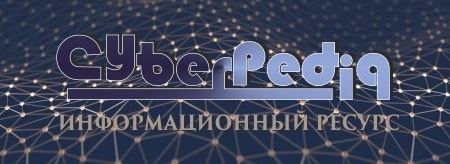
Индивидуальные очистные сооружения: К классу индивидуальных очистных сооружений относят сооружения, пропускная способность которых...
Опора деревянной одностоечной и способы укрепление угловых опор: Опоры ВЛ - конструкции, предназначенные для поддерживания проводов на необходимой высоте над землей, водой...
Топ:
Когда производится ограждение поезда, остановившегося на перегоне: Во всех случаях немедленно должно быть ограждено место препятствия для движения поездов на смежном пути двухпутного...
Техника безопасности при работе на пароконвектомате: К обслуживанию пароконвектомата допускаются лица, прошедшие технический минимум по эксплуатации оборудования...
Основы обеспечения единства измерений: Обеспечение единства измерений - деятельность метрологических служб, направленная на достижение...
Интересное:
Уполаживание и террасирование склонов: Если глубина оврага более 5 м необходимо устройство берм. Варианты использования оврагов для градостроительных целей...
Распространение рака на другие отдаленные от желудка органы: Характерных симптомов рака желудка не существует. Выраженные симптомы появляются, когда опухоль...
Лечение прогрессирующих форм рака: Одним из наиболее важных достижений экспериментальной химиотерапии опухолей, начатой в 60-х и реализованной в 70-х годах, является...
Дисциплины:
![]() |
![]() |
5.00
из
|
Заказать работу |
|
|
Таблица 1. Проектирование технологического маршрута и механическойобработки штока бурового насоса.
Операции | Наименование и содержание операции | Оборудование |
005 | Фрезерно – центровальная. Установить заготовку в приспособление; Фрезеровать одновременно торцы 1 и 2; | Станок полуавтомат центровально- подрезной двухсторонний 2Б931 фреза 2214-0153 ВК8 ГОСТ 9473-80 штангенциркуль ШЦ- -500-0,1 ГОСТ 166-89 фреза 2214-0154 ВК8 ГОСТ 9473-80 штангенциркуль ШЦ- -500-0,1 ГОСТ 166-89 |
Центровать одновременно торцы 1 и 2; Снять деталь со станка; | Сверло центровочное 2317-0000 ГОСТ 14952-75 Пробка 8133-0914 Н14 ГОСТ 14810-69 | |
Установить деталь на станке; Точить поверхность диаметром 70 мм; Точить поверхность диаметром 64 мм. | Станок токарно-винторезный 16К20 ПФ101 Резец 2103-0057 Т15К6 ГОСТ 18879-73 штангенциркуль ШЦ- -200-0,05 ГОСТ 166-89 Резец 2103-0058 Т15К6 ГОСТ 18879-73 штангенциркуль ШЦ- -200-0,05 ГОСТ 166-89 | |
010 | Токарная
Точить две фаски 1 ![]() ![]() ![]() ![]() | Резец 2102-0055 Т15К6 ГОСТ 18877-73 штангенциркуль ШЦ- -200-0,05 ГОСТ 166-89 Резец 2102-0056 Т15К6 ГОСТ 18877-73 штангенциркуль ШЦ- -200-0,05 ГОСТ 166-89 Резец прорезной 2120-0501 ГОСТ 18874-73 штангенциркуль ШЦ- -200-0,05 ГОСТ 166-89 |
015 | Резьбонакатная
Установить деталь на станке.
Накатать резьбу М 64 ![]() | Станок токарно-винторезный 16К20 ПФ101 Головка ВНГН 55Н ГОСТ19256-73 Кольцо 8211-0000 6h ГОСТ 17763-72 штангенциркуль ШЦ- -200-0,05 ГОСТ 166-89 |
020 | Кругло-шлифовальная
Установить деталь на станке;
Шлифовать поверхность 70 мм;
Накатать резьбу М 70 ![]() | Станок круглошлифовальный ЗУ12АФ11. Круг ПП 125 25 32; 25АСН5К ГОСТ 2421-83 Микрометр МК50-1 ГОСТ6507-90 |
025 | Токарная
Установить деталь на станке
Калибровать резьбу М 64 ![]() ![]() | Станок токарно-винторезный 16К20 ПФ101 Резец резьбовой 2664-0000 Кольцо 8211-0000 6h ГОСТ 17763-72 Микрометр МК50-1 ГОСТ6507-90 |
030 | Контрольная
Контролировать твердость и размеры:
диаметром 70 h8
резьбу М 70 ![]() ![]() | Микрометр МК50-1 ГОСТ6507-90 |
035 | Маркировать марку стали и номер чертежа | Керн |
040 | Упаковочные Шлифованные и рабочие поверхности смазать солидолом, укрыть накладками | Стол упаковки |
|
Закалка ТВЧ и ВИЗ
Метод закалки ТВЧ разработан советским ученым Вологдиным В.П.
