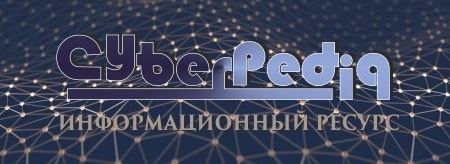
Типы сооружений для обработки осадков: Септиками называются сооружения, в которых одновременно происходят осветление сточной жидкости...
Организация стока поверхностных вод: Наибольшее количество влаги на земном шаре испаряется с поверхности морей и океанов (88‰)...
Топ:
Методика измерений сопротивления растеканию тока анодного заземления: Анодный заземлитель (анод) – проводник, погруженный в электролитическую среду (грунт, раствор электролита) и подключенный к положительному...
Оснащения врачебно-сестринской бригады.
Основы обеспечения единства измерений: Обеспечение единства измерений - деятельность метрологических служб, направленная на достижение...
Интересное:
Что нужно делать при лейкемии: Прежде всего, необходимо выяснить, не страдаете ли вы каким-либо душевным недугом...
Распространение рака на другие отдаленные от желудка органы: Характерных симптомов рака желудка не существует. Выраженные симптомы появляются, когда опухоль...
Берегоукрепление оползневых склонов: На прибрежных склонах основной причиной развития оползневых процессов является подмыв водами рек естественных склонов...
Дисциплины:
![]() |
![]() |
5.00
из
|
Заказать работу |
|
|
Аппаратура для проведения испытания
Для проведения опыта применяется следующая аппаратура:
1. Аппарат модели ЛГВО (рис.1.1) с нагревателем и термометром;
2. Щит из листовой кровельной стали; 3.Секундомер; 4.Барометр. Аппарат ЛГВО состоит из:
- металлического или фарфорового тигля высотой 46 мм и диаметром 58 мм;
- песчаной бани, в качестве которой используется металлический или фарфоровый тигель большего диаметра или глубокая металлическая чашка;
-термометра типа ТН-2 (ГОСТ 400-80);
- зажигательного приспособления.
Прибор ЛГВО должен удовлетворять следующим требованиям:
- расхождение между двумя параллельными определениями температуры вспышки, не должно превышать следующих величин, в °С:
температура вспышки до 150°С -4°С,
температура вспышки свыше 150°С - 6 °С.
Расхождение между двумя параллельными определениями температуры воспламенения не должно превышать 6 °С.
Габаритные размеры, мм: длина - 270, ширина -150, высота – 625, вес - не более 4 кг. Щит выполняется из листовой кровельной стали (или листового асбеста), окрашивается с внутренней стороны черной краской для защиты аппаратуры от движения воздуха. Высота листа 550-650 мм. Секундомер с минутной и секундной стрелкой. Барометр метеорологический в обычном исполнении.
Подготовка к испытанию
Испытуемый нефтепродукт наливают во внутренний тигель так, чтобы уровень жидкости отставал от края тигля на 12 мм для нефтепродуктов со вспышкой до 210°С включительно и на 18 мм для нефтепродуктов с температурой вспышки выше 210°С.
Правильный налив нефтепродукта проверяют шаблоном. При наливании не допускается разбрызгивания нефтепродукта, смачивания стенок внутреннего тигля выше уровня жидкости.
|
Тигли устанавливают в кольцо штатива, который ставят в таком месте комнаты, где отсутствует заметное движение воздуха и где свет настолько заметен, что вспышка хорошо видна.
Во внутренний тигель с нефтепродуктом устанавливают термометр в строго вертикальном положении, чтобы ртутный шарик находился в центре тигля приблизительно на одинаковом расстоянии от дна тигля и от уровня нефтепродукта и закрепляют термометр в таком положении в лапке штатива. Собранный аппарат окружают щитом.
Проведение испытания на температуру вспышки
Наружный тигель аппарата нагревают со скоростью 10°С в минуту.
За 40°С до ожидаемой температуры вспышки нагрев ограничивают скоростью 4°С в минуту.
За 10°С до ожидаемой температуры вспышки проводят медленно по краю тигля на расстоянии 10-14 мм от поверхности испытуемого нефтепродукта и параллельно этой поверхности пламенем зажигательного приспособления. Длина пламени должна быть 3-4 мм. Время продвижения пламени от одной стороны тигля до другой - 2-3 с. Такое испытание повторяют через 2°С подъема температуры.
