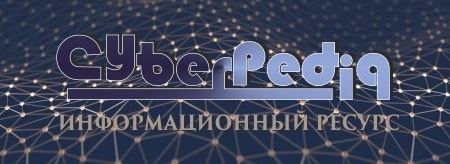
Кормораздатчик мобильный электрифицированный: схема и процесс работы устройства...
Автоматическое растормаживание колес: Тормозные устройства колес предназначены для уменьшения длины пробега и улучшения маневрирования ВС при...
Топ:
Оценка эффективности инструментов коммуникационной политики: Внешние коммуникации - обмен информацией между организацией и её внешней средой...
Процедура выполнения команд. Рабочий цикл процессора: Функционирование процессора в основном состоит из повторяющихся рабочих циклов, каждый из которых соответствует...
Характеристика АТП и сварочно-жестяницкого участка: Транспорт в настоящее время является одной из важнейших отраслей народного...
Интересное:
Аура как энергетическое поле: многослойную ауру человека можно представить себе подобным...
Инженерная защита территорий, зданий и сооружений от опасных геологических процессов: Изучение оползневых явлений, оценка устойчивости склонов и проектирование противооползневых сооружений — актуальнейшие задачи, стоящие перед отечественными...
Влияние предпринимательской среды на эффективное функционирование предприятия: Предпринимательская среда – это совокупность внешних и внутренних факторов, оказывающих влияние на функционирование фирмы...
Дисциплины:
![]() |
![]() |
5.00
из
|
Заказать работу |
|
|
ДИПЛОМНЫЙ ПРОЕКТ
О.ГД.130405.65.7.ДП.14.ПЗ.
Студента Губайдуллиной Гульфины Ринатовны
(фамилия имя отчество)
На тему: _ Проект обогатительной фабрики производительностью 1,5 млн.т/год для обогащения медной руды месторождения Юбилейное с массовой долей меди 2,34%
(полное наименование темы)
Состав дипломного проекта:
1 Пояснительная записка на ____ страницах
2 Графическая часть на ____ листах
Руководитель __________________________________ Доцент, к.т.н. Дегодя Е.Ю.
Консультанты: __________________________________ Доцент, к.т.н. Гришин И.А.
__________________________________ Доцент, к.э.н. Франюк Р.А.
__________________________________ Доцент, к.т.н. СтаростинаН.Н.
Рецензент Габбасов Б.М., доцент, к.т.н. каф. ГМ и ТТК
(подпись, дата, должность, ученая степень, звание, Ф.И.О.)
Отметка нормоконтролера _________________ / Гришин И.А. / (подпись, дата) (ФИО) | Студент ___________________ (подпись) «____» _____________ 2014г. |
МИНИСТЕРСТВО ОБРАЗОВАНИЯ И НАУКИ РОССИЙСКОЙ ФЕДЕРАЦИИ
ФЕДЕРАЛЬНОЕ ГОСУДАРСТВЕННОЕ БЮДЖЕНТОЕ ОБРАЗОВАТЕЛЬНОЕ УЧРЕЖДЕНИЕ ВЫСШЕГО ПРОФЕССИОНАЛЬНОГО ОБРАЗОВАНИЯ
«МАГНИТОГОРСКИЙ ГОСУДАРСТВЕННЫЙ ТЕХНИЧЕСКИЙ
УНИВЕРСИТЕТ ИМ. Г.И. НОСОВА»
Кафедра обогащения полезных
ископаемых
УТВЕРЖДАЮ:
Заведующий кафедрой
____________ /__________/
«____» ____________ 2014 г.
ДИПЛОМНЫЙ ПРОЕКТ
ЗАДАНИЕ
Тема: Проект обогатительной фабрики производительностью 1,5 млн.т/год для обогащения медной руды месторождения Юбилейное с массовой долей меди 2,34%
Студенту Губайдуллиной Гульфине Ринатовне
(фамилия имя отчество)
Тема утверждена приказом №____от__________ 20___ г.
Срок выполнения «_____» ____________________ 20___ г.
