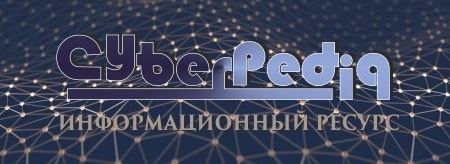
Археология об основании Рима: Новые раскопки проясняют и такой острый дискуссионный вопрос, как дата самого возникновения Рима...
Папиллярные узоры пальцев рук - маркер спортивных способностей: дерматоглифические признаки формируются на 3-5 месяце беременности, не изменяются в течение жизни...
Топ:
Генеалогическое древо Султанов Османской империи: Османские правители, вначале, будучи еще бейлербеями Анатолии, женились на дочерях византийских императоров...
Комплексной системы оценки состояния охраны труда на производственном объекте (КСОТ-П): Цели и задачи Комплексной системы оценки состояния охраны труда и определению факторов рисков по охране труда...
Основы обеспечения единства измерений: Обеспечение единства измерений - деятельность метрологических служб, направленная на достижение...
Интересное:
Аура как энергетическое поле: многослойную ауру человека можно представить себе подобным...
Отражение на счетах бухгалтерского учета процесса приобретения: Процесс заготовления представляет систему экономических событий, включающих приобретение организацией у поставщиков сырья...
Берегоукрепление оползневых склонов: На прибрежных склонах основной причиной развития оползневых процессов является подмыв водами рек естественных склонов...
Дисциплины:
![]() |
![]() |
5.00
из
|
Заказать работу |
|
|
Наименование константы | Ацетон | Метилэтил-кетон (МЭК) | Толуол |
Температура кипения, о С | 56,5 | 79,6 | 110,6 |
Температура плавления, оС | -95,5 | -86,4 | -95,0 |
Плотность при 20оС, кг/м3 | 791,5 | 805,0 | 866,9 |
Показатель преломления, ![]() | 1,3591 | 1,3789 | 1,4969 |
Молекулярная масса | 58,08 | 72,1 | 92,13 |
Вязкость при 20 оС, мм2/ с | 0,41 | 0,52 | 0,68 |
Дипольный момент, D | 2,72 | 2,76 | 0,37 |
В настоящее время в качестве растворителя применяют также высшие кетоны – метилизобутилкетон, метилизопропилкетон и др. Высшие кетоны не требуют добавления толуола.
Основным показателем, определяющим глубину депарафинизации, является температура застывания полученного продукта. Самой ответственной стадией в данном процессе является стадия кристаллизации твердых углеводородов, от которой зависят выход целевого продукта, скорость фильтрования суспензии, содержание масла в гаче (петролатуме).
Процесс депарафинизации состоит из следующих основных стадий: растворения депарафинируемого сырья в растворителе и термической обработки полученного раствора; охлаждения раствора до температуры выделения основной массы твердых углеводородов, определяемой температурой застывания масла с учетом температурного градиента депарафинизации; фильтрования – отделения жидкой фазы от твердой; отгона растворителя от фильтрата и лепешки на фильтре.
При выборе условий процесса исходят из свойств депарафинируемого сырья (содержания парафинов, вязкости) и необходимой глубины депарафинизации. Основными факторами процесса являются: природа растворителя и его кратность к сырью, способ подачи растворителя (единовременно или порционно), скорость охлаждения раствора, температура депарафинизации, которую выбирают в зависимости от требуемой температуры застывания масла и температурного эффекта депарафинизации (ТЭД). Последний определяется разностью между температурами фильтрования и застывания депарафинированного продукта. В соответствии с этим температуру конечного охлаждения или фильтрования Тф определяют, исходя из требуемой температуры застывания Тз и ТЭД для выбранного растворителя по следующему уравнению:
|
Тф = ТЭД + Тз
Примерные температурные эффекты депарафинизации для наиболее распространенных растворителей, оC:
Нафта...................От –25 до –29
Пропан...............От –15 до –20.