За температуру вспышки принимают температуру, показываемую термометром при появлении первого сильного пламени над частью или над всей поверхностью испытуемого нефтепродукта.
Истинную вспышку не следует смешивать с отблеском от пламени зажигательного приспособления.
В случае появления первой вспышки она должна быть подтверждена последующей вспышкой через 2°С.
Проведение испытания на температуру воспламенения
После установления температуры вспышки испытуемого нефтепродукта, если требуется определить температуру воспламенения, продолжают нагревание наружного тигля, так, чтобы нефтепродукт нагревался со скоростью 4°С в минуту и повторяют испытание пламенем зажигательного приспособления через каждые 2° С подъема температуры нефтепродукта.
За температуру воспламенения принимают температуру, показываемую термометром в тот момент, в который испытуемый нефтепродукт при поднесении к нему пламени зажигательного приспособления загорается и продолжает гореть не менее 5с.
|
Допускаемые расхождения для параллельных определений
Расхождения между двумя параллельными определениями температуры вспышки не должны превышать следующих величин:
Т вспышки, °С.Допускаемые расхождения, °С
до 150 4
свыше 150 6
Расхождение между двумя параллельными определениями температуры воспламенения не должно превышать 6 °С.
Содержание отчета
1.Назначение и описание аппарата для испытания масла на вспышку и воспламенение модели ЛГВО, комплектность аппарат
2. Составить эскиз общего вида аппарата с основными размерами,
3. Сделать эскиз шаблона для определения уровня масла в тигле,
4. Составить график нагрева масла с нанесением точек вспышки и воспламенения масла.
5. Рассчитать температуру вспышки с учетом барометрической поправки.
6. Дать заключение о сорте масла и пригодности его к работе.
Лабораторная работа № 2
ОПРЕДЕЛЕНИЕ ТЕМПЕРАТУРЫ ВСПЫШКИ МАСЛА
В ЗАКРЫТОМ ТИГЛЕ
Цель работы: Изучение свойств смазочных материалов для закрытых передач.
Содержание отчета
1.Назначение и описание прибора для определения температуры вспышки нефтепродуктов в закрытом тигле типа ПВНЭ (ГОСТ 1421-79).
2. Составить эскиз общего вида прибора с основными размерами.
3.Составить электрическую схему прибора ПВНЭ.
4.Составить график нагрева масла с нанесением точек вспышки и воспламенения масла.
5.Рассчитать истинную температуру вспышки с учетом барометрической поправки.
6.Дать заключение о сорте масла и пригодности его к работе.
Подготовка прибора к работе
Перед началом работы прибор необходимо заземлить. Если нефтепродукт содержит более 0,05 % воды, то перед определением температуры вспышки его обезвоживают, обрабатывая свежепрокаленной и охлажденной поваренной солью, сульфатом кальция или хлористым кальцием. После обезвоживания на испытание берут верхний слой нефтепродукта.
Тигель промывают авиационным бензином и тщательно высушивают. Перед наливом нефтепродукт и тигель должны иметь температуру не менее чем на 20°С ниже предполагаемой температуры вспышки.
Нефтепродукт наливают в тигель до кольцевой риски, закрывают чистой сухой крышкой, вставляют термометр и помещают тигель в ванну.
|
При испытании нефтепродуктов с температурой вспышки до 50°С нагревательная ванна должна быть предварительно охлаждена до комнатной температуры (20±5°С).
При отсутствии газа заправляют фитильную лампочку, вставив в ее трубку фитиль, а в коробку кусочек ваты. Фитиль и вату смачивают машинным маслом с добавлением растительного (соевого или подсолнечного) для того, чтобы температура вспышки заправляемого масла была выше температуры вспышки нефтепродукта.
Пламя лампочки регулируют так, чтобы его форма была близка к шару диаметром 3-4 мм.
Прибор помещают в таком месте, где нет заметного движения воздуха и где свет настолько затемнен, что вспышка хорошо видна. Его окружают щитом из листовой стали высотой 500-650 мм, окрашенным с внутренней стороны черной краской (щит в комплект поставки не входит).
Барометрическое давление определяют по проверенному барометру или узнают на метеорологической станции. Электрическая схема прибора приведена на (рис. 2)
Порядок работы
Прибор нагревают следующим образом. При испытании нефтепродуктов с температурой вспышки до 50°С температуру повышают со скоростью 1°С в минуту при непрерывном перемешивании нефтепродукта (от начала до конца опыта).