Исходные данные к работе:__________ Производительность 1,5 млн.т/год ___________________________________________ Массовой долей меди 2,34%
|
_____________________________________________________________________________
_____________________________________________________________________________
_______________________________________________________________________________
_____________________________________________________________________________________________________________________________________________________________
_____________________________________________________________________________________________________________________________________________________________
_____________________________________________________________________________
Перечень вопросов, подлежащих разработке в дипломном проекте:
Характеристика перерабатываемого сырья
Обоснование и расчет схем рудоподготовки и основного оборудования
Выбор и расчет технологической схемы обогащения
Выбор и расчет основного и вспомагательного оборудования
Реагентное хозяйство
Хвостовое хозяйство
Опробование, контроль и автоматизация
Безопасность и экологичность
Анализ технико-экономических показателей и обоснование экономической целесообразнос- ти принятых в проекте решений
Графическая часть:
Лист 1_Генеральный план
Лист 2_План и разрез корпуса крупного дробления
Лист 3_Качественно-количественная и водно-шламовая схема
Лист 4_План главного корпуса
Лист 5_Разрез главного корпуса
Лист 6 Специальная часть
Лист 7_Технико- экономические показатели
_
Консультанты по работе (с указанием относящихся к ним разделов):
Доцент, к.т.н. Дегодя Е.Ю. Характеристика перерабатываемого сырья
Доцент, к.т.н. Гришин И.А. Опробование, контроль и автоматизация
Доцент, к.э.н. Франюк Р.А. Анализ технико- экономических показателей и обоснование экономической целесообразности принятых в проекте решений
Доцент, к.т.н. Старостина Н.Н. Безопасность и экологичность
Руководитель:______________________________________ /_________________/
(подпись, дата)
Задание получил:___________________________________ /_________________/
(подпись, дата)
Реферат
Данный проект представляет собой комплекс технических решений и документов, необходимых для осуществления строительства и эксплуатации обогатительной фабрики. В проекте подробно рассмотрены вопросы выбора схемы и технологических показателей процесса обогащения с технико-экономическим обоснованием выбранного оборудования.
|
Проект обогатительной фабрики разработан для переработки медной руды Юбилейного месторождения. В пояснительной записке описывается район месторождения, дается характеристика полезного ископаемого. На основании обзора и анализа технологии обогащения данного типа минерального сырья производится обоснованный расчет схемы для проектируемой обогатительной фабрики.
В проекте также рассматривается такие разделы как безопасность и экологичность, водоснабжение, автоматизация, экономика.
В результате расчета схемы обогащения, массовая доля меди в медном концентрате составляет 20,43% при извлечении меди 90,03%.
Дипломный проект содержит: 110 страниц пояснительной записки, 49 таблиц, 7 приложений, 7 листов формата А1.
Ключевые слова: дробление, грохочение, обогащение, флотация, оборудование, схема, минерал, местрождение, концентрат, хвосты, извлечение, реагенты, сгущение, фильтрование, классификация.
Содержание
Введение……………………………………………………………………………………...…..7
1. Основная часть………………………………………………………………………......….…8
1.1 Характеристика минерального сырья…………………………………………………….8
1.1.1 Местоположение месторождения…………………………………………...……....8
1.1.2 Стратиграфия………………………………………………………………………....8
1.1.3 Тектоника……………………………………………………………………………..9
1.1.4 Вещественный состав……………………………………………………………….10
1.1.5 Текстурно-структурные особенности……………………………………………...12
1.1.6 Физико-механические свойства……………………………………………………13
1.1.7 Степень разведанности и запасы…………………………………………………...14
2. Обоснование, выбор и расчет схемы рудоподготовки……………………………..…....16
2.1 Обоснование схемы рудоподготовки……………………………………………..…...16
2.1.1 Расчет схемы рудоподготовки и выбор оборудования…………………………..19
2.1.2 Расчет схемы измельчения и выбор оборудования………………………………24
3. Обоснование и выбор технологической схемы обогащения сульфидных медных руд……………………………………………………………………………………………….42
3.1 Выбор схемы обогащения………………………………………………………….…..42
|
3.1.1 Практика переработки аналогичного сырья…………………………………...…42
3.1.2 Обоснование схемы обогащения……………………………………………….....44
3.1.3 Расчет качественно-количественной схемы…………………….………………45
3.1.4 Расчет водно-шламовой схемы………………………………….….……………..46
4. Выбор и расчет основного и вспомогательного оборудования……………………….....49
4.1 Выбор и расчет основного оборудования……………………………………...…….49
4.2 Выбор и расчет вспомогательного оборудования……………………………..….…53
5. Обоснование реагентного режима………………………………………………….….…..63
5.1 Характеристика применяемых реагентов ………………………………….….…......63
5.2 Индивидуальное задание………………………………...……………………..…......67
6. Хвостовое хозяйство ОФ……………………………………………………………….…70
7. Опробование, контроль и автоматизация технологического процесса…………..…….79
8. Безопасность и экологичность………………………………………………………….…84
9. Анализ технико-экономических показателей и обоснование экономической целесообразности принятых в проект решений………………………………………………90
Заключение………………………………………………………………………………….…109
Список литературы……………………………………………………………………………110
Введение
Горнорудная промышленность играет особо важную роль в народном хозяйстве страны. Развитие тяжелой и легкой промышленности во многом определяется ростом добычи руд черных, цветных и редких металлов.
