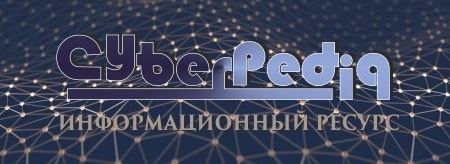
История развития хранилищ для нефти: Первые склады нефти появились в XVII веке. Они представляли собой землянные ямы-амбара глубиной 4…5 м...
Типы оградительных сооружений в морском порту: По расположению оградительных сооружений в плане различают волноломы, обе оконечности...
Топ:
Техника безопасности при работе на пароконвектомате: К обслуживанию пароконвектомата допускаются лица, прошедшие технический минимум по эксплуатации оборудования...
Оснащения врачебно-сестринской бригады.
Комплексной системы оценки состояния охраны труда на производственном объекте (КСОТ-П): Цели и задачи Комплексной системы оценки состояния охраны труда и определению факторов рисков по охране труда...
Интересное:
Как мы говорим и как мы слушаем: общение можно сравнить с огромным зонтиком, под которым скрыто все...
Мероприятия для защиты от морозного пучения грунтов: Инженерная защита от морозного (криогенного) пучения грунтов необходима для легких малоэтажных зданий и других сооружений...
Влияние предпринимательской среды на эффективное функционирование предприятия: Предпринимательская среда – это совокупность внешних и внутренних факторов, оказывающих влияние на функционирование фирмы...
Дисциплины:
![]() |
![]() |
5.00
из
|
Заказать работу |
Содержание книги
Поиск на нашем сайте
|
|
И перспективных методов решения проблемы ТБО
Наиболее распространенными методами решения проблемы отходов являются: термические методы, компостирование и захоронение. В таблице 5.4 представлено соотношение различных методов обезвреживания и переработки их в развитых странах.
Как видно из табл. 5.4, преобладающее количество ТБО (около 97%) вывозится для захоронения на загородных полигонах, большинство которых не имеют необходимой технической документации и эксплуатируются без соблюдения экологических требований и нормативов. Около 70% полигонов эксплуатируются сверхнормативно. Часть ТБО оседает на территории и за чертой города в местах неорганизованного складирования - свалках, которые представляют собой серьезную опасность для окружающей среды и здоровья населения. Состав отходов, попадающих на свалки, зачастую не контролируется, и в связи с этим на свалки могут вывозиться высокотоксичные промышленные отходы.
Небольшая часть ТБО в России (2,3 %) обезвреживается термическими методами. Большинство заводов по сжиганию отходов, функционирующих на территории России, не отвечают в полной мере современным экологическим стандартам и являются источниками эмиссии широкого спектра загрязняющих веществ. Оставшаяся часть ТБО (1%) попадает на предприятия по производству компоста.
Таблица 5.4. Соотношение различных методов обезвреживания
И переработки твердых бытовых отходов
Страна | Процент от общего накопления ТБО | |||
захоронение | термическая деструкция | компостиро- вание | прочие методы | |
Россия | 97,0 | 2,3 | 0,7 | - |
Венгрия | 92,0 | 8,0 | - | - |
Дания | 17,5 | 80,0 | 0,5 | 2,0 |
Италия | 67,0 | 18,0 | 10,0 | 5,0 |
Канада | 80,0 | 19,0 | 1,0 | - |
Франция | 46,4 | 41,0 | 12,0 | 0,9 |
ФРГ | 61,0 | 34,0 | 5,0 | - |
Швейцария | 4,0 | 80,0 | 10,0 | 6,0 |
Швеция | 34,0 | 56,0 | 9,9 | 0,1 |
Япония | 27,0 | 70,0 | 0,3 | 2,7 |
Термические методы обезвреживания ТБО. Наиболее отработанным и распространенным в мировой практике методом обезвреживания ТБО является их сжигание. Первое «мусоросжигательное заведение» было построено еще в 1870 году близ Лондона. В нашей стране первый мусоросжигательный завод был введен в действие только в 1972 году.
