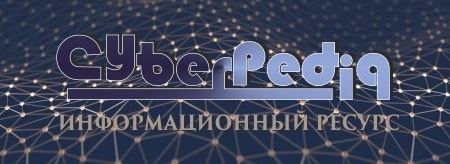
История развития пистолетов-пулеметов: Предпосылкой для возникновения пистолетов-пулеметов послужила давняя тенденция тяготения винтовок...
Археология об основании Рима: Новые раскопки проясняют и такой острый дискуссионный вопрос, как дата самого возникновения Рима...
Топ:
Устройство и оснащение процедурного кабинета: Решающая роль в обеспечении правильного лечения пациентов отводится процедурной медсестре...
Марксистская теория происхождения государства: По мнению Маркса и Энгельса, в основе развития общества, происходящих в нем изменений лежит...
Теоретическая значимость работы: Описание теоретической значимости (ценности) результатов исследования должно присутствовать во введении...
Интересное:
Финансовый рынок и его значение в управлении денежными потоками на современном этапе: любому предприятию для расширения производства и увеличения прибыли нужны...
Мероприятия для защиты от морозного пучения грунтов: Инженерная защита от морозного (криогенного) пучения грунтов необходима для легких малоэтажных зданий и других сооружений...
Национальное богатство страны и его составляющие: для оценки элементов национального богатства используются...
Дисциплины:
![]() |
![]() |
5.00
из
|
Заказать работу |
|
|
КУРСОВАЯ РАБОТА
«Производство и проектирование станочной оснастки для токарной, сверлильной обработки упора в технологическом процессе изготовления детали «Упор» с годовым объёмом выпуска 125000 шт.»
Выполнил: студент гр. 1614, Шахворостов М.В.
Научный руководитель: к.т.н., Епифанцев К.В
Дата сдачи:__________
Дата защиты:________
Оценка:_____________
Санкт-Петербург
ГОУ СПО «НЕВСКИЙ МАШИНОСТРОИТЕЛЬНЫЙ ТЕХНИКУМ»
ЗАДАНИЕ
на курсовое проектирование по специальности 151901 (ТМ)
студенту 1614 группы вечернего отделения
Шахворостов Максим Витальевич
«Производство и проектирование станочной оснастки для токарной, сверлильной обработки упора в технологическом процессе изготовления детали «Упор» с годовым объёмом выпуска 125000 шт.»
Введение
Introduction
Проектирование станочного приспособления
Анализ конструкции детали
Анализ технологического процесса, включая выполняемую операцию
Выбор элементов базирования и зажима заготовки
Схема нагрузок и расчет силы зажима
Определение размеров элементов зажима заготовки
Расчет станочного парка
Графическая компоновка приспособления
Конструкция и работа приспособления
Расчет погрешности базирования
Выводы по конструкции приспособления
Проектирование контрольной оснастки
Расчет исполнительных размеров
Конструкция и эксплуатация контрольного приспособления
Литература
FMEA
Дата выдачи задания «17» _________________ 2017г.
(число) (месяц)
Срок сдачи студентом «18» _________________ 2017г.
(число) (месяц)
Руководитель курсового проектирования ___ ______ преподаватель, к.т.н. К.В. Епифанцев
(подпись) (инициалы, фамилия)
|
Задание принял к исполнению ___________ «_____»___________2017г.
(подпись) (число) (месяц)
Содержание
Введение…………………………………………………………………..………….. Introduction……………………………………………………………………….…... 1. Проектирование станочного приспособления 1.1 Анализ конструкции детали………………………………………………..…… 1.2 Анализ технологического процесса и расчет станочного парка………….….. 2. Выбор элементов базирования и зажима заготовки и расчет погрешности… 2.1 Схема нагрузок при сверлильной операции………..……….………….……… 2.2 Схема нагрузок при токарной операции ……………………………….……… 2.3 Графическая компоновка приспособления……………………………..……… 2.4 Разработка специального инструмента необходимого для зажима заготовки при сверлильной обработке …………………….………………………………….. 2.5. Конструкция и работа приспособления …………………………….………… 2.6 Выводы по конструкции приспособления …………………………………...... 2.7 Техническое описание конструкции приспособления …………………..…… 2.8 Вывод по Курсовому проекту…………………………………..………………. 3. Литература…………………………………………………………………………. Приложение 1 «FMEA Анализ»………………………………………..………........ Приложение 2 «Чертеж детали Упор»……………………………….……………. Приложение 3 «Модель кондуктора»…………………………………...………… |
Введение
Под технологической оснасткой (ГОСТ3.1109—82) понимают средства технологического оснащения, дополняющие технологическое оборудование, для выполнения определенной части технологического процесса. Примерами технологической оснастки являются кондукторы, делительные головки, зажимные устройства, позволяющие одновременно обрабатывать несколько одинаковых деталей, уменьшать время на настройку оборудования.