Высокий уровень горнорудной промышленности залог технического прогресса во всех странах.
Предусматривается широкое развитие подземной добычи руд черных и цветных металлов с использованием высокопроизводительных машин и механизмов, расширение применения совершенных комплексов самоходного оборудования.
Ставится задача на повышение извлечения цветных металлов из руд, комплексность использования сырья, сокращение потерь руды в недрах при ее добыче. Внедрение высокопроизводительных схем обогащения руд.
Решение этих проблем требует дальнейшего улучшения подготовки инженерных кадров, широкого развития научных исследований и быстрого внедрения их в производство, так как одним из решающих факторов повышения экономики народного хозяйства является рост экономической эффективности производства отраслей горнодобывающей промышленности.
|
Основная часть
Стратиграфия
Юбилейное месторождение медно- цинковых руд приурочено к южному участку Ирандыкского синклинория и залегает среди вулканогенных пород Баймак – Бурибаевской свиты верхнесилурийского возраста.
Условно месторождение можно разделить на три стратиграфических уровня:
- верхний, включающий в себя Первую, Вторую и Третью рудные залежи с зоной развития золотосодержащих бурожелезняковых руд;
- средний – рудные залежи Четвертая и Пятая;
- нижний - самый глубокий (глубина залегания 1265 м) и наиболее значимый по запасам представлен Шестой рудной залежью.
Первое рудное тело залегает под рыхлыми отложениями на глубинах от 57,7 до 84,8 м от поверхности. Форма рудного тела линзообразная, длина его простирается на 66,25м, ширина по падению 32м, простирание северо – западное по аз.320, падение к северо – востоку под углом 72°. Руды находятся в зоне вторичного сульфидного обогащения, окисленные, вкрапленные, в висячем боку - медно –цинковые, в лежачем – медные.
Второе рудное тело залегает на глубине 325-363 м, длина его по простиранию – 117,8м, ширина 95м, простирание – субширотное, падение субгоризонтальное, форма пластообразная. Руды первичные сплошные и вкрапленные медные, вкрапленные медно –цинковые.
Третье рудное тело залегает на глубинах 167-245м. Форма рудного тела пластообразная, простирание тела северо–западное по аз.320, длина его 818м, ширина до 160м, залегание верней части субгоризонтальное, нижняя имеет падение к северо-востоку под углом до 45°.
Четвертая рудная залежь является слепой. Она расположена в 700м к с.в. от Второй залежи и залегает на глубинах от 295,4 до 585,8 м и прослежена на расстоянии 925 м. Мощность ее колеблется от 0,4м до 101,4м, составляя в среднем 270м. Ширина рудного тела колеблется от 150 до 300м. Морфология залежи пластообразная, общее простирание с. з. по аз.320°, падение сравнительно пологое на с. в. под углом от 10 до 40°, на небольших участках до 70°, склонение на северо-запад под углом 20-30°.
Пятая залежь расположена в висячем боку Четвертой, выше её нижней выклинки на 20-80 м и имеет линзообразную форму. Представлена первичными сплошными, вкрапленными медными и медно-цинковыми рудами и сплошным серным колчеданом. Длина по простиранию (аз.280°) 261м, длина по падению от 100 до 160м.
Шестая рудная залежь наиболее значимая по запасам руды, залегает на глубинах 550-1265 м. Залежь представлена семью рудными телами (6,7,8,9,10,11,12), расположенными в 500 м севернее четвертой залежи. Основная масса колчеданных руд находится в шестом рудном теле. Максимальная мощность залегания составляет 202м, в поперечных и продольных разрезах рудное тело имеет форму ассиметричной линзы со средней мощностью 54м.
|
Тектоника
Юбилейное месторождение расположено в восточном крыле одноименной горст антиклинарии, сложенной вулканогенно-осадочными породами.
