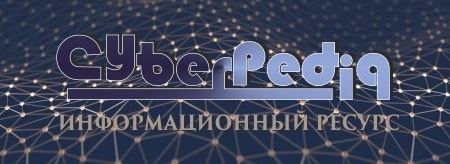
Типы оградительных сооружений в морском порту: По расположению оградительных сооружений в плане различают волноломы, обе оконечности...
Семя – орган полового размножения и расселения растений: наружи у семян имеется плотный покров – кожура...
Топ:
Выпускная квалификационная работа: Основная часть ВКР, как правило, состоит из двух-трех глав, каждая из которых, в свою очередь...
Эволюция кровеносной системы позвоночных животных: Биологическая эволюция – необратимый процесс исторического развития живой природы...
Комплексной системы оценки состояния охраны труда на производственном объекте (КСОТ-П): Цели и задачи Комплексной системы оценки состояния охраны труда и определению факторов рисков по охране труда...
Интересное:
Распространение рака на другие отдаленные от желудка органы: Характерных симптомов рака желудка не существует. Выраженные симптомы появляются, когда опухоль...
Влияние предпринимательской среды на эффективное функционирование предприятия: Предпринимательская среда – это совокупность внешних и внутренних факторов, оказывающих влияние на функционирование фирмы...
Инженерная защита территорий, зданий и сооружений от опасных геологических процессов: Изучение оползневых явлений, оценка устойчивости склонов и проектирование противооползневых сооружений — актуальнейшие задачи, стоящие перед отечественными...
Дисциплины:
![]() |
![]() |
5.00
из
|
Заказать работу |
|
|
На участок контроля-сортировки поступают детали разнородные по признакам, не связанным с механизмом обслуживания. В связи с этими признаками деталям предоставляется преимущество на контроль-сборку. Для того чтобы отличить детали по степени "важности", можно приписать каждой группе деталей приоритетный индекс (номер) i (), где I обозначает самую высшую степень важности, а S -самую низкую, и производить выбор деталей на контроль-сортировку в соответствии с приоритетным индексом.
В системах с приоритетами применяются те или иные правила освобождения канала. Соответствующее такой ситуации правило может предусматривать следующие альтернативы: а) обслуживание доводится до конца; б) обслуживание прерывается при поступлении требования с более высоким приоритетом.
На функционирование участка контроля-сортировки эти правила могут существенно влиять, если выбор контролируемого параметра случаен. Контроль может прерываться, не обнаружив деталь с критическим дефектом. Критический дефект по ГОСТ 17102-96 - это дефект, при наличии которого использование продукции по назначению практически невозможно или исключается в соответствии с требованиями безопасности. При дефектации деталей по рациональной стратегии эти правила не оказывают существенного влияния.
Пусть на участок контроля-сортировки поступает S различных потоков деталей. Причем поток деталей i -го типа имеет параметр . Если через
обозначить вероятность контроля детали i -го типа, то в качестве критерия эффективности процесса дефектации деталей S типов целесообразно принять показатель
(25)
где d - “важность" детали i -го типа, или эффект его контроля;
|
Q - абсолютная пропускная способность участка контроля-сортировки по деталям i -го типа;
- относительная пропускная способность участка по деталям i -го типа.
В приведенной формуле критерий G, очевидно, следует максимизировать. Как видно из этой формулы, от последовательности приоритетов деталей на контроль-сортировку зависят лишь вероятности . Поэтому целью исследований является такая ранжировка деталей, при которой последовательности
доставляют критерию G максимум.
Время контроля-сортировки деталей i -го числа показательное с параметром μi. Детали пронумерованы так, что детали i -го типа имеют ранг и обладают соответствующим этому рангу приоритетом, в соответствии c которым при поступлении на участок они немедленно начинают дефектоватъся, если в этот момент контролеры-дефектовщики были свободны или заняты контролем деталей низшего ранга принадлежащего потоку с номером (i>i+1). Если же в этот момент на участке дефектовались детали того или более высокого ранга, то вновь поступившая деталь получает отказ и не контролируется. "Важность" деталей всех рангов одинакова и равна d. Необходимо установить принцип, по которому должны быть проранжированы потоки деталей, чтобы полная эффективность контроля-сортировки, определенной критерием G, била максимальной. При этом оказывается., что независимо от параметра (li) входящих потоков деталей, максимум достигается при
. (26)
Это значит, что приоритет на контроль-сортировку должен предоставляться деталям, на дефектацию которых расходуется меньшее время, так как
(27)
. (28)
Такой выбор влияет на время пребывания требования в системе.
Поскольку время контроля, при прочих равных условиях, определяется количеством контролируемых параметров, то для деталей, требующих дефектации
. (30)
Пример: По техническим условиям на контроль-сортировку деталей коробки передач автомобиля ЗИЛ-130 дефектуется 29 деталей по 158 параметрам. Детали имеют различное количество контролируемых параметров (i =1,2….12). Разделим все детали, требующие дефектовки, на три группы:
|
I группа: картер - 9 контролируемых параметров; вал ведущий - 11, вал промежуточный -12, вал ведомый - 10;
(31)
II группа: крышка подшипника заднего хода – 2; ось блока шестерён – 3; крышка КП-4; ползун переключателя I- 8 передачи и заднего хода - 3; ползун переключателя 2-й и 3-й передачи - 3; ползун переключателя 4-й и 5-й передач - 3; рычаг переключателя 1-й передачи и заднего хода - 4; картер рычага переключателя передач - 3; крышка подшипника ведущего вала - 4.
(32)
III группа - все остальное (I6 деталей)
(33)
По результатам статистических исследований контроля-сортировки участок имеет следующие параметры, приведенные в (табл. 8).
