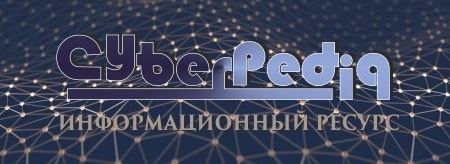
История создания датчика движения: Первый прибор для обнаружения движения был изобретен немецким физиком Генрихом Герцем...
Двойное оплодотворение у цветковых растений: Оплодотворение - это процесс слияния мужской и женской половых клеток с образованием зиготы...
Топ:
Проблема типологии научных революций: Глобальные научные революции и типы научной рациональности...
Оценка эффективности инструментов коммуникационной политики: Внешние коммуникации - обмен информацией между организацией и её внешней средой...
Методика измерений сопротивления растеканию тока анодного заземления: Анодный заземлитель (анод) – проводник, погруженный в электролитическую среду (грунт, раствор электролита) и подключенный к положительному...
Интересное:
Что нужно делать при лейкемии: Прежде всего, необходимо выяснить, не страдаете ли вы каким-либо душевным недугом...
Лечение прогрессирующих форм рака: Одним из наиболее важных достижений экспериментальной химиотерапии опухолей, начатой в 60-х и реализованной в 70-х годах, является...
Мероприятия для защиты от морозного пучения грунтов: Инженерная защита от морозного (криогенного) пучения грунтов необходима для легких малоэтажных зданий и других сооружений...
Дисциплины:
![]() |
![]() |
5.00
из
|
Заказать работу |
|
|
3.1.1. Источники образования тепла и распределение тепла
между стружкой, инструментом и деталью
Опытами П.А. Ребиндера и Г.И. Епифанова установлено, что при резании конструкционных материалов более 99,5 % работы резания переходит в тепло. Таким образом, если работа резания или любая ее составляющая выражена в кгс·м/мин, то соответствующее им количество выделяемого тепла
, ккал/мин.
На основании этого количество тепла, образующегося при резании, можно определить с помощью выражения
Q = Q д + Q т.п + Q т.з.
Расположение источников тепла представлено на рис. 82, а. Тепло деформации Q д образуется в зоне сдвигов на условной плоскости сдвига; тепло трения на передней поверхности Q т.п – в пределах площадки контакта между стружкой и инструментом шириной с; тепло трения на задней поверхности Q т.з – в пределах площадки контакта между поверхностью резания и инструментом. Образовавшеесятепло распространяется из очагов теплообразования к более холодным областям, распределяясь между стружкой, деталью и инструментом.
а б
Рис. 82. Источники образования тепла в зоне резания (а) и распределения его в стружку, инструмент и деталь (б)
Между стружкой, деталью и инструментом устанавливаются следующие тепловые потоки (рис. 82, б). Часть тепла деформации Q д.с от условной плоскости сдвига переходит в стружку. Из зоны трения на передней поверхности в стружку переходит часть тепла трения, равная Q т.п – Q п, где Q п – тепло, уходящее в инструмент.
Таким образом, температура стружки Q с определяется суммарным тепловым потоком:
Q с = Q д.с + Q т.п – Q п.
Часть тепла деформации Q д.дет от условной плоскости сдвига переходит в деталь. Туда же из зоны трения на задней поверхности переходит часть тепла трения, равная Q т.з – Q з, где Q з – тепло, уходящее в инструмент. В результате этого интенсивность теплового потока
в деталь Q дет = Q д.дет + Q т.з – Q з.
|
Температурное поле режущего клина инструмента устанавливается в результате действия суммарного теплового потока Q и с интенсивностью
Q и = Q п + Q з.
На основании этого можно составить выражение, описывающее расход образовавшегося при резании тепла:
Q = Q с + Q дет + Q и + Q ср.
где Q ср – количество тепла, уходящего в окружающую среду. Выражения в совокупности описывают тепловой баланс при резании материалов.
Поскольку образовавшееся тепло пропорционально совершаемой работе, количество тепла зависит от рода и механических свойств материала обрабатываемой детали, геометрических параметров инструмента и режима резания. На процентное распределение тепла между стружкой, деталью и инструментом главное влияние оказывают механические и теплофизические свойства материала детали и скорость резания.
