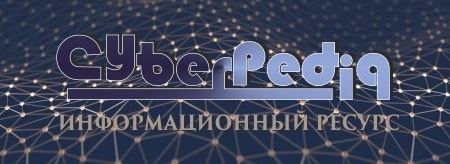
Опора деревянной одностоечной и способы укрепление угловых опор: Опоры ВЛ - конструкции, предназначенные для поддерживания проводов на необходимой высоте над землей, водой...
Индивидуальные и групповые автопоилки: для животных. Схемы и конструкции...
Топ:
Когда производится ограждение поезда, остановившегося на перегоне: Во всех случаях немедленно должно быть ограждено место препятствия для движения поездов на смежном пути двухпутного...
Отражение на счетах бухгалтерского учета процесса приобретения: Процесс заготовления представляет систему экономических событий, включающих приобретение организацией у поставщиков сырья...
История развития методов оптимизации: теорема Куна-Таккера, метод Лагранжа, роль выпуклости в оптимизации...
Интересное:
Аура как энергетическое поле: многослойную ауру человека можно представить себе подобным...
Влияние предпринимательской среды на эффективное функционирование предприятия: Предпринимательская среда – это совокупность внешних и внутренних факторов, оказывающих влияние на функционирование фирмы...
Национальное богатство страны и его составляющие: для оценки элементов национального богатства используются...
Дисциплины:
![]() |
![]() |
5.00
из
|
Заказать работу |
|
|
Резиновые и резино-металлические детали могут изготовляться путем вулканизации в формах и без форм. Если детали имеют сложную форму и их размеры должны быть строго определенными, то вулканизация таких деталей производится в формах, а изделия носят название формовых. Если к внешнему виду, форме, размерам деталей такие требования не предъявляются, то изготовление их может производиться без форм, а изделия в этом случае называются неформовыми.
Необходимо отметить, что резиновые и резино-металлические детали, несущие механическую нагрузку, особенно если эта нагрузка носит динамический характер, изготовляются, как правило, путем вулканизации в формах. Объясняется это тем, что однотипные детали машин должны иметь одни и те же строго определенные размеры, форму и механические характеристики. Поверхность деталей, испытывающих динамическую нагрузку, должна быть чистой и гладкой, так как шероховатости, раковины и другие дефекты наружных поверхностей, неизбежные при изготовлении неформовых деталей, способствуют развитию в них трещин, расслоений и других видов разрушения. Кроме того, гладкие наружные поверхности в меньшей степени подвержены химическому воздействию окружающей среды.
Изготовление формовых резиновых деталей состоит из следующих последовательных операций: приготовления резиновой смеси, заполнения формы смесью, вулканизации и отделки готовых деталей. Заполнение формы путем литья под давлением сокращает операции приготовления заготовки, обеспечивает хорошее заполнение формы и точно дозирует заготовку по объему и весу. Заполнение формы горячей резиновой смесью, имеющей температуру 80—100° С, сокращает время вулканизации изделий. Наиболее просто литье под давлением осуществляется при помощи плунжерного гидравлического пресса. Разогретая резиновая смесь из литьевого цилиндра под давлением напорного штока вытесняется в находящуюся под цилиндром форму. Заполнение формы смесью продолжается до тех пор, пока она не начинает выходить через специальное контрольное отверстие.
|
При изготовлении автомобильных резиновых деталей широко применяются продукты совместной полимеризации различных мономеров. Важнейшему представителю из них - сополимеру бутадиена со стиролом - присвоено обозначение СКС (стирольный). Он принадлежит к самым распространенным СК (доля его в мировом производстве всех СК и НК, взятых вместе, достигает 30 °%). Наиболее массовый сорт СКС, содержащий 30% стирола, имеет марку СКС-30. Резины на его базе хотя и уступают по эластичности, тепло- и морозостойкости резинам из НК, но зато превосходят их по износостойкости.
