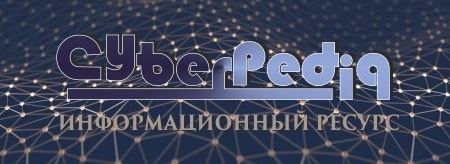
Общие условия выбора системы дренажа: Система дренажа выбирается в зависимости от характера защищаемого...
История развития хранилищ для нефти: Первые склады нефти появились в XVII веке. Они представляли собой землянные ямы-амбара глубиной 4…5 м...
Топ:
Марксистская теория происхождения государства: По мнению Маркса и Энгельса, в основе развития общества, происходящих в нем изменений лежит...
Теоретическая значимость работы: Описание теоретической значимости (ценности) результатов исследования должно присутствовать во введении...
История развития методов оптимизации: теорема Куна-Таккера, метод Лагранжа, роль выпуклости в оптимизации...
Интересное:
Аура как энергетическое поле: многослойную ауру человека можно представить себе подобным...
Что нужно делать при лейкемии: Прежде всего, необходимо выяснить, не страдаете ли вы каким-либо душевным недугом...
Как мы говорим и как мы слушаем: общение можно сравнить с огромным зонтиком, под которым скрыто все...
Дисциплины:
![]() |
![]() |
5.00
из
|
Заказать работу |
Содержание книги
Поиск на нашем сайте
|
|
Тип электрода по ГОСТ 9467 | Промышленные марки электродов |
Э42 | АНО-6*, АНО-6М*, АНО-1*, АНО-17*, ОЗС-23* |
Э42А | УОНИ-13/45, СМ-11*, ЦУ-6 |
Э46 | МР-3*, ОЗС-4*, АНО-4*, АНО-18*, АНО-24, ОЗС-6*, АНО-19, АНО-13*, ОЗС-21*, АНО-20*, ОЗС-12* |
Э46А | УОНИ-13/55К, ОЗС-22Р, ТМУ-46* |
Э50А | ЦУ-5, УОНИ-13/55, ТМУ-21У, УП-1/55*, ИТС-4С, ЦУ-7, АНО-11*, ОЗС-18*, АНО-9, АНО-10, КД-11*, ЦУ-8, ТМУ-50* |
* Электроды, помеченные звездочкой, предназначены для сварки как на переменном, так и на постоянном токе; остальные электроды - для сварки на постоянном токе обратной полярности.
Примечания. 1. Электроды ОЗС-18 применяются для сварки атмосферокоррозионностойкой стали (С345К) преимущественно толщиной до 15 мм.
2. Электроды ОЗС-12 наиболее пригодны для сварки тавровых соединений с получением мелкочешуйчатых вогнутых швов.
3. Электроды АНО-13 применяются для сварки вертикальных угловых, нахлесточных и стыковых (в разделку) швов способом «сверху-вниз». Обладают низкой стойкостью к образованию пор и кристаллизационных трещин.
4. Электроды АНО-19 особенно эффективны при сварке длинными швами листового металла толщиной 3-5 мм. Обеспечивают высокую стойкость сварных швов против образования пор и кристаллизационных трещин.
Электроды типа Э50А применяются для сварки всех групп металлоконструкций из сталей С345, С345К, С375, С390, С390К и С440 во всех климатических районах
Электроды с основным (фтористо-кальциевым) покрытием следует использовать в течение 5 суток после прокалки, остальные электроды - в течение 15 суток. По истечении указанного срока электроды должны быть перед применением повторно прокалены. Прокалка электродов может проводиться не более трех раз, не считая прокалки при их изготовлении. В случае хранения электродов в сушильном шкафу при температуре 60-100 °С срок использования их не ограничивается. Для определения размера «козырька» и прочности покрытия отбирается 10-12 электродов из 5-6 пачек и производится их расплавление в вертикальном положении при угле наклона электрода к шву 50-60°. Измерение «козырька» производится от торца стержня электрода до наиболее удаленной части оплавившегося покрытия.