В 1915 году Я.Г. Усачев установил, что наибольшее количество тепла переходит в стружку, составляя при обработке стали от 60 до 85 % от общего количества тепла. С увеличением скорости резания доля тепла, уходящего в стружку, увеличивается, а ее средняя температура растет. Исследования последних лет показали, что процентное распределение тепла сильно зависит от рода обрабатываемого материала.
При постоянной скорости резания средняя температура стружки и распределение тепла между стружкой, инструментом и деталью зависят главным образом от работы, расходуемой на резание, и теплопроводности обрабатываемого материала.
Средняя температура стружки при обработке стали значительно выше, чем при обработке чугуна и особенно алюминия, что вызвано как большей работой пластического деформирования, так и работой трения на передней поверхности. Уменьшение количества тепла, уходящего в стружку, при обработке чугуна связано с элементным типом стружки при его резании. Вследствие более высокой теплопроводности алюминия по сравнению со сталью и чугуном тепло из зоны деформации интенсивно распространяется в деталь, тем самым резко уменьшая количество тепла, остающегося в стружке.
|
Количество тепла, уходящего в инструмент, очень мало и при резании любых материалов с любыми режимами обработки намного меньше количества тепла, уходящего в стружку и деталь. Основной причиной низкой интенсивности теплоотвода в инструмент является более низкая теплопроводность инструментального материала по сравнению с обрабатываемым. Уменьшение количества тепла, отводимого в инструмент, при обработке хрупких материалов связано также с элементным видом стружки, при образовании которой отсутствует постоянный контакт между стружкой и передней поверхностью.
Распределение тепла между стружкой, деталью и инструментом коренным образом изменяется при увеличении скорости резания: количество тепла, уходящего в стружку, возрастает, а уходящего в деталь и инструмент – уменьшается. Например, при точении стали 40Х со скоростью резания 20…50 м/мин в стружку уходит в среднем
около 45 % тепла, а в деталь и инструмент – соответственно 47 %
и 4,5 %; при скорости резания 100…300 м/мин в стружку уходит 75 % тепла, а в деталь и инструмент – соответственно только 22 %
и 1,5 %.
Уменьшение доли тепла, переходящего в деталь при увеличении скорости резания, вызвано изменением соотношения между скоростью резания и скоростью распространения тепла из зоны деформации. Из очага теплообразования на условной плоскости сдвига
(см. рис. 82) в деталь течет тепловой поток Q д.дет. Скорость распространения тепла зависит от градиента температур на условной плоскости сдвига и в детали и температуропроводности обрабатываемого материала. Если скорость резания, т.е. скорость, с которой режущий клин инструмента пересекает тепловой поток, мала, то тепло от условной плоскости сдвига беспрепятственно перейдет в деталь.
По мере увеличения скорости резания клин инструмента все быстрее пересекает тепловой поток, и поэтому в деталь успевает перейти меньшее количество тепла и все большее количество тепла остается
в стружке. Уменьшение доли тепла, уходящего в инструмент, при увеличении скорости резания связано с уменьшением ширины площадки контакта на передней поверхности, через которую тепло из стружки переходит в инструмент.
|
На теплосодержание стружки и ее среднюю температуру оказывает влияние режим резания: глубина резания, подача и скорость резания. При увеличении глубины резания удельное количество тепла
в стружке уменьшается, при увеличении подачи практически остается постоянным, а при увеличении скорости резания возрастает. Увеличение глубины резания и подачи сопровождается уменьшением средней температуры стружки. При увеличении же скорости резания средняя температура стружки вначале интенсивно возрастает, а затем, после достижения скоростью резания определенного значения, рост температуры почти прекращается и она мало зависит от дальнейшего увеличения скорости. При этом средняя температура стружки стремится к некоторому пределу, величина которого определяется родом и механическими свойствами обрабатываемого материала, геометрическими параметрами инструмента, глубиной резания и подачей.
Несмотря на то, что доля тепла, уходящего в инструмент, очень мала, средняя температура q на передней поверхности инструмента
в несколько раз превосходит среднюю температуру стружки. Температура контакта на передней поверхности приблизительно равна температуре контактной поверхности стружки; это свидетельствует
о том, что температура различных слоев стружки по ее толщине неодинакова – убывает по мере приближения к свободной стороне стружки.