Таблица 8
№ групп деталей | li | μi | Kсрi |
0.4 | 0.5 | ||
0.8 | |||
1.3 |
Закон распределения времени контроля этих деталей определяется соотношением, согласно которому статистическая оценка математического ожидания времени контроля деталей смешанного потока
(34)
Определим вероятность контроля детали для неупорядоченного (смешанного) потока
. (35)
Вероятность контроля для упорядоченного входящего потока по правилу ;
(36)
Вероятность контроля для входящего потока деталей по правилу равна
(37)
Из сравнения видно, что
.
Поскольку на практике поток неупорядочен, то сравниваем
и
.
Повышение эффективности функционирования участка контроля сортировки определяем по формуле
.
Эффект от ранжировки деталей зависит от разброса параметров μ. Чем больше разброс μ i или Ki, тем больший эффект дает ранжировка.
Так, при тех же параметрах при M1=1,M2=4,M3=8, вероятность контроля для неупорядоченного входного потока равна
,
.
Для упорядоченного потока вероятность контроля равна
. (38)
Полученные значения сравниваем с .
Методика определения потребного числа контролёров-дефектовщиков при заданной надежности распознавания состояния ремфонда
Каждый контролируемый параметр должен быть измерен с вероятностью не менее . Необходимо найти потребное число контролеров-дефектовщиков при заданной надёжности (
)оценки состояния детали.
|
Вероятность контроля параметра детали определяется по следующей формуле
(39)
где A среднее число проконтролированных параметров в единицу времени:
B - количество поступивших в единицу времени контролируемых параметров.
(40)
где μ - параметр контроля;
- вероятное число контролеров-дефектовщиков;
N(n) - объем места для деталей, ожидающих контроля-сортировки;
(41)
где ma - максимальное число контролируемых параметров у деталей, требующих дефектовки;
S - количество контролируемых параметров;
λ - параметр входящего потока деталей.
Очевидно, что
. (42)
Получить ответ непосредственно из этого выражения аналитически затруднительно. Поэтому поступаем так. Для ряда значений числа (n) контролеров-дефектовщиков вычисляют вероятности (Ркон) и заносят в таблицу 9.
Таблица 9
… | i | n | |||
Pкон (n) | Pкон (1) | Pкон (2) | … | Pкон (i) | Pкон (n) |
Очевидно, что любое n, удовлетворяющее неравенству
(43)
где - ближайшее значение Ркон (n), будет обеспечивать выполнение поставленного условия.
Пример: При поступлении деталей с параметром входящего потока l =2,5 дет/мин; параметром контроля μ = 6 пар/мин; параметром ухода деталей n = 0,1 дет/мин; объемом места для ожидающих деталей N = 60 в результате расчета получены следующие данные, приведенные в таблице 10.
Таблица 10
n | ||||||
Pкон (n) | 0.445 | 0.823 | 0.916 | 0.963 | 0.983 | 0.988 |
Если Pкон =0,98, то n =5 контролеров-дефектовщиков.
Составление отчета
Отчет по данной работе составляется по форме и должен содержать следующие сведения:
- основные элементы участка контроля-сортировки как СМО;
- сущность и принцип работы магнитного дефектоскопа;
- сущность и принцип работы контрольного автомата.
- результаты обработки статистических данных о потоках деталей и потоках измерении;
- свойства потоков деталей;
- показатели эффективности функционирования участка;
- заключение о эффективности функционирования участка;
- методы повышения эффективности функционирования участка;
- заключение и подпись преподавателя.
|
Порядок выполнения работы
Получить контролируемые детали.
Произвести хронометраж времени контроля детали скобами и пробками; штангенциркулем и микрометром; магнитный дефектоскопом; контрольным автоматом.
Определить параметр измерения контролируемого параметра.
Определить показатели эффективности функционирования участка контроля-сортировки.
Произвести замеры контролируемых параметров и определить коэффициент корреляции дефектов. Минимизировать число контролируемых параметров. Определить показатели эффективности функционирования участка контроля-сортировки.
Произвести оптимальное ранжирование потоков деталей. Определить показатели эффективности функционирования участка контроля-сортировки.
Определить потребное число контролеров-дефектовщиков.
Контрольные вопросы
1. Назвать и дать краткую характеристику основным элементам участка контроля-сортировки как системы массового обслуживания смешанного типа.
2. Типы системы массового обслуживания.
3. Свойства потоков.
4. Последовательность статистической обработки данных о материальных потоках деталей.
5. Показатели эффективности функционирования участка контроля сортировки.
6. Анализ процесса контроля-сортировки.
7. Какие методы повышения эффективности функционирования участка существуют.
8. Сущность минимизации числа контролируемых параметров.
9. Оптимальная ранжировка потоков.
10. Определение потребного числа контролеров-дефектовщиков.
Лабораторная работа №7
|
|
Архитектура электронного правительства: Единая архитектура – это методологический подход при создании системы управления государства, который строится...
Историки об Елизавете Петровне: Елизавета попала между двумя встречными культурными течениями, воспитывалась среди новых европейских веяний и преданий...
Археология об основании Рима: Новые раскопки проясняют и такой острый дискуссионный вопрос, как дата самого возникновения Рима...
История создания датчика движения: Первый прибор для обнаружения движения был изобретен немецким физиком Генрихом Герцем...
© cyberpedia.su 2017-2024 - Не является автором материалов. Исключительное право сохранено за автором текста.
Если вы не хотите, чтобы данный материал был у нас на сайте, перейдите по ссылке: Нарушение авторских прав. Мы поможем в написании вашей работы!