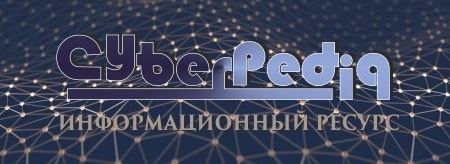
Индивидуальные очистные сооружения: К классу индивидуальных очистных сооружений относят сооружения, пропускная способность которых...
Опора деревянной одностоечной и способы укрепление угловых опор: Опоры ВЛ - конструкции, предназначенные для поддерживания проводов на необходимой высоте над землей, водой...
Топ:
Характеристика АТП и сварочно-жестяницкого участка: Транспорт в настоящее время является одной из важнейших отраслей народного хозяйства...
Особенности труда и отдыха в условиях низких температур: К работам при низких температурах на открытом воздухе и в не отапливаемых помещениях допускаются лица не моложе 18 лет, прошедшие...
Оценка эффективности инструментов коммуникационной политики: Внешние коммуникации - обмен информацией между организацией и её внешней средой...
Интересное:
Средства для ингаляционного наркоза: Наркоз наступает в результате вдыхания (ингаляции) средств, которое осуществляют или с помощью маски...
Мероприятия для защиты от морозного пучения грунтов: Инженерная защита от морозного (криогенного) пучения грунтов необходима для легких малоэтажных зданий и других сооружений...
Финансовый рынок и его значение в управлении денежными потоками на современном этапе: любому предприятию для расширения производства и увеличения прибыли нужны...
Дисциплины:
![]() |
![]() |
5.00
из
|
Заказать работу |
|
|
Общие сведения о контроле
Контроль – процесс установления соответствия между состоянием объекта (параметра) и заданными на него нормами.
В качестве объекта контроля могут выступать:
1) изделия;
2) документация;
3) процессы;
4) технологические среды;
5) организации, предприятия.
В соответствии и Госстандартом 16504-81 виды контроля могут классифицироваться:
1) по стадии существования;
2) по этапу процесса;
3) по полноте охвата;
4) по влиянию на объект контроля;
5) по применению средств контроля.
На практике и в нормативно-технической документации понятие «контроль» отличается от понятия «измерение».
Измерение – нахождение значения физической величины опытным путём с помощью специальных технических средств. В процессе измерения мы получаем количественную величину. Науку об измерениях и методах обеспечения точности измерения называют метрологией. Главная задача метрологии в производстве – метрологическое обеспечение производства. Все метрологические характеристики имеют определённое числовое выражение и определённую форму записи.
- допустимое значение систематической погрешности;
- математическое ожидание систематической погрешности;
- среднеквадратическое отклонение систематической погрешности;
- номинальное значение входного сопротивления;
- максимальное входное сопротивление.
Контроль | ||||
По этапу жизненного цикла | По этапу процесса производства | По применению средств контроля | По полноте охвата | По влиянию на объект контроля |
Производственный Эксплуатационный Проектный | Входной Операционный Приёмочный Инспекционный | Измерительный Органолептический Визуальный Регистрационный | Сплошной Выборочный Летучий Периодический Непрерывный | Разрушающий Неразрушающий (Параметрический и Диагностический) |
|
Если получаемая при первичном контроле информация имеет чётко выраженное числовое значение, то такой контроль является измерительным контролем. Погрешность измерительного контроля будет иметь две составляющие: погрешность измерения и погрешность, обусловленную невоспроизводимостью технологического процесса.
.
На этапе эксплуатации может добавиться составляющая, определяющая деградацию изделия:
.
Если первичная информация не имеет числового значения, то такой контроль называется прямым контролем.
В ряде случаев используют органолептический контроль. Он осуществляется с помощью органов чувств.
Если в процессе измерения параметры регистрируются, то такой контроль называется регистрационным.
Контроль, осуществляемый с помощью органов зрения – визуальный.
