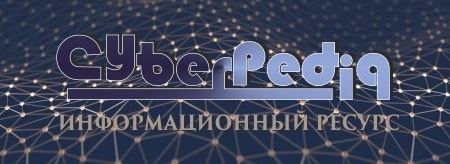
Индивидуальные очистные сооружения: К классу индивидуальных очистных сооружений относят сооружения, пропускная способность которых...
Организация стока поверхностных вод: Наибольшее количество влаги на земном шаре испаряется с поверхности морей и океанов (88‰)...
Топ:
Определение места расположения распределительного центра: Фирма реализует продукцию на рынках сбыта и имеет постоянных поставщиков в разных регионах. Увеличение объема продаж...
Отражение на счетах бухгалтерского учета процесса приобретения: Процесс заготовления представляет систему экономических событий, включающих приобретение организацией у поставщиков сырья...
Характеристика АТП и сварочно-жестяницкого участка: Транспорт в настоящее время является одной из важнейших отраслей народного...
Интересное:
Наиболее распространенные виды рака: Раковая опухоль — это самостоятельное новообразование, которое может возникнуть и от повышенного давления...
Распространение рака на другие отдаленные от желудка органы: Характерных симптомов рака желудка не существует. Выраженные симптомы появляются, когда опухоль...
Принципы управления денежными потоками: одним из методов контроля за состоянием денежной наличности является...
Дисциплины:
![]() |
![]() |
5.00
из
|
Заказать работу |
|
|
Изделия, выполненные методом шликерного литья, имеют влажность 35-40% и поэтому ее необходимо удалить с помощью сушки. При сушке происходит снижение размеров полуфабриката, его усадка.
Достаточно высушенные изделия выдерживают быстрое повышение температуры в начале обжига, благодаря этому снижается расход топлива при обжиге и повышается производительность сушильного оборудования.
Технологические отходы (формования и сушки), которые образуются при сушке, составляют от 10 до 12%. Эти отходы (сушье) поаторно применяются при изготовлении свежей массы и литейного шликера.
При однократном обжиге изделий процесс сушки составляет 35-40 % общей длительности производственного цикла.
В процессе сушки перемещение влаги ускоряется с повышением ее температуры, так как вязкость воды при 70 °С почти в 4 раза ниже, чем при 0 °С.
Процесс сушки изделий характеризуется скоростью и продолжительностью, изменением температуры и влагосодержания полуфабриката, усадкой и усадочными напряжениями.
При сушке различают период прогрева, период одинаковой скорости сушки, период снижающей скорости сушки и равновесного состояния(рис.).
Рис. 60. Кривые сушки полуфабриката I — влагоотдачи; II — скорости сушки; III — температуры материала; К — точка критической влажности.
В период прогрева происходит прогрев изделия от начальной температуры до температуры насыщенного теплоносителя (от 35-40 до 65-70 °С). Влагосодержание материала практически не изменяется. Равновесие между количеством теплоты, идущим на нагрев массы полуфабриката, и количеством, расходуемым на испарение влаги, устанавливается в конце периода. Чем выше скорость сушки, тем больше интенсивность испарения.
|
В период одинаковой скорости поступающая к поверхности по капиллярам из внутренних слоев вода равна количеству испаряющейся с поверхности полуфабриката влаге. Поверхность полуфабриката в течение второго периода сушки остается влажной. Вода поступает из внутренних слоев. Температура поверхности изделия (кривая III) остается неизменной. Теплота уходит на испарение влаги. Скорость сушки зависит от скорости перехода влаги из внутренних слоев изделия к поверхности. В конце второго периода скорость сушки резко снижается. В этот момент материал обладает критической влажностью (WKp) при данных параметрах теплоносителя. Происходит усадка, частицы уплотняются. Период характеризуется постоянным уменьшением массы. Возникновение градиента влажности приводит к появлению трещин и деформации. В конце второго периода испарение влаги перемещается внутрь изделия.
В период падающей скорости сушки и равновесного состояния полуфабриката усадка массы заканчивается. При стабильном объеме массы изделий идет испарение влаги пор и влаги, поглощенной из окружающего воздуха.
Сушку изделий останавлявают при достижении конечной влажности (Wкон)> величина, при которой масса изделия не изменяется и скорость сушки опускается до нуля.