При анализе нефтепродуктов с температурой вспышки от 50 до 150°С начальное нагревание ведут со скоростью 5-8 С в минуту, а продуктов с температурой вспышки выше 150°С - со скоростью 10-12°С в минуту при периодическом перемешивании.
Во избежание поломки гибкого вала, вращающего стержень мешалки, перемешивание следует производить плавно и медленно, вращая вал в том направлении, в котором он закручен.
После того, как нефтепродукт нагреется до температуры близкой к температуре вспышки его нагревают так, чтобы температура повышалась со скоростью 2°С в минуту.
При температуре нефтепродукта на 10°С ниже ожидаемой температуры вспышки испытание на вспыхивание начинают проводить через 1°С для продуктов с температурой вспышки до 50°С и через 2°С - для нефтепродуктов с температурой вспышки выше 50 °С.
|
Вспышкой считается появление голубоватого пламени, быстро пробегающего по поверхности нефтепродуктов. Вспышка иногда сопровождается слабым звуком; часто при испытании на вспышку гаснет лампочка. Для быстрого зажигания фитильной лампочки всегда необходимо иметь зажженную спиртовую горелку.
После получения первой вспышки испытание продолжают, повторяя зажигание через 1°С - для нефтепродуктов с температурой вспышки до 50°С и через 2°С для нефтепродуктов с температурой вспышки выше 50 °С. Если при этом вспышка не произойдет, испытание повторяют заново. Если при повторном определении температура вспышки будет такой же, как и при первом определении, а воспроизводимости вспышки через 2°С также не произойдет, определение считают оконченным, и за температуру вспышки принимают показание термометра в момент первой вспышки в тигле при двух параллельных определениях (с учетом поправок на атмосферное давление и показание термометра).
В том случае, если испытанию подвергают неизвестный нефтепродукт, делают предварительное определение температуры вспышки. После установления приближенной температуры вспышки проводят испытание по изложенной выше методике.
2.5. Допускаемые расхождения при параллельных определениях
В соответствии с ГОСТ 6356-75 расхождения между параллельными определениями температуры вспышки в закрытом тягле не должны превышать следующих величин отклонений от среднего арифметического сравниваемых результатов:
Температура вспышки, °С Допустимые расхождения
до 50 ±1
выше 50 ±2
Если барометрическое давление отличается от 0,1013 МПа (760 мм. рт. ст.) на 150 Па и более, в показанную термометром температуру вспышки вводят поправку (Аt), которую, вычисляют по формуле:
Аt = 0,0345 (0,1013-Р)
где Р - фактическое барометрическое давление, МПа.
Вычисление производят с точностью до 1 °С.
Если барометрическое давление ниже 0,1013 МПа (760 мм. рт. ст. поправку прибавляют, если выше 0,1013 МПа (760 мм. рт. ст.) - вычитают.
Содержание отчета
1. Назначение и описание прибора для определения температуры вспышки нефтепродуктов в закрытом тигле типа ПВНЭ (ГОСТ 1421-79).
2. Составить эскиз общего вида прибора с основными размерами.
3. Составить электрическую схему прибора ПВНЭ.
4. Составить график нагрева масла с нанесением точек вспышки и воспламенения масла.
5. Рассчитать истинную температуру вспышки с учетом барометрической поправки.
6. Дать заключение о сорте масла и пригодности его к работе.
\
Лабораторная работа № 2
РАСЧЁТ ОБОРУДОВАНИЯ СИСТЕМЫ ЖИДКОЙ СМАЗКИ
Цель работы: Изучить оборудование и системы жидкой смазки. Выполнить расчёт системы жидкой смазки. Согласно исходным данным (табл. 3.1) выбрать сорт масла, определить производительность насоса и параметры основного оборудования системы.
|
Общие положения
В зависимости от принципа подвода смазочных материалов к поверхностям и узлам трения различают следующие системы смазки:
![]() ![]() ![]() ![]() ![]() ![]() ![]() |
Смазка маслами
Индивидуальная смазка применяется для отдельных деталей и узлов, когда их подключение к централизованной системе затруднено. В этом случае применяют отдельные масленки, трубки Пито и др.
Смазку погружением применяют в основном в редукторах, когда тепло, выделяемое при работе узлов трения, полностью отводится в окружающее пространство.