Операционный контроль характеризуется следующими особенностями:
1) широкое разнообразие методов и средств (широкая номенклатура ЭС);
2) рост относительной трудоёмкости контрольных операций в общей трудоёмкости изготовления изделия (может достигать 30-50%);
3) постепенная замена процессов контроля продукции на процессы контроля технологических процессов.
Контроль печатных плат
Контроль внешнего вида
Контроль внешнего вида основных элементов печатных плат производится для определения соответствия геометрических размеров требованиям ТУ и чертежей, а также для выявления грубых дефектов:
Рисунок 1 - Грубые дефекты печатного рисунка.
Уровень требований к печатному рисунку определяется минимальным расстоянием между проводниками, класса точности и т.д.
Класс точности Ширина проводника
1 0,75
2 0,45
3 0,25
4 0,15
5 0,1
К дефектам печатного рисунка относят рваные края, вздутия, отслоения, разрывы, короткие замыкания, резко выраженные тёмные пятна, загрязнения и др.
|
Рисунок 2 - Особенно нежелательные дефекты печатного рисунка.
а, б – короткое замыкание (устраняется выжиганием); в – разрыв (устраняется использованием «балочек»).
Рисунок 3 - Варианты расположения отверстия и контактной площадки.
а – наилучший вариант, б – допустимый вариант, в – недопустимый вариант.
Элементы печатного рисунка должны иметь покрытие, указанное в чертеже.
Химические методы контроля
Капельный метод
1) механическая очистка;
2) химическая очистка;
3) капаем растворителем в определённое место; выдерживаем 1 минуту; снимаем каплю фильтровальной бумагой; вытираем; наносим новую каплю и т.д. до тех пор, пока не обнаружим подслой.
Толщина покрытия определяется:
,
где n – число капель; h – толщина покрытия, снимаемого (вытравливаемого) одной каплей.
Таблица 1.
Слой | Подслой | Раствор | Концентрация раствора, г/л | h, мкм |
Медь | - | Серебро азотнокислое | 1,0…1,2 | |
Серебро | Медь | Йод металлический | 0,5 | |
Калий йодистый | ||||
Никель | Медь | Железо хлорное | 0,7 | |
Медь сернокислая |
Струйный метод
В данном случае заготовка или плата защищается хлорвиниловой лентой, в которой имеются отверстия диаметром 1,5…2,0 мм. В это отверстие направляется струя борфтористоводородной кислоты (концентрация 142 г/л) под углом 45°. Фиксируется время, за которое слой растворится.
.
Таблица 2.
Значения для плёнок различных металлов
Температура раствора, °С | Плёнки металлов | |||
Медь | Никель | Серебро | ПОС | |
0,641 | 0,333 | 0,344 | - | |
0,749 | 0,467 | 0,380 | - | |
0,926 | 0,521 | 0,403 | 0,11 | |
1,042 | 0,575 | 0,420 | - | |
1,220 | 0,671 | 0,450 | - |
Физические методы контроля
Прямой метод измерения заключается в измерении толщины платы до нанесения покрытия и после.
Метод взвешивания
Плату взвешивают до нанесения покрытия и после. Определяют массу покрытия по формуле:
,
где - коэффициент,
- масса покрытия; S – площадь печатной платы;
- плотность покрытия.
Метод хорды
В этом случае используется шлифовальный круг, с помощью которого делается надрез в металлическом покрытии.
Рисунок 6 - Метод хорды
.
Метод индикаторной головки
Рисунок 7 - Метод индикаторной головки
Контроль по микрошлифам
|
Данный метод является наиболее достоверным для металлизированных отверстий и внутренних соединений проводников.
Рисунок 10 - Контроль по микрошлифам
Контроль пористости
В металлизированных покрытиях могут образовываться поры: сквозные или замкнутые. Контролю пористости подвергаются только ламели печатных плат, так как они не покрываются защитным покрытием.
Для контроля можно использовать химические методы.
В ряде случаев используют электрофизический метод контроля. В этом случае используется фильтровальная бумага. Она пропитывается десяти процентным раствором хлористого кадмия, высушивается, помещается в пяти процентный раствор сернокислого натрия до образования равномерного жёлтого цвета (CdS), бумага промывается и тщательно высушивается.
