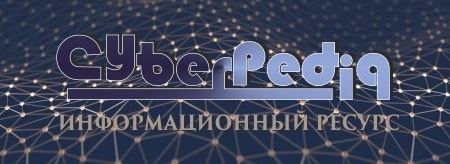
Биохимия спиртового брожения: Основу технологии получения пива составляет спиртовое брожение, - при котором сахар превращается...
Организация стока поверхностных вод: Наибольшее количество влаги на земном шаре испаряется с поверхности морей и океанов (88‰)...
Топ:
Комплексной системы оценки состояния охраны труда на производственном объекте (КСОТ-П): Цели и задачи Комплексной системы оценки состояния охраны труда и определению факторов рисков по охране труда...
Организация стока поверхностных вод: Наибольшее количество влаги на земном шаре испаряется с поверхности морей и океанов...
Интересное:
Мероприятия для защиты от морозного пучения грунтов: Инженерная защита от морозного (криогенного) пучения грунтов необходима для легких малоэтажных зданий и других сооружений...
Уполаживание и террасирование склонов: Если глубина оврага более 5 м необходимо устройство берм. Варианты использования оврагов для градостроительных целей...
Принципы управления денежными потоками: одним из методов контроля за состоянием денежной наличности является...
Дисциплины:
![]() |
![]() |
5.00
из
|
Заказать работу |
|
|
Введение
Для любой отопительной системы основной задачей является поддержание уровня температуры в отапливаемой емкости, трубопроводе, помещении. Поддерживать необходимую температуру можно разными способами, однако, самым распространенным является способ, основанный на применении специальных устройств - регуляторов температуры.
На протяжении многих веков люди стремились, собрать и как можно дольше сохранить ценность и качество молока. От глиняных крынок и бутылок до самых современных резервуаров-холодильников и технологических резервуаров прошли свой путь различные виды контейнеров для молока. Емкости широкого спектра и назначения нашли себе применение на всех этапах технологического процесса.
Невозможно представить себе производство пищевых, в том числе молочных продуктов, без емкостей.
В зависимости от принятой технологии доения и обработки молока перед отправкой на молочный завод, его некоторое время хранят на животноводческой ферме, используя для этих целей фляги, приемные баки (отрытые и вакуумные), резервуары для молока и молочных продуктов, резервуары-охладители.
История создания регуляторов температуры
В 50 годах 20 века, в эру развития систем автоматизации, появляются первые устройства для автоматического управления технологическими процессами и установками, осуществляющие поддержание технологических параметров на заданных значениях – регуляторы. Данные приборы принимают от первичного преобразователя текущие значения параметра, производят аналоговую обработку этого сигнала и выдают управляющий сигнал на исполнительный механизм. Существует классификация регуляторов в зависимости от направления действия:
|
1. Регуляторы прямого действия (управляют исполнительным механизмом за счет энергии, получаемой от регулируемой среды)
2. Регуляторы непрямого действия (управляют исполнительным механизмом за счет энергии, получаемой от постороннего источника).
Чуть позже, в конце 80-х годов, появляются более совершенные устройства, обрабатывающие информацию в цифровом виде при помощи процессоров – контроллеры. Эти устройства обладают более широкими возможностями и не только выполняют функции регулирования, но и заменяют релейные схемы управления и сигнализации. Контроллеры могут отображать параметры на индикаторах и создавать архивы параметров, т.е. выполнять функции вторичных показывающих и регистрирующих приборов. Также они могут вести журналы событий (фиксация неисправностей оборудования, его включение и отключение, отклонения параметров от заданных значений и т.д.), которые, до появления контроллеров, заполнялись операторами технологических процессов вручную.