С середины 70-х годов XX века (в разгар мирового энергетического кризиса) на твердые бытовые отходы стали смотреть как на дополнительный сырьевой источник энергии: тепло отходящих газов, образующихся при сжигании мусора, можно утилизировать (пять тонн мусора равны тонне условного топлива). Это привело к интенсивному развитию технологий по термическому обезвреживанию бытовых отходов на мусоросжигающих установках и заводах. В настоящее время создано нескольких типов таких установок, отличающихся условиями и режимами сжигания, технологий сепарации и подготовки мусора к сжиганию, очистки отходящих газов, а также переработки твердых отходов сжигания.
|
В зависимости от температуры процесса все методы термической переработки ТБО, нашедшие промышленное применение или прошедшие опытную апробацию, можно разделить на две большие группы: процессы переработки при температурах ниже температуры плавления шлака и процессы переработки при температурах выше температуры плавления шлака (табл. 5.5), более 1300 °С.
Таблица 5.5. Классификация методов термической переработки ТБО
Температурный уровень процесса | Принципиальный характер процесса |
1. Термические процессы при температурах ниже температуры плавления шлака | 1. Слоевое сжигание с принудительным перемешиванием материала |
2. Сжигание в кипящем слое | |
2. Термические процессы при температурах выше температуры плавления шлака | 1. Сжигание в слое шлакового расплава |
2. Сжигание в плотном слое кускового материала и шлаковом расплаве без принудительного перемешивания и перемещения материала | |
3. Комбинированные процессы |
В термических процессах, осуществляемых при температурах ниже температуры плавления шлака, используются следующие типы печей: решетчатые печи, вращающиеся барабанные печи и печи кипящего слоя.
Метод слоевого сжигания в решетчатых печах является наиболее распространенным и изученным. При таком способе обезвреживания сжиганию подвергают все поступающие на завод отходы без какой-либо их предварительной подготовки или обработки. Он позволяет значительно экономить земельные площади по сравнению с таковыми, отводимыми под полигоны. При этом методе, помимо целей обезвреживания отходов, возможно получение тепловой и электрической энергии, сокращение до минимума расстояния между местом сбора ТБО и мусоросжигательным заводом.
|
Эффективность слоевого сжигания отходов зависит в основном от конструктивных решений топки и колосниковой решетки. В печах решетчатого типа широкое применение нашли следующие типы колосниковых решеток: поступательно переталкивающие, обратно переталкивающие и решетки валкового типа. Наиболее эффективными вариантами конструктивного решения системы топка-решетка являются:
· система с прямым потоком газов в топочном пространстве, оптимальная для сжигания сухих отходов с высокой теплотворной способностью;
· система с обратным по отношению к перемещаемому материалу потоком газов, оптимальная для сжигания влажных отходов с низкой теплотворной способностью;
· система со средним потоком газов (компромиссный вариант), оптимальная для сжигания отходов переменного состава и влажности.
Барабанные вращающиеся печи для сжигания исходных (неподготовленных) ТБО применяют очень редко, чаще эти печи используют для сжигания специфичных (например, больничных) отходов, а также жидких и пастообразных промышленных отходов, обладающих абразивным действием.
Барабанные печи устанавливают с небольшим наклоном в направлении движения отходов. Со стороны загрузки подают отходы, воздух и топливо, шлак и золу выгружают с противоположного конца печи. Ранее такие печи часто использовались с целью дожигания продуктов сжигания ТБО на колосниковых решетках. Помимо дожигания несгоревшей части отходов, в барабанных печах происходит дробление образующегося при этом шлака, который с помощью системы шлакоудаления подают на пластинчатый конвейер и далее направляют в шлаковое отделение.
В печах с кипящим слоем термическую деструкцию компонентов ТБО осуществляют за счет создания двухфазной системы «твердое – газ» путем превращения слоя отходов в «псевдожидкость». Это достигается за счет действия динамического напора восходящего потока газа, достаточного для поддержания твердых частиц во взвешенном состоянии. Слой отходов в данном типе печей напоминает кипящую жидкость, что и дало название печам данного типа. Такая технология получила наибольшее распространение в Японии.
