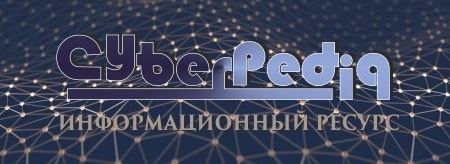
Семя – орган полового размножения и расселения растений: наружи у семян имеется плотный покров – кожура...
Автоматическое растормаживание колес: Тормозные устройства колес предназначены для уменьшения длины пробега и улучшения маневрирования ВС при...
Топ:
Установка замедленного коксования: Чем выше температура и ниже давление, тем место разрыва углеродной цепи всё больше смещается к её концу и значительно возрастает...
Техника безопасности при работе на пароконвектомате: К обслуживанию пароконвектомата допускаются лица, прошедшие технический минимум по эксплуатации оборудования...
Особенности труда и отдыха в условиях низких температур: К работам при низких температурах на открытом воздухе и в не отапливаемых помещениях допускаются лица не моложе 18 лет, прошедшие...
Интересное:
Как мы говорим и как мы слушаем: общение можно сравнить с огромным зонтиком, под которым скрыто все...
Мероприятия для защиты от морозного пучения грунтов: Инженерная защита от морозного (криогенного) пучения грунтов необходима для легких малоэтажных зданий и других сооружений...
Принципы управления денежными потоками: одним из методов контроля за состоянием денежной наличности является...
Дисциплины:
![]() |
![]() |
5.00
из
|
Заказать работу |
Содержание книги
Поиск на нашем сайте
|
|
Отходы резиновой промышленности, в частности амортизированные шины, представляют серьезную проблему во всем мире в связи с необходимостью их сжигания или захоронения. Лучшим вариантом утилизации таких отходов является использование их после соответствующей переработки на местах производства. Изготовители шин и других резинотехнических изделий должны по возможности осуществлять производство шин, их эксплуатацию и устранение отходов без загрязнения окружающей среды и предотвращать образование отходов. В перспективе стратегия повторного использования должна быть положена в основу более жестких экологических и законодательных актов с учетом концепции повторного использования. Энергетические и финансовые издержки, связанные с переработкой изношенных шин, сводятся к минимуму, если непригодные для использования изношенные шины применяют в качестве звукоизоляционных экранов, для закрепления свеженасыпанных дорожных откосов и в сельскохозяйственном строительстве; при строительстве дамб; в качестве отбойного бруса для защиты наружной стороны судов; в качестве резиновой дорожки к строительной площадке и на песчаных карьерах; для футеровки трубопроводов и т.д. Такой путь использования отходов определяется быстрым насыщением рынка, причем он может поглотить лишь часть изношенных шин.
Ключевые позиции в устранении отходов резиновой промышленности занимает их сжигание. По мнению сторонников такой позиции, сжигание экологически оправдано, экономически целесообразно и технически легко реализуется. Изношенные шины следует сжигать в промышленных установках, используемых для получения технологического тепла и для теплофикации. Сторонники технологии сжигания всегда указывают на то, что эмиссия вредных веществ может быть снижена до минимума, при этом на свалку приходится отправлять лишь небольшое количество остаточных шлаков и пыли с фильтров. Противники сжигания указывают на высокую стоимость таких установок, тем самым ставя под сомнение предполагаемую экономическую эффективность процесса. При этом не следует забывать, что при сжигании шин теряется ценное нерегенерированное сырье. Действительно, для изготовления одной шины для легкового автомобиля расходуется 35 л нефти, в то время как теплотворная способность при сжигании шины соответствует лишь 6-8 л. Энергия, затраченная на полимеризацию, при сжигании полностью теряется.
|
Большую часть изношенных шин отвозят на официальные свалки или закапывают, либо хранят на складах. При хранении на свалках изношенные шины плохо уплотняются и создают неустойчивую пружинящую поверхность. Предварительное измельчение изношенных шин может повысить насыпную массу, уменьшить включение воздуха и увеличить стабильность поверхности свалки, но эта операция является дорогостоящей. К тому же, для измельченных шин характерно большее время разложения, причем часто возникает опасность возникновения пожара, при котором происходит выделение большого количества канцерогенных веществ, загрязняющих почву, воду и воздух.