Смазка под давлением применяется в случае необходимости постоянного отвода тепла и обеспечения жидкостного трения. Масло подается в узлы трения под давлением с помощью циркуляционных систем насосами.
Аэрозольная система смазки
Применяется при работе узлов с высокими нагрузками и температурами. Достоинства: небольшой расход смазочных материалов, простота конструкции. Применяются выпускаемые промышленностью генераторы масляного тумана (ГМТ). Генератор масляного тумана состоит из следующих основных узлов: фильтра- влагоотделителя для удаления загрязнений и влаги из сжатого воздуха; электромагнитного клапана для подачи сжатого воздуха, регулятора давления воздуха, маслораспылителя, резервуара для масла приборов контроля и регулирования.
Генератор работает следующим образом. Сжатый воздух от компрессора или сети подается по воздухопроводу через фильтр- влагоотделитель, электромагнитный клапан, регулятор давления, электронагреватель воздуха в маслораспылитель и, создавая разрежение в его эжекционной камере с помощью главного и вспомогательного дросселей, всасывает в эту камеру из резервуара необходимое для распыления количество масла. Образующаяся при этом масляно-воздушная смесь (туман) находится под давлением в верхней части резервуара – области, Под созданным давлением в области масляный туман через отверстие распылителя по системам трубопроводов подается к точкам смазки.
Масло в резервуар подается по трубопроводу шестеренными насосами (их, как правило, два – один рабочий, один, резервный) через фильтр и подогревается в резервуаре с помощью электронагревателя. Уровень масла в резервуаре контролируется датчиками реле минимального и максимального уровня. Электроконтактный манометр отключает компрессор сжатого воздуха при превышении давления тумана в резервуаре сверх допустимого. Одновременно срабатывает предохранительный клапан, выпуская масляный туман в атмосферу.
Поступая по трубопроводам к узлам трения, масляный туман конденсируется в соплах и на поверхности трения подается в жидком виде, а воздух через неплотности выходит в атмосферу.
Содержание отчета
1. Расчетная часть посвященная определению основных параметров и выбору системы жидкой смазки.
2. Выводы и предложения о рациональной системе жидкой смазки.
Лабораторная работа № 4
ОПРЕДЕЛЕНИЕ СВОЙСТВ ПЛАСТИЧЕСКОЙ СМАЗКИ
Цель работы: Определение типа, качества и условий применения смазки.
Порядок работы
В условиях производства очень важно знать простые методы определения свойств консистентных смазок и уметь их различать.
Для заданной консистентной смазки определить:
1. Наличие механических примесей.
Для этого на чистое стекло размером 70x70x1 мм наносят слой смазки толщиной 0,5-1,5 мм. Нанесенный слой смазки просматривают в проходящем свете и определяют наличие механических примесей. После этого слой смазки закрывают вторым стеклом и, передвигая стекло определяют абразивные механические примеси.
2. Проверить расслаиваемость консистентной смазки. Нормальная консистентная смазка должна иметь однородную концентрацию. Признаком расслаиваемости смазки является наличие слоя
минерального масла на ее поверхности. Для проверки на расслаиваемость в стеклянную пробирку помещают около 5-8 г смазки и нагревают на спиртовой горелке до перехода смазки из пластического состояния в
жидкое. Смазка считается хорошей, если в расплавленном состоянии она однородна и в ней нет кусочков мыла.
3. Определить температуру каплепадения.
Исcледования проводят на приборе Уббеладе (рис. 4.1).
Рис. 4.1. Прибор для определения температуры каплепадения консистентных смазок: а- прибор Уббелоде: 1 - чашечка с исследуемой смазкой; 2 - гильза; 3 - держатель; 4 - термометр; 5 – резиновая пробка; б - схема монтажа прибора: 6 - лабораторный штатив с зажимами; 7 - стеклянная пробирка; 8 - резиновая пробка; 9 - термометр; 10 - стакан с водой; 11 - фильтровальная бумага, 12 - асбестовая прокладка.