Печи кипящего слоя, по сравнению с решетчатыми, обеспечивают наилучший режим теплопередачи и перемешивания обрабатываемого материала. Они обладают более простой конструкцией ввиду отсутствия в них движущих частей. С другой стороны, печи данного типа накладывают определенные ограничения на гранулометрический и морфологический состав ТБО.
В зависимости от характера псевдоожижения различают три модификации кипящего слоя: стационарный, вихревой и циркулирующий. В качестве теплоносителя в печах кипящего слоя обычно используется тонкозернистый песок, частицы которого создают большую поверхность нагрева.
|
После разогревания песка начинают подачу ТБО в кипящий слой, где последние смешиваются с песком. В процессе движения в кипящем слое отходы истираются частицами песка и начинают гореть. Тепло, выделяющееся в процессе горения ТБО, обеспечивает поддержание песка в горячем состоянии, что позволяет работать печам данного типа без подвода дополнительного топлива для обеспечения режима горения.
Вихревой кипящий слой обычно формируют с помощью одной или нескольких пластин, зафиксированных с наклоном по отношению к желобу системы шлакоудаления. Под действием направленных потоков воздуха происходит принудительное эллиптическое движение кипящего слоя.
В печах для сжигания отходов в циркулирующем кипящем слое в технологический процесс вводится циклон, с помощью которого материал постоянно циркулирует в системе печь-циклон и по всей высоте печи поддерживается равномерная температура.
На смену традиционным процессам термической деструкции постепенно приходят методы высокотемпературного обезвреживания ТБО. Это связано с тем, что для снижения количества отходящих газов и образующихся шлаков необходимо обеспечить температуру процесса выше температуры плавления шлаков (около 1300 °С), что требует, как правило, либо использования кислорода, либо подвода дополнительной энергии.
В настоящее время в мировой практике апробирован ряд методов высокотемпературной переработки ТБО.
Сжигание в слое шлакового расплава осуществляется при снижении в составе дутьевого воздуха инертных компонентов. Это связано с тем, что на нагрев инертных компонентов дутьевого воздуха требуется большое количество энергии. В начале 90-х годов в России для высокотемпературного обезвреживания ТБО были предложены металлургические печи Ванюкова. Сжигание в них осуществляют в слое находящегося в ванне печи барботируемого шлакового расплава (образуется из загружаемых в печь золошлаковых отходов ТЭЦ). Сбрасываемые в ванну ТБО погружаются в интенсивно перемешиваемый вспененный расплав. Барботаж расплава осуществляют с помощью окислительного кислородно-воздушного дутья, подаваемого через фурмы в нижней части боковых стенок печи (ниже уровня расплава), для дожигания дымовых газов предусмотрена подача дутья через ряд верхних фурм (выше уровня расплава). Минеральная часть отходов растворяется в шлаке, а металлические компоненты расплавляются.
Сжигание с использованием электрошлакового расплава является электротермическим методом, который наиболее целесообразно применять для обезвреживания шлаков, образующихся при низкотемпературном сжигании ТБО. Технологический процесс осуществляют при помощи электроплавильной печи, выполненной в виде металлического кожуха, футерованного изнутри огнеупорным кирпичом. Температура жидкой шлаковой ванны составляет 1400-1500 °С. Разогрев шлака в электропечи осуществляют с помощью графитовых электродов (обычно трех), подключенных к источнику питания. Шлак выгружают из электропечи периодически.
|
Преимуществами электроплавки шлаков являются отсутствие необходимости подачи дутьевого воздуха и простота поддержания температуры процесса. Основным недостатком данного метода является большой расход электроэнергии (около 100 кВт×ч /1 т) и относительно высоким расходом графитовых электродов (10 кг/1000 кВт×ч).
