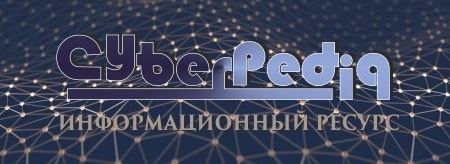
Архитектура электронного правительства: Единая архитектура – это методологический подход при создании системы управления государства, который строится...
Механическое удерживание земляных масс: Механическое удерживание земляных масс на склоне обеспечивают контрфорсными сооружениями различных конструкций...
Топ:
История развития методов оптимизации: теорема Куна-Таккера, метод Лагранжа, роль выпуклости в оптимизации...
Проблема типологии научных революций: Глобальные научные революции и типы научной рациональности...
Методика измерений сопротивления растеканию тока анодного заземления: Анодный заземлитель (анод) – проводник, погруженный в электролитическую среду (грунт, раствор электролита) и подключенный к положительному...
Интересное:
Национальное богатство страны и его составляющие: для оценки элементов национального богатства используются...
Отражение на счетах бухгалтерского учета процесса приобретения: Процесс заготовления представляет систему экономических событий, включающих приобретение организацией у поставщиков сырья...
Принципы управления денежными потоками: одним из методов контроля за состоянием денежной наличности является...
Дисциплины:
![]() |
![]() |
5.00
из
|
Заказать работу |
Содержание книги
Поиск на нашем сайте
|
|
Сплошной контроль применяется в тех случаях, когда технологический процесс не обеспечивает достаточной стабильности заданных размеров и других параметров качества продукции; при неоднородности качества материалов или комплектующих изделий; после технологических операций, от которых в значительной мере зависят точность или другие качественные показатели изделия (например, после чистового шлифования направляющих станины прецизионного станка, после растачивания отверстий под подшипники в корпусе редуктора и т. п.) а также при проверке сложной или точной готовой продукции. Следует учесть, что сплошной контроль деталей на рабочем месте самим рабочим не всегда экономически оправдан, так как при этом рабочий будет на значительное время отвлекаться от своих основных обязанностей — непосредственного выполнения операции и наблюдения за ходом технологического процесса.
По иному обстоит дело при использовании выборочного метода контроля. Здесь рабочий-оператор имеет возможность больше уделять внимания вопросу поддержания стабильности технологического процесса, обеспечивая, таким образом, бездефектную работу. При выборочном контроле особое значение имеет определение оптимальной выборки — количества проверяемых деталей из каждой партии.
При обычном выборочном контроле ее размер определяется на основании анализа ряда выборок из различных партий данного наименования детали без расчетного обоснования. Для более точного и обоснованного определения размера выборки (при котором учитывается точность проверяемого параметра, состояние оборудования и оснастки, квалификация рабочего и другие факторы, определяющие качество работы) применяется статистический метод контроля, при котором количество деталей из партии, подлежащих проверке, определяется расчетным путем. Статистический контроль применяется главным образом при проверке крупных партий деталей.
|
Однако необходимо иметь в виду, что выборочный метод контроля обработанных деталей может обеспечить достаточную информацию об их качестве лишь при хорошо налаженном и стабильном технологическом процессе. Вместе с тем данный метод является наиболее целесообразным при организации контроля на рабочих местах, внедрении бездефектной работы и личных клейм.
Необходимо при внедрении выборочного контроля создать все условия (нормальную работу станка, своевременную заточку инструмента, идентичные припуски и однородность качества материала заготовок и т. п.) для получения максимальной стабильности размеров и других качественных показателей обработанных деталей, иными словами, обеспечить все предпосылки для успешного применения метода выборочного контроля операторами на рабочих местах.
Различают также такие виды контроля, как пооперационный (после каждой операции) и групповой (после группы операций). Пооперационный контроль применяется при выполнении наиболее точных работ, а также в тех случаях, когда качество одной технологической операции существенно влияет на последующую обработку детали. (Например, фрезерование базовой поверхности корпуса редуктора, шлифование точных отверстий во втулках для последующего их хонингования и т. п.).