С Восточной тектонической зоной сопряжены тектонические зоны северо-восточного простирания до рудного заложения, которые контролировали размещение субвулканических липарит-дацитов и поступление гидротермальных растворов, с которыми связано образование медно-колчеданных руд. Тектонические движения неоднократно возобновлялись в пострудное время, что еще более осложняет строение месторождения. Пострудная тектоника характеризуется образованием милонитов, среди которых присутствуют обломки липарит-дацитовых порфиров и закатанные обломочки колчеданных руд.
Рудные залежи Юбилейного месторождения локализованы в пределах Восточной рудоносной зоны, которая в виде широкой, меридионально вытянутой полосы измененных пород и имеет крутое восточное падение с Востока и Запада рудоносная зона ограничена крутопадающими разломами.
Вещественный состав
На Юбилейном месторождении выделены два промышленных сорта (типа) руд: медные и медно-цинковые.
На месторождении незначительно преобладают медные руды (52% от общих запасов). Собственно цинковые руды составляют всего 1-2% от общих запасов, поэтому они не выделены в отдельный промышленный сорт, а включены единичными скважинами и в отдельный промышленный сорт также не выделены.
К промышленному сорту медных руд относится пиритовый, халькопирит-пиритовый, халькозин-халькопирит-пиритовый природные(минеральные) типы руд.
Минералогический состав руд
Руды верхних горизонтов отличается высоким содержанием вторичных сульфидных медных минералов.
Главные рудообразующие сульфидные минералы- пирит, халькопирит, халькозин, сфалерит. Нерудные минералы представлены кварцем, серицитом, хлоритом и кальцитом. Руды представлены сплошными вкрапленными разновидностями, для них характерны брекчиевидные, пятнистые, полосчатые вкрапленные текстуры (таблица 1).
Пирит - является основным рудообразующим минералом, составляющим 44-45 % от объема руды. Микроскопическое изучение рудных шлифов позволило выделить, по крайней мере, две разновозрастные модификации пирита, различающиеся размерами и характером срастания с другими минералами. Ранний пирит I характеризуется средне-крупнозернистой структурой с размером отдельных зерен 0,2-2,0 мм. Специфика последующих метасоматических рудообразующих процессов привела к тому, что характер срастаний с более поздним халькопиритом и сфалеритом колеблется от простого к сложному с развитием коррозионных границ. Соответственно, в случае простого срастания минералы раскрываются быстрее, чем те же самые минералы в случае коррозионных границ.
С другой стороны, поздний пирит II, характеризующийся идиоморфными кубическими очертаниями с простыми прямолинейными границами окажется весьма затруднительным для раскрытия из-за очень маленьких размеров зерен, основная часть которых не превышает 5-10 мкм. Поскольку данный пирит ассоциирует и со сфалеритом, и с халькопиритом, в продуктах измельчения будет иметь место определенная часть соответствующих практически не раскрываемых сростков.
Халькопирит - занимает 12-13 % от объема руды и является основным медьсодержащим минералом, образование которого тесно связано с образованием пирита. Поэтому наиболее часто наблюдаются ассоциации халькопирита I с пиритом, в которых халькопирит в основном играет подчиненную роль - в виде включений 5-100 мкм находится в пирите. Также наблюдаются крупные поля халькопирита, достигающие 0,5 мм, содержащие либо реликты раннего пирита неправильной формы, либо поздний тонкозернистый пирит, размеры которого не превышают 5-10 микрон.
Сфалерит - цинксодержащий минерал, доля которого в руде составляет 7-8 %. Для сфалерита характерно наличие обширных (до 0,6 мм) чистых минеральных полей в области шлифа, а также полей сфалерита (до 0,3 мм), зараженных эмульсионной вкрапленностью халькопирита. Доля сфалерита с эмульсионной вкрапленностью халькопирита составляет 15-20 % от общего количества сфалерита.
Для сфалерита наиболее характерны ассоциации с пиритом I и пиритом П. В первом случае имеют место как простые, так и сложные коррозионные границы, во втором - простые, прямолинейные, как следствие идиоморфных кристаллографических очертаний пирита I. Но, как показал минералогический анализ продуктов измельчения руды на 10 и 20 минут, высока доля сростков сфалерита с пиритом II, что доказывает трудность раскрытия сростков, содержащих вкрапленность и агрегаты тонкозернистого (5-10 мкм) пирита. Характерная для части сфалерита эмульсионная вкрапленность халькопирита является очень тонкой, составляя всего 1-3 мкм с расстоянием между включениями 15 мкм.
Незначительная часть зерен сфалерита окислена, что выражается в частичной ковеллинизации поверхности.