Воздушная усадка начинается с поверхности изделия. Поверхностные слои сжимаются и испытывают растягивающие усилия относительно мокрых внутренних слоев. Растягивающие усилия в поверхностных слоях компенсируются пластическими деформациями. На поверхности полуфабриката появляются трещины если растягивающие усилия превысят прочность связи между частицами..
В условиях автоматизированного производства важным моментом является уменьшение длительности сушки. Воздушная усадка изменяется за счет вводимых в массы отощающих материалов.
Продолжительность сушки колеблется от 10-13 мин до 4 и более часов в искусственных сушилках и до 2 суток при сушке на открытых стеллажах.
Время сушки фаянсовых изделий сокращенается при цикличной подаче теплоносителя, который должен быть нагрет до температуры 140-320 ºC и направлен на изделия со скоростью 1,5-2 м/с.
Сушка тонкокерамических изделий осуществляется преимущественно двумя способами передачи тепла: конвекцией(источником тепла служит нагретый воздух) и излучением ((радиацией) источником тепла является электроэнергия).
|
Обжиг фаянсовых изделий
В производстве фаянсовых и фарфоровых изделий обжиг обеспечивает получение черепка с необходимыми физическими и химическими свойствами (высокая прочность, плотность, химическая и термическая устойчивость, белизна, просвечиваемость и др.) и закрепление декора на поверхности глазури или под глазурью. Режим обжига фаянсовых и фарфоровых изделий отличаются.
Фаянсовый или фарфоровые изделия подвергают преимущественно двукратному обжигу. Первый обжиг они проходят после сушки; затем их при необходимости декорируют, покрывают глазурью и отправляют на второй (политой) обжиг. Изделия, декорированный по глязури (надглязурное декорирование) подвергаются и третьему обжигу. Существует и однократный обжиг изделий.
Назначение первого обжига фаянса – придать черепку механическую прочность, необходимую для выполнения последующих технологический операций и эксплкатации готовых изделий.
При двукратном обжиге фаянсовой посуды, поступающей из формовочного цеха после сушки, первый обжиг проводят при 1230-1280 (для твердого фаянса), Второй обжи зделий, покрытых глязурью, - при 1500-1150.
Первый обжиг фаянсовых изделий разделяют на ряд периодов.
Первый период. Полуфабрикат досушивается с целью удаления воды из пор и гидроскопической влаги, которая остается в изделиях после сушки (2-4%, и выше). В этот период медленно поднимает температура до 250, далее изделие выдерживают (это необходимо для того, чтобы влага испарялась равномерно по всей толщине черепка изделия. Быстрый перегрев поверхности изделий при температуре интенсивного преобразования 200-240 приводит к их разрушению из-за высоких внутренних напряжений, которые возникают в черепке. Стремительный подъем температуры может привести ко взрыву изделия из-за неравномерности прогрева наружных и внутренних слоем черепка.
Рис. 54. Кривые режимов двукратного обжига фаянсовой посуды в туннельной печи: 1 — первого, 2 — второго
|
Второй период. Температура обжига поднимается до крайней температурной точки, которая обеспечивает получение изделий с заданными физико-химическими свойствами. Для фаянса она составляет 1130-1280. С повышением температуры обжига выше оптимальной для конкретной массы уменьшается качество физико-технических свойств продукта. Происходит сильное спекание черепка, что уменьшает пористость и не дает прикрепляться глазури при глазуровке.
В начале этого периода (300 начинается выгорание органических примесей (остатки растительного и животного происхождения из сырья), которое заканчивается при небыстром подъеме температуры до 450, при быстром – примерно 700-800. Скорость испарения конструкционной воды зависит от природы глинистых материалов, их свойств и скорости подъема температуры в интервале 450- 500. При это наблюдается небольшая усадка изделий (до 0,5-1%), не вызывающая больших напряжений.
Каолинит теряет кристалически связанную воду. На сколько быстро будет удаляться конституционная вода завит от природы глинистого сырья, его структуры и скорости подъема температуры в интервале 450-1000. При этом процессе наблюдается значительная усадка изделий (до 0,5-1%), не вызывающая больших напряжений.