3.1.2. Понятие о тепловом поле
и температуре резания
На рис. 83 представлено изменение температуры q x для различных точек площадки контакта на передней поверхности инструмента. Максимальная температура соответствует точке, лежащей приблизительно на половине ширины площадки контакта. К лезвию и к концу площадки температура убывает. На площадке контакта задней поверхности инструмента с поверхностью резания температура распределяется также неравномерно. Поэтому под температурой резания q понимают среднюю температуру на поверхности контакта инструмента со стружкой и поверхностью резания. Если через qп.ср и qз.ср. обозначить средние температуры на площадках контакта передней
и задней поверхностей, то температура резания
|
q = (qп.ср. с + qз.ср. с 2)/(с + с 2).
Температуру резания иногда называют средней температурой контакта.
Для незатупленного инструмента ширина с з площадки контакта задней поверхности с поверхностью резания исчезающе мала, а поэтому температуру резания можно считать равной средней температуре на площадке контакта стружки с передней поверхностью, т.е. q = qп.ср. Передняя поверхность инструмента нагревается за счет тепла деформации и трения. Поэтому температура резания равна сумме двух температур: температуры деформации qд
и средней температуры трения на передней поверхности qп.ср., т.е.
q = qд + qп.ср.
Температура резания зависит от мощности тепловых источников в зоне деформации и на передней поверхности инструмента
и интенсивности стоков тепла в деталь и инструмент. При резании определенного материала температура резания растет с увеличением скорости резания и размеров срезаемого слоя. Однако их влияние на температуру резания неодинаково. На основании измерений получена формула, связывающая температуру резания с толщиной, шириной срезаемого слоя и скоростью резания при работе различными инструментами:
q = C q V manbq.
Коэффициент C qв формуле зависит от рода и механических свойств обрабатываемого материала, геометрических параметров инструмента и применяемой смазочно-охлаждающей жидкости. При любых видах обработки величины показателей т, п и q неодинаковы: m > n > q,т.е. на температуру резания наибольшее влияние оказывает скорость резания, затем толщина срезаемого слоя и наименьшее – ширина срезаемого слоя. Измерение температуры резания при увеличивающемся отношении b / a также свидетельствует об ее уменьшении:
.
В чем причина неодинакового влияния величин b и a на температуру резания? На рис. 84 изображены два одинаковых резца, срезающих слои материала с одинаковой площадью поперечного сечения F = 2 аb. Резец I срезает слой шириной 2 b
и толщиной а, а резецIIсрезает слой шириной b и толщиной 2 a. Таким образом, на передней поверхности резцов на площади контакта 2 bа действуют тепловые источники, мощность которых можно считать приблизительно одинаковой. Источники скользят по контактной поверхности стружки со скоростью, равной скорости стружки. Из расчетов Д.К. Иегера следует, что при увеличении отношения длины движущегося полосового источника тепла к его ширине средняя температура трения в пределах площади контакта непрерывно уменьшается. К этому следует добавить, что и условия отвода тепла через тело инструмента для резца I более благоприятны, так как источник тепла относительно более удален от вершины резца, что также способствует снижению температуры резания. Таким образом, резец I должен работать с меньшей температурой резания, нежели резец II.
|
Неодинаковое влияние ширины и толщины срезаемого слоя на температуру резания позволяет сделать следующий важный вывод: для уменьшения температуры резания при заданной площади сечения срезаемого слоя необходимо работать с возможно большим отношением b / a, т.е. с широкими и тонкими стружками.
Выражая физические размеры срезаемого слоя при точении
в формуле через глубину резания, подачу и главный угол в плане, получим
q = C q V mS nt q (sin j) n – q .
Из выражения следует, что при точении подача и глубина резания на температуру резания влияют с той же интенсивностью, что
и толщина и ширина срезаемого слоя. Следовательно, для снижения температуры резания при заданной площади сечения срезаемого слоя необходимо работать с возможно большим отношением t / s. При заданных глубине резания и подаче температуру резания можно уменьшить, уменьшая главный угол в плане резца. Последнее связано с тем, что при уменьшении угла j отношение b / a возрастает.