Существенно более важным, чем разработка способа устранения отходов, является повторное использование изношенных шин. Этого можно добиться несколькими путями. Во-первых, путем наложения нового протектора. В Германии на каждую вторую шину для грузовых автомобилей и на каждую шестую для легковых автомашин наносят новый протектор. В автомобилестроении наложение нового протектора стали проводить в послевоенное время в связи с ограниченностью средств, а также из экологических соображений, так как это является важным вкладом в сбережение ресурсов и предотвращение образования отходов: 80 % шины (бортовое крыло, каркас и металлокордный брокер) используются повторно. Если для изготовления новой шины для легкового автомобиля требуется 35 л нефти и специальная ткань из кордных нитей или из очень тонкого металлокорда, то при восстановлении шины расход нефти составляет лишь 5,5 л. Кроме того, образующиеся при восстановлении шин крошка резины и обрезки резины повторно используются в качестве сырья для вторпродуктов. Во-вторых, альтернативой повторного использования является измельчение изношенных шин с получением резиновой крошки (муки) или гранулята для замены каучука в резиновых смесях.
|
Резиновая крошка (мука) и продукты криодеструкции и высокотемпературной переработки изношенных шин нашли относительно широкое применение в промышленности. Основные направления их использования:
· в качестве инертной добавки при производстве новых покрышек, резинотехнических изделий (РТИ) и других резиновых смесей (автомобильные детали, изделия для сантехники и др.);
· в качестве добавки при строительстве шоссейных дорог, в асфальтобетонные смеси (Англия, США);
· в производстве из резиновой крошки покрытий для площадок, беговых дорожек, крыш зданий и сооружений, полов сельскохозяйственных предприятий, плит для переездов через железнодорожные и трамвайные пути, резиновых ковриков (резиновые плиты, листы, шифер, резино-пластмассовая черепица, рулонный кровельный материал и др.);
· в производстве регенерата термомеханическим методом;
· в качестве добавки при получении защитных покрытий (гидро-, звуко- и теплоизоляционные материалы, ударопрочные пластмассы и резинопласты);
· в качестве добавки для производства термопластов, пластификаторов, наполнителей для изделий из пластмасс и резины, резиновых и резинобитумных мастик;
· при получении из резиновой крошки топлива.
Получение резиновой крошки и дальнейшее её использование в качестве добавок – весьма популярное направление переработки шин. В процессе дробления происходит частичный разрыв серных связей, при этом структура эластомерной композиции (каучука) остается практически без изменений, т.е. реальна возможность использовать ценные свойства резины для производства вторичной продукции достаточно высокого качества.
|
В зависимости от способа и условий измельчения из резиновых отходов шинного производства и изношенных шин можно получать измельченные в разной степени вулканизаты, от грубых кусков до тонкодисперсных резиновых порошков.
Диапазон использования отходов в виде резиновой крошки и порошка очень широк, начиная с второстепенных изделий и кончая такими важными изделиями, как шины, клиновые ремни.
В грубоизмельченном виде, например, в виде небольших полос, изношенные шины используют при изготовлении настилов для пола, матов. Иногда эти полоски подвергают дополнительной обработке растворителем и латексным адгезивом, а потом формуют из них коврики. Шинные отходы в виде лент длиной 10-25 мм и толщиной 1,5-2 мм используют в производстве резиновых блоков для мостовых с гладкой поверхностью и высоким сопротивлением растрескиванию. С этой целью к 100 частям выпрессовок добавляют 10 частей жидкого полиуретана и 1 часть красителя. Смесь вулканизуют в прессе при 120 °С в течение 20 минут.
Однако основное внимание отечественных и зарубежных исследователей привлекает проблема применения измельченных вулканизатов в виде резиновой крошки и тонкодисперсного резинового порошка. Применение измельченных кусков резины, хотя и приносит определенную пользу, однако не исчерпывает полностью возможности полимерного вещества, заложенного в старой резине.