Кроме того, применяют стирольные каучуки СКМС (бута-диен-метилстирольный). Стирольные каучуки превосходят натуральные по износостойкости, но уступают по эластичности, тепло- и морозостойкости. При изготовлении автомобильных шин используют изопреновый (СКИ-3), который по своим свойствам близок к натуральному каучуку, и бутадиеновый (СКВ), отличающийся высокой износостойкостью. Высокой маслобензостой-костью отличаются хлорпреновый (наприт) и нитрильный (СКН) каучуки. Из этих каучуков изготавливают детали, контактирующие с нефтепродуктами. Бутилкаучук (сополимер изобутилена с изопреном) используют для изготовления камер и герметизирующего слоя бескамерных шин.
Ремонт типовых деталей.
Сведение в классы и группы деталей близких по своей конструктивной однородности имеет следующую цель. Упрощения разработки технологических процессов ремонта различных деталей и увеличения эффективности их применения.
Создано девять основных классов, в каждый из которых входят группы деталей.
|
Объединение деталей происходит на основание их конструкций. Смотри раздаточный материал.
41. Ремонт корпусных деталей на примере блока цилиндров.
К корпусным деталям относятся блок цилиндров, головка блока цилиндров и различные картеры – сцепление, коробки передач и т.д.
Характерным для этих деталей является наличие на них конструкторских, технологических и измерительных баз, привалочных плоскостей, отверстий в соответствии с точным располодением их осей под подшипники валов, плоскостей разъемов, резьбовых отверстий.
При эксплуатации в корпусных деталях бывают следующие дефекты: износ или повреждение баз, не соосность отверстий, трещины на стенках и плоскостях разъемов, поверхностях под подшипники и на опорных поверхностях, обломы шпилек, забитость, срыв или износ резьбы, коробление, забоины или деформация обработанных установочных, привалочных или стыковочных поверхностей, кавитационный износ отверстий, через которые проходит охлаждающая жидкость, выпадание заглушек водяной рубашки блока цилиндров и т.д.
Ремонт блока цилиндров следует начинать с восстановления технологических баз, удаления обломанных шпилек и болтов, повреждений резьбовых отверстий, а также устранения трещин и других повреждений, требующих применения сварочных операций, так как сварка может повлечь за собой коробление обработанных плоскостей деталей.
Коробление устраняется – шлифованием или фрезерованием. Износ внутренней поверхности устраняется:
Посадочные пояски в блоке цилиндров под гильзы растачивают под ремонтный размер.
Поверхности отверстий под толкатели клапанов развертываются под ремонтный размер.
Поверхности под вкладыши и втулки ремонтируются механической обработкой под ремонтный размер или методом наплавки, напыления металла, электроискровой обработкой, гальваническим наращиванием металла, полимерными покрытиями, дополнительными ремонтными деталями.
Трещины в корпусных деталях устраняются заваркой (пайкой) или применением полимерных клеевых композиций. Трещины предварительно ограничивают засверливанием по концам, а затем разделывают под угол 45 и 60 градусов по всей длине, тщательно очищая от загрязнений, масла и следов коррозии и заваривается (запаивается). После этого деталь проверяется на герметичность.
|
|
Папиллярные узоры пальцев рук - маркер спортивных способностей: дерматоглифические признаки формируются на 3-5 месяце беременности, не изменяются в течение жизни...
Адаптации растений и животных к жизни в горах: Большое значение для жизни организмов в горах имеют степень расчленения, крутизна и экспозиционные различия склонов...
Механическое удерживание земляных масс: Механическое удерживание земляных масс на склоне обеспечивают контрфорсными сооружениями различных конструкций...
История создания датчика движения: Первый прибор для обнаружения движения был изобретен немецким физиком Генрихом Герцем...
© cyberpedia.su 2017-2024 - Не является автором материалов. Исключительное право сохранено за автором текста.
Если вы не хотите, чтобы данный материал был у нас на сайте, перейдите по ссылке: Нарушение авторских прав. Мы поможем в написании вашей работы!