Технические характеристики терморегуляторов
Основными техническими характеристиками, по которым можно судить о работе регуляторов температуры прямого действия являются:
1) Время срабатывания - зависит от конструкции терморегулирующего механизма (сильфона и капиллярной трубки) и способа установки датчика температуры, определяющего инерционность;
2) Диапазон регулируемой температуры - температура, в пределах которой может выполняться регулирование;
3) Зона пропорциональности - отклонение значения реальной температуры от заданного значения, при котором клапан полностью открыт или полностью закрыт. Данная характеристика приводится в тех. документации к прибору;
4) Гистерезис - минимальное значение изменения температуры, на которое способен реагировать регулятор;
5) DN регулятора температуры - используемый для унификации типоразмеров для всей трубопроводной арматуры номинальный диаметр отверстия присоединительных патрубков;
|
6) PN регулятора температуры - допустимое для безаварийной эксплуатации регулятора, номинальное максимально допустимое избыточное давление (при t=20oC);
7) KN регулятора температуры - коэффициент пропускной способности регулятора температуры, применяемый в гидравлических расчетах вычисления потерь напора в системах отопления.
Рекомендации по выбору типа термопары
Тип J (железо-константановая термопара):
1. Не рекомендуется использовать ниже 0 °С, т.к. конденсация влаги на железном выводе приводит к образованию ржавчины;
2. Наиболее подходящий тип для разряженной атмосферы;
3. Максимальная температура применения – 500 °С, т.к выше этой температуры происходит быстрое окисление выводов. Оба вывода быстро разрушаются в атмосфере серы.
4. Показания повышаются после термического старения.
5. Преимуществом является также невысокая стоимость.
Тип Е (хромель-константановая термопара):
1. Преимуществом является высокая чувствительность.
2. Термоэлектрическая однородность материалов электродов.
3. Подходит для использования при низких температурах.
Тип Т (медь-константановая термопара):
1. Может использоваться ниже 0 °С;
2. Может использоваться в атмосфере с небольшим избытком или недостатком кислорода;
3. Не рекомендуется использование при температурах выше 400 °С;
4. Не чувствительна к повышенной влажности;
5. Оба вывода могут быть отожжены для удаления материалов, вызывающих термоэлекрическую неоднородность.
Тип К (хромель-алюмелевая термопара):
1. Широко используются в различных областях от – 100 °С до +1000 °С (рекомендуемый предел, зависящий от диаметра термоэлектрода);
2. В диапазоне от 200 до 500 °С возникает эффект гистерезиса, т.е показания при нагреве и охлаждении могут различаться. Иногда разница достигает 5 °С;
3. Используется в нейтральной атмосфере или атмосфере с избытком кислорода;
4. После термического старения показания снижаются;
5. Не рекомендуется использовать в разряженной атмосфере, т.к. хром может выделяться из Ni-Cr вывода (так называемая миграция), термопара при этом изменяет ТЭДС и показывает заниженную температуру;
6. Атмосфера серы вредна для термопары, т.к. воздействует на оба электрода.
Тип N (нихросил-нисиловая термопара)
|
1. Это относительно новый тип термопары, разработанный на основе термопары типа К. Термопара типа К может легко загрязняться примесями при высоких температурах. Сплавляя оба электрода с кремнием, можно тем самым загрязнить термопару заранее, и таким образом снизить риск дальнейшего загрязнения во время работы.
2. Рекомендуемая рабочая температура до 1200 °С (зависит от диаметра проволоки).
3. Кратковременная работа возможна при 1250 °С;
4. Высокая стабильность при температурах от 200 до 500 °С (значительно меньший гистерезис, чем для термопары типа К);
5. Считается самой точной термопарой из неблагородных металлов.