Пиролизом отходов принято называть процессы термического разложения топлива без доступа окислителя. При пиролизе макромолекулярных органических веществ происходит разложение больших молекул на мелкие. Эти процессы распада молекул имеют сложный механизм и окончательно не выяснены. Очень сложен также и состав продуктов реакций, протекающих в данных условиях пиролиза.
Соотношение количеств получаемых продуктов (газообразных, жидких и твердых) и их состав зависят от условий пиролиза и состава сырья. Особое влияние на процесс оказывают скорость нагревания и температура, с повышением которых значительно увеличивается выход газа (растет содержание водорода) и жидких продуктов. В зависимости от температуры методы пиролиза подразделяют на низкотемпературные (до 550 °С), характеризующиеся минимальным выходом газа, максимальным количеством смол, масел и твердых остатков; среднетемпературные (до 800 °С), при которых увеличивается выход газа, уменьшается количество смол и масел; и высокотемпературные (свыше 800 °С), при которых количество образующихся газов максимально, а смолообразных продуктов сведено к минимуму.
Благодаря восстановительной атмосфере атомы серы, хлора, кислорода и азота переходят в пиролизном газе в сероводород, хлористый водород, воду и аммиак. Пиролизный газ после очистки представляет собой высококачественный отопительный газ, его можно использовать на угольных ТЭС, а пиролизное масло – сырье для химической промышленности. Пиролиз – один из наименее требовательных к исходному сырью и наиболее доступных в финансовом плане методов.
Комбинированные методы обезвреживания ТБО связаны с осуществлением различных сочетаний процессов пиролиза, сжигания и газификации отходов.
Так, технологический процесс немецкой фирмы «Siemens KWU», функционирующий по схеме «пиролиз-сжигание», включает измельчение отходов; пиролиз отходов во вращающейся барабанной печи, снабженной обогреваемыми внутренними лопастями, с образованием пиролизного газа и пиролитического твердого остатка (смесь углерода и минеральных компонентов); выделение из пиролитического остатка металлов и минеральных компонентов (камни, стекло и пр.) грохочением; отделение черных и цветных металлов от минеральных компонентов; измельчение углеродистого остатка на угольной мельнице до крупности менее 100 мкм; совместное сжигание при небольшом избытке воздуха, угольной пыли и пиролизного газа при температуре 1300 °С с образованием расплава шлака (выход шлака от 12 до 13 %); утилизацию тепла дымовых газов в котле-утилизаторе и выработку электроэнергии в турбогенераторе.
|
Технологическая схема метода, разработанного французской фирмой «Noell», во многом аналогична схеме, рассмотренной выше. Основное отличие от процесса, разработанного фирмой «Siemens KWU», состоит в том, что продукт последней операции под большим давлением инжектируют в верхнюю часть реактора газификации, куда вводят также технический кислород и раздельно подают остальные продукты пиролиза: охлажденный пирогаз, отделенный от пиролизных масел и воды, а также жидкие продукты пиролиза (масла, вода).
Жидкий шлак и пиролизный газ выводят из зоны реакции через разгрузочное отверстие. В зоне охлаждения, находящейся ниже реакционной камеры, газ и шлак совместно охлаждают холодной водой, впрыскиваемой через форсунки. Газ выводят из зоны охлаждения с температурой от 150 до 210 °С в зависимости от давления. Шлак охлаждают и в форме гранул удаляют через шлюзовой затвор.
По технологии, разработанной шведской фирмой «Thermoselect», исходные ТБО подаются на гидравлический пресс. Далее спрессованные отходы и отжатая из них вода попадают в горизонтальный канал, где они подвергаются пиролизу при температуре 600°С в печи тоннельного типа длиной 15 м. Объем спрессованных отходов очень мал, за счет чего достигается хорошая теплопроводность массы отходов и имеется полный контакт со стенками канала. Органическая составляющая отходов разлагается на оксид углерода, углекислый газ, водород, смесь простейших углеводородов и твердый углерод. Брикеты твердого углерода, а также образовавшиеся в канале газообразные продукты реакций разложения, подаются в реактор газификации вертикального типа. В качестве газифицирующего агента используют кислород. Газификация с образованием оксида углерода происходит в нижней части реактора при контакте углеродистого остатка с кислородом. Температура при этом повышается до 2000 °С, и образовавшийся расплав поступает в шлаковую ванну, где разделяется на два слоя – металлический и собственно шлаковый.