При температуре 573 происходит модификационное превращение бетта-кварца в альфа кварц. Этот модификационный перомежуток, который сопутствуется увелечение объема кварца (+ 0,82%), происходит моментально. Объемное увеличение кварца уменьшает усадку, которая происходит за счет конструкционной воды. При обжиге толстостенный изделий при такой температуре (550-600) производят выдержку для обеспечения равномерного перехода кварца из одной модификации в другую по всей толщине черепка, иначе могут появиться микродеффекты в виде трещин.
При 700-800 в материале происходит диссоциация карбонатов CaCO3 и MgCO3 с удалением углекислого газа, которая прекращается при 950-1000, которая сопровождается увеличениеи пористости изделия.
При температуре от 200 до 400 в поры обжигаемого изделия проникает сажистый углерод из домовых газов. Выгорание углерода начинается при 400 и заканчивается при 1000. В изделии могут появиться вздутия из-за заплавления жидкой фазой части капилляров в том случае, если при 1000 в черепке не удаляется полностью углерод или сохраняются остатки воды.
|
При температуре 900-1050 появляютя первичные кристаллы муллита, которые способствуют увеличению прочности фаянсового черепка. Рост нитевидных кристаллов муллита активно происходит при температурах выше 1100.
При возрастании температуры до 1280 в черепке появляется некоторое количество стекловидной фазы (расплава), цементирущая зерна дегидратированного глинистого вещества и кварца в поверхностях соприкосновения. Черепок фаянсовых изделий, который обжигается при 1230-1280, упрочняется, сохраняя достаточную пористость (18-20%), которая необходима для глазурования.
Для того, чтобы обеспечить равномерное прохождение представленных выше процессов, располагаемых в различных местах по пересечению печного канала, производится выдержка при дохождении максимальной температуры.
С высокой скоростью протекает процесс охлаждения изделий до температуры 600-550 и здесь же заканчивается выдержкой, которая необходима для обратного модификационного перехода альфа кварца в бетта кварц. Затем производится ускоренное охлаждение. Полная усадка фаянсовых изделий составляет 9-13%
Второй обижиг фаянсовых изделий производят после наложения подглазурного декора и глазурования. Температуре плавления глазури соответствует температура второго обжига. Для декоративных изделий используется глазурь с низкой температурой плавления (1050).
Оба обжига фаянсовых изделий выполняют в окислительной газовой среде.Чтобы глазурь плавилась одновременно на всех черепках, перед последней выдержкой выравнивают температуру по всей площади канала. Протяженность выдержки в конце обжига и плавления глазури определяется плавкостью и вязкостью последней и варьируется в пределах 0,3-1ч. Слабому блеску глазури и неравномерному растеканию способствует малая выдержка. Образованию дефекта, как «сухой» край, может способствовать слишком длительная выдержка при заданной конечной температуре.
К первому обжигу не допускаются изделия, которые имеют следующие дефекты: помарки подглазурными красками, неблежнонанесенная подглазурная краска, щербины, трещины, зашибины, влажность, неплотно приставленные детали и т.д.
Полые изделия ставят на этажерки вагонеток в один ряд.
После первого обжига полые изделия вынимают из ячеек вагонетки и сортируют в ящики по ассортименту. При выгрузке полуфабрикат распределяют для того, чтобы отделить изделия, недопустимые к следующей обработке, а также выяснить характер дефекта и принять меры для устранения. Сортировку осуществляют путем визуального осмотра изделий и перезвонки (по краю ударяют палочкой, треснувшие изделия издают дребезжащий звук). По степени обжига изделия разделяют на три группы в зависимости от степени их водопоглощения (%): крепкообоженные – ниже 8,5; Нормально обоженные – 8,5 – 11,5; слабообоженные – 11,5. Слабообожженные изделия направляют на повторный обжиг, пережженные покрывают глазурью большей плотности. Отдельно ставят изделия с исправленными деффектами: наибольшими зашибами, которые можно зачистить шлифовальной шкуркой или абразивным камнем без искажения формы изделия; плохо оплавленными краями, которые нуждаются в повышенной зачистке поверхности; подрывом деталей, устраняемые подмазкой специальной мастикой.
|
Изделия, прошедшие подглазурное декорирование и глазурование загружаются в капсели и на этажерки вагонеток для второго обжига.