|
Электроды, предназначенные для сварки как на переменном так и на постоянном токе - АНО-6, АНО-6М, АНО-1, АНО-17, ОЗС-23, CM-11, УП-1/55; МР -3 для сварки на постоянном токе обратной полярности - ЦУ-6, АНО-9, АНО-10, ЦУ-8;
Перед применением электродов независимо от наличия сертификата должны быть проверены сварочно – технологические свойства электродов каждой партии
Сварочно-технологические свойства электродов должны удовлетворять требованиям ГОСТ 9466. Основные из этих требований следующие:
дуга должна легко зажигаться и стабильно гореть; покрытие должно плавиться равномерно, без чрезмерного разбрызгивания, отваливания кусков и образования «козырька», препятствующих нормальному плавлению электрода во всех пространственных положениях; образование «козырька» из покрытия размером более 4 мм и отваливание кусочков нерасплавившегося покрытия от стержня является признаком брака; образующийся при сварке шлак должен обеспечивать правильное формирование шва и легко удаляться после охлаждения; в металле шва и наплавленном металле не должно быть трещин.
При неудовлетворительных сварочно-технологических свойствах электроды следует повторно прокалить в печи. Если после повторной прокалки технологические свойства электродов не удовлетворяют приведенным выше требованиям, то данную партию электродов использовать для сварки ответственных металлоконструкций нельзя.
Продолжительность и температура прокалки электродов:
- с рутиловым покрытием - 1час при 140-190град,
- с основным покрытием - 2часа при 360 -460 град,
- порошковой проволоки ППАН3 – 2 часа при 230 -250град,
|
- флюса АН -348А – 1 час при 300 -400град,
- флюса АН -42 – 4 часа при 630 -670 град.
Прокаленные электроды и порошковую проволоку следует выдавать на рабочее место в количестве, необходимом для работы сварщика в течение одной смены. При сварке конструкций из сталей с пределом текучести более 390 МПа (40 кгс/мм2) электроды, взятые непосредственно из прокалочной или сушильной печи, необходимо использовать в течение двух часов.
РД 34.15.132-96. Основные требования к подготовке кромок и сборке.
Элементы подготовки кромок, зазоры, размеры швов, допуски должны соответствовать ГОСТ 5264 –80 на ручную дуговую сварку покрытыми электродами, ГОСТ 14771 – на дуговую сварку в защитных газах (ГОСТ 14771 – УП: углекислый плавящимся, ГОСТ 14771 – Инп: ручная аргонодуговая сварка), ГОСТ 8713 - на автоматическую сварку под флюсом, ГОСТ 16037 – на сварку стыков трубопроводов (стальных), ГОСТ 11534 – на РДС под острыми и тупыми углами, ГОСТ 23518 – на сварку в защитных газах под острыми и тупыми углами.
Обработка кромок элементов под сварку и вырезка отверстий на монтажной площадке может производиться кислородной, воздушно-дуговой, плазменно-дуговой резкой с последующей механической обработкой поверхности реза. мм;
на элементах из сталей С235 до С285 - до удаления следов резки;
на элементах из сталей С345 до С375 - с удалением слоя толщиной не менее 1 мм;
на элементах из сталей С390 и С440 - с удалением слоя толщиной не менее 2 мм.
Огневую резку кромок деталей сталей С345 и более прочных при температуре окружающего воздуха ниже минус 15 °С нужно проводить с предв. подогревом металла в зоне реза до 100 °С.
Все местные уступы и неровности, имеющиеся на собираемых деталях и препятствующие их соединению в соответствии с требованиями чертежей, надлежит до сборки устранять зачисткой в виде плавных переходов с помощью абразивного круга или напильника.
Собранные элементы (изделия) должны прихватываться в нескольких местах ручной дуговой или механизированной сваркой. Все поступающие на сборку конструкции и детали должны иметь маркировку и сопроводительную документацию, подтверждающую их приемку отделом технического контроля.
Непосредственно перед сборкой кромки и прилегающие к ним участки на ширину 20 мм при ручной или механизированной дуговой сварке и не менее 50 мм при автоматической сварке а также места примыкания начальных и выводных планок должны быть тщательно зачищены от окалины, грязи, краски, масла, ржавчины, влаги, снега и льда. В процессе сборки должно быть исключено попадание влаги, масла и других загрязнений в разделку соединений и на прилегающие поверхности.
|
Зазоры при сборке должны быть равномерными по всей длине.