Металлический расплав выносится в реактор-гомогенизатор, а затем подвергается грануляции в водяной ванне, минеральный расплав удаляется из зоны реакции отдельно от него. Стекловидный гранулят минерального расплава со свойствами, идентичными свойствам естественного минерала базальта, может найти применение в промышленности, например, при строительстве дорог; металлический гранулят подлежит утилизации в тех отраслях промышленности, где не предъявляются высокие требования к качеству металла.
Сравнивая термические методы обезвреживания ТБО, можно отметить, что к основным достоинствам этих методов относится:
· существенное сокращение объема и массы отходов;
· возможность обезвреживания несортированных отходов;
· возможность использования тепла, образующегося при обезвреживании отходов.
Основным недостатком предприятий, занимающихся термическим обезвреживанием ТБО, является негативное воздействие дымовых газов на окружающую среду. Установлено, что при в ходе термической деструкции ТБО в печи интенсивно протекают различного рода химические реакции, в результате которых образуется большое количество загрязняющих веществ, которые входят как в состав дымовых газов, так и в состав шлака. К ним относятся соединения тяжелых металлов, другие токсичные вещества (НС1, HF, NO2, SO2).
Отношение к проблеме сжигания ТБО особенно обострилось в 80-е годы после установления факта образования в процессах переработки мусора высокотоксичных экотоксикантов типа диоксинов.
Первые публикации о диоксинах относятся к 1956-1957 гг., однако основные сведения появились в 60-е гг., когда были опубликованы многочисленные научные данные, касающиеся большинства важнейших аспектов диоксиновой проблемы.
Основными источниками диоксинов являются: производство пестицидов, технических продуктов, железа, стали и др. металлов, целлюлозы, хлора, моющих средств, а также выбросы при сжигании ТБО, больничных отходов, промышленных отходов; выбросы автомобилей и сбросы сточных вод.
Представления об условиях образования диоксинов и их распада претерпели значительную эволюцию. Первоначально считалось, что необратимое разложение этих хлорорганических соединений происходит при температурах, несколько превышающих 750 °С, однако в дальнейшем было показано, что даже при 1000 °С их терморазложение – процесс обратимый.
Наличие в составе дымовых газов высокотоксичных загрязняющих веществ требует разработки новых и совершенствования уже функционирующих систем газоочистки.
Недостатком заводов по сжиганию ТБО являются вторичные отходы: шлак, а также твердые продукты газоочистки. Для их захоронения чаще всего создаются специальные полигоны. В настоящее время большое внимание уделяется проблеме использования этих продуктов (например в асфальтовых смесях, при производстве технического стекла, гранулированных шлаков и облицовочной плитки).
Все вышеперечисленные меры природоохранного характера требуют дополнительных капитальных затрат и существенно снижают рентабельность предприятий по термическому обезвреживанию ТБО.
Компостирование ТБО. Компостирование твердых бытовых отходов представляет собой биохимический процесс переработки, способной к биотрансформации органической компоненты ТБО в компост – продукт, подобный гумусу.
Производство компоста из органических материалов было известно еще в глубокой древности. Из этих отходов формировали компостные ямы (кучи), которые дополнительно увлажняли в естественных условиях, в результате чего отходы превращались в гумусоподобное вещество коричневого цвета без неприятного запаха. Полученный компост вносили в почву с целью улучшения ее структуры и повышения плодородия.
Многовековой опыт применения компостирования для получения гумуса и обезвреживания нечистот и ТБО характерен для многих стран мира - Индии, Китая, стран Ближнего Востока, России, большинства европейских стран.
