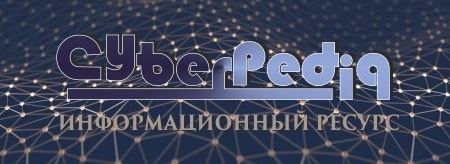
Наброски и зарисовки растений, плодов, цветов: Освоить конструктивное построение структуры дерева через зарисовки отдельных деревьев, группы деревьев...
Индивидуальные и групповые автопоилки: для животных. Схемы и конструкции...
Топ:
Устройство и оснащение процедурного кабинета: Решающая роль в обеспечении правильного лечения пациентов отводится процедурной медсестре...
Выпускная квалификационная работа: Основная часть ВКР, как правило, состоит из двух-трех глав, каждая из которых, в свою очередь...
Особенности труда и отдыха в условиях низких температур: К работам при низких температурах на открытом воздухе и в не отапливаемых помещениях допускаются лица не моложе 18 лет, прошедшие...
Интересное:
Как мы говорим и как мы слушаем: общение можно сравнить с огромным зонтиком, под которым скрыто все...
Лечение прогрессирующих форм рака: Одним из наиболее важных достижений экспериментальной химиотерапии опухолей, начатой в 60-х и реализованной в 70-х годах, является...
Инженерная защита территорий, зданий и сооружений от опасных геологических процессов: Изучение оползневых явлений, оценка устойчивости склонов и проектирование противооползневых сооружений — актуальнейшие задачи, стоящие перед отечественными...
Дисциплины:
![]() |
![]() |
5.00
из
|
Заказать работу |
Содержание книги
Поиск на нашем сайте
|
|
ЛАБОРАТОРНАЯ РАБОТА №1
ТЕМА: «ОБТОЧКА НАРУЖНЫХ ЦИЛИНРИЧЕСКИХ
ПОВЕРХНОСТЕЙ»
Цель работы:1. Повторить и знать:
- Резание металлов и режущий инструмент;
- Формирование поверхностей при точении;
- Основные способы установки заготовки на токарном станке;
- Классификация способов обработки наружных цилиндрических
поверхностей.
2. Ознакомиться с технологической документацией.
3. Ознакомиться с устройством и системой управления токарного станка.
Задачи работы:
1. Теоретическое ознакомление с технологическим процессом обточки наружных цилиндрических поверхностей.
2. Теоретически ознакомится с принципом работы токарного станка.
Основные сведения
Основные способы установки заготовок на токарном станке.
Обычно используется один из трех методов установки заготовки на токарном станке: в патроне, в центрах, В патроне с подпором задним центром. Условно на представленных эскизах эти способы установки заготовок обозначаются следующим образом:
Рисунок 1.3 - Способы установки заготовок на токарном станке: а – в патроне; б – в центрах; в – в патроне с подпором задним центром.
Установка заготовки в токарном патроне (чаще всего, трех кулачковом, самоцнтрирующем) - самый универсальный способ установки, позволяющий вести обточку поверхностей, расточку отверстий и обработку торцов.
Применяется при обработке коротких деталей.
Установка в центрах – способ, позволяющий сохранить одни и те же установочные базы на самых различных операциях и поэтому повышающий точность изготовления детали. Для установки требуется введние специальной операции – центральной, т. е. операции обработки специальных конически отверстий. Удобнее всего эту операцию осуществлять одновременно с подрезкой торцов заготовки на специальных фрезерно-центровальных станках.
|
При установке в центрах заготовка вращается или с помощью специального хомутика (используется поводковый патрон), или(значительно реже) с помощью рифленого переднего центра.
Установка в патроне с подпором задним центром применяется при обработке валов малой жёсткости (с большим отношением длинны вала к его диаметру).
Классификация основных видов обработки наружных цилиндрических поверхностей.
Рисунок 1.4 - Классификация методов обработки наружных цилиндрических поверхностей.
На рисунке перечислены все возможные методы обработки, сущность которых можно узнать по литературным источникам, указаны значения предельной точности обработки по каждому методу – квалитеты точности (вверху рамки) и параметр шероховатости Ra, мкм (внизу рамки). Квалитеты точности указаны для деталей из конструкционных сталей. Для деталей из чугуна и цветных сплавов допуск на размер можно принимать на один квалитет точнее.
Ознакомление с технологической документацией.
С каждым станком завод-изготовитель отправляет заказчику комплект технической документации, именуемый «Руководством по эксплуатации». Руководство хранят в непромокаемом пакете из полиэтиленовой пленки и при упаковке станка в несколько ящиков, находится в ящике № 1.
Руководство по эксплуатации
«Руководство по эксплуатации» - документ, содержащий описание устройства и принципа работы станка, а также сведения по его эксплуатации и удостоверяющий гарантированные предприятием-изготовителем основные параметры и технические характеристики станка.
Руководство состоит из трех основных разделов: технического описания, инструкции по эксплуатации и паспорта.