Применение измельченного вулканизата в виде крошки. Наибольшее количество публикаций, посвященных применению измельченных вулканизатов, относится к изготовлению из них неответственных, второстепенных изделий. Как правило, к таким изделиям не предъявляют высоких требований, они дешевы, но в то же время обладают некоторыми ценными свойствами. Например, листы, полученные по различной технологии из резиновой крошки изношенных шин, отличаются высокой износостойкостью и могут использоваться для внутренней обкладки труб для перекачки водных суспензий земли и песка.
Известно применение резиновой крошки для изготовления монолитных резиновых плит и особенно настилов для полов животноводческих ферм взамен деревянных и бетонных, что позволяет снизить расход дерева и уменьшить заболеваемость животных. Для этой цели крошку смешивают с мягчителем, латексной смесью и даже с отходами латексного производства – крошкой осушенного коагулюма. Резиновые покрытия из крошки со связующим из отходов производства синтетического каучука, изношенных покрышек отвечают техническим, зоогигиеническим и эксплуатационным требованиям и обладают большим экономическим эффектом по сравнению с производством полов из древесины.
|
Отработанные шины в виде крошки находят все более разнообразное применение в адгезивах для изготовления ирригационных труб, в качестве инертного наполнителя в цементных смесях, для сбора нефти с поверхности воды, как материал фильтров по очистке воды, для получения ионитов из измельченной резины (0,5-3 мм). Крошку предлагают применять в качестве добавки к почве при выращивании культурных растений, как разрыхляющий агент.
Возможно изготовление микрофильтров из резиновой крошки. Обжиг резиновой крошки с размером частиц 0,1-5,0 мм осуществляется на металлическом противне при температуре 600-700 °С в атмосфере воздуха до полного прекращения выделения газообразных продуктов. При обжиге резиновой крошки различных типов получается порошкообразный материал с пористыми частицами. Доказана возможность изготовления микрофильтрующих элементов из обожженной резиновой крошки и применение таких фильтров для эффективной очистки глицериновой воды от остатков жиров в производстве глицерина.
Будучи дешевым сырьем, резиновая крошка может найти широкое применение в дорожном и промышленном строительстве. Из нее могут быть изготовлены звукоизоляционные и вибропоглощающие материалы, антикоррозийные покрытия и электроизоляционные материалы. Возможно использование крошки в качестве материала для кровли и стен при строительстве домов. Резиновая крошка может применяться и при производстве строительных материалов, обладающих высокой прочностью, сопротивлением ударным нагрузкам, водостойкостью.
Известен способ получения резинового полотна из крошки без добавления композиционных материалов. Измельченную утильную резину смешивают с 1-15 % серы, загружают полученную смесь в зазор между двумя сжимающими вращающимися цилиндрами, прессуют в зазоре при температуре от 121 до 232 °С и давлении от 7 до 21 МПа в течение 1-10 мин так, что образуется непрерывное полотно, пригодное для покрытия площадок, крыш зданий.
Отходы каучуков, машинных масел и технического углерода в сочетании с добавками мела и серы можно успешно использовать в производстве рулонных кровельных материалов.
По сообщению австралийской «Организации научных и промышленных исследований», изношенные покрышки положительно зарекомендовали себя в создании технологии получения химического сырья – акрилонитрил-бутадиен-стирольного каучука, который наполовину состоит из резины автомобильных покрышек, вместо поливинилхлоридного пластика.
|
Эффективное применение крошка находит в покрытиях для спортивных площадок, которые изготавливают из смеси ее с песком или другим минеральным наполнителем и эластомерного связующего. Полученные монолитные резиновые плиты применяют для покрытия легкоатлетических стадионов игровых полей, секторов и площадок открытых спортивных сооружений. Резиновую крошку с размером частиц 3-5 мм в смеси с водной суспензией полиуретанового форполимера можно использовать для изготовления атмосферо- и водостойких пластин для покрытия различных спортивных площадок и укрепления откосов.