Интенсивность влияния скорости резания на температуру при различных скоростях неодинакова. Чем выше скорость резания,
тем меньшее влияние оказывает ее увеличение на возрастание температуры резания. Поэтому и величина показателя степени при
скорости резания уменьшается с ее увеличением. Например, при
V < 100 м/мин т = 0,5…0,4, а при V > 100 м/мин т = 0,4…0,25.
Уровень температуры резания зависит от рода и механических свойств обрабатываемого материала. Чем больше работа, затрачиваемая на резание, тем при прочих равных условиях выше и температура резания. Поскольку средняя температура стружки при резании
чугуна ниже, чем при резании стали, температура резания при обработке чугуна также ниже на 40…50 %. С увеличением твердости
и прочности обрабатываемого материала температура резания возрастает.
При постоянной мощности тепловых источников температуру резания можно понизить, интенсифицируя отвод тепла в деталь и инструмент. Этого можно достигнуть, охлаждая деталь, стружку, инструмент струей смазочно-охлаждающей жидкости. Так как в большинстве случаев скорость стружки превышает скорость распространения тепла в материале обрабатываемой детали, то, направляя струю жидкости на отделяющуюся от детали стружку, можно добиться понижения температуры только ее слоев, прилегающих к свободной поверхности. Температура резания при этом понижается незначительно.
Значительно большой эффект можно получить, если струя жидкости будет омывать инструмент и тем самым повышать теплообмен между инструментом и окружающей средой. Чем больше тепла перейдет в инструмент и окружающую среду, тем ниже будет температура резания. Поэтому насадок, через который смазочно-охлаждающая жидкость попадает в зону резания, должен быть расположен так, чтобы струя жидкости омывала не только деталь и стружку, но, главным образом, инструмент.
Применение инструментальных материалов, обладающих высокой теплопроводностью, также способствует понижению температуры резания. С более низкой температурой резания работают инструменты, имеющие внутреннее охлаждение режущей части.
3.1.3. Основные экспериментальные методы
изучения тепловых явлений
Несмотря на значительные успехи, достигнутые в использовании аналитических методов для изучения тепловых явлений в зоне деформации и на контактных поверхностях инструмента, экспериментальные методы благодаря их надежности и простоте являются главным инструментом исследования.
Экспериментальные методы можно разбить на две группы: косвенные и непосредственные.
Перечислим косвенные методы:
1. Метод цветов побежалости. Несмотря на свою простоту этот метод дает значительные погрешности, связанные с тем, что определяется только температура окисленной поверхности стружки.
К примеру, при резании с обильным охлаждением цвета побежалости исчезают, в то время как температура в месте контакта стружки
с инструментом очень высока.
2. Метод термокрасок. Для выявления температуры пользуются свойством специальных красок менять цвет при определенных температурах. Например, при 155 °С цвет из пурпурного переходит
в голубой, при 190 °С из белого – в зелено-коричневый, при 255 °С из зеленого – в темно-коричневый, при 305 °С из желтого – в красно-коричневый, при 440 °С из фиолетового – в белый. При использовании этого метода краска смешивается с алкоголями и наносится ровным слоем на грани исследуемых резцов. Некоторая погрешность
в данном случае заключается в том, что оттенок переходящих красок меняется в зависимости от продолжительности действия тепла. Этот метод применяется для определения температуры на поверхностях инструмента. Специальную термочувствительную краску наносят тонким слоем на поверхность инструмента. Тепло на поверхностях инструмента изменяет цвет краски. Определенная шкала «цвет–температура» позволяет определить температуру поверхности инструмента. Недостаток метода: при продолжительной работе оттенки краски изменяются и не соответствуют шкале.
3. Метод микроструктурного анализа. Основан на изменениях, которые происходят в поверхностных слоях инструмента вследствие воздействия на них тепла, возникающего в процессе резания. Оригинальный способ измерения температуры в процессе резания путем анализа микроструктуры тончайшего слоя обработанной поверхности, претерпевающей заметные изменения при достаточно большом нагреве, применил Б.И. Костецкий. Но и этот метод пока
не получил распространения, так как его можно использовать только при высоких режимах резания, когда поверхность резания или обработанная поверхность нагревается выше критических точек.
4. Калориметрический метод (предложен А.М. Даниеляном).