Метилэтилкетон (МЭК) + толуол (40% + +60%)......От – 8 до –10.
Ацетон + толуол (35% + 65%).....От – 10 до –12.
Метилизобутилкетон…….От 0 до –3.
Из всех указанных растворителей наибольшее распространение получили смеси ацетона или метилэтилкетона с толуолом; применяются и высшие кетоны. Максимальное содержание ацетона в смеси не должно превышать 40 % для дистиллятных и 35 % для остаточных рафинатов; содержание МЭК не более 50-60% и 40-50% соответственно. Высшие кетоны – метилизобутилкетон, метилизопропилкетон не требуют добавления толуола. На отечественных заводах применяют ацетон-толуол и МЭК-толуол, за рубежом – высшие кетоны. Кратность растворителя к сырью зависит от вязкости сырья и глубины охлаждения. Для дистиллятных рафинатов массовая кратность растворителя к сырью составляет 2,0 ÷ 3,5: 1; для остаточных – 3,0 ÷ 5, 0: 1. С увеличением глубины охлаждения расход растворителя возрастает. При температурах охлаждения до минус 60°С для маловязких дистиллятов кратность растворителя к сырью составляет 4 ÷ 5: 1.
Аппаратура и реагенты
Процесс депарафинизации проводят с испольэованием следующего лабораторного оборудования и реагентов:
1. Коническая колба вместимостью 0,5 ÷ 1,0 л для охлаждения раствора сырья в растворителе.
2. Металлическая баня, обтянутая войлоком, для охлаждения колбы с раствором сырья в растворителе и растворителя для промывки.
|
3. Фарфоровая воронка Бюхнера, вставленная в металлический обтянутый войлоком кожух, куда наливается охлаждающая смесь (денатурат, спирт и т.п.), и предназначена для охлаждения и поддержания необходимой температуры фильтрации.
4. Приемник фильтрата вместимостью не менее 0,5 ÷ 1,0л (колба Бунзена или цилиндрический стеклянный градуированный приемник).
5. Термометры с ценой деления 1 оС до минус 35 оС или минус 60 оС.
6. Колбы Вюрца (вместимостью 0,25 ÷ 1,0 л.) с тубусами для термометра и капилляра (для подачи инертного газа).
7. Холодильник Либиха.
8. Приемник для сбора регенерированного растворителя.
9. Колбонагреватель.
10. Вакуумный насос.
11. Вакууметр.
12. Технические весы.
13. Растворители: метилэтилкетон (ацетон), толуол.
14. Охлаждающая смесь: денатурат (спирт) и жидкий азот.
15. Бумажные фильтры.
Порядок выполнения работы
1. Перед началом депарафинизации приготовляют растворитель смешением 40 объемных долей МЭК и 60 объемных долей толуола или 30 объемных долей ацетона и 70 объемных долей толуола.
2. Подготавливают к работе баню (кристаллизатор) для охлаждения смеси и аппарат для фильтрования суспензии. Для этого в баню-кристаллизатор и баню фильтра заливают денатурат, устанавливают термометры, на воронку Бюхнера помещают бумажный фильтр.
3. Сырье разогревают до полного расплавления. В коническую колбу отвешивают навеску сырья в количестве 50-100 г. (± 0,1 г.) и приливают необходимое количество растворителя в соответствии с выбранной кратностью. Разбавление сырья – одноразовое или порционное (в зависимости от задания). Затем проводят термическую обработку при 50-60 оС в течение 10 мин. Условиями проведения опыта задаются.
Охлаждение раствора ведется при постоянном перемешивании сначала на воздухе до 30 оС, затем водой до 15 оС и после этого колбу помещают в баню-кристаллизатор с охлаждающей смесью, соблюдая скорость охлаждения суспензии – 2,0 оС в минуту. В эту же баню ставят колбу с растворителем для промывки.