В России в настоящее время активно развивается направление по использованию резиновой крошки при изготовлении дорожных оснований и дорожных покрытий. Резиновую крошку в различных количествах вводят в асфальтовые композиции и асфальтобетон. Введение в асфальтобетон 3-4 % резиновых частиц размером примерно 3 мм увеличивает сопротивление скольжению при определенной толщине ледяного слоя на дороге. Выступающие над поверхностью дорожного покрытия эластичные частицы резины деформируются под действием колес транспорта, и тонкий слой льда, покрывающий дорогу, трескается, что уменьшает скольжение. Применение резиновой крошки в асфальтобетоне в два раза повышает коэффициент сцепления на мокром покрытии. При использовании резиновой крошки до 1,0 мм трещиностойкость возрастает на 30 %. С уменьшением размера частиц трещиностойкость увеличивается. Особенно эффективно применение частиц крошки от 0,14 мм и меньше. Частицы меньше 0,08 мм за время перемешивания распадаются, составляющие модифицируют битум, улучшая его свойства. При небольших размерах частиц крошка распределяется по массе асфальтобетонной смеси более равномерно, повышая упругую деформацию при отрицательных температурах.
Разработан состав добавки в цементобетон и цементогрунт, повышающий подвижность смеси, морозостойкость, позволяющий сократить водопотребление на 15-18 %. С цементогрунтовым основанием в Пермской области и республики Удмуртия построено более 30 км автомобильных дорог.
Наиболее широко резиновую крошку используют как добавку в шинных резинах, поскольку это позволит снизить себестоимость шин за счет повторного использования дешевого материала. Изношенные покрышки измельчают до нужной величины, отделяют резину от элементов корда и добавляют в резиновую смесь.
Известно использование в резинах для восстановления шин шероховальной крошки, применение в протекторных резинах при изготовлении новых шин крошки из изношенных покрышек и подвулканизованной резиновой крошки. Введение небольших количеств измельченных отходов в резиновые смеси повышает износостойкость, сопротивление резин утомлению, что, в свою очередь, приводит к некоторому увеличению ходимости шин. Увеличение содержания резиновой крошки в шинных резинах ограничивается снижением прочностных свойств резин и технологическими возможностями. Для улучшения свойств крошки ее предварительно модифицируют. Частицы крошки, добавленные в шины, могут увеличить разброс значений их механических свойств. Известно также, что при использовании крошки из шин, длительное время хранившихся на открытом воздухе, этот разброс может быть больше.
Возможно введение резиновой крошки в верхние слои беговой части протектора после выхода протекторного массива из головки червячной машины (с последующей ее прикаткой). При этом образуется верхний бронирующий слой, наиболее насыщенный резиновой крошкой, без ухудшений свойств остальной части протекторной резины, связанной с каркасом.
Применение измельченных вулканизатов в виде тонкодисперсного порошка. Представляют интерес тонкоизмельченные (независимо от способа получения) резиновые порошки (ТИРП). Благодаря более высокой степени дисперсности они могут использоваться в тех же резинах, что и крошка, но со значительно большей эффективностью и в больших дозировках. Изделия, содержащие ТИРП, по качеству и внешнему виду превосходят изделия с крошкой.
Подобно резиновой крошке, ТИРП находит применение не только во второстепенных изделиях, но также и в более качественных. Предложен способ изготовления кровли, который включает в себя вальцевание порошка при температуре более 170 °С и зазоре, близком к нулю, до состояния чешуек, смешение их с поливинилхлоридом и последующее формование в листы. На 100 массовых частей поливинилхлорида вводят 10-80 массовых частей утильной резины. В смесь могут быть также добавлены обычные наполнители, пластификаторы, окрашивающие агенты.
Известны различные композиции для покрытий, состоящие из порошков с размерами частиц около 0,3 мм, короткого волокна и смолы в смеси с натуральным или синтетическим латексом или резорцинформальдегидной смолой. Изготавливают также смесь измельченной резины и дорожного битума, которую специальной обработкой превращают в устойчивую эмульсию, способную к течению при перемешивании. В некоторых случаях в качестве связующего для приготовления композиции применяют также жидкий полибутадиен, уретановый форполимер и др. Процесс изготовления композиции для литья изделий под давлением включает измельчение утильных шин до частиц размером 0,5 мм, добавление десульфирующего агента к полученной порошкообразной массе, проведение процесса десульфурации, добавление к полученной аморфной массе на 100 массовых частей 0,2-2 массовых частей серы, перемешивание, введение 30-100 массовых частей термопластичной смолы и последующую высокотемпературную обработку смеси.