Полые и некотрые плоские изделия утанавливают на полки этажерочных вагонето или в капсели на клинышки или крестики таким образом, чтобы после обжига на глазури не не оставались заметные следы (плешины).
Обоженые изделия выгружают из капселей или этажерок на транспортные устройства и направляют на расортировку. Полые изделия составляют в ящики, сортируя по ассортименту и величине.
Браованные изделия (отходы производства) направляют в массозаготовительный цех на переработку.
Глазурование изделий
Глазурование изделий - процесс, обеспечивающий нанесение на изделие глазурной суспензии.
Глазурование изделий осуществляют погружением, поливом и пульверизацией.
В данной работе использовался метод полива.
Глазурь наносят на обожженные или хорошо высушенные изделия в виде тонкодисперсной водной суспензии, плотность которой изменяется в значительных пределах в зависимости от водопоглощения глазуруемого полуфабриката.
Глазурь внедряется в поры подсушенного изделия, закрепляясь на поверхности полуфабриката с определенной толщиной. Расплавляясь в процессе обжига, глазурь образует на поверхности изделий при дальнейшем охлаждении тонкий стекловидный слой толщиной 0,01-0,03 мм.
Прежде чем наносить глазурь, поверхность изделий должна быть обезжирена и отчищена. В противном случае из-за остатков пыли образуются дефекты, такие как «плешины», «наколы» и др. Чистку изделий выполняют в специализированных кабинах, которые снабженны вытяжной вентиляцией.
Перед глазурованием выполняют мокрую чистку изделий (рис. 50): неглазурованные участки покрывают машинным маслом или расплавленным парафином. Изделия устанавливают ножкой или краем на пропитанное жировым веществом техническое сукно или тонкий войлок конвейера.
![]() | Рис. 50. Мокрая зачистка глазури: а - общий вид, б - зачистка вибрацией, в - зачистка двумя противоположно движущимися лентами; 1 - изделие, 2 - транспортер, 3 - барабан, 4 - ванна с водой |
Глазурование поливом
Глазурование поливом используют чаще всего при глазуровании полых.
Рис. 52. Установка АСФ-30 для глазурования полых изделий: 1 — транспортер зачистки ножки и края изделий, 2 — транспортер-удлинитель, 3 — полуавтомат глазурования, 4 — насосная станция глазури, 5 — общая рама
Принцип работы установки АСФ-30 заключается в следующем. Изделие помещается на транспортерное устройство полуавтомата глазурования 3, проходит камеру обдувки и камеру глазурования. В камере обдувки с его поверхности сжатым воздухом убирается пыль. Глазурь наносится методом полива в камере глазурования. Далее изделие поступает на смоченную ленту транспортера-удлинителя 2. Влажная лента впитывает часть глазури с края изделия и отправляет его на зачистную ленту транспортера зачистки 1. Непрерывно движущаяся и вибрирующая лента зачистного транспортера выполняет окончательную чистку края изделия. Отглазурованные и зачищенные изделия снимаются в конце транспортера зачистки.
Все перечисленные операции производятся автоматически, кроме установки и съема изделий.
Сортировка изделий
В производстве фаянсовых изделий бытового назначения при исполнении отдельных технологических процессов возникают разнообразные виды брака, обнаруживаемые методом промежуточного контроля. Итоговую сортировку изделий выполняют после политого обжига. Для каждого ассортимента отводится специальное место. Сортировку зачастую производят в две стадии:
1) первичная сортировка изделий после политого обжига;
2) окончательная сортировка с исправленными дефектами.
При первой сортировке изделия разделяют на: сортные, которые после декорирования соответствуют предусмотренным в ТУ группам сортности; нуждающиеся в дополнительной обработке (зачистки, шлифования и полирования); дефектные.
На второй стадии сортировки изделия разделяют по сортам, отбирают для соответствующего декорирования. Внешний вид, показатели физико-механических свойств, величина и количество дефектов обработки при формовании, сушке, обжиге и декорировании являются критериями для отнесения изделий к тому или иному сорту.
Фаянсовые продукты сортируют методом внешнего осмотра, инструментов и приспособлений. В ходе сортировки дают оценку по их цвету, качеству глазурного покрытия, устанавливают отклонения от формы и размеров. Для упрощения и большей объективности сортировки используют эталоны.