Формирование спая
Существует много способов формирования рабочего спая термопары: механическое скручивание, пайка, сварка и т.д. При сварке в спай добавляется третий метал, но т.к. температуры проводников, исходящих из спая одинаковы, это не может привести к какой-либо погрешности. Проблема заключается в том, что третий метал, как правило, имеет более низкую температуру плавления и при высоких температурах спай может разорваться. Более того, может происходить загрязнение электродов чужеродным испаряющимся металлом. Поэтому рекомендуется производить сварку рабочего спая. Однако процесс сварки тоже требует особого внимания, т.к. перегрев может повредить термопарную проволоку и газ, используемый для сварки, может диффундировать в проволоку. Дефектная сварка может привести в разрыву спая при эксплуатации. В программном обеспечении, используемом для считывания и обработки сигнала термопары всегда есть специальный тест на разрыв спая.
Образование термоэлектрической неоднородности. Искажение градуировочной характеристики термопары
Это наиболее серьезный и трудно диагностируемый источник погрешности, т.к. результат отсчета ТЭДС может показаться вполне приемлемым и в то же время быть ошибочным. Термоэлектрическая неоднородность может быть результатом диффузии примесей из окружающей атмосферы при высоких температурах, высокотемпературным отжигом или механической обработкой электродов. Она может образоваться в результате протягивания электродов, неосторожного обращения, ударов и вибраций, вызывающих напряжения в проволоке. Изменение состава сплава может наблюдаться на отдельном участке проволоки, находящейся длительное время в зоне резкого температурного градиента. Однако неоднородность влияет на изменение градуировочной характеристики только в том случае, если она попадает в зону температурного градиента при измерении. Чем больше градиент температуры, тем больше погрешность, возникающая из-за неоднородности. Один из способов уменьшения данной погрешности – сделать более плавным изменение температуры на длине термоэлектрода, например, используя металлические рукава и чехлы.
|
Танки для хранения молока
Танки для хранения молока имеют горизонтальную или вертикальную конструкцию. Параметрический ряд 1 000 тн. до150 000 тн. такие как – ВУ-1000; В2-ОМВ-2,5; В2-ОМВ-6,3; В2-ОМГ-10; В2-ОМВ-10; В2-ОМГ-25; В2-ОХР-25; В2-ОХР-50 и др.) В зависимости от объема они могут быть установлены и вне помещения - для экономии строительных расходов. Перемешивание продукта осуществляется одной или несколькими пропеллерными мешалками для предотвращения всплывания сливок.
Среди емкостей для хранения молока, особое место занимают резервуары, оснащенные фреоновыми охладителями (фреон 22), что позволяет охлаждать молоко до 4-6 градусов. По своей конструкции они подразделяются на ванны и танки. Фреоновое охлаждение может подаваться как в рубашку, так и в мешалку. Среднее повышение температуры молока при отключении электричества – 2 градуса в сутки. Такие резервуары могут быть укомплектованы автоматической системой промывки. Параметрический ряд таких емкостей от 600 литров до 10 000 литров и более.
Технологические емкости
Наиболее сложны по своей конструкции и комплектации технологические танки. Емкость таких танков стандартно варьируется от 100 до 10 000 литров. В зависимости от назначения они могут иметь скошенное дно (ванна нормализации высокожирных сливок ВН-600), различную конструкцию мешалок (лопастные, роторные, рамные и другие). В зависимости от назначения технологических емкостей, мешалки могут быть установлены как в нижней, так и в верхней части. Самые распространенные из них – ванны пастеризации молока марок Г2-ОПА-600; Г2-ОПБ-1000 и ВУ-1000 и резервуары для созревания сливок марки Я1-ОСВ. Установки марок ОЗУ-0,35 и ОЗУ-0,63 используются для приготовления производственных заквасок.
Кроме того, при производстве йогуртов и других кисломолочных продуктов эффективно использование емкостей с так называемым мягким нагревом продукта. Это достигается за счет спиральной паровой рубашки, сконструированной по всей высоте аппарата. Избежать пригара продукта позволяет подача пара под высоким давлением, который, в свою очередь, нагревает воду в рубашке. Такая конструкция установки так же экономит пар, который, при необходимости, возвращается обратно в котельную.
|
Большим спросом так же пользуются технологические емкости (ванны) для производства творога и сыра. Специфика которых варьируется от вида выпускаемого продукта.
