доля, % | 3-5 | 3-5 | - | |
Плотность, г/см3 | 0,77 | 0,75 | 0,70 | 0,8-1 |
Технологический газ после утилизатора 6 направляется на подогрев перед 1-й каталитической ступенью. Подогрев газа осуществляется в топке-подогревателе 7 за счет смешения с продуктами сгорания топливного газа.
Подогретый технологический газ поступает в конвертор 1-й ступени 8, представляющий собой вертикальный цилиндрический аппарат, внутри которого расположены два слоя катализатора. На катализаторе осуществляется реакция Клауса, идущая с выделением тепла, при этом температура технологического газа на выходе из конвертора 8 повышается.
Для охлаждения и конденсации серы газ из конвертора 8 направляется на 1-ю ступень конденсатора-генератора 9. Сконденсировавшаяся сера через серозатвор отводится в сборник дегазации 14.
Конденсатор-генератор 9 представляет собой аппарат газотрубного типа: в котле получается пар давлением 0,4 МПа.
Технологический газ после конденсатора 1-й ступени подогревается в топке-подогревателе 10 перед 2-й каталитической ступенью.
Подогрев осуществляется аналогично описанному выше для 1-й ступени конверсии. Подогретый технологический газ после топки-подогревателя 10 поступает в конвертор 2-й ступени 11, где на катализаторе протекает реакция Клауса с выделением тепла.
После 2-й ступени конверсии технологический газ направляется на охлаждение и конденсацию серы во 2-ю ступень конденсатора-генератора 9.
Сера через серозатвор стекает в сборник дегазации 14, а технологический газ направляется через сероуловитель 12 на адсорбцию для доочистки отходящих газов.
Для питания котлов используется паровой конденсат собственной выработки с добавкой химически очищенной воды, которые поступают в сборник 13. Для избежания потерь с вторичным паром, получаемым при вскипании парового конденсата за счет снижения его давления, предусмотрен конденсатор. Питательная вода из сборника 13 насосом 43 подается в котлы-утилизаторы 6 и 9. Часть питательной воды циркулирует в питательном контуре.
Топливный газ, поступающий на установку, проходит сепаратор 1 для отделения капельной влаги и теплообменник 4 для перевода топливного газа из насыщенного влагой состояния в перегретое во избежание конденсации влаги перед горелками топочных агрегатов. Для вывода конденсата из сепаратора 1 предусмотрен насос 40.
Очищенный технологический газ из секции адсорбции доочистки отходящих газов направляется на обезвреживание в печь дожига 16. Дожиг остаточного сероводорода, присутствующего в технологическом газе, ведется в печи дожига за счет смешения с продуктами сгорания топливного газа с целью достижения температуры 600 оС, при которой сероводород окисляется до сернистого ангидрида.
Воздух для окисления сероводорода инжектируется из атмосферы. В печи дожига 16 обезвреживается также паро-воздушная смесь из емкости дегазации 14, подаваемая эжектором 15.
Дымовые газы сбрасываются через дымовую трубу 17. Перед сбросом дымовые газы разбавляются за счет организованного подсоса воздуха из атмосферы с целью снижения температуры до 500 °С.
Жидкая сера поступает в подземный сборник 14, где осуществляется непрерывный процесс дегазации серы. Дегазация серы осуществляется за счет барботажа воздуха, подаваемого турбогазодувкой 42 в барботажную колонну. Емкость 14 разделена на две части перегородкой. В наибольшей части емкости, предназначенной непосредственно для дегазации, расположена барботажная колонна.
Дегазированная сера переливается в меньшую часть емкости 14. По мере накопления дегазированной серы, последняя откачивается насосами в хранилище жидкой серы.
Таким образом, за счет совершенствования технологического процесса, создания установок по улавливанию и рекуперации газообразных выбросов, можно резко сократить выбросы в атмосферу, что положительно скажется на состоянии природной среды и человека.
Глава 5. УТИЛИЗАЦИЯ ОТХОДОВ ПОТРЕБЛЕНИЯ
Любая хозяйственная деятельность связана с воздействием на окружающую природную среду. С одной стороны, это связано с тем, что для производства товаров и услуг необходимы природные ресурсы, потенциал которых за последнее время существенно уменьшился. С другой стороны, каждый хозяйствующий субъект эксплуатирует земельные территории, загрязняет окружающую природную среду газообразными выбросами и жидкими стоками, при этом количество твердых отходов, образующихся как при производстве продукции, так и при ее потреблении неуклонно растет.
Одной из проблем современных городов была и остается проблема твердых бытовых отходов (ТБО). Сложившаяся практика показывает, что ни один из существующих в настоящее время способов решения данной проблемы не лишен недостатков. В связи с этим основные усилия ученых направлены на совершенствование уже существующих методов в направлении увеличения их экологической безопасности и повышения их экономической эффективности.
|
|
Семя – орган полового размножения и расселения растений: наружи у семян имеется плотный покров – кожура...
История создания датчика движения: Первый прибор для обнаружения движения был изобретен немецким физиком Генрихом Герцем...
Архитектура электронного правительства: Единая архитектура – это методологический подход при создании системы управления государства, который строится...
Археология об основании Рима: Новые раскопки проясняют и такой острый дискуссионный вопрос, как дата самого возникновения Рима...
© cyberpedia.su 2017-2024 - Не является автором материалов. Исключительное право сохранено за автором текста.
Если вы не хотите, чтобы данный материал был у нас на сайте, перейдите по ссылке: Нарушение авторских прав. Мы поможем в написании вашей работы!