Борнит - медьсодержащий минерал, который в виду весьма небольшого содержания в руде (<1%) практического интереса не представляет. В рудных шлифах отмечаются единичные выделения борнита неправильных очертаний размерами 5-25 мкм. Соответственно, в продуктах измельчения руды наблюдаются единичные зерна соответствующих сростков.
Блеклая руда, представленная теннантитом, также имеет второстепенный характер (<1%) и находится в тесной ассоциации с халькопиритом, наблюдаясь в нем в виде неправильных включений размерами 20 мкм округлой формы.
Галенит - являясь второстепенным минералом (<1%), в основном находится в ассоциации со сфалеритом, наблюдаясь в нем в виде редких включений размерами 10-50 мкм. Наблюдаются также единичные зерна халькопирита, содержащие редкие включения галенита размерами 20-35 мкм.
Рациональный фазовый анализ пробы руды на медь и цинк показал, что руда 35 рудного тела является первичной сульфидной. Медь в руде на 94,5-95,8% представлена первичными, на 3,2-4,3 % - вторичными и на 0,2-1,2 % окисленными минералами.
Таблица 1- Минеральный состав руд
Рудные минералы | Нерудные минералы |
Пирит FeS2 | Кварц SiO2 |
Халькопирит CuFeS2 | Серицит KAl2(Si3Al)O10(OH)2 |
Сфалерит ZnS | Кальцит СаСО3 |
Борнит Cu5FeS4 | |
Теннантит Cu12As4S12 | |
Ковеллин CuS |
Таблица 2 - Химический состав пробы медной руды
№ | Элемент | Содержание, % |
медь | 2,5 | |
цинк | 0,44 | |
свинец | 0,052 | |
железо | 34,72 | |
сера | 36,7 | |
золото, г/т | 1,81 | |
серебро, г/т | 13,32 |
Расчет схем измельчения
Выбор и расчет мельниц
При выборе мельниц следует решить вопрос о том, будут ли применяться мельницы со стальными дробящими телами или мельницы самоизмельчения. Это вопрос решается технико-экономическим сравнением вариантов схем дробления и измельчения.
Из мельниц со стальными дробящими телами на обогатительных фабриках преимущественно применяются стержневые, шаровые с разгрузкой через решетку, шаровые с центральной разгрузкой.
Стержневые мельницы дают более высокую по сравнению с шаровыми производительность при измельчении до 1-3 мм, но они не могут эффективно работать, когда требуется получить более мелкий продукт. Эти мельницы широко применяются при грубом измельчении (до 0,5-3 мм) мелковкрапленных руд.
Из шаровых мельниц наиболее распространены мельницы с разгрузкой через решетку. Они более производительны и выдают измельченный продукт с меньшим содержанием шламов, чем мельницы с центральной разгрузкой. Удельная производительность мельниц с разгрузкой через решетку на 10-15% выше производительности мельниц с центральной разгрузкой.
Недостатком мельниц с разгрузкой через решетку является сравнительная сложность их конструкции и поэтому более высокая стоимость на единицу массы и на единицу полезного объема. Эксплуатация мельниц с решеткой также сложнее и дороже.
Недостатки мельниц с центральной разгрузкой – меньшая удельная производительность и более сильное ошламование измельчаемых продуктов. Мельницы с центральной разгрузкой должны устанавливаться в тех случаях, когда переизмельчение продукта является полезным для последующей его обработки.
В практике отмечается более широкое применение мельниц с центральной разгрузкой. Этому сильно способствовало замене спиральных классификаторов на гидроциклоны.
Для проектируемой схемы измельчения рекомендовано применять шаровые мельницы с центральной разгрузкой, которые работают в замкнутом цикле с гидроциклонами на Хайбуллинской ОФ и показывают хорошие результаты работы.
Рудное самоизмельчение и полусамоизмельчение широко применяется в современной практике обогащения медных, медно – молибденовых, алмазных, золотых и других руд.
Свойства руды предопределяют схему самоизмельчения и мероприятия, которые должны быть предусмотрены в ней для борьбы с накапливанием кусков критического размера и для интенсификации процесса.
Одностадиальные схемы с полным рудным само - или полусамоизмельчения применяются сравнительно редко, поскольку не всегда выполняются для этого условия:
1) достаточное и относительно постоянное содержание в руде крупнокускового (+100 мм) твердого материала, выполняющего роль измельчающей среды;
2) отсутствие в руде более крепких, чем основная масса разностей, вызывающих образование и аккумулирование в мельнице рудного самоизмельчения гальки критических размеров отрицательно влияющих на эффективность измельчения.