Приспособление - это составная часть технологической оснастки, которая может быть самостоятельным элементом в контрольноизмерительных и некоторых сборочных операциях.
|
Если приспособление входит в состав обрабатывающей технологической системы, его называют станочным приспособлением, если оно входит в состав сборочной технологической системы, то его принято называть сборочным приспособлением.
Приспособления предназначены, главным образом, для установки объекта, в качестве которого выступает заготовка, деталь или сборочная единица. Установка включает в себя базирование объекта и его закрепление. Поэтому основными частями приспособления являются корпус, базирующие (установочные) и зажимные элементы.
Дополнительно приспособления могут выполнять следующие функции:
-обеспечивать направление режущего инструмента;
-служить базой для установки контрольно-измерительныхприборов;
-осуществлять механический или автоматический зажим объекта в приспособлении;
-увеличивать жесткость при установке базируемого объекта;
-изменять положение детали вместе с приспособлением. Использование приспособлений способствует повышению точности и производительности обработки, контроля деталей и сборки изделий, обеспечивает механизацию и автоматизацию технологических процессов, снижение квалификации работ, расширение технологических возможностей оборудования и повышение безопасности работ. Современное механосборочное производство располагает большим парком приспособлений, значительную часть которых составляют станочные приспособления.
В повышении качества изготовления деталей машин, их сборки и контроля важное значение имеет совершенствование технологической оснастки: создание высокопроизводительных конструкций станочных приспособлений, сокращение сроков их проектирования и изготовления, повышение качества и надежности, снижение трудоемкости изготовления, сокращение количества трудозатрат.
Решение этих задач должно быть направлено на повышение производительности труда станочников, слесарей-сборщиков, наладчиков и контролеров. Применение технологической оснастки снижает трудоемкость Т и себестоимость S изготовления сборки деталей (рис.1).
На рис. 1, а показана зависимость трудоемкости Т от коэффициента оснащенности К, под которым понимается отношение числа приспособлений к Числу операций обработки данной детали. Кривая 1 характеризуют одноместные приспособления ручного типа, а 2 — механизированные и многоместные приспособления.
|
Рис.1- Зависимость трудоемкости Т от коэффициента оснащенности К(а) и себестоимости обработки S от точности изготовления IT(б)
Станочные приспособления применяют для установки заготовок и инструмента на металлорежущие станки. Приспособления, связывающие со станком обрабатываемую заготовку, относят к приспособлениям для изготовления детали, а приспособления, связывающие со станком режущий инструмент, — к приспособлениям для инструмента.
Приспособления являются наиболее сложной и трудоемкой в изготовлении частью технологической оснастки.
Современная технологическая оснастка в виде станочных приспособлений для станков значительно повышает производительность труда за счет уменьшения вспомогательного облегчает условия труда операторов станков с ЧПУ, расширяет технологические возможности оборудования. времени на установку и закрепления заготовок, повышает точность обработки,
Приспособления для станков – кондукторы, поворотные делительные головки, оправки, гидроприжимы и установы должны иметь повышенную размерную точность. Погрешности базирования и закрепления, возникающие при установке заготовок в приспособления, должны быть сведены к минимуму. Для возможности использования полной мощности станка на черновых проходах и при обработке труднообрабатываемых материалов (титановые сплавы, нержавеющие, жаропрочные стали и другие) приспособления должны иметь повышенную жесткость конструкции.