В России еще в XIX веке в приусадебном хозяйстве широко применяли компост из отходов животноводства, полеводства и ТБО. В начале XX века в России ТБО без предварительного измельчения закладывались в штабеля (бурты) и в естественных условиях при периодическом увлажнении и ворошении (перекапывании) превращались в компост.
Научный подход к процессу компостирования отходов предложил А. Howard в 30-х годах XX века. В его основе усовершенствование процесса Ивдора – полевого компостирования, традиционно применяемого в Индии, Китае, странах Ближнего Востока.
Процесс Ивдора предусматривает создание из органических отходов, легко поддающихся разложению (кухонные отбросы, фекалии, навоз животных, листья, ил из канализационных систем), компостных буртов (штабелей) на открытом воздухе высотой около 1,5 м. Компостируемая масса за период образования компоста дважды перелопачивается (ворошится).
В эти же годы ряд ученых в Европе и США проводили многочисленные разработки механизированных способов получения компоста. Один из первых механизированных процессов был предложен G. Beccari в 1920 году. Компост закладывали в биотермическую камеру, где в результате последовательного протекания аэробной и анаэробной стадии компостирования отходов обеспечивалась достаточно эффективная их переработка.
В 1949 г. Е. Eweson разработал непрерывный и полностью механизированный процесс аэробной переработки отходов в компост, позднее получивший название Эвесона-Фрейзера. Органические отходы предварительно измельчались, помещались в биологический барабан, где непрерывно перемешивались при передвижении от одного уровня к другому в условиях контакта с рециркулирующей через компостируемую массу активизированной двуокисью углерода, образующейся в процессе разложения органических материалов отходов.
В Дании была разработана новая технология компостирования, в основу которой положен принцип разделения ТБО по крупности и дробления в одном реакторе в сочетании с принудительной аэрацией, увлажнением и контролем температуры. Отходы помещались в медленно вращающийся барабан диаметром более 3 м, заполняя его на 2/3. Частичное заполнение обеспечивало всасывание воздуха, имеющиеся в концевой части барабана калиброванные отверстия позволяли разделять отходы по крупности.
В семидесятых годах в СССР были разработаны технологии промышленных методов получения компоста и началось строительство нескольких заводов по переработке ТБО в компост на основе сочетания отечественных и зарубежных технологий. Эти заводы работают в настоящее время под Москвой, Санкт-Петербургом, Минском и в других городах.
В большинстве европейских стран в последние десятилетия большое внимание уделяется проблеме внедрения системы индивидуального компостирования кухонных отходов, растительных остатков, отходов полеводства и садоводства населением на приусадебных и индивидуальных садовых участках. Разработаны и внедрены различные типы мелких компостных установок, индивидуальных дробилок, других устройств, обеспечивающих реализацию индивидуального компостирования.
В настоящее время в мире в основном используются два способа компостирования: микробиологический метод компостирования и вермикомпостирование.
Первый метод представляет собой метод биотермической переработки и обезвреживания ТБО, при котором происходит микробиологический биохимический распад органических веществ с превращением их в гумус. Протекающие при этом биохимические процессы приводят к саморазогреванию массы отходов до температуры, обеспечивающей обезвреживание патогенных микроорганизмов. Получаемый гумус используется в сельском хозяйстве для формирования и стабилизации почвенной структуры в качестве органического удобрения.
При компостировании ТБО помещаются в штабеля (бурты), кучи (полевое компостирование) или в различные виды реакторов - биобарабаны, биобашни (промышленное компостирование), где содержащиеся в отходах органические вещества при доступе кислорода воздуха интенсивно окисляются бактериями. Микрофлора разлагает биологически окисляемые органические вещества отходов до форм, легкорастворимых в воде и хорошо усваиваемых растениями.