Рисунок 11 - Электрофизический метод контроля пористости.
Пропуская постоянный ток , выдерживаем при давлении
30 секунд. Если есть пора, то ионы меди осаждаются в этом месте на бумагу.
Таблица 3.
Виды брака печатных плат
№ | Вид брака | Эскиз изделия | |
Годного | Бракованного | ||
Вздутие фольги | ![]() | ![]() | |
Отсутствие металлизации в отверстии | ![]() | ![]() | |
Отслоение СПФ | ![]() | ![]() | |
Отслоение контактных площадок и проводников | ![]() | ![]() | |
Крупнозернистое покрытие | ![]() | ![]() | |
Отслоение гальванического покрытия | ![]() | ![]() | |
Смещение отверстий | ![]() | ![]() | |
Заусенцы | ![]() | ![]() | |
Узкие контактные площадки | ![]() | ![]() | |
Порваны проводники | ![]() | ![]() | |
Трещины в металлизированных отверстиях | ![]() | ![]() | |
Недостаточная металлизация отверстий | ![]() | ![]() | |
Заросшие отверстия | ![]() | ![]() | |
Протрав проводников | ![]() | ![]() | |
Отслоение фольги | ![]() | ![]() | |
Ошибка в фотооригинале | ![]() | ![]() | |
Короткое замыкание из-за расплавленного припоя | ![]() | ![]() | |
Неметаллические включения в диэлектрике | ![]() | ![]() | |
Продолжение таблицы 3 | |||
Металлические включения в диэлектрике | ![]() | ![]() | |
Смещение контактных площадок | ![]() | ![]() | |
Деформация плат | ![]() | ![]() | |
Плохая растекаемость припоя | ![]() | ![]() | |
Нарушение металлизации при штамповке | ![]() | ![]() | |
Смещение стекла при экспонировании | ![]() | ![]() | |
Усадка материала | ![]() | ![]() | |
Перевёрнутое зеркальное изображение | ![]() | ![]() | |
Наволакивание смолы в отверстия | ![]() | ![]() | |
Риски и царапины на материале | ![]() | ![]() | |
Не выдержаны размеры при штамповке | ![]() | ![]() | |
Поломка сверла | ![]() | ![]() | |
Залипание смолы на контактные площадки | ![]() | ![]() | |
Неверный диаметр отверстий | ![]() | ![]() | |
Подтравливание проводников | ![]() | ![]() | |
Неверный диаметр базовых отверстий | ![]() | ![]() | |
Занижена толщина покрытия | |||
а) медной фольги | ![]() | ![]() | |
б) защитного | ![]() | ![]() | |
Продолжение таблицы 3 | |||
Разбиты базовые отверстия | ![]() | ![]() | |
Непротрав | ![]() | ![]() | |
Недостаточное раздублирование | ![]() | ![]() | |
Не выдержаны размеры при фрезеровании плат по контуру | ![]() | ![]() | |
Не нанесено защитное технологическое покрытие | ![]() | ![]() |
|
Контроль степени вакуума
Для контроля низких давлений (от 13,3 Па до 0,13 Па, соответственно от до
мм.рт.ст.) обычно используют термокондуктометрические вакуумметры. Чаще всего используют термопарные манометры. Схематично термопарный манометр можно представить следующим образом:
Рисунок 12 - Термопарный манометр
Принцип действия такого манометра основан на зависимости теплопроводности газа от давления. При уменьшении давления остаточных газов теплопроводность газа уменьшается. При этом количество теплоты, отводимой от спая в окружающее пространство, будет уменьшаться, соответственно, будет возрастать температура спая. Чем ниже давление остаточных газов, тем выше термоэдс.
Достоинства термопарных манометров:
· возможность контроля давления любых газов;
· простота конструкции;
· Возможность непрерывного контроля давления.
Недостаток: тепловая инерция.
Ионизационный манометр
Используется для измерения давлений в диапазоне от 0,0013Па ( мм.рт.ст.) до 0,13Па.