Наиболее существенное сокращение вспомогательного времени при зажиме – разжиме заготовки достигается за счет использования гидро и пневмоцилиндров, именно данный вид оснастки мы применили для нашей заготовки, имеющий большой объём выпуска – 125 000 в год, что в пересчете на 247 рабочих дней лает нам 506 деталей в сутки. Операции при изготовлении детали «Упор» - токарная и сверлильная, станки с ЧПУ за короткое время смогут произвести обработку деталей, однако при достаточно долгом времени настройке станка при зажиме и установке детали, мы имеем риск не произвести нужного количества деталей в 2 рабочих смены. Следовательно, нам необходимо разработать оснастку, которая минимизировала бы время на установку, а, следовательно, позволила бы нам разработать технологический процесс с максимальной производительностью.
|
Introduction
Under technological equipment (ГОСТ3.1109-82)understand the means of technological equipment, complementing the technological equipment, to perform a specific part of the process. Examples of technological equipment are jigs, dividing head, clamping devices, allowing simultaneous processing of multiple identical parts, to reduce the time for equipment setup. The fixture is an integral part of tooling, which can be an independent element in the measuring and some Assembly operations. If the fixture is part of the manufacturing technological system, it is called machine fixture, if it is part of the Assembly of the technological system, it is called an Assembly fixture.
The most significant reduction in cycle time of the clamping – jaws of the workpiece is achieved through the use of hydraulic and pneumatic cylinders, it is this type of rig we used for our workpieces having a large volume of production – 125 000 a year, equivalent to 247 working days barking at us 506 parts per day. Operations in the manufacture of the part "Detend" - turning and boring, CNC machines for a short time will be able to handle the details, but in quite a long time setting up the machine in the clip and installing parts, we have the risk of not producing the required number of items in 2 working shifts. Therefore, we need to develop tooling which minimise installation time and, therefore, would allow us to develop a technological process with maximum productivity.
Анализ конструкции детали
Деталь “Упор” является основным элементом сборочной ”. Деталь «Упор» относится к классу валов. Для изготовления данной детали выбираем заготовку, получаемую прокатом, марка материала Ст45Х (ГОСТ 4543-71).
Рис.2 – Общий вид детали «Упор»
Рис. 3 – Фронтальная проекция детали «Упор»
Деталь симметрична относительно продольной оси, деталь имеет 4 ступени (Рис.2):
1 цилиндрическая: с длиной – 16мм и диаметром -12мм,
2 цилиндрическая: с длиной – 32мм и диаметром -14мм,
3 цилиндрическая: с длиной – 6мм и диаметром -34мм,
4 цилиндрическая: с длиной – 20мм и диаметром -20мм,
Также с правого торца имеется отверстие диаметром 16мм.
Между ступеней 1 и 2 имеется кольцевая фасонная проточка с диаметром – 0,5мм (Рис.2), между ступеней 2 и 3 имеется фасонная проточка с диаметром – 1мм, между ступеней 3 и 4 имеется фасонная проточка с диаметром – 0,5мм. В детали имеется глухое центральное отверстие. Шероховатость посадочных отверстий Ra = 6,3, шероховатость сквозных отверстий Ra = 1,6. Шероховатость цилиндрической ступени Ra = 3,2. Остальные поверхности имеют шероховатость Rz=20
Исходя из этого коэффициенты точности, шероховатости и унификации должны по величине соответствовать технологичной детали. Наличие теоретического контура ухудшает технологичность детали.
Рис. 4 – 3D модель детали «Упор»
Не выбираем штамповку потому что деталь простой формы, поэтому по экономической себестоимости выгоднее использовать прокат. Упор применяется при стопорении движение полозьев штампа и ограничении движения блоков направляющих на салазках исполнительного органа, также может быть использован для стопорения механизмов автоматики.
|
Рассмотрим хим. состав марки стали, выбранной нами для производства (Таблица 1)
Таблица 1- Химический состав Ст45Х ГОСТ 4543-71
Массовая доля элементов в % | |||
Углерод | Марганец | Кремний | |
Ст45Х | 0,41-0,49 | 0,5-0,8 | 0,17-0,37 |
Выбранная нами сталь является конструкционной легированной. В данной стали есть особенность – это трудная свариваемость. В связи с этим сталь 40х в процессе сварки подвергается нагреву до 300 С, а после нее – термической обработке. Кроме этой особенности, имеется склонность к отпускной способности, а еще флокеночувствиетльность. Сталь 45х характеристики имеет следующие: – удлинение относительное – 13-17%; – ударная вязкость – до 800 кДж/кв. метр; – предел прочности – до 900 МПа.