Микробиологический процесс окисления органического вещества отходов при компостировании протекает в несколько фаз, и в нем принимают участие различные виды микроорганизмов, которые по отношению к температурным режимам компостируемой массы можно условно разделить на три группы:
· психрофилы (бактерии, плесневые грибы) – от 4 до 30 °С;
· мезофилы (бактерии, актиномицеты) – от 10 до 45 °С;
· термофилы (бактерии, актиномицеты, мезофильные споры) – от 45 до 65 °С. Отдельные виды термофилов могут выживать при температуре до 75 °С.
Условно можно выделить три фазы компостирования. Первая – подготовительная, мезофильная. В начале процесса компостируемая масса имеет температуру окружающего воздуха.
При положительных температурах наружного воздуха начинается размножение обычной психрофильной почвенной микрофлоры в компостируемой массе. При температурах выше 15 °С размножение микрофлоры становится интенсивным. При дыхании микробы поглощают только часть тепловой энергии, а большая ее часть освобождается. Чем выше энергетический потенциал питательных веществ, используемых микробными клетками, и скорость их размножения, тем больше высвобождается тепловой энергии и интенсивнее идет процесс разогревания компостируемой массы.
При достижении температуры компоста 25-30 °С в нем начинают усиленно размножаться мезофильные микробы. Мезофильная фаза сопровождается разложением органических веществ, ростом общей массы микроорганизмов.
Мезофильная фаза характеризуется окислением легко разлагающихся органических соединений, которые находятся в пищевых и растительных отходах (белков, углеводов, органических кислот). Параллельно с окислением и разрушением легко разлагающихся органических соединений идет синтез более сложных гуминовых соединений, которые являются одними из наиболее ценных в компосте.
Предварительная работа мезофилов готовит среду для термофильных микробов, которые начинают интенсивно размножаться при температурах от 42 до 45 °С. При повышении температуры на каждые 10 °С микробиологические процессы значительно ускоряются. Резко возрастают темпы и интенсивность разложения органических веществ. При переходе от мезофильной фазы к термофильной (вторая фаза компостирования) отмечается быстрое (лавинообразное) нарастание температуры от 42 до 70 °С.
При температуре выше 40 °С мезофильные микробы обычно гибнут и вытесняются термофильными.
При температурах выше 70 °С и по мере использования запасов питания начинается гибель термофилов. В этом же диапазоне температур происходит наибольшее отмирание патогенной микрофлоры.
По мере снижения температуры падает интенсивность биохимических трансформаций органических веществ и процесс опять входит в мезофильную фазу с постепенным затуханием (третья фаза компостирования).
Наступление третьей фазы свидетельствует о том, что все легко-окисляемые органические соединения уже окислены и термофильная микрофлора отмирает из-за отсутствия источников питания. Но в компостируемой массе еще остаются трудноокисляемые вещества типа лигнина, клетчатки, жиров. Вновь размножающаяся в этой фазе мезофильная микрофлора, обладающая высокоэффективными ферментами, способна разрушать эти стойкие соединения.
После завершения третьей фазы содержание органических веществ в компостируемой массе снижается на 18-26 %.
Длительность протекания и сложность оформления технологического процесса компостирования существенно зависит от многих факторов: размера частиц, влажности, температуры окружающего воздуха, качества отходов, видового состава популяций микро- и макрофлоры, рН среды, вида компостирования.
Влажность отходов должна составлять 75-85 %. Однако практически максимальное содержание влаги зависит от вида отходов. Например, для опилок и стружек – 75-90 %, для бумаги – 55-65 %, для кухонных отбросов – 50-55 % и т.д. Оптимальный диапазон рН для большинства бактерий находится в пределах от 6 до 7,5.
При вермикомпостировании используется способность некоторых видов почвенных червей перерабатывать в биогумус органическое вещество отходов, попадающих в почву. Внимание ученых и практиков с давних пор привлекают различные виды почвенных червей (и в особенности дождевые черви) как активный фактор быстрой переработки органических отходов в биогумус.