Для этого исследуемую смазку плотно набивают в чашечку 1. Излишек смазки удаляют. Чашечку помещают в металлическую гильзу 2, при этом наконечник термометра 4 входит в смазку, В дне чашечки имеется отверстие, через которое падают капли расплавленной смазки. Собирают прибор. Собранный прибор при помощи пробки 8, находящейся на конце термометра 4, закрепляют внутри пробирки 7. На дно пробирки помещают кусочек фильтровальной бумаги 11. Пробирку 7 с помощью проволочного зажима укрепляют в стакане с водой. Конец пробирки 7 должен находиться на расстоянии 30-40 мм от дна стакана. Стакан с водой ставят на электроплитку и нагревают со скоростью. 1-2 град/мин. При исследовании отмечают две температуры: размягчения, при которой из отверстия чашечки появляется капля смазки, и каплепадения, когда капля смазки отрывается и падает на дно пробирки,
4. Проверить растворимость смазки и определить тип загустителя.
Вид загустителя определяют по его способности к растворению в воде и бензине. Твердые углеводороды растворяют с в бензинах, натриевое мыло - в воде, кальциевые мыла ни в не растворяются ни в воде, бензинах. Тип загустителя определяют следующим образом. Берут две пробирки и помещают в них 2-3 г исследуемой смазки. В первую пробирку до половины наливают дистиллированную воду. Смесь размешивают. Нагревают пробирку на спиртовой горелке до температуры 60~70°С; периодически взбалтывая. Если вода в пробирке становится мутной, загуститель - натриевое мыло. Во вторую пробирку до половины наливают авиационный бензин Б-70, Пробирку нагревают в стакане горячей воды. Если загуститель углеводороды, то смазка растворится полностью. Мыльные загустители в бензине не растворяются и остаются отдельными кусочками.
5. Определить число пенетрации. Густота, или консистентность смазки, характеризуется числом пенетрации. Число пенетрации показывает глубину погружения конуса в десятых долях миллиметра в испытываемую смазку в течение 5 с.
Схема пенетрометра дана на рис. 4.2.Смазку плотно набивают в цилиндр 5. Цилиндр со смазкой помещают на столик 6. Освобождают винтом
3 стержень конуса 4 и по диску 2 регистрируют глубину погружения иглы за 5 с. Время фиксируют по секундомеру. Вес конуса равен 150 г.
Рис. 4.2. Прибор для определения числа пенетрации консистентной смазки:1 - стойка; 2 - циферблат; 3 - винт; 4 - конус; 5 - цилиндр с исследуемой смазкой; б - столик.
Таблица 4.1.
Классификация пластичных смазок по консистенции
Класс | Диапазон пенетрации | Визуальная оценка консистенции |
445...475 | Очень мягкая, аналогичная очень вязкому маслу | |
400...430 | Тоже | |
355...385 | Мягкая | |
310...340 | Тоже | |
265...295 | Вазелинообразная | |
220...250 | Почти твердая | |
175...205 | Твердая | |
130...160 | Тоже | |
85...115 | Очень твердая, мылообразная |
Считается, чем глубже погружается конус в смазку, тем меньше ее консистенция. На основании полученных данных определяют марку исследуемой смазки.
Содержание отчета
1. Результаты испытаний числа пенетрации и температуры каплепадения пластичных смазок.
2. Выводы и заключение о сорте пластичной смазке и ее эксплуатационных свойствах.
Лабораторная работа № 5
РАСЧЁТ СИСТЕМ ПЛАСТИЧНОЙ СМАЗКИ
Цель работы: выполнить расчёт системы пластической смазки. Изучить оборудование и системы пластической смазки.
Согласно варианту, по исходным данным (табл. 5.1) рассчитать основные параметры станций пластичной смазки.
Общие положения
Централизованные системы пластичной смазки (ЦСПС).
В зависимости от частоты подачи смазки, расположения и количества узлов трения для смазки оборудования применяют в основном двухмагистральные ЦСПС с ручным приводом либо автоматические с электрическим приводом петлевого и концевого типа.
Для смазки отдельных машин и механизмов с небольшим числом смазываемых узлов трения применяют ЦСПС с ручным приводом.
Для обслуживания отдельных машин, нуждающихся в частой подаче смазки, а также в тех случаях, когда от одной системы необходимо смазывать несколько крупногабаритных машин, сосредоточенных в одном месте и не расположенных в одну линию, применяют ЦСПС петлевого типа.
Для обслуживания машин и механизмов, вытянутых в линию или расположенных на большой площади, применяются ЦСПС концевого типа.