Наибольшее распространение получили двухстадиальные схемы самоизмельчения (для более тонкого измельчения более 65% класса – 74 мкм). Во второй стадии используются шаровые или рудногалечные мельницы. Схемы с шаровым измельчением во второй стадии нашли применение при строительстве крупных обогатительных фабрик, а также по данной схеме работает и Хайбуллинская ОФ. В данной схеме мельницы самоизмельчения заменяют стадии среднего и мелкого дробления и подготавливают руду к шаровому измельчению. Эта схема рациональна для влажных глинистых руд, которые невозможно раздробить сухим способом до крупности питания шаровых мельниц. Хотя схемы с включением между стадиями дробилки мелкого дробления обладают большей гибкостью и универсальностью, и являются наиболее надежными в эксплуатации при переработке руд с неустойчивым характером их физических свойств.
Таким образом выбираем мельницу самоизмельчения для первой стадии измельчения.
Расчет стадий доизмельчения
Выбор схемы обогащения
Расчет водно-шламовой схемы
Целью расчета водно-шламовой схемы является обеспечение оптимальных отношений R=Ж: Т в технологических операциях схемы, определение количеств воды, добавляемой в операции и уходящей с конечными продуктами обогащения, составление баланса воды и определение ее удельного расхода.
Основные соотношения:
Rп =(100-p)/p; (21)
где R п – отношение жидкого к твердому по массе в операции или в продукте;
p – содержание твердого в продуктах,%.
Wn=Rn Qn; (22)
где W п – количество воды в операции или в продукте, м3/ч;
Q п – масса продукта,т/ч.
Vn=Wn+Wn/δ (23)
где Vn – объем пульпы в операции или в продукте, м3/ч;
δ – плотность руды,т/м3.
По уравнению баланса определяют количество воды, добавляемой в операцию
ΣWпр+L=ΣWух, (24)
где - сумма количеств воды, приходящей в операции с продуктами, м3/ч;
L – количество воды, добавляемой в операцию, м3/ч;
- сумма количеств воды, уходящей из операции с продуктами, м3/ч.
Составляем вспомогательную таблицу 12, куда записываем численные значения исходных показателей.
Таблица 12- Исходные показатели для расчета водно-шламовой схемы
Оптимальные значения R, которые необходимо обеспечить | Нерегулируемые значения R |
RI=0,43, RII=0,52, RIII=1,85, RIV=0,65, RV=2,33, RVI=0,54, RVII=3, RVIII=3, RIX=0,67, RX =3, RXI =3,17, RXII=4, RXIII=5,25, R41=6,66 | R13=2,12,R19=2,33,R25=2,R31=1,86, R34=2,33, R37=3, R38=3,23 |
Рассмотрим пример расчета водно-шламовой схемы для операции межцикловой флотации рис.11.
Исходные данные:
R10=1,13; Q10=194 т/ч; R13=2,00; Q13=3,72 т/ч; Q14=190,28 т/ч; Rоп=2,19
Lсв
10
Межцикловая флотация
13 14
к-т хвосты
Рисунок 11- Схема операции межцикловой флотации
м3/ч;
м3/ч;
м3/ч;
м3/ч;
В операцию межцикловой флотации необходимо добавить воду в количестве:
L= Wоп –W10=424,86-219,22=205,57 м3/ч; (25)
Рассчитываем значения объёмов пульпы для всех продуктов схемы:
V10 = 424,86+(194/3,94)=409,52 м3/ч;
V13 = 7,44+(3,72/3,94)=8,83 м3/ч;
V14 = 417,42+(190,28/3,94)=465,72 м3/ч.
Аналогично рассчитываются и все другие операции. Данные наносятся на технологическую схему рис.10 приложение А.
Рассчитав схему, составляют баланс воды по фабрике, где объемы подаваемой воды с исходным сырьем и в операции должны совпадать с объемами воды, уходящими из операций.