Выбор материала зависит от условий работы детали в узле. При анализе условия работы детали в курсовом проекте учитывалось:
1) максимальную нагрузку, которая может возникнуть в изделии при эксплуатаций;
2) характер приложенной нагрузки;
3) температурные условия работы;
4) наличие агрессивной среды;
5) тип трения рабочих поверхностей изделия в процессе эксплуатации;
6) характер износа;
7)допуск на коробление и доводки, твёрдость и так же пределы отклонения других показателей.
Определим тип производства исходя из условий в задании Крусового проекта 125 000 деталей в год – Массовое (Таблица 2)
Таблица 2 - Определение типа производства
Тип произ-ва | Годовой объём выпуска деталей одного наименования | ||
Крупных (М > 50 кг) | Средних (50кг≥М≥1кг) | Мелких (М≤1 кг) | |
Единичное | До 5 | До 10 | До 100 |
Серийное | От 5 до 1000 | От 10 до 5000 | От 100 до 50000 |
Массовое | От 1000 | От 5000 | От 50000 |
Операция 010 - Сверлильная
0 Установка детали в сверлильном кондукторе с гидроприжимами, одновременно устанавливается 42 детали
1 Сверлом 2300-2465 ВК ГОСТ 10902-77. Сверлим сквозное отверстие диаметром 3мм
Проверка качества. Снять деталь, измерить размеры ШЦ 125-0.5 Штангенциркуль ГОСТ 166-89. Выполнить переустановку.
2 Зенкер-сверлом 200-0761 ГОСТ188869-73 произвести сверление в задней торцевой части детали «Упор» 16мм.
Проверка качества. Снять деталь, измерить размеры ШЦ 125-0.5 Штангенциркуль ГОСТ 166-89. Деталь маркировать
Рис 7. Токарный станок c ЧПУ Goodway - Fanuc LU AN CW 6232B
Характеристики:
Общая длина -5000 мм
диаметр обработки над станиной -350 мм
поворота Ø -500 х 200 мм
диаметр обработки над суппортом -190 мм
скорости 26-1200 об / мин
Диаметр отверстия в шпинделе -47 мм
патрон Ø -200 мм
задняя бабка записи MK4
Пределы частоты вращения шпинделя, 1/мин -45-2000
Количество подач -8
Пределы подач, мм/об -0.1-1.4
Масса станка, кг -1280
Рис 8. Вертикально-сверлильный станок с ЧПУ «CMA- TRD», (Испания)
Характеристики станка
Класс точности Н
Наибольший диаметр сверления в стали 45 ГОСТ 1050-74, мм -25
Размеры конуса шпинделя по ГОСТ 25557-82 Морзе -3
Расстояние от оси шпинделя до направляющих колонны, мм -250
Наибольший ход шпинделя, мм -200
Расстояние от торца шпинделя, мм:
- до стола 60-700
- до плиты 690-1060
Наибольшее (установочное) перемещение сверлильной головки, мм -170
Перемещение шпинделя за один оборот штурвала, мм -122.46
Рабочая поверхность стола, мм -2400x1450
Наибольший ход стола, мм -2270
Установочный размер Т-образных пазов в столе по ГОСТ 1574-75:
- центрального 14H9
- крайних 14H11
Расстояние между двумя Т-образными пазами по ГОСТ 6569-75, мм -80
Количество скоростей- 12
Пределы частоты вращения шпинделя, 1/мин- 45-2000
Количество подач- 9
Пределы подач, мм/об 0.1-1.6
Масса станка, кг- 880
Для наших целей производства выбираем 1 сверлильный и 1 токарный станок.
Расчет погрешности
Для полного базирования заготовки в приспособлении элементы базирования должны лишить заготовку шести степеней свободы (правило “шести точек”). В качестве закрепления в токарной операции выступает 3-ох кулачковый патрон. В сверлильной операции-кондуктор. Для каждой операции будет предоставлен свой чертёж установки заготовки, на котором будет указанно, где именно стоит расположить зажимное устройство.
Рис. 9 – Базирование в кулачковом патроне
Рис.10 Операция 010 (зажим в кондукторе)
Выбираем погрешность базирования не более 3%
Расчет силы зажима
С гидравлическим приводом.
