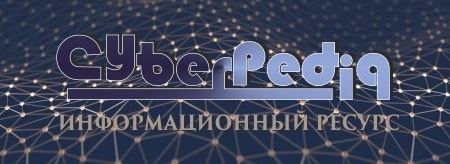
Историки об Елизавете Петровне: Елизавета попала между двумя встречными культурными течениями, воспитывалась среди новых европейских веяний и преданий...
Автоматическое растормаживание колес: Тормозные устройства колес предназначены для уменьшения длины пробега и улучшения маневрирования ВС при...
Топ:
Определение места расположения распределительного центра: Фирма реализует продукцию на рынках сбыта и имеет постоянных поставщиков в разных регионах. Увеличение объема продаж...
Выпускная квалификационная работа: Основная часть ВКР, как правило, состоит из двух-трех глав, каждая из которых, в свою очередь...
Марксистская теория происхождения государства: По мнению Маркса и Энгельса, в основе развития общества, происходящих в нем изменений лежит...
Интересное:
Наиболее распространенные виды рака: Раковая опухоль — это самостоятельное новообразование, которое может возникнуть и от повышенного давления...
Лечение прогрессирующих форм рака: Одним из наиболее важных достижений экспериментальной химиотерапии опухолей, начатой в 60-х и реализованной в 70-х годах, является...
Аура как энергетическое поле: многослойную ауру человека можно представить себе подобным...
Дисциплины:
![]() |
![]() |
5.00
из
|
Заказать работу |
|
|
Введение.
Сварка - процесс получения неразъемного соединения посредством установления межатомных связей между свариваемыми частями при их местном или общем нагреве, или пластическом деформировании, или совместно действии того и другого. Обычно применяется для соединения металлов, их сплавов или термопластов, а также в медицине.
Для производства сварки используются различные источники энергии: электрическая дуга, газовое пламя, излучение, электронный луч, трение, ультразвук. Развитие технологий позволяет в настоящее время осуществлять сварку не только на промышленных предприятиях, но и на открытом воздухе, под водой и даже в космосе. Производство сварочных работ сопряжено с опасностью возгораний, поражений электрическим током, отравлений вредными газами, облучением ультрафиолетовыми лучами и поражением глаз, которые позволяют выносить нагрузки разного рода.
В курсовом работе рассмотрена наплавка валика на массивное тело ручной дуговой сваркой. Необходимо определить склонность стали к образованию холодных трещин. Холодные трещины образуются в результате резкого охлаждения мартенситных и перлитных сталей. Данная проблема решается включением в технологический процесс сварки предварительного подогрева. При необходимости так же возможен сопутствующий подогрев и медленное остывание металла.
Классификация источника нагрева согласно ГОСТ 19521-74.
1.1. По физическим признакам
Класс сварки: термический - это форма энергии, используемой для образования сварного соединения. Вид сварки: Дуговой - вид источника энергии, непосредственно используемого для образования сварного соединения.
1.2. По техническим признакам
|
По техническому признаку дуговая сварка классифицируется по способу защиты металла в зоне сварки, по непрерывности процесса, по степени механизации процесса.
По непрерывности процесса - непрерывный; по степени механизации процесса - механизированный; по способу защиты металла в зоне термического воздействия - в среде защитных газов.
1.3. По технологическим признакам
По технологическим признакам ручная дуговая сварка делиться на 9 групп:
1. По виду электрода - проволочным плавящимся электродом сплошного сечения;
2. По виду дуги - свободной дугой;
3. По характеру воздействия дуги на основной металл - дугой прямого действия;
4. По степени погружения в сварочную ванну - нормальной дугой;
5. По роду сварочного тока - постоянным током;
6. По наличию и направлению колебаний электрода относительно оси шва - со свободным формированием шва;
7. По полярности сварочного тока - током обратной полярности;
8. По количеству дуг с раздельным питанием тока - однодуговая;
9. По количеству электродов с общим подводом сварочного тока - одноэлектродная;
10. По наличию внешнего воздействия на формирование шва - с поперечными колебаниями электрода.
[1]
Рис.1. Схема ручной дуговой сварки плавящимся электродом
Для образования сварного соединения сварщик возбуждает дугу (8) в месте будущего шва и поддерживает ее горение. Сварку выполняют сварочными электродами, которые вручную подают в дугу и перемещают вдоль стыка заготовки. В процессе сварки дуга горит между стержнем электрода (7) и основным металлом (1). Стержень электрода плавится и расплавленный металл каплями стекает в сварочную ванну (9), рис. 1.
Пространство между свариваемыми кромками детали заполняется жидким металлом кромок детали и электрода, происходит перемешивание металлов в одной жидкой ванне.