Основан на том, что если в переменное магнитное поле, создаваемое проводником-индуктором, поместить металлическую деталь, то в ней будут индуцироваться вихревые токи, вызывающие нагрев металла. Чем больше частота тока, тем тоньше получается закаленный слой.
Обычно используются машинные генераторы с частотой 50…15000 Гц и ламповые генераторы с частотой больше 106 Гц. Глубина закаленного слоя – до 2 мм.
Индукторы изготавливаются из медных трубок, внутри которых циркулирует вода, благодаря чему они не нагреваются. Форма индуктора соответствует внешней форме изделия, при этом необходимо постоянство зазора между индуктором и поверхностью изделия.
1 – закаливаемая деталь; 2 – индуктор; 3 – спрейер.
Рисунок 3. - Схема технологического процесса закалки ТВЧ
После нагрева в течение 3…5 с индуктора 2 деталь 1 быстро перемещается в специальное охлаждающее устройство – спрейер 3, через отверстия которого на нагретую поверхность разбрызгивается закалочная жидкость.
Высокая скорость нагрева смещает фазовые превращения в область более высоких температур. Температура закалки при нагреве токами высокой частоты должна быть выше, чем при обычном нагреве.
При правильных режимах нагрева после охлаждения получается структура мелкоигольчатого мартенсита. Твердость повышается на 2…4 HRC по сравнению с обычной закалкой, возрастает износостойкость и предел выносливости.
|
Перед закалкой ТВЧ изделие подвергают нормализации, а после закалки низкому отпуску при температуре 150…200oС (самоотпуск).
Наиболее целесообразно использовать этот метод для изделий из сталей с содержанием углерода более 0,4 %.
Закалка индукционная – ТВЧ (токами высокой частоты) характеризуется двумя параметрами: глубиной и твердостью закаленного слоя детали. Для получения тонкого слоя у закаливаемой детали используются индукционные нагреватели (ТВЧ установки) мощностью от 40 кВА до 160 кВА и частотой 20 - 40 кГц либо 40 - 70 кГц. Если осуществляется закалка более глубоких слоев, то используется диапазон частот 6 - 20 кГц.
У поверхностной закалки токами высокой частоты есть ряд преимуществ:
· высокая твердость
· высокая производительность;
· любой уровень глубины закаленного слоя детали;
· отсутствие окалины;
· возможность закалки деталей любых форм;
· возможность внедрения полной автоматизации закалки.
Недостатки:
· в мелкосерийном и единичном производстве изготовление индуктора и разработка технологического процесса могут быть нерентабельными.
· Во-вторых, для некоторых деталей сложной формы изготовление индуктора затруднительно или даже невозможно.
· В-третьих, на деталях, имеющих глубокие впадины, выступы, резкие переходы, острые углы и т. д., не удается получить равномерной толщины закаленного слоя.
Хотя это ограничивает возможность применения высокочастотной закалки, тем не менее в массовом и крупносерийном производстве для таких деталей, как коленчатые валы, шестерни, втулки, шпиндели, борштанги, валки холодной прокатки и др., поверхностная закалка ТВЧ находит все большее применение.
Высокочастотная импульсная закалка (ВИЗ) предназначена для поверхностного упрочнения стальных и чугунных деталей машин.
Сущность процесса заключается в скоростном нагреве поверхности детали мощным импульсным ВЧ полем и последующей быстрой автозакалке нагретого слоя теплосбросом в глубину металла. Образование высокодисперсных упрочняющих структур (мартенсит, карбиды и др.) повышает твердость, износостойкость и другие свойства металла, увеличивает ресурс работы такой детали в несколько раз.