Рис. 5.1.. ЦСПС концевого типа
Система работает следующим образом. Смазка из резервуара станции 3 плунжерным насосом через распределитель 2 подается в одну из магистралей Ml или М2, например, в магистраль M l, которая в этот период является напорной, и через сетчатые фильтры 1 по соответствующему трубопроводу 6 поступает в дозирующие питатели 4 и далее по подводящим трубопроводам 5 к точкам смазки А. Излишки смазки от дозирующих питателей по другой магистрали М2, которая является в этот период разгрузочной., через распределитель 2 возвращаются в резервуар станции.
После того как сработают все питатели, давление в напорной магистрали начинает повышаться и при достижении заданного срабатывает блок переключения 7, устанавливаемый в конце наиболее длинного ответвления главной магистрали, и подает сигнал на отключение двигателя насоса станции и переключение электромагнитного распределителя 2. Система готова к очередному циклу смазки; при этом магистраль М2 становится напорной, а магистраль M l –разгрузочной.
При наличии двух блоков переключения 7 на концах двух наиболее длинных ответвлений главной магистрали, один из блоков делают контрольным, и переключение распределителя 2 происходит после срабатывания контрольного блока.
Для подключения к системе узлов машин, смазка которых требуется через более длительные промежутками времени по сравнительно с другими машинами, на магистральных трубопроводах устанавливают двухмагистральные распределители 8.
При необходимости редких подключений машин к системе смазки применяют распределители с ручным управлением. Для отключения от системы смазки отдельных узлов трения или машин, работающих периодически, применяют запорные распределители 9. Они состоят из корпуса, золотника с двумя поршнями, открывающими и закрывающими перепускные отверстия, связанные с магистральными трубопроводами, и двух электромагнитов, связанных с золотником.
На резервуаре каждой станции 3 устанавливают два конечных выключателя типа ВК-300А, которые контролируют верхний и нижний уровень смазки в резервуаре. Заправка станций всей ЦСПС может осуществляться от централизованной автоматической системы или индивидуально с помощью перекачивающего шестеренного насоса типа НПШГ-200М.
Методика расчёта
Норму расхода пластичной смазки в единицу времени на единицу площади смазываемой поверхности определяют из выражения, см3/м2·ч,
(5.1)
где q1=II см3/м2·ч - максимальная норма расхода смазки для подшипников;
k1 - коэффициент, учитывающий зависимость нормы расхода смазки от диаметра подшипника, для подшипников скольжения;
(5.2)
для подшипников качения
(5.3)
Таблица 5.1
Исходные данные
№ | Тип подшипника | D, м | 1, м | n, об/мин | Fg, % | Тр, °C | N | L |
скольжения | 0,1 | 0,15 | ||||||
скольжения | 0,05 | 0,08 | ||||||
скольжения | 0,09 | 0,1 | ||||||
скольжения | 0,06 | 0,09 | ||||||
скольжения | 0,1 | 0,15 | ||||||
качения | 0,06 | 0,05 | ||||||
качения | 0,07 | 0,055 | ||||||
качения | 0,05 | 0,04 | ||||||
качения | 0,08 | 0,06 | ||||||
качения | 0,09 | 0,07 |
Примечание: D - внутренний диаметр подшипника, м; l - ширина подшипника, м; n -частота вращения подшипника, мин-1; Fg - суммарная площадь дефектов на поверхности контакта, %;
Тр - рабочая температура подшипника, °С; N -число узлов трения; L - длина трубопровода, м.
k2 - коэффициент, учитывающий частоту вращения подшипника n,
(5.4)
k3 - коэффициент, учитывающий качество поверхности контакта.
При хорошем качестве, когда суммарная площадь дефектов Fg на поверхности контакта не превышает 5 %, k3=1,0;
при Fg >5% k3=1,3;
k4 - коэффициент, учитывающий рабочую температуру подшипника Тр,
при Тр<75°С k4=1,0;
при Тр = 75...150°С k4=1,2
k5 - коэффициент, учитывающий нагрузку на подшипники, к5 = 1.0...1.1;
D - внутренний диаметр подшипника, мм; n - частота вращения подшип -ника, мин-1.