Данным методом определяется распределение тепла между стружкой, инструментом и обрабатываемой деталью, а также средняя температура стружки и инструмента с использованием специального калориметра.
Непосредственные методы измерения температуры являются более точными, так как позволяют получить результаты, более близкие к действительным.
К непосредственным методам относятся следующие.
1. Метод искусственной термопары Я.Г. Усачева (1914). Недостаток метода в том, что нельзя близко подойти к передней или задней поверхности. А самый большой интерес представляет температура на контактных поверхностях.
2. Метод полуискусственной термопары Я.Г. Усачева (1914–1916). Проволока термопары изолирована от резца и контактирует лишь в месте расклепки.
3. Метод естественной термопары. При этом необходимо:
– иметь в виду, что снятие термоэлектродвижущей силы (ТЭДС) с вращающейся заготовки происходит с использованием токосъемника;
– применять цельные резцы;
– проводить тщательную тарировку.
4. Метод двух резцов. Разнородные материалы резцов образуют термопару (но этот метод неудобен).
5. Оптический метод. Используется при скоростной обработке
с применением пирометров.
6. Радиационный метод. Основан на измерении теплоты лучеиспускания, но имеет ряд недостатков и поэтому малоприменим.
7. Метод бегущей термопары (точен, но трудоемок). Этот метод позволяет одновременно измерять температуры на контактных площадках «резец–стружка» и «резец–деталь». Резец перерезает защитную трубку, и проводники термопары образуют горячие спаи двух искусственных термопар. Контакты К1 – К2 выводят на соответствующие приборы.
Наиболее распространен в настоящее время метод естественной термопары; при этом для определения температуры строится тарировочный график на основе тарировки резец–деталь.
Определить температуру резания можно и аналитически при помощи теоретических формул, предложенных проф. А.Н. Резниковым, С.С. Силиным, П.И. Бобриком и другими исследователями. Однако эти формулы являются, как правило, приблизительными из-за ряда допущений.
Основными объектами изучения являются: а) количество выделяемого при резании тепла и его распределение между стружкой, деталью и инструментом; б) температура, устанавливающаяся на контактных поверхностях инструмента; в) температурные поля в зоне деформации и режущем клине инструмента.
Калориметрический метод. Метод позволяет определить
количество тепла, переходящего в стружку, деталь и инструмент.
На рис. 85 изображена схема постановки опыта при определении количества тепла Q, переходящего при точении в стружку и резец, и их средних температур q. Внизу, перед передней поверхностью резца, установлен калориметр 1 с сеткой 2 для сбора стружки и ртутным термометром 3. Для обеспечения лучшего попадания стружки в калориметр резание производят при левом вращении шпинделя. Если обозначить через qсм – температуру смеси (воды в калориметре
после резания), в град.; G в – массу воды в калориметре, в г; qв– начальную температуру воды в калориметре, в град.; G – массу стружки или резца, в г; с – теплоемкость стружки или резца, в кал, то среднюю температуру стружки или резца можно определить по формуле
q = qсм + G в(qсм – qв)/ сG,
Количество тепла, перешедшего в стружку и резец, определяют по формуле
Q = (c г – с нqн) G,
где с г – теплоемкость горячей стружки или резца, в кал;
с н – теплоемкость ненагретой стружки или резца, в кал;
qн – начальная температура стружки или резца.
Метод термопар. Для измерения средней температуры на контактных поверхностях инструмента и в различных точках контактных площадок применяют разнообразные термопары. На рис. 86 изображен метод искусственной термопары, предложенный Я.Г. Усачевым. Резец, применяемый в опытах, представляет собой корпус, к которому прижата режущая пластинка 2 из быстрорежущей стали или твердого сплава. В корпусе сделано отверстие, в которое вставлена изоляционная трубка 3. Стандартная термопара 4 (медь-константан, хромель-алюмель и др.) с гальванометром 5, подключенным к ее концам, вставлена в изоляционную трубку так, что ее спай касается нижней плоскости пластинки 2. Спай термопары регистрирует температуру опорной плоскости пластинки.
Большим достоинством метода является возможность использования стандартных термопар с известными термоэлектрическими характеристиками, а потому не нуждающихся в специальной тарировке. Располагая отверстия в различных точках передней и задней поверхностей, можно составить представление о температурном поле в режущем клине инструмента.