Мелкодисперсную резину с размером частиц 0,3-0,08 мм можно использовать при изготовлении антиадгезива для крошки каучука и резиновой смеси с целью снижения слипаемости крошки в процессе хранения и повышения ее сыпучести.
Представляет интерес способ изготовления искусственной кожи с тонким вогнуто-выпуклым рисунком на поверхности, который предусматривает добавление частиц резины с размером менее 1,3 мм к раствору винилхлоридной смолы, введение других необходимых ингредиентов (жидкого каучука, пластификаторов, стабилизаторов), с последующим интенсивным перемешиванием смеси, нанесение полученного раствора на ткань, трикотажное полотно и другие материалы. Далее идет тепловая обработка материала при 100-180 °С до отвердения раствора и придание покрытию ворсистости. В этом случае количество ТИРП составляет более 15 массовых частей на 100 массовых частей раствора винилхлоридной смолы. Полученная искусственная кожа характеризуется превосходными морозостойкостью и мягкостью. Ее применяют для изготовления одежды, перчаток.
ТИРП применяется в качестве основного ингредиента резиновых смесей. Например, из резинового порошка формуют листы методом компрессионного формования при 100-250 °С под давлением более 10 кгс/см2 без использования других ингредиентов, а также при добавлении 0,3-3 массовых частей (на 100 массовых частей крошки) ускорителя вулканизации, 0,5-4 массовых частей стеариновой кислоты с последующим формованием смеси при повышенных температуре и давлении. Полученные резиновые листы могут быть использованы при изготовлении звуконепроницаемых стен, полов, покрытий.
Для улучшения технологических свойств резиновых смесей, снижения себестоимости и потребления энергии (обычно на 20-40 %) в них вводится ТИРП с величиной частиц менее 0,2 мм, получаемый по специально разработанной технологии. Свойства резиновых смесей остаются на уровне смесей без добавок даже при высокой степени наполнения. В Германии используют резиновый порошок из утильных шин с размерами частиц около 0,5 мм, предварительно обработанный специальным составом на вальцах, в качестве наполнителя резиновых смесей. При введении 20 % порошка наблюдается рост модуля, эластичности, прочности, сопротивления раздиру.
Возможно применение тонкодисперсного резинового порошка в протекторных резиновых смесях как при изготовлении, так и при восстановительном ремонте шин до 5 %. Так, например, введение в протекторные резины измельченного вулканизата с размером частиц около 0,3 мм практически не влияет на характеристики шин. Разработан сверхтонкий регенерат, представлявший собой тонкодисперсный порошок с размером частиц 0,02 мм. Процесс получения сверхтонкого регенерата осуществляется механическим измельчением вулканизатов при температуре окружающей среды без применения или с применением химических добавок, вызывавших девулканизацию или другие химические изменения. Корректировкой рецептуры, в частности, вулканизующей группы, удалось получить высокие физико-механические свойства протекторных резин при содержании порошка до 100-150 массовых частей на 100 массовых частей каучука.
Чеховский резинорегенератный и Невинномысский шиноремонтный заводы используют в протекторных резинах при восстановительном ремонте шин резиновый порошок размером до 0,5 мм в количестве до 5 массовых частей на 100 массовых частей каучука, получаемый доизмельчением отходов, образующихся при шероховке автопокрышек.
Одна из главных проблем при получении крошки и регенерата – проблема выбора наиболее эффективного и экономичного способа измельчения изношенных покрышек. Операция измельчения условно может быть разделена на две основные стадии:
1) предварительная резка покрышек с извлечением сердечников бортовых колец, бортовой проволоки;
2) измельчение материала в крошку с последующим разделением ее по фракциям для дальнейшего использования.
Для грубого измельчения использованных шин применяют прессовое оборудование; машины, работающие по принципу гильотинных ножниц; машины с ножевыми и роторными режущими устройствами; валковые измельчители; машины, снабженные иглофрезами; машины ударного действия. Практический интерес представляют машины с натяжением материала в месте реза.
Измельчение резины до состояния крошки производится абразивным истиранием, экструзионным измельчением, дробилками.
Эффективность механического дробления резины при обычных температурах зависит от скорости отделения тонкой фракции в процессе измельчения, надежности режущих устройств, приспособленности аппаратуры к специфическим свойствам измельчаемого материала.