Принцип действия такого монтажа основан на зависимости степени ионизации газа от его давления. Схематично ионизационный манометр можно изобразить:
Рисунок 13 - Ионизационный манометр
Катод нагревается, возникает эмиссия электронов. В цепи аноа возникает электронный ток . Большая часть электронов проходит сквозь витки анода, но так катод отрицательно заряжен, то возвращаются на анод. При столкновении с атомами остаточных газов происходит ионизация последних. Положительные ионы устремляются к коллектору, следовательно, возникает ионный ток
. Таким образом, давление остаточных газов можно определить из формулы:
,
где P – давление остаточных газов, k – чувствительность манометра.
Контроль температуры
Для контроля температуры можно использовать контактные и бесконтактные методы. К контактным относятся: термопарный, терморезистивный… (); к бесконтактным: пирометрические методы.
|
Пирометр регистрирует тепловое излучение нагретого тела. Выделяют три группы пирометров:
1) радиационные;
2) яркостные;
3) фотометрические.
Радиационные пирометры воспринимают тепловое излучение во всём спектральном диапазоне. Принцип действия основан на законе Стефана-Больцмана:
где - коэффициент, который зависит от материала и свойств линзы,
- фактическая степень черноты тела.
Радиационные пирометры позволяют измерить температуру в очень широком диапазоне (до 2000 ).
Яркостные пирометры используют монохроматическое излучение. Принцип действия основан на измерении интенсивности излучения и сравнении её с интенсивностью излучения абсолютно чёрного тела на той же длине волны. Этот пирометр измеряет яркостную температуру. Яркостной температурой тела в лучах с длиной волны называют такую температуру абсолютно чёрного тела, при которой яркости обоих тел в свете одной и той же длины волны равны между собой.
Наибольшее распространение в этой группе пирометров нашли пирометры с исчезающей нитью накала.
В последние годы стали применяться так называемые фотометрические пирометры. Схематично можно изобразить:
Рисунок 14 - Фотометрический пирометр
Такие пирометры обладают высокой чувствительностью, быстродействием, надёжностью, простотой конструкции.
В качестве приёмников излучения используют фотоэлементы: фотодиоды, фоторезисторы, фототранзисторы.
Для контроля высоких температур используют термопары. Их можно использовать в труднодоступных местах, их показания не зависят от степени черноты тела, мы можем измерять температуры меньше температуры свечения тела. Наибольшее распространение получили вольфрам-рениевые термопары (W-Re). Они обладают большой стабильностью, высоким значением ЭДС, высокими химической стойкостью и точностью измерения. Такие термопары имеют линейную характеристику во всём диапазоне температур.
Метод замещения
Рисунок 18 – Схема метода замещения
Метод замещения состоит в том, что объект контроля включается вместо изделия-образца. Образец специально побирается с помощью высокоточной аппаратуры. По выходным параметрам образцового устройства судят о соответствии ОК требованиям технических условий.
Требования к сопротивлению нагрузки
Чтобы сохранить калибровку измерительного генератора по напряжению, сопротивление нагрузки должно удовлетворять требованиям:
- если генератор калиброван по напряжению в режиме холостого хода, то сопротивление нагрузки генератора должно быть много больше выходного сопротивления генератора (Rнаг.>> RГ);
- если же генератор калиброван при согласованной нагрузке (Rнаг.= RГ), то при подключении генератора к объекту контроля должно выполняться: Rнаг.= RГ.
В общем случае, необходимо применять согласующее устройство:
Рисунок 20 – Схема сопротивлений
Rвх.согл..= Rнаг, Rвых.согл.= Rвых.сх.
Сопротивление резистора выбирают таким образом, чтобы выполнялись 2 условия:
1) Rвх . согласующего устройства при подключенном объекте контроля должно быть равно Rнаг .;
2) Rвых . согласующего устройства при подключенном генераторе должно быть равно Rвых . Отключенной схемы: Rвых.согл..= Rвых.сх .