Техническое описание
В раздел «Техническое описание» входят следующие подразделы: назначение и область применения; состав станка; устройство и работа станка и его составных частей; электрооборудование; гидросистема и пневмосистема; система смазки.
|
Инструкция по эксплуатации
Второй раздел руководства «Инструкция по эксплуатации» состоит из восьми подразделов: указания мер безопасности; порядок установки станка; настройка и наладка; регулирование; особенности разборки и сборки при ремонте; схема расположения подшипников; материалы по быстроизнашиваемым деталям; инструкция по подготовке управляющих программ и тест-программы для проверки станка.
Паспорт станка
Третьим разделом руководства является паспорт станка. Паспорт содержит следующие подразделы: основные технические данные и характеристики; комплект поставки; свидетельство о приемке; гарантии.
Технические характеристики
Подраздел «Основные технические данные и характеристики» отражает возможности станка, класс его точности, габаритные размеры и массу. Основные возможности станка определены видом выполняемых работ и размерами обрабатываемых деталей.
Обязательными данными подраздела являются наибольшие размеры и масса обрабатываемых деталей, характеристика приводов главного движения и подач.
В паспорте приведены иллюстрации, отражающие базовые и присоединительные поверхности, необходимые для проектирования технологической оснастки, а также показано рабочее пространство с крайними положениями подвижных органов, перемещающихся кожухов и др.
Важным разделом паспорта является свидетельство о приемке. В нем записывают допуски и фактические отклонения от заданных требований норм точности и жесткости станка.
Нормы точности
Нормы точности нового станка при проверке на заводе-потребителе должны соответствовать фактическим данным, полученным на заводе-изготовителе при испытании, а в период последующей многолетней эксплуатации отклонения не должны выходить за пределы допускаемых значений.
В последнем подразделе паспорта установлены обязательства завода-изготовителя безвозмездно заменять или ремонтировать вышедший из строя в гарантийный период станок при соблюдении потребителем условий эксплуатации, транспортирования и хранения станка. Обычно срок гарантии составляет 18 месяцев. Начало гарантийного срока исчисляют со дня пуска станка в эксплуатацию, но не позднее 6 месяцев с момента прибытия на действующие и 9 месяцев на вновь строящиеся предприятия.
|
В наружном конверте ящика № 1 (иногда внутри ящика) есть упаковочный лист, в котором перечислены наименования и число поставленных агрегатов, отсоединенных узлов, изделий, приборов, инструментов, приспособлений, руководств, инструкций и указан номер ящика, в котором они размещены.
ЛАБОРАТОРНАЯ РАБОТА №2
ИНСТРУМЕНТОМ»
Цель работы:1. Повторить и знать:
- Осевой режущий инструмент и особенности его работы;
- Геометрию заточки спирального сверла;
- Основные виды работ, выполняемых на сверлильных станках;
- Общее устройство вертикально-сверлильного станка;
- Классификацию металлорежущих станков.
2. Ознакомиться с технологической документацией.
3. Ознакомиться с устройством и механизмами управления сверлильного станка.
Задачи работы:
1. Теоретическое ознакомление с технологическим процессом обработки металлов осевым режущим инструментом.
2. Теоретически ознакомится с принципом работы сверлильного станка.
Основные сведения
ЛАБОРАТОРНАЯ РАБОТА №3
Основные сведения
ЛАБОРАТОРНАЯ РАБОТА №4
Основные сведения
Формообразование поверхностей на фрезерном станке.
Процесс фрезерования основан на сочетаниях двух одновременно действующих равномерных движений – вращательного (фрезы) и поступательного (реже вращательного) заготовки. При фрезеровании вращательное движение фрезы считается главным, и линейная скорость вращения фрезы оценивается как скорость резания. Движение заготовки является движение подачи. У станков большинства типов оно поступательное и только у некоторых – вращательное (например, у барабанно-фрезерных станков).
Скорость резания (м/мин) устанавливается по точкам наружного диаметра фрезы:
где n – частота вращения фрезы, об/мин:
Dф - наружный диаметр фрезы мм.
Движение подачи Sz при назначении режимов резания задается количеством миллиметров па зуб фрезы (мм/зуб). Фрезерные станки имеют привод движения подачи от независимого двигателя, поэтому в паспорте станка указываются значение минутной подачи, мм/мин:
|
S = Sz × z × n
где z – число зубьев фрезы;
n – частота вращения фрезы, об/мин.
Режущие лезвия зубьев вращающейся фрезы за время одного оборота, как правило, находятся с обрабатываемой заготовкой только на некоторой части оборота, а остальная часть проходит не совершая работы. Период времени, в течении которого режущее лезвие контактирует с обрабатываемой заготовкой, называется рабочим циклом, а соответствующий угол поворота фрезы – углом контакта.
На протяжении рабочего цикла направление главного движения меняется.