Известен способ измельчения резин на валковом измельчителе с использованием поверхностно-активного вещества. Отношение скорости быстроходного валка к скорости тихоходного составляет 4:1, соотношение компонентов резина-сополимер составляет 100:0,2-0,6 (частей по сухому веществу). Производительность по крошке с частицами менее 1 мм равна 209-236 кг/ч.
Однако, несмотря на широкое распространение измельчения утильной резины покрышек механическим методом, он имеет ряд недостатков:
1) Форма частиц резины, получаемых описанным (механическим) способом абсолютно произвольна, а их поверхность рваная («лохматая»), что усиливает процесс окисления в условиях высоких температур, возникающих при размоле резины. При этом изменяются свойства исходного материала, что приводит к снижению качества получаемой резиновой крошки, и снижается возможность ее применения в высокотехнологичных резинотехнических производствах;
2) Исключается возможность 100 %-ного сепарирования резиновой крошки от остатков текстиля и металлического корда, даже при наличии специальных магнитных сепараторов и устройств типа «циклон». Это приводит к снижению качества получаемого продукта и к увеличению износа оборудования из-за наличия металлических включений;
3) Имеет место значительный износ режущего и размалывающего оборудования (ножей, шнеков и т.п.), что приводит к дополнительным затратам на его обслуживание;
4) Как следует из физикохимии дробления резины, процесс не сопровождается выделением в окружающую среду газообразных веществ, однако при измельчении покрышек в атмосферу выделяется большое количество взвешенных веществ - частиц резиновой пыли, а при измельчении покрышек с текстильным кордом выделяется еще и текстильная пыль.
В последнее время уделяется большое внимание разработке методов тонкодисперсного измельчения резин при повышенных и пониженных температурах. Криогенная технология имеет ряд преимуществ перед высокотемпературной переработкой: она более эффективна и менее энергоемка, к тому же под влиянием низких температур облегчается отделение от резины металлокорда.
Автомобильные покрышки замораживаются до состояния хрупкости и затем измельчаются с последующим отделением металлического корда и текстиля. Метод обладает наивысшей производительностью, является экологически чистым. Эта технология позволяет получать резиновую крошку с заданными параметрами и гладкой поверхностью частиц, что значительно улучшает ее физико-химические свойства и позволяет использовать для изготовления новых резиновых изделий с количеством включения до 80 %.
Так как коэффициенты термического расширения металлокорда и резины существенно различаются, то при замораживании покрышки связи между ними ослабевают, и в резине появляются локальные концентраторы напряжения, способствующие ее разрушению.
Созданы криоохладитель и приспособление для криогенного дробления покрышек, устанавливаемых на ковочном молоте. За один прием дробления (10-15 с) полностью удаляется неразрушенный металлокорд и отделяется 75 % резины, не засоренной текстильным и металлокордом. Охлаждение происходит до минус 120 °С; расход жидкого азота составляет 0,3 кг/на 1 кг исходного продукта; энергозатраты – 3,5 кВт/т материала.
Существуют технология и установки для переработки шин методом взрывоциркуляционного измельчения. Технология, называемая «РУНА», позволяет перерабатывать в тонкодисперсный резиновый порошок металлокордные покрышки различных типов и размеров, в том числе от большегрузных самосвалов. Технология включает разрушение предварительно охлажденных до температуры минус (70-80) °С автомобильных покрышек под действием взрыва во взрывоциркуляторе, представляющем собой бронекамеру специальной конструкции.
В последнее время развивается технология криоскопического измельчения резин до тонкодисперсного состояния двумя путями:
1) прохождением потока низкотемпературного газа (предлагается жидкий азот) совместно с гранулами через специальное сходящееся-расходящееся сопло при давлении на входе, превышающем давление на выходе в 10 раз;
2) ударением высокоскоростного потока о твердую поверхность.
Наиболее благоприятной средой для охлаждения является жидкий азот. Однако существуют расхождения в значениях температур: согласно одним данным температура стеклования резин, составляет минус (70-80) °С, а по другим данным – до минус (120-140) °С.
Возможно комбинирование криогенного дробления с другими методами, например, с импульсной нагрузкой, создаваемой взрывом заряда взрывчатого вещества.