Вместе со стержнем плавится покрытие электрода (6), образуя защитную газовую атмосферу (5) вокруг дуги и жидкую шлаковую ванну (4) на поверхности расплавленного металла. По мере движения дуги сварочная ванна затвердевает и формируется сварной шов (3). Жидкий шлак после остывания образует твердую шлаковую корку (2). [3]
|
Процесс плавления и переноса электродного металла на изделие происходит непрерывно во время ее горения в виде капель и последовательно повторяется в порядке, указанном на рис. 2. Как видно из рис.2а и 2б после образования капли расплавленного металла происходит ее сближение с изделием и затем кратковременное короткое замыкание и переход капли на изделие после чего возобновляется горение дуги и процесс переноса повторяется в зависимости от полярности сварочного тока, состава электродного металла и покрытия величина капель меняется, от 0,1 - 4мм. В диаметре. При сварке крупными каплями увеличиваются разбрызгивание и потери металла, мелкокапельный перенос обеспечивает стабильность процесса сварки, лучшее использование сварочного материала и лучшее качество. Обычно мелкокапельный перенос достигается при сварке покрытыми электродами. Перенос капель расплавленного металла на изделие даже в самых неудобных его положениях объясняется действием нескольких сил. Сила тяжести способствует переносу капель при сварке в нижнем положении и препятствует в других положениях. Сила поверхностного натяжения уменьшает величину капель, придает им сферическую форму, способствует удержанию их на конце электрода и переходу в ванночку расплавленного метала, удерживает от растекания и придает капле определенную форму.
Рис. 2. Каплеобразный перенос металла:
а – образование капли, б – короткое замыкание и пернос капли, в – возобновление дуги, г – образование новой капли
[4]
Особенности способа сварки.
Для сварки стали, 14ХГС, применяют следующие типы электродов: ЦЛ-14, ЦЛ-18-63, ЦЛ-30-63, НИАТ-3М, УОНИ-13/85. Исходя из параметров сварки и толщины материала я выбрал электроды ЦЛ-18-63 диаметр электрода 4мм. Источник питания я выбрал Kemppi Master MLS 3500.
При сварке электрическая дуга должна быть как можно более короткой.
предварительный разогрев металла (до 300 ºС), После окончания сварки соединения должны проходить термическую обработку для обеспечения высоких механических свойств. Для этого стали подвергают закалке при температуре 880°C. Для того, чтобы избежать деформаций и напряжений при сварке, выполняют низкотемпературный отпуск.
|
Задание : На массивное тело марки стали 14ХГС наплавляется валик с помощью РДС. Оценить возможность разупрочнения основного металла под действием термического цикла ручной дуговой сварки. Режимы сварки: I=140A, U=32B, V=15м/ч.
Валика на массивное тело.
Скорость охлаждения при наплавке валика на массивное тело определяется по формуле (1):
(1)
где: λ – коэффициент теплопроводности, Дж/(см*с*град);
Т - температура наименьшей устойчивости аустенита, °С;
Т0 - температура свариваемого изделия, °С;
q - количество тепла, вводимого дугой в изделие, Дж/с;
Wосв – скорость охлаждения металла, град/с при Тm;
Vсв – скорость сварки, см/с
Количество тепла, вводимого дугой в изделие, q, определяется по формуле:
q = U д I св 𝜂и, (2)
где Uд - напряжение на дуге, В;
Iсв - сила сварочного тока, А;
𝜂и -эффективный КПД процесса нагрева изделия дугой.
q=32*140*0.75=3360 Дж/с
Полученные результаты расчетов формулы (2) подставляем в формулу :
/с (1)
5. Расчет критической скорости охлаждения, приводящие к образованию 95 %-го ферритоперлита (ФП)
Определяется по формуле (3):
WФП95 ≅0,1* 0,343(Cэ)-4,1 (3)
где Cэ – эквивалентное содержание углерода в стали
Эквивалентное содержание углерода,Сэ, в стали рассчитывается по формуле (4):
Сэ=С%+Мп%/6+(Cr+V)/%/5+Mo%/4+(Ni+Cu)%/15 (4)
Сэ=0,14%+1%/6+0,7%/5+(0,3%+0,3%)/15=0.48%
Полученные результат расчета заносим в формулу (3):
WФП95 ≅0,1* 0,343*(0,48)-4,1=20,27℃
Полученные результаты расчетов заносим в таблицу для сравнения скорости охлаждения при наплавке валика на массивное тело и критической скорости охлаждения.
![]() | WФП95 |
120,9 | 20,27 |
В случае Woсв> WФП95 я увеличиваю температуру предварительного подогрева и вновь провожу расчеты.