Контрольно-измерительные приборы с симметричным входом или выходом подключаются к симметричным схемам через симметрирующие элементы.
Общие сведения
Микросхемы низкой степени интеграции – законченный функциональный узел. Качество таких микросхем можно оценить по параметрам многополюсника. Следовательно, процесс контроля сводится к измерению электрических параметров на внешних выводах. Различают контроль статических и динамических параметров и функциональный контроль.
Статические параметры измеряют после завершения переходного процесса как в самой микросхеме, так и в подключенных внешних цепях.
Динамические параметры (характеризуют переходный процесс) измеряют в течении переходного процесса. При измерении динамических параметров на временной оси задают начало измерения и конец, или задают и измеряют временной интервал между уровнями сигнала.
Функциональный контроль. Он обязателен для проверки работоспособности логических комбинационных микросхем, а также сложных преобразователей информации и запоминающих устройств. В процессе проведения функционального контроля проверяют правильность выполнения основной функции микросхемы. Кроме того, сравнивают выходную последовательность сигналов с расчетной.
Средства контроля микросхем должны удовлетворять следующим требованиям:
1) реализовать заданные: метод контроля, режимы контроля, последовательность коммутации;
2) обеспечить заданную точность контроля;
3) обеспечить защиту микросхемы от различных перегрузок, которые возникают в цепях коммутации во время переходного процесса, а также обеспечивать защиту от статического электричества;
4) контактирующие устройства должны обеспечивать надежный контакт с микросхемой и не вызывать механических повреждений;
5) источники измерительных сигналов и измерители параметров при динамическом и функциональном контроле должны быть соединены с объектом контроля с учетом вышеназванных рекомендаций.
Функциональный контроль
Функциональный контроль микросхем состоит в реализации функциональных тестов, подачи на микросхему определенного набора входных тест-сигналов, формирование выходных эталонных сигналов и получении результатов логического сравнения эталонного и фактического выходного набор-сигналов. Функциональный контроль может быть проведен следующим образом:
1) в составе устройства;
2) в сравнении с эталоном;
3) алгоритмической генерации сигналов;
4) кодовым сигналом;
5) по заданной программе.
Для БИС запоминающих устройств наиболее эффективны алгоритмические сигналы; для БИС микропроцессоров – сигналы по заданной программе; для матричных БИС – псевдослучайные входы.
Считается, что наиболее эффективным является не сам функциональный контроль, а функционально-параметрический контроль. Он обеспечивает одновременно контроль функционирования микросхемы и контроль статических и динамических параметров. В настоящее время разработано большое количество тестов:
1. Алгоритм теста «бег» (для контроля ОЗУ). Выполняемые операции:
а) в каждой ячейке ОЗУ последовательно производят 2 обращения: запись кода и считывания и контроль;
б) код первой ячейки изменяется на противоположный и последовательно контролируется содержимое всех основных ячеек;
в) восстанавливается предыдущее состояние первой ячейки;
г) повторяют операции б), в) последовательно для всех ячеек ОЗУ.
2. Алгоритм «марш»:
а) запись кода по всем адресам;
б) считывание и проверка записанного кода и запись обратного кода при переходе от первой ячейки к последующей;
в) считывание, проверка, запись обратного кода в той же последовательности;
г) считывание, проверка и запись обратного кода при переходе от последующей ячейки к первой;
д) снова считывание, проверка и запись обратного кода при переходе от последующей ячейки к первой.
Электрофизическая диагностика (ЭФД)электронных средств (ДНК)
Общие сведения об ЭФД
ЭФД основана на исследовании и анализе механизмов и причин отказов ЭС, на контроле и прогнозировании их качества (надёжности) по информативным параметрам. При этом предполагается наличие стохастической связи между качеством и начальными значениями информативных параметров. Можно выделить три обстоятельства, которые определяют возможность практического использования методов ЭФД:
1) возможность оперативного контроля и выявления потенциально ненадёжных изделий в процессе их изготовления;
2) возможность определять состояние изделий практически любой сложности;
3) возможность обеспечения высокой надёжности аппаратуры путем отбора для её комплектации электрорадиоизделий (ЭРИ) повышенного качества.