Длина прихваток должна быть не менее 50 мм и расстояние между ними не более 500 мм, а в конструкциях из стали с пределом текучести 440 МПа длина прихваток должна быть не менее 100 мм, расстояние между прихватками не более 400 мм. Высота прихватки должна составлять 0,3-0,5 высоты будущего шва, но не менее 3 мм.
Катет шва прихваток под РДС угловых и тавровых соединений должен быть равен катету шва, установленному рабочей документацией. В этом случае прихватки последующей переплавке не подлежат. Катет шва прихваток под автоматическую и механизированную сварку должен быть 3-5 мм и при наложении основного шва прихватка должна быть переплавлена.
Запрещается наложение прихваток у кромок, не подлежащих сварке, в местах пересечения швов и на краях будущих швов. Прихватки должны выполняться сварщиками, имеющими допуск на сварку подобных изделий, и по возможности теми, кто будет сваривать данное соединение, теми же сварочными материалами, которые будут применяться для сварки основных швов.
Прихватки должны быть полностью перекрыты и по возможности переварены при наложении основного шва. К качеству прихваток предъявляются такие же требования, как и к основному сварному шву. Все прихваточные и сварочные швы с недопустимыми дефектами необходимо удалить и заварить вновь. Удалять дефекты – механическим способом. Шлак с прихваток удалять обязательно. Св. материалы для сборки использовать те же, что и при сварке.
При сборочных работах запрещаются ударные воздействия на сварные конструкции из сталей:
с пределом текучести 390 МПа (40 кгс/мм2) и менее - при температуре ниже минус 25 °С;
с пределом текучести свыше 390 МПа (40 кгс/мм2) - при температуре ниже 0 °С.
При совмещении установки временных креплений и прихваток наложение последних следует производить после приварки креплений. Приварка вспомогательных элементов в разделку шва не допускается, они должны привариваться на расстоянии не менее 30 мм от кромки разделки (шва).
|
РД 34.15.132-96 Основные требования при сварке строительных конструкций
Сварка металлоконструкций зданий промышленных объектов должна проводиться сварщиками, имеющими удостоверения на право производства соответствующих сварочных работ, выданные им согласно требованиям «Правил аттестации сварщиков», утвержденных Госгортехнадзором России. Сварщики допускаются к тем видам работ, которые указаны в удостоверении.
Сварщики всех специальностей и квалификаций должны сдать испытания на 2-ю квалификационную группу по электробезопасности.
Сварщик, впервые приступающий к сварке в данной организации, должен перед допуском к работе независимо от наличия у него удостоверения на право производства соответствующих работ сварить пробные (допускные) образцы.
Конструкция и число пробных образцов устанавливаются руководителем сварочных работ в зависимости от типов производственных соединений и квалификации сварщика. Качество пробных сварных соединений определяется путем визуального контроля на предмет определения сплошности и формирования шва, а при необходимости (по усмотрению руководителя сварочных работ) - с помощью неразрушающих физических методов контроля.
Для сварки при температуре ниже минус 30 °С сварщик должен предварительно сварить пробные стыковые образцы при температуре не выше указанной. При удовлетворительных результатах механических испытаний пробных образцов сварщик может быть допущен к сварке при температуре на 10 °С ниже температуры сварки пробных образцов.
К руководству работами по сварке, контролю сварных соединений и операционному контролю допускаются ИТР, изучившие настоящий РД, соответствующие СНиП, рабочие чертежи изделий, производственно-технологическую документацию по сварке и методические инструкции по контролю.
Свариваемые поверхности конструкции и рабочее место сварщика должны быть ограждены от дождя, снега, ветра и сквозняков.
При температуре окружающего воздуха ниже минус 10 °С необходимо иметь вблизи рабочего места сварщика инвентарное помещение для обогрева, а при температуре ниже минус 40 °С сварка должна производиться в обогреваемом тепляке, где температура должна быть выше 0 °С.