Расчет температуры необходимого подогрева определяется по формуле (5):
Тпод=350 (5)
Где Сэб рассчитывается по формуле
Сэб=Сэ*(1+0,005* δ) (6)
При наплавке валика на массивное тело принять δ=0
Сэб=0.48*(1+0,005* 0)=0,48
Подставляем полученные результаты в формулу (5):
Тпод=350 =168
Заново рассчитываем скорость охлаждения при сварке с учетом предварительного подогрева, приняв в формуле (1) То=Тпод:
|
/с
Полученные результаты расчетов заносим в таблицу для сравнения скорости охлаждения при наплавке валика на массивное тело и критической скорости охлаждения.
![]() | WФП95 |
76,3 | 20,27 |
Заново рассчитываем скорость охлаждения увеличив температуру подогрева до 450оС
/с
Полученные результаты расчетов заносим в таблицу для сравнения скорости охлаждения при наплавке валика на массивное тело и критической скорости охлаждения.
![]() | WФП95 |
18,7 | 20,27 |
Вывод : Сравнивая скорости охлаждения, видно, что скорость охлаждения, приводящая к образованию 95%-го ферритоперлита меньше скорости охлаждения при сварке. Соответственно холодные трещины в процессе сварки образовываться будут. [6]
Введение.
Сварка - процесс получения неразъемного соединения посредством установления межатомных связей между свариваемыми частями при их местном или общем нагреве, или пластическом деформировании, или совместно действии того и другого. Обычно применяется для соединения металлов, их сплавов или термопластов, а также в медицине.
Для производства сварки используются различные источники энергии: электрическая дуга, газовое пламя, излучение, электронный луч, трение, ультразвук. Развитие технологий позволяет в настоящее время осуществлять сварку не только на промышленных предприятиях, но и на открытом воздухе, под водой и даже в космосе. Производство сварочных работ сопряжено с опасностью возгораний, поражений электрическим током, отравлений вредными газами, облучением ультрафиолетовыми лучами и поражением глаз, которые позволяют выносить нагрузки разного рода.
В курсовом работе рассмотрена наплавка валика на массивное тело ручной дуговой сваркой. Необходимо определить склонность стали к образованию холодных трещин. Холодные трещины образуются в результате резкого охлаждения мартенситных и перлитных сталей. Данная проблема решается включением в технологический процесс сварки предварительного подогрева. При необходимости так же возможен сопутствующий подогрев и медленное остывание металла.
Классификация источника нагрева согласно ГОСТ 19521-74.
1.1. По физическим признакам
Класс сварки: термический - это форма энергии, используемой для образования сварного соединения. Вид сварки: Дуговой - вид источника энергии, непосредственно используемого для образования сварного соединения.
1.2. По техническим признакам
По техническому признаку дуговая сварка классифицируется по способу защиты металла в зоне сварки, по непрерывности процесса, по степени механизации процесса.
По непрерывности процесса - непрерывный; по степени механизации процесса - механизированный; по способу защиты металла в зоне термического воздействия - в среде защитных газов.
|
1.3. По технологическим признакам
По технологическим признакам ручная дуговая сварка делиться на 9 групп:
1. По виду электрода - проволочным плавящимся электродом сплошного сечения;
2. По виду дуги - свободной дугой;
3. По характеру воздействия дуги на основной металл - дугой прямого действия;
4. По степени погружения в сварочную ванну - нормальной дугой;
5. По роду сварочного тока - постоянным током;
6. По наличию и направлению колебаний электрода относительно оси шва - со свободным формированием шва;
7. По полярности сварочного тока - током обратной полярности;
8. По количеству дуг с раздельным питанием тока - однодуговая;
9. По количеству электродов с общим подводом сварочного тока - одноэлектродная;
10. По наличию внешнего воздействия на формирование шва - с поперечными колебаниями электрода.
[1]
|
|
Эмиссия газов от очистных сооружений канализации: В последние годы внимание мирового сообщества сосредоточено на экологических проблемах...
Семя – орган полового размножения и расселения растений: наружи у семян имеется плотный покров – кожура...
Архитектура электронного правительства: Единая архитектура – это методологический подход при создании системы управления государства, который строится...
Автоматическое растормаживание колес: Тормозные устройства колес предназначены для уменьшения длины пробега и улучшения маневрирования ВС при...
© cyberpedia.su 2017-2024 - Не является автором материалов. Исключительное право сохранено за автором текста.
Если вы не хотите, чтобы данный материал был у нас на сайте, перейдите по ссылке: Нарушение авторских прав. Мы поможем в написании вашей работы!