4. Одновременно с охлаждением суспензии ведется охлаждение фильтра, помещенного в металлический кожух. Температура в бане должна быть на 4-5 оС ниже заданной температуры охлаждения сырья.
5. Прежде чем приступить к фильтрованию, со стенок фильтра гигроскопической ватой удаляют образовавшиеся при охлаждении капли росы, после чего включают вакуум-насос, в приемнике фильтрата создают вакуум 86-75 кПа (600-560 мм рт. ст.) и смачивают фильтр растворителем так, чтобы его присосало к поверхности фильтра. После этого охлажденную до заданной температуры смесь сырья и растворителя переносят на фильтр и фильтруют до появления сухой лепешки твердых углеводородов. Затем лепешку промывают охлажденным до температуры фильтрации растворителем в количестве 100% мас. на сырье и вновь фильтруют. Полное время фильтрации складывается из времени фильтрации суспензии, времени промывки и времени подсушки лепешки.
|
Одним из основных показателей процесса депарафинизации является скорость охлаждения раствора (град/ч) и скорость фильтрования (м3/м2*ч). Эти показатели определяют следующим образом: скорость охлаждения – по показаниям термометра, вставленного в охлаждаемую смесь и секундомера, включенного одновременно с охлаждением; скорость фильтрования – фиксируя время, в течение которого в приемник поступает определенное количество фильтрата (25, 50, 100 мл), и зная поверхность фильтра. Толщина лепешки на фильтре должна быть не более 10-12мм.
6. Лепешка с фильтра и фильтрат количественно переносят в колбы, взвешивают и отгоняют растворитель. Растворитель из растворов депарафинированного масла и гача (петролатума) отгоняется в токе инертного газа (во избежании местного перегрева продукта) при температуре не выше 1200С. Остатки растворителя отгоняются под вакуумом.
7.После отгона растворителя колбы охлаждают и взвешивают. Составляют материальные балансы процесса депарафинизации по формам табл.2 и 3.
Сырье, депарафинированное масло, гач (петролатум) анализируют, определяя вязкость при 400С и 1000С, плотность, температуру застывания, показатель преломления, температуру плавления гача (петролатума) табл.4.
Оформление отчета
Отчет должен содержать описание работы, условия проведения процесса:
- депарафинируемое сырье и его количество;
- состав растворителя и его количество:
а) на разбавление, % мас. на сырье,
б) на промывку, % мас. на сырье;
- температура термообработки, 0С;
|
- температура конечного охлаждения смеси сырья и растворителя, 0С;
- материальные балансы по сырью и растворам;
- качество сырья и полученных продуктов;
- выводы.
Контрольные вопросы
1. Назначение и теоретические основы процесса депарафинизации.
2. Применяемые растворители. Роль каждого компонента в парном растворителе.
3. Понятие о температурном эффекте депарафинизации (ТЭД). Выбор конечной температуры охлаждения.
4. Факторы, влияющие на процесс депарафинизации:
- скорость охлаждения;
- количество растворителя;
- состав растворителя;
- способ подачи растворителя;
- качество сырья;
- температура депарафинизации;
5.. Сравнительная оценка показателей качества сырья и депарафинированного масла.
|
|
Особенности сооружения опор в сложных условиях: Сооружение ВЛ в районах с суровыми климатическими и тяжелыми геологическими условиями...
Автоматическое растормаживание колес: Тормозные устройства колес предназначены для уменьшения длины пробега и улучшения маневрирования ВС при...
Таксономические единицы (категории) растений: Каждая система классификации состоит из определённых соподчиненных друг другу...
Историки об Елизавете Петровне: Елизавета попала между двумя встречными культурными течениями, воспитывалась среди новых европейских веяний и преданий...
© cyberpedia.su 2017-2024 - Не является автором материалов. Исключительное право сохранено за автором текста.
Если вы не хотите, чтобы данный материал был у нас на сайте, перейдите по ссылке: Нарушение авторских прав. Мы поможем в написании вашей работы!