Фрезерование
Фрезерование-обработка резанием металлических и неметаллических материалов при котором режущий инструмент - фреза - имеет вращательное движение, а обрабатываемая заготовка - поступательное. Фрезерование применяется для обработки плоскостей, криволинейных поверхностей деталей, резьбовых поверхностей, зубьев зубчатых и червячных колес и т.п. Фрезерование осуществляется на фрезерных станках.
|
Фрезерование в металлообработке, процесс резания металлов и др. твёрдых материалов фрезой. Ф. применяется для обработки плоских и фасонных поверхностей (в т. ч. резьбовых поверхностей, зубчатых и червячных колёс) и осуществляется на фрезерных станках. Главное движение при Ф. — вращение инструмента, движение подачи — поступательное перемещение заготовки; скорость резания равна окружной скорости наиболее удалённых от оси фрезы точек её зубьев. При Ф. различают три вида подачи. Минутная подача S (в мм/мин); подача на один оборот фрезы S0 (в мм/об); подача на один зуб фрезы Sz (в мм/зуб) — относительное перемещение фрезы и заготовки при повороте фрезы на один угловой шаг e =(360/z) Sz характеризует интенсивность нагрузки зуба в процессе Ф. (стойкость фрезы) и вычисляется по формуле
где z — число зубьев фрезы, n — частота вращения фрезы (об/мин). Глубина резания t (мм) при Ф. — толщина срезаемого слоя металла, измеренная перпендикулярно к обработанной поверхности. Ширина Ф. В (мм) — ширина обрабатываемой поверхности в направлении, параллельном оси фрезы. Существуют две возможные схемы Ф.: против подачи (встречное Ф.), когда в нижней точке контакта фрезы с обрабатываемой заготовкой векторы скорости резания и подачи противоположны, и по подаче (попутное Ф.), когда эти векторы совпадают, amax — наибольшая толщина срезаемого слоя металла; Y — угол контакта фрезы. При черновом Ф. обычно применяется вторая схема, при чистовом Ф. — первая. Площадь поперечного сечения слоя металла, срезаемого зубом фрезы, меняется в каждый момент времени резания и, следовательно, меняются и действующие на зуб силы. Равномерное Ф. может быть достигнуто при использовании фрез с винтовыми зубьями, работа которых характеризуется примерным постоянством площади поперечного сечения срезаемого слоя металла. Основное технологическое время при Ф.:
мин,
где L — общая длина прохода заготовки (в мм) относительно фрезы в направлении подачи, i — число проходов. Скорость резания, допускаемая при Ф., зависит от типа фрезы, материала и геометрических параметров её режущей части и др. элементов, режима резания, состояния поверхностного слоя заготовки и т.п. (см. Обработка металлов резанием). В процессе Ф. возникают силы сопротивления резанию. По окружной силе может быть определён крутящий момент на шпинделе фрезерного станка. Осевая сила действует на подшипник шпинделя станка, устройство для закрепления заготовки, а также детали и узлы механизма подачи. Радиальная сила действует на опоры шпинделя и оправку, в которой закрепляется фреза. Горизонтальная сила нагружает механизм подачи и устройство для закрепления заготовки.
|
Строгание
Обработка резанием строгальная обработка заключается в снятии верхней стружки с обрабатываемой поверхности. Весь процесс базируется на ряде возвратно-поступательных движений, которые совершает либо станок, либо сама заготовка. Все зависит от величины обрабатываемой площади и механических характеристик рабочего станка.
Для обработки используется несколько видов резцов, которые классифицируются:
- по назначению
- конфигурации стержня
- направленности головки
В последнее время широко применяются комбинированные резцы, режущая часть которых может быть выполнена из твердых сплавов или быстрорежущей стали.
Процесс резания металла посредством строгания
Обработка резанием строгальная обработка осуществляется на нескольких видах станков. Среди них строгально-долбежные, поперечно/продольно – строгальные, кромкострогальные и так далее. Главным параметров, при выборе станка на производстве выступает скорость и качество его работы, которое напрямую зависит от поступательных движений станка или резца. Для того, чтобы улучшить результат и добиться большей производительности, достаточно часто используется многорезцовый способ. Он заключается в установки нескольких широких резцов, оснащенных твердосплавной режущей частью.
В начале работы, важно все движения выполнять плавно, исключая всякую возможность резких ударов. Не менее продуктивно исключение холостого хода, которое так же способствует понижению результативности работы.