Для выбора гидроцилиндра на кондукторе необходимо сделать расчет на удержание деталей в гидравлической системе:
1. Определяем силу зажима детали, действующую на один кулачок:
W = K * PZ * R0 / f * R, где
Pz - сила резания, Pz = 2784,62 Н;
Ro – диаметр получаемой детали, мм; D = 20 мм;
K - коэффициент запаса, К=1,8;
f - коэффициент трения на рабочей поверхности кулачков, f =0,15;
R - радиус заготовки, R= 72,5мм;
W = 1,8 * 2784,62 * 70 / 0,15 * 72,5 = 24197 Н.
2. Определяем силу, действующую на пижимы:
Wo = W × n
где n – число гидропирижимов, n=3;
W0 = 3 * 24197 = 72591 Н.
3. Определяем диаметр поршня цилиндра и выбираем ближайший больший стандартный размер:
Dп = 1,13*√(W/ρ)
где p – давление масла на поршень, p=20-75кгс/см2; для перевода в ньютоны умножаю на 9,8.
Dп = 1,13 * √(72591 / 50*9,8) = 13,75 см = 137,5 мм.
Принимаем диаметр поршня 140 мм.
4. Определяем диаметр штока:
Dш = 0,5-0,7Dп
Dш = 0,7 × 140 = 98 мм.
5. Определяем потребную силу на штоке:
Q = (π/4) * (D2 – d2) * ρ * η
где D – диаметр поршня гидроцилиндра, 50мм;
р – давление масла на поршень 2,0-7,5МПа;
ŋ =0,85-0,9 – КПД гидроцилиндра;
d –диаметр штока, 35мм.
Q = (3,14/4) * (1402 - 982) *7,5 * 0,9 = 52966 Н.
6. Определяем производительность гидроцилиндра:
Q = W * L / t * ρ * η
Q = 72591 * 22 / 1,3 * 7,5 * 0,9 = 8272 м3/сек
7. Определяем время срабатывания гидроцилиндра:
Q = P * L / t * ρ * η
Q = 3,14 * 502 * 22 / 4 * 103 *8272 = 0,005 с.
где D – диаметр цилиндра;
L – ход поршня;
Q – производительность.
Расчетное усилие зажима детали 6735Н соответствует паспортным данным станка.
Вывод по Курсовому проекту
Выполняя курсовой проект я закрепил и воспользовался своими знаниями. Спроектировал станочное приспособление. Выполнил анализ конструкции детали. Создал технологический процесс на обработку детали. Выбрал элементы базирования и зажима заготовки, написал конструкцию и работу приспособления
Литература
1. Кузнецов Ю.И. и др. Оснастка для станков с ЧПУ. – М.: Машиностроение. 1990.
2. Белоусов А.П. Проектирование станочных приспособлений. – М.: Высшая школа. 1980.
3. Ансеров М.А. Приспособление для металлорежущих станков. – Л.: Машиностроение. 1975.
4. Плотицын В.Г. Наладка фрезерных станков. – Л.: Машиностроение. 1975.
5. Корсаков В.С. Основы проектирования приспособлений. – М.: Машиностроение. 1983.
6. Справочник технолога-машиностроителя под ред. Косиловой А.Г. и Мещерякова Р.К. – М.: Машиностроение. 1985.
7. Горошкин А.К. Приспособления для металлорежущих станков. – М.: Машиностроение. 1979.
8. Кутай А.К. Справочник по производственному контролю в машиностроении. – Л.: Машиностроение. 1974.
9. Кутай А.К. Справочник контрольного мастера. Лениздат. 1980.
10. Городецкий Ю.Г. Конструкция, расчет и эксплуатация измерительных инструментов и приборов. – М.: Машиностроение. 1971.
11. Допуски и посадки. Справочник. Под ред. Мягкова В.Д. – Л.: Машиностроение. 1978.
Приложение 1- FMEA анализ техпроцесса Упор
Приложение № 2 – «Чертеж детали «Упор»
Приложение 3 – Модель кондуктора
КУРСОВАЯ РАБОТА
«Производство и проектирование станочной оснастки для токарной, сверлильной обработки упора в технологическом процессе изготовления детали «Упор» с годовым объёмом выпуска 125000 шт.»
Выполнил: студент гр. 1614, Шахворостов М.В.