Среди новых разработок необходимо отметить различного вида емкости для выработки концентрированных, смешанных и многокомпонентных продуктов Смеситель – это измельчитель для производства плавленых сыров и пастообразных продуктов марки СИ-120 и аппарат для смешивания, измельчения, термической обработки жидких, вязких и пастообразных продуктов марки ГД-600. Они составляют основу линий по производству взбитых вязких молочных и молокосодержащих продуктов марок ЛПВВ-250 и по производству термизированной пасты марки П8-ЛТТМ1. В сочетании с новейшими технологиями это оборудование позволяет выпускать широкий ряд продуктов нового поколения – сыры, муссы, кремы, творожные пасты, десерты, кетчупы, майонезы и многое другое. Термическая обработка, которой подвергается продукт, позволяет увеличивать сроки хранения, таким образом, увеличивая срок реализации.
Для специалистов, интересными будут так же комбинированные емкости, состоящие из цилиндрической и конусной частей. Конструкция специальной рубашки позволяет подавать пар или охлаждающую жидкость с давлением до 9 Атм., и использовать меньшие толщины стенок емкости при работе аппарата под вакуумом или под давлением. В результате, стоимость емкости существенно снижается.
Заквасочник тип ОЗУ-0,35
Предназначен для приготовления производственных заквасок на чистых культурах молочно - кислых бактерий путем пастеризации молока, его сквашивания и охлаждения закваски.
Состоит из резервуара для сквашивания и блока управляющей аппаратуры.
Термоизолированный резервуар снабжен устройством для залива исходного и слива готового продукта, перемешивающим устройством, змеевиками пара и ледяной воды, устройством для мойки внутренней поверхности резервуара, датчиком контроля температуры процесса пастеризации и сквашивания.
Внутренняя ванна резервуара через патрубок заполняется молоком. Перемешивание молока осуществляется мешалкой. В змеевик, расположенный на дне наружной ванны, подается пар под давлением 0,3 ± 0,05 МПа и молоко через водяную ванну нагревается до температуры пастеризации 95° ± 2°С.
После окончания пастеризации продукта, с целью ускорения охлаждения молока до температуры сквашивания, происходит подача водопроводной воды, которая вытесняет горячую воду из рубашки, одновременно включается подача ледяной воды. При необходимости, готовую закваску можно охладить до температуры хранения 3-10°С и хранить до употребления.
Постоянная температура в процессе сквашивания поддерживается автоматически с точностью до ± 1°С с периодической подачей пара в теплообменник.
Требования к технологическому емкостному оборудованию
Требования к качеству молочных продуктов выдвигают и специальные требования к технологическому емкостному оборудованию.
Высокая чистота внутренней поверхности, отсутствие непроходимых зон, плавные переходы сопрягаемых поверхностей, обязательная зачистка, шлифовка и полировка сварных швов – вот основные условия.
Наружная поверхность должна так же соответствовать стандартам качества. Допустимы следующие способы - шлифованная поверхность (применяется шлифованный или полированный лист в стадии поставки), обработанная стеклошариками или объемное травление.
Все пищевое емкостное оборудование (включая крепежные материалы) изготавливается из нержавеющей стали марки 12Х18Н10Т или ее зарубежных аналогов. Алюминиевые изделия уже не актуальны. Электродвигатели закрываются кожухами. Все чаще производители используют в качестве теплоизоляционного материала экологически чистый материал армофлекс.
Минимальная комплектация резервуаров включает в себя мешалку, смотровой люк, индикатор температуры, электрод нижнего уровня, пневматический индикатор уровня, электрод максимального уровня и панель управления резервуаром.
Заключение
Наиболее современное оборудование, в основном это комплексные резервуары, которые имеют значительные преимущества по сравнению с аналогичными процессами при использовании фляг, а именно:
1. Улучшение качества молока в результате своевременного охлаждения до достаточно низкой температуры.