На станках используются исключительно прямые или изогнутые строгальные резцы. Прямые устанавливаются при малых вылетах, так как они не виброустойчивы, но очень просты в применении. Недостатки их применения заключаются в невозможности получить максимально точный слой снятого металла. При возможном усилении нажима, изменения в конфигурации детали или сплава, из которого она сделана, прямые резцы слишком сильно углубляются и способны испортить изделие. Изогнутые резцы более универсальны и пользуются большой популярностью в сфере обработки металлов. Они в обязательном порядке устанавливаются во время обработки большого вылета, и там где необходимо качественное, до миллиметра точное снятие металла с обрабатываемой поверхности. Во время усиления нажима они пружинят, снимая стружку с максимальной точностью и не создавая брак.
|
Шлифование
Шлифование — один из видов обработки металлов резанием. При шлифовании припуск на обработку снимается абразивными инструментами — шлифовальными кругами. Шлифовальный круг представляет собой пористое тело, состоящее из большого количества мелких зерен. Эти зерна соединены между собой особым веществом, которое называется связкой. Твердые материалы, из которых образованы зерна шлифовального круга, называются абразивными материалами. Процесс шлифования состоит в том, что шлифовальный круг снимает с детали тонкий слой металла (стружку) острыми гранями своих абразивных зерен
Принципиальной разницы в законах резания металлов металлическими и неметаллическими инструментами не существует.
Однако процесс резания металлов различными инструментами, в том числе и шлифование, кроме общих закономерностей, имеет свои особенности.
К особенностям процесса шлифования следует отнести:
1) высокую скорость резания;
2) сильное размельчение и своеобразный характер снимаемой стружки;
3) невыгодную геометрию режущих зерен шлифовального круга;
4) высокое нагревание обрабатываемой поверхности и стружки.
Поясним кратко эти особенности. При обычном шлифовании скорость резания принимается равной 30 м/сек, или 1800 м/мин, а при скоростном — 50 м/сек, или 3000 м/мин. Это в 10—30 раз превышает скорость резания при токарной обработке. Процесс снятия стружки абразивным (режущим) зерном осуществляется примерно за 0,0001—0,00005 сек.
Число абразивных зерен, расположенных на периферии шлифовального круга, очень велико, оно измеряется на кругах средних размеров десятками и сотнями тысяч штук. Поэтому при шлифовании стружка снимается огромным числом беспорядочно расположенных режущих зерен, к тому же неправильной формы, что приводит к очень сильному размельчению стружки и вызывает большой расход энергии. Затрата энергии на единицу веса снимаемого металла при шлифовании в 4—5 раз больше, чем при фрезеровании, и в 12—13 раз больше, чем при точении.
Абразивные зерна, как правило, имеют отрицательные углы резания. Работу каждого отдельно взятого абразивного зерна можно сравнивать с работой резца, имеющего отрицательный передний угол. Так, если при работе другими инструментами их режущей части можно придать наивыгоднейшую геометрию, то с зернами шлифовального круга этого сделать нельзя.
|
Шлифовальный круг имеет прерывистую, режущую кромку. Высокие скорости резания, трение связки шлифовального круга об обрабатываемую поверхность, произвольная геометрия абразивных зерен, сильное размельчение стружки приводят к тому, что в зоне шлифования выделяется большое количество тепла. Высокая температура поверхностных слоев шлифуемой детали, достигающая 1000° и больше, вызывает изменение структуры и физических свойств металла.
Снимаемая стружка в большей своей части похожа на стружку, снимаемую другими инструментами. Часть стружки отлетает от шлифуемой детали, а некоторая часть ее размещается в порах шлифовального круга и вымывается из них охлаждающей жидкостью. Небольшая часть ее сгорает. По мере притупления шлифовальные зерна врезаются в металл все с большим и большим усилием. В тот момент, когда усилие по величине превзойдет прочность зерна или удерживающей его связки, зерно разрушится или полностью выкрошится.
ЭСКИЗ
ОПЕРАЦИОННАЯ КАРТА
ОПЕРАЦИОННАЯ КАРТА
ОПЕРАЦИОННАЯ КАРТА
Часть II
|
|
Механическое удерживание земляных масс: Механическое удерживание земляных масс на склоне обеспечивают контрфорсными сооружениями различных конструкций...
Индивидуальные и групповые автопоилки: для животных. Схемы и конструкции...
История создания датчика движения: Первый прибор для обнаружения движения был изобретен немецким физиком Генрихом Герцем...
Археология об основании Рима: Новые раскопки проясняют и такой острый дискуссионный вопрос, как дата самого возникновения Рима...
© cyberpedia.su 2017-2024 - Не является автором материалов. Исключительное право сохранено за автором текста.
Если вы не хотите, чтобы данный материал был у нас на сайте, перейдите по ссылке: Нарушение авторских прав. Мы поможем в написании вашей работы!