Условия резания в каждой точке траектории определяется сочетанием главного движения реза и движением подачи. При фрезеровании устанавливаются следующие определения параметров процесса.
t – глубина фрезерования, мм – это кратчайшее расстояние между поверхностью, в которой лежат все точки конца контакта зуба фрезы с заготовкой и поверхностью, в которой лежат все точки конца контакта, т. е. глубина фрезерования всегда измеряется в плоскости вращения фрезы (т.е. в плоскости вращения фрезы).
В – ширина фрезерования, мм – это размер заготовки, измеренный в плоскости, расположенной вдоль эрой фрезы, перпендикулярно оси фрезерования.
Геометрия заточки фрезы.
В качестве примера геометрии заточки фрезы рассмотрим заточка торцевой фрезы (Рисунок 4.2).
Рисунок 4.2 – Геометрия заточки фрезы.
Зуб торцевой фрезы по своей геометрии напоминает резец с главным углом в плане φ. У большинства фрез φ=60-900. Вспомогательный угол на плане φ1 уменьшает трение вспомогательной режущей кромки об образованную поверхность. Передний угол γ торцевой фрезы может быть положительным (γ=10-200) и отрицательным (γ=-5…-150). Задний угол α=10-250 служит для уменьшения трения зуба о поверхность резания. Угол наклона зуба ω =100.
Число зубьев фрезы и их диаметр колеблются в широких пределах зависимости от конструкции фрезы и материала еѐ режущих зубьев. Так, например, торцевые фрезы из быстрорежущей стали (ГОСТ 9304-69) имеют наименьший диаметр Da = 630 мм при числе зубьев Z = 32.
Оформление карты эскизов.
На картах оформляется весь процесс технологической обработки деталей. Карту эскизов необходимо разрабатывать для выполнения операций и переходов. В этом документе указываются необходимые для технологического процесса сведения: размеры, предельные отклонения, обозначение шероховатости поверхностей и т.д. На карте поверхности, подвергаемые обработке, нумеруют арабскими цифрами. Порядковый номер ставят в окружности диаметром 6 - 8 мм, а затем соединяют выносной линией с изображением данной поверхности.
|
Эскиз включает изображение рабочего инструмента в конце хода и способ крепления заготовки. В документе используют краткое обозначение названий технологических операций.
ЛАБОРАТОРНАЯ РАБОТА №5
Основные сведения
Технические характеристики.
Наибольшие размеры обрабатываемого пруткового материала, мм:
круглого – 18; шестигранного – 14; квадратного – 12;
Наибольший диаметр изделия, мм:
— устанавливаемого над станиной – 250
— над поперечным суппортом – 130
Расстояние от торца шпинделя до револьверной головки, мм – 95-250
Наибольшая длина заправляемого прутка, мм – 2100
Наименьший остаток прутка, мм – 70
Размеры, мм:
¾ длина – 2680
¾ ширина – 575(640- для 1Б318)
¾ высота – 1200
¾ Вес, кг – 570 (660 — для 1Б318)
Принцип работы.
Процедура изготовления деталей на таком оборудовании, как станок универсальный револьверного типа, выглядит следующим образом: Устанавливают основной и вспомогательный режущий инструмент. Крепят зажимной механизм для заготовок. Настраивают приспособление, предназначенное для регулировки амплитуды движения суппорта и подачи заготовок. Монтируют рукоятки и кулачки, обеспечивающие необходимую скорость движения рабочего механизма. Производят необходимый вид работ.
Вывод: Я повторил и закрепил свои знания по данной теме, а также ознакомился с технической документацией, устройством и системой управления токарно - револьверного станка.
ЛАБОРАТОРНАЯ РАБОТА №1
ТЕМА: «ОБТОЧКА НАРУЖНЫХ ЦИЛИНРИЧЕСКИХ
ПОВЕРХНОСТЕЙ»
Цель работы:1. Повторить и знать:
- Резание металлов и режущий инструмент;
- Формирование поверхностей при точении;
- Основные способы установки заготовки на токарном станке;
- Классификация способов обработки наружных цилиндрических
поверхностей.
2. Ознакомиться с технологической документацией.
3. Ознакомиться с устройством и системой управления токарного станка.
Задачи работы:
1. Теоретическое ознакомление с технологическим процессом обточки наружных цилиндрических поверхностей.
2. Теоретически ознакомится с принципом работы токарного станка.
Основные сведения
|
|
Археология об основании Рима: Новые раскопки проясняют и такой острый дискуссионный вопрос, как дата самого возникновения Рима...
Опора деревянной одностоечной и способы укрепление угловых опор: Опоры ВЛ - конструкции, предназначенные для поддерживания проводов на необходимой высоте над землей, водой...
Автоматическое растормаживание колес: Тормозные устройства колес предназначены для уменьшения длины пробега и улучшения маневрирования ВС при...
Кормораздатчик мобильный электрифицированный: схема и процесс работы устройства...
© cyberpedia.su 2017-2024 - Не является автором материалов. Исключительное право сохранено за автором текста.
Если вы не хотите, чтобы данный материал был у нас на сайте, перейдите по ссылке: Нарушение авторских прав. Мы поможем в написании вашей работы!