Достоинства ЭФД:
1. Простота получения информации.
2. Оперативность.
3. Возможность использования при автоматизированном контроле.
4. Ресурсосбережение по сравнению с испытанием на термоциклы и электротренировки.
5. Возможность надёжного проектирования.
Области применения:
1. Технологические испытания в дополнение к разрушающим испытаниям.
2. Технологические испытания взамен разрушающим испытаниям.
3. Входной контроль ЭРИ для отбора наиболее надёжной базы при сборке аппаратуры.
4. Анализ отказов в повторяющихся случаях и выявление скрытых дефектов, приводящих к отказам.
5. Исследование ЭРИ с целью прогнозирования их надёжности.
6. Разработка предложений для принятия решений при определении сроков эксплуатации аппаратуры.
Возможная эффективность ЭФД
1. Повышение проценты выхода годной продукции.
2. Снижение затрат на снижение санкции по рекламациям.
3. Сокращение затрат на испытания.
4. Снижение отказов ЭРИ в общей доле отказов аппаратуры.
5. Оперативность и повышение достоверности анализа отказов.
6. Снижение затрат на проведение исследований.
7. Объективность оценок состояния и принятия решений о продлении сроков эксплуатации.
Классификация методов ЭФД
В зависимости от способа наблюдения за проявлением особенностей ЭС принято различать три основные группы методов ЭФД по интегральным электрофизическим эффектам.
Первая группа основана на рассеянии или диссипации энергии внутри системы или во внешнюю среду. Вторая группа – на внутренних флуктуациях спонтанного типа. Третья группа – на нелинейности функциональных характеристик
При этом обычно выделяют шесть групп методов:
1) группа ВАХ;
2) группа вольт-фарадных характеристик;
3) группа удельного сопротивления;
4) группа пробивного напряжения;
5) группа шумовых параметров;
6) группа измерения параметров носителей заряда.
Конкретные методы приведены на рисунке 25.
Рисунок 25 – Методы ЭФД
Методы ВАХ
Группа методов ВАХ основана на получении, преобразовании и анализе зависимостей токов и напряжений, токов и сопротивления на входе и выходе путём сравнения вида ВАХ исследуемого образца и ВАХ образцового или контрольного изделия. Если в качестве примера взять транзистор, то различают входные и выходные характеристики для схем с ОБ и ОЭ. Если имеем входные характеристики, то по ним можно легко определить интегральное и дифференциальное сопротивления. Имея входные ВАХ для схем с ОЭ можно определить выходное сопротивление, коэффициент передачи, остаточное напряжение на открытом транзисторе, сопротивление насыщения, а также зависимости этих параметров от токов и напряжений. Методы ВАХ находят применение при исследовании влияния механических, тепловых и электрических нагрузок на возникновение дефектов, для выявления влаги, других загрязнений, для оценки распределения концентрации носителей заряда, а также для оценки эффективности различных операций технологического процесса на стадии лабораторных исследований и определительных испытаний.
Метод m-характеристик
Он является одним из эффективных методов получения информации о качестве полупроводникового прибора. Этот метод основан на анализе ВАХ прямо смещённого р-n-перехода. Уравнение прямой ветви ВАХ описывается выражением:
, (*)
- тепловой ток (обратный ток насыщения);
q – элементарный заряд;
U – прямое напряжение, приложенное к р-n-переходу;
k – постоянная Больцмана;
Т – абсолютная температура р-n-перехода.
Формула (*) отражает некоторое приближение для случая идеального р-n-перехода. Для реального р-n-перехода:
m – безразмерный параметр ВАХ.
Из этого выражения можно определить параметр m:
.
Для идеального р-n-перехода m=1. Для реального – отличается от 1.