Однако методу присущи и серьезные недостатки, ограничивающие область его применения. Измеряемая термопарой температура ниже температуры на контактных поверхностях инструмента, и разность температур зависит от расстояния спая термопары от указанных поверхностей, увеличиваясь при увеличении толщины режущей пластинки.
Практически не удается достигнуть толщины пластинки менее 1,5…2,0 мм, а поэтому из-за большого градиента температур измеряемая температура на 50…80° ниже действительной. При долговременном резании вследствие износа передней и задней поверхностей инструмента расстояние между спаем термопары и контактными поверхностями сокращается, что приводит к непрерывному возрастанию температуры. Наконец, метод искусственной термопары трудно использовать при вращающемся инструменте.
Более простым и совершенным является метод естественной термопары, предложенный Е. Гербертом и К. Готвейном. Метод основан на том, что в процессе резания (рис. 87, а) в месте соприкосновения передней поверхности инструмента со стружкой и задней поверхности с поверхностью резания естественным путем создаются термопары, электродами которых являются материал обрабатываемой детали и материал режущей части инструмента. Величина электродвижущей силы и направление термотока зависят от рода инструментального и обрабатываемого материалов, образующих термопару.
а б
Рис. 87. Естественная термопара (а) и схема измерения температуры
резания естественной термопарой (б)
Если обрабатываемую деталь и инструмент включить в замкнутую электрическую цепь, то величина термоэлектродвижущей силы, возникающей в термоэлементе, будет пропорциональна температуре скользящего «спая» образовавшейся термопары. Методом естественной термопары измеряют не максимальную, а некоторую среднюю контактную температуру на передней и задней поверхностях инструмента. Например, при обработке углеродистой стали инструмент является положительным электродом, если он изготовлен из быстрорежущей стали, и отрицательным, если он из твердого сплава.
Схема измерения температуры при точении методом естественной термопары изображена на рис. 87, б. Обрабатываемая заготовка 1 изолирована от патрона 3 и центра задней бабки эбонитовыми прокладками и пробкой 5. Цельный резец 2 из быстрорежущей стали или твердого сплава изолирован от резцедержателя эбонитовыми прокладками. Резец делают цельным для того, чтобы в месте приваривания или припаивания режущей пластинки к корпусу резца
не образовались паразитные термопары. Заготовка медным проводником 10 соединена с гибким валом 6, закрепленным в эбонитовой втулке, установленной на конце шпинделя станка 4. Контактный наконечник 7 гибкого вала опущен в ванночку со ртутью 8. Милливольтметр 9 одной клеммой соединен с торцом резца, а вторым –
с ртутным токосъемником. Замкнутая электрическая цепь состоит из заготовки–проводника–гибкого вала–токосъемника–милливольтметра–резца–заготовки. Заготовку изолируют от станка для устранения влияния паразитных термопар, могущих возникнуть между отдельными деталями станка. Однако роль паразитных термопар при высокой температуре контактных поверхностей инструмента незначительна, и за счет некоторого снижения точности измерения установку можно упростить, отказавшись от изоляции заготовки, сохранив изоляцию только резца.
Достоинством метода естественной термопары является то, что его легко осуществить не только при точении, но и при сверлении, нарезании резьбы метчиком, строгании, фрезеровании, протягивании и других видах работ. Для перевода показаний миливольтметра
в градусы Цельсия естественная термопара должна быть предварительно подвергнута специальной тарировке. В электропечь помещают тигель с расплавленным металлом, имеющим низкую температуру плавления: свинцом, оловом, сурьмой, сплавом вуда и т.п.; стержни из обрабатываемого и инструментального материалов опускают на одинаковую глубину в расплавленный металл, а к их концам присоединяют милливольтметр, применяемый в опытах по измерению температуры при резании. Между стержнями помещают контрольную термопару, гальванометр которой проградуирован в градусах. Нагревая и охлаждая расплавленный металл, сравнивают показания милливольтметра в милливольтах и гальванометра в градусах и строят тарировочный график мВ– q °С.
Большим неудобством при применении метода естественной термопары является необходимость новой тарировки термопары при изменении материалов детали или инструмента.