Таблица 13. Баланс общей воды на фабрике
Баланс схемы по воде | |||
Поступает в процесс | м3/ч | Выходит из процесса | м3/ч |
с исходной рудой | 10,67 | Cu концентрат м/ц флота- ции | 7,44 |
в I-ую стадию измельчения | 72,75 | Cu концентрат III перечистки | 20,67 |
в межцикловую флотацию | 205,57 | отвальные хвосты 1 | 411,48 |
в I-ую основную Cu флотацию | 27,84 | отвальные хвосты 2 | 325,51 |
в 1-ую ст. классификаци | 31,44 | отвальные хвосты 3 | 61,93 |
во II-ую Основную Cu флотацию | 168,65 | ||
во 2-ую стадию классифи- кации | 41,75 | ||
в доизмельчение 2 стадии | 5,54 | ||
в I-ую Cu перечистку | 23,17 | ||
во II-ую Cu перечистку | 61,92 | ||
в III-ую Cu перечистку | 11,69 | ||
в промпродуктовую фло- тацию | 30,16 | ||
Итого: | 827,03 | 827,03 |
Общий расход воды на 1 тонну обогащаемого сырья:
(26)
Удельный расход воды по фабрике q, м3/т будет
(27)
q
Выбор и расчет флотомашин
На Хайбуллинской обогатительной фабрике установлены пневмомеханические флотомашины РИФ. Для нашей фабрики выбираем флотомашины РИФ.
Определяем минутный дебит пульпы в каждой операции флотации.
, м3/мин, (28)
где Vопер – объем пульпы, поступающей в операцию, м3/ч.
Определяем оптимальный объем камеры флотомашины. Требуемый объем флотомашин рассчитывается исходя из времени пребывания пульпы в камере флотомашины. Для пневмомеханических машин Vтреб.
, м3, (29)
где Vтреб – требуемый объем камеры;
t=2÷5 мин – время пребывания пульпы в одной камере.
Число камер определяется по формуле
(30)
где n – количество камер;
Vкам - объем камеры принятой флотомашины, м3;
tфл – время флотации, мин.
Рассчитаем объемы камер флотомашин и их количество для операции «Межцикловая флотация»
м3/мин;
Выбираем флотомашину объемом камеры 25 м3.
n= 17,88*4/25*0,85=3,4 принимаем n=4;
Таким образом, в операции «Межцикловая флотация» принимаем к установке 4 камеры флотомашины типа РИФ 25.
Аналогичным образом производим расчет флотационных машин для других операций. Результаты расчетов представлены в таблице 14
Таблица 14- Результаты расчета флотомашин
Наименование операции | V,м3/ч | tфл, мин | Vтреб, м3 | Тип фл. машины | Число камер | Vкам,м3 |
Межцикловая флотация | 268,53 | 17,88 | РИФ 25 | |||
I Основная Cu флотация | 465,71 | 23,28 | РИФ 25 | |||
II Основная Сu флотация | 288,63 | 14,43 | РИФ 25 | |||
П/п Cu флотация | 249,75 | 8,32 | РИФ 6,3 | 6,3 | ||
I Cu перечистка | 273,63 | 9,1 | РИФ 16 | |||
II Cu перечистка | 47,06 | 3,9 | РИФ 16 | |||
III Cu перечистка | 27,01 | 2,25 | РИФ 16 |
Выбор и расчет сгустителей
В зависимости от конструкции и расположения привода механизма разгрузки сгустителя их разделяют на сгустители с центральным приводом и с периферическим приводом. Сгустители с центральным приводом находят наиболее широкое распространение на обогатительных фабриках.
Рассчитаем необходимую площадь сгущения и количество сгустителей по формулам
(31)
(32)
где Q ─ производительность по твердому в сгущаемом продукте, т/ч;
q ─ удельная производительность, т/(м2·ч);
─ площадь зеркала сгустителя, м2.
Q39=20,00 т/ч (по данным качественно – количественной схемы);
q=0,33 т/(м2*ч) – принимаем удельную производительность по данным практики действующей фабрики.
Примем к установке сгуститель «СЕТКО» Ø9 м.
Требуется установка 1 сгустителя «СЕТКО» Ø9 м с центральным приводом.
Расчет приемного бункера
Руда месторождения «Юбилейное» добывается открытым способом и доставляется на фабрику автосамосвалами БелАз 7540 грузоподъемностью 40т. Так как производительность фабрики 210 т/ч, тогда количество автосамосвалов, требуемых в единицу времени, определяется как:
N= (37)
Полезная емкость приемного бункера:
V= ; (38)
где Кн – коэффициент неравномерности подачи автосамосвалов на разгрузку;
N=5 - количество автосамосвалов, подаваемых на разгрузку в единицу времени;
Ра - грузоподъемность автосамосвала т, Ра = 40т.
Ρ- насыпная плотность груза т/м3, Ρ=2,54 т/м3.
Количество ячеек в бункере принимаем, равной единице.