Научный руководитель: к.т.н., Епифанцев К.В
Дата сдачи:__________
Дата защиты:________
Оценка:_____________
Санкт-Петербург
ГОУ СПО «НЕВСКИЙ МАШИНОСТРОИТЕЛЬНЫЙ ТЕХНИКУМ»
ЗАДАНИЕ
на курсовое проектирование по специальности 151901 (ТМ)
студенту 1614 группы вечернего отделения
Шахворостов Максим Витальевич
«Производство и проектирование станочной оснастки для токарной, сверлильной обработки упора в технологическом процессе изготовления детали «Упор» с годовым объёмом выпуска 125000 шт.»
Введение
Introduction
Проектирование станочного приспособления
Анализ конструкции детали
Анализ технологического процесса, включая выполняемую операцию
Выбор элементов базирования и зажима заготовки
Схема нагрузок и расчет силы зажима
Определение размеров элементов зажима заготовки
Расчет станочного парка
Графическая компоновка приспособления
Конструкция и работа приспособления
Расчет погрешности базирования
Выводы по конструкции приспособления
Проектирование контрольной оснастки
Расчет исполнительных размеров
Конструкция и эксплуатация контрольного приспособления
Литература
FMEA
Дата выдачи задания «17» _________________ 2017г.
(число) (месяц)
Срок сдачи студентом «18» _________________ 2017г.
(число) (месяц)
Руководитель курсового проектирования ___ ______ преподаватель, к.т.н. К.В. Епифанцев
(подпись) (инициалы, фамилия)
Задание принял к исполнению ___________ «_____»___________2017г.
(подпись) (число) (месяц)
Содержание
Введение…………………………………………………………………..………….. Introduction……………………………………………………………………….…... 1. Проектирование станочного приспособления 1.1 Анализ конструкции детали………………………………………………..…… 1.2 Анализ технологического процесса и расчет станочного парка………….….. 2. Выбор элементов базирования и зажима заготовки и расчет погрешности… 2.1 Схема нагрузок при сверлильной операции………..……….………….……… 2.2 Схема нагрузок при токарной операции ……………………………….……… 2.3 Графическая компоновка приспособления……………………………..……… 2.4 Разработка специального инструмента необходимого для зажима заготовки при сверлильной обработке …………………….………………………………….. 2.5. Конструкция и работа приспособления …………………………….………… 2.6 Выводы по конструкции приспособления …………………………………...... 2.7 Техническое описание конструкции приспособления …………………..…… 2.8 Вывод по Курсовому проекту…………………………………..………………. 3. Литература…………………………………………………………………………. Приложение 1 «FMEA Анализ»………………………………………..………........ Приложение 2 «Чертеж детали Упор»……………………………….……………. Приложение 3 «Модель кондуктора»…………………………………...………… |
Введение
Под технологической оснасткой (ГОСТ3.1109—82) понимают средства технологического оснащения, дополняющие технологическое оборудование, для выполнения определенной части технологического процесса. Примерами технологической оснастки являются кондукторы, делительные головки, зажимные устройства, позволяющие одновременно обрабатывать несколько одинаковых деталей, уменьшать время на настройку оборудования.
Приспособление - это составная часть технологической оснастки, которая может быть самостоятельным элементом в контрольноизмерительных и некоторых сборочных операциях.
Если приспособление входит в состав обрабатывающей технологической системы, его называют станочным приспособлением, если оно входит в состав сборочной технологической системы, то его принято называть сборочным приспособлением.
Приспособления предназначены, главным образом, для установки объекта, в качестве которого выступает заготовка, деталь или сборочная единица. Установка включает в себя базирование объекта и его закрепление. Поэтому основными частями приспособления являются корпус, базирующие (установочные) и зажимные элементы.
Дополнительно приспособления могут выполнять следующие функции:
-обеспечивать направление режущего инструмента;
-служить базой для установки контрольно-измерительныхприборов;
-осуществлять механический или автоматический зажим объекта в приспособлении;
-увеличивать жесткость при установке базируемого объекта;
-изменять положение детали вместе с приспособлением. Использование приспособлений способствует повышению точности и производительности обработки, контроля деталей и сборки изделий, обеспечивает механизацию и автоматизацию технологических процессов, снижение квалификации работ, расширение технологических возможностей оборудования и повышение безопасности работ. Современное механосборочное производство располагает большим парком приспособлений, значительную часть которых составляют станочные приспособления.