Криодеструкция обладает и рядом недостатков. Во всех известных установках для охлаждения резины используется жидкий азот. Сложность его доставки, хранения, высокая стоимость и высокие энергозатраты на его производство являются основными причинами, сдерживающими в настоящее время внедрение низкотемпературной технологии.
Для получения температур в диапазоне от минус 80 до минус 120 °С более эффективными являются турбохолодильные машины. В этом диапазоне температур применение турбохолодильных машин позволяет снизить себестоимость получения холода в 3-4 раза, а удельные энергозатраты в 2-3 раза по сравнению с процессом, где применяется жидкий азот. Результаты экспериментальных работ подтвердили перспективность применения турбохолодильных машин для охлаждения шинной резины в технологическом процессе переработки изношенных шин. Был разработан технологический процесс, в котором используется производимое промышленностью Украины и России оборудование. Оборудование предлагаемой технологической схемы компактно и позволяет получить резиновую крошку с размером частиц от 0,2 мм до 1,0 мм.
Переработка шин в хрупком, как при криодеструкции, состоянии весьма удобна, но затраты на предварительное охлаждение весьма велики. Уже высказывалось мнение о том, что хрупкое разрушение эластичных материалов возможно и при комнатной температуре, если скорость нагружения будет достаточно высокой. Луч квантового генератора, если он имеет достаточную энергию, попадая в жидкую среду, приводит к последствиям, которые определяются нелинейными эффектами поглощения, что в ряде случаев может привести к возникновению сильных гидравлических волн с большой амплитудой давления.
Для измельчения изношенных шин используют и энергию взрыва. Вышедшие из употребления автомобильные шины взрывают в ограниченном пространстве при добавлении от 1,5 до 20 % взрывчатого вещества с положительным кислородным балансом в присутствии 0,4-1,5 % СаС2; 1-25 % Са(ОН)2; 0-0,6 % пороха для дробления камня и 0-60 % воды. Этот способ резко снижает расход электроэнергии и воды на дробление.
Вопрос о возможности извлечения металлической арматуры и текстильного корда из изношенных покрышек остается весьма актуальным. Разработано устройство, снабженное ножами с закрепленными на хвостовиках штангами, захватами. При работе надрезающие кромки захватов прорезают резину бортового кольца до соприкосновения с металлической арматурой и захватывают ее, нагревают металлическую арматуру до оплавления близлежащих слоев резины, вырезают арматуру из покрышки и затем ножами захватов разрезают вырванную арматуру.
Возможно извлечение металлической арматуры из резаных покрышек, при котором покрышку с арматурой помещают в высокочастотное электромагнитное поле, локальный участок покрышки зажимают между двумя парами прижимных валков. Нагрев осуществляется между ними до температуры пиролиза близлежащих к арматуре слоев резины и образования пиролизного вздутия. Затем придают покрышке вращение относительно валков и отделяют арматуру от покрышки.
Так как процесс измельчения амортизованных шин без охлаждения очень энергоемок (на измельчение 1 т шин расходуется от 800 до 1500 кВт-ч), то необходимы поиски других путей измельчения шин. Одним из них может быть использование кумулятивных ножей.
Альтернативным путем устранения эластомеров может служить способ, по которому пришедшие в негодность продукты разлагаются химическим способом на исходное сырье, а из последнего вновь изготавливаются новые продукты (термический распад в отсутствие воздуха при высокой температуре).
|
|
Биохимия спиртового брожения: Основу технологии получения пива составляет спиртовое брожение, - при котором сахар превращается...
Адаптации растений и животных к жизни в горах: Большое значение для жизни организмов в горах имеют степень расчленения, крутизна и экспозиционные различия склонов...
Таксономические единицы (категории) растений: Каждая система классификации состоит из определённых соподчиненных друг другу...
Индивидуальные и групповые автопоилки: для животных. Схемы и конструкции...
© cyberpedia.su 2017-2024 - Не является автором материалов. Исключительное право сохранено за автором текста.
Если вы не хотите, чтобы данный материал был у нас на сайте, перейдите по ссылке: Нарушение авторских прав. Мы поможем в написании вашей работы!