. Электросварщик для допуска к работе должен иметь на рабочем месте следующий минимальный набор инвентаря и инструмента: защитный щиток или маску, рукавицы, очки с прозрачными стеклами, молоток, зубило или крейцмессель для отбивки шлака, стальную щетку, личное клеймо, ящик или сумку для электродов с отделением для электродных огарков, соответствующие шаблоны для проверки геометрии шва.
|
К сварке стыков разрешается приступать только после приемки мастером по сварке или прорабом по монтажу собранных стыков, о чем производится отметка в журнале сварочных работ.
Сварку деталей из сталей с пределом текучести 345 МПа и более (С345 и выше) следует выполнять без перерыва до заполнения хотя бы половины толщины шва или по всей его длине или на участке длиной не менее 800-1000 мм (при длине шва более 1 м). При вынужденных перерывах в работе необходимо обеспечить медленное и равномерное охлаждение стыка любыми доступными средствами (например обкладкой стыка листовым асбестом), а при возобновлении сварки стык должен быть подогрет до температуры 120-160 °С.
В качестве источника питания переменным током используются однопостовые сварочные трансформаторы. Для питания сварочной дуги постоянным током применяются однопостовые и многопостовые источники питания в виде преобразователей и выпрямителей.
При сварке постоянным током для регулирования величины тока в сварочную цепь должен включаться балластный реостат типов РБ-201, РБ-300, РБГ-502 и др.
Периодичность осмотров, проверок, ремонтов должна соответствовать требованиям паспортов или других документов.
Таблица 4.1
Периодичность осмотра и ремонта сварочного оборудования
Вид оборудования | Вид обслуживания и межремонтные сроки | ||
осмотр | текущий ремонт | капитальный ремонт | |
Сварочные трансформаторы и выпрямители | 2 раза в месяц | 4 раза в год | 1 раз в 3 года |
Сварочные преобразователи | еженедельно | 6 раз в год | 1 раз в 2 года |
Сварочные автоматы и полуавтоматы | ежедневно | 4 раза в год | 1 раз в 2 года |
Сечение провода для присоединения источника питания для сварки к сети следует подбирать по данным табл.1.1. При ручной дуговой сварке электрододержатель соединяют со сварочной цепью гибким медным проводом с резиновой изоляцией марок ПРД, ПРИ, КОГ 1, КОГ 2, сечение которого необходимо выбирать в зависимости от сварочного тока: при токе до 100 А - не менее 16 мм2, при 250 А - 25 мм2, при 300 А - 50 мм2. Длина гибкого провода должна быть не менее 5 м.
Таблица 1.1
Сечение провода для подсоединения к сети источников сварочного тока
Максимальный сварочный ток источника питания, А | Сечение медного* провода, мм2, при напряжении сети, В | |
- | ||
- |
* Сечение алюминиевого провода должно быть в 1,5 раза больше.
Швы длиной более 1 м, выполняемые ручной или механизированной сваркой, следует сваривать обратноступенчатым способом
При толщине стали 15-20 мм и более рекомендуется применять сварку способом «двойного слоя»
Сварка листовых объемных конструкций из стали толщиной более 20 мм, особенно из стали с пределом текучести 390 МПа и более, должна производиться способами, обеспечивающими уменьшение скорости охлаждения - каскадом или «горкой»
При сварке перекрещивающихся швов в первую очередь следует сваривать швы, выполнение которых не создает жесткого контура для остальных швов. Нельзя прерывать сварку в месте пересечения и сопряжения швов.
Стыковые швы должны выполняться в первую очередь, а угловые швы - во вторую.
При многослойной сварке разбивать шов на участки следует с таким расчетом, чтобы «замки» швов в соседних слоях не совпадали, а были смещены на величину не менее 20 мм.
При температуре окружающего воздуха ниже 0 °С РДС металлоконструкций независимо от марки свариваемой стали следует выполнять электродами с основным типом покрытия.
Ручную и механизированную дуговую сварку стальных конструкций разрешается производить без подогрева при температуре окружающего воздуха, приведенной в табл. 6.1, При более низкой температуре окружающего воздуха сварку надлежит производить с предварительным местным подогревом металла до 120-160 °С в зоне шириной не менее 100 мм с каждой стороны соединения.