В повышении качества изготовления деталей машин, их сборки и контроля важное значение имеет совершенствование технологической оснастки: создание высокопроизводительных конструкций станочных приспособлений, сокращение сроков их проектирования и изготовления, повышение качества и надежности, снижение трудоемкости изготовления, сокращение количества трудозатрат.
Решение этих задач должно быть направлено на повышение производительности труда станочников, слесарей-сборщиков, наладчиков и контролеров. Применение технологической оснастки снижает трудоемкость Т и себестоимость S изготовления сборки деталей (рис.1).
На рис. 1, а показана зависимость трудоемкости Т от коэффициента оснащенности К, под которым понимается отношение числа приспособлений к Числу операций обработки данной детали. Кривая 1 характеризуют одноместные приспособления ручного типа, а 2 — механизированные и многоместные приспособления.
Рис.1- Зависимость трудоемкости Т от коэффициента оснащенности К(а) и себестоимости обработки S от точности изготовления IT(б)
Станочные приспособления применяют для установки заготовок и инструмента на металлорежущие станки. Приспособления, связывающие со станком обрабатываемую заготовку, относят к приспособлениям для изготовления детали, а приспособления, связывающие со станком режущий инструмент, — к приспособлениям для инструмента.
Приспособления являются наиболее сложной и трудоемкой в изготовлении частью технологической оснастки.
Современная технологическая оснастка в виде станочных приспособлений для станков значительно повышает производительность труда за счет уменьшения вспомогательного облегчает условия труда операторов станков с ЧПУ, расширяет технологические возможности оборудования. времени на установку и закрепления заготовок, повышает точность обработки,
Приспособления для станков – кондукторы, поворотные делительные головки, оправки, гидроприжимы и установы должны иметь повышенную размерную точность. Погрешности базирования и закрепления, возникающие при установке заготовок в приспособления, должны быть сведены к минимуму. Для возможности использования полной мощности станка на черновых проходах и при обработке труднообрабатываемых материалов (титановые сплавы, нержавеющие, жаропрочные стали и другие) приспособления должны иметь повышенную жесткость конструкции.
Наиболее существенное сокращение вспомогательного времени при зажиме – разжиме заготовки достигается за счет использования гидро и пневмоцилиндров, именно данный вид оснастки мы применили для нашей заготовки, имеющий большой объём выпуска – 125 000 в год, что в пересчете на 247 рабочих дней лает нам 506 деталей в сутки. Операции при изготовлении детали «Упор» - токарная и сверлильная, станки с ЧПУ за короткое время смогут произвести обработку деталей, однако при достаточно долгом времени настройке станка при зажиме и установке детали, мы имеем риск не произвести нужного количества деталей в 2 рабочих смены. Следовательно, нам необходимо разработать оснастку, которая минимизировала бы время на установку, а, следовательно, позволила бы нам разработать технологический процесс с максимальной производительностью.
Introduction
Under technological equipment (ГОСТ3.1109-82)understand the means of technological equipment, complementing the technological equipment, to perform a specific part of the process. Examples of technological equipment are jigs, dividing head, clamping devices, allowing simultaneous processing of multiple identical parts, to reduce the time for equipment setup. The fixture is an integral part of tooling, which can be an independent element in the measuring and some Assembly operations. If the fixture is part of the manufacturing technological system, it is called machine fixture, if it is part of the Assembly of the technological system, it is called an Assembly fixture.
The most significant reduction in cycle time of the clamping – jaws of the workpiece is achieved through the use of hydraulic and pneumatic cylinders, it is this type of rig we used for our workpieces having a large volume of production – 125 000 a year, equivalent to 247 working days barking at us 506 parts per day. Operations in the manufacture of the part "Detend" - turning and boring, CNC machines for a short time will be able to handle the details, but in quite a long time setting up the machine in the clip and installing parts, we have the risk of not producing the required number of items in 2 working shifts. Therefore, we need to develop tooling which minimise installation time and, therefore, would allow us to develop a technological process with maximum productivity.
Проектирование станочного приспособления
Анализ конструкции детали
Деталь “Упор” является основным элементом сборочной ”. Деталь «Упор» относится к классу валов. Для изготовления данной детали выбираем заготовку, получаемую прокатом, марка материала Ст45Х (ГОСТ 4543-71).