Оптический и радиационный методы. Оптические пирометры для измерения температуры резания применяются при скоростной обработке металла, когда стружка и резец нагреваются весьма сильно вплоть до светлого каления. Однако опыт использования этого метода недостаточен, чтобы можно было делать определенные выводы.
Стационарный инфракрасный пирометр применяется для бесконтактного измерения температуры неметаллических или окрашенных (анодированных) металлических объектов или металлических объектов с покрытием в диапазоне от 0 до 500 °С (рис. 88).
Рис. 88. Инфракрасный бесконтактный
пирометр IN3000
Данный пирометр имеет фиксированную установку коэффициента излучения 95 % и оптическое соотношение (соотношение расстояния до объекта контроля и диаметра области измерения) 5:1. Эти характеристики в сочетании с временем отклика 300 мс позволяют решать различные задачи измерения (рис. 89).
Рис. 89. Схема инфракрасного пирометра (слева) и параметры измеряемого объекта (справа)
Упрочненная конструкция пирометра гарантирует высокую безопасность даже в неблагоприятных промышленных условиях. Также имеется версия пирометра IN 3000со встроенным блоком воздушной продувки.
Область применения пирометров IN 3000:окрашенные металлы, металлы с покрытием, анодированные металлы. Некоторые характеристики:3 диапазона измерения температуры, 3 выхода: 10 мВ/°С, термопара типа J или K, невысокая стоимость, корпус из нержавеющей стали с резьбой PG11, простая установка и подключение, малые размеры, рабочая температура окружающего воздуха до 70 °С без охлаждения. Этот пирометр в большей степени удовлетворяет требованиям исследования температуры резания: невысокая стоимость, простота установки и подключения, малые размеры, возможность подключения к прибору «Камертон» и т.д. Но недостатком является узкий диапазон измеряемой температуры: от 0 до 500 °С. Ведь температура в зоне резания может достигать при скоростной обработке 800 °С, а на поверхности трения по передней грани – даже 1200 °С
и выше.
3.1.4. Зависимость температуры резания
от условий обработки
При рассмотрении вопроса о влиянии различных факторов на среднюю температуру контакта речь будет идти о температуре, измеренной естественной термопарой. Как правило, температура на передней поверхности резца выше, нежели на задней. Однако температура изношенного резца часто выше, чем на передней.
При обработке аустенитных сталей и сплавов температура
в 1,5–2 раза выше, чем при обработке конструкционных сталей.
При обработке жаропрочных сталей и сплавов температураеще выше, так как помимо высоких прочностных свойств эти материалы, как правило, обладают и низкой теплопроводностью.
Чем ниже теплопроводность инструментального материала, тем выше температура резания. Например, минералокерамика имеет теплопроводность ниже, чем твердосплавные инструменты, а поэтому температурапри работе с минералокерамикой будет выше.
Твердые сплавы группы ТК имеют температурувыше, чем резцы из ВК, так как титан имеет низкую теплопроводность.
Из элементов режима резания наибольшее влияние оказывает скорость резания (рис. 90, 91). Однако температура резания
повышается с увеличением скорости непропорционально, поскольку с ростом скорости V уменьшается пластическая деформация, а следовательно, и количество тепла, образующегося
в результате деформации.
а б
Рис. 91. Температурное поле зоны резания при сверлении с различными скоростями резания (расчет методом конечных элементов); радиус режущей кромки 4 мм; глубина резания 5 мм: а – скорость резания 1,2 м/с; б – скорость
резания 2,4 м/с
– 20 °C;
– 300 °C;
– 600 °C
Tемпература резания повышается также непропорционально глубине резания t и подаче s. С увеличением t увеличивается работа резания, а следовательно, и количество тепла, но одновременно
с этим увеличивается активная длина режущей кромки инструмента, что улучшает теплоотвод.
С увеличением подачи S увеличивается количество тепла, но рост силы отстает от роста подачи. Кроме того, с увеличением S увеличивается ширина контакта с передней поверхностью, что улучшает условия теплоотвода. Следует отметить, что глубина резания t больше, чем S, влияет на температуру. Это объясняется тем, что с увеличением t теплоотвод лучше, чем с увеличением S. Этот факт лежит
в основе II закона резания: «С точки зрения температурного режима работать нужно на больших глубинах, даже за счет снижения подачи». Поэтому выбор режимов резания начинают с глубины резания t.