Ток прямосмещённого p-n перехода состоит из нескольких составляющих. Каждая из составляющая имеет своё значение параметра m:
1) m ≈ 1 объёмный диффузионный ток
2) ток генерации рекомбинации в объёме полупроводника 1≤m≤2
3) ток генерации рекомбинации на поверхности 1≤m≤2
4) ток, обусловленный поверхостными каналами в области p-n перехода 1≤m≤10
По величине m и зависимости m = f (Iпер) можно определить вклад каждой из составляющих тока и определить класс или группу дефектов. Зависимость m = f (Iпер) как функцию тока через переход имеет вид:
Рисунок 27 - Зависимость m = f (Iпер)
Имеется небольшое количество дефектов.
Рисунок 28 - Зависимость m = f (Iпер)
Здесь аномальный процесс генерации-рекомбинации, связанный с аномалией дефектов.
Рисунок 29
При наличии поверхностных дефектов они ведут к дополнительному току генерации рекомбинации.
На практике кроме вида m – характеристики используют зону или границу забракования. Методика определения этой зоны состоит в следующем: определяется m – параметр. Для его определения используются генератор тока с постоянным отношением . В этом случае измеряют дифференциальное сопротивление.
В любой точке диапазона токов через p-n-переход задаётся прямой ток и одновременно накладывается переменный сигнал от генератора импульсов тока с низкой частотой, например 10 Гц. При обеспечении величина m параметра будет пропорциональна ΔU. Измеряя значение переменной составляющей напряжения на p-n – переходе с помощью вольтметра, получим значение m.
Прямой метод
Рисунок 36 - Схема измерения прямым методом
Несмотря на простоту, метод характеризуется высокими требованиями к точности измерения: усилитель должен иметь низкое значение собственных шумов, должен иметь широкую полосу пропускания, Fш оценивается отношением мощности шума при включенном и выключенном генераторе шума. Этот метод требует тщательной градуировки измерительного тракта. В этом отношении является более простым сравнительный метод.
Сравнительный метод
Этот метод основан на сравнении шума от образцового генератора с шумом на испытуемом образце. При этом измерительный тракт не нуждается в градуировке.
Рисунок 37 - Схема сравнительного метода в общем случае.
Измерение коэффициента шума осуществляется сравнением шума образцового источника шума с шумом контролируемого изделия. С этой целью с помощью аттенюатора на измерителе устанавливается то же значение шума. Что было получено от образцового источника. Коэффициент шума определяется как отношение показаний аттенюатора при замерах шума от генератора шума.
Общим недостатком шумовых методов является малая повторяемость результатов измерения даже на одном и том же рабочем месте.
Общие сведения о контроле
Контроль – процесс установления соответствия между состоянием объекта (параметра) и заданными на него нормами.
В качестве объекта контроля могут выступать:
1) изделия;
2) документация;
3) процессы;
4) технологические среды;
5) организации, предприятия.
В соответствии и Госстандартом 16504-81 виды контроля могут классифицироваться:
1) по стадии существования;
2) по этапу процесса;
3) по полноте охвата;
4) по влиянию на объект контроля;
5) по применению средств контроля.
На практике и в нормативно-технической документации понятие «контроль» отличается от понятия «измерение».
Измерение – нахождение значения физической величины опытным путём с помощью специальных технических средств. В процессе измерения мы получаем количественную величину. Науку об измерениях и методах обеспечения точности измерения называют метроло
|
|
История создания датчика движения: Первый прибор для обнаружения движения был изобретен немецким физиком Генрихом Герцем...
История развития пистолетов-пулеметов: Предпосылкой для возникновения пистолетов-пулеметов послужила давняя тенденция тяготения винтовок...
Автоматическое растормаживание колес: Тормозные устройства колес предназначены для уменьшения длины пробега и улучшения маневрирования ВС при...
Механическое удерживание земляных масс: Механическое удерживание земляных масс на склоне обеспечивают контрфорсными сооружениями различных конструкций...
© cyberpedia.su 2017-2024 - Не является автором материалов. Исключительное право сохранено за автором текста.
Если вы не хотите, чтобы данный материал был у нас на сайте, перейдите по ссылке: Нарушение авторских прав. Мы поможем в написании вашей работы!