Для получения тока высокой частоты применяются машинные и ламповые генераторы.
|
В зависимости от формы, размеров закаливаемых деталей и предъявляемых к ним требований различают три способа высокочастотной закалки.
Для закалки небольших деталей применяют способ одновременной закалки: вся поверхность закаливаемой детали находится в зоне действия индуктора и нагревается одновременно. Деталь в индукторе должна вращаться. После нагрева реле времени отключает индуктор от генератора и включается водяной душ, который одновременно охлаждает всю деталь.
а – одновременный; б – непрерывно – последовательный; в – последовательный; 1 – деталь; 2 – индуктор; 3 – закалочное устройство; 4 – шланг.
Рисунок 3 – Способы ВИЗ
Детали значительной длины закаливают непрерывно-последовательным способом. Вал 1 вращается вокруг вертикальной оси и перемещается внутри индуктора 2 сверху вниз, последовательно проходя через зону нагрева и зону охлаждения закалочного устройства 3, к которому по шлангу 4 подается вода. Непрерывно-последовательную закалку стальных плит выполняют при помощи плоских индукторов.
Для закалки отдельных участков детали применяют способ последовательной закалки: поверхность нагревается и охлаждается по частям.
Максимальная глубина ВИЗ – 3.5 мм.
Достоинства ВИЗ:
· Снижение хрупкости за счет пластичной сердцевины и диспергирования зерна;
· Возможность упрочнения внутренних и наружных поверхностей;
· Возможность локального упрочнения;
· Снижение затрат энергии на нагрев;
· Технологическая простота метода, легкость автоматизации процесса.
Основы монтажа оборудования
Общие сведения
Монтаж – это последовательный процесс сборки, установки оборудования и механизмов, включающий общие подготовительные, монтажные, механические и технические действия квалифицированных специалистов, для последующего запуска оборудования.
При монтаже оборудования следует выполнять следующие правила:
- монтаж оборудования проводят чаще всего днем;
- монтаж нельзя проводить на открытых площадках при ветре более шести баллов, при дожде, снегопаде, гололеде;
- подъем груза должен доводиться до проектного положения, если это не удалось сделать до конца смены, то груз должен быть опущен на нулевую отметку;
|
- груз при подъеме должен быть надежно застропован, т.е. стропы налагаются равномерно без узлов и перекруток и угол между ветвями строп не должен быть больше 90°;
расстроповку груза проводят только после его установки и надежного закрепления
Создавая промышленное производство, стремятся снизить удельные капитальные вложения, эксплуатационные расходы и себестоимость продукции. Данные показатели во многом зависят от качества монтажных и ремонтных работ. Уже на стадии проектирования оборудования и изготовления его необходимо предусматривать методы монтажа и ремонтопригодность технологических машин и аппаратов.
Монтаж оборудования, как правило, состоит из следующих этапов:
· организационно-техническая подготовка монтажа;
· производство монтажных работ;
· пуско-наладочные работы.
Организационно-техническая подготовка монтажа состоит из следующих мероприятий:
· получение монтажной организацией от заказчика технической документации;
· организация монтажной площадки;
· обеспечение строительной готовности объекта;
· организация поставки оборудования;
· оснащение участка монтажным оборудованием;
· разработка и создание безопасных условий труда;
· организация контроля качества работ, подготовка кадров.
1.Техническая документация содержит: планы расположения строящихся объектов; планы и разрезы цехов; чертежи на фундаменты и монтаж оборудования; чертежи на трубопроводы и металлоконструкции; смету на производство монтажных работ; дополнительную документацию на монтаж отдельных узлов.
Монтажная организация составляет план производства работ (ППР), который содержит основные принципиальные решения по монтажу. ППР оформляется в виде пояснительной записки, к которой прикладывается генеральный план, график производства работ, ведомость трудовых затрат и график движения рабочей силы, монтажные чертежи.
Следует отметить, что график движения рабочей силы должен иметь плавный характер (рис. 4.1).
Рисунок 4.1 - График движения рабочей силы
2.Площадка для складирования является составной частью монтажной площадки ирасполагается по возможности вблизи монтируемого объекта.
Размеры площадки П, м2 определяются по формуле:
,
где М - общий вес оборудования, т;
К - коэффициент одновременности поступления (0,5... 0,9);
В - удельная загрузка, т/м2.
Удельная загрузка зависит от вида оборудования и материалов.