3.1.5. Эмпирическая формула
для расчета температуры резания
Обобщенная формула зависимости температуры от режимов резания имеет следующий вид:
q = С q V x S у t z, °С.
Причем х > у > z, а переменная х никогда не равна 1, х < 1. Коэффициент С qзависит от физико-механических свойств обрабатываемого материала, геометрических параметров инструмента, применяемых СОТС.
3.1.6. Понятия об оптимальной температуре
резания
Оптимальная температура резания (контакта) – это температура, при которой наблюдается наименьшая интенсивность износа инструмента (рис. 92). Оптимальная температура зависит от свойств как обрабатываемого, так и инструментального материалов.
Например, при обработке сталей 40 ХНМА, ЭИ736 и ЭИ654 резцом Т14К8 значение оптимальной температуры резания qо составляет соответственно 820, 770 и 930 °С, а при обработке стали X18Н9Т резцами ВК8, ВK2 и Т14К8 – 785, 800 и 850 °С.
Определенное влияние на температуру резания оказывают и геометрические параметры инструмента.
С увеличением j происходит уменьшение рабочей длины лезвия – теплоотвод ухудшается, в результате температура растет,
и наоборот (рис. 93, а).
Увеличение радиуса резца при вершине R способствует увеличению рабочей длины лезвия – улучшается теплоотвод, что приводит
а б в
Рис. 93. Зависимость температуры резания q от главного угла в плане j,
радиуса при вершине резца R и угла резания d
к снижению температуры резания q (рис. 93, б). С увеличением угла резания d температура резания растет (рис. 93, в).
Увеличение площади поперечного сечения стержня резца приводит к снижению температуры резания за счет лучшего теплоотвода.
3.2. Смазывающе-охлаждающие
технологические средства
Одним из наиболее простых и доступных путей интенсификации процесса механообработки является увеличение режимов обработки. Наибольший эффект в этом случае дает увеличение толщины срезаемого слоя. Но при этом приходится существенно снижать скорость резания для сохранения заданного периода стойкости. Исключить эти ограничения возможно, если при резании использовать смазочно-охлаждающие технологические средства.
СОТС являются одним из наиболее важных переменных факторов состояния системы резания. За счет изменения состава и состояния СОТС можно эффективно осуществлять глубокие и многосторонние изменения параметров функционирования системы резания.
Применение эффективных СОТС выдвигают на первый план всякий раз, когда создают или совершенствуют существующие методы обработки резанием в целях обеспечения резкого повышения режима резания, что сопровождается соответствующим увеличением объема сжимаемой стружки в единицу времени. В этих случаях СОТС играют роль, с одной стороны, фактора, снижающего интенсивность силовых и тепловых нагрузок на режущий инструмент и обрабатываемую деталь, а с другой стороны – средства, позволяющего своевременно удалять из зоны резания образующуюся стружку
и продукты износа инструмента. Таким образом, СОТС являются органическим элементом комплекса средств, обеспечивающих эффективную эксплуатацию металлообрабатывающего оборудования
и освоение новых прогрессивных методов и технологических процессов обработки металлов. Являясь одним из наиболее важных переменных факторов состояния системы резания, СОТС оказывают глубокое и многостор
|
|
Поперечные профили набережных и береговой полосы: На городских территориях берегоукрепление проектируют с учетом технических и экономических требований, но особое значение придают эстетическим...
История развития хранилищ для нефти: Первые склады нефти появились в XVII веке. Они представляли собой землянные ямы-амбара глубиной 4…5 м...
Адаптации растений и животных к жизни в горах: Большое значение для жизни организмов в горах имеют степень расчленения, крутизна и экспозиционные различия склонов...
Архитектура электронного правительства: Единая архитектура – это методологический подход при создании системы управления государства, который строится...
© cyberpedia.su 2017-2024 - Не является автором материалов. Исключительное право сохранено за автором текста.
Если вы не хотите, чтобы данный материал был у нас на сайте, перейдите по ссылке: Нарушение авторских прав. Мы поможем в написании вашей работы!