Деформацию полых изделий устанавливают по разности высшего и минимального диаметров. Для этого используют вставляемыми в зазор специализированные калибры в виде ступенчатых клиньев с утолщением ступени постепенно на 0,5 мм. Изделия ставят на диск вверх дном и прижимают к нему вертикальным штифтом, который надавливается на центр дна. Сигнальные лампы включают в зависимости от степени искривления борта отдельные клавиши опускаются на различную глубину, которые показывают к какому сорту по признаку деформации следует приложить изделие.
Размеры изделий устанавливают при помощи линейки миллиметровой, толщиномера или штангенциркуля. Емкость изделий определяют в литрах воды; полых - по количеству воды, заполняющей изделие полностью. Объем воды рассчитывается мерным цилиндром.
Физико-механические свойства испытываемых изделий (белизна, твердость механическая прочность, термостойкость, химическая стойкость глазури, пористость) проверяют в лаборатории циклично выборочным путем (один раз в квартал). Требования к физико-механическим свойствам указываются в технических условиях.
Сортировка фаянсовых изделий, мало отличающихся весьма разнообразным ассортиментом, осуществляется вручную.
Маркировка изделий
На готовых фарфоровых и фаянсовых изделиях должны быть указаны марка завода, товарный знак, обозначающий их сортность (иногда приводится номер, сложность разделок), и цена.
Для маркировки фарфоровых изделий используют штампы (резиновые или желатиновые), на которых изображена марка завода и обозначен сорт изделия. Товарный знак может быть выполнен декалькоманией (переводная картинка). Товарный знак ставят в центре дна готовых изделий с внешней стороны надглазурными красками: на продукцию высшего и I сортов - красной краской, II - синей, III -зеленой. Сухую надглазурную краску смешивают со скипидаром и скипидарным маслом на палитре, разравнивают тонким слоем и с помощью штампа наносят на изделие. Товарный знак должен быть четким, без помарок. Закрепляется он на изделиях посредством обжига на температуру 820 °С.
Для клеймения холодным способом используют надглазурные краски, расправленные на связке, состоящей из терпентина (50%) и скипидарного масла (50 %) или вареной олифы (70 %) и терпентина (30 %). Краску смешивают со связующими веществами на палитре или стекле, разравнивают ровным тонким слоем и с помощью резинового штампа наносят на изделие. Закрепляется краска на изделиях без обжига через 3-5 ч.
При маркировке фаянсовых изделий марка завода (без указания сорта) наносится на поверхность неглазурованных изделий, прошедших первый обжиг, после сортировки и обдувки (обеспыливания). Маркировка проводится зеленой подглазурной краской с помощью резинового штампа с изображением марки завода (если изделия не были маркированы методом тиснения при их формовке). Сухую подглазурную зеленую краску смешивают с водой и глицерином и тщательно растирают курантом на стеклянной палитре. Соотношение компонентов подбирается в ходе работы таким образом, чтобы получался четкий, чистый и одинаковой интенсивности отпечаток по всей площади. Клеймо ставят в центре дна изделий, с внешней стороны
На готовые сортовые фаянсовые изделия наносят клеймо холодным способом, указывая соответствующий сорт (I сорт - красная надглазурная краска, II - синяя, III - зеленая), группу разделки, рабочий номер сортировщика и цену. Краски расправляют на палитре на вареной олифе или специальном лаке.
|
|
Индивидуальные очистные сооружения: К классу индивидуальных очистных сооружений относят сооружения, пропускная способность которых...
Историки об Елизавете Петровне: Елизавета попала между двумя встречными культурными течениями, воспитывалась среди новых европейских веяний и преданий...
Типы оградительных сооружений в морском порту: По расположению оградительных сооружений в плане различают волноломы, обе оконечности...
Особенности сооружения опор в сложных условиях: Сооружение ВЛ в районах с суровыми климатическими и тяжелыми геологическими условиями...
© cyberpedia.su 2017-2024 - Не является автором материалов. Исключительное право сохранено за автором текста.
Если вы не хотите, чтобы данный материал был у нас на сайте, перейдите по ссылке: Нарушение авторских прав. Мы поможем в написании вашей работы!