Рис.2 – Общий вид детали «Упор»
Рис. 3 – Фронтальная проекция детали «Упор»
Деталь симметрична относительно продольной оси, деталь имеет 4 ступени (Рис.2):
1 цилиндрическая: с длиной – 16мм и диаметром -12мм,
2 цилиндрическая: с длиной – 32мм и диаметром -14мм,
3 цилиндрическая: с длиной – 6мм и диаметром -34мм,
4 цилиндрическая: с длиной – 20мм и диаметром -20мм,
Также с правого торца имеется отверстие диаметром 16мм.
Между ступеней 1 и 2 имеется кольцевая фасонная проточка с диаметром – 0,5мм (Рис.2), между ступеней 2 и 3 имеется фасонная проточка с диаметром – 1мм, между ступеней 3 и 4 имеется фасонная проточка с диаметром – 0,5мм. В детали имеется глухое центральное отверстие. Шероховатость посадочных отверстий Ra = 6,3, шероховатость сквозных отверстий Ra = 1,6. Шероховатость цилиндрической ступени Ra = 3,2. Остальные поверхности имеют шероховатость Rz=20
Исходя из этого коэффициенты точности, шероховатости и унификации должны по величине соответствовать технологичной детали. Наличие теоретического контура ухудшает технологичность детали.
Рис. 4 – 3D модель детали «Упор»
Не выбираем штамповку потому что деталь простой формы, поэтому по экономической себестоимости выгоднее использовать прокат. Упор применяется при стопорении движение полозьев штампа и ограничении движения блоков направляющих на салазках исполнительного органа, также может быть использован для стопорения механизмов автоматики.
Рассмотрим хим. состав марки стали, выбранной нами для производства (Таблица 1)
Таблица 1- Химический состав Ст45Х ГОСТ 4543-71
Массовая доля элементов в % | |||
Углерод | Марганец | Кремний | |
Ст45Х | 0,41-0,49 | 0,5-0,8 | 0,17-0,37 |
Выбранная нами сталь является конструкционной легированной. В данной стали есть особенность – это трудная свариваемость. В связи с этим сталь 40х в процессе сварки подвергается нагреву до 300 С, а после нее – термической обработке. Кроме этой особенности, имеется склонность к отпускной способности, а еще флокеночувствиетльность. Сталь 45х характеристики имеет следующие: – удлинение относительное – 13-17%; – ударная вязкость – до 800 кДж/кв. метр; – предел прочности – до 900 МПа.
Выбор материала зависит от условий работы детали в узле. При анализе условия работы детали в курсовом проекте учитывалось:
1) максимальную нагрузку, которая может возникнуть в изделии при эксплуатаций;
2) характер приложенной нагрузки;
3) температурные условия работы;
4) наличие агрессивной среды;
5) тип трения рабочих поверхностей изделия в процессе эксплуатации;
6) характер износа;
7)допуск на коробление и доводки, твёрдость и так же пределы отклонения других показателей.
Определим тип производства исходя из условий в задании Крусового проекта 125 000 деталей в год – Массовое (Таблица 2)
Таблица 2 - Определение типа производства
Тип произ-ва | Годовой объём выпуска деталей одного наименования | ||
Крупных (М > 50 кг) | Средних (50кг≥М≥1кг) | Мелких (М≤1 кг) | |
Единичное | До 5 | До 10 | До 100 |
Серийное | От 5 до 1000 | От 10 до 5000 | От 100 до 50000 |
Массовое | От 1000 | От 5000 | От 50000 |
|
|
Кормораздатчик мобильный электрифицированный: схема и процесс работы устройства...
Типы оградительных сооружений в морском порту: По расположению оградительных сооружений в плане различают волноломы, обе оконечности...
Историки об Елизавете Петровне: Елизавета попала между двумя встречными культурными течениями, воспитывалась среди новых европейских веяний и преданий...
Архитектура электронного правительства: Единая архитектура – это методологический подход при создании системы управления государства, который строится...
© cyberpedia.su 2017-2024 - Не является автором материалов. Исключительное право сохранено за автором текста.
Если вы не хотите, чтобы данный материал был у нас на сайте, перейдите по ссылке: Нарушение авторских прав. Мы поможем в написании вашей работы!