Объём пластичной смазки, периодически подаваемый питателем к узлу трения, определяют по формуле, см3,
(5.5)
где F – площадь контрольной поверхности, м;
(5.6)
где l - ширина подшипника, м; Т - период между двумя последовательными подачами смазки, ч. Его выбирают в зависимости от конструктивных особенностей и условий эксплуатации узлов трения (обычно Т = 0.4...2.0 ч). По значению V и числу узлов трения (числу отводов) выбирают тип питателя с ближайшим большим значением номинальной подачи в соответствии с табл. 10.2. Если объём пластичной смазки V существенно превышает подачу Vн, указанную в таблице 2, выбирают несколько питателей, суммарная номинальная подача которых будет равна или больше объёма пластичной смазки V. В этом случае количество пластичной смазки (см3), расходуемое за один цикл работы системы, определяют по формуле:
(5.7)
где - число питателей данного типа;
- номинальная подача питателя данного типа, см3/ход.
Суточный расход пластичной смазки определяют по формуле, см;
(5.8)
Производительность П н.р. насоса автоматической централизованной системы пластичной смазки (ЦСПС) вычисляют по формуле, см3/мин: (5.9)
где Р - коэффициент, учитывающий снижение производительности при износе насоса; Р = 0,75...0,8;
Тн - время нагнетания смазки, мин;
Тн = 5...20 мин.
По результатам расчётов Пн.р. принимают ближайшую производительность Пн.р. из табл.5.3.
Число автоматических ЦСПС определяют по формуле:
(5.10)
где - фактически производительность насоса (см /мин) выбранной станции смазки по табл. 5.3.
По результатам расчётов Nа округляют число автоматических ЦСПС до ближайшего целого значения.
Диаметр условного прохода трубопровода определяют по эмпирической формуле, мм:
(5.11)
где L – длина трубопровода, м (табл. 5.1)
Таблица 5.2.
Техническая характеристика питателей
Тип питателя | Ун, см /ход | Число узлов трения |
2-0200-1, 2-0200-1 -К | 2,0 | |
2-0200-2, 2-0200-2-К | 2,0 | |
2-0200-3, 2-0200-3-К | 2,0 | |
2-0200-4, 2-0200-4-К | 2,0 | |
2-0500-1, 2-0500-1-К | 5,0 | |
2-0500-2, 2-0500-2-К | 5,0 | |
2-0500-3, 2-0500-3-К | 5,0 | |
2-0500-4, 2-0500-4-К | 5,0 | |
2-1000-1, 2-1000-1-К | 10,0 | |
2-1000-2, 2-1000-2-К | 10,0 | |
2-2500-2, 2-2500-2-К | 25,0 |
Таблица 5.3
Технические характеристики станций густой смазки
Параметры | Тип станции петлевой, концевой | ||
0600-1-1-1 0600-2-1-1 | 0150-1-1-1 0150-2-1-1 | 0075-1-1-1 0075-2-1-1 | |
Производительность насоса, см3 /мин | 0,6·10+3 | 0,15·10+3 | 0,075·10+3 |
Номинальное давление, МПа | |||
Вместимость резервуара, дм3 | |||
Мощность электродвигателя, КВт | 1,1 | 0,75 | 0,37 |
Тип электродвигателя | ЧАХ80А4 | ЧАХ71В4 | ЧАА63В4 |
Масса, кг | |||
В горных машинах широко применяется централизованная система пластичной смазки - автоматическая или ручная. Пример ручной пластичной смазки приведен на рис. 5.2.
Принцип работы ручной пластичной смазки заключается в следующем. При качании рукоятки в станции смазка подаётся по одному из магистральных трубопроводов 5, который в это время является напорным. Второй трубопровод разгрузочный при этом соединён через золотниковый распределитель 2 с резервуаром станции и не находится под давлением. В процессе нагнетания срабатывают питатели 6 и к узлам трения подаются строго определённые порции смазки.
После срабатывания всех питателей давление в напорном трубопроводе начинает быстро возрастать и при достижении определённой величины, наблюдаемой по манометру и гарантирующей срабатывание всех питателей, нагнетания смазки рукояткой прекращается.
После завершения цикла подачи смазки вручную переключают золотниковый распределитель: система готова к очередному циклу работы, в период между циклами обе магистрали не находятся под давлением.
При очередном цикле магистральные трубопроводы меняются ролями: напорный становится разгрузочным и наоборот.
![]() |
Содержание отчета
1. Расчет системы пластичной смазки.
2. Принципиальная схема системы пластичной смазки.
3. Выводы и заключение о рациональной схеме пластичной смазки.