Температура окружающего воздуха, при которой разрешается производить ручную и механизированную сварку стальных конструкций без подогрева Таблица 6.1.
Толщина свариваемых элементов, мм | Максимально допустимая температура окружающего воздуха, °С, при сварке конструкций | ||||
решетчатых | листовых объемных и сплошно-стенчатых | решетчатых | листовых объемных и сплошно-стенчатых | решетчатых и листовых | |
из стали | |||||
углеродистой | низколегированной с пределом текучести, МПа (кгс/мм2) | ||||
£ 390(40) | > 390(40) | ||||
До 16 | -30 | -30 | -20 | -20 | -15 |
Св. 16 до | |||||
-30 | -20 | -10 | При толщине более 25 мм предварительный местный подогрев следует производить независимо от температуры окружающего воздуха | ||
Св. 25 до 30 | -30 | -20 | -10 | ||
Св. 30 до 40 | -10 | -10 | +5 | ||
Св. 40 | +5 | +10 |
Места приварки монтажных приспособлений к элементам конструкций из стали толщиной более 25 мм с пределом текучести 390 МПа и более необходимо предварительно подогреть до 120-160°.
При температуре окружающего воздуха ниже минус 5 °С сварку шва следует производить без перерыва, за исключением времени, необходимого на смену электрода или электродной проволоки и зачистку шва в месте возобновления сварки.
Для сварки металлоконструкций должны применяться электроды диаметром 2,5-6 мм.
Диаметр - в зависимости от толщины свариваемого металла и положения шва в пространстве. Для сварки корневых слоев шва и для подварки шва с обратной стороны следует применять электроды диаметром 2,5-4 мм.
Режим сварки определяется в зависимости от диаметра электрода и положения шва в пространстве и должен уточняться для каждого конкретного случая. Потолочный участок шва следует выполнять электродами диаметром не более 4 мм.
Ориентировочные значения сварочного тока для электродов различных диаметров при сварке в нижнем положении
Покрытие электродов | Диаметр электрода, мм | Ток, А |
Основное | ||
(электроды УОНИ-13/55, ЦУ-5, ТМУ-21У, ЦУ-7, ИТС-4С и др.) | 90-110 | |
120-170 | ||
170-210 | ||
200-290 | ||
Рутиловое | ||
(электроды ОЗС-4, АНО-6, МР-3, ОЗС-6 и др.) | 90-130 | |
140-190 | ||
180-230 | ||
220-300 |
Примечание. При вертикальном и потолочном положениях шва ток должен быть уменьшен на 10-20 %.
Допускаемые отклонения принятых значений силы сварочного тока и напряжения на дуге не должны превышать ±5 % от номинальных.
Сварка ведется на возможно короткой дуге. Перед гашением дуги сварщик должен заполнить кратер путем нескольких частых коротких замыканий электрода и вывести место обрыва дуги на шов на расстоянии 8-10 мм от его конца. Последующее зажигание дуги производится на металле шва на расстоянии 12-15 мм от кратера.
Клеймо сварщика проставляется на расстоянии 40-60 мм от границы выполненного им (ими) шва сварного соединения: одним сварщиком - в одном месте, при выполнении несколькими сварщиками - в начале и конце шва. Взамен постановки клейм допускается составление исполнительных схем с подписями сварщиков.
РД 34.15.132-96. Дефекты сварного шва и контроль качества сварных соединений
. Операционный контроль сварочных работ выполняется производственными мастерами службы сварки и контрольными мастерами службы технического контроля (СТК).
Контроль качества сварных соединений стальных конструкций производится:
внешним осмотром с проверкой геометрических размеров и формы швов в объеме 100 %;
неразрушающими методами (радиографированием или ультразвуковой дефектоскопией) в объеме не менее 0,5 % длины швов.
Контроль размеров сварного шва и определение величины выявленных дефектов следует производить измерительным инструментом, имеющим точность измерения ±0,1 мм, или специальными шаблонами для проверки геометрических размеров швов. При внешнем осмотре рекомендуется применять лупу с 5-10-кратным увеличением.