3. Строительная готовность объекта. Под этим термином понимают такое состояние строительной части возводимого объекта, когда можно вести монтаж в безопасных условиях и обеспечивать сохранность оборудования и рациональные методы его монтажа. В перекрытиях и стенах должны быть предусмотрены монтажные проемы для транспортировки оборудования.
|
4.Фундаменты под технологическое оборудование. Фундаменты бывают групповые и индивидуальные.
Групповые фундаменты представляют собой бетонное или железобетонное полотно толщиной до 300 мм, с аппаратами весом до 2 т.
Индивидуальные фундаменты используются для установки тяжелого оборудования, а также оборудования, работающего с большими динамическими нагрузками.
5. Поставка и прием оборудования. Для рациональной организации монтажа необходима комплектная поставка оборудования. Правила поставки оборудования следующие.
Малогабаритное оборудование должно поставляться в собранном виде, на подкладках, с установленными внутренними устройствами и деталями для строповки. Защитные покрытия свинцом, медью, лаком, эмалью выполняются на заводе-изготовителе, а футеровка кирпичом и плиткой на месте монтажа.
Крупногабаритное оборудование поставляется максимально укрупненными блоками с соответствующей маркировкой.
Поставляемое оборудование должно иметь ответные фланцы нам штуцерах, а также крепежные детали и анкерные болты.
Порядок транспортировки оборудования по железной дороге и реке следующий:
- по железной дороге допускается перевозка машин и аппаратов по согласованию с Министерством путей сообщения весом до 240 т, диаметром 4 ми длиной 30 м;
- по рекам на судах: диаметром до 8 ми длиной 55 м, ас буксировкой на плаву: диаметром до 10 ми длиной до 100 м по согласованию с Министерством речного флота.
Прием оборудования в монтаж производится на складе путем осмотра без разборки на узлы и детали. При этом проверяют:
- соответствие оборудования чертежам и проектной спецификации;
- комплектность оборудования по упаковочным ведомостям;
- наличие и полноту технической документации завода-изготовителя;
- отсутствие трещин, поломок и т.п.
Для обеспечения нормальной работоспособности оборудования и технологической схемы в целом необходимо точно установить и выверить это оборудование в плане и по высоте. Оборудование, как правило, устанавливается на фундаменте (рис. 4.2), и суммарная жесткость системы "станина оборудования - фундамент" во многом определяет надежность работы технологической схемы. Оборудование устанавливается в основном двумя способами:
- непосредственно на фундамент или бетонную подливку на фундаменте;
- с применением пакетов плоских металлических подкладок.
Для компенсации неточности размеров фундаментов применяются пакеты подкладок, установочные болты, упругие шайбы, фундаментные болты.
1 - оборудование; 2 - пакет пластин; 3 - подливка; 4 - фундамент
Рисунок 4.2 - Установка оборудования на фундаменте
До установки аппаратов на фундамент укладывают подкладки или приспособления для выверки оборудования. При выверке аппаратов на фундаменте проверяют соблюдение требований горизонтальности, соосности, параллельности, вертикальности и привязки осей аппарата к осям здания и строительных конструкций.
Выверку горизонтального положения оборудования следует производить по базовым поверхностям (плоскостям разъема и расточкам под вкладыши подшипников или по контрольным площадкам).
Проверку соосности валов машин и агрегатов, соединяемых муфтами, следует производить в два приема:
1) предварительная проверка при помощи линейки и щупа - это делается до затяжки фундаментных болтов и подливки бетоном плит, рам;
2) окончательная проверка при помощи специальных скоб, устанавливаемых на полумуфтах.
|
|
Состав сооружений: решетки и песколовки: Решетки – это первое устройство в схеме очистных сооружений. Они представляют...
Эмиссия газов от очистных сооружений канализации: В последние годы внимание мирового сообщества сосредоточено на экологических проблемах...
Своеобразие русской архитектуры: Основной материал – дерево – быстрота постройки, но недолговечность и необходимость деления...
Архитектура электронного правительства: Единая архитектура – это методологический подход при создании системы управления государства, который строится...
© cyberpedia.su 2017-2024 - Не является автором материалов. Исключительное право сохранено за автором текста.
Если вы не хотите, чтобы данный материал был у нас на сайте, перейдите по ссылке: Нарушение авторских прав. Мы поможем в написании вашей работы!