Лабораторная работа № 6
УПРОЧНЕНИЕ ДЕТАЛЕЙ МЕТОДОМ НАКАТЫВАНИЯ
Цель работы: Изучить оборудовать приборы, режимы и методику упрочнения деталей методом накатывания шариковым инструментом.
6.1. Общие положения.
Надежность и ресурс деталей машин в основном определяется качественным состоянием их поверхностного слоя, являющимся носителем конструктивных, технологических и эксплуатационных концентраторов напряжений, величина и характер которых представляют усталостное разрушение конструкции в эксплуатации.
Наиболее существенными с точки зрения эксплуатации свойствами поверхностного слоя деталей являются шероховатость, твердость и уровень остаточных напряжений.
Требуемые параметры качества поверхности и практически все важнейшие эксплуатационные свойства деталей машин могут быть обеспечены процессами упрочнения их методом поверхностного пластического деформирования, максимально проявляющими потенциальные возможности материала. Упрочнение методом ППД приводит к повышению поверхностной твердости, образованию в поверхностных слоях деталей остаточных напряжений сжатия и благоприятному изменению микрогеометрии поверхностей. В результате в зависимости от функционального назначения и условий эксплуатации деталей повышается их усталостная и контактная прочность, износостойкости и сопротивление коррозии, гидроплотности и маслоудерживающей способности.
Эффективность способов упрочнения методом ППД в сочетании с высокой производительностью и экономичностью делает их перспективными во всех отраслях промышленности – от приборостроения до тяжелого машиностроения.
Номенклатура деталей в машиностроении, подлежащих упрочнению методом ППД, весьма значительна, причем подавляющее большинство деталей приходится на долю автотракторного, авиационного, сельскохозяйственного и тяжелого машиностроения.
Анализ использования метода ППД для упрочнения деталей машин в отечественной и зарубежной практике показал многообразие применяемых способов упрочнения, подтверждает особую эффективность использования метода ППД для упрочнения деталей с концентраторами напряжений, подвергающихся знакопеременным, циклическим нагрузкам и дает возможность определить основные направления развития и расширения области внедрения метода ППД в отечественной промышленности, включающие:
1. Создание научнообщественной теоретической базы для углубленного исследования механизма ППД и его влияния на напряженно деформированное состояние материала детали в очаге деформирования с целью интенсификации процессов пластичного деформирования, оптимизации режимов упрочнения, повышения производительности и эффективности процессов упрочнения и создания для разработки системы управления качеством и режимом изделий машиностроения.
2. Разработка новых способов упрочнения деталей методом ППД, в том числе комбинированных, предусматривающих сочетание упрочняющего воздействия метода ППД с эффектами меча, лазера, электронного луча, химико-термической обработки, электрохимического нанесения композиционных покрытий и др.
3. Создание новых конструкций высокоэффективного деформирующего инструмента и устройств (раскатки, дорны), где величина усилия деформирования может регулироваться, вместо жестких инструментов, где величина и стабильность усилий деформирования обеспечивается за счет жестких требований к точности обработки упрочняемых поверхностей.
4. Создание гаммы специализированного упрочняющего оборудования, в том числе и ЧПУ, встраиваемого в автоматизированные, роботизированные технологические комплексы упрочнения деталей узлов в условиях серийного и массового производства, а так же средств неразрушающего контроля напряженно-деформированного состояния детали до и после упрочнения, встраиваемых в упрочняющее оборудование.
5. Организация систематизированных предприятий по разработке и централизованному изготовлению промышленных образцов упрочняющего инструмента, оборудования и средств контроля, отличаю
|
|
Биохимия спиртового брожения: Основу технологии получения пива составляет спиртовое брожение, - при котором сахар превращается...
Адаптации растений и животных к жизни в горах: Большое значение для жизни организмов в горах имеют степень расчленения, крутизна и экспозиционные различия склонов...
История развития пистолетов-пулеметов: Предпосылкой для возникновения пистолетов-пулеметов послужила давняя тенденция тяготения винтовок...
Общие условия выбора системы дренажа: Система дренажа выбирается в зависимости от характера защищаемого...
© cyberpedia.su 2017-2024 - Не является автором материалов. Исключительное право сохранено за автором текста.
Если вы не хотите, чтобы данный материал был у нас на сайте, перейдите по ссылке: Нарушение авторских прав. Мы поможем в написании вашей работы!