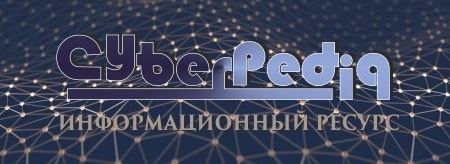
Механическое удерживание земляных масс: Механическое удерживание земляных масс на склоне обеспечивают контрфорсными сооружениями различных конструкций...
Эмиссия газов от очистных сооружений канализации: В последние годы внимание мирового сообщества сосредоточено на экологических проблемах...
Топ:
Оснащения врачебно-сестринской бригады.
Организация стока поверхностных вод: Наибольшее количество влаги на земном шаре испаряется с поверхности морей и океанов...
Проблема типологии научных революций: Глобальные научные революции и типы научной рациональности...
Интересное:
Финансовый рынок и его значение в управлении денежными потоками на современном этапе: любому предприятию для расширения производства и увеличения прибыли нужны...
Мероприятия для защиты от морозного пучения грунтов: Инженерная защита от морозного (криогенного) пучения грунтов необходима для легких малоэтажных зданий и других сооружений...
Инженерная защита территорий, зданий и сооружений от опасных геологических процессов: Изучение оползневых явлений, оценка устойчивости склонов и проектирование противооползневых сооружений — актуальнейшие задачи, стоящие перед отечественными...
Дисциплины:
![]() |
![]() |
5.00
из
|
Заказать работу |
Содержание книги
Поиск на нашем сайте
|
|
Как уже говорилось, отдельно испытать зону термического влияния на прочность затруднительно ввиду её малой ширины. Косвенную оценку прочностным свойствам можно дать, если измерить твёрдость зоны.
В зависимость от вида сварки от её условий, или от свариваемого металла, твёрдость зоны может превышать значение 700 HV. При сварке низколегированных сталей, или нелегированных, значение наибольшей возможной твёрдости в зоне термического влияния можно определить по формуле:
HVmax=90+1050C+47Si+75Mn+30Ni+31Cr, %
Для конструкционных сталей значение наибольшей допустимой твёрдости определяют косвенно, испытывая сталь на склонность к образованию холодных трещин при сварке и определяя значение ударной вязкости.
В сплошных сварных соединениях с удовлетворительными показателями ударной вязкости, наибольшие величины твёрдости составляют 340-350 HV. В случаях неудовлетворительного значения ударной вязкости, следует поменять режимы сварки или ввести последующую термообработку сварного соединения.
Наибольшее возможное значение твёрдости в зоне термического влияния (да и, вообще, в металле), зависит, в основном, от содержания углерода в составе стали. Углерод сильно влияет на свариваемость стали. Давая оценку свариваемости сталей, можно утверждать, что стали с низким содержанием углерода (менее 0,20%), свариваются без ограничений. А стали с повышенным содержание углерода (более 0,25%), уже необходимо сваривать с предварительным подогревом, последующей термообработкой (отпуском или отжигом) и контролем погонной энергии сварки.
Ударная вязкость в зоне термического влияния
В отличии от прочности, ударную вязкость зоны термического влияния определить возможно. Чаще всего испытания проводят типовой пробой, в соответствии с рекомендациями международного института сварки (МИС).
|
Для испытания необходимы образцы с острыми надрезами. Вершины надрезов находятся в околошовной зоне, на расстоянии 0,5-1,5 мм от линии сплавления. Для проведения испытания подбирают пластины с разной толщиной, при этом, свариваемые кромки должны иметь вид 1/2V или К, в этом случае, зона термического влияния получается более ровная.
Сварку выполняют ручной дуговой сваркой, выбирая любой способ сварки данного типа. Необходимо, также, обеспечить перпендикулярность линий проката листов к сварному шву. Применяют предварительный подогрев до температуры 125±15°C и последний наплавленный слой выполняют со стороны корня надреза.
При испытании листов с толщиной 10-12 мм, образцы вырезают по всей глубине сварного шва. При сварке листов большей толщины - на глубине, равной половине толщины сварного шва. Образцы вырезают по схемам, указанным на рисунке:
Режимы сварки необходимо выбирать одинаковые для всего сварного шва. Кроме того, процесс сварки должен обеспечивать минимальное, но постоянное проплавление кромок свариваемого металла.
Необходимую погонную энергию сварки можно определить по формуле:
Q=KUI/(1000V), кДж/см
Где U - напряжение на дуге, В;
I - сила сварочного тока, А;
V - скорость сварки, см/с;
К - КПД процесса сварки металла. К берётся в пределах 90-98% в случае сварки под флюсом, и 66-85% в случае ручной дуговой сварки или сварки в защитных газах плавящимся электродом. Если применяется сварка неплавящимся электродом в защитных газах, то КПД принимают равным 20-50%.
С помощью такой методики можно найти ударную вязкость в любом месте зоны термического влияния, обычно её величина в этой зоне пониженная. Понижение ударной вязкости - вопрос достаточно серьёзный. И в этом направлении проводились исследования по изучению влияния химического состава и технологии сварки на величину ударной вязкость сварного соединения.
|
В том случае, если в структуре зоны термического влияния преобладают феррит и бейнит, то температура перехода в хрупкое состояние определяется по формуле:
Т=5,4DIB-27(%Ni)+9, °C, где DIB - показатель упрочнения.
Если же в зоне преобладает переходная структура, то эта температура рассчитывается по формуле:
Т=-2,2DIB-25(%Ni)+22, °C
При исследованиях низколегированных сталей со следующим содержанием легирующих элементов (в %): углерода 0,06-0,22; меди не более 0,3; марганца 0,55-2,3; никеля не более 2,5; кремния 0,2-0,4; хрома не более 1,0; фосфора не более 0,025; молибдена не более 0,1; кремния не более 0,25; ванадия не более 0,1 была определена склонность стали к охрупчиванию околошовной зоны. Склонность к охрупчиванию выражается показателями РВА и РВВ.
Показатель РВА вычисляется в случае, если зона термического влияния имеет переходную структуру:
РВА=(%С) - 1/6(%Cu) - 1/11(%Mo)+4(%S)
Показатель РВВ определяется, если зона термического влияния имеет структуру верхнего бейнита и феррита:
Рвв=(%С)+1/10(%Mn)+1/6(%Cu)+1/12(%Cr)+1/13(%Mo) - 1/50(%Ni)
Источник: http://taina-svarki.ru/svarivaemost/otsenka-svarivaemosti-staley-formula-uglerodnogo-ekvivalenta.php
Вопрос 25
|
|
Типы оградительных сооружений в морском порту: По расположению оградительных сооружений в плане различают волноломы, обе оконечности...
Двойное оплодотворение у цветковых растений: Оплодотворение - это процесс слияния мужской и женской половых клеток с образованием зиготы...
Биохимия спиртового брожения: Основу технологии получения пива составляет спиртовое брожение, - при котором сахар превращается...
Папиллярные узоры пальцев рук - маркер спортивных способностей: дерматоглифические признаки формируются на 3-5 месяце беременности, не изменяются в течение жизни...
© cyberpedia.su 2017-2024 - Не является автором материалов. Исключительное право сохранено за автором текста.
Если вы не хотите, чтобы данный материал был у нас на сайте, перейдите по ссылке: Нарушение авторских прав. Мы поможем в написании вашей работы!