Длина ячеек приемного бункера согласуется с шириной кузова автосамосвала, а ширина бункера зависит от способа разгрузки (при односторонней составляет от 5,5м до 6,5м, при двухсторонней до 7,5м). Ширина кузова БелАз составляет 7540-5240мм. Разгрузка в бункер производится с одной стороны. На основании выше изложенного, принимаем длину ячеек, равную 5,8м, а ширину -5,8м.
Для крупнокусковых грузов (а|mах>300м) наименьший размер выпускного отверстия определяется по формуле:
b≥k*(a|max+80)*tgφ=2,4*(800-80)* tg450=1665мм; (39)
где k=2,4-опытный коэффициент для рядовых грузов;
a|max=800 - крупность максимального куска, мм;
tgφ=450- угол естественного откоса.
Принимаем размер выпускного отверстия 1600 мм.
Угол наклона стенок (α) принимаем равной 500 (угол естественного откоса 450)
Объем пирамидальной воронки бункера , м3:
(40)
где A = B = 5,8 м – длина и ширина ячейки бункера в плане (в свету),
» 2,8 м. (41)
= 49,46 м3=50 м3
Определим общую высоту бункера.
Требуемый объем бункера (Vтр) 28м3, объем пирамидальной части- 49,46м3, тогда объем прямоугольной части бункера определяется как:
Vпр= Vпир -Vтр=50-28=22м3 (42)
Высота прямоугольной части бункера определяется как:
h= =
принимаем высоту прямоугольной части бункера равной 1м.
Общая высота приемного бункера (Н,м) будет равна сумме высот пирамидальной и прямоугольной части высот бункера:
Н=hпир*hпрям=2,8+1=3,8м. (43)
Исходные данные для расчета
На основании практики работы Хайбуллинской обогатительной фабрики принимаются следующие исходные данные:
1) Минералогический и гранулометрический составы твердого; средневзвешенная крупность частиц твердой фазы dcp=0034 мм;
2) Отношение Ж:Т в хвостах по технологии R=W/Q=4;
3) Производительность фабрики по хвостам, Qn м3/ч; Qn = V;
Q1=Qгод/365*24*0,88=1500000/365*24*0,88=194 т/ч;
Qхв=Q1*γхв=194*0,89=172,66 т/ч;
;
4) Плотность хвостовой пульпы, γ п, т/м3; ,т/м3
;
5) Плотность твердого в пульпе, γт, т/м3; γт=3,94т/м3 ;
6) Расстояние транспортирования хвостов L = 2км=2000м;
7) Геодезическая отметка хвостохранилища=411м;
8) Геодезическая отметка главного корпуса фабрики=419м.
Расчет систем напорного гидравлического транспорта заключается в определении критической скорости потока, диаметра трубопровода гидравлического уклона и необходимого напора для транспортирования пульпы. По результатам расчета производится выбор необходимого оборудования.
Гидротранспорт пульпы происходит при скорости потока v, равной или большей критической скорости vкр. Под критической скоростью пульпы подразумевают скорость, при которой еще происходит перемещение твердых частиц без отложения неподвижного слоя на нижней стенке трубы. Основной целью расчета гидравлического транспорта является выбор такого стандартного диаметра трубопровода, при котором движение гидросмеси (при заданном расходе и консистенции пульпы и гранулометрическом составе хвостов) происходит при скорости равной или выше критической, характеризующейся минимальными потерями на трение.
До настоящего времени отсутствует универсальная методика расчета гидравлического транспорта. Предложено несколько эмпирических формул для определения критической скорости потока, пользоваться которыми рекомендуется при определенных характеристиках гидросмеси.
В этих формулах приняты следующие обозначения:
D - диаметр трубопровода, м;
Wn - гидравлическая крупность хвостов,м/с;
Наброски и зарисовки растений, плодов, цветов: Освоить конструктивное построение структуры дерева через зарисовки отдельных деревьев, группы деревьев...
Общие условия выбора системы дренажа: Система дренажа выбирается в зависимости от характера защищаемого...
Организация стока поверхностных вод: Наибольшее количество влаги на земном шаре испаряется с поверхности морей и океанов (88‰)...
Индивидуальные и групповые автопоилки: для животных. Схемы и конструкции...
© cyberpedia.su 2017-2024 - Не является автором материалов. Исключительное право сохранено за автором текста.
Если вы не хотите, чтобы данный материал был у нас на сайте, перейдите по ссылке: Нарушение авторских прав. Мы поможем в написании вашей работы!