2. Уменьшение потерь молока при сборе и перевозках.
3. Уменьшение производственных площадей как на фермах, так и на перерабатывающих заводах в результате устранения ряда операций по погрузке, опорожнению, мойке.
4. Снижение затрат труда
5. Увеличение срока службы оборудования
Список литературы
1. http://www.bibliofond.ru/view.aspx?id=513594
2. http://milk-industry.ru/kislomolochnye-produkty/2970-termostatnyy-sposob-proizvodstva-kislomolochnyh-produktov.html
3. http://www.vec-ing.ru/?do=menu&id=37658
4. http://www.metotech.ru/art_termopary_4.htm
Введение
Для любой отопительной системы основной задачей является поддержание уровня температуры в отапливаемой емкости, трубопроводе, помещении. Поддерживать необходимую температуру можно разными способами, однако, самым распространенным является способ, основанный на применении специальных устройств - регуляторов температуры.
На протяжении многих веков люди стремились, собрать и как можно дольше сохранить ценность и качество молока. От глиняных крынок и бутылок до самых современных резервуаров-холодильников и технологических резервуаров прошли свой путь различные виды контейнеров для молока. Емкости широкого спектра и назначения нашли себе применение на всех этапах технологического процесса.
Невозможно представить себе производство пищевых, в том числе молочных продуктов, без емкостей.
В зависимости от принятой технологии доения и обработки молока перед отправкой на молочный завод, его некоторое время хранят на животноводческой ферме, используя для этих целей фляги, приемные баки (отрытые и вакуумные), резервуары для молока и молочных продуктов, резервуары-охладители.
История создания регуляторов температуры
В 50 годах 20 века, в эру развития систем автоматизации, появляются первые устройства для автоматического управления технологическими процессами и установками, осуществляющие поддержание технологических параметров на заданных значениях – регуляторы. Данные приборы принимают от первичного преобразователя текущие значения параметра, производят аналоговую обработку этого сигнала и выдают управляющий сигнал на исполнительный механизм. Существует классификация регуляторов в зависимости от направления действия:
1. Регуляторы прямого действия (управляют исполнительным механизмом за счет энергии, получаемой от регулируемой среды)
2. Регуляторы непрямого действия (управляют исполнительным механизмом за счет энергии, получаемой от постороннего источника).
Чуть позже, в конце 80-х годов, появляются более совершенные устройства, обрабатывающие информацию в цифровом виде при помощи процессоров – контроллеры. Эти устройства обладают более широкими возможностями и не только выполняют функции регулирования, но и заменяют релейные схемы управления и сигнализации. Контроллеры могут отображать параметры на индикаторах и создавать архивы параметров, т.е. выполнять функции вторичных показывающих и регистрирующих приборов. Также они могут вести журналы событий (фиксация неисправностей оборудования, его включение и отключение, отклонения параметров от заданных значений и т.д.), которые, до появления контроллеров, заполнялись операторами технологических процессов вручную.
|
|
Археология об основании Рима: Новые раскопки проясняют и такой острый дискуссионный вопрос, как дата самого возникновения Рима...
Опора деревянной одностоечной и способы укрепление угловых опор: Опоры ВЛ - конструкции, предназначенные для поддерживания проводов на необходимой высоте над землей, водой...
Двойное оплодотворение у цветковых растений: Оплодотворение - это процесс слияния мужской и женской половых клеток с образованием зиготы...
Индивидуальные очистные сооружения: К классу индивидуальных очистных сооружений относят сооружения, пропускная способность которых...
© cyberpedia.su 2017-2024 - Не является автором материалов. Исключительное право сохранено за автором текста.
Если вы не хотите, чтобы данный материал был у нас на сайте, перейдите по ссылке: Нарушение авторских прав. Мы поможем в написании вашей работы!