Дождевые черви проделывают ходы, которые улучшают воздушный и водный режим почвы или отходов; пропускают через свой кишечник землю (отходы); выделяют в почву (отходы) биологически активные вещества.
При средней массе дождевого червя 0,5 г и количестве особей на 1 кв. м около 400-600 на 1 га общее количество червей составляет 4-6 млн. экз. При такой плотности популяции червей суммарный объем ходов превышает 1,5 - 2,0 % от общего объема почвы.
За сутки червь пропускает через себя количество почвы (отходов), равное его массе. Таким образом, при плотности популяции 5000000 особей на 1 га за сутки она пропускает через себя 0,25 т земли (отходов). При активной деятельности в году около 200 дней общее количество перерабатываемой массы составит от 400 до 600 т/га. При переработке массы почвы черви не только интенсифицируют процессы разложения органики, но и избирательно влияют на микрофлору. Выделяемые ими антибиотики отрицательно влияют на патогенную микрофлору. Такую биологическую активность и производительность червей трудно переоценить.
Несмотря на очевидность важности использования червей для переработки органических отходов, первые хозяйства по развитию червей на отходах были созданы только в сороковых годах в США. Сначала червей разводили для получения наживки для рыбной ловли, а затем перешли на коммерческое производство вермикомпоста и биомассы червей, используемой в качестве кормовых добавок в птицеводстве и животноводстве.
В настоящее время в ряде стран за рубежом с большим коммерческим успехом работают многие фирмы, специализирующиеся на утилизации бытовых, сельскохозяйственных и промышленных отходов. Только в США работают около 1500 относительно крупных и множество мелких фирм, специализирующихся в получении вермикомпоста. Созданы крупные установки, способные перерабатывать до 150 т отходов в сутки.
В Италии вермикомпостирование получило распространение после 1976 года, когда туда была завезена специальная вермикультура – красный калифорнийский червь. В Дании разработана и внедрена технология переработки ТБО и некоторых видов промышленных отходов. ТБО сортируют с целью удаления металлического лома, дробят и увлажняют путем добавки жидкого осадка сточных вод городских систем канализации и укладывают в хорошо аэрируемые невысокие бурты. По мере оседания массы бурты наращивают до нужной высоты.
Промышленное применение вермикомпостирования в СССР было начато с конца восьмидесятых годов на Украине в Ивано-Франковской области, где были созданы ящичные технологии выращивания червей и переработки сельскохозяйственных отходов в биогумус и биомассу.
В ряде западных стран переработка ТБО состоит из трех основных процессов: сортировка отходов, собственно компостирование и сжигание (пиролиз) неутилизируемой части ТБО. В России ТБО практически не сортируются, получаемый компост не может быть использован в сельском хозяйстве: при его реализации возникают трудности из-за высокого содержания в нем солей тяжелых металлов, канцерогенных веществ, стекла. Поэтому возникает вопрос не только об экономической нецелесообразности функционирования подобных производств, но и о возможности загрязнения окружающей природной среды.
Выраженный сезонный характер сбыта требует больших площадей для складирования готового компоста в межсезонные периоды. Расходы на транспортировку компоста даже на относительно небольшие расстояния часто превышают его стоимость. Все эти факты свидетельствуют о том, что производство компоста из ТБО является малорентабельным и требует дополнительных источников финансирования со стороны государства.
|
|
Таксономические единицы (категории) растений: Каждая система классификации состоит из определённых соподчиненных друг другу...
Индивидуальные очистные сооружения: К классу индивидуальных очистных сооружений относят сооружения, пропускная способность которых...
Кормораздатчик мобильный электрифицированный: схема и процесс работы устройства...
Двойное оплодотворение у цветковых растений: Оплодотворение - это процесс слияния мужской и женской половых клеток с образованием зиготы...
© cyberpedia.su 2017-2024 - Не является автором материалов. Исключительное право сохранено за автором текста.
Если вы не хотите, чтобы данный материал был у нас на сайте, перейдите по ссылке: Нарушение авторских прав. Мы поможем в написании вашей работы!