При внешнем осмотре качество сварных соединений конструкций должно удовлетворять требованиям табл. П14.1:
- п одрезы допускаются: глубиной до 5 % толщины свариваемого проката, но не более 1 мм; вдоль усиления - глубина - не более 0,5 мм при толщине свариваемого проката до 20 мм и не более 1 мм - при большей толщине; местные подрезы поперек усиления длиной не более удвоенной длины оценочного участка. Непровары в корне шва сварных соединений доступных для сварки с двух сторон и соединений, выполненных на подкладках по результатам радиографического контроля допускаются, высотой – до 5 % толщины свариваемого проката, но не более 2 мм, длиной – не более удвоенной длины оценочного участка.
Непровар в корне шва сварных соединений без подкладок, доступных для сварки с одной стороны по результатам радиографического контроля допускаются, высотой – до 15 % толщины свариваемого проката, но не более 3 мм.
Выборочному контролю швов сварных соединений, качество которых согласно проекту требуется проверять неразрушающими физическими методами, должны подлежать участки, где наружным осмотром выявлены дефекты, а также участки пересечения швов. Длина контролируемого участка не менее 100 мм.
В соединениях, доступных сварке с двух сторон, а также в соединениях на подкладках суммарная площадь дефектов (наружных, внутренних или тех и других одновременно) на оценочном участке не должна превышать 5 % площади продольного сечения сварного шва на этом участке.
Ослабление сечения при обработке сварных соединений (углубление в основной металл) не должно превышать 3% толщины сввариваемого элемента, но не более 1мм.
Недопустимые дефекты, обнаруженные при контроле, должны быть устранены с последующим контролем исправленных участков.
Удаление дефектов следует проводить механическим способом - механизированной зачисткой или механизированной рубкой - с обеспечением плавных переходов в местах выборок.
Допускается удаление дефектных участков воздушно-дуговой, воздушно-плазменной или кислородной резкой с последующей обработкой поверхности выборки механическим способом.
На участках шва с трещиной должны быть засверлены сверлом диаметром 2-4 мм, после чего дефектный металл удаляется полностью.
Обнаруженные при внешнем осмотре, ультразвуковой дефектоскопии или радиографировании св. соединений металлоконструкций дефекты сварных швов должны исправляться следующим образом:
а) чрезмерные усиления сварных швов нужно удалить механическим способом, недостаточные усиления - исправить подваркой предварительно зачищенного шва;
б) наплывы удалить механическим способом и при необходимости подварить;
в) подрезы и углубления между валиками подварить, предварительно зачистив места подварки;
г) дефектные участки - трещины, незаплавленные кратеры, поры, неметаллические включения, несплавления и непровары - удалить до «здорового» металла, не оставляя острых углов, и подварить до получения шва нормального размера;
д) все ожоги поверхности основного металла сварочной дугой следует зачищать абразивным инструментом на глубину 0,5-0,7 мм.
Исправленные участки независимо от методов и объемов контроля, которым подвергаются такие же бездефектные сварные соединения, должны быть проконтролированы:
путем внешнего осмотра и магнитопорошковой или капиллярной дефектоскопии либо травления - выборки, не подвергавшиеся последующей заварке;
Исправление дефектов на одном и том же участке сварного соединения допускается проводить не более трех раз. Вопрос о возможности исправления дефектов на одном участке сварного соединения более трех раз должен решаться по согласованию с отраслевой специализированной организацией.
|
|
Таксономические единицы (категории) растений: Каждая система классификации состоит из определённых соподчиненных друг другу...
Механическое удерживание земляных масс: Механическое удерживание земляных масс на склоне обеспечивают контрфорсными сооружениями различных конструкций...
История развития пистолетов-пулеметов: Предпосылкой для возникновения пистолетов-пулеметов послужила давняя тенденция тяготения винтовок...
История развития хранилищ для нефти: Первые склады нефти появились в XVII веке. Они представляли собой землянные ямы-амбара глубиной 4…5 м...
© cyberpedia.su 2017-2024 - Не является автором материалов. Исключительное право сохранено за автором текста.
Если вы не хотите, чтобы данный материал был у нас на сайте, перейдите по ссылке: Нарушение авторских прав. Мы поможем в написании вашей работы!